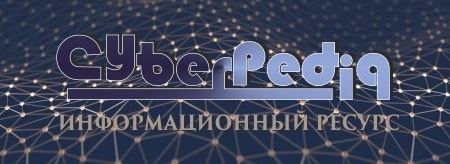
Папиллярные узоры пальцев рук - маркер спортивных способностей: дерматоглифические признаки формируются на 3-5 месяце беременности, не изменяются в течение жизни...
Общие условия выбора системы дренажа: Система дренажа выбирается в зависимости от характера защищаемого...
Топ:
Эволюция кровеносной системы позвоночных животных: Биологическая эволюция – необратимый процесс исторического развития живой природы...
Теоретическая значимость работы: Описание теоретической значимости (ценности) результатов исследования должно присутствовать во введении...
Процедура выполнения команд. Рабочий цикл процессора: Функционирование процессора в основном состоит из повторяющихся рабочих циклов, каждый из которых соответствует...
Интересное:
Лечение прогрессирующих форм рака: Одним из наиболее важных достижений экспериментальной химиотерапии опухолей, начатой в 60-х и реализованной в 70-х годах, является...
Отражение на счетах бухгалтерского учета процесса приобретения: Процесс заготовления представляет систему экономических событий, включающих приобретение организацией у поставщиков сырья...
Аура как энергетическое поле: многослойную ауру человека можно представить себе подобным...
Дисциплины:
![]() |
![]() |
5.00
из
|
Заказать работу |
Компрессорные станции (назначение, подразделение, оборудование).
Объекты, содержащие сооружения и оборудование, необходимое для перекачки продукта называются перекачивающими станциями (далее компрессорными станциями). Роль компрессорной станции заключается в обеспечении надежной работы магистрального газопровода
В зависимости от величины давления воздуха, получаемого на компрессорной станции, они подразделяются на станции:
низкого давления (0,3 - 2,5 мПа);
среднего давления (2,5 - 6,0 мПа);
высокого давления (6,0-35,0 мПа);
сверхвысокого давления (35,0 МПа и выше).
По суммарной производительности всех установленных компрессоров станции подразделяются на:
• малые (до 100 м³/мин.);
• средние (100 - 500 м³/мин.);
• большие (свыше 500 м³/мин.).
Существуют также компрессорные станции для специальных технологических установок, например, холодильные, криогенные и т.д.
Изобретение парового двигателя дало толчок развитию человеческой деятельности во многих отраслях техники, в том числе и технике получения сжатого;
газа, т.к. паровой двигатель конструктивно аналогичен поршневому компрессору.
В России незначительное производство поршневых компрессоров началось в 1900г. Развитие компрессоростроения как отрасли получило во время первых пятилеток. В 1929г. в стране уже три завода выпускали компрессора, в том числе и холодильные. К концу первой пятилетки был освоен выпуск вертикальных бескрейцкопфных компрессоров, с частотой вращения коленчатого вала до 550 об/мин. Во второй и третьей пятилетках было освоено производство горизонтальных компрессоров двойного действия. В послевоенные годы осуществляется переход на повышенные скорости (до 760 - 920 об/мин), были улучшены в 2 - 4 раза массогабаритные показатели. С 1957г. начали выпускаться новые холодильные компрессоры - центробежные и ротационные.
В настоящее время в стране выпускаются практически все типы компрессоров для сжатия и транспортировки газов производительностью от 0,004 до!50м3/с и мощностью привода от нескольких десятых до десятков тысяч кВт.
Уровень создаваемых давлений составляет от 0,01 мПа (вентиляторы) до
350 мПа(компрессоры химических производств).
2. Дополнительная информация
• Добыча природного газа млрд. м³
1950 1960 1970 1975 1980 1985
5,8 45,3 200 320 600 800
• Мощность газопровода Крайний Север - Центр (диаметр трубопровода 2500 мм) составляет 3,5 млн. КВт
• Промышленность увеличивает спрос на кислородные компрессора. Производство кислорода составляет (млн. м3)
1970 1975 1980 1985
14,3 33,2 45,6 65
• Непрерывно возрастает потребность в компрессорах общего назначения (Р=0,8-1,0 мПа)
1970 1975 1980 1985
650 810 1000 1250
• Потребность в передвижных компрессорных станциях и тыс. КВт привода 1970 1975 1980 1985 540 750 1050 1400
• Следует отметить, что на машиностроительных заводах 20 -25% потребляемой энергии приходится на сжатый воздух. Возрастает роль вакуумных машин, микро компрессоров и пневмоавтоматики.
