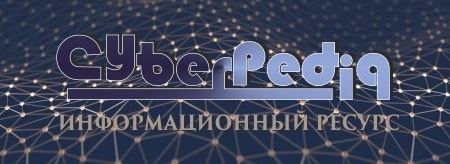
Двойное оплодотворение у цветковых растений: Оплодотворение - это процесс слияния мужской и женской половых клеток с образованием зиготы...
История развития пистолетов-пулеметов: Предпосылкой для возникновения пистолетов-пулеметов послужила давняя тенденция тяготения винтовок...
Топ:
Марксистская теория происхождения государства: По мнению Маркса и Энгельса, в основе развития общества, происходящих в нем изменений лежит...
Техника безопасности при работе на пароконвектомате: К обслуживанию пароконвектомата допускаются лица, прошедшие технический минимум по эксплуатации оборудования...
Основы обеспечения единства измерений: Обеспечение единства измерений - деятельность метрологических служб, направленная на достижение...
Интересное:
Берегоукрепление оползневых склонов: На прибрежных склонах основной причиной развития оползневых процессов является подмыв водами рек естественных склонов...
Инженерная защита территорий, зданий и сооружений от опасных геологических процессов: Изучение оползневых явлений, оценка устойчивости склонов и проектирование противооползневых сооружений — актуальнейшие задачи, стоящие перед отечественными...
Уполаживание и террасирование склонов: Если глубина оврага более 5 м необходимо устройство берм. Варианты использования оврагов для градостроительных целей...
Дисциплины:
![]() |
![]() |
5.00
из
|
Заказать работу |
Курсовая работа: «Разработка технологического процесса восстановления элементов деталей скользящей вилки промежуточного карданного вала автомобиля ЗИЛ 431410»
ВВЕДЕНИЕ
В процессе эксплуатации автомобиля его рабочие свойства постепенно ухудшаются из-за изнашивания деталей, а также коррозии и усталости материала, из которого они изготовлены. В автомобиле появляются отказы и неисправности, которые устраняют при ТО и ремонте.
Исправным считают автомобиль, который соответствует всем требованиям нормативно-технической документации. Работоспособный автомобиль в отличие от исправного должен удовлетворять лишь тем требованиям, выполнение которых позволяет использовать его по назначению без угрозы безопасности движения.
Повреждением называют переход автомобиля в неисправное, работоспособное состояние, переход его в работоспособное состояние называют отказом.
Необходимость и целесообразность ремонта автомобилей обусловлены прежде всего неравной прочностью их составных частей. Поэтому в процессе эксплуатации автомобили проходят на АТП периодическое ТО и при необходимости ТР, который осуществляется путём замены отдельных деталей и агрегатов автомобиля. Это позволяет поддерживать автомобиль в техническом состоянии. При длительной эксплуатации автомобили достигают такого состояния, когда их ремонт в условиях АТП становится технически невозможным или экономически нецелесообразно. В этом случае они направляются в централизованный текущий или КР на авторемонтное предприятие (АРП). Текущий ремонт должен обеспечить гарантированную работоспособность автомобиля на пробеге до очередного планового ремонта. Капитальный ремонт должен обеспечить исправность и полный ресурс автомобиля или агрегата путём восстановления и замены любых сборочных единиц и деталей, включая базовые.
Себестоимость КР автомобиля и их составных частей обычно не превышает 60-70% стоимости новых аналогичных изделий. При этом достигается большая экономия металла и энергетических ресурсов.
При КР полнокомплектных автомобилей они на длительный срок выбывают их эксплуатации. Стремление сократить простои автомобилей в ремонте привело к практике строительства АРП в местах высокой концентрации автомобильного парка, с тем чтобы максимально их приблизить к поставщикам ремонтного фонда.
Одной из прогрессивных тенденций в отечественной практике ремонта явилось распространение агрегатов метода при ТР и автомобилей.
Он осуществляется путём плановой замены неработоспособных агрегатов новыми или заранее отремонтированными, взятыми из оборотного фонда.
При ремонте автомобилей агрегаты в зависимости от их технического состояния подвергаются ТР или КР. Агрегатный метод определяет процессы индустриального ремонта агрегатов от работ по их демонтажу и вмонтажу в эксплуатационных условиях и тем самым обеспечить значительное сокращение простоев автомобилей в ремонте и способствует централизации работ как по капитальному, так и по текущему ремонту агрегатов.
