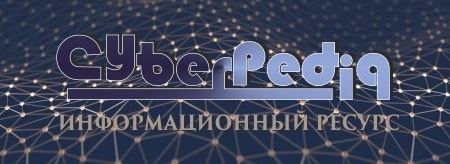
Семя – орган полового размножения и расселения растений: наружи у семян имеется плотный покров – кожура...
Эмиссия газов от очистных сооружений канализации: В последние годы внимание мирового сообщества сосредоточено на экологических проблемах...
Топ:
Эволюция кровеносной системы позвоночных животных: Биологическая эволюция – необратимый процесс исторического развития живой природы...
Генеалогическое древо Султанов Османской империи: Османские правители, вначале, будучи еще бейлербеями Анатолии, женились на дочерях византийских императоров...
Интересное:
Средства для ингаляционного наркоза: Наркоз наступает в результате вдыхания (ингаляции) средств, которое осуществляют или с помощью маски...
Как мы говорим и как мы слушаем: общение можно сравнить с огромным зонтиком, под которым скрыто все...
Принципы управления денежными потоками: одним из методов контроля за состоянием денежной наличности является...
Дисциплины:
![]() |
![]() |
5.00
из
|
Заказать работу |
Схемы печей
Рисунок 1[15]
Печи периодического действия делятся на (рис.1):
а) камерные; б) с выкатным подом; в) элеваторные (с подъемным подом);
г) ямные (со съемным или сдвигаемым сводом); д) шахтные (с раздвижным сводом); е) колпаковые; ж) печи-ванны.
Рисунок 2[15]
Печи непрерывного действия в зависимости от способа транспортирования изделий через рабочую камеру делятся на (рис.2):
а) толкательные;
б) конвейерные;
в) с роликовым подом;
г) туннельные;
д) барабанные;
е) с вращающимся подом (тарельчатым или кольцевым);
ж) с пульсирующим подом.
Существуют и другие способы транспортирования изделий.
Рисунок 3 (56[8])
Огнеупорная кладка нагревательных печей не имеет достаточной прочности, а поэтому из-за температурных расширений и под действием силы тяжести может развалиться. Для придания кладке необходимой прочности применяют металлические каркасы, которые изготовляются трех типов; стоечные, или подвижные, жесткие и каркасы-кожухи. Каркас печи используют также для монтажа рам, механизмов подъема заслонок, топливосжигающих устройств, механизмов для перемещения изделий и т. д.
На рисунке 3(а)приведена конструкция стоечного (подвижного) каркаса. Вертикальные стойки 1 и 3 скрепляются тягами 2, 4 и 6. К боковым стойкам 1 крепятся пятовые балки 5. Для того чтобы при разогреве печи не происходило выпучивания свода вследствие расширения кладки, тяги постепенно ослабляются путем отвинчивания гаек. При остывании печи производится натяжение тяг, чтобы свод не смог провалиться внутрь рабочего пространства.
При частых разогревах и охлаждениях печи неизбежны неточности в регулировании тяг. Часть тяг оказывается натянутой сильнее, а другая — слабее. Поэтому некоторые стойки могут деформироваться. Наклон стоек в ту или иную сторону приводит к изменению формы печи. Поэтому в кузнечных цехах за последнее время получают распространение жесткие каркасы (рис. 3, б).В этом случае стойки внизу закрепляются в фундаменте. При этом часть фундамента у стойки армируется круглым железом 11. Вверху стойки скрепляются с помощью связей 7 и 8, выполненных из уголков или полос. Связи скрепляются со стойками сваркой.
Футеровка
Рисунок 4 (46[15])
На данном рисунке показаны элементы кладки камерной печи. Под 1, боковые 2 и торцовые 4 и 7 стенки выложены вперевязку, а свод кольцами. В задней стенке размешена горелочная амбразура (горелочный камень) 5. Под печи всегда выполняют многослойным.
Рисунок 5 (49[15])
Свод печи наиболее ответственная часть футеровки. Его выполняют обычно арочным (рис.5).
Свод из огнеупорного кирпича 4 имеет тепловую изоляцию 6, удерживаемую от осыпания столбиками 5 из красного кирпича. Горизонтальная составляющая от массы кирпича и термического расширения распирает стенки. Распорное усилие воспринимается пятовым кирпичом 3, подпятовой балкой 2 и стойкой каркаса 1.
Рисунок 6 (1.8.[1])
Конструкции подвесных сводов:
а и в – подвеска на балочках;
б и г – подвеска кирпичей на специальных захватах.