• Выпуск компрессоров в тыс. штук
1970 1975 1980 1985
116 160 260 411
• В СССР компрессоры выпускались на 28 заводах.
• Сравнительные данные по производству компрессоров
Тип компр-ов Мировое пр-во, % Пр-вовСССР, %
Турбокомпрес-
соры 23 13
Ротационные и
винтовые 15 9
Поршневые 62 78
Общие понятия о газораспределительных станциях.
Компрессорные станции, принимающие газ непосредственно от источников газоснабжения, называются головными (ГКС), а расположенные вдоль газопровода - промежуточными (ПКС) или линейными. Имеются также специальные станции, например, для закачки газа в подземные хранилища, для ожижения природного газа, для перекачки попутного газа и др.
По типу используемых компрессоров станции подразделяются на поршневые, турбокомпрессорные и комбинированные, по числу ступеней сжатия - на одно- и многоступенчатые.
Независимо от типа установленного оборудования и технологической схемы компрессорных станций на магистральных трубопроводах предусматриваются следующие процессы обработки газа:
очистка от пыли и капельной влаги;
очистка от сероводорода (при необходимости только на ГКС);
компримирование (сжатие);
осушка и очистка газа от масла (только на ГКС и КС подземного хранения газа);
охлаждение;
одоризация (только на ГКС).
Технологической схемой предусматриваются также установки и системы не-обходимые для работы компрессорной станции. К ним относятся системы охлаждения, смазки, питания топливом, пуска и др.
Рисунок 3 –Принципиальная технологическая схема компрессорной станции подземного хранилища газа
Из газопровода 1 через открытую задвижку 2 газ поступает в пылеуловители 3 из которых по трубопроводам 4 направляется во всасывающий коллектор 5 газо-моторного компрессора 6 первой ступени сжатия. Сжатый газ идет в холодильники 7 и далее в установку 8 для осушки. После осушки по трубопроводу9 через открытую задвижку 10 он попадает в коллектор 11 компрессоров 12 второй ступени сжатия. Сжатый до рабочего давления газ поступает в сепаратор 13 для предварительной очистки от масла.
Тонкой очистки от следов масла газ подвергается в адсорберах 16. Очищенный газ под рабочим давлением направляется в подземное хранилище по трубопроводу 17. При необходимости по трубопроводу 17 через открытую задвижку 18 он поступает в пылеуловители 3 из которых при бескомпрессорной подаче в газопровод по трубопроводу 20 через открытую задвижку 19 подаётся в установку 8 для осушки. Осушенный газ по трубопроводу 22 через открытую задвижку 21 поступает в газопровод 1.
При компрессорной подаче газ из пылеуловителей поступает на первую ступень компрессоров 6. После сжатия до рабочего давления в компрессорах первой ступени он поступает в холодильники 7, а далее - в установку для осушки и по трубопроводу 22 - в газопровод. Пополнение хранилища производится при избытке газа в магистральном газопроводе.
Рисунок 4 - Схема установки для ожижения газа
Из газопровода 1 газ через открытую задвижку 2 поступает в пылеуловители, а от туда по трубопроводу 4 - во всасывающий коллектор компрессоров 5. После сжатия до необходимого давления (обычно до 5,5 мПа)он идет в оросительные холодильники 6, а затем в испаритель 7 каскадной холодильной машины. Здесь газ охлаждается до температуры минус 83°С. Для более глубокого охлаждения газ
дросселируется в устройстве 8; при этом его температура понижается до минус 180°С. При этом жидкий метан стекает на дно сосуда 9, а не сжиженные газы (азот, гелий) поступают в компрессор 10 и далее на разделительную газовую установку 11. Сжиженный газ через открытую задвижку 12 направляется в хранилище 13. При необходимости он из хранилища подается в испарительную установку 14, из неё -во всасывающий коллектор 15 дожимного компрессора 16 и далее по трубопроводу 17 - в магистральный газопровод.
Холодильная машина двухкаскадная. В нижнем каскаде холодильный агент -этилен, в верхнем - аммиак. В состав нижнего каскада входят компрессор 13, конденсатор-испаритель 19, испаритель 7 и дроссельное устройство. В состав верхнего каскада - компрессор 20, конденсатор 21, испаритель-конденсатор 19 и дроссельное устройство. Для уменьшения необратимых потерь при дросселировании используются переохладители 23 и 24. Для переохлаждения используется сжиженный газ, который из сосуда 9 по трубопроводу 22 подаётся в переохладители. Испарившийся метан по трубопроводу 25 поступает во всасывающий коллектор 15 дожимного компрессора 16, который подаёт его в магистральный газопровод. Сжиженный природный газ используется для покрытия пиковых нагрузок, как сырьё для химической промышленности и как топливо для автотранспорта.
