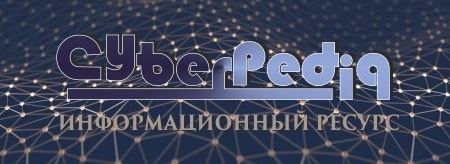
Общие условия выбора системы дренажа: Система дренажа выбирается в зависимости от характера защищаемого...
История развития хранилищ для нефти: Первые склады нефти появились в XVII веке. Они представляли собой землянные ямы-амбара глубиной 4…5 м...
Топ:
Когда производится ограждение поезда, остановившегося на перегоне: Во всех случаях немедленно должно быть ограждено место препятствия для движения поездов на смежном пути двухпутного...
Основы обеспечения единства измерений: Обеспечение единства измерений - деятельность метрологических служб, направленная на достижение...
Оценка эффективности инструментов коммуникационной политики: Внешние коммуникации - обмен информацией между организацией и её внешней средой...
Интересное:
Отражение на счетах бухгалтерского учета процесса приобретения: Процесс заготовления представляет систему экономических событий, включающих приобретение организацией у поставщиков сырья...
Влияние предпринимательской среды на эффективное функционирование предприятия: Предпринимательская среда – это совокупность внешних и внутренних факторов, оказывающих влияние на функционирование фирмы...
Средства для ингаляционного наркоза: Наркоз наступает в результате вдыхания (ингаляции) средств, которое осуществляют или с помощью маски...
Дисциплины:
![]() |
![]() |
5.00
из
|
Заказать работу |
|
|
Курсовая работа
по дисциплине: «Металлургия»
на тему:
«ВЗВЕШАННАЯ ПЛАВКА НИКЕЛЕВОГО КОНЦЕНТРАТА В ПЕЧИ ВЗВЕШАННОЙ ПЛАВКИ»
Выполнил: Бельтюков С.Н.
Проверил: Рогова Л.И.
Группа: Экм-99-У ВО Подпись: _______________
Шифр: 060800 Дата проверки:
Дата выполнения
Норильск, 2000г.
СОДЕРЖАНИЕ
1. Выбор технологии производства…………………………2
2. Описание основного агрегата……………………………..3
3. Физико-химические основы процесса……………………5
4. Технико-экономические показатели……………………..11
5. Металлургический расчет…………………………………12
Библиографический список
1. ВЫБОР ТЕХНОЛОГИИ ПРОИЗВОДСТВА
Плавка во взвешенном состоянии на подогретом дутье была осуществлена в промышленном масштабе финской фирмы «Оутокумпу» на заводе «Харьявалта». В первоначальном варианте для плавки применяли воздушное дутье, подогретое до 400—500 °С. Начиная с конца 60-х годов, этот процесс по лицензии фирмы «Оутокумпу» стали широко применять на металлургических заводах многих стран. В настоящее время он внедрен более чем на 30 предприятиях для переработки медных, никелевых и пиритных концентратов, в т.ч. на Надеждинском металлургическом заводе. Финскую плавку на сегодня можно считать самым распространенным в промышленности и наиболее технологически и аппаратурно отработанным автогенным процессом плавки сульфидных концентратов.
Особенностями взвешенной плавки являются:
- высокая производительность (удельный проплав 10-15 т/м2 в сутки);
- низкий расход топлива - процесс плавки сульфидного концентрата протекает в режиме, близком к автогенному;
- возможность полного автоматического управления процессом плавки с помощью системы "Проскон-103'';
|
- возможность получения штейна требуемого состава;
- утилизация серы из высококонцентрированных серных газов.
Конструкция ПВП и комплекс других технических решений обеспечивают получение пара энергетических параметров и высокую степень утилизации серы из отходящих газов, что резко снижает выброс двуокиси серы в окружающую среду и значительно улучшают условия труда обслуживающего персонала.
В плавильном цехе НМЗ имеется две печи взвешенной плавки одинаковой конструкции для плавки медного и никелевых концентратов.
Передел взвешенной плавки - структурное подразделение плавильного цеха HMЗ.
2. ОПИСАНИЕ ОСНОВНОГО АГРЕГАТА
Конструкция печи для плавки во взвешенном состоянии на подогретом дутье достаточно сложна — она сочетает в себе две вертикальные шахты (реакционную и газоход-аптейк) и горизонтальную камеру-отстойник.
