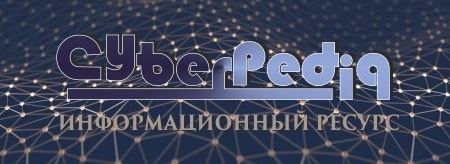
Эмиссия газов от очистных сооружений канализации: В последние годы внимание мирового сообщества сосредоточено на экологических проблемах...
Особенности сооружения опор в сложных условиях: Сооружение ВЛ в районах с суровыми климатическими и тяжелыми геологическими условиями...
Топ:
Теоретическая значимость работы: Описание теоретической значимости (ценности) результатов исследования должно присутствовать во введении...
Особенности труда и отдыха в условиях низких температур: К работам при низких температурах на открытом воздухе и в не отапливаемых помещениях допускаются лица не моложе 18 лет, прошедшие...
Интересное:
Берегоукрепление оползневых склонов: На прибрежных склонах основной причиной развития оползневых процессов является подмыв водами рек естественных склонов...
Как мы говорим и как мы слушаем: общение можно сравнить с огромным зонтиком, под которым скрыто все...
Что нужно делать при лейкемии: Прежде всего, необходимо выяснить, не страдаете ли вы каким-либо душевным недугом...
Дисциплины:
![]() |
![]() |
5.00
из
|
Заказать работу |
|
|
Выбор и обоснование технологической схемы установки первичной переработки нефти (АВТ)
Блок ЭЛОУ
В блоке ЭЛОУ для получения обессоленной нефти с содержанием хлористых солей £1 мг/л при степени обессоливания в каждой ступени 95% устанавливается две ступени обессоливания [13]. Это позволяет довести содержание хлористых солей после первой ступени до 5,95 мг/л, т.к.
119 – 119 × 0,95 = 5,95 мг/л и после второй ступени до ~0,3 мг/л, т.к.
5,95 – 5,95 × 0,95» 0,3 мг/л.
где 119 – содержание хлористых солей в сырой нефти, мг/л (см.таблицу 2.1).
Концентрация хлористых солей в воде, находящейся в сырой нефти:
Концентрация хлористых солей в воде, находящейся в обессоленной нефти:
где 0,0067 – содержание воды в сырой нефти, масс. доля (0,67%);
0,8895 – относительная плотность нефти;
1 – содержание хлористых солей в обессоленной нефти, мг/л;
0,001 – содержание воды в обессоленной нефти, масс. доля (0,1 % масс.).
Для понижении концентрации хлористых солей в воде подают промывную воду.
Расход промывной воды (В) определяется из уравнения:
Для девонской нефти с учетом вышеуказанных концентраций солей в воде это уравнение имеет вид:
,
откуда В=16,85 л/м3 нефти или 1,685 % об. на нефть. Обычно промывную воду подают с избытком 50-200%. В данном случае принимается расход промывной воды 2,0% на нефть.
Для уменьшения неутилизируемых отходов (соленые стоки) свежая промывная вода подается только во вторую ступень обессоливания, а дренажная вода из электродегидраторов второй ступени поступает в электродегидраторы первой ступени через прием сырьевого насоса (3% об.), т.е. применяется циркуляция воды.
Дренажные воды из электродегидраторов сбрасываются в специальную емкость для отстоя, а после отстоя – в канализацию соленых вод и далее на очистные сооружения. Деэмульгатор неионогенного типа подается в количестве 8 г/т нефти в виде 2% водного раствора (400 г/т) на прием сырьевого насоса из специальной емкости. В связи с этим в технологической схеме установки АВТ предусматриваются дополнительные емкости и насосы.
|
Блок колонн
3.2.1 Атмосферный блок
В настоящее время наиболее распространены три вида оформления атмосферного блока:
1. с одной сложной ректификационной колонной
2. с предварительным испарителем
3. с отбензинивающей колонной
Рис. 3.1. Атмосферный блок.
Схему 1 применять нецелесообразно. Она рассчитана на переработку стабилизированных нефтей с содержанием бензиновых фракций до 10%(масс.), а в нашем случае – 13,5%(масс.). Переработка нефтей с высоким содержанием растворенного газа и низкокипящих фракций по этой схеме затруднительна, так как повышается давление на питательном насосе до печи, наблюдается нестабильность температурного режима и давления в основной колонне из-за колебаний состава сырья, невозможность конденсации легких бензиновых фракций, насыщенных газообразными компонентами, при низком давлении в воздушных конденсаторах. Повышение же давления в колонне уменьшает четкость фракционирования.
В схеме 2 одновременная ректификация в одной колонне легких и тяжелых фракций снижает температуру печи, но при высоком содержании бензиновых фракций и растворенных газов атмосферная колонна чрезмерно перегружается по парам, что заставляет увеличивать ее диаметр. Все коррозионно-активные вещества попадают вместе с парами из испарителя в колонну, т.е. испаритель не защищает атмосферную колонну от коррозии.
