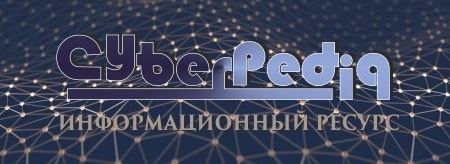
Особенности сооружения опор в сложных условиях: Сооружение ВЛ в районах с суровыми климатическими и тяжелыми геологическими условиями...
Индивидуальные и групповые автопоилки: для животных. Схемы и конструкции...
Топ:
Эволюция кровеносной системы позвоночных животных: Биологическая эволюция – необратимый процесс исторического развития живой природы...
Когда производится ограждение поезда, остановившегося на перегоне: Во всех случаях немедленно должно быть ограждено место препятствия для движения поездов на смежном пути двухпутного...
Интересное:
Отражение на счетах бухгалтерского учета процесса приобретения: Процесс заготовления представляет систему экономических событий, включающих приобретение организацией у поставщиков сырья...
Финансовый рынок и его значение в управлении денежными потоками на современном этапе: любому предприятию для расширения производства и увеличения прибыли нужны...
Наиболее распространенные виды рака: Раковая опухоль — это самостоятельное новообразование, которое может возникнуть и от повышенного давления...
Дисциплины:
![]() |
![]() |
5.00
из
|
Заказать работу |
|
|
СОДЕРЖАНИЕ
ВВЕДЕНИЕ | ||
1 | ИСХОДНЫЕ ДАННЫЕ | |
1.1 | Характеристика типа производства | |
1.2 | Конструктивные особенности детали, материал детали | |
1.3 | Характеристика заготовки | |
2 | РАЗРАБОТКА ПЛАНИРОВКИ УЧАСТКА | |
2.1 | Выбор типа планировки | |
2.2 | Характеристика оборудования | |
2.3 | Расчет и размещение складских помещений | |
2.4 | Планирование размещения контрольных плит | |
2.5 | Выбор способа удаления стружки | |
2.6 | Выбор способа перемещения заготовок и деталей по участку | |
2.7 | Расположение и наполнение пожарного щита на участке | |
3 | ТРЕБОВАНИЯ ОХРАНЫ ТРУДА НА УЧАСТКЕ | |
ВЫВОД | ||
СПИСОК ИСТОЧНИКОВ ИНФОРМАЦИИ | ||
ПРИЛОЖЕНИЯ |
ВВЕДЕНИЕ
Принципы расстановки оборудования. Оборудование участков располагают по одному из принципов: в порядке следования технологических операций; по типам
оборудования. Оборудование участка желательно разместить в пределах одного пролета. Минимальная площадь производственных участков и минимальная транспортная работа по перемещению изделий и отходов будут при плотной расстановкетехнологического оборудования и прямолинейности (прямоточности) перемещения изделий. Оборудования своей длинной стороной может быть установлено вдоль пролета, поперек него или под углом. Наименьшей площади требует планировки при расположении оборудования длинной стороной поперек пролета. Расположением оборудования регулируют длину производственного участка. Расположение в шахматном порядке под углом 15–30 о к оси пролета применяют для оборудования (автоматов, токарно-револьверных станков), работающего с прутковым материалом, и длинных станков (продольных фрезерных, шлифовальных и строгальных).
|
Расположение токарных станков в затылок друг другу, но под углом к оси пролета, повышает безопасность работ: вырвавшаяся заготовка из патрона во время работы не травмирует людей, работающих на соседних станках. Оборудование располагают группами в пролете в два, три или четыре ряда в зависимости от размеров оборудования и ширины пролета. При расположении оборудования длиной стороной поперек пролета, а рядами – вдоль пролета между их рядами оставляют проезд для транспорта. При трех рядах оборудования продольных проездов может быть два. Возле одного проезда может сдвоенный ряд оборудования.
ИСХОДНЫЕ ДАННЫЕ
Характеристика типа производства
Структура технологического процесса, выбор оборудования, технологической оснастки и инструмента во многом зависит от типа производства.
В зависимости от размера производственной программы, характера изготовляемой продукции, а также технологических и экологических требований условий производственного процесса все производства делятся на три основных вида: единичное, серийное и массовое.
В машиностроении и металлообработке наибольшее распространение имеет серийное производство.
