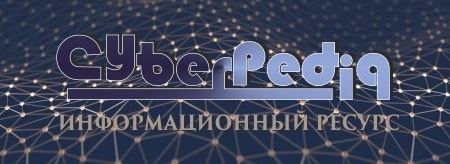
Автоматическое растормаживание колес: Тормозные устройства колес предназначены для уменьшения длины пробега и улучшения маневрирования ВС при...
Механическое удерживание земляных масс: Механическое удерживание земляных масс на склоне обеспечивают контрфорсными сооружениями различных конструкций...
Топ:
Марксистская теория происхождения государства: По мнению Маркса и Энгельса, в основе развития общества, происходящих в нем изменений лежит...
Проблема типологии научных революций: Глобальные научные революции и типы научной рациональности...
Интересное:
Национальное богатство страны и его составляющие: для оценки элементов национального богатства используются...
Мероприятия для защиты от морозного пучения грунтов: Инженерная защита от морозного (криогенного) пучения грунтов необходима для легких малоэтажных зданий и других сооружений...
Берегоукрепление оползневых склонов: На прибрежных склонах основной причиной развития оползневых процессов является подмыв водами рек естественных склонов...
Дисциплины:
![]() |
![]() |
5.00
из
|
Заказать работу |
|
|
Загрязняющие вещества | Защитные мероприятия | Примечание |
Технические моющие средства | применение технологических процессов мойки деталей и узлов с замкнутым циклом | канализация отработанных растворов через отстойники и очистные сооружения |
Отработанные смазки | сбор в технологические емкости, утилизация (регенерация) | |
Лакокрасочные материалы (потери при транспортировке, хранении, приготовлении, нанесении покрытий) | сокращение потерь, совершенствование технологии нанесения покрытий | |
Технологические отходы производства | соблюдение порядка накопления, транспортирования, обезвреживания и захоронения токсичных промышленных отходов. сбор, утилизация вторичного сырья |
Ремонт
4.1. Общие требования
4.1.1. Новые детали и узлы, устанавливаемые на думпкары, взамен забракованных, при выполнении ремонтных работ должны быть изготовлены на вагоностроительных предприятиях или предприятиях, освоивших их производство в соответствии с требованиями действующих нормативных документов по постановке на производство продукции производственно-технического назначения. На запасные части и комплектующее оборудование, подлежащие обязательному подтверждению соответствия должны быть представлены соответствующие документы (сертификат, декларация и др.).
4.1.2. Восстановление деталей думпкаров сваркой и наплавкой, а также приемку после сварочных и наплавочных работ проводить в соответствии с требованиями РД ВНИИЖТ-059/01-2019.
4.1.3. Сварочные работы в местах, имеющих неогнестойкие элементы (деревянные, резиновые детали и т.д.), проводить с обязательной разборкой и удалением этих элементов из мест возможного соприкосновения с нагреваемым металлом, защитой от попадания брызг расплавленного металла, касания электродом.
|
4.1.4. Неогнестойкие элементы, расположенные вблизи места сварки, во избежание попадания на них брызг расплавленного металла или касания электродом, изолировать огнезащитным материалом.
4.1.5. Сопрягаемые плоскости металлических и деревянных деталей (не антисептированных) перед соединением их между собой прокрашивают или грунтуют.
4.1.6. При креплении деталей запрещается оставлять или устанавливать вновь болты и гайки, имеющие изношенную, или забитые грани, а также ставить болты, не соответствующие размерам отверстий и соединяемым частям или имеющие разнотипную с гайкой резьбу;
применять крепежные детали, не удовлетворяющие техническим требованиям, стандартам, комплекту конструкторской документации;
прожигать отверстия в деталях.
4.1.7. Шплинты и чеки на болты или валики ставят новые, типовые (стандартизированные).
При отсутствии специальных требований они должны отстоять от гайки или шайбы не более чем на 3 мм. Концы шплинтов и чек разводят под углом не менее 90°. Ослабшие и нестандартные заклепки и ШОГ (штифт с обжимной головкой) соединения заменяют.
Запрещается:
заменять предусмотренные конструкцией вагона заклепочные и ШОГ соединения на сварные или болтовые;
ставить простые гайки вместо корончатых, предусмотренных чертежом (техническими условиями);
производить подчеканку, заварку и подтягивание заклепок и ШОГ соединения;
оставлять без грунтовки металлические части кузова и рамы, в местах прилегания снятых для замены деталей;
применять материалы, не имеющие сертификата соответствия.
4.1.8. Заклепки должны соответствовать ГОСТ 10299-80, ГОСТ 10300-80, а также диаметру отверстия, и плотно скреплять соединяемые детали. Головки заклепок должны быть полномерными, без зарубок, трещин, вмятин, плотно прилегать к соединяемым деталям и располагаться центрально по отношению к оси стержня. Головки потайных заклепок не должны выступать над поверхностью листа более чем на 1мм.
|
4.1.9. Поврежденные доски пола заменить на новые, изготовленные из сосны, ели, лиственницы толщиной 60 - 75 мм. Доски настила пола должны быть плотно прижаты друг к другу. Бруски и доски должны быть пропитаны антисептиком по ОСТ 38.01117-76.
