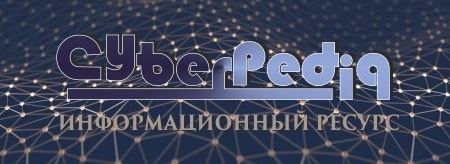
Своеобразие русской архитектуры: Основной материал – дерево – быстрота постройки, но недолговечность и необходимость деления...
Поперечные профили набережных и береговой полосы: На городских территориях берегоукрепление проектируют с учетом технических и экономических требований, но особое значение придают эстетическим...
Топ:
Характеристика АТП и сварочно-жестяницкого участка: Транспорт в настоящее время является одной из важнейших отраслей народного...
Проблема типологии научных революций: Глобальные научные революции и типы научной рациональности...
Интересное:
Как мы говорим и как мы слушаем: общение можно сравнить с огромным зонтиком, под которым скрыто все...
Финансовый рынок и его значение в управлении денежными потоками на современном этапе: любому предприятию для расширения производства и увеличения прибыли нужны...
Средства для ингаляционного наркоза: Наркоз наступает в результате вдыхания (ингаляции) средств, которое осуществляют или с помощью маски...
Дисциплины:
![]() |
![]() |
5.00
из
|
Заказать работу |
|
|
Оглавление
Задание……………………………………………………………………………………...…….3
Введение………………………………………………………………………………….………4
1.Описание детали……………………………………………………………….………………5
2.Карта дефектации………………………..…………………………………………………...10
3.Обоснование способа восстановления……………………………………………………...11
4.План технологических операций на устранение дефекта…………………………………12
5.Расчет режимов и норм времени по операциям……………………………………………13
6.Технологический процесс на картах
7.Приспособление………………………………………………………………………………16
8.Проект производственного участка ………………………………………………………...17
Техника безопасности на рабочем месте автослесаря…………………………………….....19
Список литературы…………………………...……………………………………….……….21
Задание
Введение
В процессе эксплуатации автомобиля в результате воздействия на него целого ряда факторов (воздействие нагрузок, вибраций, влаги, воздушных потоков, абразивных частиц при попадании на автомобиль пыли и грязи, температурных воздействий и т. п.) происходит необратимое ухудшение его технического состояния, связанное с изнашиванием и повреждением его деталей, а также изменением ряда их свойств (упругости, пластичности и др.). Изменение технического состояния автомобиля обусловлено работой его узлов и механизмов, воздействием внешних условий и хранения автомобиля, а также случайными факторами. К случайным факторам относятся скрытые дефекты деталей автомобиля, перегрузки конструкции и т. п. Основными постоянно действующими причинами изменения технического состояния автомобиля при его эксплуатации является изнашивание, пластические деформации, усталостные разрушения, коррозия, а также физико-химические изменения материала деталей (старение).
На изменение технического состояния автомобиля существенное влияние оказывают условия эксплуатации: дорожные условия (техническая категория дороги, вид и качество дорожного покрытия, уклоны, подъемы спуски, радиусы закруглений дороги), условия движения (интенсивное городское движение, движение по загородным дорогам), климатические условия (температура окружающего воздуха, влажность, ветровые нагрузки, солнечная радиация), сезонные условия (пыль летом, грязь и влага осенью и весной), агрессивность окружающей среды (морской воздух, соль на дороге в зимнее время, усиливающие коррозию), а также транспортные условия (загрузка автомобиля). Чтобы обеспечить работоспособность автомобиля в течение всего периода эксплуатации, необходимо периодически поддерживать его техническое состояние комплексом технических воздействий, которые в зависимости от назначения и характера можно разделить на две группы: воздействия, направленные на поддержание агрегатов, механизмов и узлов автомобиля в работоспособном состоянии в течение наибольшего периода эксплуатации; воздействия, направленные на восстановление утраченной работоспособности агрегатов, механизмов и узлов автомобиля. Комплекс мероприятий первой группы составляет систему технического обслуживания и носит профилактический характер, а второй - систему восстановления (ремонта). Для поддержания подвижного состава автомобильного транспорта в технически исправном состоянии, необходимом для нормальной эксплуатации, у нас в стране принята планово-предупредительная система технического обслуживания и ремонта автомобилей. Сущность этой системы состоит в том, что техническое обслуживание осуществляется по плану, а ремонт - по потребности.
|
Описание детали
|
Карта дефектации
Карта технических требований на дефектацию блока цилиндров компрессора | ||||||
| Деталь: | |||||
Блок цилиндров | ||||||
Номер детали: | ||||||
№ 5320-3509028 | ||||||
Материал | Твердость | |||||
СЧ 18 | HB – 187-241 | |||||
Позиция на эскизе
Возможные дефекты
Способ установле-ния дефекта, измерительные инструменты
Размеры, мм
Заключение
○60+0,03
3
Индикаторный нутромер
Обработать в ремонтный размер
3. Обоснование способа восстановления
Обработка деталей под ремонтный размер.
