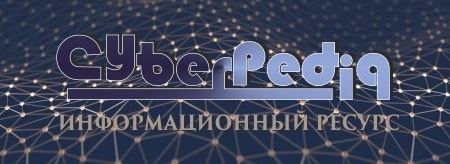
Индивидуальные очистные сооружения: К классу индивидуальных очистных сооружений относят сооружения, пропускная способность которых...
Наброски и зарисовки растений, плодов, цветов: Освоить конструктивное построение структуры дерева через зарисовки отдельных деревьев, группы деревьев...
Топ:
Организация стока поверхностных вод: Наибольшее количество влаги на земном шаре испаряется с поверхности морей и океанов...
Оценка эффективности инструментов коммуникационной политики: Внешние коммуникации - обмен информацией между организацией и её внешней средой...
Процедура выполнения команд. Рабочий цикл процессора: Функционирование процессора в основном состоит из повторяющихся рабочих циклов, каждый из которых соответствует...
Интересное:
Наиболее распространенные виды рака: Раковая опухоль — это самостоятельное новообразование, которое может возникнуть и от повышенного давления...
Лечение прогрессирующих форм рака: Одним из наиболее важных достижений экспериментальной химиотерапии опухолей, начатой в 60-х и реализованной в 70-х годах, является...
Средства для ингаляционного наркоза: Наркоз наступает в результате вдыхания (ингаляции) средств, которое осуществляют или с помощью маски...
Дисциплины:
![]() |
![]() |
5.00
из
|
Заказать работу |
|
|
Задание 1
1. Приведите краткую характеристику материалов, применяемых в доменном производстве для получения чугуна. Опишите способы их предварительной подготовки железной руды.
Природным сырьем для производства чугуна и стали служат железные руды, в которых железо представлено различными оксидными минералами. Основные типы этих руд: Гематитовые руды (красный железняк) содержат железо в виде гематита Fe2O3 (70,8% Fe). Руды этого типа обычно богаты железом (45-65%). Руды этого типа, содержащие менее 40% Fe и до 40-50% SiO2, называют железистыми кварцитами. Бурые железняки содержат железо в виде Fe2O3.nH2O (52,2-66,1% Fe), где n = 0,5-3 (2Fe2O3.H2O – турьит, Fe2O3.H2O – гетит, Fe2O3.3H2O – лимнит и др.). Руды этого типа содержат 25-50% Fe.
Магнетитовые руды содержат железо в виде магнетита Fe3O4 (72,4% Fe) и преимущественно богатые (50-60% Fe). Основной минерал сидеритовых руд FeCO3 – сидерит (48,2% Fe). Руды этого типа содержат 30-40% Fe.
Подготовка железных руд к металлургической переработке начинается на обогатительных фабриках, где их подвергают дроблению, измельчению, классификации по крупности, обогащению (промывка, магнитная сепарация, флотация и др.). В результате обогащения из руд получаются концентраты, содержащие 55-68% Fe, 5-10% SiO2 и другие примеси.
Основным методом металлургической переработки железосодержащего сырья продолжает оставаться двухстадийная технология, при которой в первой стадии сначала получают чугун, а затем его перерабатывают в сталь во второй стадии. Производство чугуна в основном осуществляют доменной плавкой, получая при этом два вида чугуна: передельный (перерабатывают в сталь) и литейный (идет в литейное производство). При наличии дешевой электроэнергии можно получать чугун и в электропечах. В доменных печах можно получать также некоторые ферросплавы, но в основном ферросплавы получают в электрических печах.
|
ПОДГОТОВКА МЕЛКОГО ЖЕЛЕЗОСОДЕРЖАЩЕГО СЫРЬЯ К ДОМЕННОЙ ПЛАВКЕ
Подготовка заключается в его окусковании. В основном для этих целей используют два метода: агломерацию и получение железорудных окатышей.
При выборе способа окускования руководствуются следующими соображениями. Если после обогащения получают грубозернистый концентрат, то всегда применяют агломерацию. Из тонкозернистых концентратов (– 0,05 мм) производят окатыши обычно в тех случаях, когда фабрика окускования находится на удалении от доменного цеха, т.к. окатыши имеют более высокую прочность в холодном состоянии и лучше (без разрушения) переносят транспортировку.