Изделия изготавливаются партиями или сериями, состоящими из одноименных, однотипных по конструкции и одинаковых по размерам изделий, запускаемых в производство одновременно.
В условиях серийного производства представляется возможным расположить оборудование в последовательности технологического процесса для одной или нескольких деталей, требующих одинакового порядка обработки.
Выпуск продукции производится применительно к изделиям сериями, а по отношению к деталям – партиями.
Технико-организационные особенности серийного производства обуславливают ряд экономических преимуществ по сравнению с единичным производством:
|
¾ сокращение производственного цикла,
¾ повышение качества продукции,
¾ рост производительности труда,
¾ снижение себестоимости.
Данный тип производства позволяет обрабатывать одноименные и однотипные по конструкции детали и достигать при этом большого экономического эффекта, за счет оптимальных трудовых и материальных затрат на изготовление продукции требуемого качества.
Данная работа выполнена с учётом работы участка в условиях серийного производства.
РАЗРАБОТКА ПЛАНИРОВКИ УЧАСТКА
2.1 Выбор типа планировки
Серийное производство занимает промежуточное положение между единичным и массовым. Это самый распространенный тип производства. Изготовление деталей производится партиями (сериями), состоящими из одноименных, однотипных по конструкции и одинаковых по размерам деталей, запускаемых в производство одновременно. В зависимости от типоразмера детали, размера партии, количества изделий в серии и частоты повторяемости серий в течение года выделяют мелко- средне- и крупносерийное производство.
В серийном производстве технологический процесс разделен на отдельные операции, закрепленные за определенными станками. Применяется самое разнообразное оборудование: универсальное, специализированное, автоматизированное и агрегатные станки. Оснастка – универсально-переналаживаемая. Квалификация рабочих – средняя.
Линейный принцип применяется при поточном производстве и характеризуется определенной последовательностью выполнения операций технологического процесса в каждый момент времени. В этом случае оборудование располагается по ходу технологического процесса.
Предметный принцип применяется при расширении номенклатуры изделий в условиях серийного производства и основан на применении однотипных технологических процессов. В этом случае группирование оборудования осуществляется по конструктивным особенностям деталей, например, участки обработки валов, зубчатых колес, корпусных деталей, в пределах которых оборудование располагается по ходу технологического процесса.
2.2 | Характеристика оборудования |
Технологическое оснащение – комплекс элементов, обеспечивающий выполнение процесса изготовления деталей заданной точности и производительности с оптимальными затратами на производство. [6]
|
Современное технологическое оборудование имеет жесткую конструкцию, позволяющую совмещать черновую и чистовую обработки, обеспечивая при этом высокую точность и качество обрабатываемых поверхностей. Требования к точности и жесткости станков постоянно повышаются, так как погрешности, допущенные при изготовлении станка, переносятся на обработанную деталь. При оценке возможности обеспечения заданной точности обработки заготовок учитываются индивидуальные возможности станка и степень его износа.
Выбор технологического оборудования – станков зависит от:
¾ типа производства, требуемой производительности и себестоимости;
¾ метода обработки отдельных элементов детали;
¾ габаритных и обрабатываемых размеров детали и мощности, необходимой для резания;
¾ возможности обеспечения требуемой точности размеров и формы и качества поверхностей изготовляемой детали;
¾ степени удобства и безопасности работы станка.
Токарный полуавтомат с ЧПУ FORT модели Д 500
Станина из высококачественного чугуна гарантирует высокую жесткость и виброустойчивость. Жесткость шпинделя обеспечивается 4-мя коническими двухрядными подшипниками. Высокоточные ШВП класса точности СЗ со сдвоенной гайкой гарантирует жесткость и точность. Увеличенный диаметр ШВП по оси 2 до 50 мм гарантирует стабильность на максимальных режимах резания.
Оси «С» и «Y» значительно расширяют технологические возможности, позволяет производить фрезерование, вне осевое сверление и нарезание резьбы и другие операции Ось «С» и фрезерная функция значительно расширяют технологические возможности станка.