При этом способе восстановления одна из сопряженных деталей, обычно более дорогостоящая, обрабатывается под ремонтный размер, а вторая, сопряженная с ней, заменяется новой, так называемой ремонтной, или восстанавливается также до ремонтного размера. Обработкой под ремонтный размер восстанавливают геометрическую форму, требуемую шероховатость и точные параметры изношенных поверхностей деталей. Этот вид восстановления деталей эффективен лишь в случае, когда изменение размера не приводит к ликвидации термически обработанного поверхностного слоя детали.
Восстанавливаемые поверхности деталей могут иметь несколько ремонтных размеров. Их количество и конкретное значение зависят от износа деталей за межремонтный срок службы автомобиля, припуска на обработку и запаса прочности детали. Припуск на механическую обработку зависит от вида обработки: при чистовом точении и растачивании он составляет 0,05—0,10 мм, при шлифовании 0,03—0,05 мм на радиус.
|
Обработкой деталей под ремонтный размер восстанавливают гильзы блока цилиндров, коренные и шатунные шейки коленчатого вала, опорные шейки распределительного вала и многие другие детали. К преимуществам восстановления деталей обработкой до ремонтного размера следует отнести простоту технологического процесса и высокую экономическую эффективность. К недостаткам этого способа относятся увеличение номенклатуры запасных частей, поставляемых промышленностью, и некоторое усложнение организации процессов комплектования деталей.
«Микрогеометрия» - это микропрофиль зеркала цилиндров. От того, какой получилась поверхность после ремонта, зависит трение и износ деталей, в первую очередь, поршневых колец. Для этого микропрофиль поверхности должен удовлетворять противоречивым требованиям - быть гладким, но одновременно и шероховатым, чтобы удерживать масло. Кроме того, необходимо, чтобы трущиеся детали имели минимальное время приработки.
Всем этим требованиям, как известно, лучше всего соответствует поверхность, имеющая впадины (риски) так называемой основной шероховатости глубиной до 0,005-0,010 мм и сглаженные (плоские) вершины - опорные поверхности. Такая поверхность формируется в процессе плосковершинного хонингования.
План технологических операций на устранение дефекта
№ операции | Наименование содержание операции | Оборудование | Приспособления | Инструмент | |
Рабочий | Измерительный | ||||
005 | Моечная Промыть цилиндры, высушить | Ванна моечная, шкаф сушильный | |||
010 | Расточная Обработка цилиндров под ремонтный размер с припуском на хонингование | Алмазно – расточной станок 2А78Н | Приспособление для установки и крепления блока цилиндров | Резец проходной с пластинкой ВК3М | Индикаторный нутромер НИ -50-75(ГОСТ 10-75) |
015 | Моечная Промыть цилиндр после расточки, высушить | Ванна моечная, шкаф сушильный | 5 % раствор соды, 60 С | ||
020 | Контрольная Произвести замеры | Стол контролера | Индикаторный нутромер НИ -50-75 (ГОСТ 10- 75 ) | ||
025 | Доводочная Доводка точных внутренних размеров | Хонинговальный станок 3Г88 | Приспособление для установки и крепления блока цилиндров | Хонинговальный брусок 64С10ПСТ2-Т27К5А | |
030 | Контрольная Произвести замеры | Стол контролера | Индикаторный нутромер НИ -50-75 (ГОСТ 10- 75 ) |
|
Операция расточная
