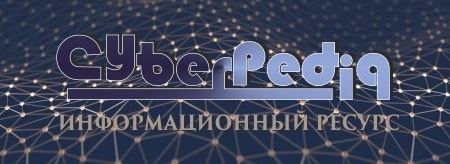
История развития хранилищ для нефти: Первые склады нефти появились в XVII веке. Они представляли собой землянные ямы-амбара глубиной 4…5 м...
Индивидуальные и групповые автопоилки: для животных. Схемы и конструкции...
Топ:
Характеристика АТП и сварочно-жестяницкого участка: Транспорт в настоящее время является одной из важнейших отраслей народного хозяйства...
Интересное:
Мероприятия для защиты от морозного пучения грунтов: Инженерная защита от морозного (криогенного) пучения грунтов необходима для легких малоэтажных зданий и других сооружений...
Влияние предпринимательской среды на эффективное функционирование предприятия: Предпринимательская среда – это совокупность внешних и внутренних факторов, оказывающих влияние на функционирование фирмы...
Принципы управления денежными потоками: одним из методов контроля за состоянием денежной наличности является...
Дисциплины:
![]() |
![]() |
5.00
из
|
Заказать работу |
|
|
Общие положения и неисправности
Основными агрегатами трансмиссии автомобиля являются: сцепление, коробка передач, раздаточная коробка, карданная передача, ведущий мост.
Трансмиссия автомобиля работает в условиях высоких знакопеременных динамических нагрузок. Основные рабочие детали трансмиссии большую часть времени находятся под высокими удельными нагрузками и напряжениями — это одна из трудностей достижения требуемой надежности трансмиссии. Затраты на ТО и текущий ремонт (ТР) агрегатов трансмиссии грузовых автомобилей составляют от 12 до 22 % общих затрат по их обслуживанию.
Основными причинами отказов трансмиссии являются: нарушение параметров регулировки и режимов смазки; образование чрезмерных суммарных зазоров в сопряжениях, вызывающих значительные динамические нагрузки в элементах кинематических пар агрегатов трансмиссии.
Основные неисправности механизмов трансмиссии:
· пробуксовка или неполное выключение сцепления;
· резкое включение сцепления (рывки при трогании с места);
· шум при работе коробки передач;
· самопроизвольное выключение и затрудненное переключение передач;
· биение карданного вала;
· шум и усиленный нагрев главной передачи ведущего моста.
При пробуксовке сцепления часть мощности, развиваемой двигателем, бесполезно расходуется на нагрев и усиленный износ сцепления; резко ухудшаются тяговые качества автомобиля (особенно при возрастании нагрузки) и значительно увеличивается расход топлива.
Основные причины пробуксовки сцепления:
· износ фрикционных накладок;
· замасливание дисков;
· потеря упругости нажимных пружин;
· ослабление затяжки центральной пружины (у сцеплений с центральной пружиной);
|
· отсутствие свободного хода педали сцепления;
· неправильная установка внутренних концов выжимных рычагов сцепления относительно рабочей поверхности нажимного диска;
· потеря упругости диафрагменного диска (у сцеплений диафрагменного типа).
При неполном выключении сцепления (сцепление «ведет») затрудняется переключение передач в коробке передач, при переключении передач наблюдаются шумы и стуки в коробке передач, усиленно изнашиваются шестерни и синхронизаторы коробки передач.
Основные причины неполного выключения сцепления:
· большой зазор между выжимным подшипником и выжимными рычагами;
· наличие воздуха в гидравлическом приводе сцепления;
· коробление ведомого диска;
· установка внутренних концов выжимных рычагов в плоскости, не перпендикулярной к оси коленчатого вала, или не в одной плоскости;
· поломка нажимных пружин;
· неправильная регулировка отхода переднего ведущего диска (у двухдисковых сцеплений).
При резком включении сцепления наблюдаются рывки в момент, когда автомобиль трогается с места, что существенно увеличивает динамические нагрузки в трансмиссии и вызывает поломки зубьев шестерен коробки передач и заднего моста.
Основные причины резкого включения сцепления:
· коробление ведомого диска;
· установка внутренних концов выжимных рычагов не в одной плоскости или в плоскости, не перпендикулярной к оси коленчатого вала;
· наличие сетки мелких трещин на рабочей поверхности ведущего диска, появляющихся вследствие перегрева при пробуксовке сцепления.
