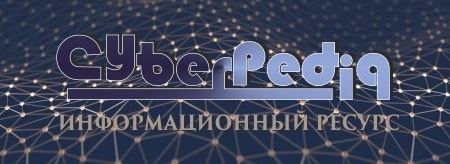
Наброски и зарисовки растений, плодов, цветов: Освоить конструктивное построение структуры дерева через зарисовки отдельных деревьев, группы деревьев...
Таксономические единицы (категории) растений: Каждая система классификации состоит из определённых соподчиненных друг другу...
Топ:
Организация стока поверхностных вод: Наибольшее количество влаги на земном шаре испаряется с поверхности морей и океанов...
Определение места расположения распределительного центра: Фирма реализует продукцию на рынках сбыта и имеет постоянных поставщиков в разных регионах. Увеличение объема продаж...
Интересное:
Подходы к решению темы фильма: Существует три основных типа исторического фильма, имеющих между собой много общего...
Принципы управления денежными потоками: одним из методов контроля за состоянием денежной наличности является...
Инженерная защита территорий, зданий и сооружений от опасных геологических процессов: Изучение оползневых явлений, оценка устойчивости склонов и проектирование противооползневых сооружений — актуальнейшие задачи, стоящие перед отечественными...
Дисциплины:
![]() |
![]() |
5.00
из
|
Заказать работу |
|
|
Термическая обработка стали
Методические указания
для выполнения лабораторных работ
по дисциплине «Материаловедение»
Северодвинск
2019
УДК
Обловацкая Н.С. Закалка стали Методические указания к лабораторной работе по дисциплине «Материаловедение».— Северодвинск: Севмашвтуз.– 2019 г.– 59 с., ил.
Ответственный редактор к.т.н. Фомин Е.В.
Рецензенты:
Худяков М.П. – к.т.н., доцент кафедры «Технология металлов и машиностроения», Севмашвтуз
Боев О.В. – начальник ПТБ РЭЦ, «ФГУП«МП Звёздочка»
Методические указания предназначены для выполнения студентами направлений 15.03.05 и 15.03.01 лабораторной работы «Закалка стали» по дисциплине «Материаловедение».
Пособие предполагает приобретение студентами знаний в области термообработки машиностроительных материалов, а именно, закалки и отпуска, навыков определения механических свойств конструкционных материалов и изучения изменения структуры и свойств материалов после термообработки.
Лицензия на издательскую деятельность Код 221. Серия ИД. №01734 от 11 мая 2000 г.
ISBN ©Севмашвтуз 2017 г.
Содержание
Введение……………………………………………………………………………….......4
Теоретические основы термообработки стали…………………………...……………..5
Оборудование и порядок проведения работы………………………………………....15
Отчет по лабораторной работе………………………………………………………….30
Контрольные вопросы……………………………………………………......................48
Список литературы……………………………………………………………………...58
|
Введение
Дисциплина «Технология конструкционных материалов» входит в учебный план следующих специальностей: 170900, 220300, 140100, 140200, 140400, 141200, 140307(330300), 120500 и предполагает изучение машиностроительных материалов и процессов их обработки.
В методических указаниях к лабораторным работам подробно изложен материал об обозначении конструкционных материалов и области применения, способах определения их механический свойств, а также приведены методики проектирования некоторых заготовок деталей машин.
Рекомендуемая форма контроля выполнения лабораторных работ – защита индивидуальных отчётов по контрольным вопросам с учётом вопросов преподавателей.
Обязательным условием успешного освоения дисциплины является знание соответствующего лекционного материала.
Перед проведением работ студенты должны быть ознакомлены с инструктажем по технике безопасности с индивидуальной подписью в журнале по технике безопасности.
МИКРОСТРУКТУРА СТАЛИ ПОСЛЕ ТЕРМИЧЕСКОЙ ОБРАБОТКИ
Цель работы: изучить влияние различных видов термической обработки на микроструктуру и свойства сталей.