При агломерации (аглообжиге) шихту, состоящую из мелких железосодержащих материалов (рудная мелочь, концентрат, пыли), известняка, оборотных материалов и коксика (5-7%, крупность 3мм), увлажняют до 8-15% и подают на паллеты (тележки с дном в виде колосниковой решетки) ленточной агломерационной машины (рис.1) равномерным слоем высотой 250-400 мм. Проходя под зажигательным горном, поверхностный слой шихты нагревается до 750-850 и коксик начинает гореть. При дальнейшем движении паллет к разгрузочному концу в зоне горения коксика температура шихты достигает 1300-1500
, часть ее переходит в расплавленное состояние, смачивает нерасплавившиеся частицы шихты, а после снижения температуры затвердевает и скрепляет их. В результате этого образуется пористый кусковой продукт – агломерат.
На практике используют агломашины с площадью спекания 50-600 м2. Их удельная производительность по шихте 30-40 т/м2*сут. Для улучшения показателей доменной плавки агломерат получают офлюсованный
Рис. 1. Схема процесса спекания на агломерационной машине ленточного типа: 1 – спекательные тележки – паллеты; 2 – укладчик постели; 3 – челноковый питатель ленты шихтой; 4 – газовый зажигательный горн; 5 – постель; 6 – зона сырой шихты; 7 – зона сушки и подогрева шихты; 8 – зона горения твердого топлива; 9 – зона готового агломерата; 10 – разгрузочный конец машины; 11 – вакуумкамера; 12 – ведущая звездочка привода ленты; 13 – сборный газопровод
|
При получении железорудных окатышей мелкую шихту, увлажненную до 8-10%, без добавки или с добавкой связующего (чаще всего бентонит; 0,5-1,5% от массы концентрата) окомковывают на барабанных (диаметр до 3 м, длина до 10-11 м) или тарельчатых (наклонная под углом 30-60 градусов чаша диаметром до 6-8 м с бортами; n = 5-15 об/мин) грануляторах (окомкователях), получая гранулы диаметром 12-25 мм. Сырые окатыши подвергают упрочняющему обжигу, нагревая их до 1200-1400 на конвейерных машинах (аналогичны ленточной агломашине) с рабочей площадью 100-780 м2 или в комбинированных агрегатах, состоящих из конвейерной машины (сушка и подогрев окатышей) и трубчатой вращающейся печи (обжиг окатышей).
ПРОИЗВОДСТВО ЧУГУНА
Шихта доменных печей состоит из кускового железосодержащего материала (руда, агломерат, окатыши), кокса (топливо и восстановитель) и флюсов (известняк). Цель доменной плавки – извлечь из сырья железо в виде чугуна. Доменная печь представляет собою агрегат с рабочим пространством, вертикально вытянутым вверх. Главными ее элементами являются колошник, шахта печи, распар, заплечики и горн. Основным огнеупорным материалом для кладки печи является высококачественный шамот; горн внутри выложен из углеродистых блоков. Характеризуются доменные печи объемом рабочего пространства, составляющего 1000-5500 м3. Высота доменной печи объемом 5500 м3 достигает 41 м, а диаметр в области распара 16,5 м. Шихта, загруженная в печь, перемещается сверху вниз навстречу восходящему потоку газов, образующемуся за счет горения кокса в области фурм. Воздух подается в печь через фурмы предварительно нагретым в кауперах до 1000-1200 . Давление дутья 280-420 кПа. Вместе с дутьем практикуют подачу в печь топливных добавок (природный газ, угольная пыль и др.). Максимальная температура продуктов сгорания кокса достигает1900-2000
, но уже на расстоянии 1,5-2 м от фурм она снижается до 1450-1600
. Температура газов, удаляемых из доменной печи, 200-400
.
Из загруженной в доменную печь шихты в результате совокупности протекающих в ней процессов (химических, физических, теплообменных, массообменных, механических) получают продукты плавки: чугун, шлак, газы и пыль. Жидкие продукты плавки (чугун и шлак), скапливающиеся в горне печи, периодически или непрерывно выпускают через соответствующие летки.
|
Основными физическими и химическими процессами, протекающими в доменной печи, являются: дегидратация шихты, разложение карбонатов, горение кокса, восстановление оксидов, науглероживание железа и превращение его в чугун, шлакообразование и расплавление шлака, взаимодействие металла и шлака.
Физико-механическая влага удаляется из шихты при ее нагреве до 100-200 , гидроксиды железа обезвоживаются при температуре около 300
, а из гидратированных силикатов влага уходит при температурах до 900
.
Карбонаты железа разлагаются при 400-600 , а карбонаты кальция при 800-900
.