Шум при работе коробки передач наблюдается из-за износа подшипников, шестерен и валов коробки передач.
Причинами самопроизвольного выключения передач является износ фиксаторов, шестерен и синхронизаторов.
Причины затрудненного переключения передач:
· загрязнение механизма управления коробки передач, неправильная регулировка этого механизма;
· неправильная регулировка привода управления коробкой передач;
|
· неправильная регулировка сцепления (сцепление «ведет»).
Причинами биения карданного вала являются:
· изгиб вала вследствие наезда на дорожные препятствия;
· нарушение балансировки из-за износа шлицевой вилки и шлицевого наконечника карданного вала, а также крестовин и их подшипников;
· неправильная сборка карданного вала (вилки вала должны лежать в одной плоскости, причем метки на шлицевой вилке и шлицевом наконечнике, которые наносятся при балансировке карданного вала, должны быть совмещены, а при отсутствии таких меток они должны быть нанесены перед разборкой карданного вала).
При наличии биения карданного вала усиленно изнашиваются агрегаты трансмиссии, появляется вибрация кузова.
Основной причиной шумной работы главной передачи ведущего моста является нарушение правильного зацепления шестерен вследствие износа шестерен и подшипников.
ТО агрегатов трансмиссии
ТО‑1. Сцепление. Проверить:
· действие оттяжной пружины и свободный ход педали сцепления;
· герметичность системы гидропривода выключения сцепления;
· уровень жидкости в гидроприводе механизма выключения сцепления.
У автомобилей, оборудованных пневмоусилителем сцепления, проверить крепление кронштейна и составных частей силового цилиндра усилителя.
Коробка передач. Проверить:
· крепление коробки передач и ее внешних деталей;
· в действии механизм переключения передач на неподвижном автомобиле.
Прочистить сапуны коробки передач и мостов.
Карданная передача. Проверить:
· люфт в шарнирных и шлицевых соединениях карданной передачи;
· состояние и крепление промежуточной опоры и опорных пластин игольчатых подшипников;
· крепление фланцев карданных валов.
Задний мост. Проверить: герметичность соединений заднего (среднего) моста; крепление картера редуктора, фланцев полуосей и крышек колесных передач.
ТО‑2. Сцепление. Проверить:
· крепление картера сцепления;
· проверить действие оттяжной пружины, свободный и полный ход педали, работу сцепления и усилителя привода.
Прокачать гидропривод сцепления.
Коробка передач. Заменить масло в картерах агрегатов и бачках гидроприводов автомобиля в соответствии с химмотологической картой. Проверить:
· действие механизма переключения передач (при необходимости закрепить коробку передач и ее узлы);
|
· состояние, действие и крепление привода механизма переключения передач.
Карданная передача. Проверить:
· люфт в шарнирах и шлицевых соединениях карданной передачи;
· состояние и крепление промежуточной опоры и опорных пластин игольчатых подшипников;
· крепление фланцев карданных валов.
Задний мост. Проверить крепление гайки фланца ведущей шестерни главной передачи (при снятом карданном вале); закрепить фланцы полуосей.
Общее диагностирование
Общее состояние АКП определяют по ее внешнему виду, по уровню и состоянию рабочей жидкости (масла). Если система управления АКП электронная, тогда с помощью либо бортовой системы диагностики, либо специального сканера считываются коды неисправностей, которые были записаны в память блока управления в период эксплуатации автомобиля. После всех процедур диагностирования выводится отчет о найденных ошибках. На его основании принимается решение о дальнейшем ремонте либо замене неисправных частей автомобиля.
Следующим шагом диагностирования является проверка давлений в системе управления АКП. После этого проверяют исправность датчиков, проводки, переключателей и разъемов.
В случае необходимости может быть проведена тестовая проверка при движении автомобиля.
Проверка давления в гидросистеме трансмиссии. При работе в разных диапазонах в АКП поддерживается разное давление рабочей жидкости. Это необходимо для нормального функционирования фрикционных элементов управления, нагрузки на которые могут существенно различаться при разных режимах работы.
Перед проверкой давления необходимо прогреть рабочую жидкость до рабочей температуры и проверить ее уровень в АКП.