КРАТКИЕ СВЕДЕНИЯ ИЗ ТЕОРИИ
В машиностроении при изготовлении деталей машин термическая обработка проводится обычно два раза. Первая предварительная термическая обработка ведется для заготовок с целью улучшения технологических свойств, а после механической обработки резанием на металлорежущих станках выполняется окончательная упрочняющая термическая обработка деталей машин для обеспечения требуемых по условиям работы деталей в машине механических, эксплуатационных и других свойств.
В основу термической обработки изделий машиностроения положены фазовые превращения первого рода, происходящие в твердом состоянии на этапах нагрева и охлаждения у железоуглеродистых сплавов (рис. 11).
Рис. 11. Интервал температур нагрева на диаграмме состояния
железо - углерод при отжиге и закалке изделий
|
В процессе медленного нагрева в печах при проведении закалки или отжига по достижении температуры, обозначенной tАс1 (для углеродистых сталей 727 °С) происходит фазовое превращение перлита в аустенит:
П (Ф+Ц) ® А.
В доэвтектоидных сталях (Ср < С < Cs) при последующем нагреве в интервале температур tАс1…tАс3 происходит после завершения превращения П ® А еще фазовое превращение феррита в аустенит: Ф ® А.
Важнейшую роль при термической обработке играет этап охлаждения, на котором формируется из аустенита окончательная микроструктура. В зависимости от степени переохлаждения аустенита ниже температуры tА1 (727 °С) происходит одно из трех фазовых превращений:
перлитное: А ® Ф + Ц;
бейнитное: А ® Б;
мартенситное: А ® М.
Интервалы температур указанных фазовых превращений для одной из доэвтектоидных углеродистых сталей показаны на диаграмме изотермического превращения переохлажденного аустенита. (рис. 12). На этой диаграмме горизонтальными пунктирными линиями нанесены температуры фазовых превращений Ас1 и Ас3 в равновесном состоянии, а сплошные линии разделяют диаграмму на области с различными фазами (границу между перлитным и бейнитным превращениями в виде линии диаграмма не показывает). Приведены также нанесенные на диаграмму кривые охлаждения: V1 - с печью (полный отжиг); V2 - на спокойном воздухе (нормализационный отжиг); V3 - в масле (частичная закалка); V4 > Vкр. зак. - в воде (полная закалка).
Рис. 12. Диаграмма изотермического превращения переохлажденного аустенита доэвтектоидной углеродистой стали
При перлитном превращении А ® Ф + Ц с понижением его температуры уменьшаются толщины пластин феррита dф и одной цементита dц (d = dф+ +dН), а твердость смеси Ф + Ц возрастает. Структуры, отличающиеся по величинам d и твердости, получили разное наименование:
перлит (d = 0,6…1,0мкм),
сорбит (d = 0,25…0,30 мкм),
троостит (d = 0,10…0,15 мкм).
Бейнит представляет собой двухфазную структуру из несколько перенасыщенного твердого раствора углерода в a -железе с искаженной кристаллической решеткой ОЦК и дисперсных кристаллов карбидов. Он характеризуется высокой твердостью HRC 38…46 и прочностью.
Мартенсит является перенасыщенным твердым раствором внедрения углерода в искаженной кристаллической решетке железа ОЦК (тетрагональная решетка с отношением с/а > 1). В конструкционных среднеуглеродистых сталях микроструктура представляет собой пакетный мартенсит из параллельных тонких пластин толщиной 0,1…0,2 мкм с большой твердостью HRC > 45.
|
На перлитном превращении основано проведение полного и нормализационного отжига, а на мартенситном – закалки изделий.
После закалки выполняется еще одна термическая обработка - отпуск (нагрев до температур не выше tАс1 (727 0С)). В зависимости от конкретной температуры нагрева образуются различные структуры. При нагреве до 160…200 °С (низкий отпуск) формируется структура отпущенного мартенсита (мартенсит, из которого частично путем диффузии выделился углерод в виде дисперсных пластин особого e-карбида).