Тонкоизмельченная шихта, предварительно высушенная до содержания влаги менее 0,2%, подается по системе ленточных конвейеров и пневмотранспорта в бункер шихты. Из бункера шихта двумя скребковыми транспортерами "Редлер" подается через свод реакционной камеры с помощью четырех специальных горелок. Основное назначение горелки — приготовление и подготовка шихтововоздушной смеси для ускорения процесса горения сульфидов. Перемешивание шихты с дутьем достигается разбиванием струи шихты о конус-рассекатель и подачей дутья через воздушный патрубок и распределительную решетку.
|
Схема горелки печи завода
1 — дутье; 2 — шихтовая воронка; 3 — загрузочный патрубок;
4 — воздушный патрубок; 5 — конус-рассекатель;
6 — распределительная решетка; 7 — диффузор
Вся печь взвешенной плавки выполнена в виде кладки из магнезитового кирпича. Футеровка реакционной шахты и аптейка заключена в металлические кожухи из листовой стали. В кладку всех элементов печи заложено большое количество водоохлаждаемых
|
Печь для плавки во взвешенном состоянии
1 — горелка; 2 — реакционная камера; 3 — отстойная ванна; 4 — аптейк;
5 — котел-утилизатор; 6 — паровой воздухоподогреватель;
7 — топливный воздухоподогреватель
элементов, что позволяет значительно удлинить срок службы агрегата. Аптейк непосредственно сочленен с котлом-утилизатором туннельного типа. В боковой стене отстойной камеры установлены две медные водоохлаждаемые плиты с отверстиями для выпуска шлака, а в передней торцевой стене — чугунные шпуры для выпуска штейна.
Габариты печи определены на основании технологических расчетов произведенных с помощью ЭВМ, исходя из проектной производительности печи и других исходных параметров для проектирования.
В реакционной шахте, для окисления компонентов концентрата, используется воздух обогащенный кислородом и подогретый до 200°С. Согласно теплового баланса - степень обогащения дутья кислородом на ПВП никеля составляет 26%при среднем составе шихты, что позволяет реакционной шахте работать автогенно, без применения дополнительного топлива Оборудование рассчитано на максимальное обогащение кислородом до 40%, если по каким-либо причинам:
1. Теплопотребление шихты увеличится
2. Увеличатся тепловые потери печи;
3. Подогрев воздуха уменьшится.
Если обогащения дутья кислородом до 40% из-за вышеперечисленных факторов окажется недостаточным, то для восполнения недостатка тепла в реакционной шахте, используют природный газ.
Расплавленные частицы падают на поверхность ванны отстойника. В отстойной зоне печи происходит расслоение сульфидно-силикатного расплава на шлак и штейн. Для поддержания заданной температуры шлака и штейна в отстойной зоне смонтировано 18 горелок природного газа. При выходе из реакционной шахты направление движения газов изменяется на 90° - газовый поток проходит горизонтально над ванной в отстойной зоне печи. Затем направление движения газа вновь изменяется на 90° - газ поднимается по вертикальному аптейку печи вверх. В аптейк инжектируется угольная пыль, где и происходит восстановление сернистого газа до элементарной серы. Благодаря такой конструкции печи происходит достаточно полное отделение сульфидно-силикатных частиц, находящихся во взвешенном состоянии, от газового потока.
|
Пылевынос из печи взвешенной плавки составляет 12-15% от веса загружаемой шихты.
После аптейка газы поступают в котел-утилизатор, где охлаждаются с 1350°С до 550°С, а затем после очистки в электрофильтрах от пыли, поступают в серный цех для улавливания из газов элементарной серы.
Печь взвешенной плавки является головным агрегатом в цепи переработки серосульфидных концентратов. Агрегат обладает высокой интенсивностью плавления. В связи с этим печь имеет сложную и многообразную систему охлаждения.
Агрегат должен обладать высокой герметичностью. Нарушение герметичности ведет к подсосам, что нарушает тепловой баланс печи, разубоживает отходящие газы и увеличивает их объемы, увеличивает расход восстановителя. Вышеперечисленные причины отрицательно сказываются не дальнейшей обработке газов в серном цехе,
Все три части печи взвешенной плавки должны иметь высокую герметичность, требуют жесткого поддержания заданных параметров, что обеспечивается работой печи в автоматическом режиме с помощью ЭВМ.