Автомобиль вывешивают, отвертывают пробку для контроля давления и в отверстие вместо пробки вворачивают трубопровод контрольного манометра. Рычаг привода стояночного тормоза ставят в крайнее верхнее положение. Запускают двигатель, выжимают педаль тормоза и проверяют давление рабочей жидкости при различных положениях селектора (давление не должно превышать значений, указанных в технической характеристике на данный автомобиль). Если давление не соответствует требуемому, необходимо провести диагностирование отдельных составляющих АКП.
|
Проверка электротехнических деталей АКП. Электромагнитные клапаны взаимодействуют с системой управления движением и включаются и выключаются по сигналам электронного блока управления, осуществляя переключение соответствующих повышенных передач. Такие клапаны устанавливают на АКП с электронным управлением.
Сначала электромагнитные клапаны проверяют на сопротивление между контактом и корпусом. К контактам соленоидов клапанов подводят напряжение аккумуляторной батареи, при этом должен быть слышен звук срабатывания соленоида. Затем проверяют механическую часть клапана, так как при наличии в ней посторонних частиц даже при срабатывании клапана управление потоком рабочей жидкости АКП осуществляться не будет; в клапан подают сжатый воздух и определяют полноту его открытия. После этого проверяют электрическую часть клапана путем подачи напряжения на его электромагнит, при этом клапан не должен пропускать воздух. Если работа электромагнитного клапана не соответствует норме, его заменяют.
Датчик температуры фиксирует температуру рабочей жидкости в АКП: при температуре масла примерно 150 °С на сигнализатор (лампочку) поступает сигнал от датчика.
Для проверки датчика температуры необходимо опустить его в емкость, залитую рабочей жидкостью для АКП, и определить электропроводность датчика при температуре 145…155 °С. Если при указанной температуре датчик не срабатывает, его необходимо заменить.
Смазочные работы
Проверка уровня рабочей жидкости. В АКП заливается рабочая жидкость марки ATF Dexron типа ATF D II E: GM Dexron II E-25300. Все рабочие жидкости для автоматических коробок Dexron можно смешивать друг с другом, однако никаких других добавок применять нельзя. Чтобы отличать рабочую жидкость ATF от других, ее иногда подкрашивают красным красителем.
Проверку уровня рабочей жидкости в АКП необходимо проводить один раз в год или через каждые 10 тыс. км пробега. Перед проверкой масло должно быть прогрето до рабочей температуры (примерно 60 °С). Как правило, рабочая температура достигается через 10…20 км пробега при температуре окружающего воздуха около 20 °С. Если нет возможности прогреть коробку передач пробегом, необходимо выполнить следующие операции: устанавливают автомобиль на ровной площадке, запускают двигатель и дают ему поработать в режиме холостого хода; устанавливают селектор в положение «Р» и, нажав на педаль тормоза, перемещают селектор через все положения, задерживаясь в каждом в течение 4…5 с, затем возвращают селектор в положение «Р». Уровень рабочей жидкости проверяют через 2 мин.
|
Температура окружающей среды при проверках уровня рабочей жидкости должна быть не ниже 20 °С, иначе результаты проверки могут быть недостоверными. Вытянув мерный стержень (щуп), проверяют уровень рабочей жидкости. Он должен находиться между метками «MIN» и «MAX». Если уровень ниже требуемого, следует долить соответствующее количество рабочей жидкости. У некоторых АКП на щупе могут быть указаны метки «MIN», «MAX» и температура, при которой проверяют уровень рабочей жидкости, например, 20 °С на одной стороне щупа и 90 °С на другой. Иногда на щупе есть еще и нижняя метка, соответствующая уровню холодной рабочей жидкости. Эта метка предназначена для приблизительного определения количества залитой рабочей жидкости в случае ее замены. Окончательно уровень рабочей жидкости все равно следует проверять после ее прогрева.
Нельзя допускать повышения уровня рабочей жидкости, так как это может привести к ее аэрации и вспениванию в результате завихрения жидкости шестернями. Кроме того, из-за повышения давления рабочая жидкость будет вытекать через вентиляционное отверстие насоса. Если произошел перелив рабочей жидкости, ее необходимо слить или удалить с помощью шприца.
