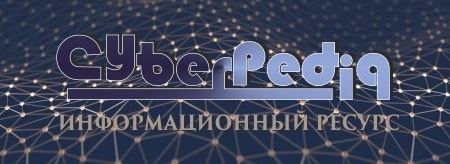
Опора деревянной одностоечной и способы укрепление угловых опор: Опоры ВЛ - конструкции, предназначенные для поддерживания проводов на необходимой высоте над землей, водой...
Типы оградительных сооружений в морском порту: По расположению оградительных сооружений в плане различают волноломы, обе оконечности...
Топ:
Выпускная квалификационная работа: Основная часть ВКР, как правило, состоит из двух-трех глав, каждая из которых, в свою очередь...
Эволюция кровеносной системы позвоночных животных: Биологическая эволюция – необратимый процесс исторического развития живой природы...
Интересное:
Средства для ингаляционного наркоза: Наркоз наступает в результате вдыхания (ингаляции) средств, которое осуществляют или с помощью маски...
Отражение на счетах бухгалтерского учета процесса приобретения: Процесс заготовления представляет систему экономических событий, включающих приобретение организацией у поставщиков сырья...
Влияние предпринимательской среды на эффективное функционирование предприятия: Предпринимательская среда – это совокупность внешних и внутренних факторов, оказывающих влияние на функционирование фирмы...
Дисциплины:
![]() |
![]() |
5.00
из
|
Заказать работу |
|
|
Основные параметры процесса прокатки на оправке.
Одним из основных параметров процесса прокатки является сила прокатки. Зная величину усилия прокатки на рабочие валки стана, можно определять оптимальные режимы, при которых достигается максимальная производительность прокатных станов и обеспечивается безопасная работа всех деталей главной линии стана. Определение величины силы прокатки дает возможность выбора режимов обжатий, типа смазки (см. презентацию) скорости прокатки, температуры прокатки и других условий, позволяющих провести процесс с минимальным расходом энергии и высокой производительностью при заданном качестве готового изделия.
Полное усилие при прокатке в круглом калибре P может быть определено как произведение среднего нормального напряжения p ср и горизонтальной проекции контактной поверхности с калибром рабочего валка F к.
P = p ср F к
При прокатке на короткой и длинной оправках, в связи с различным характером деформации металла в зонах редуцирования и обжатия по стенке трубы, необходимо раздельное определение усилий в каждой из этих зон.
Рисунок 9. Схема прокатки на короткой оправке.
P = p ср.1 F к1+ p ср.2 F к.2,
где p ср.1, F к1 – среднее нормальное напряжение и горизонтальная проекция контактной поверхности в зоне редуцирования -l1,
p ср.2, F к.2 - среднее нормальное напряжение и горизонтальная проекция контактной поверхности в зоне обжатия трубы по стенке - l2.
Среднее обжатие трубы по стенке можно определить аналитически. См. лекции по теории прокатки.
В общем случае также, как и при продольной прокатке формула для определения среднего нормального напряжения имеет вид:
|
p ср = β σт n σ nv n н,
где β = 1 - 1,15 -коэффициент, учитывающий влияние среднего главного напряжения,
σт – предел текучести при статических испытаниях
n σ = n'σ n"σ n"'σ, где n'σ - коэффициент, учитывающий влияние внешнего трения; n"σ - коэффициент, учитывающий влияние внешних зон; n"'σ - коэффициент, учитывающий влияние натяжения или подпора
Произведение σи=σтnv n н определяет истинное сопротивление деформации. Коэффициент nv, учитывающий упрочение при холодной прокатке при горячей можно принять равным единице. При горячей прокатке обычно определяется nv, σs по экспериментальным данным.
Для малоуглеродистой стали nv, σs зависимости от температуры можно воспользоваться графическими зависимостями, полученными еще в 20 веке (следует изменить размерность!):
Для определения нормальных напряжений при прокатке труб в круглых калибрах различными способами известно большое количество формул, из которых следует отметить наиболее распространенные. Среднее нормальное напряжение при прокатке труб на оправке в зоне редуцирования можно определить по формуле В.П.Анисифорова:
p ср= ή KF 2 Т0/ d ср,
где KF - сопротивление деформации при данной температуре,
d ср - средний диаметр трубы в зоне редуцирования,
Т0 - начальная толщина стенки
ή – коэффициент, учитывающий влияние внешних зон:
ή=1+ 0,9 d ср / l р√ t 0 / d ср,
l р - длина зоны редуцирования.
Литература.