Рисунок 7 (61[8])
Заслонки рабочих окон могут подниматься вручную или с помощью пневматических механизмов. Для подъема заслонок весом до 200—400 кг наибольшее распространение получили ручные секторные механизмы (рис.7, г). Заслонка 7 прикреплена цепью 5 к направляющему сектору 4. С помощью тяги 2 поворачивается рычаг подъема 3. Вес заслонки уравновешивается противовесом (контргрузом) 1. При правильной регулировке положения противовеса на рычаге усилие на тяге 2 не превышает 20 кг. Секторный механизм обеспечивает быстрый и легкий подъем заслонки. Механизмы, изображенные на рисунке а и б, могут применяться для подъема заслонок весом до 800 кг. Для предупреждения падения заслонки при обрыве цепи предусмотрены предохранительные скобы
Для облегчения подъема тяжелых заслонок наиболее часто применяются пневматические цилиндры, работающие от цеховой сети компрессорного воздуха. Конструкция такого подъемного механизма приведена на рисунке в. Пневматический цилиндр 8 устанавливается сбоку печи, где он не может нагреваться излучением из печи или омываться выбивающимися газами. Ход цилиндра обычно равен высоте подъема заслонки. В тол нательных печах путем блокировки пускового клапана подъемного цилиндра с клапаном цилиндра толкателя возможно осуществить автоматический подъем заслонок как на стороне загрузки, так и на стороне выгрузки. Недостатком пневматических подъемников является трудность регулирования высоты подъема заслонки.
Для подъема тяжелых заслонок в некоторых случаях используют электрические лебедки. Преимущество применения электрических лебедок для подъема заслонок состоит в том, что заслонки можно открывать на любую высоту. Кроме того, электрические механизмы удобно применять в поточных линиях с автоматическим включением лебедки при начале движения толкателя. Однако электрические лебедки дороже, чем пневматические подъемники, и, кроме того, в кузнечных цехах быстро выходят из строя. Для подвешивания заслонок применяют цепи, диаметр которых выбирается с 6—10-кратным запасом прочности. Тросы для подвешивания заслонок непригодны, так как при перегреве они теряют свою прочность.
Загрузочные механизмы
Рисунок 8 (2-8[13])
Для перемещения деталей в толкательных печах применяют гидравлические и электромеханические толкатели. Наиболее просты по конструкции гидравлические толкатели, что обусловило их надежиую работу. Они состоят (рис. 8, а) из цилиндра 1, на штоке 3 которого укрепляется траверса 4. Толкающая траверса и часть штока выходят в нагревательную камеру. Для того чтобы масло в цилиндре не перегревалось, на штоке установлена специальная водоохлаждаемая направляющая 2.
Цепные толкатели применяют при больших рабочих ходах. На рис. 8, б показан горизонтальный цепной толкатель. Он состоит из пластинчатой цепи 1, звездочки с валом 2, электромеханического привода 4 и корпуса 3.
Пластинчатые цепи 1 (рис. 8), работающие внутри печной камеры, изготавливают из жароупорной листовой стали марки Х23Н18. Если цепь не подвержена нагреву, то ее изготавливают из обычной стали.
Рисунок 9 (2-9[13])
При больших ходах применяют цепные таскатели. По конструкции они аналогичны вертикальным цепным толкателям, но у таскателей, как правило, две цепи, а вместо толкающей траверсы к цепям крепят специальные штанги (рис. 9, а), В печи на эги штанги наталкивается поддон и транспортируется до упора; после остановки поддона штанги вытаскивают из-под него, а поддон опускается на другую плоскость, по которой и выгружается (обычно выталкивается) из камеры.
На рис. 9, б показана конструкция таскателя с *собачками*. Каретка подается гидроцилиндром в печь, *собачкой* захватывает поддон снизу за ребро и при движении каретки вперед извлекается из печи. Другие «собачки» в это время продвигают ряд поддонов на один шаг.
Рисунок 10(2-10[13])
Конструкция металлической направляющей и способ установки ее в печи показаны на представленном рисунке 10. Направляющие 1 и шпалы 2,3 устанавливаются на опоры 5, между собой направляющие соединяются болтами 4. Шпалы 2 могут заделываться в футеровку 6. Металлические детали отливаются из жароупорной стали. В углеродсодержащей атмосфере до 1000° С применяют стали марки 15Х25Н19С2Л, в окислительной среде — 30Х24Н12СЛ. Средний срок службы таких направляющих составляет 2—3 года.
Рисунок 11(2-11[13])
На данном рисунке показан поддон, применяемый в толкательных печах. Поддоны изготавливают литьем из жароупорных сталей. Они могут иметь размеры 0,5Х0,5; 0,6Х0,4; 0,8Х0,8 м. Поддоны могут иметь боковые стенки при разгрузке деталей навалом или отверстия дл крепления приспособлений.
Если поддоны продвигаются по металлическим рельсам, то в нижней плоскости выполняют пазы для бокового ограничения при движении поддона. Если направляющие из карбида кремния, то пазы не делают. При этом ограничение бокового смещения поддона осуществляется боковыми направляющими из карбида кремния.
Для увеличения истирающей и несущей способности поддон не следует подвергать механической обработке.