При проверке уровня рабочей жидкости по следам, оставшимся на щупе, следует определить ее качество; жидкость должна быть без посторонних примесей и характерного горелого запаха. Коричневый оттенок и характерный запах рабочей жидкости свидетельствуют о сложных условиях эксплуатации: жидкость долгое время использовалась при высоких температурах и подгорала, что привело к появлению характерного запаха. Коричневый оттенок без запаха может появиться при долгом использовании жидкости без ее замены.
Черный оттенок рабочей жидкости свидетельствует о подгорании дисков муфты, износе втулок и шестерен. Он особенно сильно проявляется, когда алюминиевый порошок изнашиваемых втулок попадает в жидкость, которая чернеет.
Молочный оттенок рабочей жидкости указывает на попадание в коробку передач охлаждающей жидкости; охлаждающая жидкость может попасть в АКП из-за повреждений системы охлаждения коробки передач, поэтому необходимо проверить систему охлаждения, устранить неисправности и заменить рабочую жидкость.
Замена рабочей жидкости. Замена рабочей жидкости в АКП, как и в механических коробках передач, производится, как правило, через 60…150 тыс. км пробега с одновременной заменой масляного сетчатого фильтра в масляной ванне.
Для замены рабочей жидкости автомобиль устанавливают на подъемник или осмотровую канаву. Под поддон картера помещают большую емкость, поскольку большинство АКП не имеет традиционной сливной пробки и слив рабочей жидкости происходит при снятии поддона.
Снятый поддон картера осматривают на наличие на нем металлических частиц и волокон. Незначительное количество инородных материалов на поверхности поддона картера не связано с неисправностями АКП, за исключением случаев проскальзывания или запаздывания в переключении передач. Значительное количество загрязнений является следствием усиленного изнашивания деталей АКП.
При замене рабочей жидкости в АКП заменяют и фильтр. Перед установкой поддон картера и магнит, вблизи которого собираются частички металла, необходимо очистить растворителем.
Заполняют АКП рабочей жидкостью через воронку и удлинительный шланг в отверстие щупа. Количество рабочей жидкости, заливаемой в АКП, зависит от вида проводимых ремонтных работ и конкретного автомобиля. После заливки первоначального количества рабочей жидкости, нажав на педаль тормоза, запускают двигатель и, установив селектор в положение «Р», как и при операциях по проверке уровня рабочей жидкости, перемещают селектор по всем положениям и возвращают его в положение «Р». Проверяют уровень рабочей жидкости и при необходимости (по показаниям маслоизмерительного щупа) доливают до требуемого количества. Уровень рабочей жидкости проверяют при работающем двигателе в режиме холостого хода, в положении селектора «Р» и включенном стояночном тормозе.
Методы локализации утечек рабочей жидкости из АКП. При понижении уровня рабочей жидкости в АКП необходимо локализовать место утечки. Существует несколько методов локализации. Перед использованием любого метода необходимо тщательно очистить и вытереть насухо место предполагаемой утечки.
При использовании общего метода локализации утечки следует прогреть рабочую жидкость АКП до нормальной рабочей температуры путем пробега или другим способом, установить автомобиль на лист чистого картона (бумаги), заглушить двигатель и осмотреть подложенный лист на наличие масляных пятен.
При локализации утечки с помощью пудры предполагаемое место утечки покрывают пудрой из аэрозольной упаковки, известью или тальком. Прогрев рабочую жидкость до рабочей температуры, следует заглушить двигатель, осмотреть АКП и по месту появления рабочей жидкости определить место утечки.
При локализации с помощью специального красителя в рабочую жидкость через заливное отверстие в картере трансмиссии заливают специальный краситель в количестве, рекомендуемом его изготовителем. По месту появления красителя определяют место утечки.
После обнаружения мест утечки рабочей жидкости необходимо установить и устранить причины утечки. Возможные причины утечки:
· слабая затяжка резьбовых соединений;
· коррозионные повреждения и загрязнения резьбы отверстий в картере трансмиссии или крепежных соединений;
· смещение, повреждение или износ прокладок и уплотнений;
· повреждение или коробление уплотняемых отверстий и плоскостей;
· наличие зазубрин или других повреждений на валике переключателя диапазонов;
· увеличенный люфт и износ подшипников, приводящий к быстрому изнашиванию уплотнений втулок;
· дефекты литья картера и крышек;
· засорение вентиляционного отверстия (сапуна);
· наличие воды или антифриза в рабочей жидкости трансмиссии.