Объектом курсового проекта является вилка, скользящая кардана 130-220-248 с такими дефектами:
Износ отверстия под подшипники;
Износ направляющей шейки.
ОБЩАЯ ЧАСТЬ
Характеристика детали
Вилка, скользящая кардана номер 130-220-248 образует шлицевый наконечник, который вместе со шлицевой втулкой образует подвижное шлицевое соединение, компенсирующее изменение длины карданного вала в результате перемещения заднего моста.
Данная деталь изготовляется из стали 45 которая имеет следующие химический состав и механические свойства.
Таблица 1 - Химический состав Ст 45,% (ГОСТ 1050-74)
Наименование и марка материала | Химический элемент и его процентное содержание, % | ||||||
C | Si | Mn | Cr | S | P | Cu | |
Ст 45 | 0,42-0,50 | 0,17-0,37 | 0,50-0,80 | 0,25 | 0,04 | 0,035 | 0,25 |
Таблица 2 - Механические свойства поковок (ГОСТ 8479-70)
Термообработка | Сечение | σ0,2 | σb | δ5 | φ | KCU, Дж/см2 | HB, Не более |
МПа | % | ||||||
Нормализация | 100-300 | 275 | 530 | 17 | 38 | 34 | 156-197 |
1.2 Технические требования на дефектацию детали
Таблица 3 - Карта технических требований на дефектацию детали
Наименование детали (сборочной единицы): Вилка скользящая карданного вала ![]() |
ТЕХНОЛОГИЧЕСКАЯ ЧАСТЬ
Выбор технологических баз
Правильное взаимодействие деталей в агрегате достигается соблюдением при их изготовлении или ремонте требуемой точности не только размеров, качества обработки поверхностей, но и взаимного расположения осей и отдельных поверхностей. Все это зависит от правильности выбора технологических баз при механической обработке детали.
Для обработки поверхности А, используем торец Г,она является установочной базой, лишает заготовку 3х степеней свободы; В является направляющей базой лишает заготовку 2х степеней свободы. При обработке направляющей шейки заготовка лишается 5 степеней свободы.
При обработке отверстия Б вилку устанавливают в призмы, поверхностью А, которая является явной базой, двойной направляющей лишает заготовку 4х степеней свободы. Торец Г является упорной базой - лишает заготовку 1 степени свободы; база Д при закреплении лишает шестую степень свободы.
Рисунок 1 - Схемы базирования
Расчет режимов обработки
Токарная операция:
Точить поверхность Ø48 начерно
1. Выбор РИ: Резец Т5Л10 ГОСТ 18879-73 (φ= )
2. Глубина резани: t=h=0,8 мм
3. Подача:
4. Скорость резания:
5. Частота вращения шпинделя:
6. Частота вращения шпинделя по станку:
7. Действительная скорость резания:
м/мин
8. Машинное время:
=
мин
7. Расчет норм времени:
Токарная операция:
Общее основное время:
где
время одного перехода
Вспомогательное время:
1. На установку и снятие детали:
2. Вспомогательное время, связь с переходом:
3. Вспомогательное время, связанное с переходом на приемы
не вошедшие в комплексы :
=
= 0,07+0,06+0,07+0,02+0,5=0,72
4. Вспомогательное время на контрольные измерения
Общее время на контрольные измерения определяется:
время измерения одной поверхности инструментов данного вида- количество поверхностей, контрол. инструмент данного вида
5. Поправочный коэффициент на вспомогательное время:
6. Общее вспомогательное время:
Оперативное время:
кардан вилк 0,2+1,15=1,35
4. Время на обслуживание рабочего места:
Время перерывов на отдых и личные надобности:
Штучное время:
Подготовительно заключительное время:
Общее определяется:
=10+7+2.5=19.5
Штучное калькуляционное время:
Норма выработки:
2. Шлифовальная операция:
Основное время: мин.
Вспомогательное время:
1.На установку и снятие детали: мин.
2. Вспомогательное время, связанное с обработкой: мин.
3. Вспомогательное время на измерения: мин.
4. Поправочный коэффициент на вспомогательное время:
5. Общее вспомогательное время, мин:
Оперативное время, мин:
мин.