Рисунок 2 - Технологическая схема компрессорной станции
Из газопровода 1 под давлением газ поступает в пылеуловители 2. Отсюда по трубопроводам 4 очищенный газ поступает в коллектор 5, из которого идет на сероочистку 6 (если содержание серы в газе более 2г на 100 м3) и далее во всасывающий коллектор 7. При отсутствии серы газ из коллектора 5 через открытую задвижку 8, минуя сероочистку, попадает во всасывающий коллектор, из которого по трубопроводам 9 идет во всасывающий коллектор 10 газомоторных компрессоров 11. Сжатый газ под давлением по трубопроводам 12 направляется в нагнетательный коллектор 13, из которого при необходимости поступает в оросительные холодильники градирни 14 или, минуя их, в установку 15 для осушки от влаги. Сухой газ по трубопроводу 16 попадает в установку 17 для одоризации, затем на замерный участок 18 и далее по трубопроводу 19 через открытую задвижку 20 в магистральный газопровод. Пылеуловители оборудованы свечой 3.
Часть масла, уносимого газом из пылеуловителей и компрессорных цилиндров, остается в масло отделителях 21 и 22, которые установлены на всасывающем и нагнетательном коллекторах.
Особенность схемы - параллельное подключение газомоторных компрессоров, что позволяет резервировать любой компрессор в цехе, не нарушая режим транспортирования газа.
Рисунок 5
Из газопровода или городских газовых сетей по трубопроводу 1 газ поступает в фильтр 2, а из него через замерный участок 3 в газосборник 4. Оттуда по трубопроводам 5 он идет в приёмные коллекторы четырёхступенчатых компрессоров 6. После сжатия до 35 мПа газ подаётся в газосушильную установку 7, а затем - в распределительную установку 8. Отсюда по трубопроводам 9 он направляется в секции аккумуляторов высокого давления 10 (два или три). Каждая секция аккумуляторов связана раздаточным блоком 11, из которого по трубопроводам 12 газ попадает на раздаточные колонки 13.
В начале и в конце магистрального газопровода, а также в тех пунктах, где производится отбор газа из газопровода сооружаются газораспределительные станции. Газ, поступающий из газосборных сетей, попадает в сепараторы 1, затем через мерные устройства 2 расходомеров в газопровод. Перед мерными устройствами обязательно измеряется давление и температура. С помощью запорной арматуры можно отключить любой из её аппаратов не нарушая её работы в целом
Задачи ГРС.
Газораспределительная станция (ГРС), служит для понижения давления газа до уровня, необходимого по условиям его безопасного потребления
По назначению различают несколько типов ГРС:
§ станции на ответвлении магистрального газопровода (на конечном участке его ответвления к населённому пункту или промышленному объекту) производительностью от 5—10 до 300—500 тыс. м3 в час;
§ промысловая ГРС для подготовки газа (удаление пыли, влаги), добытого на промысле, а также для снабжения газом близлежащего к промыслу населённого пункта;
§ контрольно-распределительные пункты, размещаемые на ответвлениях от магистральных газопроводов к промышленным или сельскохозяйственным объектам, а также для питания кольцевой системы газопроводов вокруг города (производительностью от 2—3 до 10—12 тыс. м³ в час);
§ автоматическая ГРС для снабжения газом небольших населённых пунктов, совхозных и колхозных посёлков на ответвлениях от магистральных газопроводов (производительностью 1—3 тыс. м³ в час):
§ газорегуляторные пункты (ГРП) (производительностью от 1 до 30 тыс. м³ в час) для снижения давления газа и поддержания его на заданном уровне на городских газовых сетях высокого и среднего давления;
§ газорегуляторные установки для питания газовых сетей или целиком объектов с расходом газа до 1,5 тыс. м3 в час.
ГРС на магистральных газопроводах понижают начальное давление газа (например, 5 Мн/м², то есть 50 кгс/см²) по одно-, двух- или трёхступенчатой схеме до 0,1 Мн/м² и менее, на автоматических ГРС давление снижается с 5,5 до 3 ·10-2 Мн/м²-, на газорегуляторных пунктах высокое давление (1,2 или 0,6 Мн/м²) снижается до среднего (0,3 Мм/м²) или низкого (300 мм вод. ст.)Технологическая схема АГРС включает все необходимые узлы и системы, укомплектованные современным оборудованием, в том числе: узел переключений, узел очистки газа и сбора конденсата, подогрева, редуцирования, замера, одоризации, подготовки газа для собственных нужд, подготовки теплоносителя, отопления.