4.1.10. При ремонте деревянных деталей мелкие механические повреждения досок и брусьев, местные вмятины, отколы и т.п., не нарушающие сопряжения с другими деталями, допускается оставлять без ремонта.
4.2. Автосцепное устройство
4.2.1. Ремонт автосцепного устройства производить в соответствии с Инструкцией по ремонту и обслуживанию автосцепного устройства подвижного состава железных дорог, Типовым технологическим процессом ремонта автосцепного устройства ТК-289 и Инструкцией по сварке и наплавке при ремонте грузовых вагонов РД ВНИИЖТ-059/01-2019.
4.3. Тормозное оборудование
4.3.1. Ремонт тормозного оборудования производить в соответствии с требованиями N 732-ЦВ-ЦЛ.
4.4. Ходовые части
4.4.1. Тележки из-под вагонов выкатить, промыть в моечной машине и разобрать. Детали тележек очистить от грязи, продуктов коррозии и осмотреть.
4.4.2. Ремонт тележек производить в соответствии с требованиями РД 32 ЦВ 052-2009 "Ремонт тележек грузовых вагонов тип 2 по ГОСТ 9246 с боковыми скользунами зазорного типа. Общее руководство по ремонту".
4.4.3. Ремонт тележек моделей 18-9855, 18-194-1 с осевой нагрузкой 25 тс не включенных в РД 32 ЦВ 052-2009 "Ремонт тележек грузовых вагонов тип 2 по ГОСТ 9246 с боковыми скользунами зазорного типа. Общее руководство по ремонту", выполняется в соответствии с требованиями Руководства по ремонту 4701-09.00.00.000 РК "Тележка двухосная 18-9855, тип 3 ГОСТ 9246-2013" и Руководства по ремонту 194.00.000-1 РК "Тележка двухосная модель 18-194-1".
4.4.4. Осмотр и ремонт колесных пар проводить в соответствии с требованиями Руководящего документа по ремонту и техническому обслуживанию колесных пар с буксовыми узлами грузовых вагонов магистральных железных дорог колеи 1520 (1524) мм РД ВНИИЖТ 27.05.01-2017.
4.5. Нижняя рама
4.5.1. Нижнюю раму вагона, показанную на рисунке 4.1, очистить от грязи, отслоившейся краски, ржавчины, проверить состояние всех элементов. Ослабленные заклепки заменить. Сварные швы, имеющие трещины, разделать и заварить вновь в соответствии с требованиями Инструкции по сварке и наплавке при ремонте грузовых вагонов РД ВНИИЖТ-059/01-2019 и Руководства по капитальному ремонту грузовых вагонов РД 32 ЦВ 168-2017.
|
4.5.2. Нижняя рама вагона не должна иметь трещин и изломов.
Допускается не ремонтировать хребтовую балку с прогибами в горизонтальной и вертикальной плоскостях не более 25 мм.
Допускается оставлять без исправления прогибы по всей длине шкворневых, цилиндровых и торцевых балок нижней рамы в горизонтальной и вертикальной плоскостях не более 10 мм, при этом прогибы их консольных частей не должны превышать 5 мм. Прогиб кронштейна тормозного цилиндра допускается не более 5 мм.
Балки нижней рамы, имеющие прогибы более допустимых критериев изложенных в разделе 3 Требований по исключению из инвентаря грузовых вагонов, согласованных протоколом заседания Комиссии Совета по железнодорожному транспорту полномочных специалистов вагонного хозяйства железнодорожных администраций от 16 - 17 декабря 2008 г., восстановлению не подлежат.
4.5.3. Трещины и повреждения коррозией хребтовой, шкворневых, цилиндровых и концевых балок ремонтировать в соответствии с требованиями Инструкции по сварке и наплавке при ремонте грузовых вагонов РД ВНИИЖТ-059/01-2019.
4.5.4. Ударные розетки, упорные угольники автосцепного устройства, имеющие трещины и износ поверхностей, отремонтировать сваркой и наплавкой в соответствии с Инструкцией по сварке и наплавке при ремонте грузовых вагонов РД ВНИИЖТ-059/01-2019.
4.5.5. Предохранительные планки хребтовых балок между упорными угольниками поглощающего аппарата с износом не более 3 мм допускается восстанавливать наплавкой с последующей механической обработкой до чертежных размеров. Планки с износом более 3 мм заменить на новые.
4.5.6. Трещины и изломы упоров кузова нижней рамы ремонтировать сваркой с последующей установкой усиливающих накладок в соответствии с требованиями Инструкции по сварке и наплавке при ремонте грузовых вагонов РД ВНИИЖТ-059/01-2019.
4.5.7. Проверить состояние шкворневых и цилиндровых опор кузова и их крепления на раме.