Рисунок 4. Токарный п/а с ЧПУ FORT модели Д 500
Таблица 4 – Техническая характеристика
Параметры | Значение |
Максимальный диаметр обрабатываемой детали, мм: Максимальная длина обрабатываемой детали, мм: Расстояния между поверхностями двух шпинделей, мм: Перемещение по осям: "X" / "Z" / Y , мм: Мощность привода, кВт: Диапазон частот вращения, мин-1: Размер под патрон / Диаметр патрона, мм: Отверстие в шпинделе, мм: Ускоренное перемещение по оси X1, X2 / Z1, Z2 м/мин: Ускоренное перемещение по оси B / по оси Y м/мин: Количество позиций инструмента/ из них вращающихся Диаметр хвостовика (по DIN69880) / высота резца, мм: Время индексации головки на одну позицию, с: Максимальная частота вращения, мин-1: Максимальный диаметр /скорость вращения инструмента, мм/мин-1: Сечение резца, мм: Мощность приводного инструмента, кВт: Точность позиционирования, мм: Габариты станка, мм: | 190 350 750 135 / 450 / ±40 15 0 - 8000 А2-5/250 А5/55 18 18 / 24 6 / 24 12 15/20 0,14 4500 16/6000 20×20 3,5 ±0,005 3500´1600´1900 |
|
Рисунок 5. Токарно – фрезерный полуавтомат с ЧПУ модели NEF 400
Ключевые особенности NEF 400 Интегрированный шпиндель-двигатель ISM: увеличенное отверстие шпинделя, более высокое число оборотов, увеличенная точность/жесткость по оси С, увеличенные диаметры подшипников для повышения жесткости, жидкостное охлаждение для улучшения термической стабильности, удобство сервисного обслуживания – отсутствует необходимость периодической регулировки ремня. Увеличенный обзор рабочей зоны, удобное управление, компактная конструкция. Компактная конструкция за счет очень жесткой, массивной литой станины станка. Револьверная головка VDI 30 на 12 инструментов и задняя бабка с автоматическим управлением и гидравлическим приводом в стандартной комплектации.
Таблица 5 – Техническая характеристика
Параметры | Значение |
Максимальный диаметр устанавливаемой детали через станину , мм: | 385 |
Максимальный диаметр обточки через станину, мм: | 350 |
Быстрый ход (X), мм: | 255 |
Продольное перемещение (Z) мм: | 800 |
Шпиндельная головка, Size: | 170 h5 |
Диаметр в передней опоре, мм: | 87 |
Диаметр патронных заготовок, мм: | 130 |
Сверление шпинделем , мм: | 200/250 |
Мощность привода (40/100% цикла нагрузки), kW: | 11,5 / 8 |
Диапазон скорости, об/мин: : | 0 – 4 500 |
Быстрый ход (X/Z), мм: | 30/30 |
Диаметр хвостовика (DIN 69880) 30(BDI 30), | 30 (VDI 30) |
Габариты (длина´ширина´высота), мм: | 2812×2638×2810 |
3. Зубофрезерный полуавтомат модели с ЧПУ GHO-200
Зубофрезерный станок с ЧПУ GHO-200 для высокоскоростного, прецизионного зубофрезерования. На станке могут быть обработаны следующие типы колес: цилиндрические прямозубые колеса; цилиндрические косозубые колеса; звездочки; червячные колеса.
