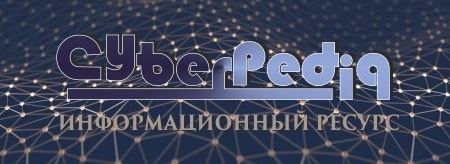
Архитектура электронного правительства: Единая архитектура – это методологический подход при создании системы управления государства, который строится...
Эмиссия газов от очистных сооружений канализации: В последние годы внимание мирового сообщества сосредоточено на экологических проблемах...
Топ:
Марксистская теория происхождения государства: По мнению Маркса и Энгельса, в основе развития общества, происходящих в нем изменений лежит...
Эволюция кровеносной системы позвоночных животных: Биологическая эволюция – необратимый процесс исторического развития живой природы...
Интересное:
Влияние предпринимательской среды на эффективное функционирование предприятия: Предпринимательская среда – это совокупность внешних и внутренних факторов, оказывающих влияние на функционирование фирмы...
Аура как энергетическое поле: многослойную ауру человека можно представить себе подобным...
Отражение на счетах бухгалтерского учета процесса приобретения: Процесс заготовления представляет систему экономических событий, включающих приобретение организацией у поставщиков сырья...
Дисциплины:
![]() |
![]() |
5.00
из
|
Заказать работу |
|
|
16.1. Ремонтно-монтажные работы на трубопроводах производят после их подготовки в соответствии с действующей "Инструкцией по организации и безопасному производству ремонтных работ на предприятиях и в организациях нефтеперерабатывающей и нефтехимической промышленности".
16.2. Переустройство технологических трубопроводов при реконструкции и внедрении рационализаторских предложений можно производить только по рабочим чертежам.
Ремонт трубопроводов выполняют по актам ревизии и отбраковки с приложением выкопировки из схем трубопроводов.
16.3. Трубы, фасонные соединения, фланцы, прокладочные материалы, электроды крепежные и другие детали, применяемые при ремонтно-монтажных работах, по качеству и технической характеристике должны отвечать требованиям государственных стандартов, нормалей машиностроения или специальных технических условий. Взаимозаменяемость отечественных и импортных сталей приведена в табл.55, 56.
Элементы трубопроводов, не имеющие сертификатов или паспортов, можно применять для трубопроводов категории II и ниже только после проверки и испытания в соответствии с государственными стандартами, нормалями и техническими условиями.
Трубы, фланцы и фасонные детали трубопроводов из легированных сталей, независимо от наличия сертификатов и заводской маркировки (Ру, Dy, марка стали), можно применять для технологических трубопроводов только после предварительной проверки марки стали (химическим анализом, стиллоскопированием и т.п.).
Арматуру, не имеющую паспорта и маркировки, можно использовать для трубопроводов категорий IV и V только после ее ревизии и испытания.
Арматуру, имеющую маркировку завода-изготовителя с указанием Ру, Dy и марки материала, но не имеющую паспортов, допускается применять для трубопроводов всех категорий только после ее ревизии, испытания и проверки марки материала.
|
16.4. Все детали перед ремонтно-монтажными работами должны быть осмотрены. Поверхности труб, фасонных деталей, фланцев, прокладок, корпусов и крышек арматуры не должны иметь трещин, раковин, плен, заусенцев и других дефектов, снижающих их прочность и работоспособность.
Маркировка должна соответствовать сертификатам.
Толщину стенки труб и фасонных деталей следует проверять замером на обоих концах в четырех точках. Наружный диаметр, овальность и толщина стенки должны соответствовать требованиям государственных стандартов, нормалей и специальных технических условий.
На поверхности резьбы крепежных деталей не должно быть следов коррозии, вмятин, надрывов и других дефектов, снижающих их прочность.
16.5. Чугунную арматуру с условным проходом более 300 мм, независимо от наличия паспорта, маркировки и срока хранения перед установкой следует подвергать ревизии и гидравлическому испытанию на прочность и плотность.