3. ФИЗИКО-ХИМИЧЕСКИЕ ОСНОВЫ ПРОЦЕССА
Процесс плавки сульфидных концентратов с утилизацией серы из отходящих газов очень сложен, поэтому на производительность печи, полноту протекания окислительных и восстановительных реакций влияют многие факторы, основными из них являются;
- размеры частиц и время нахождения частиц в газовом потоке;
- время нагрева частиц;
- скорость, направление и последовательность окислительных реакций, влияние температуры на конечное химическое равновесие;
- минералогический состав концентратов;
- вид восстановителя сернистого ангидрида и влияние температуры на конечное равновесное состояние восстановительных реакций.
Образование фаялита
2FeO+SiO2=(FeO)2SiO2
Разложение магнетита
3Fe3O4+FeS+5SiO2=5(FeO)2xSiO2+SO2
Плавкость сульфидов
В сравнении с окислами сульфиды являются более легкоплавкими соединениями. Температуры плавления основных сульфидов, входящих в состав медных и никелевых штейнов:
Сульфид железа 1171 С
Халькозин – 1135 С
Сульфид кобальта – 1140 С
|
Хизлевудит – 788 С
Эвтектические сплавы, образованные двумя различными сульфидами, а так же эвтектики между сульфидом и его металлом более легкоплавки, чем отдельные компоненты.
Штейны при плавке сульфидных компонентов всегда является многокомпонентными системами. Составы штейнов не всегда отвечают составам эвтектик, но тем не менее, температуры плавления штейнов все же ниже, чем температуры плавления входящих в них сульфидов. Обычно при температуре 850-900°С штейны находятся в жидкотекучем состоянии,
Комп.
Cu
Ni
Fe
S
Оксиды
Прочие
Общ. мас.
Предварительный расчёт по выходу штейна.
Извлечение в штейн из шихты:
Cu – 91%
Ni – 91 %
Всего в штейн перейдет:
Cu 3,75х0,91= 3,41
Ni 7,58х0,91= 6,9
Вес штейна на 100 кг концентрата при 50 % содержании металлов:
(3,41+6,9)х0,5= 20,61
По данным Б.П. Недведецкого, в штейнах с 50% металла содержится 2% О2 и 23,7% S
В этом случае содержание железа в штейне составит:
Fe: 100-(50+2+23,7)= 24,3%
Предварительный состав штейна.
Таблица № 3
Хим. Сост. | Масса кг. | % |
Ni | 6,9 | 33,48 |
Cu | 3,41 | 16,55 |
S | 4,88 | 23,7 |
O2 | 0,41 | 2 |
Fe | 5,01 | 24,3 |
Итого | 20,61 | 100 |
Перейдет в шлак железа: 43-5,01=37,99 кг
Флюсы:
Для получения кондиционных отвальных шлаков и в связи с высоким содержанием Fe в исходном сырье в шихту вводятся флюсующие присадки. Основным флюсующим компонентом в шихте служит песчаник.
Примем следующий состав песчаника:
SiO2 – 80 %, MgO – 1,5%, Al2O3 – 8,7%
CaO – 1,3 %, FeO – 2,5%,
Расчет ведем на получение шлака, содержащего 30% SiO2.
Примем, что Х – общая масса шлака, кг; У – масса загружаемого песчаника, кг. Составляющие песчаника переходят в шлак целиком. Тогда общая масса шлака будет, кг:
Х=У+37,99х71,85/55,85+5,88+6,65= У+61,4
37,99х71,85/55,85 – количество FeO, образовавшаяся из железа концентрата, перешедшего в шлак.
6,65 – количество SiO2 в концентрате
5,88 – количество CaO, MgO, Al2O3
Второе уравнение получаем из баланса:
0,30 Х=6,65+0,8У
Решая систему уравнений получаем:
У=23,54 (песчаник) Х = 84,94 (шлак)
Результат проверяем подсчетом количества и состава шлака:
FeO | 48,87+23,54х0,025=49,46 | 58,23 |
SiO2 | 6,65+23,54х0,8=25,48 | 30,00 |
Al2O3 | 1,52+23,54*,087=3,57 | 4,19 |
CaO | 2,35+23,54х0,013=2,66 | 3,12 |
MgO | 2,02+23,54х0,015=2,37 | 2,79 |
Прочие | 1,42 | 1,67 |
Итого | 84,94 | 100 |
Для расчета состава и количества отходящих газов примем, что весь кислород, необходимый для осуществления реакций, поступает с подогретым дутьем. При этом необходимо учитывать, что на практике имеются неорганизованные подсосы холодного воздуха, количество которого может колебаться от 2% до 6%.