Измерение расхода газа в ГРС осуществляется турбинными или ротационными газосчетчиками, размещёнными на газопроводе среднего давления на выходе из ГРС. Температура газа измеряется показывающим термометром в диапазоне от −35 до +50 °C на входе в ГРС и на обоих линиях редуцирования за газовым счётчиком.
Давление газа измеряется с помощью манометров, размещённых на входном газопроводе, выходном газопроводе, перед и за фильтром (или будет применён дифференционный манометр), перед газовым счётчиком, на байпасе, за регулятором давления и на линии редуцирования для котельной. Давление газа на входе и выходе регистрируется в регистрационном устройстве.
В большинстве случаев, ГРС были построены в середине 1970-х годов. [2] В целом, срок эксплуатации российской газотранспортной системы приближается к полувеку: 14 % газопроводов отработали более 33 лет и требуют немедленной замены, еще 20 % приближаются к этому возрасту, 37 % построены 10-20 лет назад и еще 29 % моложе 10 лет. Оптимальным решением является полноценное финансирование и реализация «Газпромом» программы реконструкции и технического перевооружения
Рисунок 7
Газ поступает на осушку в нижнюю часть абсорбционной колонны 1, в которой расположен сепаратор с металлической насадкой, задерживающей капельки воды и масла, а также механические примеси, которые могут быть в газовом потоке. Средняя часть колонны представляет собою ректификационную колонну с несколькими (4 - 10) тарелками. В этой части и происходит в основном осушка газа. В верхней части колонны установлен сепаратор, который улавливает и возвращает обратно капельки сорбента, увлекаемого газовым потоком.
Сорбент поступает в колонну на верхнюю тарелку, с которой затем переливается на ниже расположенные, входя в соприкосновение с газом идущим противотоком и барботирующим через сорбент на каждой тарелке. Газ, пройдя через колонну, подаётся в магистральный газопровод.
Отработанный сорбент собирается на нижней тарелке и направляется в теплообменник 2, а из него в испарительную колонну 3, В теплообменнике 2 происходит подогрев отработанного раствора сорбента до 110 - 130°С теплом горячего регенерированного раствора, идущего из испарительной колонны 3.
В испарительной колонне раствор, стекая по тарелкам, продолжает нагреваться при этом наиболее интенсивно - в нижней части колонны, где находится змеевиковый или трубчатый теплообменник 4, называемый рибойлером. В этой части происходит бурное кипение раствора, а выделяющийся при этом пар поднимается вверх, подогревая стекающий вниз раствор. При этом часть диэтиленгликоля, испарившаяся при кипении, вновь конденсируется. Очищенный от влаги диэтиленгликоль, пройдя теплообменник 2, накапливается в резервуаре 6 и далее насосом 5 подаётся вновь в абсорбционную колонну 1.
Очистка и одоризация газа
В состав ряда природных газов входит в качестве вредной примеси сероводород. Его количество колеблется от 0,02 до 6%, а иногда и до 10%. Сероводород вызывает активную коррозию металла, уменьшая срок службы самого трубопровода, а также арматуры и приборов. Взаимодействуя с металлами сероводород образовывают пирофорные соединения железа обладающие высокой активностью и способностью самовозгорания.
Сероводород и продукт его сгорания - сернистый газ вызывает отравление живых организмов даже при небольшой концентрации, губит растительность, создаёт антисанитарные условия. С другой стороны сероводород может быть с большой пользой использован для получения серы, гипосульфита и т.д. Всё это обуславливает необходимость и экономическую целесообразность очистки газа от сероводорода
Очистка газа от сероводорода может производиться сухим или мокрым способом. При сухом способе газ пропускают через слои твердых поглотительных веществ, при мокром - газ промывают различными растворами. Чаще всего используют при сухом способе активированный уголь, а при мокром - гидрат окиси железа.
При очистке больших объёмов газа используется эталоминовый способ. Поглотителями являются моноэталомин, диэталомин, триэталомин. Способ основан на том, что органические основания интенсивно поглощают сероводород (при температуре 25 - 40°С) и углекислоту, образуя нестойкие соединения, которые при последующем нагреве (выше 105 °С) распадаются выделяя поглощённые газы.
