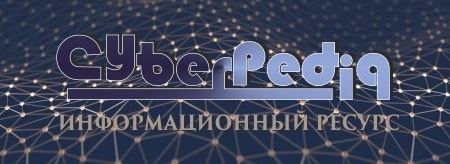
Автоматическое растормаживание колес: Тормозные устройства колес предназначены для уменьшения длины пробега и улучшения маневрирования ВС при...
История развития хранилищ для нефти: Первые склады нефти появились в XVII веке. Они представляли собой землянные ямы-амбара глубиной 4…5 м...
Топ:
Когда производится ограждение поезда, остановившегося на перегоне: Во всех случаях немедленно должно быть ограждено место препятствия для движения поездов на смежном пути двухпутного...
Установка замедленного коксования: Чем выше температура и ниже давление, тем место разрыва углеродной цепи всё больше смещается к её концу и значительно возрастает...
Интересное:
Берегоукрепление оползневых склонов: На прибрежных склонах основной причиной развития оползневых процессов является подмыв водами рек естественных склонов...
Лечение прогрессирующих форм рака: Одним из наиболее важных достижений экспериментальной химиотерапии опухолей, начатой в 60-х и реализованной в 70-х годах, является...
Влияние предпринимательской среды на эффективное функционирование предприятия: Предпринимательская среда – это совокупность внешних и внутренних факторов, оказывающих влияние на функционирование фирмы...
Дисциплины:
![]() |
![]() |
5.00
из
|
Заказать работу |
|
|
Для того, чтобы подшипник не изнашивался, цапфа должна плавать на смазочном слое, толщина которого должна быть больше неровностей на поверхности цапфы (шейки) и вкладыша (рис. 8, а).
Рис. 8. Схема работы подшипника скольжения
Это условие выполнимо при достаточной подаче масла и такой окружной скорости цапфы, которая достаточна для развития подъемной силы в смазочном слое (условие жидкостного трения).
При малых скоростях или при недостаточной подаче смазки условия жидкостного трения не обеспечиваются, возникает граничное трение и опасность истирания сопряженных поверхностей цапфы и вкладыша; величина истирания зависит в значительной степени от шероховатости этих поверхностей, а также от «аварийных свойств» материала подшипника.
Таким образом, для работы подшипников скольжения самым благоприятным является режим, при котором осуществляется жидкостная смазка.
Различают гидродинамическую и гидростатическую жидкостные смазки. В первом случае жидкостная смазка осуществляется в результате давления, возникающего в слое жидкости при относительном движении поверхностей трения, а во втором случае – за счет поступления жидкости в зазор между поверхностями трения под внешним давлением (например, создаваемым шестеренным насосом). Тем самым устраняется непосредственный контакт между поверхностями скольжения, что приводит к резкому снижению трения и износа. Они применяются при высоких окружных скоростях (до 150 м/сек) и при точных перемещениях.
В неработающей машине, когда угловая скорость вала равна нулю, его цапфа занимает положение в подшипнике, как это показано на рис. 8, б.
Зазор в подшипнике полностью заполнен смазочным материалом.
|
При пуске машины, по мере возрастания угловой скорости вала, вращающаяся цапфа увлекает за собой смазочный материал и всплывает, а ее центр смещается в сторону вращения относительно центра вкладыша (рис. 8, в). Образовавшийся клиновой зазор непрерывно заполняется смазочным материалом, увлекаемым вращающейся цапфой, вследствие чего и образуется гидродинамическая подъемная сила. При дальнейшем возрастании угловой скорости и соблюдении рассмотренных ниже условий появляется сплошной устойчивый гидродинамический клин, полностью разделяющий поверхности трения. Толщина слоя смазочного материала h зависит от характеристики рабочего режима подшипника и толщина слоя смазочного материала возрастает с увеличением вязкости и угловой скорости цапфы. С увеличением нагрузки толщина слоя смазочного материала уменьшается.