Источники энергии
Рисунок 15 (1.14[1])
Горелки, применяемые в термических печах, можно разделить на четыре группы: пламенные, беспламенные, микрофакельные и диффузионные. В пламенных горелках образование смеси газа и воздуха начинается в них, а заканчивается в рабочем пространстве печи. Такие горелки конструируются двухпроводными преимущественно на низкое давление газа и воздуха (до 5000 Па). В зависимости от способа смешения газа с воздухом горелки могут иметь факел различной длины (в том числе регулируемый) и неодинаковой излучающей способности.
На рис.15, а показана горелка типа «труба в трубе». Горелка состоит из сопла 1, тройника 2 и носика 3. Скорость истечения смеси из носика должна быть не менее 5 и не более 40 м/с, а газа из сопла d1 не выше 100 м/с. Факел получается растянутым по длине, при повышении избытка воздуха (а=1,10—1,20) он укорачивается. Преимущества горелки: простота конструкции, малые габариты, возможность использования высоконагретого воздуха и большие пределы регулирования производительности (1:8).
В термических печах широко применяются горелки ГНП (рис. 15, б) конструкции Теплопроекта (девять типоразмеров). Газ поступает по центральной трубке 1 через одно или несколько отверстий, расположенных под углом 45°, в воздушный поток, закручиваемый с помощью лопаток 2. Горелки рассчитаны на сжигание природного газа (при давлении 2400 Па) и воздуха (1600 Па).
Рисунок 16 (1.20[1])
На рисунке приведены конструкции радиационных нагревательных элементов, применяемых в промышленности.
Горизонтальная U-образная радиационная труба (рис.16, а) для увеличения теплопередающей поверхности расширяется в рабочей части 2 от 90 до 170 мм, дымовые газы из нее удаляются с помощью эжектора 1. При подводе всего газа и воздуха в начале трубчатого элемента достаточную равномерность нагрева трубы можно получить, применяя горелку с регулируемой длиной факела.
Вертикальная радиационная труба 2 (рис.16, б), используемая в цементационных печах конструкции ЗИЛ, имеет однопроводную систему с инжекционными горелками 3 и песочным затвором 1, охлаждаемым водой.
На рис.16, в показан вертикальный трубчатый элемент 3 параболической формы, что позволяет заменять его, не разбирая кладки печи. Горелка или форсунка 4 подводится снизу трубы, а продукты сгорания удаляются вверх. Для более полного сгорания топлива и повышения коэффициента теплопередачи трубы заполняют керамическими вставками 2. Чтобы избежать взрывов, ее делают открытой с обоих концов и снабжают электрическим зажигателем 3.
На рис.16, г и д представлены две конструкции нагревательных элементов: Р-образная и U-образная трубы. Первая имеет дополнительную ветвь 2, по которой продукты сгорания возвращаются, проходят рекуператор 1, а часть их захватывается свежей смесью, увеличивая количество циркулирующих газов и снижая их температуру на выходе. Вторая снабжена горелкой 3 с регулируемым факелом, а с другого конца воздушным рекуператором 4; воздух в рекуператор поступает по центральной трубе 5, омывает ее поверхность снаружи и через патрубок 6 подается в горелку, продукты сгорания проходят по кольцевому пространству между рекуператором и стенкой радиационной трубы.
Чаще применяют радиационные трубы диаметром 100—150 мм с толщиной стенки 6—8 мм. Из условий прочности отношение рабочей длины трубы к ее диаметру должно быть равно 10—15.
Пределы регулирования тепловой мощности радиационных труб для камерных печей обычно составляют n =4—5, а для проходных печей с автоматическим регулированием теплового режима n=2—3. При необходимости большого уменьшения расхода топлива приходится часть трубчатых элементов отключать.
Условия сжигания газа в трубах значительно отличаются от обычных. Теория горения, закономерности теплопередачи и механики газов в нагревательных трубчатых элементах пока еще недостаточно разработаны. При рабочей температуре печи 850—950°С и диаметре нагревательного элемента 100—120 мм температура стенки нагревательного элемента составляет 1000— 1100°С, а температурный перепад около 150 °С.
При температурах 950—1100°С удельный теплосъем с поверхности хорошо работающей радиационной трубы равняется 3—5 Вт/см2. Коэффициент теплоотдачи от газов к стенке трубы при температуре газов 1000— 1200°С составляет около 60 Вт/(м2К), а перепад температуры по длине трубы не более 20—25 °С на 1 м.
Иногда требуется оградить электрические нагревательные элементы от агрессивной среды (например, при газовой цементации). В этом случае их размещают в прямых радиационных трубах (рис., е). Спиральные электрические нагреватели 3 изолируют керамическими вставками 4. Ток подводится через изоляционную пробку 2 и вывод 1. Нагреватели по длине трубы делают обычно четыре или шесть оборотов.