Производство чугуна и стали относится к отрасли черной металлургии. Чугуны и стали – это сплавы железа с углеродом, стали содержат до 2% углерода, чугуны – до 3,5%. Производство стали в подавляющем большинстве является двухстадийным процессом, технологическая цепочка включает доменный процесс, конечным продуктом которого является чугун, и процесс передела чугуна в сталь, который может осуществляться одним из трех путей – конвертерный передел, плавка в мартеновской печи и электроплавка. В настоящее время порядка 60% выплавляемой стали получают в конвертерах, около 30% - в электропечах и менее 10% -мартеновская сталь.
Сущностью доменного процесса, имеющего восстановительный характер, является восстановление оксидов железа руды и науглероживание железа. Перед доменной плавкой железорудный концентрат подвергают окускованию – агломерации. Для получения чугуна в доменную печь загружают железный агломерат, флюсы и топливо - кокс. Продукты доменной плавки – чугун, шлак и газы. Ценным продуктом является чугун, большая часть которого идет на получение стали, а около 20% общего объема получаемого чугуна – это литейный чугун.
Процесс получения стали – это окислительный процесс, сутью которого является окисление примесей –углерода, марганца, кремния, фосфора, серы, содержащихся в чугуне. Окислителем примесей является кислород, источником которого в разных процессах являются дутье, железная руда, скрап. В зависимости от выбора агрегата для выплавки стали механизм взаимодействия кислорода и примесей может быть различным. После удаления примесей в шлак в виде оксидов сталь раскисляют, добавляя марганец, кремний и алюминий для удаления избытка окислителя и газов.
|
В последнее время все большее развитие получают процессы бездоменной металлургии, позволяющие получать стать прямым восстановлением железа из руд.
Литье под давлением
Литьё в пресс-формы происходит под давлением от 35 до 700 МПа, обеспечивающим удаление воздушной пористости.
Высокие скорости впуска обеспечивают хорошее качество поверхностей отливки.
Метода литья под давлением получают детали для которых не требуются вообще или нет в технологии изготовления дальнейшей механической обработки.
Расплавленный металл заливается в камеру прессования, а затем под действием прессующего поршня, перемещающегося в этой камере, через литниковые каналы заполняет с высокой скоростью полость формы.
Преимущества:
- Высокое качество отливки
- Высокая производительность, т.к. металл напрямую идет в пресс форму
Недостатки
• Необходимо соблюдать режимы давления при литье
• Специфические требования технологичности конструкций литых деталей
• Высокая стоимость пресс-форм
• Литье под давлением позволяет получать сложные по геометрии тонкостенные отливки, близкие по размерам к конечной продукции. Этот способ литья очень производителен при автоматизации процесса. Наиболее широко применяется литье под давлением для изготовления отливок из магниевых, цинковых и алюминиевых.
Задание 2
1. Изобразите эскизы пяти профилей сортового проката. Перечислите прокатные операции технологического процесса получения сортового проката, начиная с указания исходного материала.
Рисунок 1- Сортовой прокат
Прокат можно разбить на следующие основные четыре группы: сортовой, листовой, трубы, специальные виды проката (бандажи, колеса, периодические профили и пр.). Наиболее разнообразной является группа сортового проката, который подразделяется на простые и фасонные профили.
Прокат в виде круга, квадрата, полос плоского сечения относится к простым профилям. Прокат сложного поперечного сечения относится к фасонным профилям. В зависимости от назначения фасонные профили подразделяются на профили общего или массового потребления (угловой профиль, швеллеры, двутавровые балки, шестигранные профили и др.) и профили специального назначения (рельсы железнодорожные широкой и узкой колеи, рельсы трамвайные, профили сельскохозяйственного машиностроения, электропромышленности, нефтяной промышленности и др.).
|
Весь сортовой прокат подразделяется на четыре группы: сталь крупносортная, сред несортная, мелкосортная и катанка диаметром от 5,5 до 9мм.
Процесс прокаткиПрокатка металла осуществляется при прохождении его между валками, вращающимися в разных направлениях. При прокатке металл обжимается, в результате чего толщина полосы уменьшается, а её длина и ширина увеличиваются.Опишите технологический процесс изготовления поковки способом ковки на паровоздушном ковочном молоте. При выполнении работы следует: 1) описать сущность процесса ковки и указать область ее применения; 2) изобразить схему пресса и описать его работу; 3) описать механизацию процесса ковки.
Сущность процесса ковки.
Ковкой называют процесс горячей обработки металлов давлением, при котором путем многократного действияуниверсального подкладного инструмента или бойков металл заготовки пластически деформируется, постепенно приобретая заданные форму, размеры и свойства.