Время на обслуживании рабочего места, мин:
мин.
Время на отдых и личные надобности, мин:
мин.
Штучное время, мин:
мин.
Подготовительно-заключительное время, мин:
мин.
8. Штучно-калькуляционное время, мин:
мин
где ПЗ - партия запуска деталей.
Норма выработки деталей в смену:
Сверлильная операция:
Общее основное время:
где
время одного перехода
Вспомогательное время:
1. На установку и снятие детали:
2. Вспомогательное время, связь с переходом:
3. Вспомогательное время, связанное с переходом на приемы
не вошедшие в комплексы :
=
= 0,02+0,08+0,17+0,7=0,97
4. Вспомогательное время на контрольные измерения
Общее время на контрольные измерения определяется:
время измерения одной поверхности инструментов данного вида- количество поверхностей, контрол. инструмент данного вида
5. Поправочный коэффициент на вспомогательное время:
6. Общее вспомогательное время:
Оперативное время:
0,14+1,54=1,68
Время на обслуживание рабочего места:
Время перерывов на отдых и личные надобности:
Штучное время:
Подготовительно заключительное время:
Общее определяется:
=12+6=18
Штучное калькуляционное время:
Норма выработки:
Наплавочная операция
Основное время: мин.
Вспомогательное время:
1.На установку и снятие детали: мин.
2.Вспомогательное время, связанное с переходом: мин.
3.Вспомогательное время, связанное с переходом на приемы, не вошедшие в комплексы: мин.
4. Вспомогательное время на измерения:
мин.
5. Поправочный коэффициент на вспомогательное время:
2.6. Общее вспомогательное время, мин:
(49)
мин.
КОНСТРУКТОРСКАЯ ЧАСТЬ
Расчет приспособления
Сила резания:
1
Сила зажима
Крутящий момент
М=518.53*27=14000.31 Н мм
Суммарная сила зажима детали тремя кулачками патрона:
Сила зажима детали одним кулачком: - число кулачков
Сила зажима
Крутящий момент
М=518.53*27=14000.31 Н мм
Суммарная сила зажима детали тремя кулачками патрона:
Сила зажима детали одним кулачком:
Величина силы зажима:
Сила на штоке пневмоцилиндров трехкулачкового патрона:
Диаметр поршня пневмоцилиндров:
Фактическая сила зажима детали по принятому диаметру:
ТЕХНИКА БЕЗОПАСНОСТИ
Требования техники безопасности на объекте проектирования
Общие положения техники безопасности
Настоящие Правила пожарной безопасности распространяются на все действующие предприятия автомобильного транспорта общего пользования Министерства автомобильного транспорта РФ. Настоящие Правила разработаны в соответствии с требованиями ГОСТ 12.1.004-76, ГОСТ 1271.010-76, ГОСТ 12.2.013-75, ГОСТ 12.3.005-75,ГОСТ 12.4.009-75, ГОСТ 12.4.026-76, ГОСТ 25289-82, С НиП 11-93-74, С НиП 11-4-79, С НиП 11-33-75, Типовых правил пожарной безопасности для промышленных предприятий, утверждённых Госгортехнадзором СССР 28.09.1971.; Правил и норм техники безопасности, пожарной безопасности и производственной санатории для окрасочных цехов, утверждённых Минхиммашем СССР 15.08.1974г.; Правил технической эксплуатации подвижного состава автомобильного транспорта, утверждённых Минавтотрансом РСФСР 09.12.1970г.; Правил дорожного движения, утверждённых МВД СССР 02.11.1979г.
В соответствии с действующим законодательством ответственность за обеспечение пожарной безопасности предприятия несёт его руководитель. Контроль и помощь в обеспечении противопожарной защиты предприятия осуществляет вышестоящая организация.
Ответственность за пожарную безопасность мест для стоянок, технического обслуживания (ТО) и ремонта (ТР) автомобилей, отдельных цехов, участков и складов возлагается на их руководителей.
За нарушение настоящих Правил виновные несут дисциплинарную, а также иную ответственность, предусмотренную действующим законодательством, в зависимости от характера нарушения и тяжести его последствий.