Отпуск при температурах 350…470 °С (средний отпуск) приводит к формированию игольчатой структуры троостита отпуска, состоящей из феррита и кристаллов цементита размером 0,5…1,0 мкм. Возрастание температуры отпуска до 550…650 0С (высокий отпуск) обеспечивает получение сферических частиц цементита размером карбидов до 1,5…2 мкм в ферритной основе (сорбит отпуска).
Кроме объемного упрочнения применяются способы поверхностного упрочнения. Широко используется в машиностроении поверхностная закалка способом индукционного нагрева с использованием токов высокой частоты (ТВЧ) в десятки тысяч и более герц. Деталь помещают с некоторым зазором в специальное устройство - индуктор из медных трубок, к которому подают or машинного или лампового генератора ток высокой частоты. Вследствие возникновения в детали электрических вихревых токов с наибольшей плотностью в поверхностном слое происходит нагрев этого слоя выше температур фазовых превращений Ac1 и Асз и образование аустенита.
При последующем быстром охлаждении в поверхностном слое аустенит превращается в мартенсит.
При термической обработке с лазерным нагревом (лазерное термоупрочнение) используются газовые и твердотельные лазерные установки, которые снабжаются системами транспортировки и фокусировки луча лазера, механизмами перемещения изделий по заданному режиму. При воздействии лазерного луча на поверхность происходит поглощение и передача энергии высокой концентрации тонкому поверхностному слою, соответствующий нагрев выше температур Ac1 и Асз, возможно плавление и переход в жидкое состояние тонкого поверхностного слоя. В процессе быстрого охлаждения нагретого объема путем интенсивного теплоотвода холодной массой изделия без применения специальной охлаждающей среды создается скорость охлаждения до 1000 градусов в секунду (Vохл.>>Vкрит. зак.), происходит фазовое превращение в нагретом малом объеме металла аустенита в мартенсит, то есть закалка.
|
Рекомендации по проведению экспериментов
Основные области применения для наиболее часто используемых способов испытания на твёрдость следующие:
1) по Бринеллю – металлические материалы твёрдостью до НВ 450;
2) по Виккерсу – металлические материалы от очень низкой до очень высокой твёрдости, а также для маленьких и тонких образцов;
3) по Роквеллу (шкала С) – стили и сплавы в диапазоне твёрдости HRC 20-67;
4) по Роквеллу (шкала В) – материалы средней твёрдости: низкоуглеродистые стали, латуни, бронзы и др. в диапазоне твёрдости HRB 35-100.
Результаты практического испытания та твёрдость в первую очередь зависят от правильности выбора способа испытания, от надёжности испытательной аппаратуры и соблюдения инструкций по проведению испытания.
Повышению точности и достоверности определяемых значений твёрдости способствует соблюдение следующих указаний:
1. При подготовке к испытанию на твёрдость рекомендуется проводить проверку прибора путём промера эталонных образцов различной твёрдости. Кроме того, следует проверить индентор на пригодность и на плотность посадки.
2. Испытываемая поверхность образца должна иметь металлический блеск и быть обработана таким образом, чтобы можно было точно замерить диаметр, диагональ или глубину отпечатка индентора. Рекомендуется производить обработку таким образцом, чтобы не происходил нагрев образца.
3. Образец следует установить таким образом, чтобы испытываемая плоскость образца была расположена перпендикулярно направлению действия нагрузки.
4. Расстояние центра отпечатка от края образца должно быть, по крайней мере, в 2,5 раза больше среднего диаметра отпечатка. Расстояние между центрами двух соседних отпечатков должно быть равно четырём средним диаметрам отпечатка.
5. При испытаниях методом Роквелла расстояние между центрами двух соседних отпечатков или расстояние центра отпечатка индентора от края образца должно составлять не менее 3 мм
6. На каждом образце твёрдость измеряют не менее чем 3-5 точках и подсчитывают среднее значение.