Рекуператоры
Рисунок 18(46[11])
В термических печах для подогрева воздуха применяются рекуператоры, в которых дымовые газы и воздух отделяются стенкой. По принципу работы рекуператоры делятся на противоточные (рис. 18,а), прямоточные (рис. 18, б) и перекрестные (рис.18, в), а по конструкции — на трубчатые (рис. 18, г), ребристые (рис. 18, д), игольчатые (рис. 18, е). Для изготовления рекуператоров используют стали, чугуны и керамические материалы. Металлические рекуператоры для нагрева до температуры 350° изготовляют из углеродистой стали, до 500° — из чугуна, до 700° —из жаропрочного чугуна, до 800—850° —из алитированной или жаростойкой стали. Для производства керамических рекуператоров применяют шамот и карборунд. Герметичность керамических рекуператоров увеличивается при использовании фасонных кирпичей и блоков. Кирпичи имеют отверстия, и при установке их друг на друга отверстия образуют каналы, по которым снизу вверх движется воздух.
Дымовые газы пропускают по горизонтальным каналам между кирпичами. Керамические рекуператоры допускают высокую температуру нагрева, особенно карборундовые, огнеупорность которых выше 2000°. Тем не менее металлические рекуператоры имеют преимущества перед керамическими, так как занимают меньшую площадь и объем, обладают меньшей тепловой инерцией и большей теплоотдачей и не имеют неплотностей, характерных для керамических рекуператоров; поэтому наиболее распространены металлические рекуператоры, из которых хорошо себя зарекомендовали игольчатые. Дымовые газы пропускают по горизонтальным каналам между кирпичами. Керамические рекуператоры допускают высокую температуру нагрева особенно карборундовые, огнеупорность которых выше 2000°. Тем не менее металлические рекуператоры имеют преимущества перед керамическими, так как занимают меньшую площадь и объем, обладают меньшей тепловой инерцией и большей теплоотдачей и не имеют неплотностей, характерных| керамических рекуператоров; поэтому наиболее распространены металлиские рекуператоры, из которых хорошо себя зарекомендовали игольчатые.
Они представляют собой чугунные трубы, имеющие игольчатые выступы внутри и снаружи. Нагреваемый воздух пропускается внутри труб, а дымовые газы омывают трубы снаружи. Рекомендуются следующие скорости: для воздуха 4—10 м/сек (обычно не более 5 м/сек), для дымовых, газов 1 — 2 м/сек. Коэффициент теплопередачи игольчатых рекуператоров может достигать 80 ккал/м2час (поверхность в м2 считается для гладкой трубы). При температуре отходящих газов 500—750° нагрев воздуха в игольчатом рекуператоре может достигать 180—350° (обычно 250°).
Недостатками игольчатых рекуператоров являются высокая стоимость изготовления, сложность ремонтов и низкая стойкость при высокой температуре дымовых газов (выше 800°). Средняя стойкость игольчатых рекуператоров 3—5 лет.
В рекуператорах из гладких труб коэффициент теплопередачи равен 15—25 ккал/м2часּград, подогрев воздуха 150—250°, стойкость рекуператора 3—4 года.
Рисунок 19 (69[8])
Трубчатые рекуператоры наиболее просты в изготовлении и удобны в монтаже и обслуживании. Они изготовляются сваркой из газовых труб диаметром от 15 до 75 мм. Для повышения стойкости трубчатого рекуператора желательно применять толстостенные окалиностойкие трубы.
Для кузнечных и термических печей чаще всего применяют двух- или четырехоборотные рекуператоры с горизонтальным расположением труб (рис.19, а). Горизонтальное расположение труб облегчает монтаж и наблюдение за рекуператором. В случае прогара труб можно за короткое время их заварить без демонтажа всего рекуператора. В некоторых случаях трубчатые рекуператоры могут располагаться в боровах печей (рис.19, б). В этом случае трубы могут свободно удлиняться, и поэтому стойкость сварных соединений больше. В рекуператорах этого типа можно подогревать не только воздух, но и газ.
При установке стальных трубчатых рекуператоров над сводами термических печей удается обеспечить подогрев воздуха до 150—200° С при скорости воздуха в трубах рекуператора 6—8 м/сек. При этом срок службы трубчатых рекуператоров составляет примерно 3—4 года. Такие же рекуператоры, установленные над сводами кузнечных толкательных и камерных печей, при подогреве воздуха до 200—250° С, имеют срок службы около года. С повышением температуры подогрева воздуха до 350° С срок службы трубчатого рекуператора снижается до 6 месяцев. Коэффициент теплопередачи трубчатых рекуператоров изменяется от 15 до 25 ккал/м2 час град в зависимости от диаметра труб и их расположения, скорости воздуха и дымовых газов. Аналитическое определение коэффициента теплопередачи затруднено. Поэтому при расчетах трубчатых рекуператоров коэффициент теплопередачи можно принимать в указанных выше пределах. Гидравлические сопротивления трубчатого рекуператора меньше, чем игольчатого, если скорость воздуха не превышает 8—12 м/сек, а дымовых газов 1—3 м/сек. Рисунок 19: а - четырехходовый рекуператор с горизонтальным расположением труб; б – рекуператор с вертикальным расположением труб.