Скорость резания для чугуна V = 80м/мин при принятой подаче S = 0,05 мм/об
Определяем частоту вращения шпинделя станка:
n = (1000 × V) / (π × D) = (1000 × 80) / (3,14 × 60) = 424,6 об/мин
V – скорость резания для чугуна
D – диаметр цилиндра
Принимаем по паспорту станка n = 420 об/мин
Определяем основное (машинное) время по формуле:
Т0 = Lp / (n × S), мин; Lp = l + l1 + l2
l – длина обрабатываемого отверстия, по чертежу = 92 мм
l1 + l2 – величина врезания и выхода резца, соответственно, принимаю l1 + l2 = 10мм
Т0 = 112 / (420 × 0,05) = 5,33 мин
На два цилиндра:
5,33 × 2 = 10,66 мин
Определяем вспомогательное время:
Тв = Твсу + Твпр
Твсу –вспомогательное время на установку и снятие детали и выверкой ее по индикатору при массе детали до 5кг – 1,29мин;
Твпр – вспомогательное время на проход – 0,85 мин
Тв = 1,29 + 0,85 = 2,14 мин
Дополнительное время:
Тд = К(Т0 + ТВ)/100
К – процент дополнительного времени – 8%
Тд = 8 × (10,66 + 2,14) / 100 = 1,02 мин
Штучное время:
ТШТ = Т0 + Тв + Тд;
ТШТ = 10,66 + 2,14 + 1,02 = 13,82 мин
Подготовительно-заключительное время Тпз = 12 мин
Операция Хонингование
Определяем длину брусков:
lи = (1/3…3/4) × l, мм
l – длина хонингования, мм
lи = (1/3…3/4) × 92 = 30,7…69мм, принимаем длину брусков 65 мм
Определяем выход брусков за торцы обрабатываемой поверхности y, мм:
y = (0,2 – 0,4) × 65 = 13…26мм, принимаем у = 20 мм
Определяем длину рабочего хода бруска Lр, мм:
Lр = l + 2 × у - lи = 92 + 2 × 20 – 65 = 67, принимаем Lр = 70мм
Принимаем скорость возвратно поступательного движения хонинговальной головки
Vпост = 12 м/мин при черновой обработке и Vпост = 8 м/мин при чистовой
Определяем скорость вращения хонинговальной головки:
Vокр = (3…5) × Vпост
-при черновой обработке: Vокр = (3…5) × 12 = 36…60 м/мин
-при чистовой обработке: Vокр = (3…5) × 8 = 24…40 м/мин
Определяем частоту вращения хонинговальной головки:
n = (1000 × V) / (π × D)
V1 = 40
V2 = 30
-при черновой обработке: n1 = (1000 × 40) / (3,14 × 60) = 212,3 об/мин
-при чистовой обработке: n2 = (1000 × 30) / (3,14 × 60) = 159,4 об/мин
Определяем частоту двойных ходов хонинговальной головки:
nдв.ход = (1000 × Vпост) / (2 × Lр), дв.ход/мин;
-при черновой обработке: nдв.ход = (1000 × 12) / (2 × 70) = 85,7 дв.ход/мин;
-при чистовой обработке: nдв.ход = (1000 × 8) / (2 × 70) = 57,1 дв.ход/мин;
Определяем основное время:
То = h / (b × nдв.ход), мин
h – припуск на диаметр, мм
b – толщина слоя металла
-переход 1: То = 0,1 / (0,002 × 80) = 0,63 мин
-переход 1: То = 0,02 / (0,0004 × 36) = 1,39 мин
|
∑ То = 2 × (0,63 + 1,39) = 4,04 мин
Определяем вспомогательное время:
Твсп = Твсу + Твпр
Твсу –вспомогательное время на установку и снятие детали в специальном приспособлении
С ручным зажимом и выверкой ее по индикатору при массе детали до 3кг – 2,12мин;
Твпр – вспомогательное время связанное с переходом – 1,55 мин
Твсп = 2,12 + 1,55 = 3,67 мин
Дополнительное время:
Тд = К(Т0 + ТВ)/100
К – процент дополнительного времени – 10%
Тд = 10 × (4,04 + 3,67) / 100 = 0,77 мин
Штучное время:
ТШТ = Т0 + Тв + Тд;
ТШТ = 4,04 + 3,67+ 0,77 = 8,48 мин
Подготовительно-заключительное время Тпз = 12 мин
Операция Моечная
Принимаем основное время мойки деталей с трехразовым погружением и промывкой вручную при массе корзины с деталями до 12 кг – 2,39 мин и основное время сушки в шкафу – 10 мин.
Тосн = 12,39мин.
