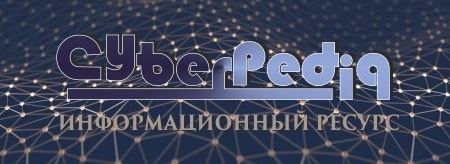
Эмиссия газов от очистных сооружений канализации: В последние годы внимание мирового сообщества сосредоточено на экологических проблемах...
Автоматическое растормаживание колес: Тормозные устройства колес предназначены для уменьшения длины пробега и улучшения маневрирования ВС при...
Топ:
Генеалогическое древо Султанов Османской империи: Османские правители, вначале, будучи еще бейлербеями Анатолии, женились на дочерях византийских императоров...
Марксистская теория происхождения государства: По мнению Маркса и Энгельса, в основе развития общества, происходящих в нем изменений лежит...
Комплексной системы оценки состояния охраны труда на производственном объекте (КСОТ-П): Цели и задачи Комплексной системы оценки состояния охраны труда и определению факторов рисков по охране труда...
Интересное:
Отражение на счетах бухгалтерского учета процесса приобретения: Процесс заготовления представляет систему экономических событий, включающих приобретение организацией у поставщиков сырья...
Наиболее распространенные виды рака: Раковая опухоль — это самостоятельное новообразование, которое может возникнуть и от повышенного давления...
Уполаживание и террасирование склонов: Если глубина оврага более 5 м необходимо устройство берм. Варианты использования оврагов для градостроительных целей...
Дисциплины:
![]() |
![]() |
5.00
из
|
Заказать работу |
|
|
Гранулирование
Гранулирование – это совокупность физических и физико-химических процессов, обеспечивающих формирование частиц определенного спектра размеров, формы, необходимой структуры и физических свойств.
Гранулирование – процесс превращения порошкообразного материала в частицы (зерна) определенной величины.
Гранулирование позволяет предотвратить расслаивание многокомпонентных таблетируемых масс, улучшить сыпучесть порошков, обеспечить их равномерную скорость поступления в матрицу таблетного пресса, точность дозирования и равномерное распределение активного компонента, а следовательно, большую гарантию лечебных свойств каждой таблетки. Задача гранулирования состоит в обеспечении тесного сближения частиц порошкообразного материала и формирования из них однородных и прочных гранул определённого размера.
Методы гранулирования:
1) Сухое гранулирование (брикетирование)
2) Влажное гранулирование
· гранулирование путем продавливания через фильеру(экструзия)
· гранулирование методом окатывания
· виброгранулирование
· структурноегранулирование в псевдоожиженном слое
3) Другие методы гранулирования
· гранулирование плавлением
· гранулирование распылительной сушкой
· топогрануляция
- прессование сухих порошков (получение брикетов, плиток и т.п. с последующим дроблением их на гранулы требуемого размера);
- формование или экструзия (продавливание вязкой жидкости или пастообразной массы через отверстие);
- формирование гранул в процессе их агрегации или послойного роста с последующим уплотнением структуры (окатывание);
- диспергирование жидкости в свободный объем или нейтральную среду (образование или отвердевание капель жидкости при охлаждении капель в газе или жидкости);
- диспергирование жидкости на поверхность гранул, находящихся во взвешенном состоянии (кристаллизация тонких пленок в результате их обезвоживания или охлаждения на поверхности гранул)
|
В общем случае гранулирование включает следующие технологические стадии переработки:
подготовку исходного сырья, дозирование, смешение компонентов
собственно гранулообразование (агломерация, наслаивание, кристаллизация, уплотнение, и др.)
стабилизацию структуры (упрочнение связей между частицами сушкой, охлаждением, полимеризацией и др.)
выделение товарной фракции (классификация по размерам.дробление крупных частиц)
Используемый метод гранулирования определяется свойствами гранулируемых веществ и субстанций. Так, для гранулирования пластично-вязких порошковидных и пастообразных материалов более пригодны методы формирования и экструдирования, для пластично-невязких порошковидных веществ можно рекомендовать непрерывное или периодическое прессование, для гранулирования суспензионных растворов предпочтение следует отдавать методам распыливания этих растворов на поверхность частиц, составляющих вращающийся, взвешенный или псевдоожиженный слой, с одновременной сушкой продукта до требуемой влажности.