Схема 3 (рис. 3.1.) самая распространенная в отечественной практике. Она наиболее гибка и работоспособна при значительном изменении содержания бензиновых фракций и растворенных газов. Коррозионно-агрессивные вещества удаляются через верх первой колонны, таким образом, основная колонна защищена от коррозии. Благодаря предварительному удалению бензиновых фракций в змеевиках печи и теплообменниках не создается высокого давления, что позволяет устанавливать более дешевое оборудование без усиления его прочности. Но при работе по этой схеме следует нагревать нефть в печи до более высокой температуры, чем при однократном испарении, вследствие раздельного испарения легких и тяжелых фракций. Кроме того, установка оборудована дополнительной аппаратурой.
|
В отбензинивающей колонне К-1 дистиллятом будут являться растворенные газы С2-С4 и фракция нк-140 0С – нестабильный бензин, который направляем на блок стабилизации в колонну К-3 для извлечения из нестабильного бензина растворенных газов. Это позволяет полностью удалить газы из жидкой фазы уже на входе в колонну К-2 вследствие чего колонна работает при более низком давлении температуре. Уменьшается металлоемкость и стоимость оборудования, затраты на нагрев сырья. Кроме того, в колонне К-1 наряду с газами С2- С4 удаляются солёная вода и коррозионно-активные газы, что благоприятно влияет на сохранность последующего ректификационного и теплообменного оборудования.
В колоннах К-1 и К-2 устанавлаваем клапанные тарелки, которые эффективно работают в широком интервале нагрузок.
В основной атмосферной колонне К-2 дистиллятом будет являться фракция нк-140оС; фракции 140-180 0С, 180-230°С и 230-360°С выводятся боковыми продуктами в жидком виде, снизу колонны выводится мазут (>360°С). Фракцию нк-140оС объединяем с продуктом колонны К-1 и направляем на блок стабилизации. Фракцию 180-230°С можем использовать после гидроочистки как компонент зимнего ДТ или в смеси с фракцией 230-360°С как летнее дизельное топливо – в этом случае фракции объединяем после блока теплообменников. Для четкости разделения фракций применяем стриппинги.
Данная схема, в случае необходимости, позволяет получать керосиновую фракцию (140-180 0С+180-230°С), что положительно сказывается на возможном ассортименте нефтепродуктов.
В низ колонны подается водяной пар в количестве 1% на отбензиненную нефть. Для отвода тепла в основной атмосферной колонне К-2 применяем три циркуляционных (верхнее, среднее и нижнее) орошения, теплоту которых используем для подогрева сырой нефти.
|
3.2.2. Блок стабилизации и чёткой ректификации.
Стабилизации подвергаем бензин из К-1 и фракцию нк-140оС сверху К-2. Согласно рекомендациям [18] блок стабилизации оснащается стабилизатором и несколькими простыми ректификационными колонами числом на единицу меньшим, чем количество выводимых фракций. В нашем случае – одна колонна четкой ректификации, что соответствует заданию. В колонне К-3 производим разделение нестабильного бензина на газ и бензин. Температура в низу стабилизационной колонны поддерживается за счет циркуляции через испаритель нижнего продукта, что позволяет отказаться от печи и снизить расход топлива и выбросы дымовых газов. Стабильный бензин из куба колонны стабилизации отправляется в колонну чёткой ректификации К-4 с целью получения сырья процессов изомеризации (нк-70оС) и каталитического риформинга (70-140оС).
Рис. 3.2. Блок стабилизации бензина.
Из-за отсутствия в нефти растворенного метана и малого количества этана получить сухой газ практически невозможно. Поэтому в емкости орошения получаем сухой газ с содержанием пропана до 7 %, который подаем в качестве топлива в технологические печи установки и рефлюкс.
3.2.3. Вакуумный блок.
На практике существует два основных варианта получения широкой масляной фракции.
1. Тарельчатая ректификационная колонна.
2. Вакуумная колонна с высокоэффективной насадкой.
Рис. 3.3. Вакуумный блок.
За основу принимаем второй вариант, так как насадка является более эффективным контактным устройством и обладает малым гидравлическим сопротивлением. Из-за того, что получать базовые масла из вакуумных дистиллятов нецелесообразно, из колонны выводим два боковых погона и вакуумный газойль. Затемненный продукт используем для подогрева низа колонны в качестве «горячей струи». Теплоту вакуумных дистиллятов используем для подогрева сырой нефти.
Для получения остаточного давления в колонне 4-6 кПа, применяем вакуумсоздающую систему, которая состоит из трёх ступеней паровых эжекторов и поверхностных конденсаторов [18] (одна ступень обеспечивает остаточное давление около 13кПа, две – 7-8кПа).
|
Над вводом сырья и вводом верхнего циркуляционного орошения устанавливаем отбойные тарелки для предотвращения уноса капель жидкости.