Ревизию производят в соответствии с КО-1-79.
16.6. Арматуру, предназначенную для установки на трубопроводах категории I, а также всю арматуру (независимо от категории трубопровода) с просроченным гарантийным сроком перед установкой необходимо подвергать гидравлическому испытанию на прочность и плотность в соответствии с ГОСТ 356-80.
16.7. Разметка труб и деталей производится способами, не нарушающими качества последних и обеспечивающими четкое нанесение на заготовках осевых линий, размеров и форм, необходимых при изготовлении деталей и сборке их в узлы.
16.8. Резку труб можно производить любым способом с соблюдением следующих условий:
конец трубы после резки должен быть чистым, без внешних и внутренних заусенцев и грата;
отклонение от перпендикулярности торцового среза к продольной оси не должно превышать для труб с Dy 150 мм - 1 мм, а для труб с Dy > 150 мм - 1,5 мм, которое берется на величину внутреннего диаметра.
|
16.9. Трубы из легированных сталей предпочтительнее резать механическим способом (резцами, фрезами, абразивными дисками и т.п.). Допускаются огневые способы резки с последующей обработкой концов труб в соответствии с указаниями параграфа 18.
16.10. Гибку труб из углеродистой и легированной стали производят в холодном и горячем состоянии различными способами. Способ гибки выбирает изготовитель трубопроводов с условием, что принятый способ обеспечит необходимое качество изготовления.
При этом целесообразно руководствоваться следующими рекомендациями:
гибку в холодном состоянии по шаблону (гибочному сектору) на двух опорах без наполнителя (песок) или с ним можно применять для труб с условным проходом до 125 мм, в качестве оборудования использовать ручные гидравлические трубогибы типа ТГР-2 для труб с условным проходом до 50 мм и с электроприводом типа ТГС-127 для труб с условным проходом до 125 мм;
гибку в холодном состоянии обкаткой роликом без наполнителя можно применять для труб с условным проходом до 32 мм, в качестве оборудования использовать ручные трубогибочные станки или приспособления типа СТГ, станки с электроприводом типа ВМС-23;
гибку в холодном состоянии вращающимся гибочным сектором с внутренним калибрующим дорном (оправкой) и без него можно применять для труб с условным проходом 32-150 мм, в качестве оборудования использовать трубогибочные станки типа ТГМ-38-159, СТГ-3;
гибку с нагревом токами высокой частоты (ТВЧ) - для труб с условным проходом до 500 мм, в качестве оборудования использовать трубогибочные станки с нажимным отклоняющим роликом типа ТГУ-300Б для труб с условным проходом до 250 мм, типа ТГС-530 - 200-500 мм, а также станки с "подсадкой" трубы в процессе гибки;
гибку труб по шаблонам с наполнителем (песком) в холодном состоянии, а также с нагревом в печах и горнах применять только в исключительных случаях, при отсутствии специального трубогибочного оборудования или оснастки.
16.11. Трубы из легированной стали (в том числе из нержавеющей) гнуть с наполнителем в горячем состоянии не рекомендуется.
16.12. Трубы из углеродистых сталей марок Ст 2, Ст 3, 10, 20, можно гнуть различными способами в холодном и горячем состоянии (в том числе с нагревом ТВЧ) без последующей термообработки, если она не предусмотрена проектом.
|
16.13. Трубы толщиной стенки до 20 мм из сталей марок 10Г2, 12Х1МФ и 15ГС гнуть в холодном состоянии без последующей термообработки, если она не предусмотрена проектом.
16.14. Трубы из легированной нержавеющей стали аустенитного класса марок 12Х18Н10Т, 10Х17Н13М2Т, 08Х17Н16МЗТ, 10Х23Н18 следует гнуть при нагреве ТВЧ до 1050-1200 °С и охлаждать за индуктором водой, без последующей термообработки. Гибка труб при этом совмещается с термической обработкой - аустенизацией. При их гибке нельзя допускать понижения температуры нагрева ниже 900 °С, так как могут образоваться трещины из-за уменьшения пластичности металла.