Природный газ не имеет резко выделенного запаха, поэтому его утечку определить трудно. Чтобы отвести угрозу отравления и взрывов в газ добавляют одорант - вещество с резким и неприятным запахом. В качестве одоранта используется этилмеркаптан - органическое сернистое соединение. Добавляют его в количестве 16г (19,1 см3) на 1000 м3. Одоранты легколетучие, горючие жидкости, их пары образуют с воздухом взрывоопасные смеси. При работе с одорантами необходимо строго выполнять правила безопасной эксплуатации установок (противогазы, рукавицы, нейтрализация - марганцовокислым катаем или хлорной известью).
Требования к застройке компрессорной станции.
В расчётных точках трассы определяют площадку для строительства, которая должна удовлетворять следующим требованиям:
•размеры площадки должны удовлетворять условию размещения всех сооружений и объектов;
• рельеф площадки должен быть спокойным;
• грунты должны обладать хорошей несущей способностью;
•уровень грунтовых вод должен быть низким.
Однако, наличие всех требований не всегда можно подобрать, особенно в условиях Крайнего Севера и Сибири (вечномерзлые грунты, болота), трудно доставлять туда материалы и оборудование.
Застройка территории должна проектироваться компактной, однако, необходимо выдерживать расстояния между соседними зданиями и сооружениями обеспечивающими достаточный уровень безопасности.
Таблица 1. Расстояния между зданиями и сооружениями компрессорной станции
Здания и | |||||||
сооруже | КЦ | УОч | УОс | ГРСП | Град | ГСМ | РММ |
ния КС | |||||||
КЦ | - | 10 | 10 | 10 | 20 | 30 | 30 |
УОч | 10 | - | 10 | 10 | 20 | 20 | 30 |
УОс | 10 | 10 | _ | 10 | 20 | 20 | 30 |
ГРСП | 10 | 10 | 10 | . | 20 | 20-30 | 15-30 |
Град | 20 | 20 | 20 | 20 | - | 20 | 20 |
ГСМ | 30 | 20 | 20 | 20-30 | 20 | - | 24 |
РММ | 30 | 30 | 30 | 15-30 | 20 | 24 | . |
КЦ - компрессорный цех; УОч - установки очистки газа от пыли; УОс - установки осушки газа; ГРСП - газораспределительные станции (пункты); Град – градирни вентиляторные; ГСМ - склад масел до 1000м; РММ - ремонтно-механические мастерские и др. вспомогательные здания.
Все сооружения компрессорной станции, как правило, размещают по одну сторону от магистрального газопровода, который на территории станции прокладывается подземным с глубиной укладки не менее 0,8 м.
Инженерные сети и коммуникации обычно проектируют как единую систему в специально отводимых для этого технических полосах
В последние годы находят применение новые конструктивно-планировочные решения - блочно-компклектные автоматизированные компрессорные станции (БККС). Особенность их в том, что на территории станции не будет ни одного капитального здания, всё оборудование, технологические установки и аппаратура, входящие в состав функциональных блоков, скомпонованы в виде транспортабельных монтажных блоков, блок-боксов и блок-контейнеров.
Блок-боксы - транспортабельные здания, внутри которых могут размещаться либо технологические установки, либо инвентарное оборудование. В них длительно пребывает обслуживающий персонал.
Блок-контейнеры - технологические установки с индивидуальными укрытия-ми. Может быть создан искусственный климат для нормальной работы оборудования. Обслуживающий персонал бывает в блок-контейнерах только для ремонта и наблюдения за работой оборудования.
Компрессорные станции с ГМК состоят из одного зала, станции с центробежными нагнетателями - из двух залов, в одном размещены газотурбинные установки, в другом - нагнетатели. Для нагнетателей зал в два-три раза меньше, чем для газотурбинных установок. Если в качестве привода установлены электродвигатели, то стена между залом - монолитная, газонепроницаемая, если газотурбинные установки - то кирпичная или из замоноличенных бетонных панелей.
Основу каркаса здания составляют колонны с консолями для подкрановых балок, подкрановые балки, фермы перекрытия и обвязочные балки. Более подробно со строительными конструкциями компрессорных цехов и их компоновками можно познакомиться в,с.41-42, насосных цехов в, с.44.
В настоящее время при проектировании и строительстве компрессорных станций используются типовые объёмно-планировочные решения, в которых унифицированы основные размеры: пролёты, шаг колонн, высота помещений и т.д.
В одноэтажных зданиях пролёты размером до 18м кратны модулю 3000мм (6,9, 12,15 и 18м), а пролёты более 18м - модулю 6000мм.