Вакуумные камерные печи
Рисунок 25 (2.9[1])
Ответственные детали часто обрабатываются в вакуумных печах. На рис. 25, а показана схема камерной вакуумной электропечи СНВ-5.10.5/11,5 для нагрева и охлаждения деталей в нейтральном газе или в масле. Она состоит из камер 3,1 и 6, предназначенных соответственно для нагрева садки, ее охлаждения в потоке циркулирующего инертного газа, совершаемого вентилятором 2, и закалки в масле с помощью механизма 5. Корпус печи 4 имеет двойные стенки, охлаждаемые водой, а камера 3 футерована шамотным кирпичом. Максимальная температура печи 1200 °С.
Камерная вакуумная печь СНВ-7,5. 20.7/11,5 для отжига деталей из специальных сплавов изображена на рис. 25, б. Рабочая камера печи 5 выложена из легковесного шамота и находится внутри цилиндрического сварного водоохлаждаемого кожуха 8. Между футеровкой печи и кожухом установлены металлические экраны 7, улучшающие условия нагрева изделий. Загрузочное окно закрывают водоохлаждаемой дверцей 3, уплотненной вакуумной резиной. Дверцу поднимают и опускают с помощью механического привода 4. На боковых стенках и на своде печи располагают спиральные нагревательные элементы 6 из проволоки диаметром 5,5 мм. Детали загружают на поддон 2 специальной тележкой 1. В ряде камерных вакуумных печей футеровку из огнеупорного кирпича заменяют металлическими экранами.
Печи с выдвижным подом
Рисунок 26 (2.10[1])
На рисунке показана типовая конструкция топливной печи с выдвижным подом. Печь имеет горелки 3, расположенные в два ряда по ее высоте. Продукты сгорания отводятся с пода по каналам 4. в боковых стенках в два борова 6, которые под печью соединяются в один. Под 2 выдвигают на роликах 1 с помощью реечного механизма. Для герметизации пода на тележке устанавливают затворы 5. Небольшие печи обычно имеют один ряд нижних горелок. При ширине печи свыше 4 м целесообразно применять подвесной свод (при обычном своде его стрела значительно увеличивается, что снижает равномерность нагрева садки).
Рисунок 27 (2.12[1])
На рисунке дан поперечный разрез печи с разделением пламени. Для ее отопления можно использовать газ или мазут. Топки 5 вынесены на уровень пода 3 выдвижной тележки и отделены от рабочего пространства невысокой решетчатой стенкой 4, выложенной из карборунда или шамотного кирпича. Детали укладываются на подставках. Газы, сгорая, поднимаются вверх под свод печи, а частично проходят через решетчатую разделительную стенку под садку. Продукты сгорания отводятся по каналам, расположенным между топками. Под выдвигается на роликах 1. Герметизация пода и нагревательной камеры осуществляется песочным затвором 2.
Хорошую герметизацию печи дает водяной затвор, выполненный в виде желоба по всему периметру пода. При движении пода в печь желоб с помощью рычажной системы поднимается, закрывая щели между подом и стенками печи. Пары воды из затвора отсасываются по вытяжным каналам.
Рисунок 28 (2.13[1])
В электрических печах с выдвижным подом нагревательные элементы 1 располагаются на боковых стенках, в печах с большой шириной рабочего пространства — на выдвижном поду и заслонке. Ток к нагревателям выдвижного пода подводят по гибкому кабелю. Под выдвигается на роликах 2 с помощью реечного механизма 3. При низких температурах в печах с выдвижным подом принудительную циркуляцию продуктов сгорания или нагретого воздуха осуществляют вентиляторами.
Рисунок 29 (2.14[1])
На рис. 29, а представлена конструкция большой камерной пламенной вентиляторной печи с выдвижным подом для высокого отпуска. Печь имеет двойной свод и двойные боковые стенки, между которыми происходит обратная циркуляция газов. С одной стороны боковых стенок размещают вентиляторы 3, а с другой — ряд щелевых каналов 1, Вентиляторы отсасывают газы из рабочей камеры, направляют их вверх в пространство 2 между двойным сводом. Омывая внутренний свод, газы опускаются у противоположной стенки и через ряд каналов попадают вновь в рабочее пространство. Продукты сгорания поступают параллельными потоками и смешиваются с циркулирующими газами в междусводовом пространстве.
В некоторых печах для получения устойчивого горения топливо сжигают в специальных жаростойких трубах 5(рис. 29,б), вводимых с торца печи над вентиляторами. Трубы имеют ряд отверстий, через которые продукты сгорания поступают в поток циркулирующих газов.