1. Радаточный материал-передан на флеш-карте в начале семестра.
2. Машиностроение: энциклопедия: В 40 т. - М.: Машиностроение, 2000. - 780 с.: ил.-ISBN 5-217-02816-5. Том IV -5 Машины и агрегаты металлургического производства.. С 608-640.
3. Колесников А.Г., Яковлев Р.А. Мальцев А.А. Технологическое оборудование прокатного производства. Издательтво МГТУ им.Н.Э.Баумана,2014.- 158 с:илл.
Вопросы к лекциям (войдут во второй модуль).
1. Сортамент труб, выпускаемых на ТПА с автомат-станом и станом тандем.
|
2. Особенности организации технологии на агрегатах с автомат-станом и станом тандем.
3. Нарисовать схему деформации на автомат стане, указав все зоны деформации.
4. Нарисовать схему деформации на автомат стане, указав все силы, действующие на трубу и оправку.
5. Описать технологию производства труб на автомат стане.
6. Описать технологию производства труб на ТПА с автомат станом.
7. Алгоритм расчета основных параметров при прокатке труб.
8. Алгоритм расчета основных параметров при продольной горячей прокатки
9. Дефекты труб при прокатке на автомат стане.
10. Смазки, применяемые при горячей прокатке труб.
11. Какие параметры при расчете силы прокатки следует учитывать в случае горячей прокатки?
12. Надо ли охлаждать рабочий инструмент при горячей прокатки труб? Как?
Лекция. Семинар. ТПА С АВТОМАТ-СТАНОМ (СТАНОМ ТАНДЕМ).
Агрегаты с автомат-станом являются наиболее распространенными при производстве бесшовных труб, что объясняется их высокой маневренностью и универсальностью, а также высокой производительностью. В настоящее время отечественной промышленностью освоено производство труб на ТПА с автоматическим станом из углеродистых, средне- и высоколегированных сталей и сплавов, в том числе и из жаропрочных, коррозионностойких сталей. В большом объеме выпускаются трубы нефтяного сортамента (обсадные, бурильные, насосно-компрессорные), крекинговые, заготовки деталей машиностроения, заготовки для холодного деформирования и др. В состав агрегата входит стан продольной прокатки на короткой оправке (стан Штифеля) трех типоразмеров (малые агрегаты типа 140 для прокатки труб диаметром 40-159 с толщиной стенки 3,5-30 мм, средние типа 220 и 250 мм для производства труб 102-245 с толщиной стенки 45-50 мм, большие типа 350-400 для производства труб диаметром 127-426 с толщиной стенки 4-50 мм.
По составу оборудования используются один или два прошивных стана, одна или две нагревательные печи, редукционно-растяжной или калибровочный стан. В состав оборудования, как правило, также входят два риллинг-стана (обкатные машины).
В агрегатах с автомат станами используется каскадное расположение оборудования, что являлось прогрессивным в конце 19 века, когда этот способ был изобретен (рис.1). Этот принцип позволяет компактно расположить оборудование. В агрегатах со станом тандем в качестве передающего механизма чаще используют рольганги. Хотя длина агрегата становиться больше, потери тепла при транспортировке с одного стана на другой не изменяются за счет увеличения скорости движения заготовки.
|
Рисунок 1. Каскадное расположение оборудования.
Преимущества ТПА с автомат-станом.:
· Высокая маневренность, позволяющая в короткий промежуток времени осуществить переход с одного типоразмера труб на другой.
· Универсальность, обеспечивающая производство труб широкого сортамента, труб из различных марок стали, с разным соотношением диаметра трубы к толщине стенки (с 4-5 до 40-50).
· Удовлетворительная производительность.
· Низкий расходный коэффициент металла.
· Высокая степень автоматизации и механизации производственного процесса.
Технологический процесс в целом аналогичен рассмотренному выше процессу производства труб на агрегате ТПА 30-102 и подробно изложен в учебниках рис. 2). См. раздаточный материал.
Прошивку осуществляют на повышенных углах подачи (до 15 град) и до 12 градусов при двух прошивных станах. С целью получения гильз высокого качества, повышения технологической гибкости и достижения высокой производительности лучше использовать прошивной стан с грибовидными валками (рис.3).
Рисунок 2. Схема прокатки на ТПА с автомат-станом.
а.
б.
Рисунок 3. Схемы двухвалковой прошивки. 1-валок, 2-заготовка, 3-стержень оправки, 4-гильза.
а- стан с грибовидными (коническими) валками,
б- стан с бочковидными валками.