Высота цеха от пола до низа несущей конструкции покрытия кратна модулю брФ|1№ при высоте от 3,6 до 4,8м, удвоенному модулю (12 м) при высоте от 4,8 до 10,8 м и утроенному (1800мм) при высоте более 10,8м. На рисунке 21 приведена габаритная схема здания компрессорной станции.
Пролет Высота, м
L, м H1 H2
12 3,8 2,2
12 5,0 2,2
18 8,5 4,1
18 10,3 4.1
2.9.1 Фундаменты зданий и сооружений
Фундаменты должны удовлетворять следующим требованиям: воспринимать расчётную нагрузку и равномерно распределять её на грунт; осадка фундамента не должна превышать расчётную величину; фундамент должен выдерживать в необходимых случаях боковое давление грунта без горизонтальных сдвижек и т.п.
Фундаменты под одиночные сосредоточенные нагрузки (колонны, стойки) изготавливают из бетона или железобетона. Состоят они из фундаментных подушек и фундаментных стенных блоков, которые устраивают по всей длине стены. Такие фундаменты называются ленточными.
Широко используются свайные фундаменты, в них используют сваи-стойки и висячие сваи. Несущей поверхностью сваи-стойки является нижняя часть сваи, как правило сваи опираются конусами на твёрдые, чаще скальные, слои грунта. Несущая способность висячих свай обуславливается силами трения по боковой поверхности сваи сил сопротивления по нижнему концу. Свайные фундаменты незаменимы на грунтах с вечной мерзлотой. Глубина заложения фундамента (его подошвы) не должна быть меньше глубины промерзания грунта в районе строительства, т.к. при замерзании грунты вспучиваются и фундаменты поднимаются. При оттаивании грунтов возможны неравномерные осадки фундаментов, образование в них трещин, перекосов.
Фундаменты под динамические нагрузки (компрессоры, ГТУ, электродвигатели) рассчитываются по специальным методикам /,с.58 /.
2.9.2 Несущие и ограждающие конструкции
К ним относятся элементы составляющие каркас здания: колонны, подкрановые балки, балки покрытий, фундаментные балки, т.е. элементы воспринимающие нагрузку от других частей здания. Колонны выполняются железобетонными или металлическими. Железобетонные колонны могут быть прямоугольного сечения или двухветвевыми. Металлические колонны могут быть сплошными и решетчатыми. Подкрановые балки - составная часть каркаса здания, одновремённо по ним укладываются пути для мостового крана. Чаще их делают из железобетона, имеют тавровое сечение. Балки покрытий выполняют из железобетона или из металлических ферм.
Несущие элементы (балки, фермы) опираются на колонны и образуют вместе с ними пространственный каркас здания.
Ограждающие конструкции - блоки и панели, укладываемые, и навешиваемые на несущие конструкции. Стеновые панели делают из железобетона, иногда асбоцементные на алюминиевом каркасе, Стеновые панели могут изготовляться с монтажными отверстиями и проёмами для пропуска коммуникаций, существуют так же оконные и карнизные панели. Панели и плиты покрытия здания обычно железобетонные.
Узлы монтажа стен, крепление подкрановых балок, стыковка стеновых панелей. устройство покрытия и т.д. см. с.68 - 73.
Осушка воздуха на КСОН.
В некоторых случаях отделение воды и масла от сжатого газа бывает недостаточным, особенно в установках среднего и высокого давлений (6,0 – 30,0Мпа). Поэтому используются специальные установки для осушки газа. Наиболее эффективным способом осушки является адсорбционный способ, при котором используются вещества, обладающие способностью поглощать влагу (адсорбенты).
Из твёрдых поглотителей наиболее распространены силикагель, алюмогель, феррогель и др., поглотительная способность которых основана на поверхностной конденсации и капиллярной структурой адсорбента,
Алюмогелъ - активированный алюминий, состоит из 92% окиси алюминия 8% различных примесей. Инертное вещество, не коррозирует аппаратуру, не ядовит, не растворяется в воде, устойчив против истирания. Размеры зерен 3-6 м удельный вес - 0,8т/м3, свободный объём 50% от объёма., занимаемого адсорбентом.
Силикагель - состав близок к кварцевому песку, улавливает влагу от 4 до 10% по массе. Легко регенерируется. Время работы блока 8 часов, затем в течении 3 часов регенерируется сухим воздухом или нейтральным газом, чаще азотом, при t = 240 - 300°С и в течение 5 часов остывает. Если в установке два блока, то во время регенерации одного, второй работает.