Рисунок 30 (2.16[1])
Вакуумная печь с выдвижным подом представляет собой горизонтальный цилиндрический водоохлаждаемый кожух 4, закрытый с торцов сферическими крышками 2. Внутри кожуха размешается сама печь 3, футерованная легковесным шамотным кирпичом. Под 5 печи и передняя торцевая стенка 1 смонтированы на выдвижной тележке. Нагреватели, выполненные в виде зигзагов из проволоки сплава Х20Н80, размещены на стенках печи, своде и поду. Разъем крышек герметизируется с помощью затвора 8. Механизм 7, смонтированный на тележке 6, вкатывает ее и закрывает крышку загрузочного окна. В зависимости от применяемых насосов в печи обеспечивается вакуум 10-1 Па (бустерными насосами) и 10-3 Па (высоковакуумными). В ряде вакуумных печей вместо футеровки используют экранную изоляцию из листов нержавеющей стали или молибдена. Печи с экранной изоляцией при разогревах имеют меньшие потери тепла (на аккумуляцию кладки).
Элеваторные печи
Рисунок 31 (36[10])
На данном рисунке показана конструкция элеваторной печи. Печь установлена на десяти металлических колоннах 3. Тепловая мощность 650 кBт, рабочая температура 950°C. Футерованная тележка 4 поднимается на платформе гидравлическим подъемником 5. Масса садки изделий, загружаемых в печь, 30 т. Поднятая тележка удерживается в верхнем положении гидравлическими затворами 6. Герметизацию загруженной рабочей камеры печи осуществляют с помощью песочного затвора 7. Для контроля и регулирования температуры в печи установлены две термопары 1. Отжиг на ковкий чугун в такой печи ведут в жароупорных герметичных ящиках или в контролируемой атмосфере. Печь снабжена двумя тележками.
Рисунок 32 (95[3])
Печи динамических потерь работают по следующему принципу. В закрытой теплоизолированной рабочей камере помещена особой формы крыльчатка 2, приводимая во вращение электродвигателем 1 через редуктор. Привод вынесен за пределы рабочей камеры. При помощи плоского экрана и шиберного устройства 3 регулируются потоки воздуха в замкнутом объеме рабочей камеры. Значительная часть энергии привода такой печи превращается при этом в теплоту. Печи этого типа характеризуются равномерностью нагрева всего объема рабочей камеры (2 — 4 град).
Мощность приводного электродвигателя в печах ПАП двадцати разработанных типоразмеров колеблется в пределах от 2 до 150 квт, номинальная температура рабочей камеры — от 140 до 550° С, к. п. д. — от 0,75 до 0,92.
Ряд изготовленных хозяйственным способом печей ПАП нашел применение для нагрева под закалку, отжига и искусственного старения изделий из алюминиевых сплавов, отпуска изделий из титана, закалки деталей из магниевых сплавов, нагрева деталей из нержавеющей стали для снятия напряжении после сварки и в других случаях.
Рисунок 33 (96[3])
Термические печи схема которых представлена на данном рисунке называют воздушно-циркуляционными закалочными агрегатами ЭТА (электротермический агрегат). Такой агрегат представляет собой среднетемпературную циркуляционную механизированную элеваторную электропечь сопротивления 5 для нагрева металла до 500—550°С; на эстакаде 4, сооруженной над сводом печи, установлены вентиляторы 1 и цепная лебедка 2,3 для подъема и опускания садки; печь оборудована откатным подом 8 и расположенным в приямке под электропечью закалочным водяным баком 9.
Нихромовые ленточные электронагреватели подвешены на всех четырех боковых стенках печи.
Благодаря направленной циркуляции печной атмосферы (скорость воздуха в незагруженной рабочей камере достигает 2 м/с) и экранированию электронагревателей, питаемых от трансформатора током пониженного напряжения, перепад температур в рабочем пространстве не превышает ±5 град. Регулирование температуры — автоматическое.
Садка в закалочный бак опускается со скоростью 0,5—0,6 м/сек, при этом происходит интенсивное перемешивание закаливающей жидкости сжатым воздухом.
Мощность печей ЭТА достигает 500 кBт.
Следует отметить низкие технико-экономические показатели электропечей этого вида, в частности это относится к значительным габаритам всей установки, отнесенным к единице полезного рабочего пространства.
Рисунок 34 (12[2])
Печь с передвижной нагревательной камерой предназначена для прочностного и антикоррозионного газового азотирования средне- и крупногабаритных стальных изделий.