Определяем вспомогательное время:
- время передвижения рабочего и перемещение деталей в процессе работы на тележке на расстоянии до 4м – 0,20 мин
- время на разгрузку тележки и укладку деталей в корзину – 0,18 мин
- время на загрузку корзины в ванну и выгрузку – 0,19 мин
- время на загрузку деталей в сушильный шкаф и выгрузку – 0,65 мин
Полное значение вспомогательного времени составит:
Твсп = 0,20 + 0,18 + 0,19 + 0,65 = 1,22 мин.
Оперативное время составит:
Tоп = Тосн + Твсп
Tоп = 12,39 + 1,22 = 13,61 мин
Прибавочное время 7% от оперативного:
Тпр = 0,07 × 13,61 = 0,95 мин
Подготовительно-заключительное время Тпз = 4 мин
Приспособление
Съемник седла выпускного клапана.
Оборудование и оснастка
Наименование | Тип, модель | Кол-во | Размер в плане (мм) | Общая площадь(м2) |
1.Станок алмазно-расточной | 2А78Н | 1 | 1200×1520 | 1,82 |
2.Станок хонинговальный | 3Г88 | 1 | 1270×1215 | 1,54 |
3.Шкаф для инструментов | 1 | 600×600 | 0,72 | |
4.Ванна для мойки деталей | 1 | 1000×800 | 0,8 | |
5.Шкаф сушильный | 1 | 1000×800 | 0,8 | |
6.Стеллаж для деталей | 1 | 1000×600 | 0,6 | |
7.Ларь для обтирочных материалов | 1 | 800×800 | 0,64 | |
8.Ящик для песка | 1 | 500×600 | 0,3 | |
9.Раковина мойка | 1 | 600×600 | 0,36 | |
Итого, площадь занимаемая оборудованием | 7,58 |
Fу = 7,58 × (4,0…5,0) = 30,3…37,5 кв.м
Остюда ширина помещения = 6м, длина = 6м, общая площадь участка составит 36 м2.
Техника безопасности на рабочем месте автослесаря.
1.Перед техническим обслуживанием или ремонтом машины на подъемнике
(гидравлическом, электромеханическом) на пульте управления подъемником вывесить предупреждающий знак «Не трогать - под автомобилем работают люди!» Плунжер подъемника зафиксировать от самопроизвольного опускания упором (штангой).
2.Слить бензин, масло и воду при ремонте деталей и агрегатов, связанных с системами охлаждения и смазки. Не допускать расплескивания и разлива жидкостей.
Случайно пролитые жидкости следует засыпать песком или опилками, которые потом необходимо убрать с помощью совка и щетки.
3.Обеспечить безопасность работы под машиной:
- затормозить ручным тормозом;
- включить низшую передачу;
- выключить зажигание (подачу топлива);
- под колеса подложить упоры (башмаки).
4.При работах, связанных с проворачиванием коленчатого или карданного вала, дополнительно проверить выключение зажигания, подачу топлива (для дизельных автомобилей), поставить рычаг переключения передач в нейтральное положение, освободить рычаг ручного тормоза.
После выполнения необходимых работ затянуть ручной тормоз и вновь включить низшую передачу
5.При ремонте машины вне осмотровой канавы, эстакады или подъемника использовать лежаки или подстилки.
б.Влезать под машину и вылезать из-под нее только со стороны, противоположной проезду. Под машиной размещаться между колесами вдоль машины.
7.Перед снятием и установкой агрегатов и узлов (двигателей, рессор, задних и передних мостов и т.п.) разгрузить их от веса кузова путем поднятия кузова подъемным механизмом с последующей установкой козелков.
8.Разборку и сборку рессор производить с помощью специальных приспособлений. Проверять совпадение отверстия ушка рессоры и серьги только с помощью бородка или оправки. Запрещается такую проверку производить пальцами.
9.Снятие отдельных агрегатов и деталей (тормозных и клапанных пружин, барабанов, рессорных пальцев и т.п.), связанное с приложением значительных физических нагрузок или с неудобством в работе, производить с применением приспособлений (съемников), обеспечивающих безопасность работ.
10.Перед снятием колес убедиться в надежной установке машины на козелках и в наличии упоров под неснятыми колесами.
11.Перед демонтажем шины полностью выпустить воздух из камеры колеса.
12.Демонтаж и монтаж шин должны выполняться в шиномонтажном отделении с применением для этих работ специального оборудования и инструмента с применением ограждений, обеспечивающих безопасность.