16.15. Трубы из легированной стали мартенситного класса марок 15Х5, 15Х5М, 15Х5ВФ, 12Х5МА, 12Х8ВФ, а также из легированной стали перлитного класса марок 15ХМ, 30ХМА следует гнуть на станках с нагревом ТВЧ и последующей термообработкой, которая должна восстановить свойства материала в пределах требований государственных стандартов или технических условий на поставку этих труб. Рекомендуемые режимы термообработки приведены в табл.39.
16.16. Гибку труб из легированной стали по ГОСТ 9940-81, 9941-81, 550-75 из марок сталей, не указанных в пп.16.13, 16.14, 16.15, следует производить только после предварительной экспериментальной гибки их и отработки режимов нагрева с контролем свойств и структуры металла согнутых труб. При этом свойства металла должны быть не ниже, чем у металла труб до гибки.
16.17. При гибке труб поперечные сварные швы на гнутых участках труб не допускаются.
При гибке прямошовных электросварных и водогазопроводных труб продольные швы следует располагать в зоне наименьших деформаций (на боковых поверхностях гиба).
16.18. Технологию гибки труб устанавливают по производственным инструкциям. Радиусы гиба принимают не менее указанных:
1) при гибке труб в холодном состоянии на специальных станках по размерам, указанным в паспортах этих станков;
2) при гибке труб с нагревом и набивкой песком - не менее 3,5 наружных диаметров трубы;
3) при гибке труб с нагревом ТВЧ - не менее 3,0 наружных диаметров трубы.
|
Примечание. Допускаются радиусы гиба менее указанных в пп.2) и 3), если способ гибки гарантирует сохранение толщины стенки в любом месте гиба, равной не менее 85% номинальной толщины с учетом минусового допуска.
В любом случае радиус гиба должен быть равен не менее двух наружных диаметров трубы.
16.19. При гибке труб допускаются следующие отклонения от геометрических размеров и формы детали:
угловые отклонения осевых линий не должны превышать 2 мм/м при Dy £ 200 мм и 3 мм/м при Dy > 200 мм;
отклонение радиуса гиба (при R £ 4 Dн) не должно превышать значений, указанных ниже:
Dy, мм | 80 | 80-100 | 125 | 150 | 200 |
Допуск на радиус гиба (при R £ 4 Dн), мм | ±5 | ±8 | ±10 | ±12 | ±16 |
16.20. При гибке труб допускаются следующие изменения их сечения в зоне гиба:
овальность сечений в месте гиба, определяемая как отношение разности наибольшего и наименьшего наружных диаметров к номинальному наружному диаметру, не должна превышать 8%;
толщина стенки в любом месте гиба должна быть не менее 85% номинальной толщины с учетом минусового допуска.
16.21. На внутренней стороне гнутых участков допускается плавная волнистость с наибольшей высотой гофр, равной номинальной толщине стенки трубы, но не более 10 мм.
Расстояние между гофрами должно быть не менее трехкратной толщины стенки трубы.
16.22. При гибке труб допускается дополнительная холодная или горячая подгибка их. При этом запрещается горячая подгибка труб из углеродистой стали при температуре ниже 700 и выше 1000 °С, из легированной стали при температуре ниже 800 °С, а из нержавеющей стали типа 12Х18Н10Т - при температуре ниже 900 °С. Термообработка труб из легированной стали после горячей подгибки обязательна.
При подгибке не допускаются трещины, раковины, надрывы, расслоения и растяжки с образованием утонения.
16.23. Расстояние от ближайшего поперечного сварного шва до начала закругления гиба должно быть не меньше наружного диаметра трубы, но не менее 100 мм (исключая случаи крутозагнутых отводов).