В процессе ковки предварительно нагретая заготовка укладывается на нижний боек молота или пресса, а верхним бойком наносятся удары либо по самой заготовке, либо по подкладному инструменту. При этом металл свободно течет в стороны, не ограниченные рабочими поверхностями инструмента,
Область применения.
Ковкой получают фасонные заготовки для последующей механической обработки. Эти заготовки называют коваными поковками или просто поковками.
Процесс ковки является малопроизводительным, так как требует многократных перемещений заготовки между бойками. При ковке небольших по массе поковок эти перемещения осуществляются вручную, а тяжелые заготовки перемещаются различными средствами механизации. Поковки, полученные ковкой, имеют большие припуски на механическую обработку.
На предприятиях тяжелого машиностроения ковка является одним из основных заготовительных процессов. Ковка экономически выгодна в единичном и мелкосерийном производствах для получения поковок любой массы. Для крупных деталей машин массой от 2 т. до 250 т. ковка является единственно возможным способом изготовления. Примерами тяжелых поковок могут служить валы гидрогенераторов, турбинных дисков, коленчатых валов судовых двигателей, валков прокатных станов, роторы мощных гидротурбин, валы корабельных двигателей и т. п.
Поковки меньшей массы от 0,5 кг до десятков и сотен килограммов, можно изготовлять и ковкой, и штамповкой. Хотя штамповка имеет ряд преимуществ перед ковкой, однако в единичном и мелкосерийном производстве ковка обычно экономически более целесообразна. Объясняется это тем, что при ковке используют универсальный (годный для изготовления различных поковок) инструмент, а изготовление специального инструмента (штампа) при небольшой партии одинаковых поковок экономически невыгодно.
Ковочные молоты. Молоты создают динамическое (ударное) воздействие инструмента (верхнего бойка) на заготовку. Продолжительность деформации при ковке на молотах 10-3с, а скорость деформирования — 6...6,5 м/с. Наибольшее применение получили паровоздушные и приводные молоты.
В паровоздушном молоте (рис. 4) подъем и опускание бабы 10 с закрепленным на ней верхним бойком И по направляющим 7 производится при подаче пара или сжатого воздуха давлением 0,7...0,9 МПа в рабочий цилиндр 5. Подача пара регулируется с помощью золотникового устройства 4. При перемещении золотника 3 с помощью рычага 1 и тяги 2 вверх или вниз пар поступает в верхнюю или нижнюю полость цилиндра 5 и перемещает поршень 6, соединенный штоком 8 с бабой 10. При падении бабы давление пара на верхнюю часть поршня создает дополнительное усилие. Нижний боек 12 неподвижно закреплен на массивной стальной фундаментной плите — шаботе 13, лежащей на дубовой подушке на отдельном фундаменте. Чем больше масса шабота, тем большая часть кинетической энергии падающих частей превращается в энергию деформации заготовки. Обычно она в 15 раз больше массы падающих частей.
Установка станины 9 и шабота 13 на отдельных фундаментах обеспечивает свободный доступ к бойкам, оберегает конструкцию молота от сотрясений, но не гарантирует параллельности бойков. Паровоздушные молоты строят с массой падающих частей 1...8 т.
Из приводных молотов наибольшее применение получили пневматические. В них подъем и опускание поршня, шток которого одновременно является бабой молота и к которому крепится верхний боек, совершается с помощью сжатого воздуха давлением 0,2... 0,3 МПа. Сжатый воздух поступает в рабочий цилиндр от поршневого компрессора, приводимого в движение кривошипно-шатунным механизмом от отдельного электродвигателя. Рабочий и компрессионный цилиндры расположены на одной станине. Пневматические молоты имеют массу падающих частей 50...1000 кг и применяются для ковки мелких поковок (до 20 кг).
Рис. 4. Паровоздушный ковочный молот.
Механизация и автоматизация ковки
Механизация и автоматизация малопроизводительного процесса свободной ковки имеет большое значение.
При ковке широко применяют механизмы и устройства, снижающие трудоемкость вспомогательных операций: мостовые краны, ковочные поворотные краны, лебедки, подвесные клещи, электротележки с поворотными столами, электрические кантователи, посадочные машины, манипуляторы и др..
Посадочные машины относят к специальным манипуляторам, управляемым оператором. Применяют их в комплексах «нагревательная печь – ковочная машина» для загрузки и разгрузки заготовок, а также для транспортирования и установки их в рабочую зону оборудования.