13.Перед сборкой колеса проверить состояние съемных фланцев обода и стопорного кольца. Фланцы обода и стопорные кольца должны быть очищены от ржавчины, не иметь вмятин, трещин, заусенцев. Диски колес, стопорные кольца и съемные фланцы должны соответствовать размерам шин.
14.При монтаже шины следует вводить стопорное кольцо всей его внутренней поверхностью в выемку на диске колеса.
15.Накачивать шины воздухом необходимо в специальных приспособлениях. Перед накачиванием убедиться, что запорное кольцо полностью лежит в замковом пазе. Допускается исправлять положение шины на диске постукиванием только после прекращения поступления воздуха.
1б.Перед обслуживанием и ремонтом днища кузова легкового автомобиля на поворотном стенде необходимо укрепить на нем автомобиль, слить топливо из топливных баков и воду из системы охлаждения, закрыть плотно маслозаливную горловину двигателя и снять аккумуляторную батарею.
17.Промывать детали керосином необходимо в специально отведенном месте. Обдувать их сжатым воздухом в специальных закрытых шкафах, оборудованных вытяжной вентиляцией.
18.Четко согласовать свои действия при выполнении работы совместно с другими рабочими.
19.Запрещается:
- техническое обслуживание и ремонт автомобиля при работающем двигателе, кроме случаев регулировки систем питания и электрооборудования и опробования тормозов;
- производить ремонтные работы на автомобиле, вывешенном только на одних подъемных механизмах, без подставок;
- работать под автомобилем без лежаков или подстилок, лежа на земле или полу;
- применять случайные предметы (доски, кирпичи и т. п.) в качестве подставок или тормозных упоров (башмаков);
- работать с поврежденными или неправильно установленными упорами, а также устанавливать на упоры груженый кузов;
- выбивать при демонтаже диски колес кувалдой или молотком;
- во время накачивания шины осаживать стопорное кольцо молотком или кувалдой;
- подходить к открытому огню, курить или зажигать спички, если руки или спецодежда смочены бензином.
20.Перед испытанием и опробованием тормозов на стенде автомобиль закрепить цепью или тросом, исключающими его скатывание со стенда.
21.До пуска двигателя автомобиль затормозить, рычаг коробки передач поставить в нейтральное положение.
22.Пуск двигателя осуществлять с помощью стартера. Пуск двигателя при открытом капоте производить при отсутствии посторонних лиц на рабочем месте.
23. Запрещается:
- при обкатке двигателя на стенде касаться вращающихся частей;
- работа двигателя в закрытом невентилируемом помещении
Список литературы
1.Епифанов Л. И., Епифанов Е. А. Техническое обслуживание и ремонт автомобилей: Учебное пособие для студентов учреждения среднего профессионального образования. – М.: ФОРУМ: ИНФРА-М, 2003.- 280 с.: ил. – (Серия «Профессиональное образование»)
2.Карагодин В. И., Митрохин Н. Н. Ремонт атвомобилей и двигателей: Учеб. для студ. сред. проф. учеб. заведений. – М.: Мастерство; Высш. школа, 2001. – 496 с.
3.Козлов Ю. С. Материаловедение. Издательство «АТАР», 1999 – 180 с.
4.Кубышкин Ю. И., Маслов В. В., Сухов А. Т. ВАЗ-2110, -2111, -2112. Эксплуатация, обслуживание, ремонт, тюнинг. Иллюстрированное руководство. – М.: ЗАО «КЖИ «За рулем», 2004. – 280 с.: ил. – (Серия «Своими силами»).
5.Шестопалов С. К. Устройство, техническое обслуживание и ремонт легковых автомобилей: Учеб. для нач. проф. образования; Учеб. пособие для сред. проф. образования. – 2-е изд., стер. – М.: Издательский центр «Академия»; ПрофОбрИздат, 2002. – 544 с
6. Адаскин А. М. Материаловедение (металлообработка): Учебник для нач. проф. образования: Учеб. пособие для сред. проф. образования/ А. М. Адаскин, В. М. Зуев.- 3-е изд., стер.- М.: Издательский центр «Академия», 2004. – 240 с.
7.Макиенко Н. И. Общий курс слесарного дела: Учеб. для ПТУ. – 3-е изд., испр. – М.: Высш. шк., 1989. – 335 с.: ил.