Блок теплообменников
Схема теплообмена на установке должна обеспечивать подогрев нефти до температуры не менее 245 ºС. Основой расчета схемы теплообмена является температура теплоносителей и их расход. В таблице 3.1 представлена характеристика теплоносителей, которые получаются на АВТ. Температура теплоносителей принята на основе литературных и практических данных по установкам АВТ на ОАО «Нафтан» и МНПЗ. Расходы – на основании материального баланса (п. 5)
Таблица 3.1. - Характеристика теплоносителей
Теплоноситель | Расход, % масс. на нефть | Начальная температура теплоносителя, °С |
Теплоносители основной атмосферной колонны К-2 | ||
Верхнее циркуляционное орошение К-2 (ВЦО К-2) кратность 4 | 10 | 150 |
Среднее циркуляционное орошение К-2 (СЦО К-2) в районе фракции 180-230оС кратность 3 | 18 | 220 |
Фракция 180-230°С | 5,9 | 200 |
Фракция 230-360°С | 16,13 | 320 |
Нижнее циркуляционное орошение К-2 (НЦО К-2) кратность 2 | 32 | 320 |
Теплоносители вакуумной колонны К-7 | ||
Верхнее циркуляционное орошение К-7 (ВЦО К-7) кратность 15 | 43 | 170 |
Среднее циркуляционное орошение К-7 (СЦО К-7) кратность 2 | 25 | 270 |
Нижнее циркуляционное орошение К-7 (НЦО К-7) кратность 1 | 11 | 330 |
Фр. 360-450оС | 12,5 | 260 |
Фр. 450-550оС | 10,55 | 320 |
Гудрон (>530°С) | 37,54 | 340 |
Расчет схемы теплообмена до электродегидраторов:
1-й поток
Т-101:
∆t н=(150-50)∙5/50=10 ºC
10+10=200С
Т-102:
∆t н=(125-70)∙21,5/50=24 ºC
20+24=44 ºC
Т-103:
∆t н=(145-120)∙18,0/50=9 ºC
44+9=53 ºC
Т-104:
∆t н=(155-100)∙12,5/50=14 ºС
53+14=67 ºС
Т-105:
∆t н=(230-170)∙37,54/50=51 ºС
67+51=118 ºС
2-ой поток
Т-201:
∆t н=(150-50)∙5/50=10 ºC
10+10=200С
Т-202:
∆t н=(125-70)∙21,5/50=24 ºC
20+24=44 ºC
Т-203:
∆t н=(200-65)∙5,9/50=16 ºC
44+16=60 ºC
Т-204:
∆t н=(255-110)∙16,13/50=47 ºС
60+47=107 ºС
Потоки объединяем и с температурой 113,5 оС направляем в электродегидраторы.
Таблица 4.1Состав смеси на входе в емкость орошения
Номер компо-нента по табл.1.2 | Компонент (фракция) | Массовая доля компонента в нефти | Количество компонентов в нефти, кг/ч | Смесь углеводородов на входе в емкость с учетом орошения | |
кг/ч | масс. доля | ||||
3 | С2Н6 | 0,000278 | 99 | 297 | 0,0036 |
6 | С3Н8 | 0,003654 | 1305 | 3915 | 0,0472 |
7 | ∑С4 | 0,006068 | 2167 | 6501 | 0,0784 |
8 | 28-62°С | 0,018 | 6429 | 19287 | 0,2326 |
9 | 62-85°С | 0,016 | 5714 | 17142 | 0,2067 |
10 | 85-105°С | 0,019 | 6786 | 20358 | 0,2455 |
11 | 105-140°С | 0,0144 | 5143 | 15429 | 0,1861 |
Итого: | 0,0774 | 27643 | 82929 | 1,0000 |
Результаты расчета состава и количества газа и бензина в емкости орошения отбензинивающей колонны представлены в таблицах 4.2 – 4.5.