При наличии трещин или излома уха опор кузова допускается ремонтировать не более двух несмежных шкворневых и цилиндровых опор путем приварки с двух сторон усиливающих типовых накладок толщиной 20 мм.
|
4.5.8. Отверстия в кронштейнах для валиков упорных тяг открывания бортов, разработанные по диаметру, ремонтировать наплавкой или установкой стальных втулок, с обваркой по периметру сплошным швом и последующей механической обработкой.
4.5.9. Пятники демонтировать с думпкара, проверить на отсутствие трещин. Пятники, имеющие трещины, ремонтировать по технологии, изложенной в технологических инструкциях ТИ-ТНП-2010 или ТИ-ТНП/Ш-2011, в зависимости от материала пятника.
Износ рабочих поверхностей пятника ремонтировать наплавкой с последующей механической обработкой до чертежных размеров, при условии, что глубина износа не превышает 7 мм.
Для повышения износостойкости наплавленного слоя рекомендуется использовать наплавочную проволоку марки СВ-10ХГ2 СМФ ТУ 0805-001-18486807-99 в среде углекислого газа.
1 - хребтовая балка; 2 - шкворневая балка; 3 - цилиндровая балка; 4 - торцевая балка; 5 - упор верхней рамы; 6 - шкворневая опора; 7 - цилиндровая опора; 8 - цилиндровый подшипник; 9 - цилиндровая скоба; 10 - кронштейн цилиндра; 11 - пятник; 12 - скользун; 13 - кронштейн упорной тяги механизма открывания бортов; 14 - кронштейн тормозного цилиндра
Рис. 4.1 - Нижняя рама
4.6. Верхняя рама
4.6.1. Верхнюю раму, показанную на рисунке 4.2, очистить от грязи, отслоившейся краски, ржавчины, проверить состояние металлических балок, кронштейнов, упоров, нижнего и верхнего металлических листов пола. Сварные швы, имеющие трещины, разделать и заварить в соответствии с требованиями Инструкции по сварке и наплавке при ремонте грузовых вагонов РД ВНИИЖТ-059/01-2019.
4.6.2. Трещины и изломы боковых, шкворневых, цилиндровых, упорных, продольных, поперечных балок и кронштейнов ремонтировать сваркой с последующей постановкой усиливающих накладок в соответствии с требованиями Инструкции по сварке и наплавке при ремонте грузовых вагонов РД ВНИИЖТ-059/01-2019.
4.6.3. Прогибы боковых и продольных балок верхней рамы в горизонтальной и вертикальной плоскости допускаются не более 25 мм. Прогибы по всей длине шкворневых, цилиндровых и поперечных балок в вертикальной и горизонтальной плоскостях должны быть не более 10 мм, при этом прогибы их консольных частей не должны превышать 5 мм.
Балки верхней рамы, имеющие прогибы более допустимых критериев изложенных в разделе 3 Требований по исключению из инвентаря грузовых вагонов, согласованных протоколом заседания Комиссии Совета по железнодорожному транспорту полномочных специалистов вагонного хозяйства железнодорожных администраций от 16 - 17 декабря 2008 г., восстановлению не подлежат.
|
4.6.4. Шкворневые и цилиндровые опорные оси (трубы) и оси подъёма кузова не должны иметь продольных и поперечных трещин и износов рабочей поверхности.
Оси с износом рабочих поверхностей по диаметру ремонтировать наплавкой с последующей механической обработкой или заменять новыми.
4.6.5. Отверстия петель для осей подъёма кузова и петель осей крепления продольных бортов, имеющие износ по диаметру ремонтировать наплавкой или установкой и обваркой втулок с последующей механической обработкой.
1 - балка боковая; 2 - балка шкворневая; 3 - балка цилиндровая; 4 - балка поперечная; 5 - балка поперечная; 6 - ось опорная шкворневая; 7 - ось опорная цилиндровая; 8 - петля бортов; 9 - деревянный настил; 10 - лист верхний; 11 - лист нижний; 12 - балка продольная; 13 - кронштейн; 14 - ось подъема кузова; 15 - козырек; 16 - балка упорная
Рис 4.2 - Рама верхняя
4.6.6. Верхний металлический лист верхней рамы демонтировать.
Доски и бруски деревянного настила перебрать, не отвечающие требованиям п. 4.1.9, 4.1.10, заменить.
4.6.7. Вмятины глубиной более 20 мм и разрывы верхнего и нижнего металлических листов пола выправить или ремонтировать установкой накладок с обваркой их сплошным швом по периметру.
Трещины зачистить, заварить и усилить накладками с обваркой сплошным швом по периметру. Накладки должны перекрывать поврежденное место не менее чем на 50 мм.
Края пробоин выправить. Лучевые трещины, идущие от пробоин, вырезать. Образовавшиеся отверстия закрыть с наружной стороны накладками, перекрывающими их не менее чем на 50 мм. Накладки приварить с наружной стороны сплошным, с внутренней стороны прерывистым швом.