Оглавление
Задание……………………………………………………………………………………...…….3
Введение………………………………………………………………………………….………4
1.Описание детали……………………………………………………………….………………5
2.Карта дефектации………………………..…………………………………………………...10
3.Обоснование способа восстановления……………………………………………………...11
4.План технологических операций на устранение дефекта…………………………………12
5.Расчет режимов и норм времени по операциям……………………………………………13
6.Технологический процесс на картах
7.Приспособление………………………………………………………………………………16
8.Проект производственного участка ………………………………………………………...17
Техника безопасности на рабочем месте автослесаря…………………………………….....19
Список литературы…………………………...……………………………………….……….21
Задание
Введение
В процессе эксплуатации автомобиля в результате воздействия на него целого ряда факторов (воздействие нагрузок, вибраций, влаги, воздушных потоков, абразивных частиц при попадании на автомобиль пыли и грязи, температурных воздействий и т. п.) происходит необратимое ухудшение его технического состояния, связанное с изнашиванием и повреждением его деталей, а также изменением ряда их свойств (упругости, пластичности и др.). Изменение технического состояния автомобиля обусловлено работой его узлов и механизмов, воздействием внешних условий и хранения автомобиля, а также случайными факторами. К случайным факторам относятся скрытые дефекты деталей автомобиля, перегрузки конструкции и т. п. Основными постоянно действующими причинами изменения технического состояния автомобиля при его эксплуатации является изнашивание, пластические деформации, усталостные разрушения, коррозия, а также физико-химические изменения материала деталей (старение).
На изменение технического состояния автомобиля существенное влияние оказывают условия эксплуатации: дорожные условия (техническая категория дороги, вид и качество дорожного покрытия, уклоны, подъемы спуски, радиусы закруглений дороги), условия движения (интенсивное городское движение, движение по загородным дорогам), климатические условия (температура окружающего воздуха, влажность, ветровые нагрузки, солнечная радиация), сезонные условия (пыль летом, грязь и влага осенью и весной), агрессивность окружающей среды (морской воздух, соль на дороге в зимнее время, усиливающие коррозию), а также транспортные условия (загрузка автомобиля). Чтобы обеспечить работоспособность автомобиля в течение всего периода эксплуатации, необходимо периодически поддерживать его техническое состояние комплексом технических воздействий, которые в зависимости от назначения и характера можно разделить на две группы: воздействия, направленные на поддержание агрегатов, механизмов и узлов автомобиля в работоспособном состоянии в течение наибольшего периода эксплуатации; воздействия, направленные на восстановление утраченной работоспособности агрегатов, механизмов и узлов автомобиля. Комплекс мероприятий первой группы составляет систему технического обслуживания и носит профилактический характер, а второй - систему восстановления (ремонта). Для поддержания подвижного состава автомобильного транспорта в технически исправном состоянии, необходимом для нормальной эксплуатации, у нас в стране принята планово-предупредительная система технического обслуживания и ремонта автомобилей. Сущность этой системы состоит в том, что техническое обслуживание осуществляется по плану, а ремонт - по потребности.
Описание детали
Назначение и условия работы компрессора.
Компрессор входит в состав пневматической тормозной системы автомобиля и предназначен для нагнетания воздуха в ресиверы, откуда через тормозной кран сжатый воздух подается к тормозным камерам колесных механизмов. Компрессор работает в жестком температурном режиме, который выражается в нагревании его как в процессе работы по сжиманию воздуха, так и со стороны работающего двигателя. Детали компрессора работают в условиях повышенного трения, воспринимают знакопеременные динамические нагрузки, нагрузки от сил давления воздуха при его сжатии. Также компрессор подвергается воздействию внешней агрессивной среды: пыли, влаги, и т.д.
Устройство автомобильного компрессора во многом подобно устройству двигателя (за исключением самого процесса внутреннего сгорания) и по аналогии с двигателем компрессор имеет шатунно-поршневой и клапанный механизмы, систему охлаждения, смазки и питания атмосферным воздухом, устройства привода и регулирования давления.
Шатунно-поршневой механизм компрессора включает следующие основные детали: один или несколько цилиндров; поршень с поршневыми кольцами и шатун, соединенные поршневым пальцем; коленчатый вал, подшипники которого
установлены в картере компрессора.