16.24. Не разрешается вварка штуцеров, бобышек, дренажей в сварные швы, в гнутые и штампованные детали трубопровода, изготовленные любым способом.
В порядке исключения в гнутые и штампованные детали может быть вварен один штуцер с внутренним диаметром не более 20 мм, если эта вварка предусмотрена проектом.
Допускается вварка штуцеров в отбортованные заглушки, при этом ось штуцера должна совпадать с осью трубопровода, а его условный проход должен быть не более половины условного диаметра заглушки.
16.25. Разделку концов труб и деталей трубопроводов и сборку их под сварку, а также сварку следует производить в соответствии с требованиями, изложенными в параграфе 18.
16.26. При сопряжении двух труб, труб с деталями, деталей между собой угловые отклонения (излом осей) не должны превышать 2,5 мм/м, но не более 8 мм на весь последующий прямой участок трубопровода; линейные отклонения (смещение осей) не должны превышать 3 мм на каждый метр длины трубопровода, но не более 10 мм на всю длину. Совмещение кромок труб и деталей с применением усилий, нагрева или искривления труб при сборке не допускается, за исключением трубопроводов из углеродистой стали марок 10 и 20, для которых в процессе сборки допускается подгонка кромок методом подкатки (подбивка кувалдой) по всему периметру или его части с предварительным подогревом кромок до 850-900 °С. При подкатке должен обеспечиваться плавный переход с углом не более 15° от деформированной кромки к недеформированной части трубы.
|
16.27. При сборке фланцев под сварку с различными деталями (патрубками, фасонными частями, бесфланцевой арматурой, компенсаторами и т.п.) необходимо обеспечивать перпендикулярность и соосность уплотнительной поверхности фланцев к оси смежной детали.
Для трубопроводов категорий III, IV, V допускается отклонение от перпендикулярности уплотнительной поверхности фланца к оси смежной трубы или детали при давлении Ру £ 4 МПа (40 кгс/см2), равное 4 мм/м, а при давлении Ру > 4 МПа (40 кгс/см2) - 2 мм/м.
Смещение осей фланцев, приварных встык, относительно осей смежных с ними деталей не должно превышать половины допуска на смещение кромок сопрягаемых концов.
16.28. При сборке фланцевых соединений труб, деталей трубопроводов и арматуры необходимо обеспечивать параллельность уплотнительных поверхностей фланцев.
16.29. При сборке фланцев с трубами и деталями следует симметрично располагать отверстия под болты и шпильки относительно оси фланцевого соединения. Смещение отверстий двух смежных фланцев не должно превышать половины разности номинальных диаметров отверстия и устанавливаемого болта (или шпильки).
16.30. При сборке труб и деталей с плоскими приварными фланцами расстояние между уплотнительной поверхностью фланца и торцом трубы (недовод трубы) должно приниматься равным толщине трубы плюс 1 мм или выбираться в зависимости от условного прохода трубы:
Dy трубы, мм | 20 | 20-50 | 70-150 | 200 | 225 | 250-300 | 350-450 |
Недовод, мм | 4 | 5 | 8 | 8 | 9 | 10 | 11 |
16.31. При сборке фланцевых соединений трубопроводов необходимо выполнять следующие требования:
шпильки трубопроводов, работающих при температуре свыше 300 °С, перед установкой должны быть прографичены;
размеры прокладок следует принимать согласно ГОСТ 15180-70; при необходимости размеры прокладок можно назначать по нормативным документам проектных организаций;
паронитовые прокладки перед установкой натереть с обеих сторон сухим графитом;
гайки болтов располагать с одной стороны фланцевого соединения;
болты (шпильки) затягивать равномерно с поочередным постепенным завертыванием гаек (крест-накрест), обеспечивающим параллельность фланцев;
длина шпилек и болтов фланцевого соединения должна быть одинаковой и обеспечивать превышение резьбовой части над гайкой не менее чем на один шаг резьбы.