|
Влажность шихты 0,2%, следовательно в печь поступит ее
(100+23,54)х0,002=0,25 кг
С учетом содержания серы в штейне и шлаке ее перейдет в газы:
28,28 – 4,88- 0,67=22,73 кг
32S-64 SO2
22,73 S - X SO2, что составляет 45,46 кг SO2
На окисление железа, переходящего в шлак, расход кислорода составит 48,87-37,99=10,88кг
Общая потребность кислорода на плавку 100 кг концентрата будет, кг:
- На окисление серы – 22,73
- На окисление железа – 10,88
- Переходит в штейн – 0,41
Итого:34,02 кг
Вместе с кислородом в печь поступит азота
34,02/0,23 х 0,77=113,8 кг
Из практики работы известно, что со шлаком теряется: Cu – 2%, Ni – 4,5%
Cu= 3,75 x 0,02= 0,075
Ni= 7,58 x 0,045=0,34
S в шлак = 28,28- (4,88+22,73)=0,67
В технические газы отходит:
Cu: 3,75-(3,41+0,08)= 0,26
Ni: 7,58-(6,9+0,34)=0,34
Статьи баланса | Всего | В том числе | |||||||||||
Cu | Ni | Fe | S | SiO2 | CaO | MgO | Al2O3 | O2 | N2 | H2O | прочие | ||
Загружено: | |||||||||||||
Шихты | 100,22 | 3,75 | 7,58 | 43,00 | 28,28 | 6,65 | 2,35 | 2,02 | 1,52 | - | - | 0,20 | 4,87 |
Песчаника | 21,59 | 18,83 | 0,31 | 0,35 | 2,05 | - | - | 0,05 | |||||
Воздуха | 147,82 | 34,02 | 113,80 | ||||||||||
Всего: | 269,63 | 3,75 | 7,58 | 43,00 | 28,28 | 25,48 | 2,66 | 2,37 | 3,57 | 34,02 | 113,80 | 0,25 | 4,87 |
Получено: | |||||||||||||
Штейна | 20,61 | 3,41 | 6,90 | 5,01 | 4,88 | - | - | - | - | 0,41 | - | ||
Шлаков | 88,91 | 0,08 | 0,34 | 37,99 | 0,67 | 25,48 | 2,66 | 2,37 | 3,57 | 10,88 | 4,87 | ||
Технические газы | 160,11 | 0,26 | 0,34 | 22,73 | 22,73 | 113,80 | 0,25 | ||||||
Всего: | 269,63 | 3,75 | 7,58 | 43,00 | 28,28 | 25,48 | 2,66 | 2,37 | 3,57 | 34,02 | 113,80 | 0,25 | 4,87 |
Курсовая работа
по дисциплине: «Металлургия»
на тему:
«ВЗВЕШАННАЯ ПЛАВКА НИКЕЛЕВОГО КОНЦЕНТРАТА В ПЕЧИ ВЗВЕШАННОЙ ПЛАВКИ»
Выполнил: Бельтюков С.Н.
Проверил: Рогова Л.И.
Группа: Экм-99-У ВО Подпись: _______________
Шифр: 060800 Дата проверки:
Дата выполнения
Норильск, 2000г.
СОДЕРЖАНИЕ
1. Выбор технологии производства…………………………2
2. Описание основного агрегата……………………………..3
3. Физико-химические основы процесса……………………5
4. Технико-экономические показатели……………………..11
5. Металлургический расчет…………………………………12
Библиографический список
1. ВЫБОР ТЕХНОЛОГИИ ПРОИЗВОДСТВА
Плавка во взвешенном состоянии на подогретом дутье была осуществлена в промышленном масштабе финской фирмы «Оутокумпу» на заводе «Харьявалта». В первоначальном варианте для плавки применяли воздушное дутье, подогретое до 400—500 °С. Начиная с конца 60-х годов, этот процесс по лицензии фирмы «Оутокумпу» стали широко применять на металлургических заводах многих стран. В настоящее время он внедрен более чем на 30 предприятиях для переработки медных, никелевых и пиритных концентратов, в т.ч. на Надеждинском металлургическом заводе. Финскую плавку на сегодня можно считать самым распространенным в промышленности и наиболее технологически и аппаратурно отработанным автогенным процессом плавки сульфидных концентратов.