Гранулирование безводных расплавов целесообразнее осуществлять разбрызгиванием и охлаждением их в грануляционных башнях (для расплавов с малым содержанием твердой взвеси) или распыливанием на поверхность частиц динамического слоя с одновременным охлаждением гранул.
Эффективность процесса гранулирования зависит от механизма гранулообразования, который, в свою очередь, определяется способом гранулирования и его аппаратурным оформлением.
Сухое гранулирование (брикетирование)
Гранулирование сухих порошков методом прессования, т.е. уплотнения под действием внешних сил, основано на формировании плотной структуры вещества, что обусловлено возникновением прочных когезионных связей между частицами при их сжатии. Полученный в результате уплотненный брикет (плитка) дробят и направляют на рассев для отбора кондиционной фракции гранул, являющихся готовым продуктом.
|
Сухое гранулирование является достаточно распространенным методом получения гранул благодаря тому, что исключается необходимость контакта влаги с материалом, отсутствует стадия сушки гранулята. Метод незаменим в технологии препаратов с использованием термолабильных и гигроскопичных субстанций.
Смешение компонентов
Получение однородной по составу таблетной смеси является очень важной и довольно сложной технологической операцией, в связи с тем, что порошки обладают различными физико-химическими свойствами: дисперсностью, насыпной плотностью, влажностью, сыпучестью и др. Качественное смешение обеспечивает точность и однородность дозирования лекарственного вещества в таблетках.
V -образный смесительфирмы DGM PharmaApparate
Сухое гранулирование
Влажное гранулирование
Влажная масса гранулируется на специальных машинах – грануляторах, принцип работы которых состоит в том, что материал протирается лопастями, пружинящими валиками или другими приспособлениями через перфорированный цилиндр или сетку. Выбор сит для гранулирования имеет очень большое значение. Установлено, что влажную массу необходимо пропускать через сито с диаметром отверстий 3 –5 мм.
Гранулирование методом формования или экструзии
Используется для порошков, имеющие плохую сыпучесть и недостаточную способность к сцеплению между частицами. Влажное гранулирование проводят в 2 этапа. Первичная грануляция – вещества тщательно смешивают, увлажняют соответствующими связывающими веществами до получения влажной массы, перемешивание смоченных порошков сопровождается некоторым уплотнением массы, что позволяет получать более плотные твердые гранулы. Время перемешивания влажной массы для простых смесей 7 - 10 минут, для сложных – 15-20 минут.
Необходимое количество связывающих веществ устанавливают опытным путем для каждой таблетируемой массы. Увлажнитель в смесь сухих порошков добавляют небольшими порциями для предотвращения комкования. Оптимальное количество увлажнителя определяется экспериментально: если увлажнителя ввести мало – гранулы после сушки будут рассыпаться, если много – масса будет вязкой, липкой и плохо гранулируемой. Масса с оптимальной влажностью представляет собой влажную, плотную смесь, не прилипающую к руке, но рассыпающуюся при сдавливании на отдельные комочки.
|
Недостатки метода:
длительное, иногда неблагоприятное воздействие гранулирующей жидкости и температуры сушки на гранулят;
требует введение значительного количества вспомогательных веществ;
образование пыли при сухой грануляции с загрязнением воздуха и потери массы;
неоднородность гранул;
недостаточная механическая прочность гранул;
периодичность цикла не позволяет сделать процесс непрерывным.
Гранулятор для влажного гранулирования
Гранулирование методом окатывания
Гранулирование методом окатывания состоит в предварительном образовании агрегатов из равномерно смоченных частиц или в наслаивании сухих частиц на смоченные ядра – центры гранулообразования. Этот процесс обусловлен действием капиллярно-адсорбционных сил сцепления между частицами и последующим уплотнением структуры, вызванным силами взаимодействия между частицами в плотном динамическом слое, например, в грануляторах барабанного или тарельчатого типов.