Произвести измерения твёрдости методом Бринелля образцов из конструкционных углеродистых и легированных марок сталей.
|
При испытаниях по методу Бринелля после снятия нагрузки и удаления шарика замеряются два взаимно перпендикулярных диаметра оставшегося отпечатка. В случае анизотропных материалов величина этих отпечатков может быть различной. Твёрдость по Бринеллю НВ определяется при этом для среднего диаметра с учётом диаметра шарика и величины нагрузки по формуле (18) и таблице твёрдости (табл.6).
Найденные значения твёрдости следует занести в протокол испытания, где, кроме того, указывается использованный способ и условия испытания (табл. 4).
По найденным значениям твёрдости, используя формулы из табл. 2, необходимо: рассчитать условный предел прочности и условный предел текучести, оформить отчёт по лабораторной работе.
Задание №3
Произвести измерения твёрдости методом Роквелла образцов из конструкционных и инструментальных марок сталей.
При испытаниях по Роквеллу после снятия испытательной нагрузки на испытательном приборе ТК-2 считывается значение числа твёрдости по Роквеллу. Найденные значения твёрдости следует занести в протокол испытания (табл. 5). Оформить отчёт по лабораторной работе.
Таблица 4
Протокол испытания на твёрдость методом Бринелля
№ п/п | Марка стали | Химический состав | Способ испытания | Испытательная нагрузка, кгс | Длительность испытания, с | Диаметры отпечатков (первый отпечаток) | НВ для первого отпечатка | … | … | … | … | НВ среднее значение | Примечание (sВ, sТ) | ||||||
d1 | d2 | dСР | … | … | … | … | … | … | |||||||||||
Таблица 5
Протокол испытания на твёрдость методом Роквелла
№ п/п | Марка стали | Химический состав | Способ испытания | Испытательная нагрузка, кгс | Значение твёрдости | Примечание | |||
Первый отпечаток | Второй отпечаток | Третий отпечаток | Среднее значение твёрдости | ||||||
Составление отчёта
Отчёт о лабораторной работе должен включать:
1. Наименование и цель работы.
2. Краткое описание методики проведения экспериментов.
3. Схемы проведения опытов и экспериментальных установок.
4. Расчётные формулы.
5. Таблицы экспериментальных результатов.
6. Выводы по результатам лабораторной работы.
Список литературы
Термическая обработка стали
Методические указания
для выполнения лабораторных работ
по дисциплине «Материаловедение»
Северодвинск
2019
УДК
Обловацкая Н.С. Закалка стали Методические указания к лабораторной работе по дисциплине «Материаловедение».— Северодвинск: Севмашвтуз.– 2019 г.– 59 с., ил.
Ответственный редактор к.т.н. Фомин Е.В.
Рецензенты:
Худяков М.П. – к.т.н., доцент кафедры «Технология металлов и машиностроения», Севмашвтуз
Боев О.В. – начальник ПТБ РЭЦ, «ФГУП«МП Звёздочка»
Методические указания предназначены для выполнения студентами направлений 15.03.05 и 15.03.01 лабораторной работы «Закалка стали» по дисциплине «Материаловедение».
Пособие предполагает приобретение студентами знаний в области термообработки машиностроительных материалов, а именно, закалки и отпуска, навыков определения механических свойств конструкционных материалов и изучения изменения структуры и свойств материалов после термообработки.
Лицензия на издательскую деятельность Код 221. Серия ИД. №01734 от 11 мая 2000 г.
ISBN ©Севмашвтуз 2017 г.