4.7. Продольные борта
4.7.1. Трещины и изломы верхнего козырька, нижней обвязки, стоек и листов обшивки продольных бортов, приведенных на рисунке 4.3, ремонтировать сваркой с постановкой усиливающих накладок.
Допускается оставлять без исправления горизонтальные и вертикальные прогибы продольных бортов не более 50 мм.
4.7.2. Отверстия петель для крепления бортов на верхней раме и концевых петель механизма открывания бортов, имеющие износ более 3 мм, ремонтировать наплавкой или установкой втулок с последующей их обваркой и механической обработкой.
4.7.3. Отклонение от перпендикулярности концевых петель относительно листа обшивки борта допускается не более 3 мм.
4.7.4. Продольный борт в закрытом положении должен вплотную прилегать к полу и торцевым стенкам. Допускается зазор между полом кузова и бортом не более 20 мм, а бортом и торцовой стенкой у основания борта не более 10 мм. Для обеспечения зазора между торцовой стенкой и закрытым бортом допускается приварка к кромкам листа торцевой стенки на всю высоту борта планок шириной 30 - 40 мм и толщиной 8 - 10 мм; планки ставят с наружной стороны кузова и приваривают с двух сторон, катет шва 6 мм.
1 - козырек; 2 - гнутый профиль; 3 - внутренний лист; 4 - петля; 5 - концевая петля; 6 - нижняя обвязка; 7 - стойка
Рис. 4.3 - Борт продольный
4.8. Торцевые стенки
4.8.1. Листы торцевых стенок кузова, показанных на рисунке 4.4, имеющие прогиб до 50 мм, допускается не править. Поврежденные листы, козырек и стойки ремонтировать сваркой с постановкой усиливающих накладок.
4.8.2. Отверстия внутренних и наружных кронштейнов механизма открывания бортов, имеющие износ более 3 мм, ремонтировать наплавкой или запрессовкой втулок.
4.9. Механизм открывания бортов
4.9.1. Механизм открывания бортов, показанный на рисунке 4.5, разобрать. Погнутые рычаги и тяги выправить или заменить новыми, имеющие изломы, трещины и надрывы заменить. Валики шарниров с трещинами и изгибами заменить.
4.9.2. Износ валиков свыше 3 мм при суммарном зазоре между валиком и отверстием свыше 5 мм не допускается. Валики подлежат замене, а отверстия наплавке и механической обработке или запрессовке стальных втулок. Резьбу регулировочных тяг проверить и смазать универсальной смазкой УС-2 ГОСТ 1033. Пазы головок тяг, имеющие износ свыше 3 мм, наплавляют и обрабатывают.
Резьбу регулировочных тяг проверяют и смазывают графитной смазкой ГОСТ 3333.
4.9.3. Отремонтированные регулировочные тяги с головками испытать на растяжение под нагрузкой 196 кН (20 тс) в течение времени необходимого для осмотра. При этом осуществлять остукивание деталей легкими ударами молотка по ГОСТ 2310-77. При испытаниях длина навинчивания головки на тягу должна быть не более 55 мм (не далее контрольного отверстия 5 мм на головке). Испытания проводить на стенде, отвечающем требованиям N 736-2010 ПКБ ЦВ.
4.9.4. Кронштейны торцевых стенок для механизма открывания бортов осмотреть, проверить на прочность крепления к раме. Между опорной поверхностью упорного кронштейна и нижней кромкой горизонтального рычага при закрытом борте должен быть зазор от 2 до 5 мм.
1 - крайняя стойка; 2 - съемный лист; 3 - козырек; 4 - внутренний лист;
5 - внутренний кронштейн; 6 - средняя стойка; 7 - поручень-ступенька;
8 - наружный кронштейн
Рис. 4.4 - Стенка торцевая
1 - тяга упорная; 2 - рычаг; 3 - тяга регулировочная; 4, 5, 6, 7, 8 - валики
Рис. 4.5 - Механизм открывания бортов
4.10. Цилиндры подъёма
4.10.1 Показанные на рисунке 4.6 цилиндры подъёма, демонтировать с вагона, разобрать и промыть.
4.10.2. На корпусе цилиндра подъема не допускаются:
риски и задиры на рабочей поверхности (зеркала) рубашек и корпусов цилиндров;
овальность и износ по внутреннему диаметру более 3 мм;
коррозия, неравномерный износ рабочей поверхности;
механические повреждения элементов (трещины, отколы, вмятины и т.д.);
осевшие или лопнувшие пружины штоков;
отклонение рабочей поверхности от цилиндричности более 3 мм;
износы опорных приливов более 5 мм по диаметру.
4.10.3. Допускается производить восстановление корпусов, крышек и днищ цилиндров правкой, сваркой, наплавкой с последующей механической обработкой.
4.10.4. Отклонение от цилиндричности рабочих поверхностей и износ поверхностей наружного диаметра поршня более 3 мм ремонтировать наплавкой с последующей механической обработкой.