Несмотря на нестабильность процессов ковки, в производстве используют и промышленные роботы. Более того, в производстве создаются роботизированные технологические комплексы (РТК) для ковки. РТК называется совокупность единицы технологического оборудования, промышленного робота (ПР) и средств оснащения, автономно функционирующая и осуществляющая многократные циклы. В РТК промышленный робот может быть использован в качестве технологического оборудования. При ковке в состав РТК может входить быстроходный гидравлический пресс (усилие до 50МН) и ПР (типа МКП-25), оснащенный автоматизированной системой числового программного управления (ЧПУ), которая обеспечивает чередование во времени автоматического режима управления с ручным. Система ЧПУ – четырех координатная, она управляет подъемом руки, перемещением руки параллельно рельсам, ротацией клещей и движением бойка пресса.
Задание 3
Применяемое оборудование
Когда речь заходит о выполнении электродугового сваривания на промышленном предприятии, то, прежде чем приступать к работе, рабочий закрепляет соединяемые изделия на особом сборочном стенде либо посредством специальных инструментов. Благодаря этому возможно предотвратить перемещения обрабатываемых деталей при осуществлении ручной сварки.
При прокладывании труб обычно применяют мобильные сварные головки. Для изготовления листовых конструкций используют или стационарные аппараты, или универсальные мобильные (например, сварной трактор). Трактор для сваривания под флюсовым слоем представляет собой тележку-самоход с электрическим мотором, на которой монтирована автоматическая сварная головка. Подобный аппарат способен передвигаться продольно соединяемым изделиям по рельсам.
Еще на производстве часто применяются мобильные либо стационарные сварные колонны. Они, в сочетании с опорами на роликах либо вращателями, позволяют сваривать продольные, а также кольцевые швы.
Используемые материалы
От правильности выбора проволоки электрода зависит качество сваривания. Химический состав проволоки определяет шовные характеристики. Желательно использовать проволоку из стали, соответствующую ГОСТ 2246-70. Она производится из легированной, высоколегированной, малоуглеродистой стали. Размеры готовой проволоки соответствуют стандарту (диаметр составляет 0,3-12 миллиметров).
Поставляется проволока обычно в восьмидесятиметровых бухтах. Иногда, с разрешения покупателя, используются кассеты, катушки. Перед применением проволоки, которая определенный период хранилась в складском помещении, эксперты рекомендуют очищать ее, обрабатывать бензином/керосином. Это дает возможность устранить с нее ржавчину и грязь.
Для соединения деталей из алюминия используется проволока, соответствующая ГОСТ 7871-75. Нередко используют проволоку, покрытую медью. Ее не нужно предварительно обрабатывать. Качество сварки, осуществляемой флюсовой проволокой без газа, прямо зависит от характеристик флюса. От состава флюса зависят показатели газовой среды, жидкого шлака. Взаимодействуя с деталью, шлак определяет структуру шовного металла. От его структуры зависит устойчивость изделия к растрескиванию.
Флюс используется для того, чтобы:
легировать шовный металл;
изолировать сварную ванну от внешних воздействий;
создавать шовную поверхность;
стабилизировать дуговой разряд.
Технология сварки
Технология автоматической сварки под флюсом различается с обычной сваркой тем, что электрическая дуга при ее осуществлении прогорает под особым веществом (флюсом). При зажигании дуги изделие и электрод подвергаются плавлению вместе с флюсом.
Как автоматическая дуговая сварка под флюсом, так и механизированная располагают следующими особенностями:
Сварочный процесс возможно выполнять с применением токов большой величины. Обычно сила электрического тока при осуществлении подобной процедуры составляет 1000 – 2000 ампер. Иногда ее значение может равняться 4000 ампер. Обыкновенное дуговое сваривание проводится при силе тока, не превышающей 600 ампер. Последующее повышение данного показателя является причиной того, что металл разбрызгивается, становится невозможно создать сварное соединение. Однако чем больше сила тока, тем быстрее проходит сваривание и тем качественнее и надежнее шов.
Автоматическая сварка под слоем флюса предполагает формирование закрытой электрической дуги, расплавляющей металлическое изделие достаточно глубоко. Благодаря этому кромки обрабатываемого изделия возможно не подготавливать перед началом сварочного процесса.
Ввиду того что при флюсовом сваривании используется сильный ток, процедура проходит достаточно быстро. Если провести сравнение скорости флюсового сваривания со скоростью обычной сварки, становится ясно, что первый показатель превышает второй в десять раз.