Величина зазора в подшипнике влияет на несущую способность смазочного слоя, а тем самым и на «грузоподъемность» подшипника, которая тем больше, чем меньше этот зазор. Поэтому чем больше среднее удельное давление в подшипнике и чем меньше скорость цапфы, тем меньшим принимается зазор в подшипнике. Напротив, при малых давлениях и больших скоростях нужно принимать больший зазор в подшипнике (его величина зависит и от вязкости масла), поскольку в подшипнике с малым зазором цапфа работает в неустойчивом режиме, происходит чрезмерный нагрев, а в худшем случае – истирание ненагруженной части подшипника.
Зазор в подшипнике обычно принимается по зависимости:
Меньшие значения берут при малых окружных скоростях и больших нагрузках, а большие – при больших скоростях и меньших нагрузках.
Для определения величины зазора можно пользоваться также зависимостью:
где dвк–dц – диаметральный зазор между вкладышем и цапфой, d – номинальный диаметр подшипника: δ=0,002 ÷ 0,003 – при жидкостном трении; δ=0,01 ÷ 0,02 – при его отсутствии.
Если поле допуска отверстия подшипника по Н7 (Н8), то при малых скоростях цапфа вала выполняется по g6, f6, при средних скоростях – e8, d9, f8, при высоких скоростях – d10. Для обычных условий работы опор можно рекомендовать зазоры в подшипнике, указанные в табл. 1 (с учетом рабочей температуры).
|
Таблица 1. Зазоры в радиальных подшипниках качения
Подводить масло необходимо в ненагруженную часть подшипника, лучше всего – под углом 90° перед зоной максимального нагружения так, чтобы масло могло проникнуть в нагруженную зону возможно быстрее, не успев чрезмерно нагреться, и с требуемым давлением (рис. 9, а). Если вал должен вращаться в обоих направлениях, то масло следует подводить в точке, лежащей против точки приложения равнодействующей нагрузки (рис. 9; б, в).
Рис. 9. Места подвода смазки в подшипник скольжения
Смазочные канавки должны распределять масло в подшипнике так, чтобы это способствовало нагнетательному действию цапфы. При жидкостном трении достаточно разводить масло вдоль вкладыша. Канавки не должны доходить до торцов подшипника, иначе масло будет вытекать (рис. 10, а). Сечение канавок должно суживаться в направлении всасывания цапфы (рис. 10, б); они также не должны быть слишком глубокими.
Не рекомендуется делать поперечные канавки в нагруженной части вкладыша – это ведет к уменьшению «грузоподъемности» (подъемной силы) смазочного слоя подшипника скольжения. При больших скоростях и очень малых давлениях иногда применяют радиальные (круговые) канавки (рис. 9, а) в подшипнике скольжения с целью улучшения отвода тепла из подшипников.
Рис. 10. Смазочные канавки в подшипниках скольжения
В нагруженной части подшипника продольные смазочные канавки делают только при очень малых (близких к нулю) скоростях, когда жидкостное трение недостижимо, и масло иначе не попадет под действием цапфы в нагруженные места (например, у цапф качающихся, совершающих возвратно-вращательное движение). По возможности, особенно при большой скорости и большой удельной нагрузке подшипника, следует отказаться от смазочных канавок.
Длина подшипника также влияет на его грузоподъемность (несущую способность). Из очень коротких подшипников вытекает много масла, и в результате этого уменьшается грузоподъемность смазочного слоя. У длинных подшипников прогиб вала влияет очень неблагоприятно на распределение давления.
|
Подшипники имеют наилучшую грузоподъемность при отношении длины к диаметру:
l/d=0,4 ÷ 0,7.
Ввиду большой утечки масла через торцовые зазоры это соотношение принимают лишь для механизмов с циркуляционной смазкой.
Подшипники с индивидуальной смазкой могут быть более длинными:
l/d=1,0
(в исключительных случаях l/d=1,5).
Остальные размеры выбирают по следующим зависимостям:
Н=(1,1 ÷ 1,3)S+5 мм; k ≈ 0,5H; h=1 ÷ 5 мм; S ≈ 5 мм при d=35 ÷ 60 мм; S ≈ 7,5 мм при d=65 ÷ 100 мм; S ≈ 10 мм при d=120 ÷ 200 мм.