Гранулирование в аппаратах барабанного и тарельчатого типов осуществляется в присутствии жидкой фазы, которая вносится с твердыми компонентами или специально вводится в виде растворов и расплавов.
High Sear Granulating
1-загрузочнаяворонка
2-аппарат
3-рубашка
4-пневмотическая форсунка
5-выгрузка гранултяа
6-нижня мешалка
7-верхняя мешалка
8-измельчитель(чоппер)
9-воздушный фильтр
Структурное гранулирование в псевдоожиженном слое
Гранулирование во взвешенном слое можно отнести к влажному гранулированию, но, в свою очередь, он является наиболее технически совершенным и перспективным, т.к. позволяет совместить все операции в одном аппарате и организовать непрерывное производство с высокой производительностью при одновременном улучшении санитарно-гигиенических условий производства и качества продукта. Основные процессы: смешивание компонентов, увлажнение смеси гранулирующей жидкостью, гранулирование, сушка и опудривание гранулята – протекают в одном аппарате
|
Псевдоожиженный слой представляет собой гетерогенную систему газ-твердое, в которой твердые частицы ведут себя как жидкость.
Достоинства:
1) большая поверхность контакта фаз - поверхность каждой частицы омывается потоком газа;
2) высокая интенсивность тепло-массообмена;
3) хорошее перемешивание материала;
Недостатки:
1) высокое гидравлическое сопротивление системы и существенные энергозатраты на псевдоожижение
Псевдоожиженный слой характеризуется
гидравлическим сопротивлением;
порозностью
Схема аппарата псевдоожиженного слоя
Гидравлическое сопротивление слоя:
Порозность слоя:
- объём слоя
- объём частиц
- для неподвижного слоя шарообразных частиц;
– для псевдоожиженного слоя
- для уноса частиц
Схема режимов псевдоожижения:
Аппараты для гранулирования в ПС:
Аппарат СГ- 30
1 – тележка;
2– пневмоцилиндр подъема продуктового резервуара;
3 – продуктовый резервуар;
4 – обечайка распылителя;
5 – обечайка рукавных фильтров;
6 – встряхивающее устройство;
7 – предохранительный клапан;
8 – вентилятор;
9 – шибер;
10 – механизм управления заслонкой;
11 – корпус;
12 – фильтр воздушный;
13 – насос дозирующий;
14 – емкость для гранулирующей жидкости;
15 – распыливающийся сжатый воздух;
16 – паровой калорифер.
Система распределения газов
Виды газораспределительных решеток
PZ sieve fabric Conidur bottom wedge-wire bottom
Схемы фильтров:
Способы выгрузки из аппарата с воздушной сепарацией:
Гранулирование
Гранулирование – это совокупность физических и физико-химических процессов, обеспечивающих формирование частиц определенного спектра размеров, формы, необходимой структуры и физических свойств.
Гранулирование – процесс превращения порошкообразного материала в частицы (зерна) определенной величины.
Гранулирование позволяет предотвратить расслаивание многокомпонентных таблетируемых масс, улучшить сыпучесть порошков, обеспечить их равномерную скорость поступления в матрицу таблетного пресса, точность дозирования и равномерное распределение активного компонента, а следовательно, большую гарантию лечебных свойств каждой таблетки. Задача гранулирования состоит в обеспечении тесного сближения частиц порошкообразного материала и формирования из них однородных и прочных гранул определённого размера.
Методы гранулирования:
1) Сухое гранулирование (брикетирование)
|
2) Влажное гранулирование
· гранулирование путем продавливания через фильеру(экструзия)
· гранулирование методом окатывания
· виброгранулирование
· структурноегранулирование в псевдоожиженном слое
3) Другие методы гранулирования
· гранулирование плавлением
· гранулирование распылительной сушкой
· топогрануляция
- прессование сухих порошков (получение брикетов, плиток и т.п. с последующим дроблением их на гранулы требуемого размера);
- формование или экструзия (продавливание вязкой жидкости или пастообразной массы через отверстие);
- формирование гранул в процессе их агрегации или послойного роста с последующим уплотнением структуры (окатывание);
- диспергирование жидкости в свободный объем или нейтральную среду (образование или отвердевание капель жидкости при охлаждении капель в газе или жидкости);
- диспергирование жидкости на поверхность гранул, находящихся во взвешенном состоянии (кристаллизация тонких пленок в результате их обезвоживания или охлаждения на поверхности гранул)
В общем случае гранулирование включает следующие технологические стадии переработки:
подготовку исходного сырья, дозирование, смешение компонентов
собственно гранулообразование (агломерация, наслаивание, кристаллизация, уплотнение, и др.)