Пpoгpaммa << OIL >>
Pacчeт пpoцecca oднoкpaтнoгo иcпapeния
|
Pacxoд нeфти или фpaкции G= 82929 Kг/чac
Pacxoд вoдянoгo пapa Z= 0 Kг/чac
Плoтнocть ocтaткa P19= 975.2000122070312 Kг/M^3
Дaвлeниe пpи oднoкpaктнoм иcпapeнии P= 250 KПa
Teмпepaтуpa oднoкpaтнoгo иcпapeния T= 30 ^C
Peзультaты pacчeтa:
Maccoвaя дoля oтгoнa пapoв e1= 3.992608981207013E-006
Moльнaя дoля oтгoнa пapoв e= 9.99999883788405E-006
Moлeкуляpнaя мacca иcxoднoй cмecи Mi= 80.63008880615234
Moлeкуляpнaя мacca жидкoй фaзы Ml= 80.63030242919922
Moлeкуляpнaя мacca пapoвoй фaзы Mp= 32.19244384765625
Taблицa 4.2 - Cocтaв жидкoй фaзы |
| ||||||
кoмпoнeнты | мoльн.дoли | мacc.дoли | Kмoль/чac | Kг/чac | |||
Этaн Пpoпaн Бутaн 28–62 62–85 85–105 105–140 | 0.0096746 | 0.0035996 0.0471984 0.0783994 0.2326003 0.2067007 0.2455009 0.1860007 | 9.9504 | 298.5120 3914.0989 6501.5552 19289.2383 17141.4102 20359.0625 15424.7930 | |||
CУMMA | 1.0000 | 1.0000 | 1028.5050 | 82928.6719 | |||
|
| ||||||
Taблицa 4.3 - Cocтaв пapoвoй фaзы | |||||||
кoмпoнeнты | мoльн.дoли | мacc.дoли | Kмoль/чac | Kг/чac | |||
Этaн Пpoпaн Бутaн 28–62 62–85 85–105 105–140 | 0.1050484 | 0.0978942 0.4533812 0.2365882 0.1406191 0.0438330 0.0223423 0.0053422 | 0.0011 | 0.0324 0.1501 0.0783 0.0466 0.0145 0.0074 0.0018 | |||
CУMMA | 0.6638 | 1.0000 | 0.0068 | 0.3311 | |||
|
| ||||||
Taблицa 4.4 - Иcxoднaя cмecь | |||||||
кoмпoнeнты | мoльн.дoли | мacc.дoли | Kмoль/чac | Kг/чac | |||
Этaн Пpoпaн Бутaн 28–62 62–85 85–105 105–140 | 0.0096756 | 0.0036000 0.0472000 0.0784000 0.2326000 0.2067000 0.2455000 0.1860000 | 9.9515 | 298.5444 3914.2490 6501.6338 19289.2852 17141.4238 20359.0703 15424.7939 | |||
CУMMA | 1.000 | 1.000 | 1028.5118 | 82929.0000 | |||
Taблицa 4.5 - Moлeкуляpныe мaccы, дaвлeния нacыщeныx пapoв и кoнcтaнт paвнoвecия кoмпoнeнтoв | |||
кoмпoнeнты | мoлeк. мacca | Pi, KПa | Ki |
Этaн Пpoпaн Бутaн 28–62 62–85 85–105 105–140 | 30.0000 43.0000 57.0000 75.4538 85.7501 94.7538 107.8197 | 2.714525E+03 9.588057E+02 3.012137E+02 6.034317E+01 2.116672E+01 9.083817E+00 2.866811E+00 | 1.085810E+01 3.835223E+00 1.204855E+00 2.413727E-01 8.466689E-02 3.633527E-02 1.146724E-02 |
По формуле (2.3) находим минимальное давление смеси, при котором эта смесь находится в жидком состоянии
р= S рн i xi / £ ре
где р – давление, при котором данная смесь находится в жидком состоянии, кПа;
ре – давление в емкости орошения, кПа;
рн i – давление насыщенных паров i-компонента смеси при температуре в емкости орошения (~30°С), кПа;
xi / – молярная доля i-компонента смеси.
S рн i xi =
99,8кПа < 250кПа.
Следовательно, в емкости орошения получается только жидкая фаза – нестабильный бензин.
Результаты расчёта показывают, что, при выбранных условиях в ёмкости орошения отбензинивающей колонны, пары переходят в жидкую фазу.
И установки в целом
Все расчёты проводятся на основании таблиц приведённых в разделе 1.
5.1 Материальный баланс отбензинивающей колонны К-1
В отбензинивающую колонну приходит обессоленная и обезвоженная нефть в количестве Gн=3000000∙1000/(350∙24)=357143 кг/ч
фракцию газ + н.к.-140°С составляет газ, н.к.-85°С, 85-105°С и 105-140оС (40% масс. от потенциала, 60% остаётся в уходящей нефти), взяты из таблицы 1.2.
Xгаз+н.к.-140°С=1,0+5,3+0,4•3,6=7,74 % масс.
На основании этих данных составляем материальный баланс К-1 и сводим результаты в таблицу 5.1.