Рисунок 7 Зубофрезерный полуавтомат модели с ЧПУ GHO-200
Таблица 6 – Техническая характеристика
Параметры | Значение |
Максимальный диаметр, модуль заготовки, мм: | Ø 200/ 5,5 |
Диаметр стола Ø, мм: | 240 |
Перемещение по оси Z / оси X, мм: | 350/200 |
Угол наклона фрезы, °: | ±45 |
Конус оправки червячной фрезы | NT.№40 |
Максимальный диаметр / длина фрезы, мм: | Ø 180 / 190 |
Максимальная скорость вращения фрезы, об/мин: | 500 |
Максимальная скорость вращения стола, об/мин: | 230 |
Ход задней стойки, мм: | 380-780 |
Ускоренная подача по оси Z, X, м/мин: | 12 |
Ускоренная подача по оси Y, мм/с: | 1 |
Расстояние от поверхности стола до центра фрезы по оси Z, мм: | 200-550 |
Расстояние от поверхности стола до центра фрезы по оси X, мм: | 15-215 |
Привод оси B, вращение инструмента, кВт: | АС 12 / 16 |
Привод оси A, поворотное движение фрезерного шпинделя, кВт: | 1,6 |
Привод оси Z, верт. перемещение фрезерного шпинделя, Нм: | 27 / 2:1 |
Привод оси X, радиальное перемещение передней стойки (Нм) | 27 |
Привод оси C, вращение стола, Нм: | 410 |
Привод оси Y, тангенциальное перемещение инструмента, Нм: | 6 / 10:1 |
Привод оси Y, тангенциальное перемещение инструмента, Нм: | 0,2/0,9 |
Привод системы смазки/ СОЖ, кВт: | 3,7 / 2,2 |
Привод гидросистемы, кВт: | 7600 |
Фиксация фрезерного шпинделя, кг: | 280 -1120 |
Фиксация заготовки | (Ø цилиндра 120 мм) |
Количество управляемых от ЧПУ осей/ одновременно | 6 (X,Y,Z,A,B,C) /4 |
Габариты (длина´ширина´высота), мм: | 2812×2638×2810 |
|
Шлифовальный п/а с ЧПУ мод. GU-3250
Предназначен для наружного шлифования цилиндрических поверхностей изделий и конических поверхностей изделий с небольшой конусностью.
Таблица 7 – Техническая характеристика
Параметры | Значение |
Межцентровое расстояние, мм: | 500 |
Максимальный диаметр шлифования, мм: | 280 |
Предельные углы поворота стола ,° : | -0,5…+8 |
Частота вращения шпинделя бабки изделия, мин-1: | 5-750 |
Шлифовальный круг, мм: | 405´63´127 |
Окружная скорость шлифовального круга, м/сек: | 33 |
Угол поворота шлифовальной бабки,° : | +45, -15 |
Минимальная величина перемещения по оси X/Z, мм: | 0,001 |
Конус шпинделя бабки изделия / пиноли задней бабки | КМ4 |
Ход пиноли задней бабки, мм: | 35 |
Скорость подачи стола, м. мин-1: | 0,005 ÷ 5 |
Общая потребляемая мощность станка, кВт: | 8 |
Габариты (длина×ширина×высота), мм | 3810×2100×1850 |
Рисунок 8 Шлифовальный п/а с ЧПУ мод. GU-3250
Зубошлифовальный п/а с ЧПУ Reishauer RZ 500
На станке Reishauer RZ 1000 обеспечивается преимущества процесса обкатного зубошлифования Reishauer при изготовлении зубчатых колес.
Таблица 8 – Технические характеристики
Параметры | Значение |
Диаметр окружности вершин зубьев, мм: | 500 mm |
Модуль, мм: | 0,8 - 10 |
Угол наклона зубьев, °: | ±40 |
Ширина зубчатого колеса, мм: | макс 250 |
Скорость резания при шлифовании, м/с: | макс. 80 |
Диаметр окружности шлифовального колеса, мм: | 300-205 |
Ширина шлифовального колеса, мм: | 145 |
Диаметр правящего инструмента, мм: | 160 |
Габариты (длина×ширина×высота), мм: | 2800×2760×3100 |
Рисунок 9 Зубошлифовальный п/а с ЧПУ Reishauer RZ 1000
![]() | ![]() |
а | б |
![]() | ![]() |
в | г |
Рисунок 10 Рабочие позиции станка RZ 1000 |
а – позиция шлифования; б – позиция правки; в – позиция смены шлифовального круга; г – позиция контроля.
С помощью поворотной стойки станка шлифовальный шпиндель устанавливается на три различные позиции: шлифования (рис. 10 а), правки (рис. 10 б), смены шлифовального круга (рис. 10 в)
Планирование размещения контрольных плит
Промежуточный (межоперационный) контроль – производится между операциями. В единичном и серийном производстве выполняется на специальных контрольных площадках, установленных в конце каждой группы станков (контрольные площадки указываются в планировке).
Контрольные операции обязательно включают в технологическую карту изготовления детали, так как подробный расчет потребного количества контролеров производится на основе разработанных контрольных карт. Но это требует значительного времени. Обычно число контролеров принимают укрупненно в процентном отношении от числа основных станков:
· в серийном (непоточном) производстве − 5…7 %;
· в массовом (поточном) производстве − 7…10 %.
