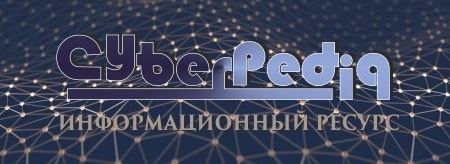
Своеобразие русской архитектуры: Основной материал – дерево – быстрота постройки, но недолговечность и необходимость деления...
Организация стока поверхностных вод: Наибольшее количество влаги на земном шаре испаряется с поверхности морей и океанов (88‰)...
Топ:
История развития методов оптимизации: теорема Куна-Таккера, метод Лагранжа, роль выпуклости в оптимизации...
Методика измерений сопротивления растеканию тока анодного заземления: Анодный заземлитель (анод) – проводник, погруженный в электролитическую среду (грунт, раствор электролита) и подключенный к положительному...
Интересное:
Как мы говорим и как мы слушаем: общение можно сравнить с огромным зонтиком, под которым скрыто все...
Национальное богатство страны и его составляющие: для оценки элементов национального богатства используются...
Средства для ингаляционного наркоза: Наркоз наступает в результате вдыхания (ингаляции) средств, которое осуществляют или с помощью маски...
Дисциплины:
![]() |
![]() |
5.00
из
|
Заказать работу |
|
|
Способ, качество и точность получения заготовки определяют объем работы, которую необходимо выполнить. Необходимо стремиться к наивысшему коэффициенту используемого материала, то есть максимально приближать тип и габариты заготовки к размеру и форме готовой детали в зависимости от ее изготовления.
При оформлении заготовки соблюдаем следующий порядок действий:
- тип заготовки подбирается с учетом вида изделия, экономии металла и рабочего объема;
- для всех поверхностей, обработанных по ГОСТ 7505-79 - припуски на обработку;
- выполняется чертеж заготовки, считающийся общепринятым.
Назначаем вид заготовки – поковка (рисунок 2).
Рисунок 2 – Заготовка детали
Выбор технологических баз и схем базирования
Выбор баз основан на следующих общих принципах:
1. При обработке деталей, полученных заливкой или герметизацией, неформованные грани можно использовать только на первой операции.
2. В первой практике полностью необработанные забои используются для пустующих участков, которые не были разработаны как технологическая основа.
3. Точность работы будет максимальной, когда во всех операциях будут применяться одни и те же принципы.
4. При использовании в качестве технологической основы проектно-измерительной базы рекомендуется соблюдать перекрытие оснований.
5. Выбранные основы должны обеспечивать простую и надежную конструкцию устройства, упрощая установку и снятие деталей.
На рисунке 3 представлены базы для обработки детали фланец.
Рисунок 3 – Базы обработки детали
Выбор методов обработки
Когда предусмотрен способ обработки, необходимо обеспечить, чтобы многие поверхности поверхности обрабатывались одинаково, разработать операции с наибольшим сочетанием этих конкретных поверхностей, уменьшить общее количество операций, продолжительность обработки, чтобы повысить эффективность и точность работы.
|
В этом разделе мы предоставим вам выбор и обоснование способов обработки всех частей деталей, исходя из технических требований к чертежу деталей, типа граней, качества заготовки, типа продукт; когда мы выбираем методы обработки, мы будем использовать справочные таблицы для оценки экономической точности обработки, которые включают информацию о технических возможностях различных методов обработки.
Таблица 4 – Способы обработки поверхностей детали фланец
поверхность | квалитет | шероховатость | метод |
Ø180e8 | e8 | Ra 1,25 | Обтачивание и шлифование однократное |
Ø150h9 | H9 | Ra 2,5 | Двукратная расточка и шлифование |
Ø78 | h14 | Rz 40 | Расточка однократная |
Ø108 | H14 | Rz 40 | Точение |
Ø179 | H14 | Rz 40 | Точение |
Ø6h7 | h7 | Ra 1,25 | Сверление и двукратное развертывание |
18, 70, 20 | H14 | Rz 40 | Подрезка торца |
7 Выбор варианта технологического маршрута
005 Токарная с ЧПУ 16К20Ф3С32
- точить поверхность Ø180 с допуском на шлифование
- подрезать торец Ø180
- расточить отверстие Ø150 с образованием фаски
- подрезать торец Ø150
- расточить отверстие Ø78 с образованием фаски
010 Токарная с ЧПУ 16К20Ф3С32
- точить поверхность Ø108
- подрезать торец Ø108
- подрезать торец Ø179
- точить поверхность Ø179
- точить фаску в отверстии Ø78
015 Сверлильная с 2Н118
- сверлить отверстие Ø5,7
- развернуть отверстие Ø5,9
- развернуть отверстие Ø6 окончательно
020 Сверлильная с 2Н118
- сверлить 4 отверстия Ø5,7 последовательно
- развернуть 4 отверстия Ø 5,9 последовательно
- развернуть 4 отверстия Ø6 последовательно и окончательно
025 Закалочная
- закалить Ø150 на длине 19 до HRCэ 42…51
030 Шлифовальная круговая 3М152
- шлифовать поверхность Ø180е8
035 Внутришлифовальная 2К229
|
- шлифовать поверхность Ø150
040 Слесарная
045 Моющая
050 Контрольная
Расчет режимов резания
Произведём расчёт обработки Æ 108 мм точением.