стабилизацию структуры (упрочнение связей между частицами сушкой, охлаждением, полимеризацией и др.)
выделение товарной фракции (классификация по размерам.дробление крупных частиц)
Используемый метод гранулирования определяется свойствами гранулируемых веществ и субстанций. Так, для гранулирования пластично-вязких порошковидных и пастообразных материалов более пригодны методы формирования и экструдирования, для пластично-невязких порошковидных веществ можно рекомендовать непрерывное или периодическое прессование, для гранулирования суспензионных растворов предпочтение следует отдавать методам распыливания этих растворов на поверхность частиц, составляющих вращающийся, взвешенный или псевдоожиженный слой, с одновременной сушкой продукта до требуемой влажности.
Гранулирование безводных расплавов целесообразнее осуществлять разбрызгиванием и охлаждением их в грануляционных башнях (для расплавов с малым содержанием твердой взвеси) или распыливанием на поверхность частиц динамического слоя с одновременным охлаждением гранул.
Эффективность процесса гранулирования зависит от механизма гранулообразования, который, в свою очередь, определяется способом гранулирования и его аппаратурным оформлением.
Сухое гранулирование (брикетирование)
Гранулирование сухих порошков методом прессования, т.е. уплотнения под действием внешних сил, основано на формировании плотной структуры вещества, что обусловлено возникновением прочных когезионных связей между частицами при их сжатии. Полученный в результате уплотненный брикет (плитка) дробят и направляют на рассев для отбора кондиционной фракции гранул, являющихся готовым продуктом.
Сухое гранулирование является достаточно распространенным методом получения гранул благодаря тому, что исключается необходимость контакта влаги с материалом, отсутствует стадия сушки гранулята. Метод незаменим в технологии препаратов с использованием термолабильных и гигроскопичных субстанций.
Смешение компонентов
Получение однородной по составу таблетной смеси является очень важной и довольно сложной технологической операцией, в связи с тем, что порошки обладают различными физико-химическими свойствами: дисперсностью, насыпной плотностью, влажностью, сыпучестью и др. Качественное смешение обеспечивает точность и однородность дозирования лекарственного вещества в таблетках.
V -образный смесительфирмы DGM PharmaApparate
Сухое гранулирование
Влажное гранулирование
Влажная масса гранулируется на специальных машинах – грануляторах, принцип работы которых состоит в том, что материал протирается лопастями, пружинящими валиками или другими приспособлениями через перфорированный цилиндр или сетку. Выбор сит для гранулирования имеет очень большое значение. Установлено, что влажную массу необходимо пропускать через сито с диаметром отверстий 3 –5 мм.
Гранулирование методом формования или экструзии
Используется для порошков, имеющие плохую сыпучесть и недостаточную способность к сцеплению между частицами. Влажное гранулирование проводят в 2 этапа. Первичная грануляция – вещества тщательно смешивают, увлажняют соответствующими связывающими веществами до получения влажной массы, перемешивание смоченных порошков сопровождается некоторым уплотнением массы, что позволяет получать более плотные твердые гранулы. Время перемешивания влажной массы для простых смесей 7 - 10 минут, для сложных – 15-20 минут.
Необходимое количество связывающих веществ устанавливают опытным путем для каждой таблетируемой массы. Увлажнитель в смесь сухих порошков добавляют небольшими порциями для предотвращения комкования. Оптимальное количество увлажнителя определяется экспериментально: если увлажнителя ввести мало – гранулы после сушки будут рассыпаться, если много – масса будет вязкой, липкой и плохо гранулируемой. Масса с оптимальной влажностью представляет собой влажную, плотную смесь, не прилипающую к руке, но рассыпающуюся при сдавливании на отдельные комочки.