Пузырь газа, формируемый при проведении флюсового сварного процесса, не дает разбрызгиваться металлу, из которого изготовлена обрабатываемая рабочим деталь. Благодаря этому возможно создавать высококачественные сварные соединения. Кроме того, сильно уменьшаются потери металла электрода, составляющие 2% от веса расплавившегося материала (максимальное значение). Благодаря этому обеспечивается экономия электрода, электроэнергии.
Режимы сварки под флюсом выбираются при учете:
размера применяемой проволоки электрода;
вида электрического тока, его полярности;
скорости выполнения сварочного процесса;
напряжения, формирующего сварную дугу.
Дополнительными показателями, которые влияют на выбор сварочного режима, считаются:
величина частичек, состав и плотность применяемого флюса;
значение вылета проволоки электрода;
взаимное расположение электродного элемента и обрабатываемого изделия.
Список литературы
1. Материаловедение в машиностроении и промышленных технологиях: учеб.-справ. руководство / В. А. Струк [и др.]. – Долгопрудный: Интеллект, 2010. – 536 с.
2. Перинский В.В.. Лясников В.Н., Фетисов Г.П. Материаловедение специальных материалов машиностроения: учебное пособие / В.В. Перинский, В.Н. Лясников, Г.П. Фетисов. Саратов: СГТУ, 2011. 504 с.
3. Адаскин, А.М. Материаловедение и технология материалов: Учебное пособие / А.М. Адаскин, В.М. Зуев.. - М.: Форум, НИЦ ИНФРА-М, 2013. - 336 c.
4. Зарембо, Е. Г. Материаловедение: иллюстрированное учебное пособие (альбом)/ Е.Г. Зарембо.-М.: ГОУ «УМЦ ЖДТ», 2008.
Задание 1
1. Приведите краткую характеристику материалов, применяемых в доменном производстве для получения чугуна. Опишите способы их предварительной подготовки железной руды.
Природным сырьем для производства чугуна и стали служат железные руды, в которых железо представлено различными оксидными минералами. Основные типы этих руд: Гематитовые руды (красный железняк) содержат железо в виде гематита Fe2O3 (70,8% Fe). Руды этого типа обычно богаты железом (45-65%). Руды этого типа, содержащие менее 40% Fe и до 40-50% SiO2, называют железистыми кварцитами. Бурые железняки содержат железо в виде Fe2O3.nH2O (52,2-66,1% Fe), где n = 0,5-3 (2Fe2O3.H2O – турьит, Fe2O3.H2O – гетит, Fe2O3.3H2O – лимнит и др.). Руды этого типа содержат 25-50% Fe.
Магнетитовые руды содержат железо в виде магнетита Fe3O4 (72,4% Fe) и преимущественно богатые (50-60% Fe). Основной минерал сидеритовых руд FeCO3 – сидерит (48,2% Fe). Руды этого типа содержат 30-40% Fe.
Подготовка железных руд к металлургической переработке начинается на обогатительных фабриках, где их подвергают дроблению, измельчению, классификации по крупности, обогащению (промывка, магнитная сепарация, флотация и др.). В результате обогащения из руд получаются концентраты, содержащие 55-68% Fe, 5-10% SiO2 и другие примеси.
Основным методом металлургической переработки железосодержащего сырья продолжает оставаться двухстадийная технология, при которой в первой стадии сначала получают чугун, а затем его перерабатывают в сталь во второй стадии. Производство чугуна в основном осуществляют доменной плавкой, получая при этом два вида чугуна: передельный (перерабатывают в сталь) и литейный (идет в литейное производство). При наличии дешевой электроэнергии можно получать чугун и в электропечах. В доменных печах можно получать также некоторые ферросплавы, но в основном ферросплавы получают в электрических печах.
ПОДГОТОВКА МЕЛКОГО ЖЕЛЕЗОСОДЕРЖАЩЕГО СЫРЬЯ К ДОМЕННОЙ ПЛАВКЕ
Подготовка заключается в его окусковании. В основном для этих целей используют два метода: агломерацию и получение железорудных окатышей.
При выборе способа окускования руководствуются следующими соображениями. Если после обогащения получают грубозернистый концентрат, то всегда применяют агломерацию. Из тонкозернистых концентратов (– 0,05 мм) производят окатыши обычно в тех случаях, когда фабрика окускования находится на удалении от доменного цеха, т.к. окатыши имеют более высокую прочность в холодном состоянии и лучше (без разрушения) переносят транспортировку.