Печь состоит из передвижной камеры и двух стендов с муфелями 4. Передвижная камера представляет собой сварной каркас 1 в виде П-образной рамы, опирающейся на колеса. С торцов камеры устанавливаются подъемные дверцы 2. Футеровка стен печи 12 выполнена из легковесного шамота, а в качестве теплоизоляции используется минеральная вата. Нагревательные элементы 14 печи имеют зигзагообразную форму и изготовлены из ленты сплава марки Х20Н80. Стенды имеют сварную конструкцию и зафутерованы легковесным шамотом и диатомитовым кирпичом 5.
Футеровку обшивают листовой сталью марки Х23Н18. К верхнему листу приварены желоба, в которые устанавливают прямоугольный муфель 4, сваренный из стали марки Х23Н18. На каждом стенде установлены по два центробежных вентилятора 15, которые сверху закрыты литой решеткой, служащей для укладки деталей. Аммиак вводится в печь через стенд у каждого вентилятора. Газ отводится через трубки, введенные в стенд и в карманы у четырех углов муфеля. Печь устанавливается на уровне пода. Для обслуживания вентиляторов и системы газоподвода под печью делается приямок. Термообработка производится следующим образом: после окончания цикла нагрева и выдержки на одном стенде деталей камера передвигается с помощью электромеханического привода 10 на другой, подготовленный к работе стенд, на первом стенде происходит охлаждение деталей под муфелем до температуры 200°С при непрерывной подаче аммиака.
Колпаковые печи
Рисунок 35 (2.18[1])
Колпаковые печи состоят из нагревательного колпака 3, который нагревает садку 10, находящуюся под муфелем 9. Садка находится на неподвижном стенде 4 и герметизируется песочным затвором 11. Колпак 3 с помощью ПТО переносится за проушину 9 по очереди на неподвижные стенды 4, количество которых может доходить до 4-х. При накрывании колпаком садки для его центрирования применяются направляющие 6 и направляющие кольца 8. Печь, изображенная на рис.35, а, нагревается газом, сжигаемым в U-образных радиационных трубах 1, расположенных горизонтально на боковых стенках. Продукты сгорания от радиационных труб отводятся сборным трубопроводом 2 в боров.
На рис. 35, б приведена схема разреза колпаковой электрической печи СГЗ-18.38.19/7 с металлическими зигзагообразными нагревателями 2 из нихрома Х20Н80. Внутренний металлический муфель 1 сварен из листов стали Х23Н18.
Рисунок 36 (11[2])
Конструкция печи состоит из переносного футерованного колпака, четырех стационарных стендов и четырех жароупорных муфелей.
Колпак имеет цилиндрическую форму. На стенке колпака укреплены крючки, на которые подвешивают нагреватели, изготовленные из ленты 3x30 мм сплава марки Х20Н80.
Муфель — двойной газонепроницаемый сваривается из листовой стали Х23Н18. В муфель вводится защитный газ, состоящий из 0,5% С02, 2% СО, 2% Н2 и остальное - N2. Расход защитного газа 2,5 м3/ч. Стенд служит для опоры садки и состоит из каркаса, опорных колец, направляющего аппарата для защитного газа и вентилятора. На стенде имеются приспособления для подвода и отвода газа, а также устанавливают термопары, с помощью которых температура регулируется автоматически. Рулоны стальной ленты укладывают на подставку стенда. Для лучшего нагрева и циркуляции атмосферы между рулонами прокладываются специальные кольца. После загрузки на стенд все уложенные рулоны с кольцами закрываются муфелем, входящим внизу в песочный затвор.
Шахтные печи
Рисунок 37 (2.24[1])
На рисунке приведены конструкции малых низкотемпературных вертикальных печей с принудительной циркуляцией атмосферы. Такие печи широко применяют для отпуска стальных изделий и нагрева под закалку небольших деталей из алюминиевых сплавов. Вертикальная циркуляционная печь, отапливаемая газом или жидким топливом (рис. 37, а), имеет установленный на дне печи вентилятор 2 с электродвигателем 3. Детали загружают сверху в корзину 1 с дырчатым дном, которую помещают внутри металлического цилиндра со сплошными боковыми стенками. Газ или жидкое топливо сжигают в специальной кольцевой камере 4 с тангенциально расположенными горелками или форсунками. Продукты сгорания, выходя из камеры, попадают в общий поток циркулирующих газов.
В вертикальных печах типа с электрическим нагревом до 700 °С (рис. 37, б) вентилятор 1 размещают в крышке печи. Дли загрузки деталей крышку поднимают рычагом 2 и отводят в сторону, печь при этом автоматически выключается. В больших печах подъем и поворот крышки осуществляются электродвигателем через червячный редуктор или гидравлическим цилиндром.
На рис. 37, в, г показаны схемы малых вертикальных печей типа «Циклон» с газовым и электрическим нагревом. Газовая печь имеет три отделения: рабочую камеру 1 (обычно цилиндрической формы); камеру 4 для размещения вентилятора и топочную камеру 5 с верхней горелкой. Избыточные газы отводятся по трубе 3. Вентилятор засасывает газы через боковые центральные отверстия и по распределительной коробке 2 гонит их в рабочее пространство 1. Потери тепла компенсируются подводом горячих газов из камеры 5. При электрическом нагреве (рис. 37г) вентилятор 3 устанавливают внизу камеры 2, а над ним размещают калорифер 1 с нагревательными элементами.
