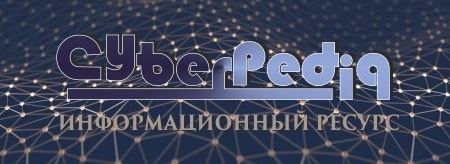
Семя – орган полового размножения и расселения растений: наружи у семян имеется плотный покров – кожура...
История развития хранилищ для нефти: Первые склады нефти появились в XVII веке. Они представляли собой землянные ямы-амбара глубиной 4…5 м...
Топ:
Особенности труда и отдыха в условиях низких температур: К работам при низких температурах на открытом воздухе и в не отапливаемых помещениях допускаются лица не моложе 18 лет, прошедшие...
Интересное:
Наиболее распространенные виды рака: Раковая опухоль — это самостоятельное новообразование, которое может возникнуть и от повышенного давления...
Влияние предпринимательской среды на эффективное функционирование предприятия: Предпринимательская среда – это совокупность внешних и внутренних факторов, оказывающих влияние на функционирование фирмы...
Распространение рака на другие отдаленные от желудка органы: Характерных симптомов рака желудка не существует. Выраженные симптомы появляются, когда опухоль...
Дисциплины:
![]() |
![]() |
5.00
из
|
Заказать работу |
|
|
Основные положения пуска и остановки производственного объекта при нормальных условиях. Особенности остановки и пуска в зимнее время
Подготовка к пуску и пуск установки производится по письменному распоряжению начальника цеха или его заместителя под непосредственным руководством начальника установки.
Общая подготовка установки к пуску производится в следующей последовательности:
1. Проверить законченность всех строительных и монтажных работ.
2. Тщательно осмотреть аппаратуру, трубопроводы и оборудование, проверить плотность крепления фланцев и задвижек, закрытие люков.
3. Все аппараты, трубопроводы и периодически действующие системы подвергнуть гидравлическому или пневматическому испытанию в соответствии с действующими правилами и нормами.
4. Проверить исправность и готовность к использованию системы паротушения, наличие и состояние противопожарного инвентаря, средств индивидуальной защиты.
5. Произвести проверку технической исправности систем АПС и ПАЗ с составлением акта.
Перед пуском установки включить все технологические блокировки. Отключение отдельных параметров ПАЗ (при выводе установки на режим) производится по отдельному распоряжению с записью в журнале инструктажа технологического персонала. (см. инстр.21А)
6. Включить в работу приточные и вытяжные вентиляторы, проверить исправность телефонной связи.
7. Проверить наличие и состояние технологической документации (вахтовых журналов, режимных листов, норм технологического режима, инструкций, графика лабораторного контроля, ПЛАС).
8. Проверить исправность промканализации и гидрозатворов.
9. Проверить, сняты ли все ранее установленные заглушки, кроме заглушек, которые необходимы для ведения технологического режима, и сделать соответствующую запись в журнале заглушек.
|
10. Отглушить дренажи и воздушники согласно «Перечня постоянно установленных заглушек»
11. Проверить состояние территории и рабочих мест.
12. Укомплектовать штат работниками, прошедшими обучение и аттестацию в установленном порядке и не имеющими медицинских противопоказаний.
13. Проверить соответствие установленного электрооборудования требованиям ПУЭ.
14. Все, не включаемое в работу оборудование и трубопроводы должно быть отключено от общей системы паспортными заглушками с регистрацией последних в специальном журнале.
15. Проверить все предохранительные устройства и клапаны, заземление аппаратов, оборудования.
16. Вытеснение воздуха из аппаратов, емкостей и трубопроводов перед пуском установки в общезаводской факельный трубопровод запрещается.
17. Подать отопительную воду в линии обогрева трубопроводов и аппаратов (в зимнее время).
18. Проверить сборку технологических схем по блокам.
19. Предупредить о предстоящем пуске:
а) диспетчера НПЗ и объединения;
б) старших операторов установок гидроочистки дизтоплива;
в) работников цеха КИП, электроцеха, УВК и ОСВ, СЩС;
г) работников ТСЦ, площадки «Д»;
д) работников УЭС по теплоснабжению;
е) лаборатории.
ж) ст. операторов установки Л-35/6, СЖГ, ТК-2, Л-35/11-1000, парк АВТ,
ГО-2,3, Л-16-1, ЭЛОУ-АВТ-4;
з) работников факельного хозяйства НХЗ и НПЗ.
и) работников цеха № 32,33, 9,51 о приеме водорода;
к) работников установки элементарной серы, о подаче сероводорода.
20. Принять на установку МЭА (ТЭА), инертный газ, водяной пар, топливо, воду, электроэнергию, воздух для контрольно-измерительных приборов.