Клапанный механизм состоит обычно из автоматических клапанов, перемещающихся под действием давления воздуха в цилиндре, и их пружин. В компрессорах обычно применяются плоские пластинчатые металлические клапаны: впускной и выпускной (нагнетательный). Седло впускного клапана бывает расположено в цилиндре или в головке, седло выпускного - в головке.
Все детали указанных механизмов компрессора, как правило, металлические: цилиндр изготавливается из чугуна; головка, картер, поршень - чугунные или алюминиевые; шатун - стальной или алюминиевый; коленчатый вал - стальной или чугунный; клапаны, их пружины и седла, поршневой палец - стальные.
Питание компрессора атмосферным воздухом обязательно производится с очисткой через фильтр. Для этой цели используется воздушный фильтр двигателя или собственный автономный фильтр компрессора.
Охлаждением компрессора решаются три задачи:
– улучшение параметров рабочего цикла и повышение производительности компрессора, так как снижение температуры воздуха в цилиндре повышает его наполнение;
– снижение термонагруженности деталей компрессора, находящихся в контакте с нагретым сжатым воздухом (цилиндр, поршень, головка цилиндров, клапаны и их пружины и т. п.), и тем самым повышение долговечности этих деталей;
– уменьшение температуры находящегося на стенках цилиндра смазочного масла, вследствие чего улучшаются физико-химические характеристики масла и предотвращается образование нагара.
Система охлаждения компрессора может быть воздушной, водяной или смешанной. В первом случае охлаждение наиболее нагреваемых деталей компрессора (цилиндра и головки) осуществляется за счет наличия на их поверхности большого числа ребер. Во втором случае головка и верхняя часть цилиндра имеют водяные рубашки, в которые подается вода от системы охлаждения двигателя. При смешанном охлаждении головка охлаждается водой, а цилиндр имеет ребра для воздушного охлаждения.
Эффективность водяного охлаждения значительно выше, чем воздушного. Вследствие этого поверхность теплоотдачи при воздушном охлаждении должна быть в 20-30 раз больше, чем при водяном. Так как достичь этого при существующих конструктивных ограничениях практически невозможно, нагрев компрессора с воздушным охлаждением на 20-50 °С выше, чем с водяным. Разница в температуре сжатого воздуха при этом достигает 35-70 °С.
Смазкой компрессора решаются следующие функции:
– уменьшение трения между движущимися деталями и тем самым снижение потребляемой компрессором мощности двигателя;
– уменьшение температуры деталей компрессора, что особенно важно для цилиндра, поршня и поршневых колец;
– повышение (за счет масляной пленки) уплотнения между поршнем и цилиндром;
– защита деталей компрессора от коррозии.
В автомобильном компрессоре имеются различные виды трущихся подвижных соединений. Для них используют смазку разбрызгиванием из масляной ванны в картере или принудительную смазку от системы смазки двигателя.
Для регулирования давления в приводе после повышения его до заданного уровня подача сжатого воздуха от компрессора отключается.
Ранее некоторое распространение имели компрессоры, не отключаемые совсем. У этих компрессоров степень сжатия была выбрана такой, что давление в цилиндре равнялось максимальному давлению в приводе и при его достижении подача сжатого воздуха в привод прекращалась (один и тот же объем воздуха многократно сжимается, «мнется» в цилиндре). В этом случае не было необходимости в регуляторе, но компрессор работал постоянно в режиме нагрузки, что значительно снижало его долговечность и увеличивало расходы на техническое обслуживание.
Блок цилиндров КАМАЗа изготавливается из серого чугуна СЧ 18 по ГОСТ 1412-85, химический состав и механические свойства которого приведены в таблицах 1 и 2.
Химический состав серого чугуна СЧ 18 по ГОСТ 1412-85, %
Таблица 1
Углерод | Кремний | Марганец | Сера | Фосфор | Хром | Никель |
НЕ БОЛЕЕ | ||||||
3,0 – 3,3 | 1,3 – 1,7 | 0,8 – 1,2 | 0,3 | 0,15 | 0,15 | 0,5 |
Механические свойства серого чугуна СЧ 18 по ГОСТ 1412-85
Таблица 2.