Глубина резанья:
По выбранной глубине резанья и шероховатости назначаем подачу S=0,6-1,2 мм/об
Выбираем значение подачи по паспортным данным стакнкаS=0,8 мм/об.
Определяем скорость резанья при заданной стойкости резца, глубине резанья и подачи:
(по справочнику).
Определяем частоту вращения шпинделя:
Корректируем частоту вращения шпинделя по станку:
.
Определяем фактическое значение скорости:
Определяем по справочнику силу резанья:
Определяем мощность резанья:
Обработка на станке возможна если выполняется условие:
Условие выполняется, резание возможно.
Определяем основное технологическое время Т0:
где l0- длина обрабатываемой поверхности,
l1-величина врезания инструмента при точении,
l2-величина перебега инструмента.
где i- количество проходов.
Определяем минутную подачу:
Произведём расчёт обработки торца Æ 180 точением.
Глубина резанья:
По выбранной глубине резанья и шероховатости назначаем подачу S=0,6-1,2 мм/об
Выбираем значение подачи по паспортным данным стакнка S=0,8 мм/об.
Определяем скорость резанья при заданной стойкости резца, глубине резанья и подачи:
(по справочнику).
Определяем частоту вращения шпинделя:
Корректируем частоту вращения шпинделя по станку:
.
Определяем фактическое значение скорости:
Определяем по справочнику силу резанья:
Определяем мощность резанья:
Обработка на станке возможна если выполняется условие:
Условие выполняется, резание возможно.
Определяем основное технологическое время Т0:
где l0- длина обрабатываемой поверхности,
l1-величина врезания инструмента при точении,
l2-величина перебега инструмента.
где i- количество проходов.
Определяем минутную подачу:
Произведём расчёт расточки отверстия Æ 150 мм точением.
Глубина резанья:
По выбранной глубине резанья и шероховатости назначаем подачу S=0,6-1,2 мм/об
Выбираем значение подачи по паспортным данным стакнка S=0,8 мм/об.
Определяем скорость резанья при заданной стойкости резца, глубине резанья и подачи:
(по справочнику).
Определяем частоту вращения шпинделя:
Корректируем частоту вращения шпинделя по станку:
|
.
Определяем фактическое значение скорости:
Определяем по справочнику силу резанья:
Определяем мощность резанья:
Обработка на станке возможна если выполняется условие:
Условие выполняется, резание возможно.
Определяем основное технологическое время Т0:
где l0- длина обрабатываемой поверхности,
l1-величина врезания инструмента при точении,
l2-величина перебега инструмента.
где i- количество проходов.
Определяем минутную подачу:
Произведём расчёт обработки торца Æ 150 мм точением.
Глубина резанья:
По выбранной глубине резанья и шероховатости назначаем подачу S=0,6-1,2 мм/об
Выбираем значение подачи по паспортным данным стакнка S=0,8 мм/об.
Определяем скорость резанья при заданной стойкости резца, глубине резанья и подачи:
(по справочнику).
Определяем частоту вращения шпинделя:
Корректируем частоту вращения шпинделя по станку:
.
Определяем фактическое значение скорости:
Определяем по справочнику силу резанья:
Определяем мощность резанья:
Обработка на станке возможна если выполняется условие:
Условие выполняется, резание возможно.
Определяем основное технологическое время Т0:
где l0- длина обрабатываемой поверхности,
l1-величина врезания инструмента при точении,
l2-величина перебега инструмента.
где i- количество проходов.
Определяем минутную подачу:
Произведём расчёт расточки Æ 74 мм точением.
1)Глубина резанья:
2)По выбранной глубине резанья и шероховатости назначаем подачу
S=0,6-1,2 мм/об
Выбираем значение подачи по паспортным данным стакнкаS=0,8 мм/об.
3)Определяем скорость резанья при заданной стойкости резца, глубине резанья и подачи:
(по справочнику).
4)Определяем частоту вращения шпинделя:
5)Корректируем частоту вращения шпинделя по станку:
.
6)Определяем фактическое значение скорости:
7)Определяем по справочнику силу резанья:
8)Определяем мощность резанья:
Обработка на станке возможна если выполняется условие:
Условие выполняется, резание возможно.
9)Определяем основное технологическое время Т0:
где l0- длина обрабатываемой поверхности,
|
l1-величина врезания инструмента при точении,
l2-величина перебега инструмента.
где i- количество проходов.
10) Определяем минутную подачу:
Нормирование одной операции
Расчёт норм времени проводим для операции 005.