Общие положения и неисправности
Основными агрегатами трансмиссии автомобиля являются: сцепление, коробка передач, раздаточная коробка, карданная передача, ведущий мост.
Трансмиссия автомобиля работает в условиях высоких знакопеременных динамических нагрузок. Основные рабочие детали трансмиссии большую часть времени находятся под высокими удельными нагрузками и напряжениями — это одна из трудностей достижения требуемой надежности трансмиссии. Затраты на ТО и текущий ремонт (ТР) агрегатов трансмиссии грузовых автомобилей составляют от 12 до 22 % общих затрат по их обслуживанию.
Основными причинами отказов трансмиссии являются: нарушение параметров регулировки и режимов смазки; образование чрезмерных суммарных зазоров в сопряжениях, вызывающих значительные динамические нагрузки в элементах кинематических пар агрегатов трансмиссии.
Основные неисправности механизмов трансмиссии:
· пробуксовка или неполное выключение сцепления;
· резкое включение сцепления (рывки при трогании с места);
· шум при работе коробки передач;
· самопроизвольное выключение и затрудненное переключение передач;
· биение карданного вала;
· шум и усиленный нагрев главной передачи ведущего моста.
При пробуксовке сцепления часть мощности, развиваемой двигателем, бесполезно расходуется на нагрев и усиленный износ сцепления; резко ухудшаются тяговые качества автомобиля (особенно при возрастании нагрузки) и значительно увеличивается расход топлива.
Основные причины пробуксовки сцепления:
· износ фрикционных накладок;
· замасливание дисков;
· потеря упругости нажимных пружин;
· ослабление затяжки центральной пружины (у сцеплений с центральной пружиной);
· отсутствие свободного хода педали сцепления;
· неправильная установка внутренних концов выжимных рычагов сцепления относительно рабочей поверхности нажимного диска;
· потеря упругости диафрагменного диска (у сцеплений диафрагменного типа).
При неполном выключении сцепления (сцепление «ведет») затрудняется переключение передач в коробке передач, при переключении передач наблюдаются шумы и стуки в коробке передач, усиленно изнашиваются шестерни и синхронизаторы коробки передач.
Основные причины неполного выключения сцепления:
· большой зазор между выжимным подшипником и выжимными рычагами;
· наличие воздуха в гидравлическом приводе сцепления;
· коробление ведомого диска;
· установка внутренних концов выжимных рычагов в плоскости, не перпендикулярной к оси коленчатого вала, или не в одной плоскости;
· поломка нажимных пружин;
· неправильная регулировка отхода переднего ведущего диска (у двухдисковых сцеплений).
При резком включении сцепления наблюдаются рывки в момент, когда автомобиль трогается с места, что существенно увеличивает динамические нагрузки в трансмиссии и вызывает поломки зубьев шестерен коробки передач и заднего моста.
Основные причины резкого включения сцепления:
· коробление ведомого диска;
· установка внутренних концов выжимных рычагов не в одной плоскости или в плоскости, не перпендикулярной к оси коленчатого вала;
· наличие сетки мелких трещин на рабочей поверхности ведущего диска, появляющихся вследствие перегрева при пробуксовке сцепления.
Шум при работе коробки передач наблюдается из-за износа подшипников, шестерен и валов коробки передач.
Причинами самопроизвольного выключения передач является износ фиксаторов, шестерен и синхронизаторов.
Причины затрудненного переключения передач:
· загрязнение механизма управления коробки передач, неправильная регулировка этого механизма;
· неправильная регулировка привода управления коробкой передач;
· неправильная регулировка сцепления (сцепление «ведет»).
Причинами биения карданного вала являются:
· изгиб вала вследствие наезда на дорожные препятствия;
· нарушение балансировки из-за износа шлицевой вилки и шлицевого наконечника карданного вала, а также крестовин и их подшипников;
· неправильная сборка карданного вала (вилки вала должны лежать в одной плоскости, причем метки на шлицевой вилке и шлицевом наконечнике, которые наносятся при балансировке карданного вала, должны быть совмещены, а при отсутствии таких меток они должны быть нанесены перед разборкой карданного вала).