16.32. При ремонте и установке опор необходимо соблюдать следующие требования:
трубы должны плотно, без зазоров и перекосов укладываться на подушки неподвижных опор, хомуты для крепления труб плотно прилегать к трубе и не допускать ее перемещения в неподвижной опоре;
верхние плоскости опор должны быть выверены по уровню, если это требование предусмотрено проектом;
ролики, шарики и катки должны свободно вращаться и не выпадать из гнезд, опорные поверхности прилегать по всей площади соприкосновения без перекосов;
сжатие пружин на опорах и подвесках должно быть обеспечено распорными приспособлениями; пружины при установке следует затягивать в соответствии с указаниями на чертеже;
тяги подвесок трубопроводов, не подверженных тепловым удлинениям (перемещениям), устанавливают отвесно, а подверженных тепловым удлинениям - с наклоном в сторону, обратную перемещению, на половину этого перемещения;
прокладки для обеспечения необходимого уклона трубопровода устанавливают под подошву опоры, установка прокладок между трубой и опорой не допускается;
при креплении опор на стенах или колоннах кронштейны должны прилегать не к штукатурке, а к бетону или кирпичной кладке;
при укладке трубопроводов сварные стыки необходимо располагать на расстоянии не менее 50 мм от опор и подвесок;
при укладке на опоры труб, имеющих продольные сварные швы, необходимо располагать их так, чтобы они были доступны для осмотра.
16.33. При необходимости вварки вставок на трубопроводах их длина должна быть не менее 100 мм, независимо от диаметра трубопровода.
Расстояние от штуцера или другого элемента с угловым (тавровым) швом до начала гиба трубы или поперечного сварного шва должно быть не менее 50 мм для трубопроводов с условным проходом до 100 мм и не менее 100 мм - для трубопроводов больших условных проходов.
Сварка крутоизогнутых отводов между собой допускается без переходного прямого участка.
16.34. Для поперечных сварных соединений, подлежащих ультразвуковому контролю, длина свободного прямого участка трубы (элемента) в каждую сторону от оси шва (до ближайших приварных деталей, начала гиба, оси соседнего поперечного шва и т.д.) должна быть не менее:
100 мм при толщине стенки трубопровода до 15 мм; (5 S + 25) мм - при толщине стенки трубопровода от 15 до 30 мм (значение S в мм).
16.35. Длина участков по обе стороны поперечных стыковых сварных соединений, подлежащих местной термической обработке, должна быть не менее величины, определяемой по формуле: , но не менее 100 мм (значения Dн и S в мм).
16.36. При установке арматуры для определения ее правильного положения на трубопроводе необходимо в каждом случае руководствоваться указаниями, имеющимися в каталогах, технических условиях на арматуру, заводских нормалях или рабочих чертежах.
Направление осей штурвалов определяется проектом.
16.37. Арматура перед приваркой должна быть полностью открыта. Если приварка производится без подкладных колец, закрывать арматуру по окончании приварки можно только после обстукивания сварных швов, промывки и продувки трубопровода.
16.38. Сильфонную арматуру следует устанавливать на трубопроводах после их испытания, промывки и продувки. На время испытания, промывки и продувки вместо сильфонной арматуры необходимо временно устанавливать инвентарные катушки.
16.39. Арматуру необходимо ремонтировать в ремонтно-механических мастерских. Мелкий ремонт арматуры (смена прокладок, перенабивка сальников, замена шпилек, штурвалов и т.п.) можно проводить на месте ее установки.
16.40. Предохранительные клапаны следует ремонтировать в соответствии с указаниями РУПК-78.
16.41. На арматуре технологических трубопроводов должны быть указаны условное давление, марка материала и заводской или инвентарный номер.
16.42. После ремонта арматура подлежит опрессовке на прочность и плотность, причем опрессовку на прочность следует производить при открытом запорном устройстве.