Таблица 5.1-Материальный баланс отбензинивающей колонны К-1
Название | %масс. на нефть | %масс. на сырьё | Расход | ||
т/г·10-6 | кг/ч | кг/с | |||
Приход | |||||
Нефть обессоленная и обезвоженная | 100 | 100 | 3 | 357143 | 99,21 |
Расход | |||||
Газ + н.к.-140°С | 7,74 | 7,74 | 0,232 | 27643 | 7,68 |
Нефть отбензиненая | 92,26 | 92,26 | 2,768 | 329500 | 91,53 |
Итого: | 100 | 100 | 3 | 357143 | 99,21 |
5.2 Материальный баланс основной колонны К-2
Фракция н.к.-140оС будет содержать 60% масс. фр. 105-140оС % масс. на нефть.
Так как известно, что при ректификации, из-за нечёткости разделения, в мазуте остаётся 5%(на мазут) дизельной фракции [4,9], то выход мазута на отбензиненную нефть будет:
,
где Xн— потенциальное содержание мазута в нефти, %масс.;
Yн— выход отбензиненной нефти на нефть, масс. доли;
a— содержание светлых в мазуте, масс. доли.
Следовательно выход дизельной фракции 230-360°С уменьшится с 19,0%(масс.) до 16,13% (масс.) на нефть.
На основании этих данных составляем материальный баланс К-2 и сводим результаты в таблицу 5.2.
Таблица 5.2 - Материальный баланс основной колонны К-2
Название | %масс. на нефть | %масс. на сырье | Расход | ||
т/г·10-6 | кг/ч | кг/с | |||
Приход | |||||
Нефть отбензиненная | 92,26 | 100 | 2,768 | 329500 | 91,53 |
Расход | |||||
фр.н.к.-140С | 2,16 | 2,34 | 0,065 | 7714 | 2,14 |
фр.140-180С | 4,6 | 4,99 | 0,138 | 16429 | 4,56 |
фр.180-230С | 5,9 | 6,40 | 0,177 | 21071 | 5,85 |
фр.230-360С | 16,13 | 17,48 | 0,484 | 57607 | 16,01 |
Мазут (>360С) | 63,47 | 68,80 | 1,904 | 226679 | 62,97 |
Итого: | 92,26 | 100 | 2,768 | 329500 | 91,53 |
5.3 Материальный баланс стабилизационной колонны К-3
В колонну К-3 поступает объединённая фракция газ + н.к.-140°С из ёмкости орошения К-1 и фр. н.к.-140оС из К-2 по таблицам 5.1 и 5.2:
Gгаз+н.к.-140°С+ Gн.к.-140°С =27643+7714=35357 кг/ч.
На основании этих данных составляем материальный баланс К-3 и сводим результаты в таблицу 5.3.
Таблица 5.3 - Материальный баланс стабилизационной колонны К-3
Название | %масс. на нефть | %масс. на сырье | Расход | ||
т/г·10-6 | кг/ч | кг/с | |||
Приход | |||||
Газ + н.к.-140°С | 7,74 | 78,18 | 0,232 | 27643 | 7,68 |
фр.н.к.-140С | 2,16 | 21,82 | 0,065 | 7714 | 2,14 |
Итого: | 9,90 | 100 | 0,297 | 35357 | 9,82 |
Расход
Приход
Расход
5.5 Материальный баланс вакуумной колонны К-7
Так как известно, что из-за нечёткости разделения в гудроне остаётся до 10%(на гудрон) масляной фракции [4,9], то выход гудрона на мазут будет:
где Xн— потенциальное содержание гудрона в нефти, %масс.;
Yн— выход мазута на нефть, масс. доли;
a— содержание светлых в гудроне, масс. доли.
Следовательно выход масляной фракции 450-550°С уменьшится с 14,3% до 10,55% на нефть. При вакуумной перегонке неизбежно образуются газы разложения — около 0,02% на мазут. Выход гудрона уменьшится:
Xм=59,17-0,02=59,15% масс. на мазут.
Выход вакуумного газойля 2,87% масс. на нефть (п. 5.2).
На основании этих данных составляем материальный баланс К-7 и сводим результаты в таблицу 5.4:
Таблица 5.4 - Материальный баланс вакуумной колонны К-7
Название | % масс. на нефть | % масс. на сырье | Расход | ||
т/г·10-6 | кг/ч | кг/с | |||
Приход | |||||
Мазут (>360С) | 63,47 | 100 | 1,904 | 226679 | 62,97 |
Расход | |||||
Газы разложения | 0,01 | 0,02 | 0,0004 | 45 | 0,013 |
Вакуумный газойль | 2,87 | 4,52 | 0,0861 | 10250 | 2,847 |
фр.360-450С | 12,50 | 19,69 | 0,3750 | 44643 | 12,403 |
фр.450-550 | 10,55 | 16,62 | 0,3163 | 37670 | 10,465 |
Гудрон (>550С) | 37,54 | 59,15 | 1,1262 | 134071 | 37,242 |
Итого: | 63,47 | 100,00 | 1,904 | 226679 | 62,97 |
Приход
Расход
ΔQ=Qп-Qр=6945,016-6945,018=0,002 кВт.