Воздухосборники КСОН.
В компрессорных установках с поршневыми компрессорами имеют место пульсации газа, Колебания потока могут также возникать при подключении или отключении крупных потребителей. Пульсирующий в трубопроводах поток газа приводит к колебанию давления нагнетания, что снижает производительность компрессора и повышает расход электроэнергии (на 1,5 - 3,0%).
Для исключения пульсаций применяют воздухосборники (ресиверы), выравнивающие давление и аккумулирующие сжатый газ. Кроме того в воздухосборниках происходит дополнительное отделение масла и воды.
Воздухосборник представляет собой герметичный сосуд цилиндрической форы, вертикального или горизонтального исполнения.
Воздухосборники относятся к сосудам работающим под давлением, поэтому их эксплуатация производится в соответствии со специальными правилами. Изготовляются воздухосборники из листовой стали с помощью электросварки На аппаратах имеются патрубки и лаз. На нижнем днище - лапы для крепления на фундаменте.
Из основных требований к воздухосборникам следует отметить:
• на воздухосборнике должны быть установлены два предохранительных клапана отрегулированных на предельное давление, превышающее рабочее 10%;
• обязательна установка манометра с предельной шкалой, превышающей 0,2Мпа давление, необходимое для испытания воздухосборника (1,2Мпа - воя 0.,8Мпа - воздухом);
• при диаметре аппарата до 0,8м в воздухосборнике устраивается люк, а диаметре свыше 0,8м - лаз, которые позволяют производить внутренний осмотр и очистку;
• на аппарате устанавливается запорный вентиль для отключения воздух сборника от сети, спускные приспособления - кран, вентиль или конденсатоотводчик для выпуска масла и воды., а также продувки аппарата;
• на аппарате может быть установлена легкоплавкая предохранитель пробка (в верхней части аппарата), которая дублирует предохранительный клапан. Расчёт воздухосборника сводится к определению его объёма
, м3 ;
где Qk - максимальная подача воздуха в воздухосборник, м3/мин.
Высота аппарата находится в следующем соотношении с его диаметром
Н = (2,0-2,7)D, м.
Объём воздухосборника для передвижного компрессора в 7 - 10 раз меньше чем для стационарного.
Воздухосборники обычно устанавливают вне помещения компрессор станции в местах не опасных для обслуживающего персонала. Территория занимаемая воздухосборниками огораживается. По согласованию с технической инспекцией и пожарной охраной возможна установка аппаратов и в помещении. Воздухосборник устанавливается на фундаменте на расстоянии не превышающем 2,5м от стены (до оси аппарата), но не более 25 м от нагнетательного патрубка компрессора, Устанавливают аппараты в теневой стороне, окрашивая в светлые тона.
Над горизонтальными аппаратами устраивают навес, а сами аппараты устанавливаются с небольшим уклоном (0,003 - 0,005) в сторону спускного вентиля, который соединяется с баком для конденсата. Выпуск масла и воды осуществляется раз в смену, а также перед пуском и остановкой компрессора. На воздухопроводе между воздухосборником и компрессором не разрешается устанавливать запорный вентиль, если до него нет предохранительного клапана.
Воздухосборники испытываются в следующих случаях:
• после монтажа при вводе в эксплуатацию;
• после ремонта;
• через шесть лет нормальной работы;
• при переводе на более высокое давление;
• по специальному предписанию технической инспекции. Воздухосборник не прошедший испытания к эксплуатации не допускается. Предприятие должно иметь зарегистрированный в технической ив журнал на каждый аппарат, в котором должны быть:
• чертёж воздухосборника с технической характеристикой;
• акт освидетельствования и гидравлического испытания;
• расчёты аппарата на прочность, а также сведения об испытаниях, при авариях воздухосборника, как аппарата работающего под давлением. Освидетельствование проводят не реже:
• одного раза в год - наружный осмотр;
• одного раза в три года - внутренний осмотр;
• одного раза в шесть лет - гидравлические испытания.
Требования к линейной части магистральных газопроводов.
Для установления оптимальных параметров рассчитываемого газопровода не-обходимо прежде всего установить связь между его пропускной способностью, давлением газа в расчётном участке и перепадом давления на этом участке.
Пропускная способность газопровода, при перепаде высоты по длине не более 200 м, определяется по формуле
где Q - пропускная способность газопровода (t=20 °С, Р=760мм рт.ст.), м3/сутки;
D- внутренний диаметр трубопровода, см;
Р1, Р2 - давление газа на входе и на выходе из расчётного участка, кг/см2;
Тср - средняя на участке температура, К;
zср- средний по участку коэффициент сжимаемости газа;
L – длина расчетного участка, км.