Рисунок 38 (4[14])
На рисунке показан общий вид электропечи СШЗ-6.6/7М1, предназначенной для высокого и низкого отпуска стальных изделий, термообработки цветных металлов и сплавов в защитной атмосфере. Корзина 4 ставится на подставку 10. Газ подводится через газопровод, который обеспечивает регулирование и контроль атмосферы в печи. В целях безопасности при подъеме крышки 6 и прекращении подачи воды для охлаждения вентилятора, с помощью системы 9 нагреватели 3 и вентилятор 8 автоматически отключаются. Печь представляет собой футерованный каркас 1, 2.
Техническая характеристика: установленная мощность 37,2 кВт, рабочая температура 700°С, время разогрева до номинальной температуры 2,5 ч, масса садки 600 кг; размеры рабочего пространства: диаметр 600 мм, высота 600 мм, масса электропечи 2400 кг.
Рисунок 39 (7[14])
В печах серии СШЦ-4.9/10,5 вентилятор 1 устанавливают сбоку. Отработанный газ снизу отсасывается вентилятором и смешивается со свежим. Печь состоит из цилиндрической нагревательной камеры с футеровкой 5, на которой кренятся зигзагообразные нагреватели 4. Камера закрывается крышкой 6, подъем которой осуществляется с помощью механизма 7. Садка загружается в корзины 3. Рядом с печью располагают колодец для охлаждения — стальной цилиндр с двойными стенками, между которыми пропускается проточная вода. Крышка колодца имеет песочный затвор. В колодец пропускается от печи отработанный газ для предупреждения окисления. Охлаждение деталей ведется в колодце до температуры 500—550°С, а затем на воздухе. Печи и колодцы обслуживает электротельфер.
Рисунок 40(22[2])
Модернизированная печь типа ПН-31Ас принудительной циркуляцией атмосферы предназначена для отпуска стальных деталей и для термической обработки деталей из цветных и легких сплавов. Кожух печи 1 сварен из листовой и профилированной стали. Сверху кожух накрыт плитой, в которой имеется кольцевой карман песочного затвора 5. Футеровка печи состоит из диатомитового кирпича и асбовермикулитовых плит. Под печи для прочности выложен из шамотного легковесного кирпича. Нагреватели 6 печи выполнены в виде спиралей из проволоки диаметром 5 мм из сплава марки Х15Н60. Нагреватели подвешивают на специальных кронштейнах вдоль боковой стенки. В пролетах между кронштейнами вся поверхность нагревателей обдувается воздухом. В рабочее пространство печи на литое основание устанавливают жароупорную корзину 4 с решетчатым дном и ушками для подъема. Для того чтобы при загрузке и выгрузке корзины не было повреждений нагревателей, последние защищены специальным ограждением. Крышка 2 печи теплоизолирована асбовермикулитовыми плитами. В нижней части крышки имеется нож песочного затвора 5. Подъем крышки осуществляется с помощью гидравлического устройства; отвод в сторону ручной. На крышке установлен вентилятор 3 для создания замкнутой принудительной циркуляции атмосферы. Крыльчатка вентилятора центробежного типа.
Рисунок 41(15[2])
Печь СШЗ-4.8/10 имеет сварной кожух 1, в который заключена огнеупорная и теплоизоляционная кладка 2. Футеровка печи состоит из легковесного шамотного кирпича, ультралегковесного и минераловатных плит. Рабочее пространство печи имеет размеры: диаметр 400 мм, высота 800 мм. Подъем и опускание крышки 4 печи механизированы. При опускании крышки ее наружная выступающая часть заходит в песочный затвор и тем самым осуществляет герметизацию печи.
Особенностью печи данного типа является использование в рабочем пространстве печи контролир
Историки об Елизавете Петровне: Елизавета попала между двумя встречными культурными течениями, воспитывалась среди новых европейских веяний и преданий...
Индивидуальные очистные сооружения: К классу индивидуальных очистных сооружений относят сооружения, пропускная способность которых...
Организация стока поверхностных вод: Наибольшее количество влаги на земном шаре испаряется с поверхности морей и океанов (88‰)...
История развития пистолетов-пулеметов: Предпосылкой для возникновения пистолетов-пулеметов послужила давняя тенденция тяготения винтовок...
© cyberpedia.su 2017-2024 - Не является автором материалов. Исключительное право сохранено за автором текста.
Если вы не хотите, чтобы данный материал был у нас на сайте, перейдите по ссылке: Нарушение авторских прав. Мы поможем в написании вашей работы!