16.43. Значение опрессовочного давления на прочность принимают в соответствии с ГОСТ 356-80 или табл.1, 2 и 3. Испытание на плотность проводят при рабочем давлении. Нормы герметичности арматуры приведены в табл.9-12.
16.44. Качество выполненных работ подтверждается "Удостоверением о качестве ремонта трубопровода" (приложение 2), которое подшивают к паспорту или эксплуатационному журналу трубопровода и хранят с исполнительной документацией на ремонт установки. При сдаче трубопровода из ремонта исполнитель ремонтных работ передает заказчику "Удостоверение" и предъявляет первичные документы, подтверждающие качество выполненных работ и примененных материалов: сертификаты на примененные материалы, сварочные электроды, детали трубопроводов, паспорта на трубопроводную арматуру и компенсаторы, заключение о качестве сварных швов, акты на промывку, продувку и испытание трубопровода.
Первичные документы на ремонт хранятся у владельца трубопровода.
16.45. Результаты ремонта и испытания арматуры оформляют актом (приложение 4). Акт хранят вместе с паспортом или эксплуатационными журналами на трубопроводы.
16.46. На чугунной арматуре не допускается исправление дефектов сваркой.
16.47. На стальной литой арматуре допускается исправление электросваркой:
единичных (до двух) раковин на уплотнительных и опорных поверхностях;
газовых и иных раковин местного характера, давших течь при гидравлическом испытании, местных рыхлостей, трещин и сквозных раковин, занимающих в сумме не более 10% поверхности отливки, при условии, что расстояние между кромками дефектных мест после их разделки не менее 50 мм;
дефектов в стойках и маховиках;
дефектов на опорных поверхностях гнезда под кольцо и корпусах задвижек и клапанов путем наплавки всей опорной поверхности.
16.48. Дефектные места для исправления сваркой должны быть подготовлены механическим способом (вырубкой зубилом, фрезерованием и т.п.), при этом дефектное место зачищают до неповрежденного металла. При удалении трещины ее края предварительно засверливают. Разделка под сварку должна иметь чашеобразную форму с отлогими стенками без резких переходов по краям разделки.
16.49. Если невозможно выполнить подготовку дефектных мест под сварку механическим способом, допускается в виде исключения по согласованию с отделом технического надзора (ОТН) (для сред категорий III, IV и V) удаление дефектов газовой резкой (исключая трещины) арматуры из сталей 15Л, 20Л, а также из стали 25Л при условии содержания углерода не более 0,27%.
16.50. Качество подготовки дефектных мест под сварку должен проверять инженерно-технический работник, ответственный за качество ремонта арматуры.
16.51. Исправление дефектов сваркой следует производить при положительной температуре на спокойном воздухе (без сквозняков).
Наплавленный сварной шов не должен иметь резких переходов к основному металлу; после сварки изделие должно быть зачищено от брызг металла и шлака.
16.52. К сварке допускаются лица, прошедшие испытания на право выполнения ответственных сварочных работ в соответствии с "Правилами аттестации сварщиков", утвержденными Госгортехнадзором СССР.
16.53. Рекомендации по выбору электродов при исправлении дефектов сваркой, о необходимости подогрева изделия до сварки, по термической обработке после исправления дефектов и другие даны в табл.40.
|
|
Общие условия выбора системы дренажа: Система дренажа выбирается в зависимости от характера защищаемого...
Автоматическое растормаживание колес: Тормозные устройства колес предназначены для уменьшения длины пробега и улучшения маневрирования ВС при...
Типы сооружений для обработки осадков: Септиками называются сооружения, в которых одновременно происходят осветление сточной жидкости...
Индивидуальные очистные сооружения: К классу индивидуальных очистных сооружений относят сооружения, пропускная способность которых...
© cyberpedia.su 2017-2024 - Не является автором материалов. Исключительное право сохранено за автором текста.
Если вы не хотите, чтобы данный материал был у нас на сайте, перейдите по ссылке: Нарушение авторских прав. Мы поможем в написании вашей работы!