4.10.5. Овальные отверстия в штоке поршня, имеющие износ более 3 мм, ремонтировать наплавкой с последующей механической обработкой.
4.10.6. Поршень цилиндра со штоком и пружиной разобрать, осевшие более чем на 10 мм или лопнувшие пружины заменить. Изношенные направляющие ребра и поверхности штоков поршня, упирающиеся в рога опрокидывания и запоры, а также направляющие трубы поршня восстановить наплавкой с последующей механической обработкой до размеров, указанных в рабочих чертежах.
4.10.7. Заусеницы на штоке поршня зачистить шлифовальной шкуркой 2С П1 15А М40 ГОСТ 6456.
4.10.8. Зазор между штоком поршня и горловиной крышки цилиндра не должен превышать 6 мм. При большем зазоре отверстие горловины наплавить и обработать до чертежных размеров.
4.10.9. Резиновые манжеты поршня, имеющие трещины и разрывы, заменить. Новые и исправные резиновые манжеты перед постановкой на поршни смазать смазкой ЖТ-79Л ТУ 0254-002-01055954-01 или ПЛАСТМА-75 ТУ 0254-006.1742726-05.
4.10.10. Уплотнительные прокладки потерявшие упругость или имеющие вырывы, разрывы и трещины заменить новыми. Перед постановкой прокладки покрыть смазкой ЖТ-79Л или ПЛАСТМА-75 или универсальной смазкой УС-2 ГОСТ 1033.
1 - корпус; 2 - крышка; 3 - днище; 4 - поршень; 5 - шток; 6 - манжета;
7 - цапфа; 8, 9, 10 - прокладка
Рис. 4.6 - Цилиндр подъема
4.10.11. Отремонтированные цилиндры разгрузки одинарного или двойного действия, перед постановкой на вагон должны подвергаться гидравлическим испытаниям на прочность давлением не менее 0,9 МПа (9 кгс/см2) в следующем порядке:
установить цилиндр на стенд, обеспечивающий выход штока не более 930 мм, подключить к жидкостной линии и плавно поднять давление до 0,9 МПа (9 кгс/см2), выдерживая его не менее 3 мин;
снизить давление до рабочего 0,6 МПа (6 кгс/см2) и осмотреть цилиндр, обстукивая сварные швы деревянным молотком массой до 1 кг. Увеличение давления и снижение его до рабочего производить постепенно;
давление, равное рабочему, поддерживать в течение времени, необходимого для осмотра цилиндра.
Цилиндр считается выдержавшим испытание, если:
в элементах цилиндра не оказалось признаков разрыва;
отсутствует утечка в разъёмных соединениях.
4.10.12. После испытания на цилиндр разгрузки нанести трафарет о проведённых гидравлических испытаниях с последующей записью в журнале произвольной формы, согласованном с местным органом Госгортехнадзора.
4.11. Пневмосистема разгрузки
4.11.1. Пневматическое устройство механизма опрокидывания демонтировать с вагона, разобрать при необходимости гидравлического испытания давлением 0,9 МПа (9 кгс/см2) в течение 5 минут. При испытании не допускается просачивание воды через стенки резервуара и швы. Запрещается заварка пороков в сварных швах. Заварка трещин по основному металлу резервуаров и приварка накладок запрещаются.
4.11.2. Трубопроводы магистрали системы разгрузки, показанные на рисунке 4.7, разобрать и осмотреть. Трубы, имеющиеся трещины, разрывы и срывы резьбы заменить. Допускается приварка новых частей стальных труб взамен поврежденных при условии, что расстояние между сварными стыками труб не менее 0,5 м.
Новые части трубопроводов изготавливать из стальных усиленных оцинкованных труб по ГОСТ 3262-75.
Радиусы гиба труб должны быть не менее:
70 мм для труб диаметром 3/4";
120 мм для труб диаметром 1";
500 мм для труб диаметром 11/4".
4.11.3. Соединительные рукава, имеющие трещины, надрывы, расслоение, потертости и прорыв слоя матерчатой прокладки, заменить на новые. После ремонта соединительные рукава для проверки на прочность должны подвергаться гидравлическому испытанию под давлением воды в них (1,2 0,02) Мпа (12
0,2) кгс/см2 с выдержкой под давлением от 1,5 до 2 минут.
Соединительный рукав считается выдержавшим испытание если не было обнаружено:
срыва деталей;
просачивания воды во время испытания;
надрывов резинотекстильной трубки.
Для проверки на герметичность соединительные рукава подлежат пневматическому испытанию с выдержкой под давлением воздуха в них (0,6+0,05) Мпа (6+0,5) кгс/см2 при полном их погружении в ванну с водой.
Соединительный рукав считается выдержавшим испытание, если в течение 1 минуты не было обнаружено выделения пузырьков воздуха в любой части соединительного рукава. При обнаружении пузырьков воздуха на поверхности резинотекстильной трубки необходимо соединительный рукав выдержать под давлением в ванне с водой до 10 минут и, если выделение пузырьков на поверхности резинотекстильной прекратится, считать его выдержавшим испытание, в ином случае соединительные рукав считается не выдержавшим испытание.