Толщину вкладыша S в зависимости от материала рекомендуют определять по следующим эмпирическим зависимостям: для стальных вкладышей толщина S=(0,03 ÷ 0,05)d, для бронзовых – S=(0,04 ÷ 0,08)d, для чугунных – S=(0,08 ÷ 0,15)d, для пластмассовых – S=(0,07 ÷ 0,30)d. Меньшие значения коэффициентов относятся к большим значениям d цапфы.
Качество обработки рабочих поверхностей цапфы и вкладыша влияет на грузоподъемность и износ подшипника при малых окружных скоростях цапфы и при частых пусках и остановах машин. Шероховатость поверхности цапфы должна составлять 1..3 мкм в зависимости от диаметра, твердость должна быть возможно большей (цементация и закалка). Любая деформация, овальность, большая шероховатость поверхности уменьшают несущую способность подшипника и увеличивают его износ, особенно там, где имеет место граничное трение.
Вкладыши следует обрабатывать так, чтобы были обеспечены соосность цапфы и вкладыша, прилегание поверхности цапфы по всей длине вкладыша и правильное круглое сечение цапфы. Вкладыши с заливкой из антифрикционного сплава нельзя пришабривать. Чем выше давление и чем меньше окружная скорость, тем более совершенным должно быть качество рабочей поверхности.
При скоростях свыше 1-2 м/сек (в зависимости от нагрузки) опасность разрыва смазочного слоя не возникает, и поэтому обеспечение минимальной шероховатости поверхности не так важно. В подобных случаях решающее значение имеет точность посадки. Для более шероховатой поверхности зазор в подшипнике надо брать большим, но это увеличивает работу трения и вибрацию вала.
Подшипниковые втулки – это, по существу, неразъемные вкладыши (рис. 9, в). Они широко применяются, для цапф от 3 до 200 мм, в подшипниках скольжения при ограниченных габаритах корпусных деталей, особенно для цапф малых диаметров. Для втулок без заливки применяют в зависимости от условий работы серый чугун, бронзы, латунь, металлокерамические материалы, текстолит, капролон и др. Применяют также втулки с заливкой. Для металлических втулок применяют следующие предельные отклонения: по внутреннему диаметру d – H7 (H8); по наружному диаметру D – у незакрепленных втулок – r7 при D=7…100 мм и t7 при D=105…220 мм; у закрепленных втулок – p7, n6, n7 при D=7…100 мм и p7, r6, r7 при D=105…220 мм.
|
Для втулок из текстолита натяг выбирают больше, а припуск на обработку после запрессовки 0,08…1,40 мм в зависимости от диаметра втулки. Максимальная длина – для втулок из металлокерамических материалов l=1,5D.
Запрессовка втулок производится давлением, а не ударами. Тонкостенные втулки запрессовывают с оправкой.
Полиамидные втулки (нейлоновые), преимущественно тонкостенные, не запрессовывают. Их насаживают на цапфу с зазором в стальной втулке или наклеивают. Учитывая значительное тепловое удлинение, во втулке делают винтовую канавку, с целью обеспечения расширения в осевом направлении.
|
|
Индивидуальные очистные сооружения: К классу индивидуальных очистных сооружений относят сооружения, пропускная способность которых...
Индивидуальные и групповые автопоилки: для животных. Схемы и конструкции...
Типы оградительных сооружений в морском порту: По расположению оградительных сооружений в плане различают волноломы, обе оконечности...
Типы сооружений для обработки осадков: Септиками называются сооружения, в которых одновременно происходят осветление сточной жидкости...
© cyberpedia.su 2017-2024 - Не является автором материалов. Исключительное право сохранено за автором текста.
Если вы не хотите, чтобы данный материал был у нас на сайте, перейдите по ссылке: Нарушение авторских прав. Мы поможем в написании вашей работы!