Время на установку и снятие детали в трехкулачковом патроне с пневмозажимом при массе детали до 10 кг:
Туст.=0,33мин.
Время на открепление и закрепление детали (способ крепления: рукояткой пневматического зажима при массе детали до 10кг):
Тзакр. =0,024 мин.
Время на включение/выключение станка кнопкой:
Твкл. =0,01 мин.
Время на подвод и отвод инструмента к детали при обработке:
Тподв. =0,025 мин.
Время на измерение штангенциркулем:
1)диаметра Ø180 мм Тизм1 =0,16 мин.
2)толщины детали 70 мм Тизм2 =0,12 мин.
Вспомогательное время:
Твсп.=Туст+Тзакр.+Твкл.+Тподв.+ Тизм1+Тизм2 =
=0,33+0,024+0,01+0,025+0,16+0,12=0,669мин.
Оперативное время:
Топ=Твсп.+То=0,699+1,93=2,629 мин.
Время на техобслуживание рабочего места (составляет 10% от оперативного времени):
Ттех. =0,1∙Топ =0,1∙2,629=0,2629 мин.
Время на организационное обслуживание рабочего места (составляет 1,4% от оперативного времени):
Торг. =0,014∙Топ =0,014∙2,629=0,036 мин.
Время отдыха (составляет 7% от оперативного времени):
Тотдыха. =0,07∙Топ =0,07∙2,629=0,18 мин.
Подготовительно заключительное время составляет Тзаключ.=8 мин.
Штучно-калькуляционное время:
Тшт.к.=То+Твсп.+Ттех.+Торг.+Тотдыха+Тзаключ./n=
=1,93+0,699+0,2629+0,036+0,018+8/100=3,02 мин,
где n- количество деталей в партии, шт.
Заключение
В результате проведенной работы разработан технологический процесс изготовления детали «Фланец», при этом были учтены все существующие рекомендации и выбран наиболее оптимальный вариант технологического процесса, который способствует наименьшей себестоимости изготовления детали. При разработке курсового проекта были рассчитаны припуски на обработку заданной поверхности, а также режимы резания при растачивании этой поверхности и выбраны оптимальные варианты ремонта детали.
В результате получены практические навыки выбора оптимального варианта процесса изготовление, что важно для дальнейшей работы в области конструирования и способствует развитию инженерного подхода к проектированию машин, механизмов и отдельных деталей.
Список используемой литературы
1. Косилова А.Г., Мещерякова Р.К. Справочник технолога машиностроителя в 2-х т. – 4-е изд., перераб. и доп. – М.: Машинострорение, 1985. – ил.
2. Косилова А.Г., Мещерякова Р.К., Калинин М.А. Точность обработки. Справочник технолога. М., «Машиностроение», 1976. 288с. с ил.
3. Матвеев В.В., Тверской М.М., Бойков Ф.И. и др. Размерный анализ технологических процессов – М.: Машиностроение, 1982. – 264 с., ил.
|
4. Сергеев А. В. Размерный анализ технологических процессов изготовления деталей машин: практикум по дисц. "Технология машиностроения" / А. В. Сергеев; ТГУ; каф. "Оборудование и технологии машиностроительного производства". - Тольятти: ТГУ, 2008. - 83 с.
5. Сергеев А. В. Проектирование рациональных технологических процессов с применением размерного анализа: учеб.-метод. пособие по дисц. "Технология машиностроения" / А. В. Сергеев; ТГУ; каф. "Оборудование и технологии машиностроительного производства". - Тольятти: ТГУ, 2008. - 89 с.
6. Расторгуев Д. А. Разработка плана изготовления деталей машин: учеб.-метод. пособие / Д. А. Расторгуев; ТГУ; Ин-т машиностроения; каф. "Оборудование и технологии машиностроит. пр-ва". - ТГУ. - Тольятти: ТГУ, 2013. - 51 с.
7. Расторгуев Д. А. Проектирование технологических операций [Электронный ресурс]: электрон. учеб.-метод. пособие / Д. А. Расторгуев; ТГУ; Ин-т машиностроения; каф. "Оборудование и технологии машиностроит. пр-ва". - Тольятти: ТГУ, 2015. - 140 с.
Приложение А
|
|
Механическое удерживание земляных масс: Механическое удерживание земляных масс на склоне обеспечивают контрфорсными сооружениями различных конструкций...
Состав сооружений: решетки и песколовки: Решетки – это первое устройство в схеме очистных сооружений. Они представляют...
Таксономические единицы (категории) растений: Каждая система классификации состоит из определённых соподчиненных друг другу...
Типы сооружений для обработки осадков: Септиками называются сооружения, в которых одновременно происходят осветление сточной жидкости...
© cyberpedia.su 2017-2024 - Не является автором материалов. Исключительное право сохранено за автором текста.
Если вы не хотите, чтобы данный материал был у нас на сайте, перейдите по ссылке: Нарушение авторских прав. Мы поможем в написании вашей работы!