Площадь контрольных пунктов и контрольного отделения можно определить по планировкам всех рабочих мест работников контроля, оборудования и инвентаря, учитывая, что площадь стандартного контрольного пункта составляет 2×3=6 м2.
Требования к пожарным щитам по Правилам ПБ и ГОСТ 12.4.009
Требования к пожарным щитам приведены в следующих документах:
· Правила противопожарного режима действующие с 01.01.2021 по пост. №1479
· ГОСТ 12.4.009-83 Система стандартов безопасности труда (ССБТ). Пожарная техника для защиты объектов. Основные виды. Размещение и обслуживание
· Выделим основные пункты данных документов, которые касаются требований к пожарным щитам.
Требования охраны труда на участке
1. Правила по охране труда при обработке металлов (далее - Правила) устанавливают государственные нормативные требования охраны труда при выполнении работ в литейном производстве, работ, связанных с термической, холодной и газоплазменной обработкой металлов, а также при
выполнении кузнечно-прессовых работ.
2. Требования Правил обязательны для исполнения работодателями - юридическими лицами независимо от их организационно-правовых форм и физическими лицами (за исключением работодателей - физических лиц, не являющихся индивидуальными предпринимателями), при организации и осуществлении ими работ в литейном производстве, работ, связанных с термической, холодной и газоплазменной обработкой металлов, а также при выполнении кузнечно-прессовых работ.
3. Ответственность за выполнение Правил возлагается на работодателя.
На основе Правил и требований технической (эксплуатационной) документации организации - изготовителя технологического оборудования, применяемого в литейном производстве, при обработке металлов и выполнении кузнечно-прессовых работ (далее - организация-изготовитель), работодателем разрабатываются инструкции по охране труда для профессий и (или) видов выполняемых работ, которые утверждаются локальным нормативным актом работодателя с учетом мнения соответствующего профсоюзного органа либо иного уполномоченного работниками, осуществляющими работы в литейном производстве, при обработке металлов и выполнении кузнечно-прессовых работ (далее - работники), представительного органа (при наличии).
4. В случае применения материалов, технологической оснастки и технологического оборудования, выполнения работ, требования охраны труда к которым не регламентированы Правилами, следует руководствоваться требованиями нормативных правовых актов, содержащих государственные нормативные требования охраны труда, и требованиями технической (эксплуатационной) документации организации-изготовителя.
5. Работодатель обязан обеспечить:
1) безопасность осуществляемых производственных процессов при выполнении работ в литейном производстве, при обработке металлов и выполнении кузнечно-прессовых работ, содержание технологического оборудования и оснастки в исправном состоянии и их эксплуатацию в соответствии с требованиями Правил и технической (эксплуатационной) документации организации-изготовителя;
2) обучение работников по охране труда и проверку знаний требований охраны труда;
3) контроль за соблюдением работниками требований инструкций по охране труда.
6. При выполнении работ в литейном производстве, при обработке металлов и выполнении кузнечно-прессовых работ на работников возможно воздействие вредных и (или) опасных производственных факторов, в том числе:
1) движущегося промышленного транспорта, грузоподъемных машин и механизмов, подвижных элементов технологического оборудования, перемещаемых материалов, заготовок, изделий;
2) падающих материалов, элементов технологического оборудования и инструмента;
3) острых кромок, заусенцев и шероховатостей на поверхности заготовок и изделий, оборудования, инструмента;
4) расположения рабочих мест на значительной высоте (глубине) относительно поверхности пола (земли);
5) замыкания электрических цепей через тело работника;
6) повышенного уровня шума и вибрации;
7) повышенной или пониженной температуры воздуха рабочей зоны;
8) повышенной или пониженной температуры материальных объектов производственной среды;
9) повышенной температуры воды и пара;
10) недостаточной освещенности рабочей зоны;
11) повышенной загазованности и (или) запыленности воздуха рабочей зоны;
12) повышенной или пониженной влажности воздуха рабочей зоны;
13) токсических и раздражающих химических веществ, проникающих в организм человека через органы дыхания, желудочно-кишечный тракт, кожные покровы и слизистые оболочки;
14) физических и нервно-психических перегрузок.
7. При организации выполнения работ, связанных с воздействием на работников вредных и (или) опасных производственных факторов, работодатель обязан принимать меры по их исключению или снижению до уровней допустимого воздействия, установленных требованиями соответствующих нормативных правовых актов.