Дисбаланс тепла компенсируется изменением расхода орошения в процессе эксплуатации колонны
7.4 Расчет диаметра колонны
Диаметр колонны можно определить по уравнению [15]:
D= ,
Где Gп – объемный расход паров, м3/с
Vл - допустимая линейная скорость паров, м/с.
Для расчета диаметра ректификационной колонны необходимо определить объемный расход паров (м3/с) в тех сечениях колонны где они образуются.
Объемный расход паров [15]:
Gп = 22,4∙Т∙0,101∙∑ (Gi/Мi)/(273∙Р)/3600,
где Т – температура системы, К;
Р – давление в системе, МПа;
Gi – расход компонента, кг/ч;
Мi – молекулярная масса компонента кг/кмоль.
Определение объемного расхода паров в точке ввода сырья:
Температура в точке ввода сырья 1400С
Давление в точке ввода сырья 350 кПа
Расход паров 16890 кг/ч
Молекулярная масса паров 88,99 кг/кмоль
Тогда объёмный расход паров:
Gп=22,4∙(140+273)∙0,101∙(16890/(3600∙88,99))/(273∙0,350)=0,516 м3/с,
Определение объемного расхода паров в точке ввода горячей струи:
Температура в точке ввода горячей струи 2000С
Давление в точке ввода горячей струи 356 кПа
Расход паров 10756 кг/ч (табл. 7.3)
Молекулярная масса паров 100,6 кг/кмоль
Тогда объёмный расход паров:
Gп=22,4∙(200+273)∙0,101∙(10756/(3600∙100,6))/(273∙0,356)=0,327 м3/с,
Определение объемного расхода паров в точке вывода паров дистиллята:
Температура в точке вывода паров дистиллята 93,50С
Давление в точке вывода паров дистиллята 341 кПа
Расход паров: фр нк-70оС+орошение 7500+15000=22500 кг/ч (табл. 7.3).
Молекулярная масса паров 76,5 кг/кмоль
Тогда объёмный расход паров:
Gп=22,4∙(93,5+273)∙0,101∙(22500/(3600∙76,5))/(273∙0,341)=0,73 м3/с,
Дальнейшее определение диаметра производим по максимальному расходу паров т.е. Gп=0,73 м3/с.
Допустимая линейная скорость паров [15]:
Vл= (0,305*С*Ö(ρж – ρп)/ ρп)/3600,
где С – коэффициент, зависящий от расстояния между тарелками и условий ректификации; С=300 [15];
ρж , ρп – абсолютная плотность соответственно жидкости и паров, кг/м3.
а) Плотность жидкой фазы
r1515 = 1,03∙М/(44,29+М),
где М – молярная масса паровой фазы, кг/кмоль.
r1515 = 1,03∙76,6/(44,29+76,6)=0,6526
r493,5=r1515-(93,5-15)∙a=0,6526-93∙0,000962= 0,5771
rж(93,5°С)= 577,1 кг/м3
б) Плотность паровой фазы
rп=rо∙Т0∙Р/(Т∙Р0) [15],
где rо – плотность пара при нормальных условиях, кг/м3
rп=76,6∙273∙0,341/(22,4∙381∙0,101)=0,86 кг/м3
Получаем,
Vл= 0,305∙300∙Ö((577,1-0,86) / 0,86) /3600=0,66 м/с
Соответственно диаметр колонны равен:
D =
По ГОСТ 21944-76 принимаем диаметр 1,3 м.
![]() |
7.7 Расчет высоты колонны
Рис. 6. К расчету высоты колонны четкой ректификации.
h1 = ½D=½∙1,3=0,65 м
h2=(nв-1)∙hт=(36-1)∙0,25=8,75 м
h3= hт∙3=0,25∙3=0,75 м
h4=(nн-1)∙ hт=(24-1)∙0,25=5,75 м
h5=1,5 м
Высоту слоя жидкости в нижней части колонны рассчитывают по её запасу на 10 минуты, необходимому для обеспечения нормальной работы насоса. Принимая запас на 600 с, объем кубового остатка с учётом расхода горячей струи составит:
V=(Gк+Gгс)∙600/3600r
Где r - плотность кубового остатка при температуре внизу колонны, кг/м3:
r=(0,7151-0,000884∙(154-15))∙1000=679,7 кг/м3
тогда
V=(24286+5621)∙600/(3600∙679,7)=7,33 м3
Площадь поперечного сечения колонны:
S=pD2/4=0,785∙1,32=1,33 м2
тогда
h6=V/S=7,33/1,33=5,6 м.
Высоту юбки h7 принимают, исходя из практических данных, равной 4 м.