Содержание
Введение……………………………………………………………………………….......4
Теоретические основы термообработки стали…………………………...……………..5
Оборудование и порядок проведения работы………………………………………....15
Отчет по лабораторной работе………………………………………………………….30
Контрольные вопросы……………………………………………………......................48
Список литературы……………………………………………………………………...58
Введение
Дисциплина «Технология конструкционных материалов» входит в учебный план следующих специальностей: 170900, 220300, 140100, 140200, 140400, 141200, 140307(330300), 120500 и предполагает изучение машиностроительных материалов и процессов их обработки.
В методических указаниях к лабораторным работам подробно изложен материал об обозначении конструкционных материалов и области применения, способах определения их механический свойств, а также приведены методики проектирования некоторых заготовок деталей машин.
Рекомендуемая форма контроля выполнения лабораторных работ – защита индивидуальных отчётов по контрольным вопросам с учётом вопросов преподавателей.
Обязательным условием успешного освоения дисциплины является знание соответствующего лекционного материала.
Перед проведением работ студенты должны быть ознакомлены с инструктажем по технике безопасности с индивидуальной подписью в журнале по технике безопасности.
МИКРОСТРУКТУРА СТАЛИ ПОСЛЕ ТЕРМИЧЕСКОЙ ОБРАБОТКИ
Цель работы: изучить влияние различных видов термической обработки на микроструктуру и свойства сталей.
КРАТКИЕ СВЕДЕНИЯ ИЗ ТЕОРИИ
В машиностроении при изготовлении деталей машин термическая обработка проводится обычно два раза. Первая предварительная термическая обработка ведется для заготовок с целью улучшения технологических свойств, а после механической обработки резанием на металлорежущих станках выполняется окончательная упрочняющая термическая обработка деталей машин для обеспечения требуемых по условиям работы деталей в машине механических, эксплуатационных и других свойств.
В основу термической обработки изделий машиностроения положены фазовые превращения первого рода, происходящие в твердом состоянии на этапах нагрева и охлаждения у железоуглеродистых сплавов (рис. 11).
Рис. 11. Интервал температур нагрева на диаграмме состояния
железо - углерод при отжиге и закалке изделий
В процессе медленного нагрева в печах при проведении закалки или отжига по достижении температуры, обозначенной tАс1 (для углеродистых сталей 727 °С) происходит фазовое превращение перлита в аустенит:
П (Ф+Ц) ® А.
В доэвтектоидных сталях (Ср < С < Cs) при последующем нагреве в интервале температур tАс1…tАс3 происходит после завершения превращения П ® А еще фазовое превращение феррита в аустенит: Ф ® А.
Важнейшую роль при термической обработке играет этап охлаждения, на котором формируется из аустенита окончательная микроструктура. В зависимости от степени переохлаждения аустенита ниже температуры tА1 (727 °С) происходит одно из трех фазовых превращений:
перлитное: А ® Ф + Ц;
бейнитное: А ® Б;
мартенситное: А ® М.
Интервалы температур указанных фазовых превращений для одной из доэвтектоидных углеродистых сталей показаны на диаграмме изотермического превращения переохлажденного аустенита. (рис. 12). На этой диаграмме горизонтальными пунктирными линиями нанесены температуры фазовых превращений Ас1 и Ас3 в равновесном состоянии, а сплошные линии разделяют диаграмму на области с различными фазами (границу между перлитным и бейнитным превращениями в виде линии диаграмма не показывает). Приведены также нанесенные на диаграмму кривые охлаждения: V1 - с печью (полный отжиг); V2 - на спокойном воздухе (нормализационный отжиг); V3 - в масле (частичная закалка); V4 > Vкр. зак. - в воде (полная закалка).
Рис. 12. Диаграмма изотермического превращения переохлажденного аустенита доэвтектоидной углеродистой стали
При перлитном превращении А ® Ф + Ц с понижением его температуры уменьшаются толщины пластин феррита dф и одной цементита dц (d = dф+ +dН), а твердость смеси Ф + Ц возрастает. Структуры, отличающиеся по величинам d и твердости, получили разное наименование:
перлит (d = 0,6…1,0мкм),
сорбит (d = 0,25…0,30 мкм),
троостит (d = 0,10…0,15 мкм).