4.11.4. Снятое с вагона тормозное оборудование ремонтируют в соответствии с требованиями Общего руководства по ремонту тормозного оборудования вагонов N 732-ЦВ-ЦЛ.
4.11.5. Воздухозамедлители разобрать, очистить и промыть.
Корпус воздухозамедлителя, а также кронштейн, сектор и направляющую, имеющие трещины и изломы, заменить. Манжеты или резиновые прокладки воздухозамедлителя заменить.
Воздухозамедлители после ремонта должны быть испытаны на герметичность сжатым воздухом давлением от 0,6 до 0,7 Мпа (от 6 до 7 кгс/см2):
для проверки герметичности соединения крышки пружины с корпусом необходимо провести обмыливание соединения и подать сжатый воздух в отверстие "к разгрузочной магистрали";
для проверки герметичности перекрытия вертикальными клапаном канала корпуса необходимо сектор установить его тонкой частью под горизонтальный клапан, провести обмыливание отверстия в "атмосферу" и подать сжатый воздух в отверстие "к разгрузочной магистрали";
для проверки герметичности соединения кронштейна с корпусом и герметичности перекрытия горизонтальным клапаном канала в кронштейне необходимо сектор установить тонкой частью под клапан, провести обмыливание соединения кронштейна с корпусом и отверстие "к цилиндрам разгрузки", после чего подать сжатый воздух в отверстия "к разгрузочной магистрали" и "к крану разгрузки";
для проверки герметичности перекрытия поршнем канала в корпусе необходимо установить сектор тонкой частью под горизонтальный клапан, провести обмыливание отверстия "в атмосферу" и подать сжатый воздух в отверстия "к разгрузочной магистрали" и "к крану разгрузки";
для проверки герметичности соединения крышки с корпусом и манжеты поршня необходимо провести обмыливание фланцевого соединения крышки с корпусом и отверстия "в атмосферу", после чего подать сжатый воздух в отверстие "к крану разгрузки".
1 - трубопровод магистрали системы разгрузки; 2 - цилиндр подъема;
3 - воздухозамедлитель; 4 - кран управления разгрузкой; 5 - кран концевой
Рис. 4.7 - Схема пневмосистемы разгрузки
Сборка
5.1. Сборка нижней рамы
5.1.1. Установить на нижнюю раму, показанные на рисунке 4.1, шкворневые и цилиндровые опоры, упоры верхней рамы и пятники в соответствии с требованиями конструкторской документации на вагон.
5.1.2. Установить автосцепное устройство в соответствии с требованиями Инструкции по ремонту и обслуживанию автосцепного устройства подвижного состава железных дорог.
5.1.3. Установить тормозное оборудование в соответствии с требованиями Общего руководства по ремонту тормозного оборудования вагонов 732-ЦВ-ЦЛ.
5.1.4. Установить воздухозамедлители, краны управления, концевые краны, а также трубопроводы пневмосистемы разгрузки.
5.2. Сборка верхней рамы
5.2.1. Уложить доски пола и поджать их клиньями, после чего сбить клинья гвоздями.
Поставить, подогнать и приварить верхний металлический лист пола.
5.2.3. Установить и приварить торцевые стенки, если они были демонтированы для ремонта.
5.2.4. Собрать механизм открывания продольных бортов, завести его в торцевую стенку и закрепить рычаги центральным валиком. Установить предохранительную планку.
5.3. Сборка и испытание цилиндра подъёма
5.3.1. Цилиндр подъёма собрать в следующей последовательности:
соединить днище и прокладку с корпусом цилиндра болтами;
на поршень надеть манжету, шток и закрепить его;
поршень со штоком установить в корпус цилиндра;
установить крышку с прокладками и закрепить болтами.
5.3.2. Помимо гидравлических испытаний на прочность по п. 4.10.11 настоящего Руководства, цилиндр испытать на герметичность плавной подачей воздуха до давления 0,55 МПа (5,5 кгс/см2) при поднятом до размера рабочего хода поршне. После достижения давления, равного 0,55 МПа (5,5 кгс/см2), перекрыть магистраль подачи воздуха к цилиндру. Падение давления воздуха в цилиндре не должно превышать 0,02 МПа (0,2 кгс/см2) в течение 5 мин.
5.4. Сборка вагона
5.4.1. Отремонтированные и собранные тележки, нижняя рама, верхняя рама, цилиндры подъема и другие узлы и детали вагона подаются в вагоносборочный участок.
5.4.2. При сборке вагона необходимо:
установить тележки на позиции сборки вагона;
проверить наличие смазки, указанной в приложении 3, подпятников и скользунов тележек;
подклинить крайние колёсные пары тележек;
опустить нижнюю раму на тележки, соединить тормозную рычажную передачу вагона и тележек в соответствии с требованиями "Общего руководства по ремонту тормозного оборудования вагонов" 732-ЦВ-ЦЛ.