Раскатка гильзы в трубу на автоматическом стане осуществляется в два прохода (Рисунок 4), что часто создает диспропорцию в эксплуатации и технологических возможностях автомат-стана. Решить эту проблему можно за счет использования стана-тандем для продольной прокатки труб на короткой оправке. На этом стане осуществлено разделение проходов на две самостоятельных операции в отдельных клетях с осевой выдачей труб после прокатки. То есть, вместо возвращения заготовки на входную сторону автомат-стана, в агрегате со станом тандем последовательно устанавливается две клети, в которых валки расположены под углом 90 градусов так, чтобы участок заготовки, находящийся в вершине калибра, попал в зону выпусков во второй клети. Тем самым можно значительно повысить пропускную способность агрегата.
|
Рисунок 4. Схема прокатки на современном автомат-стане.
а- прокатка, б- возврат заготовки на входную часть стана.
Записываем…
Гильза подается в валки 2,3 с помощью гидравлического толкателя 1 в автомат-стане и с помощью фрикционных валков – в стане тандем. Перед вторым проходом заготовку кантуют на 90 градусов для того, чтобы выпуски на трубах попадали в вершину калибра при последующей продольной прокатке труб. Стан тандем, в отличие от автомат-стана имеет две клети, что позволяет исключить возврат заготовки перед вторым проходом.
После каждого прохода оправку 4 удаляют со стержня 5, возврат заготовки 8 осуществляется роликами обратной подачи 6,7, которые сводятся, в то время как верхний валок 2 поднимается, пропуская заготовку на входную часть стана. То есть после каждого прохода оправка снимается со стержня вручную или с помощью специального механизма (рис.5), а труба возвращается на входную сторону стана с помощью роликов обратной подачи, расположенных за рабочими валками и вращающимися в направлении, противоположном вращению рабочих валков. Для возврата трубы верхний рабочий валок несколько приподнимается, образуя увеличенный холостой калибр, а нижний ролик обратной подачи, поднимаясь с помощью пневматического цилиндра, прижимает трубу к верхнему ролику и вместе с последним сообщает трубе обратное движение.
Рисунок 5. Схема механизма установки оправки.
1-пневмоцилиндр, 2-корпус, 3-лоток, 4-копир 5-оправка.
В результате труба (благодаря трению роликов о трубу) передается через увеличенный по высоте калибр рабочих валков на переднюю (входную) сторону стана.
Первоначально валки стана-автомата были многоручьевыми (рис.6) с разными калибрами, что делало возможным без перевалки прокатывать трубы разного диаметра. В этом случае передний стол перемещался и устанавливался таким образом, что ось входной стороны совпадала с осью требуемого калибра. Затем стали использовать одноручьевые валки, так как станы в основном использовались для массового производства труб. В настоящее время все чаще возвращаются к первоначальному варианту, что позволяет сделать производство более гибким.
Рисунок 6. Автомат стан старой конструкции с многоручьевыми валками.
Длина выходной стороны автоматического стана определяет наибольшую возможную длину прокатываемых труб и составляет 12-18 м.
|
Риллинг-станы (обкатные станы) предназначены для раскатки выпусков на поверхности трубы, снижения продольной и поперечной разностенности, устранения продольных рисок на внутренней поверхности трубы, при этом обычно увеличивается диаметр трубы и устраняется ее овальность. По конструкции риллинг-станы аналогичны прошивным станам. Классически использовалась двухвалковая схема с бочкообразными валками, затем появились трехвалковые станы. По аналогии с прошивными станами стали использовать грибовидные валки.
Прокатный стан в виде вращающегося расширителя (именуемый в технике просто «расширитель») представляет собой стан для горячей прокатки бесшовных трубных изделий, в котором трубное изделие деформируется между двумя приводными рабочим валками и оправкой.
Оси вращения двух валков расположены наклонно относительно оси прокатки под углом β примерно 60°. Горизонтальная плоскость, содержащая ось валков, расположена на некотором расстоянии от горизонтальной плоскости, проходящей через ось прокатки. В некоторых вариантах расстояния являются равными, в то время как в других вариантах они немного отличаются друг от друга.
Разворот валков обеспечивает поступательное движение винтового типа, так что труба подвергается деформации при движении вперед между валками и оправкой.
Таким образом происходит утонение стенки трубы при увеличении ее диаметра без изменения длины трубы.