Общая высота колонны составляет:
H=h1+ h2+ h3+ h4+ h5+ h6+ h7 =0,65+8,75+0,75+5,75+1,5+5,6+4=27,00 м
8 Расчет полезной тепловой нагрузки печи атмосферного блока
Печь атмосферного блока для нагрева и частичного испарения отбензиненной нефти подаваемой в колонну К-2 и «горячей струи» для подогрева низа колонны К-1. В расчете используем доли отгона, найденные с помощью ПЭВМ. Количество теплоты Qпол.(кВт), затрачиваемой на нагрев и частичное испарение отбензиненной нефти, определяется по формуле [12]:
Qпол.=Gc∙(е∙Нt2п+(1-е)∙ Нt2ж- Нt1ж)/3600,
где Gс – расход сырья, кг/ч;
е – массовая доля отгона отбензиненной нефти на выходе из печи;
Нt1ж, Нt2ж, Нt2п – энтальпия жидкой и паровой фаз отбензиненной нефти при температурах на входе (t1) и выходе (t2) из печи, кДж/кг.
Зададимся следующими данными для расчета:
- температура нефти на входе в печь- 260 оС;
- температура выхода «горячей струи» в К-1 – 330 оС;
- температура выхода нефти в К-2 – 360 оС;
- давление в колонне К-1 – 350 кПа;
- давление в колонне К-2 – 150 кПа;
- расход «горячей струи» в К-1 (30% на сырье) – 329500∙0,3=98850 кг/ч;
Таблица 8.1. - Для нахождения доли отгона в печи атмосферного блока
Номер компонента | Компоненты, фракции | Массовая доля компонента в нефти, xi | Массовая доля компонента в смеси, xi |
11 | 105-140°С | 0,0216 | 0,0233 |
12 | 140-180°С | 0,046 | 0,0499 |
13 | 180-210°С | 0,039 | 0,0423 |
14 | 210-310°С | 0,138 | 0,1496 |
15 | 310-360°С | 0,072 | 0,078 |
16 | 360-400°С | 0,061 | 0,0661 |
17 | 400-450°С | 0,064 | 0,0694 |
18 | 450-500°С | 0,062 | 0,0672 |
19 | >500°С | 0,419 | 0,4542 |
Итого: | 0,9226 | 1,0000 |
Найденные доли отгона:
Поток в К-1
Peзультaты pacчeтa:
Мaccoвaя дoля oтгoнa пapoв e1=.1237363666296005
Мoльнaя дoля oтгoнa пapoв e=.2630500495433807
Мoлeкуляpнaя мacca иcxoднoй cмecи Mi= 326.7590942382812
Мoлeкуляpнaя мacca жидкoй фaзы Ml= 388.5292358398438
Мoлeкуляpнaя мacca пapoвoй фaзы Mp= 153.7045288085938
- энтальпия паровой фазы отбензиненной нефти на выходе из печи в колонну К-1 (3300С):
r1515=1,03∙М/(44,29+М)=1,03∙154/(44,29+154)=0,7999;
Нп=b∙(4 - r1515) – 308,99=425,15∙(4 – 0,7999) – 308,99=1051,52 кДж/кг;
- энтальпия жидкой фазы отбензиненной нефти на выходе из печи в колонну К-2 (3300С):
r1515=1,03∙М/(44,29+М)=1,03∙339/(44,29+339)=0,9110;
Нж =а/(r1515)0,5=742,00/0,91100,5=777,40 кДж/кг
- энтальпия жидкой фазы отбензиненной нефти на входе в печь при температуре 2600С (температура куба колонны К-1):
=0,9752+0,00270=0,9779
Нж =а/(r1515)0,5=533,75/0,97790,5=539,75 кДж/кг
Qпол. К-1= 98850∙(0,124∙1051,52+(1-0,124)∙777,40-539,75)=26,852∙106 кДж
Поток в К-2
Peзультaты pacчeтa:
Maccoвaя дoля oтгoнa пapoв e1=.3821409940719604
Moльнaя дoля oтгoнa пapoв e=.6407902240753174
Moлeкуляpнaя мacca иcxoднoй cмecи Mi= 326.7590637207031
Moлeкуляpнaя мacca жидкoй фaзы Ml= 562.0350952148438
Moлeкуляpнaя мacca пapoвoй фaзы Mp= 194.8656921386719
- энтальпия паровой фазы отбензиненной нефти на выходе из печи в колонну К-2 (3600С):
r1515=1,03∙М/(44,29+М)=1,03∙195/(44,29+195)=0,8394;
Нп=b∙(4 - r1515) – 308,99=450,76∙(4 – 0,8394) – 308,99=1115,70 кДж/кг
- энтальпия жидкой фазы отбензиненной нефти на выходе из печи в колонну К-2 (3600С):
r1515=1,03∙М/(44,29+М)=1,03∙562/(44,29+562)=0,9548;
Нж =а/(r1515)0,5=827,81/0,95480,5=847,20 кДж/кг
- энтальпия жидкой фазы отбензиненной нефти на входе в печь при температуре 2600С (температура куба колонны К-1):
=0,9752+0,00270=0,9779
Нж =а/(r1515)0,5=533,75/0,97790,5=539,75 кДж/кг
Qпол.К-2= 329500∙(0,382∙1115,70+(1-0,382)∙847,20-539,75)=135,101∙106 кДж
Теплопроизводительность трубчатой печи (Qп, МВт) определяется по уравнению [12]:
Qп= (Qпол.К-1+ Qпол.К-2)/η,
где η – КПД печи, равное 0,85 [12].