Особенностями взвешенной плавки являются:
- высокая производительность (удельный проплав 10-15 т/м2 в сутки);
- низкий расход топлива - процесс плавки сульфидного концентрата протекает в режиме, близком к автогенному;
- возможность полного автоматического управления процессом плавки с помощью системы "Проскон-103'';
- возможность получения штейна требуемого состава;
- утилизация серы из высококонцентрированных серных газов.
Конструкция ПВП и комплекс других технических решений обеспечивают получение пара энергетических параметров и высокую степень утилизации серы из отходящих газов, что резко снижает выброс двуокиси серы в окружающую среду и значительно улучшают условия труда обслуживающего персонала.
В плавильном цехе НМЗ имеется две печи взвешенной плавки одинаковой конструкции для плавки медного и никелевых концентратов.
Передел взвешенной плавки - структурное подразделение плавильного цеха HMЗ.
2. ОПИСАНИЕ ОСНОВНОГО АГРЕГАТА
Конструкция печи для плавки во взвешенном состоянии на подогретом дутье достаточно сложна — она сочетает в себе две вертикальные шахты (реакционную и газоход-аптейк) и горизонтальную камеру-отстойник.
Тонкоизмельченная шихта, предварительно высушенная до содержания влаги менее 0,2%, подается по системе ленточных конвейеров и пневмотранспорта в бункер шихты. Из бункера шихта двумя скребковыми транспортерами "Редлер" подается через свод реакционной камеры с помощью четырех специальных горелок. Основное назначение горелки — приготовление и подготовка шихтововоздушной смеси для ускорения процесса горения сульфидов. Перемешивание шихты с дутьем достигается разбиванием струи шихты о конус-рассекатель и подачей дутья через воздушный патрубок и распределительную решетку.
|
Схема горелки печи завода
1 — дутье; 2 — шихтовая воронка; 3 — загрузочный патрубок;
4 — воздушный патрубок; 5 — конус-рассекатель;
6 — распределительная решетка; 7 — диффузор
Вся печь взвешенной плавки выполнена в виде кладки из магнезитового кирпича. Футеровка реакционной шахты и аптейка заключена в металлические кожухи из листовой стали. В кладку всех элементов печи заложено большое количество водоохлаждаемых
Печь для плавки во взвешенном состоянии
1 — горелка; 2 — реакционная камера; 3 — отстойная ванна; 4 — аптейк;
5 — котел-утилизатор; 6 — паровой воздухоподогреватель;
7 — топливный воздухоподогреватель
элементов, что позволяет значительно удлинить срок службы агрегата. Аптейк непосредственно сочленен с котлом-утилизатором туннельного типа. В боковой стене отстойной камеры установлены две медные водоохлаждаемые плиты с отверстиями для выпуска шлака, а в передней торцевой стене — чугунные шпуры для выпуска штейна.
Габариты печи определены на основании технологических расчетов произведенных с помощью ЭВМ, исходя из проектной производительности печи и других исходных параметров для проектирования.
В реакционной шахте, для окисления компонентов концентрата, используется воздух обогащенный кислородом и подогретый до 200°С. Согласно теплового баланса - степень обогащения дутья кислородом на ПВП никеля составляет 26%при среднем составе шихты, что позволяет реакционной шахте работать автогенно, без применения дополнительного топлива Оборудование рассчитано на максимальное обогащение кислородом до 40%, если по каким-либо причинам:
1. Теплопотребление шихты увеличится
2. Увеличатся тепловые потери печи;
3. Подогрев воздуха уменьшится.
Если обогащения дутья кислородом до 40% из-за вышеперечисленных факторов окажется недостаточным, то для восполнения недостатка тепла в реакционной шахте, используют природный газ.
Расплавленные частицы падают на поверхность ванны отстойника. В отстойной зоне печи происходит расслоение сульфидно-силикатного расплава на шлак и штейн. Для поддержания заданной температуры шлака и штейна в отстойной зоне смонтировано 18 горелок природного газа. При выходе из реакционной шахты направление движения газов изменяется на 90° - газовый поток проходит горизонтально над ванной в отстойной зоне печи. Затем направление движения газа вновь изменяется на 90° - газ поднимается по вертикальному аптейку печи вверх. В аптейк инжектируется угольная пыль, где и происходит восстановление сернистого газа до элементарной серы. Благодаря такой конструкции печи происходит достаточно полное отделение сульфидно-силикатных частиц, находящихся во взвешенном состоянии, от газового потока.
Пылевынос из печи взвешенной плавки составляет 12-15% от веса загружаемой шихты.