Оправка закреплена на стержне, который обычно удерживается с помощью соответствующих направляющих устройств, состоящих из трех элементов и расположенных на выходной стороне, эти устройства постепенно открываются по мере движения трубы. Диаметр оправки должен быть меньше внутреннего диаметра трубы у выхода прокатного стана что приводит к колебаниям стержня и оправки внутри трубы. То есть если в горизонтальной плоскости оправка удерживается за счет действия со стороны двух валков и прокатываемого материала, то в вертикальной плоскости он свободно перемещается в зазоре, существующем между оправкой и внутренним диаметром расширяемой трубы.
Расширяемая труба удерживается в вертикальном направлении с помощью направляющих линеек, которые можно заменить поддерживающими роликами. В контактной области между наконечником и рабочими валками (рис.7) существуют следующие зоны.
Рисунок 7 Схема деформации в стане-расширителе.
- зона А: труба входит в контакт с валками в сужающейся зоне и постепенно приобретает форму овала;
- зона В: труба достигает точки минимального расстояния, именуемой как «узкая часть»;
- зона С: начало зоны расширения, где труба находится в контакте с оправкой и валками, а толщина ее стенки постепенно уменьшается с последующим увеличением диаметра;
- зона D: профили оправки и роликов параллельны, и в этой зоне труба выправляется между ними с постепенным уменьшением овальности (наиболее длинная ось овала находится рядом с вертикалью);
- зона Е: в этой зоне расширяемая труба отделяется от оправки, при этом остаточная овальность должна быть полностью устранена, и труба снова становится круглой.
Фактически, в основном из-за того, что оправка надлежащим образом не удерживается в вертикальной плоскости, влияние выравнивающей зоны D не является полностью эффективным в устранении винтообразных неровностей по толщине стенки расширенной трубы (на профиле трубы могут быть заметны остаточные неровности, например, такие формы, как пропорционально увеличивающиеся треугольники, спирали или пилообразные уступы), поскольку оправка свободно колеблется в вертикальной плоскости.
Отрицательное влияние неидеальной круглой формы расширенного сечения трубы, выходящей из прокатного стана, таким образом, определяется на выходе из зоны Е, в результате чего сечение также может быть овальным, и форма трубы не является идеально ровной.
Известны попытки решить эти проблемы за счет монтажа второй отдельной установки, но фактически, эта известная система является очень громоздкой и очень дорогостоящей.
Точные размеры готовой трубы получают на калибровочных и редукционно-растяжных станах. На трубопрокатных агрегатах старого типа редуцирование производят без натяжения, что приводит к некоторому утолщению стенки трубы, но при этом происходит выравнивание стенки по толщине.
Рисунок 6 - Редукционные трехвалковый и двухвалковый станы.
При редуцировании с натяжением длина труб достигает 50-60 м. Разрезка осуществляется летучими пилами. Для уменьшения обрези в современных агрегатах целесообразно использовать программу оптимизации длин
(необходимо рассчитать длину исходной заготовки так, чтобы после прохождения через весь ТПА от сплошной заготовки до готовой трубы после холодильника, длина последний была кратна длине готовой трубы по ГОСТу или по требованию заказчика).
После охлаждения на цепном холодильнике трубы распределяются по поточным линиям отделки, включающие трубоправильные машины, трубоподрезные станки, линии автоматического контроля качества труб по марке стали, сплошности металла, качеству внутренней поверхности труб, размеров и др. Кроме этого в состав линии трубо-отделки входят станки для разрезки, ремонта, нанесения смазки, упаковки и т.д.
Рассмотрим технологический процесс прокатки труб на ТПА 140. Трубопрокатная установка ТПА 140 предназначена для выпуска горячекатанных труб диаметром от 57 до 136 миллиметров с толщиной стенки от 3,6 до 18 миллиметров, а также труб из нержавеющей стали диаметров от 83 до 121 миллиметра и с толщиной стенки от 5 до 11,5 миллиметров. Самые ходовые марки стали 12Х18Н10Т и 08Х18Н10Т.
ТПА 140 состоит из одной методической перекатной нагревательной печи, прошивного стана, автоматического стана, двух обкатных машин, нагревательной методической печи с шагающим подом, редукционного стана, который также выполняет функцию калибровочного стана, охладительного стола и оборудования для холодной отделки труб. Технологический процесс участка заключается в нескольких операциях: подготовка металла к прокатке, нагрев заготовки, прошивка заготовки в гильзу, раскатка гильзы в трубу, обкатка трубы и редуцирование трубы, применяемое для получения труб малого диаметра и калибровки труб по нужному диаметру. Заготовка, сломанная на гидравлическом прессе, нагревается в методической печи с наклонным ходом (рисунок.7).