При наличии биения карданного вала усиленно изнашиваются агрегаты трансмиссии, появляется вибрация кузова.
Основной причиной шумной работы главной передачи ведущего моста является нарушение правильного зацепления шестерен вследствие износа шестерен и подшипников.
Методы диагностирования трансмиссии
Для своевременного обнаружения неисправностей и предупреждения отказов агрегатов трансмиссии применяются различные методы диагностирования: метрический, акустический, виброакустический, термический и др.
К метрическому методу диагностирования технического состояния агрегатов трансмиссии можно отнести способы контроля по параметрам, количественные значения которых измеряются сравнительно несложными приборами — люфтомером или индикатором. Для проверки зазора в карданном шарнире или шлицевом соединении одной рукой берут карданный вал около места соединения, другой стараются повернуть его в обе стороны либо покачать, а также приподнимают каждую из сторон шарнира 1 (рис. 1).
Рис. 1. Направление вращения и перемещения карданного вала во время проверки зазора в карданном шарнире (1) и шлицевом соединении (2)
Увеличенные люфты в карданной передаче и в остальных агрегатах трансмиссии можно определять с помощью люфтомера углового, который позволяет определять угловой зазор в трансмиссии автомобиля и ее отдельных агрегатах.
Люфтомер типа КИ-4832 (рис. 2) состоит из динамометрической рукоятки, зажима с двумя губками для установки люфтомера на вилке карданного шарнира заднеприводного автомобиля и измерительного диска.
Измерительный диск, вращающейся на оси, проградуирован (в угловых градусах): пределы измерений ±90°, цена деления шкалы 0,5°. На измерительном диске имеется герметичное полукольцо из прозрачного материала, в которое до половины его объема залита подкрашенная жидкость.
Рис. 2. Люфтомер угловой КИ-4832: 1 — губки зажима; 2 — измерительный диск; 3 — полукольцо с жидкостью; 4 — стрелка измерения момента поворота; 5 — шкала динамометрической рукоятки; 6 — динамометрическая рукоятка
С помощью специальных зажимов прибор закрепляют на валу, который проворачивают в одну сторону до устранения зазора, и устанавливают нулевую отметку на шкале измерительного диска. Полное устранение зазора определяют по резкому увеличению показаний рычажного динамометра. Проворачивая вал в другую сторону, определяют величину суммарного зазора карданной передачи, соединенной с валом.
Для определения зазора в главной передаче шестерни в коробке передач устанавливают в нейтральное положение и затормаживают ведущие колеса. Согласно экспериментальным данным предельные значения угловых зазоров в трансмиссии грузовых автомобилей равны: в карданной передаче 5…6°, в коробке передач 5…15°, в главной передаче 55…65°.
Для проверки величины биения карданного вала применяют устройство КИ-8902А (рис. 3).
Устройство имеет электромагнит 1, к которому через телескопический зажим 5 крепится индикатор 7 перемещений часового типа. Его крепят к раме автомобиля с помощью электромагнита, подключенного к бортовой сети напряжением 12 В, вывешивают ведущие колеса неработающей машины и включают нейтральную передачу. Пользуясь телескопическим зажимом, подводят поводок индикатора до соприкосновения с карданным валом. Проворачивая карданный вал на один оборот, определяют величину биения;
Рис. 3. Схема устройства КИ-8902А: 1 — электромагнит; 2 — рукоятка; 3 — рычаг; 4 — сухарь; 5 — телескопический зажим; 6 — корпус; 7 — индикатор; 8 — крышка; 9 — карданный вал для грузовых автомобилей эта величина не должна превышать 1,2 мм.
Проверку пробуксовки сцепления проводят с помощью стробоскопа, в котором момент возникновения вспышек синхронизирован с частотой вращения коленчатого вала двигателя.
На карданный вал в месте, доступном для освещения стробоскопом, наносится меловая отметка. Для создания нагрузки на сцепление автомобиль устанавливают на стенд с беговыми барабанами, в коробке передач включается прямая передача, затем стробоскопом освещают вращающийся карданный вал. При отсутствии пробуксовки сцепления меловая отметка будет казаться неподвижной. Состояние уплотнений карданных шарниров и шлицевого соединения проверяют путем внешнего осмотра.