После аптейка газы поступают в котел-утилизатор, где охлаждаются с 1350°С до 550°С, а затем после очистки в электрофильтрах от пыли, поступают в серный цех для улавливания из газов элементарной серы.
Печь взвешенной плавки является головным агрегатом в цепи переработки серосульфидных концентратов. Агрегат обладает высокой интенсивностью плавления. В связи с этим печь имеет сложную и многообразную систему охлаждения.
Агрегат должен обладать высокой герметичностью. Нарушение герметичности ведет к подсосам, что нарушает тепловой баланс печи, разубоживает отходящие газы и увеличивает их объемы, увеличивает расход восстановителя. Вышеперечисленные причины отрицательно сказываются не дальнейшей обработке газов в серном цехе,
Все три части печи взвешенной плавки должны иметь высокую герметичность, требуют жесткого поддержания заданных параметров, что обеспечивается работой печи в автоматическом режиме с помощью ЭВМ.
3. ФИЗИКО-ХИМИЧЕСКИЕ ОСНОВЫ ПРОЦЕССА
Процесс плавки сульфидных концентратов с утилизацией серы из отходящих газов очень сложен, поэтому на производительность печи, полноту протекания окислительных и восстановительных реакций влияют многие факторы, основными из них являются;
- размеры частиц и время нахождения частиц в газовом потоке;
- время нагрева частиц;
- скорость, направление и последовательность окислительных реакций, влияние температуры на конечное химическое равновесие;
- минералогический состав концентратов;
- вид восстановителя сернистого ангидрида и влияние температуры на конечное равновесное состояние восстановительных реакций.
Размеры частиц и величина удельной поверхности компонентов шихтовых материалов
Обычно руды измельчают перед флотацией в пределах нижнего класса крупностью от 60% класса - 0,0605 мм до 90% класса -0,088мм. Средней величиной зерна флотационных концентратов можно считать от 0,07мм до 0,03мм.
Процессы нагревания сульфидных частиц, диссоциации высших сульфидов и взаимодействия сульфидов с кислородом печной атмосферы в ходе взвешенной плавки являются типичными гетерогенными процессами, скорость которых при прочих, равных условиях линейно зависит от величины поверхности раздела на границе твердое - газ.
Произведя несложный расчет, можно убедиться что 1 кг материала с удельным весом 4 г/см3 при среднем диаметре зерна 0,04мм, что соответствует размеру зерен флотационных концентратов., имеет удельную поверхность 59,5 м2/кг, Будучи взятым в виде компактного шара, тот же I кг материала имеет поверхность всего 0,019 м2. Таким образом, измельчение материала влечет за собой резкое увеличение его удельной поверхности, Однако, излишнее переизмельчение шихтовых материалов нежелательно, так как в этом случае возрастает пылеунос,
Движение частиц в газовом потоке.
Очень важным параметром процесса плавки во взвешенном состоянии является время пребывания шихтовых частиц в потоке от момента поступления в пространство реакционной шахты до соударении с поверхностью расплава в отстойной зоне печи.
Поскольку и газы, и частицы шихты движутся в одной направлении сверху вниз, очевидно, что время пребывания шихтовых частиц в полете определится суммой скоростей свободного падения частицы и движения газового поток. В условиях плавки сульфидных флотационных концентратов скорость собственного падения самых крупных зерен концентрата не превышает I м/сек. Сульфидные частицы, вдуваемые в реакционную шахту, незначительно опережают газовый поток и время, необходимое для прохождения частиц концентрата по всей высоте плавильной шахты, равно 0,8 - 0.9 времени прохождения газом этого же пути, И если газ проходит шахту печи за 2,8 сек., то частицы флотационного концентрата будут находиться во взвешенном состоянии примерно 2,20 – 2,50 сек.
|
|
История развития хранилищ для нефти: Первые склады нефти появились в XVII веке. Они представляли собой землянные ямы-амбара глубиной 4…5 м...
Индивидуальные очистные сооружения: К классу индивидуальных очистных сооружений относят сооружения, пропускная способность которых...
История развития пистолетов-пулеметов: Предпосылкой для возникновения пистолетов-пулеметов послужила давняя тенденция тяготения винтовок...
Кормораздатчик мобильный электрифицированный: схема и процесс работы устройства...
© cyberpedia.su 2017-2024 - Не является автором материалов. Исключительное право сохранено за автором текста.
Если вы не хотите, чтобы данный материал был у нас на сайте, перейдите по ссылке: Нарушение авторских прав. Мы поможем в написании вашей работы!