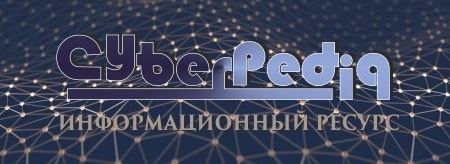
Поперечные профили набережных и береговой полосы: На городских территориях берегоукрепление проектируют с учетом технических и экономических требований, но особое значение придают эстетическим...
Индивидуальные и групповые автопоилки: для животных. Схемы и конструкции...
Топ:
Когда производится ограждение поезда, остановившегося на перегоне: Во всех случаях немедленно должно быть ограждено место препятствия для движения поездов на смежном пути двухпутного...
Оценка эффективности инструментов коммуникационной политики: Внешние коммуникации - обмен информацией между организацией и её внешней средой...
Теоретическая значимость работы: Описание теоретической значимости (ценности) результатов исследования должно присутствовать во введении...
Интересное:
Инженерная защита территорий, зданий и сооружений от опасных геологических процессов: Изучение оползневых явлений, оценка устойчивости склонов и проектирование противооползневых сооружений — актуальнейшие задачи, стоящие перед отечественными...
Финансовый рынок и его значение в управлении денежными потоками на современном этапе: любому предприятию для расширения производства и увеличения прибыли нужны...
Влияние предпринимательской среды на эффективное функционирование предприятия: Предпринимательская среда – это совокупность внешних и внутренних факторов, оказывающих влияние на функционирование фирмы...
Дисциплины:
![]() |
![]() |
5.00
из
|
Заказать работу |
|
|
Выбор режима резания для операции № - Токарная (точение d=10мм)
Глубина резания. Заданный припуск срезаем за один проход, t= 4 мм.
Назначение подачи. Для получения шероховатости Ra=6,3 мкм рекомендуют подачу S= мм/об, [6, табл. 37, стр. 285]; Принимаем S= мм/об.
Частота вращения шпинделя рассчитывается по формуле:
(24)
Корректируем число оборотов, по паспорту станка n = об/мин.
Пересчитываем V по принятому nв
(25)
Минутную подачу определяем по формуле:
Sм = S· n; (26)
Sм = 1,2 · = мм/мин;
Проверка по мощности станка.
Окружная сила резания при фрезеровании, Н:
, (27)
где Cp, q, w, x, y, n – коэффициенты, учитывающие нагрузки при фрезеровании, определяется по [6, табл. 41 стр. 291]:
Cp = 47, q = 0,86, w = 0, x = 0,86, y = 0,72, и = 0,1
(28)
где n - показатель степени n = 0,3 [6, табл. 9, стр. 264];
Н.
Мощность резания рассчитаем по формуле, кВт:
; (29)
кВт.
Мощность на шпинделе станка Nэ=Nд×η.
Nд=7,5 кВт; η=0,8 (по паспорту станка). Nэ=7,5×0,8=6 кВт.
Так как Nэ=6 кВт >N=0,03 кВт, то обработка возможна.
Основное (машинное) время определяем по формуле:
, (30)
где l – длина обрабатываемой поверхности, l =29,7 мм;
l1 – длина врезания l1 = 4 мм по [4];
l2 – длина на взятие пробной стружки, l2 = мм.
t0=
Таблица 10 – Сводная таблица режимов резания
№ оп. |
Наименование операции
|
Режимы резания | |||||||
D, мм | L, мм | t, мм | S, мм/об | V, м/мин | n, об/мин | to, мин | |||
010 | Токарная: черновая | 35 | 17,5 | 1 | 0,1 | 55 | 500 | 0,43 | |
20,5 | 95 | 4 | 0,35 | 40,5 | 630 | 0,9 | |||
ΣТ010 | = 0,43 + 0,9 = 1,33 мин. | ||||||||
015 | Фрезерная: Фрез. торца Фрез. контура | 36 | 35 | 1 | 0,2 | 88 | 800 | 0,37 | |
36 | 30 | 6 | 0,2 | 88 | 800 | 1,35 | |||
ΣТ010 | = 0,37 + 1,35 = 1,72 мин. | ||||||||
020 | Фрезерная | 63 | 10 | 10 | 1,2 | 12,5 | 63 | 0,45 | |
025 | Фрезерная | 10 | 34 | 1 | 0,2 | 15,7 | 500 | 2,12 | |
030 | Сверлильная | 16,2 | 22 | 8,1 | 0,24 | 40,7 | 800 | 0,2 | |
035 | Токарная: Чистовая Нарез. резьбы Точ. фаску | 20,157 | 95 | 0,17 | 0,25 | 50,6 | 800 | 0,49 | |
М20 | 65 | 0,08 | Шаг резьбы 2,5 мм | 25,1 | 400 | 0,65 | |||
20 | 2,5 | 2,5 | 0,12 | 39,6 | 630 | 0,07 | |||
ΣТ010 | = 0,49 + 0,65 + 0,07 = 1,21 мин. |
Расчет норм времени
Расчет норм времени выполняем для операции №010 - токарная
Для обработки d=10 мм время рассчитывается по формуле:
(31)
где tшт – штучное время, мин;
tп-з – подготовительно-заключительное время, мин;
п – количество деталей в партии, шт.