При агломерации (аглообжиге) шихту, состоящую из мелких железосодержащих материалов (рудная мелочь, концентрат, пыли), известняка, оборотных материалов и коксика (5-7%, крупность 3мм), увлажняют до 8-15% и подают на паллеты (тележки с дном в виде колосниковой решетки) ленточной агломерационной машины (рис.1) равномерным слоем высотой 250-400 мм. Проходя под зажигательным горном, поверхностный слой шихты нагревается до 750-850 и коксик начинает гореть. При дальнейшем движении паллет к разгрузочному концу в зоне горения коксика температура шихты достигает 1300-1500
, часть ее переходит в расплавленное состояние, смачивает нерасплавившиеся частицы шихты, а после снижения температуры затвердевает и скрепляет их. В результате этого образуется пористый кусковой продукт – агломерат.
На практике используют агломашины с площадью спекания 50-600 м2. Их удельная производительность по шихте 30-40 т/м2*сут. Для улучшения показателей доменной плавки агломерат получают офлюсованный
Рис. 1. Схема процесса спекания на агломерационной машине ленточного типа: 1 – спекательные тележки – паллеты; 2 – укладчик постели; 3 – челноковый питатель ленты шихтой; 4 – газовый зажигательный горн; 5 – постель; 6 – зона сырой шихты; 7 – зона сушки и подогрева шихты; 8 – зона горения твердого топлива; 9 – зона готового агломерата; 10 – разгрузочный конец машины; 11 – вакуумкамера; 12 – ведущая звездочка привода ленты; 13 – сборный газопровод
При получении железорудных окатышей мелкую шихту, увлажненную до 8-10%, без добавки или с добавкой связующего (чаще всего бентонит; 0,5-1,5% от массы концентрата) окомковывают на барабанных (диаметр до 3 м, длина до 10-11 м) или тарельчатых (наклонная под углом 30-60 градусов чаша диаметром до 6-8 м с бортами; n = 5-15 об/мин) грануляторах (окомкователях), получая гранулы диаметром 12-25 мм. Сырые окатыши подвергают упрочняющему обжигу, нагревая их до 1200-1400 на конвейерных машинах (аналогичны ленточной агломашине) с рабочей площадью 100-780 м2 или в комбинированных агрегатах, состоящих из конвейерной машины (сушка и подогрев окатышей) и трубчатой вращающейся печи (обжиг окатышей).
ПРОИЗВОДСТВО ЧУГУНА
Шихта доменных печей состоит из кускового железосодержащего материала (руда, агломерат, окатыши), кокса (топливо и восстановитель) и флюсов (известняк). Цель доменной плавки – извлечь из сырья железо в виде чугуна. Доменная печь представляет собою агрегат с рабочим пространством, вертикально вытянутым вверх. Главными ее элементами являются колошник, шахта печи, распар, заплечики и горн. Основным огнеупорным материалом для кладки печи является высококачественный шамот; горн внутри выложен из углеродистых блоков. Характеризуются доменные печи объемом рабочего пространства, составляющего 1000-5500 м3. Высота доменной печи объемом 5500 м3 достигает 41 м, а диаметр в области распара 16,5 м. Шихта, загруженная в печь, перемещается сверху вниз навстречу восходящему потоку газов, образующемуся за счет горения кокса в области фурм. Воздух подается в печь через фурмы предварительно нагретым в кауперах до 1000-1200 . Давление дутья 280-420 кПа. Вместе с дутьем практикуют подачу в печь топливных добавок (природный газ, угольная пыль и др.). Максимальная температура продуктов сгорания кокса достигает1900-2000
, но уже на расстоянии 1,5-2 м от фурм она снижается до 1450-1600
. Температура газов, удаляемых из доменной печи, 200-400
.
Из загруженной в доменную печь шихты в результате совокупности протекающих в ней процессов (химических, физических, теплообменных, массообменных, механических) получают продукты плавки: чугун, шлак, газы и пыль. Жидкие продукты плавки (чугун и шлак), скапливающиеся в горне печи, периодически или непрерывно выпускают через соответствующие летки.
Основными физическими и химическими процессами, протекающими в доменной печи, являются: дегидратация шихты, разложение карбонатов, горение кокса, восстановление оксидов, науглероживание железа и превращение его в чугун, шлакообразование и расплавление шлака, взаимодействие металла и шлака.
Физико-механическая влага удаляется из шихты при ее нагреве до 100-200 , гидроксиды железа обезвоживаются при температуре около 300
, а из гидратированных силикатов влага уходит при температурах до 900
.
Карбонаты железа разлагаются при 400-600 , а карбонаты кальция при 800-900
.