21. Продуть азотом систему трубопроводов и аппаратов установки с выходом через воздушники аппаратов в атмосферу.
22. Произвести обкатку оборудования, насосов, компрессоров, воздуходу-вок, электродвигателей и вентиляторов.
|
6.1 Прием воды на установку
Вода на установку принимается по согласованию с диспетчером УВК и ОСВ и работниками водооборотного узла № 595. Открыть задвижки на выходе и входе воды со всех холодильников, воздушники на трубопроводах для выхода воздуха из системы.
Приоткрыть задвижки на магистральном трубопроводе воды на установку, как по 1 так и по II системам.
При появлении воды из воздушников закрыть их, проверить поступление воды на все холодильники, открыть задвижки на магистральных трубопроводах.
Прием пара на установку
Прием пара на установку осуществляется в следующей последовательности:
1. Опрессовать все паровые трубопроводы и обогревы.
2. Закрыть все задвижки на подаче пара в аппараты и трубопроводы.
3. Открыть все воздушники и дренажи на трубопроводе.
4. Согласовать прием пара на установку со службой УЭС по теплоснабжению и вызвать представителя.
5. Приоткрыть общую задвижку на линии пара на установку.
6. Сдренировать конденсат из трубопровода и при появлении сухого пара, дренажи и воздушники закрыть и открыть полностью задвижку на паропроводе.
7. По мере необходимости дать пар в подогреватели и обогревы.
8. Открыть сброс конденсата в линию КС.
Пуск установки
Пуск установки производится в следующей последовательности:
1. Подготовка к пуску.
2. Сушка, восстановление и сульфидирование катализатора.
3. Пуск блоков установки.
4. Пуск котла-утилизатора согласно инструкции № 9565.
6.5.1 Подготовка к пуску
6.5.1.1 Загрузка катализатора.
6.5.1.2 Испытание на герметичность.
6.5.1.3 Продувка и испытание на герметичность блоков подготовки, стабилизации и ректификации, очистки газов.
6.5.1.1 Загрузка катализатора
Перед загрузкой катализатора вся система (аппаратура, трубопроводы) должна быть тщательно очищена от всякого рода загрязнений, промыта, продута, высушена.
Продувку реакторного блока от загрязнений рекомендуется производить инертным газом.
Перед загрузкой в реакторы рекомендуется производить отсев мелочи от свежего катализатора. Отсев мелочи от катализатора, бывшего ранее в употреблении, обязателен. Рассев катализатора должен производиться на специальном оборудовании, предусматривающем улавливание катализаторной пыли.
|
Недопустимо попадание дождя или снега на катализатор во время загрузки, рассева, т.к. при этом резко снижается прочность катализатора.
Загрузка катализатора в реакторы должна производиться способом, предотвращающим его истирание или дробление.
Бочки с катализатором должны перемещаться с помощью механических приспособлений, катализатор из бочек пересыпается в загрузочные бункеры, которые поднимаются к горловине реактора.
При засыпке катализатора в реакторы используются тканевые рукава, погружаемые в реактор до уровня насыпаемого слоя.
Чтобы уменьшить давление на нижний слой катализатора и тем самым сохранить его прочность, а также для предотвращения износа катализатора должна предшествовать загрузка фарфоровых шаров Æ 20мм слоем 240мм.
Нежелательные термические реакции удается свести до минимума, заполняя катализатором максимальную часть объема реактора, насколько это совместимо с прочими проектными показателями.
Перед засыпкой из каждой бочки отбирается проба катализатора для составления средней пробы всей партии. Поверх катализатора засыпаются фарфоровые шары слоем 300мм. После окончания загрузки катализатора, монтажа верхних распределительных тарелок, закрыть люка, катализатор продуть в течение 30-40 минут путем подачи азота в трубопровод на входе в реактор с выходом в дымовую трубу по линии сброса газов регенерации.
Инертный газ должен быть достаточно сухим, чтобы не допустить образование на катализаторе капельной влаги. После продувки штуцер сброса газов регенерации отглушить и производить опрессовку реактора на рабочее давление совместно со всей системой блока.
Сушка катализатора производится азотом или водородсодержащим газом.
6.5.1.2 Испытание на герметичность реакторного блока
Перед включением в работу периодически действующих систем продувок и испытаний на плотность обеспечить тщательную проверку исправности трубопроводов, арматуры, аппаратов, приборов КИП и А и предохранительных устройств.
Испытание систем высокого давления гидроочистки производится путем опрессовки азотом на максимальное рабочее давление.
|
1. Е-9 воздушник до отсекающей задвижки.
прием насосов Н-13¸18®выкид Н-13¸18®межтр.пр-воТ-6(1).