Штучное время определяем по формуле
tшт= tо + tвсп + tдоп (32)
где tвсп – вспомогательное время при обработке, мин;
tдоп – дополнительное время на обработку,мин.
Вспомогательное время при обработке будет состоять из нескольких компонентов.
tвсп = tуст + tупр + tконтр + tп.пер (33)
где tутс – время на установку и снятие детали, tуст = 0,19 мин.[7, стр.138 карта 51]
tупр. = 0,41 мин – вспомогательное время на приемы управления станком
tконтр = tконтр. н · К · і (34)
где tконтр – нормативное время на контроль, tконтр = 0,16 мин[7, стр.161 карта 64].
К = 0,3 – коэффициент периодичности проверки;
і = 2 – количество измерений.
tконтр = 0,16 · 0,3 · 2 = 0,10 мин.
Время связанное с переходом: tп.пер = 0,76 мин.[7, стр.150 карта 60].
tвсп = 0,19 + 0,41 + 0,10 + 0,76 = 1,46 мин
Определяем оперативное время по формуле:
tоп = tо + tвсп (35)
|
tоп = 1,33 + 1,46 = 2,79 мин.
Дополнительное время определяем по формуле:
αдод = (αтех + αорг + αотд) · tоп (36)
где αтех = 1,2 мин [7, стр.136, карта 49]
αорг =2% от tоп =0,06; αотд=4 % от tоп =0,11 мин
αдод = (1,2 + 0,06 + 0,11) · 2,79 = 3,82 мин.
tшт= 1,33 + 1,46 + 3,82 = 6,61 мин.
Подготовительно-заключительное время необходимо для настройки станка на обработку партии заготовок.
tнал = 14 мин. – нормативное время на настройку станка, инструмента и приспособления;
t = 2 мин. – нормативное время на дополнительные приемы;
t = 7 мин. – норматив времени на получение инструментов и приспособления до начала и сдача после окончания обработки;
п = 40 шт.
tп-з = 14 + 2 + 7 = 23 мин.
= 7,18 мин.
Таблица 11 – Результаты технического нормирования
№ оп. | Наименование операции | Модель станка | tо, мин | tв, мин | tоп, мин | tшт, мин | tп-з, мин | tшт-к, мин |
010 | Токарная | 16К20 | 1,33 | 1,46 | 2,79 | 6,61 | 23 | 7,18 |
015 | Фрезерная | 6Р12 | 1,72 | 0,57 | 2,29 | 4,35 | 20 | 4,85 |
020 | Фрезерная | 6Р82 | 0,45 | 0,85 | 1,3 | 2,86 | 20 | 3,36 |
025 | Фрезерная | 6Р12 | 2,12 | 0,57 | 2,69 | 6,19 | 20 | 6,69 |
030 | Сверлильная | 2Н135 | 0,2 | 1,35 | 1,55 | 2,94 | 17 | 3,36 |
035 | Токарная | 16К20 | 1,21 | 1,46 | 2,67 | 6,14 | 23 | 6,71 |
7. Окончательное оформление технологического процесса
По произведенным расчетам выполняем окончательное оформление технологического процесса, заполнения ОК.
Расчет режущего инструмента
Согласно технологической части проекта и таблице 8 все механические операции техпроцесса можно выполнять стандартизованным режущим
инструментом. Рассчитываем токарный сборный резец оснащенный сменной пластиной из твердого сплава Т15К6.
Данный резец представляет собой призматический стержень с
закрепленной на нем пластинкой из твердого сплава.
Конструкция узла крепления многогранной пластинки во многом определяет работоспособность резцов. Для обеспечения необходимой нам надежности закрепления используем крепление пластинки плоским клином.