Осматривают также переднюю эластичную резиновую муфту: на ней не должно быть раздутий и повреждений резины, расколов вокруг монтажных болтов; наличие масляных загрязнений на муфте свидетельствует об износе заднего сальника коробки передач, на заднем карданном шарнире — об износе сальника главной передачи. Аналогичным образом осматривают промежуточную опору. Подшипник промежуточной опоры проверяют путем подъема вала; если при этом ощущается перемещение (люфт), подшипник необходимо снять и проверить его состояние, покрутив наружное кольцо рукой; при значительном износе подшипник подлежит замене. В процессе осмотра необходимо также проверить затяжку всех монтажных болтов.
Сущность акустического метода заключается в том, что работа любого агрегата трансмиссии сопровождается ударными нагрузками деталей, соединенных в кинематические пары: шестерен, подшипников, шлицевых соединений и др. Звуковые волны, вызванные ударами сопряженных деталей друг о друга, являются сигналами, несущими информацию к диагностической аппаратуре. Приемником этих волн является диагностический датчик, который крепится в наиболее удобном месте на картере агрегата. Воспринимаемые датчиками колебания волны преобразуются в электросигналы, которые по проводам передаются к приборам блока обработки и анализа информации. Сложность расшифровки полученной информации состоит в том, что в работающем агрегате все его кинематические пары генерируют звуковые сигналы одновременно. Поэтому диагностическая аппаратура решает две задачи: вначале все зафиксированные сигналы надо разделить на отдельные составляющие, т.е. выявить сигналы по различиям генерирующих их пар, затем расшифровать интересующий (выделенный) сигнал, т.е. по его значению определить техническое состояние сопряжения.
Виброакустический метод диагностирования состоит в следующем. В подвижных сопряжениях агрегата трансмиссии энергия, передаваемая от одной детали к другой, и амплитуда вибраций пропорциональны величинам зазора или надлома, количеству трещин и осколков в деталях данной пары. Увеличение или уменьшение зазора вызывает рост ускорения вибраций. Таким образом, измерив ускорение вибрации данного сопряжения и сравнив его с эталонным значением, можно оценить техническое состояние диагностируемого узла. В процессе эксплуатации автомобилей можно по параметрам вибраций установить такой зазор, при котором обеспечивается наилучшая геометрия зацепления, т.е. исправное техническое состояние агрегата.
В основе термического метода диагностирования состояния агрегатов трансмиссии автомобиля лежит измерение температурных полей. Сравнивая полученное при измерении температуры выбранного на агрегате поля с эталонным, можно дать заключение о техническом состоянии диагностируемого агрегата.
Главным недостатком акустического, виброакустического и термического методов диагностирования является высокая стоимость оборудования, поэтому они не нашли широкого практического применения.
При общем диагностировании трансмиссии определяют механические потери по продолжительности движения автомобиля накатом, шумы и перегревы агрегатов, самопроизвольное выключение передач при ходовых или стендовых испытаниях автомобиля. Одновременно с этим принимают во внимание данные о механических потерях в трансмиссии, полученные при диагностировании автомобиля в целом, а также результаты внешнего осмотра (отсутствие подтеканий, деформаций и др.).
При поэлементном диагностировании трансмиссии определяют техническое состояние сцепления, коробки передач, раздаточной коробки, карданной передачи и ведущих мостов.
|
|
Общие условия выбора системы дренажа: Система дренажа выбирается в зависимости от характера защищаемого...
Кормораздатчик мобильный электрифицированный: схема и процесс работы устройства...
Особенности сооружения опор в сложных условиях: Сооружение ВЛ в районах с суровыми климатическими и тяжелыми геологическими условиями...
Наброски и зарисовки растений, плодов, цветов: Освоить конструктивное построение структуры дерева через зарисовки отдельных деревьев, группы деревьев...
© cyberpedia.su 2017-2024 - Не является автором материалов. Исключительное право сохранено за автором текста.
Если вы не хотите, чтобы данный материал был у нас на сайте, перейдите по ссылке: Нарушение авторских прав. Мы поможем в написании вашей работы!