Предел прочности при растяжении, ОР, мПа | Предел прочности при изгибе, ОИ, мПа | Стрела прогиба, мм, при расстоянии между опорами | Твердость, НВ | |
600 | 300 | |||
210 | 400 | 9 | 3 | 187 - 241 |
Компрессор автомобиля КамАЗ - двухцилиндровый, с рядным расположением цилиндров, питание атмосферным воздухом осуществляется от воздушного фильтра двигателя, охлаждение водяное, смазка принудительная от системы смазки двигателя, привод – шестеренный от распределительных шестерен двигателя. Компрессор установлен в развале цилиндров двигателя и крепится на переднем торце блока распределительных шестерен.
Компрессор имеет блок цилиндров 19, головку 17, крепящуюся к блоку с помощью восьми шпилек, и картер 9, закрытый снизу нижней крышкой 25, а сзади - крышкой 23. В картере 9 на двух шарикоподшипниках 8 вращается коленчатый вал 7. В переднем торце коленчатого вала установлен уплотнитель 4, поджимаемый пружиной 5 к штуцеру, по которому по трубке подводится масло от системы смазки двигателя под давлением 1-5 кгс/см. На коленчатом валу 7 установлены шатуны 11, связанные с поршнем 16 при помощи плавающих пальцев 14. От осевого перемещения пальцы в бобышках поршня фиксируются упорными кольцами. На головке поршня установлены два компрессионных кольца, на юбке одно маслосъемное. В верхней части блока 19 расположены седла пластинчатых впускных клапанов. Впускные клапаны толщиной 1 мм прижимаются к седлам пружинами и удерживаются от бокового смещения направляющими. В головке блока 17 установлены пластинчатые нагнетательные клапаны толщиной 1,4 мм, которые прижимаются к своим седлам пружинами.
Верхняя часть блока и головка компрессора имеют водяную рубашку и охлаждаются водой или антифризом, подводимыми к блоку из системы охлаждения
двигателя.
Масло к шатунным подшипникам компрессора, имеющим стале-баббитовые съемные вкладыши, поступает через уплотнитель 4 по каналам, выполненным в щеках коленчатого вала 7. Коренные шарикоподшипники 8, поршневые пальцы 14 и стенки цилиндров смазываются разбрызгиванием. Избыток масла через сливное отверстие в нижней крышке картера 9 компрессора стекает по трубке в масляный картер двигателя.
Компрессор здесь не имеет разгрузочного устройства, его отключение происходит при открытии атмосферного клапана регулятора давления, который соединяет нагнетательную магистраль компрессора с атмосферой.
Основные требования к компрессорам - это достаточная производительность, а также минимальная потребляемая мощность, минимальное количество масла в сжатом воздухе, малые габариты и масса, бесшумность работы, достаточная долговечность и минимальная трудоемкость технического обслуживания.
Производительность компрессора (количество сжатого воздуха, подаваемое компрессором в тормозной привод за 1 мин и приведенное к атмосферному давлению) и потребляемая им мощность зависят от рабочего объема компрессора, давления в приводе и частоты коленчатого вала. Производительность компрессора прямо пропорциональна частоте коленчатого вала и обратно пропорциональна давлению в приводе, а потребляемая мощность прямо пропорциональна обоим этим параметрам. Следует отметить, что в практике эксплуатации компрессор проверяется обычно только на производительность. В качестве критерия оценки производительности применяется давление сжатого воздуха, создаваемое компрессором в сосуде, из которого воздух выпускается в атмосферу через тарированное отверстие (дроссель). Компрессор должен создавать в воздушном баллоне, имеющем сообщение с атмосферой через дроссель диаметром 1,6 мм и длиной 3 мм, давление не ниже 6 кгс/см.
Количество масла в воздухе, подаваемом компрессором, определяется следующим образ
|
|
Типы оградительных сооружений в морском порту: По расположению оградительных сооружений в плане различают волноломы, обе оконечности...
Наброски и зарисовки растений, плодов, цветов: Освоить конструктивное построение структуры дерева через зарисовки отдельных деревьев, группы деревьев...
Особенности сооружения опор в сложных условиях: Сооружение ВЛ в районах с суровыми климатическими и тяжелыми геологическими условиями...
История развития пистолетов-пулеметов: Предпосылкой для возникновения пистолетов-пулеметов послужила давняя тенденция тяготения винтовок...
© cyberpedia.su 2017-2024 - Не является автором материалов. Исключительное право сохранено за автором текста.
Если вы не хотите, чтобы данный материал был у нас на сайте, перейдите по ссылке: Нарушение авторских прав. Мы поможем в написании вашей работы!