установить цилиндры подъёма на нижнюю раму;
установить скобы цилиндровые, соединить цилиндры подъёма кузова гибкими шлангами с пневматической системой разгрузки;
установить верхнюю раму в сборе на нижнюю раму, соединить штоки цилиндров подъёма с осями кронштейнов подъёма верхней рамы и упорные тяги механизмов открывания бортов с их кронштейнами на нижней раме;
установить продольные борта на верхнюю раму, соединить осями петли бортов с петлями верхней рамы, соединить концевые петли бортов с регулируемыми тягами механизмов открывания бортов.
5.5. Требования к сборке вагона
5.5.1. Продольный борт вагона в закрытом положении должен вплотную прилегать к полу и торцевым стенкам. Местный зазор между полом кузова и бортом должен быть не более 20 мм, а бортом и торцевой стенкой у основания борта не более 10 мм. Для обеспечения минимального зазора между торцовой стенкой и закрытым бортом допускается приварка к кромкам листа торцевой стенки на всю высоту борта планок шириной 30 - 40 мм и толщиной 8 - 10 мм.
5.5.2. Между опорной поверхностью кронштейна и нижней кромкой отверстия рычага при закрытом борте должен быть зазор от 2 до 5 мм.
5.5.3. На собранном вагоне цапфы цилиндров подъёма должны плотно прилегать к нижней части цилиндровых подшипников нижней рамы. Допускаются местные зазоры не более 3 мм. В горизонтальной плоскости зазор между цапфой и цилиндровым подшипником не контролируется.
5.5.4. Суммарный зазор между скользунами нижней рамы и тележки должен быть в пределах от 6 до 12 мм. Отсутствие зазоров между скользунами, расположенными по диагонали не допускается.
Величина суммарного зазора по диагонали должна быть не менее 6 мм.
Для регулировки зазоров применяют регулировочные прокладки из листовой стали толщиной 1,5 - 5,0 мм в количестве не более четырех.
5.5.5. Верхняя рама должна опираться на 8 точек нижней рамы, показанных на рисунке 5.1. Допускается зазор не более 8 мм между одной из шкворневых опорных осей верхней рамы и шкворневой опорой нижней рамы или зазор не более 10 мм между одной из цилиндровых осей верхней рамы и цилиндровой опорой нижней рамы. При зазоре более 8 мм или 10 мм между шкворневыми и цилиндровыми осями и опорами регулировку производить с помощью приварки подкладок соответствующей толщины, но не более одной подкладки, под каждую опору.
5.6. Регулировка и испытание механизмов наклона кузова и открывания бортов вагона
5.6.1. После сборки вагона необходимо произвести регулировку и испытание механизмов наклона кузова и открывания бортов. При этом необходимо:
подключить источник сжатого воздуха к разгрузочной магистрали;
наклонить кузов вагона до полного открывания продольного борта;
добиться с помощью регулируемых тяг механизма открывания бортов равномерного прилегания внутренних листов бортов к планкам торцевых стенок. При регулировке необходимо достичь синхронной работы двух механизмов открывания каждого борта, чтобы в транспортном положении все звенья обоих механизмов не имели слабины и находились в натянутом состоянии, зависание кузова на механизмах открывания бортов не допускается. При этом должны соблюдаться требования п. 5.5.5 настоящего Руководства;
при максимальном (45°) наклонном положении кузова опорные поверхности петель борта должны упираться в кронштейны петель верхней рамы, а механизмы открывания борта должны иметь слабину. При наличии натяжения механизма наварить пять планок размером 40x60 мм необходимой толщины на кронштейны петель верхней рамы под опорную поверхность петель борта;
проверить при наклоне кузова работоспособность механизмов наклона, открывания и закрывания бортов, пневматического оборудования, положение секторов на воздухозамедлителях;
проверить герметичность воздушной магистрали разгрузки соединений и приборов;
проверить величину угла наклона кузова (45 1)°.
В случае отказа в работе одного из механизмов, отключить от источника питания систему пневматики, выпустить воздух из системы.
Только после этого допускается приступить к устранению неисправностей механизмов.
При проверке герметичности наполнить воздухопровод сжатым воздухом давлением 0,6 МПа (6 кгс/см2) и перекрыть его. Места соединений трубопроводов обмазать мыльным раствором, осмотреть, образование мыльных пузырей не допускается. Падение давления воздуха не должно превышать 0,01 МПа (0,1 кгс/см2) в течение 5 мин. После окончания проверки выпустить сжатый воздух из пневматической системы и отключить ее от источника питания.