Производство чугуна и стали относится к отрасли черной металлургии. Чугуны и стали – это сплавы железа с углеродом, стали содержат до 2% углерода, чугуны – до 3,5%. Производство стали в подавляющем большинстве является двухстадийным процессом, технологическая цепочка включает доменный процесс, конечным продуктом которого является чугун, и процесс передела чугуна в сталь, который может осуществляться одним из трех путей – конвертерный передел, плавка в мартеновской печи и электроплавка. В настоящее время порядка 60% выплавляемой стали получают в конвертерах, около 30% - в электропечах и менее 10% -мартеновская сталь.
Сущностью доменного процесса, имеющего восстановительный характер, является восстановление оксидов железа руды и науглероживание железа. Перед доменной плавкой железорудный концентрат подвергают окускованию – агломерации. Для получения чугуна в доменную печь загружают железный агломерат, флюсы и топливо - кокс. Продукты доменной плавки – чугун, шлак и газы. Ценным продуктом является чугун, большая часть которого идет на получение стали, а около 20% общего объема получаемого чугуна – это литейный чугун.
Процесс получения стали – это окислительный процесс, сутью которого является окисление примесей –углерода, марганца, кремния, фосфора, серы, содержащихся в чугуне. Окислителем примесей является кислород, источником которого в разных процессах являются дутье, железная руда, скрап. В зависимости от выбора агрегата для выплавки стали механизм взаимодействия кислорода и примесей может быть различным. После удаления примесей в шлак в виде оксидов сталь раскисляют, добавляя марганец, кремний и алюминий для удаления избытка окислителя и газов.
В последнее время все большее развитие получают процессы бездоменной металлургии, позволяющие получать стать прямым восстановлением железа из руд.
Опишите последовательность изготовления формы методом ручной формовки.
Технология изготовления отливок в песчанно-глинистых формах
Сущность процесса заключается в заливке расплавленного металла в формы, которые изготовлены из формовочных смесей, основными материалами которых является формовочные пески и глина, путем их уплотнения с использованием модельного комплекта, после затвердевания сохраняет заданную конфигурацию
Рис. 2. Литейная форма и литниковая система:
1,2 – нижняя и верхняя полуформы, 3 – литейный стержень, 4 – металлический центрирующий штырь, 5 – выпор (прибыль), 6 – литниковая чаша, 7 – стояк, 8 – опока, 9 – шлакоуловитель, 10 – питатель.
Основные операции технологического процесса в песчанно-глинистые формы:
- изготовление формы;
- плавка металла;
- заливка металла в формы;
- выбивка отливки из формы;
- очистка отливки;
- отрезка литниковой системы;
- термическая обработка;
- контроль отливки.
Изготовлением формы называется операция формовки и определяется наличием литейной оснастки, которая включает в себя следующие элементы:
1) модельный комплект – часть технологических приспособлений необходимых для получения в форме контуров отливки включающие модель отливки, модели литниковой системы, стержневые ящики;
2) формовочный комплект – приспособления для проведения формовки включающие опоки, штыри, модельные плиты для установки и крепления моделей, сушильные плиты, шаблоны.
Модель – это приспособление, с помощью которого в форме получают отпечаток, соответствующий конфигурации отливки. Модель изготавливают с увеличением размеров на усадку металла отливки и припусками на механическую обработку рабочих поверхностей отливки и назначаются ГОСТами. На вертикальных стенках предусматривают формовочные уклоны для облегчения извлечения модели из полости формы. С торцов располагаются знаки, предназначенные для получения гнезд, в которые устанавливаются стержни. Модели бывают деревянные или металлические, разъемные и неразъемные. Разъемную модель применяют, как правило, в тех случаях, когда модель не имеет плоской поверхности.
Модели литниковой системы предназначены для изготовления литниковой системы – совокупность каналов и резервуаров, по которым расплав металла поступает в фо<
|
|
Эмиссия газов от очистных сооружений канализации: В последние годы внимание мирового сообщества сосредоточено на экологических проблемах...
Индивидуальные и групповые автопоилки: для животных. Схемы и конструкции...
Адаптации растений и животных к жизни в горах: Большое значение для жизни организмов в горах имеют степень расчленения, крутизна и экспозиционные различия склонов...
Таксономические единицы (категории) растений: Каждая система классификации состоит из определённых соподчиненных друг другу...
© cyberpedia.su 2017-2024 - Не является автором материалов. Исключительное право сохранено за автором текста.
Если вы не хотите, чтобы данный материал был у нас на сайте, перейдите по ссылке: Нарушение авторских прав. Мы поможем в написании вашей работы!