Бейнит представляет собой двухфазную структуру из несколько перенасыщенного твердого раствора углерода в a -железе с искаженной кристаллической решеткой ОЦК и дисперсных кристаллов карбидов. Он характеризуется высокой твердостью HRC 38…46 и прочностью.
Мартенсит является перенасыщенным твердым раствором внедрения углерода в искаженной кристаллической решетке железа ОЦК (тетрагональная решетка с отношением с/а > 1). В конструкционных среднеуглеродистых сталях микроструктура представляет собой пакетный мартенсит из параллельных тонких пластин толщиной 0,1…0,2 мкм с большой твердостью HRC > 45.
На перлитном превращении основано проведение полного и нормализационного отжига, а на мартенситном – закалки изделий.
После закалки выполняется еще одна термическая обработка - отпуск (нагрев до температур не выше tАс1 (727 0С)). В зависимости от конкретной температуры нагрева образуются различные структуры. При нагреве до 160…200 °С (низкий отпуск) формируется структура отпущенного мартенсита (мартенсит, из которого частично путем диффузии выделился углерод в виде дисперсных пластин особого e-карбида).
Отпуск при температурах 350…470 °С (средний отпуск) приводит к формированию игольчатой структуры троостита отпуска, состоящей из феррита и кристаллов цементита размером 0,5…1,0 мкм. Возрастание температуры отпуска до 550…650 0С (высокий отпуск) обеспечивает получение сферических частиц цементита размером карбидов до 1,5…2 мкм в ферритной основе (сорбит отпуска).
Кроме объемного упрочнения применяются способы поверхностного упрочнения. Широко используется в машиностроении поверхностная закалка способом индукционного нагрева с использованием токов высокой частоты (ТВЧ) в десятки тысяч и более герц. Деталь помещают с некоторым зазором в специальное устройство - индуктор из медных трубок, к которому подают or машинного или лампового генератора ток высокой частоты. Вследствие возникновения в детали электрических вихревых токов с наибольшей плотностью в поверхностном слое происходит нагрев этого слоя выше температур фазовых превращений Ac1 и Асз и образование аустенита.
При последующем быстром охлаждении в поверхностном слое аустенит превращается в мартенсит.
При термической обработке с лазерным нагревом (лазерное термоупрочнение) используются газовые и твердотельные лазерные установки, которые снабжаются системами транспортировки и фокусировки луча лазера, механизмами перемещения изделий по заданному режиму. При воздействии лазерного луча на поверхность происходит поглощение и передача энергии высокой концентрации тонкому поверхностному слою, соответствующий нагрев выше температур Ac1 и Асз, возможно плавление и переход в жидкое состояние тонкого поверхностного слоя. В процессе быстрого охлаждения нагретого объема путем интенсивного теплоотвода холодной массой изделия без применения специальной охлаждающей среды создается скорость охлаждения до 1000 градусов в секунду (Vохл.>>Vкрит. зак.), происходит фазовое превращение в нагретом малом объеме металла аустенита в мартенсит, то есть закалка.
|
|
История создания датчика движения: Первый прибор для обнаружения движения был изобретен немецким физиком Генрихом Герцем...
Папиллярные узоры пальцев рук - маркер спортивных способностей: дерматоглифические признаки формируются на 3-5 месяце беременности, не изменяются в течение жизни...
Архитектура электронного правительства: Единая архитектура – это методологический подход при создании системы управления государства, который строится...
Адаптации растений и животных к жизни в горах: Большое значение для жизни организмов в горах имеют степень расчленения, крутизна и экспозиционные различия склонов...
© cyberpedia.su 2017-2024 - Не является автором материалов. Исключительное право сохранено за автором текста.
Если вы не хотите, чтобы данный материал был у нас на сайте, перейдите по ссылке: Нарушение авторских прав. Мы поможем в написании вашей работы!