Руководители автотранспортных предприятий обязаны: организовывать на подведомственных объектах изучение, выполнение всеми инженерно-техническими работниками (ИТР), слушащими и рабочими настоящих Правил, а также постановлений исполкомов местных Советов народных депутатов, указаний и приказов вышестоящих организаций; организовывать добровольные познанные дружины (ДПД) и пожарнотехническую комиссию и обеспечивать их работу в соответствии с действующими положениями (приложения 1 и 2); организовывать проведение противопожарного инструктажа и занятия по пожарно-техническому минимуму по соответствующей программе (приложение 3); установить на территории, в производственн0-административных, складских и вспомогательных помещениях строгий противопожарный режим оборудовать места и допустимое количество единоверного хранения легковоспламеняющихся горючих веществ, сырья и готовой продукции; установить чёткий порядок осмотра и закрытия помещений после окончания работы) и постоянно обеспечивать строгчайшее соблюдение всеми работающими; назначать приказов лиц, явственных за обеспечение пожарной безопасности мест стоянок автомобилей, помещений для ТО и ТР, участков, цехов и т.д.
Требования техники безопасности при выполнении основных работ
При ТО и ремонте электрооборудования необходимо соблюдать следующие меры безопасности:
при выполнении контрольно-регулировочных работ при работающем двигателе (проверка работы генератора, регулировка реле-регулятора и др.) включить вентиляционный местный отсос;
во избежание захвата одежды или рук обслуживающего персонала вращающимися частями (шкив генератора, лопасти вентилятора и др.) перед началом работы застегнуть рукава и привести в порядок другие части одежды и головного убора;
работать чистым и исправным инструментом; наждачный круг защищать стальным кожухом так, чтобы открытой оставалась только рабочая часть круга;
не работать со снятым кожухом; корпуса электродвигателей и оборудование электротехнического отделения обязательно заземлять.
При мойке агрегатов и деталей ТС необходимо соблюдать следующие требования: концентрация щелочных моющих растворов должна быть не более 5%, после мойки щелочным раствором обязательна незамедлительная промывка горячей водой; детали, работающие в контакте с этилированным бензином, должны подвергаться нейтрализации отложений тетра этил свинца керосином или другой нейтрализующей жидкостью с последующей мойкой горячей водой. Моечные ванны с керосином и другими моющими жидкостями по окончании мойки должны закрываться крышками.
Пожарная безопасность
Меры противопожарной защиты можно разделить на пассивные и активные. Пассивные меры сводятся к архитектурно-планировочным решениям. При проектировании здания необходимо предусмотреть удобство подхода и проникновения в помещения пожарных подразделений; снижение опасности распространения огня между этажами, отдельными помещениями и зданиями, конструктивные меры, обеспечивающие незадымляемость зданий, противопожарные разрывы, преграды для распространения огня, выполнение конструкции здания из трудно горючих материалов и т.д.
Активные меры заключаются в создании автоматической пожарной сигнализации, установке систем автоматического пожаротушения и др. Причинами возникновения пожара может быть: неосторожное обращение с огнём неисправность отопительных приборов, электропроводки, оборудования.
МЧС разделяет пожарную опасность на 5 категорий:
А - взрывопожароопасное производство (карбюраторный участок, малярный);
Б – аналогично (участок ремонта двигателей и других подобных узлов, зоны ТО-1, ТО-2 связаны с ГСМ);
В - пожароопасное производство (шиномонтажный участок, деревообрабатывающий и т.п.);
Г - участки где используются вещества в горючем состоянии, а также сжигающие твёрдые, жидкие и газообразные вещества;
Д - не сжигаемые вещества и материалы в холодном состоянии.
Курсовая работа: «Разработка технологического процесса восстановления элементов деталей скользящей вилки промежуточного карданного вала автомобиля ЗИЛ 431410»
ВВЕДЕНИЕ
В процессе эксплуатации автомобиля его рабочие свойства постепенно ухудшаются из-за изнашивания деталей, а также коррозии и усталости материала, из которого они изготовлены. В автомобиле появляются отказы и неисправности, которые устраняют при ТО и ремонте.
Исправным считают автомобиль, который соответствует всем требованиям нормативно-технической документации. Работоспособный автомобиль в отличие от исправного должен удовлетворять лишь тем требованиям, выполнение которых позволяет использовать его по назначению без угрозы безопасности движения.
Повреждением называют переход автомобиля в неисправное, работоспособное состояние, переход его в работоспособное состояние называют отказом.