Рисунок 7 – Методическая перекатная печь для нагрева круглых заготовок.
Нагретая до заданной температуры заготовка выдается из печи фрикционным выталкивателем. По наклонной решетке заготовка скатывается на промежуточный рольганг. В конце рольганга имеется пневматический зацентровщик, центрующий заготовку в горячем состоянии. Далее оцентрованная заготовка передается сбрасывателем на наклонную решетку, по которой она поступает во вводной желоб прошивного стана. Чтобы избежать сильного биения заднего конца заготовки при прошивке, желоб закрывается специальной крышкой. Это особенно важно при прошивке заготовок большой длинны. Чтобы процесс протекал правильно, ось заготовки, лежащей в приемном желобе, должна совмещаться с осью прошивки. Возможно регулирование желоба по высоте, что необходимо при переходе на прокатку труб другого диаметра. Заготовка задается в валки прошивного стана пневматическим толкателем через вводную воронку, установленную между шпинделями на передней стороне рабочей клети. Толкатель расположен в задней части желоба. Передвигаясь под действием толкателя, заготовка захватывается валками (см. лекцию первичный и вторичный захват заготовки в прошивном стане). Для ограничения предварительной подачи заготовок в воронке установлен убирающий упор. Валки прошивного стана вращаются в одну сторону, сообщая заготовке вращательно-поступательное движение в сторону прокатного стержня с оправкой, установленного на выходе из валков, и заготовка прошивается в гильзу (Рисунок 2).
После прошивки и извлечения из трубы оправки со стержнем при боковой выдаче и открытия механизма стержня оправки при осевой выдаче, прошитая гильза по наклонной решетке перекатывается в приемный желоб автоматического (автомат) стана, который служит для раскатки гильзы в трубу с заданной толщиной стенки. В комплекс механизмов автоматического стана входят: рабочая клеть, главный привод, передний и задний столы, механизм роликов обратной подачи с приводом и вспомогательное оборудование: пневматический сбрасыватель, вталкиватель, клиновое устройство подъема валка.
На вводной стороне обкатного стана установлены перекрыватель, приемные рычаги и вводной рольганг. Перекрыватель расположен над вводным рольгангом и служит для пропуска труб, перекатывающихся из автоматического стана ко второму стану, или для передачи недоката в карман брака. Приемные рычаги, предназначенные для планового укладывания труб на вводной рольганг, закреплены на общем продольном валу, получающем качательное движение от пневматического цилиндра. Труба, скатываясь по наклонной решетке, попадает на вводной приводной рольганг одного из станов, с помощью которого задается в валки. Подача труб в обкатные станы производится поочередно. Конструкция рабочей клети аналогична рабочим клетям прошивного стана. Станина рабочей клети открытого типа; она состоит из корпуса и крышки, скрепляемых откидными болтами на клиньях. Рабочие валки в клети наклонены один к другому и образуют с осью прокатки в вертикальной плоскости постоянный угол подачи от 6 до 8 градусов. Оба валка установлены на четырехрядных роликовых подшипниках и состоят из кованных стальных осей и чугунных съемных бочек, насаженных на ось горячей посадкой. Наклон рабочих валков обеспечивается соответствующим расположением гнезд подшипников в подушках.
После обкатки трубы с обеих машин выдаются выбрасыватели по решеткам на общий отводный рольганг, по которому она транспортируется к методической печи с шагающим подом (рисунок 8) калибровочного стана.
Рисунок 8 - Методическая печь с шагающим подом.
На выходе из печи трубы поступают в калибровочный стан, где они калибруются по наружному диаметру и редуцируются (см. лекцию по редуцированию), если требуется получить трубу меньшего диаметра.
|
|
Опора деревянной одностоечной и способы укрепление угловых опор: Опоры ВЛ - конструкции, предназначенные для поддерживания проводов на необходимой высоте над землей, водой...
Особенности сооружения опор в сложных условиях: Сооружение ВЛ в районах с суровыми климатическими и тяжелыми геологическими условиями...
Механическое удерживание земляных масс: Механическое удерживание земляных масс на склоне обеспечивают контрфорсными сооружениями различных конструкций...
Индивидуальные очистные сооружения: К классу индивидуальных очистных сооружений относят сооружения, пропускная способность которых...
© cyberpedia.su 2017-2024 - Не является автором материалов. Исключительное право сохранено за автором текста.
Если вы не хотите, чтобы данный материал был у нас на сайте, перейдите по ссылке: Нарушение авторских прав. Мы поможем в написании вашей работы!