Недостатки метода:
длительное, иногда неблагоприятное воздействие гранулирующей жидкости и температуры сушки на гранулят;
требует введение значительного количества вспомогательных веществ;
образование пыли при сухой грануляции с загрязнением воздуха и потери массы;
неоднородность гранул;
недостаточная механическая прочность гранул;
периодичность цикла не позволяет сделать процесс непрерывным.
Гранулятор для влажного гранулирования
Гранулирование методом окатывания
Гранулирование методом окатывания состоит в предварительном образовании агрегатов из равномерно смоченных частиц или в наслаивании сухих частиц на смоченные ядра – центры гранулообразования. Этот процесс обусловлен действием капиллярно-адсорбционных сил сцепления между частицами и последующим уплотнением структуры, вызванным силами взаимодействия между частицами в плотном динамическом слое, например, в грануляторах барабанного или тарельчатого типов.
Гранулирование в аппаратах барабанного и тарельчатого типов осуществляется в присутствии жидкой фазы, которая вносится с твердыми компонентами или специально вводится в виде растворов и расплавов.
High Sear Granulating
1-загрузочнаяворонка
2-аппарат
3-рубашка
4-пневмотическая форсунка
5-выгрузка гранултяа
6-нижня мешалка
7-верхняя мешалка
8-измельчитель(чоппер)
9-воздушный фильтр
Структурное гранулирование в псевдоожиженном слое
Гранулирование во взвешенном слое можно отнести к влажному гранулированию, но, в свою очередь, он является наиболее технически совершенным и перспективным, т.к. позволяет совместить все операции в одном аппарате и организовать непрерывное производство с высокой производительностью при одновременном улучшении санитарно-гигиенических условий производства и качества продукта. Основные процессы: смешивание компонентов, увлажнение смеси гранулирующей жидкостью, гранулирование, сушка и опудривание гранулята – протекают в одном аппарате
Псевдоожиженный слой представляет собой гетерогенную систему газ-твердое, в которой твердые частицы ведут себя как жидкость.
Достоинства:
1) большая поверхность контакта фаз - поверхность каждой частицы омывается потоком газа;
2) высокая интенсивность тепло-массообмена;
3) хорошее перемешивание материала;
Недостатки:
1) высокое гидравлическое сопротивление системы и существенные энергозатраты на псевдоожижение
Псевдоожиженный слой характеризуется
гидравлическим сопротивлением;
порозностью
Схема аппарата псевдоожиженного слоя
Гидравлическое сопротивление слоя:
Порозность слоя:
- объём слоя
- объём частиц
- для неподвижного слоя шарообразных частиц;
– для псевдоожиженного слоя
- для уноса частиц
Схема режимов псевдоожижения:
Аппараты для гранулирования в ПС:
Аппарат СГ- 30
1 – тележка;
2– пневмоцилиндр подъема продуктового резервуара;
3 – продуктовый резервуар;
4 – обечайка распылителя;
5 – обечайка рукавных фильтров;
6 – встряхивающее устройство;
7 – предохранительный клапан;
8 – вентилятор;
9 – шибер;
10 – механизм управления заслонкой;
11 – корпус;
12 – фильтр воздушный;
13 – насос дозирующий;
14 – емкость для гранулирующей жидкости;
15 – распыливающийся сжатый воздух;
16 – паровой калорифер.
Аппарат с хаотичным движением потока частиц
Отработанный воздух
|
|
|
Воздух
|
|
Типы оградительных сооружений в морском порту: По расположению оградительных сооружений в плане различают волноломы, обе оконечности...
Таксономические единицы (категории) растений: Каждая система классификации состоит из определённых соподчиненных друг другу...
Кормораздатчик мобильный электрифицированный: схема и процесс работы устройства...
Своеобразие русской архитектуры: Основной материал – дерево – быстрота постройки, но недолговечность и необходимость деления...
© cyberpedia.su 2017-2024 - Не является автором материалов. Исключительное право сохранено за автором текста.
Если вы не хотите, чтобы данный материал был у нас на сайте, перейдите по ссылке: Нарушение авторских прав. Мы поможем в написании вашей работы!