1, 2, 3, 4 - шкворневые опорные точки; 5, 6, 7, 8 - цилиндровые опорные точки
Рис. 5.1 - Опорные точки нижней рамы
Окрашивание и надписи
6.1. Подготовка поверхности под окрашивание, окрашивание и сушка должны соответствовать:
вагоны принадлежности ОАО "РЖД" требованиям, изложенным в Инструкции по окрашиванию грузовых вагонов при плановых видах ремонта" N 655-2010 ПКБ ЦВ-ВНИИЖТ, утвержденной распоряжением ОАО "РЖД" от 18 ноября 2010 г. N 2352р, и Схем окраски в фирменном стиле ОАО "РЖД" и идентификации вагонов собственности Центральной дирекции инфраструктуры, утвержденным Центральной дирекции инфраструктуры 25 октября 2016 г.;
собственные вагоны требованиям, изложенным в Положении об окраске собственных грузовых вагонов, утвержденного протоколом Совета по железнодорожному транспорту государств - участников Содружества от 6 - 7 мая 2014 г. N 60.
6.2. Знаки и надписи на вагонах должны соответствовать требованиям, изложенным в Альбоме-справочнике. Знаки и надписи на вагонах грузового парка железных дорог колеи 1520 мм N 632-2011 ПКБ ЦВ, утвержденным протоколом Совета по железнодорожному транспорту государств - участников Содружества от 16 - 17 октября 2012 г. N 57.
Приемка вагона из ремонта
7.1. Общие требования
7.1.1. В процессе ремонта вагона-самосвала мастера участков производят приёмку отремонтированных узлов и деталей по мере их готовности.
Приёмщик вагонов осуществляет контроль за качеством ремонта.
7.1.2. По окончании ремонта начальник вагоноремонтного предприятия или лица назначенные приказом руководителя вагоноремонтного предприятия (заместитель начальника, старший мастер), сдают отремонтированные вагоны приемщику вагонов.
7.1.3. При приемке контролируется:
наличие смазки в узле пятник-подпятник. Узел должен быть смазан смазкой КТСМ по ТУ 0254-110-01124328;
наличие подножек, поручней;
расстояние от упора головы автосцепки до грани розетки переднего упора. Размер должен быть не менее 120 мм при утопленном положении автосцепки и не более 140 мм при выдвинутом;
высота оси автосцепки над уровнем головок рельсов. Размер должен быть от 1080 до 1020 мм;
положение автосцепки относительно горизонтали. Отклонение автосцепки вниз (провисание) должно быть не более 10 мм, отклонение вверх не более 3 мм;
свободное перемещение автосцепки из среднего положения в крайнее от усилия одного человека. В исходное положение автосцепка должна возвращаться под действием собственной массы. Проверку выполняют, когда аппарат плотно прилегает дном корпуса к задним упорам и через упорную плиту к передним упорам;
длина блокировочной цепи. При перемещении автосцепки в горизонтальном направлении блокировочная цепь должна натянуться, когда расцепная цепь, натянувшись, повернет валик подъемника от его нормального положения против часовой стрелки на расстоянии от 20 до 30 мм, измерение по верхней кромке отверстия для крепления цепи в валике подъемника;
занижение фрикционных клиньев относительно опорной поверхности надрессорной балки должно быть 4 - 12 мм, завышение не допускается;
суммарный зазор между скользунами с обеих сторон каждой тележки должен быть в пределах от 6 до 12 мм;
суммарный зазор между скользунами по диагонали должен быть не менее 6 мм;
отсутствие зазоров между скользунами расположенными по диагонали не допускается;
наличие клейм ответственных деталей вагона;
наличие и исправность пломб в установленных местах, сроки освидетельствования сосудов, работающих под давлением, предохранительных устройств;
монтаж, крепление и состояние оборудования;
комплектность вагона;
оформляется документация на приёмку вагона из ремонта.
7.1.4. Все ответственные детали вагона: колесные пары, детали тележек, автосцепные устройства, тормозное оборудование, должны иметь соответствующие клейма, указывающие место и дату изготовления, ремонта и испытания. На раме, колесах, литых деталях тележек вагона должны быть коды государства-собственника в соответствии с требованиями РД 32 ЦВ 168-2017.
Выпуск вагонов из ремонта без клейм, с неясными клеймами или трафаретами на ответственных деталях запрещается.
7.2. Определение линейных размеров в ответственных местах вагона
7.2.1. Все контрольно-измерительн
|
|
Эмиссия газов от очистных сооружений канализации: В последние годы внимание мирового сообщества сосредоточено на экологических проблемах...
Археология об основании Рима: Новые раскопки проясняют и такой острый дискуссионный вопрос, как дата самого возникновения Рима...
Автоматическое растормаживание колес: Тормозные устройства колес предназначены для уменьшения длины пробега и улучшения маневрирования ВС при...
Типы сооружений для обработки осадков: Септиками называются сооружения, в которых одновременно происходят осветление сточной жидкости...
© cyberpedia.su 2017-2024 - Не является автором материалов. Исключительное право сохранено за автором текста.
Если вы не хотите, чтобы данный материал был у нас на сайте, перейдите по ссылке: Нарушение авторских прав. Мы поможем в написании вашей работы!