При невозможности исключения или снижения уровней вредных и (или) опасных производственных факторов до уровней допустимого воздействия в связи с характером и условиями производственного процесса выполнение работ без обеспечения работников соответствующими средствами индивидуальной и (или) коллективной защиты запрещается.
8. Работодатель в зависимости от специфики своей деятельности и исходя из оценки уровня профессионального риска
вправе:
1) устанавливать дополнительные требования безопасности, не противоречащие Правилам. Требования охраны труда должны содержаться в соответствующих инструкциях по охране труда, доводиться до работника в виде распоряжений, указаний, инструктажа;
2) в целях контроля за безопасным производством работ применять приборы, устройства, оборудование и (или) комплекс (систему) приборов, устройств, оборудования, обеспечивающие дистанционную видео-, аудио- или иную фиксацию процессов производства работ.
9. Допускается возможность ведения документооборота в области охраны труда в электронном виде с использованием электронной подписи или любого другого способа, позволяющего идентифицировать личность работника, в соответствии с законодательством Российской Федерации.
II. Требования охраны труда, предъявляемые к производственным зданиям и сооружениям, производственным помещениям и организации рабочих мест
10. Производственные помещения, в которых происходит выделение пыли, должны регулярно очищаться от пыли в сроки, определяемые работодателем или иным уполномоченным работодателем должностным лицом, с использованием систем централизованной пылеуборки или передвижных пылеуборочных машин, а также другими способами, исключающими вторичное пылеобразование.
11. Площадки для обслуживания технологического оборудования, расположенные на высоте 0,5 м и выше от уровня пола, должны иметь ограждения (перила) высотой не менее 1,1 м со сплошной обшивкой по низу (бортиком) высотой не менее 0,15 м и дополнительной ограждающей планкой на высоте 0,5 м от настила площадки.
Ширина площадок должна быть не менее 0,5 м.
12. Высота от настила площадок до конструктивных элементов производственного помещения должна быть не менее 2,0 м. В галереях, тоннелях и на эстакадах допускается уменьшение указанной высоты до 1,8 м.
13. Технологическое оборудование, создающее повышенный уровень шума, должно размещаться в отдельных помещениях, снабженных средствами звукопоглощения и шумоизоляции.
Допускается размещение указанного оборудования в общих помещениях при условии применения средств индивидуальной и коллективной защиты (звукопоглощающих и шумоизолирующих устройств, кожухов, ограждений и других глушителей шума).
14. Технологическое оборудование и трубопроводы, имеющие температуру наружных поверхностей выше 45°С и расположенные в пределах обслуживаемой зоны, подлежат тепловой изоляции.
Тепловая изоляция может заменяться ограждающими конструкциями, исключающими контакт работников с нагретыми поверхностями.
15. В производственных помещениях в местах хранения вредных и (или) опасных веществ и работы с ними должны быть вывешены знаки безопасности с поясняющими надписями.
III. Требования охраны труда при осуществлении производственных процессов и выполнении работ
16. Охрана труда работников, участвующих в осуществлении производственных процессов и выполнении работ в литейном производстве, при обработке металлов и выполнении кузнечно-прессовых работ, обеспечивается:
1) автоматизацией и герметизацией производственных процессов, являющихся источниками вредных и (или) опасных производственных факторов;
2) комплексной механизацией и автоматизацией ручного труда, дистанционным управлением производственными процессами и операциями, связанными с наличием вредных и (или) опасных производственных факторов;
3) заменой производственных процессов и операций, связанных с наличием вредных и (или) опасных производственных факторов, процессами и операциями, при которых указанные факторы отсутствуют или имеют меньшую интенсивность;
4) заменой токсичных и горючих веществ менее токсичными, нетоксичными и негорючими веществами;
5) устранением непосредственного контакта работников с веществами, растворами, исходными материалами, заготовками, полуфабрикатами, готовой продукцией и отходами производства, оказывающими вредное воздействие на организм работника, а также своевременным их удалением и обезвреживанием, а при невозможности устранения контакта с вредными и опасными веществами - применением средств индивидуальной защиты;
6) использованием блокировочных устройств, средств световой и звуковой сигнализации и аварийного отключения технологического оборудования при нарушении производственных процессов;
7) применением безопасных способов хранения и транспортирования исходных и вспомогательных материалов, заготовок и готовой продукции.