Qп=(26,852+135,101)∙106/(3600∙0,85)=52926 кВт
В ТЕПЛООБМЕННИКЕ «НЕФТЬ-ДТ»
Произведём расчёт коэффициента теплопередачи теплообменника Т-204 с помощью программы “Ktepper”. Для этого на основании количества и свойств нефти и ДТ подготовим исходные данные для расчёта.
Расход теплоносителей:
Gн=357143∙0,5=178571,5 кг/ч — расход нефти, теплоноситель 1.
Gдт=357143∙0,1613=57607 кг/ч — расход ДТ через теплообменник по одному потоку, теплоноситель 2;
Средние температуры теплоносителей:
Физические свойства теплоносителей:
– относительные плотности нефти:
- относительные плотности ДТ:
определим кинематические вязкости:
и
— для нефти, тогда можно составить систему уравнений из формулы
и определить A и B.
отсюда .
и
— для ДТ, тогда можно составить систему уравнений из формулы
и определить A и B.
отсюда .
Принимаем кожухотрубчатый теплообменник в соответствии с ГОСТ 15122–79 [13]. Заносим необходимые данные в таблицу 9.1.
таблица 9.1 исходные данные для расчёта коэффициента теплопередачи
Наименование параметра | размерность | значение |
средняя температура ДТ в трубном пространстве | 4. К | 450,5 |
плотность ДТ в трубном пространстве при 288 К | кг/м3 | 863,3 |
плотность ДТ в трубном пространстве при 450,5 К | кг/м3 | 749,7 |
вязкость ДТ в трубном пространстве при 450,5 К | м2/с | 0,00000034 |
средняя температура нефти в межтрубном пространстве | К | 356,5 |
плотность нефти в межтрубном пространстве при 288 К | кг/м3 | 892,8 |
плотность нефти в межтрубном пространстве при 356,5 К | кг/м3 | 842,6 |
вязкость нефти в межтрубном пространстве при 356,5 К | м2/с | 0,00000615 |
внутренний диаметр труб | м | 0,021 |
Наружный диаметр труб | м | 0,025 |
толщину стенки труб | м | 0,002 |
количество труб на поток | шт. | 51 |
площадь проходного сечения в вырезе перегородки | м2 | 0,045 |
площадь проходного сечения между перегородками | м2 | 0,040 |
коэффициент теплопроводности материала труб | вт/м•к | 17,5 |
расход ДТ в трубном пространстве | кг/ч | 57607 |
расход нефти в межтрубном пространстве | кг/ч | 178571,5 |
Результаты расчёта теплообменника по программе “Ktepper” представлены в таблице 9.2.
таблица 9.2 - Результаты расчёта теплообменника
Наименование параметра | размерность | значение |
Скорость потока в трубном пространстве | м/с | 1,2 |
Скорость потока в межтрубном пространстве | м/с | 1,39 |
Коэффициент теплоотдачи в трубном пространстве | Вт/м2•К | 1965 |
Коэффициент теплоотдачи в межтрубном пространстве | Вт/м2•К | 65 |
Коэффициент теплопередачи | Вт/м2•К | 57,3 |
----------------------------------------------------------------
Показатели ! Пространство
!---------------------------------------
! Трубное! Межтрубное
----------------------------------------------------------------
Скорость потока,м/с! 1.208945
|
|
Папиллярные узоры пальцев рук - маркер спортивных способностей: дерматоглифические признаки формируются на 3-5 месяце беременности, не изменяются в течение жизни...
Своеобразие русской архитектуры: Основной материал – дерево – быстрота постройки, но недолговечность и необходимость деления...
История создания датчика движения: Первый прибор для обнаружения движения был изобретен немецким физиком Генрихом Герцем...
Организация стока поверхностных вод: Наибольшее количество влаги на земном шаре испаряется с поверхности морей и океанов (88‰)...
© cyberpedia.su 2017-2024 - Не является автором материалов. Исключительное право сохранено за автором текста.
Если вы не хотите, чтобы данный материал был у нас на сайте, перейдите по ссылке: Нарушение авторских прав. Мы поможем в написании вашей работы!