Из уравнения видно, что производительность газопровода в первую очередь
зависит от диаметра газопровода и в меньшей мере от давления. Поэтому необходимо стремиться к возможно большему диаметру трубопровода. В настоящее время основной сортамент труб используемых имеет диаметр от 1400 до 2500 мм.
Толщина труб определяется в основном из соображений прочности. Такая толщина стенок в сочетании с применением сталей 14ХГС, 16ГН, 17ГС
позволяет поддерживать в газопроводе давление 5,0-5,5мПа и более. Это давление является наиболее выгодным и приводит к минимальному расходу металла.
Компрессорные станции (назначение, подразделение, оборудование).
Объекты, содержащие сооружения и оборудование, необходимое для перекачки продукта называются перекачивающими станциями (далее компрессорными станциями). Роль компрессорной станции заключается в обеспечении надежной работы магистрального газопровода
В зависимости от величины давления воздуха, получаемого на компрессорной станции, они подразделяются на станции:
низкого давления (0,3 - 2,5 мПа);
среднего давления (2,5 - 6,0 мПа);
высокого давления (6,0-35,0 мПа);
сверхвысокого давления (35,0 МПа и выше).
По суммарной производительности всех установленных компрессоров станции подразделяются на:
• малые (до 100 м³/мин.);
• средние (100 - 500 м³/мин.);
• большие (свыше 500 м³/мин.).
Существуют также компрессорные станции для специальных технологических установок, например, холодильные, криогенные и т.д.
Изобретение парового двигателя дало толчок развитию человеческой деятельности во многих отраслях техники, в том числе и технике получения сжатого;
газа, т.к. паровой двигатель конструктивно аналогичен поршневому компрессору.
В России незначительное производство поршневых компрессоров началось в 1900г. Развитие компрессоростроения как отрасли получило во время первых пятилеток. В 1929г. в стране уже три завода выпускали компрессора, в том числе и холодильные. К концу первой пятилетки был освоен выпуск вертикальных бескрейцкопфных компрессоров, с частотой вращения коленчатого вала до 550 об/мин. Во второй и третьей пятилетках было освоено производство горизонтальных компрессоров двойного действия. В послевоенные годы осуществляется переход на повышенные скорости (до 760 - 920 об/мин), были улучшены в 2 - 4 раза массогабаритные показатели. С 1957г. начали выпускаться новые холодильные компрессоры - центробежные и ротационные.
В настоящее время в стране выпускаются практически все типы компрессоров для сжатия и транспортировки газов производительностью от 0,004 до!50м3/с и мощностью привода от нескольких десятых до десятков тысяч кВт.
Уровень создаваемых давлений составляет от 0,01 мПа (вентиляторы) до
350 мПа(компрессоры химических производств).
2. Дополнительная информация
• Добыча природного газа млрд. м³
1950 1960 1970 1975 1980 1985
5,8 45,3 200 320 600 800
• Мощность газопровода Крайний Север - Центр (диаметр трубопровода 2500 мм) составляет 3,5 млн. КВт
• Промышленность увеличивает спрос на кислородные компрессора. Производство кислорода составляет (млн. м3)
1970 1975 1980 1985
14,3 33,2 45,6 65
• Непрерывно возрастает потребность в компрессорах общего назначения (Р=0,8-1,0 мПа)
1970 1975 1980 1985
650 810 1000 1250
• Потребность в передвижных компрессорных станциях и тыс. КВт привода 1970 1975 1980 1985 540 750 1050 1400
• Следует отметить, что на машиностроительных заводах 20 -25% потребляемой эн<
Кормораздатчик мобильный электрифицированный: схема и процесс работы устройства...
Адаптации растений и животных к жизни в горах: Большое значение для жизни организмов в горах имеют степень расчленения, крутизна и экспозиционные различия склонов...
Индивидуальные очистные сооружения: К классу индивидуальных очистных сооружений относят сооружения, пропускная способность которых...
Поперечные профили набережных и береговой полосы: На городских территориях берегоукрепление проектируют с учетом технических и экономических требований, но особое значение придают эстетическим...
© cyberpedia.su 2017-2024 - Не является автором материалов. Исключительное право сохранено за автором текста.
Если вы не хотите, чтобы данный материал был у нас на сайте, перейдите по ссылке: Нарушение авторских прав. Мы поможем в написании вашей работы!