17. Производственные процессы в литейном производстве, при обработке металлов и выполнении кузнечно-прессовых работ должны осуществляться в соответствии с технологическими регламентами (технологическими инструкциями), утвержденными работодателем (уполномоченным работодателем должностным лицом).
Вывод
Конструкция детали полностью отвечает требованиям, предъявленным к ней, соответствует назначению и условиям работы, поверхности детали имеют оптимальные степени точности и шероховатость, что дает возможность применение типового технологического процесса для ее изготовления.
Материал заготовки сталь 45 по назначению, химическому составу, механическим и технологическим свойствам соответствует служебному назначению данной детали.
Выбранный метод получения заготовки для изготовления данной детали – штамповка является наиболее рациональным, так как размеры заготовки приближены максимально к размерам готовой детали, что сокращает трудоемкость изготовления детали «Вал-шестерня редуктора», сокращает количество отходов, увеличивает период стойкости режущего инструмента.
Расчет заготовки и операционных припусков обеспечивают правильное распределение припусков, стабильное качество, оптимальный выбор режимов резания, повышает ресурс инструмента, что говори о рациональности выбора заготовки и методов обработки и конечно дипломного проекта.
Маршрут обработки детали составлен в соответствии формирования установочных и измерительных баз, точности обработки и шероховатости поверхностей. Он направлен на повышение технического уровня производства, качества продукции и производительности труда.
Используемое оборудование является в основном полуавтоматическим. Обработка деталей на таком оборудовании производится в полуавтоматическом цикле, поэтому возможно применение более производительных режимов резания, что сокращает время обработки детали на станке, значит, повышает производительность труда на участке. Применяются станки с ЧПУ, они производительны и просты в управлении.
Применяемая технологическая оснастка сокращает трудоемкость обработки, за счет механизации, расширяет технологические возможности станков, повышает качество и точность обработки деталей.
Высокая точность и качество обработки обеспечиваются применением высокопроизводительного режущего инструмента, снижающего себестоимость и учитывающего свойства обрабатываемого материала, а применение резцов с твердосплавными пластинами на механическом креплении, обеспечивают долговечность режущего инструмента и быстроту замены износившейся пластины.
Оптимальные режимы обработки и нормы времени на операциях обеспечиваются полнотой использования режущих свойств инструмента и производственных возможностей технологического оборудования. Хорошая организация технического контроля на участке позволяет сократить и не допустить брака. Правильный контроль способствует повышению производительности труда контролера и станочника, улучшает условия выявления дефектных деталей.
Техпроцесс обработки детали «Вал-шестерня редуктора» обеспечивает рациональное использование оборудования, материальных, трудовых ресурсов, своевременное выполнение заданий с высоким качеством продукции.
Список используемых источников информации
1. Мельников Г.Н., Вороненко В.П. Проектирование механосборочных цехов: Учебник для студентов машиностроительных специальностей вузов. М.: Машино-строение, 1990 – 352с.
2. Вороненко В.П., Схиртладзе А.Г., Брюханов В.Н. Машиностроительное производство. – М.: Высш. школа, Издательский центр «Академия», 2001 –304с.
3. Балабанов А.Н. Краткий справочник технолога – машиностроителя., М.: Изд–во стандартов, 1992.– 464 с.
4. Типовая схема технического обслуживания и ремонта металло- и деревооб - рабатывающего оборудования/ Минстанкопром СССР, ЭНИМС. – М.: Машино-строение, 1988 – 672 с.
5. 5 Положение о системе технического обслуживания и ремонта технологиче-оборудования газопереработающих М.ВНИИЭгазпром, 1989 – 185 с.
6. Мельников Г.Н., Вороненко В.П. Проектирование механосборочных цехов: Учебник для студентов машиностроит. специальностей вузов/Под ред. А.М. Дальского. – М.: Машиностроение, 1990. – 352 с., ил. – (Технология автоматизированного машиностроения)
7. Сурина Е.С. Определение коэффициента приведения и расчет приведенной производственной программы. Методическое пособие к практической работе по курсу «Проектирование машиностроительного производства» для студентов специальности 151001 – «Технология машиностроения» (для всех форм обучения), Новоуральск, НГТИ, 2006. – 17с.