Необходимость и целесообразность ремонта автомобилей обусловлены прежде всего неравной прочностью их составных частей. Поэтому в процессе эксплуатации автомобили проходят на АТП периодическое ТО и при необходимости ТР, который осуществляется путём замены отдельных деталей и агрегатов автомобиля. Это позволяет поддерживать автомобиль в техническом состоянии. При длительной эксплуатации автомобили достигают такого состояния, когда их ремонт в условиях АТП становится технически невозможным или экономически нецелесообразно. В этом случае они направляются в централизованный текущий или КР на авторемонтное предприятие (АРП). Текущий ремонт должен обеспечить гарантированную работоспособность автомобиля на пробеге до очередного планового ремонта. Капитальный ремонт должен обеспечить исправность и полный ресурс автомобиля или агрегата путём восстановления и замены любых сборочных единиц и деталей, включая базовые.
Себестоимость КР автомобиля и их составных частей обычно не превышает 60-70% стоимости новых аналогичных изделий. При этом достигается большая экономия металла и энергетических ресурсов.
При КР полнокомплектных автомобилей они на длительный срок выбывают их эксплуатации. Стремление сократить простои автомобилей в ремонте привело к практике строительства АРП в местах высокой концентрации автомобильного парка, с тем чтобы максимально их приблизить к поставщикам ремонтного фонда.
Одной из прогрессивных тенденций в отечественной практике ремонта явилось распространение агрегатов метода при ТР и автомобилей.
Он осуществляется путём плановой замены неработоспособных агрегатов новыми или заранее отремонтированными, взятыми из оборотного фонда.
При ремонте автомобилей агрегаты в зависимости от их технического состояния подвергаются ТР или КР. Агрегатный метод определяет процессы индустриального ремонта агрегатов от работ по их демонтажу и вмонтажу в эксплуатационных условиях и тем самым обеспечить значительное сокращение простоев автомобилей в ремонте и способствует централизации работ как по капитальному, так и по текущему ремонту агрегатов.
Объектом курсового проекта является вилка, скользящая кардана 130-220-248 с такими дефектами:
Износ отверстия под подшипники;
Износ направляющей шейки.
ОБЩАЯ ЧАСТЬ
Характеристика детали
Вилка, скользящая кардана номер 130-220-248 образует шлицевый наконечник, который вместе со шлицевой втулкой образует подвижное шлицевое соединение, компенсирующее изменение длины карданного вала в результате перемещения заднего моста.
Данная деталь изготовляется из стали 45 которая имеет следующие химический состав и механические свойства.
Таблица 1 - Химический состав Ст 45,% (ГОСТ 1050-74)
Наименование и марка материала | Химический элемент и его процентное содержание, % | ||||||
C | Si | Mn | Cr | S | P | Cu | |
Ст 45 | 0,42-0,50 | 0,17-0,37 | 0,50-0,80 | 0,25 | 0,04 | 0,035 | 0,25 |
Таблица 2 - Механические свойства поковок (ГОСТ 8479-70)
Термообработка | Сечение | σ0,2 | σb | δ5 | φ | KCU, Дж/см2 | HB, Не более |
МПа | % | ||||||
Нормализация | 100-300 | 275 | 530 | 17 | 38 | 34 | 156-197 |
1.2 Технические требования на дефектацию детали
Таблица 3 - Карта технических требований на дефектацию детали
Наименование детали (сборочной единицы): Вилка скользящая карданного вала ![]() |
Двойное оплодотворение у цветковых растений: Оплодотворение - это процесс слияния мужской и женской половых клеток с образованием зиготы...
Эмиссия газов от очистных сооружений канализации: В последние годы внимание мирового сообщества сосредоточено на экологических проблемах...
Состав сооружений: решетки и песколовки: Решетки – это первое устройство в схеме очистных сооружений. Они представляют...
Механическое удерживание земляных масс: Механическое удерживание земляных масс на склоне обеспечивают контрфорсными сооружениями различных конструкций...
© cyberpedia.su 2017-2024 - Не является автором материалов. Исключительное право сохранено за автором текста.
Если вы не хотите, чтобы данный материал был у нас на сайте, перейдите по ссылке: Нарушение авторских прав. Мы поможем в написании вашей работы!