Рисунок 3 – Схема крепления
В державку 1 запрессовывают штифт 4. Штифт имеет бочкообразную форму верхней части и насеченную нижнюю часть, что повышает надежность закрепления пластины и снижает требование к точности изготовления отверстия в державке под запрессовку штифта. Сменная подкладка 2 из твердого сплава имеет коническое отверстие, получаемое при прессовании подкладки. Закрепляют ее в гнезде державки штифтом 4, для чего последний имеет конический участок головки. Многогранную пластину 3 из твердого сплава крепят расклиниванием ее между штифтом и задней опорной стенкой державки клином 5 и винтом 6.
|
Пластина имеет выкружки вдоль всех режущих кромок, получаемых при прессовании пластины. Это обеспечивает положительное значение переднего угла при резании, удовлетворительное завивание и удачный отвод стружки.
Принимаем γ = 15°, α = 8° и α1 = 8°.
При конструировании твердосплавных резцов необходимо правильно
расположить пластину на корпусе, для этого производим необходимый расчет параметров расположения паза под пластину.
В соответствии с заданными условиями обработки выбираем форму
многогранной пластины.
При черновой и чистовой обработке с равномерным припуском, а также в качестве подрезного применяем проходной упорный резец с трехгранной пластиной с главным углом в плане φ = 93° и вспомогательным углом в плане φ1 = 10°.
Определяем расчетное число граней пластины по формуле:
(37)
Так как расчетное число граней получилось дробным, округляем его до целого. Принимаем n = 3. При этом сохраняем заданное значение главного угла в плане, а фактическое значение вспомогательного угла в плане определяем расчетом:
(38)
= 27°
В резце с многогранными пластинками нельзя задавать независимо друг от друга все шесть основных геометрических параметров режущей части как в цельных резцах, так как они связаны как с формой пластинки, так и между собой.
Рисунок 4 – Схема расположения опорной поверхности пластины на
державке резца
После выбора числа граней пластинки определяют угол поворота μопорной плоскости пластинки относительно основной плоскости резца, а также положение оси поворота Т – Т относительно главной режущей кромки резца (угол 90° - β). Значение этих параметров находят по приближенным формулам:
|
(39)
, (40)
где ε – угол при вершине многогранной пластины.
(41)
= 60°
= 0,5774; β = 30°
; μ = 15°
Угол наклона главной режущей кромки определяют по формуле:
tgλ = tgα · сtgβ (42)
tgλ = tg8° · сtg30° = 0,2435; tgλ = 13°
Установку державок на станке производят в трехповоротных тисках. Для настройки тисков необходимо определить углы поворота их отдельных частей вокруг соответствующих осей, после настройки, на которые опорная плоскость гнезда под пластинку займет требуемое положение.
Для этой цели опорную плоскость гнезда под пластинку задают двумя прямыми, расположенными в поперечном сечении корпуса под углом ω2 и в продольном сечении под углом ω1. Углы ω1 и ω2 определяют по формулам:
(43)
(44)
= 0,1328; ω1 = 7°34΄
= 0,1514; ω2 = 8°36΄
После обработки опорной поверхности державку устанавливают в обойме и на ней закрепляют многогранную пластинку.Ориентацию пластинки в державке производят по главному углу в плане φ.
Конструктивные размеры резца.
Для заданных режимов резания определяем сечение срезаемого слоя f = t · S = 3 · 0,35 = 1,05 мм2. Пользуясь таблицей, находим, что для станка 16К20 при площади сечения срезаемого слоя f=1,05 мм2 резец должен иметь рабочую высоту h = 16 мм и диаметр описанной окружности D = 18 мм.
Основные размеры резца принимаем по ГОСТ 20872-80. Рабочая высота резца h = 16 мм, ширина корпуса резца b = 16 мм, высота корпуса резца h1 = 19 мм, длина резца L = 125 мм.
|
|
Опора деревянной одностоечной и способы укрепление угловых опор: Опоры ВЛ - конструкции, предназначенные для поддерживания проводов на необходимой высоте над землей, водой...
Таксономические единицы (категории) растений: Каждая система классификации состоит из определённых соподчиненных друг другу...
Особенности сооружения опор в сложных условиях: Сооружение ВЛ в районах с суровыми климатическими и тяжелыми геологическими условиями...
Двойное оплодотворение у цветковых растений: Оплодотворение - это процесс слияния мужской и женской половых клеток с образованием зиготы...
© cyberpedia.su 2017-2024 - Не является автором материалов. Исключительное право сохранено за автором текста.
Если вы не хотите, чтобы данный материал был у нас на сайте, перейдите по ссылке: Нарушение авторских прав. Мы поможем в написании вашей работы!