8. Сурина Е.С. Проектирование сборочного цеха по изготовлению станков. Методическое пособие к практической работе по курсу «Проектирование машиностроительного производства» для студентов специальности 151001 – «Технология машиностроения» (для всех форм обучения), Новоуральск, НГТИ, 2006. – 28с.
СОДЕРЖАНИЕ
ВВЕДЕНИЕ | ||
1 | ИСХОДНЫЕ ДАННЫЕ | |
1.1 | Характеристика типа производства | |
1.2 | Конструктивные особенности детали, материал детали | |
1.3 | Характеристика заготовки | |
2 | РАЗРАБОТКА ПЛАНИРОВКИ УЧАСТКА | |
2.1 | Выбор типа планировки | |
2.2 | Характеристика оборудования | |
2.3 | Расчет и размещение складских помещений | |
2.4 | Планирование размещения контрольных плит | |
2.5 | Выбор способа удаления стружки | |
2.6 | Выбор способа перемещения заготовок и деталей по участку | |
2.7 | Расположение и наполнение пожарного щита на участке | |
3 | ТРЕБОВАНИЯ ОХРАНЫ ТРУДА НА УЧАСТКЕ | |
ВЫВОД | ||
СПИСОК ИСТОЧНИКОВ ИНФОРМАЦИИ | ||
ПРИЛОЖЕНИЯ |
ВВЕДЕНИЕ
Принципы расстановки оборудования. Оборудование участков располагают по одному из принципов: в порядке следования технологических операций; по типам
оборудования. Оборудование участка желательно разместить в пределах одного пролета. Минимальная площадь производственных участков и минимальная транспортная работа по перемещению изделий и отходов будут при плотной расстановкетехнологического оборудования и прямолинейности (прямоточности) перемещения изделий. Оборудования своей длинной стороной может быть установлено вдоль пролета, поперек него или под углом. Наименьшей площади требует планировки при расположении оборудования длинной стороной поперек пролета. Расположением оборудования регулируют длину производственного участка. Расположение в шахматном порядке под углом 15–30 о к оси пролета применяют для оборудования (автоматов, токарно-револьверных станков), работающего с прутковым материалом, и длинных станков (продольных фрезерных, шлифовальных и строгальных).
Расположение токарных станков в затылок друг другу, но под углом к оси пролета, повышает безопасность работ: вырвавшаяся заготовка из патрона во время работы не травмирует людей, работающих на соседних станках. Оборудование располагают группами в пролете в два, три или четыре ряда в зависимости от размеров оборудования и ширины пролета. При расположении оборудования длиной стороной поперек пролета, а рядами – вдоль пролета между их рядами оставляют проезд для транспорта. При трех рядах оборудования продольных проездов может быть два. Возле одного проезда может сдвоенный ряд оборудования.
ИСХОДНЫЕ ДАННЫЕ
Характеристика типа производства
Структура технологического процесса, выбор оборудования, технологической оснастки и инструмента во многом зависит от типа производства.
В зависимости от размера производственной программы, характера изготовляемой продукции, а также технологических и экологических требований условий производственного процесса все производства делятся на три основных вида: единичное, серийное и массовое.
В машиностроении и металлообработке наибольшее распространение имеет серийное производство.
Изделия изготавливаются партиями или сериями, состоящими из одноименных, однотипных по конструкции и одинаковых по размерам изделий, запускаемых в производство одновременно.
В условиях серийного производства представляется возможным расположить оборудование в последовательности технологического процесса для одной или нескольких деталей, требующих одинакового порядка обработки.
|
|
Индивидуальные и групповые автопоилки: для животных. Схемы и конструкции...
Архитектура электронного правительства: Единая архитектура – это методологический подход при создании системы управления государства, который строится...
Кормораздатчик мобильный электрифицированный: схема и процесс работы устройства...
Типы оградительных сооружений в морском порту: По расположению оградительных сооружений в плане различают волноломы, обе оконечности...
© cyberpedia.su 2017-2024 - Не является автором материалов. Исключительное право сохранено за автором текста.
Если вы не хотите, чтобы данный материал был у нас на сайте, перейдите по ссылке: Нарушение авторских прав. Мы поможем в написании вашей работы!