2. Азот на выкид ЦК-1 ® межтр. пр-во Т-6(1) ® Т-7(1,2,3) ® Т-6® П-2®
Х-14
Р-1®Т-6® Т-18® Т-7(3шт) ®Т-6(1) ®ВХК-3® ®С-1®К-8®
Х-14а
® С-5а® С-5® свеча (воздушник)
3. С-1® Т-8(1) ®С-3® Х-15® К-9
4. Опрессовать систему гидроочистки на рабочее давление, включив воздушный компрессор на азоте по схеме: азот от ПК-5 ® Р-1.
Опрессовку системы высокого давления производить следующим образом: после заполнения аппаратов и трубопроводов инертным газом, равномерно, в течение часа, поднять давление до 0,5 МПа (5 кгс/см2) и прекратить подъем давления, произвести обмыливание фланцевых соединений.
В случае наличия дефектов, пропусков, давление в системе сбросить и устранить дефекты. После этого поднять давление до 0,5 МПа (5 кгс/см2).
При удовлетворительных результатах опрессовки продолжить плавный подъем давления со скоростью 0,5 МПа (5 кгс/см2) в час с остановками, обмыливанием и выявлением дефектов при давлении 1 МПа (10 кгс/см2), 2 МПа (20 кгс/см2), 3 МПа (30 кгс/см2), 4 МПа (40 кгс/см2) и далее до рабочего.
После опрессовки и устранения всех дефектов реактор готов к сушке катализатора.
Скорость подъема давления в системе производится со скоростью не более 5 кгс/см2 в час.
Выполнение всех операций по испытанию системы на герметичность производится согласно ПБ 09-540-03.
6.5.1.3 Продувка на проходимость и испытание на герметичность блоков установки
Опрессовка системы осуществляется инертным газом на максимальное рабочее давление из системы высокого давления.
Продувка аппаратов и трубопроводов всех блоков азотом до содержания кислорода не более 0,5% объемных.
А) Блок подготовки сырья.
1. Азот на прием насоса Н-1,2 ® прием Е-25 ® свеча.
2. Азот на прием насоса Н-1,2 ® трубное пространство Т-1® Т-1А® Т-2® К-1®ВХК-1® Е-1 ® свечи (воздушник)
Н-5,6 ® воздушник на клапане регулятора расхода
орошения К-1 (поз.210д).
Ф-1,2® Е-9® свеча (воздушник).
3. Азот на прием Н-7,8 ® обратным ходом ® К-1
® межтр. пр-во Т-2 ® П-1 ®К-1
® межтр. пр-во Т-1А ® ВХ-1 ® свеча на КРУ К-1
(поз.304е)
4. Азот с К-1®боковой погон®Н-9,10® Ф-1,2 ® Е-9® свеча (воздушник).
Опрессовать колонну и связанные с ней аппараты на 0,25 МПа (2,5кгс/см2).
Б) Блок ректификации.
Для продувки системы ректификации, а также для опрессовки используется азот из системы гидроочистки.
|
1. С-1® Т-8(1) ®С-3® Т-8(2) ® Т-3 ® Т-9 ® Т-11 ® К-3 ® Т-8(1,2) ® ВХК-5 ® ХК-5 ® Е-4 ® свеча.
2. Азот на прием Н-36,37®Т-4 ®Т-22® К-2® Т-4® Х-6®воздушник.
К-3
3. Азот на прием Н-36,37® К-2® К-12® свеча (воздушник)
4. Азот на прием Н-11,12 ® К-2®ВХК-2 ® ХК-1®свеча® Е-3®свеча
К-11®свеча
5. Азот на прием насосов Н-38,39 ® Т-18® П-5® К-3®Е-4® Х-15®К-9
ВХК-6® Е-5®свеча
6. К-3 ® К-4 ® К-5 ® ВХК-7® Е-6®свеча
7. Азот на прием Н-34,35 ® П-6® К-4
Т-9®Т-3® ВХК-8® Х-5 ® воздушник.
К-5
8. Азот на прием Н-46,47 ® Х-3® воздушник.
Азот на прием Н-48,49 ® ВХ-3 ® Х-4 ® воздушник.
К-5
10. Опрессовать колонну К-3 и связанные с ней аппараты азотом из С-1 на 1,25 МПа (12,5 кгс/см2).
11. Опрессовать колонну К-4 и связанные с ней аппараты на 0,45 МПа (4,5 кгс/см2).
12. Опрессовать колонну К-5 и связанные с ней аппараты на 0,3 МПа (3 кгс/см2).
В) Блок очистки газов.
® К-9® топливная сеть ®газ к печам П-1,2,5,6 ® Т-15 ®
®коллекторы печей П-1,2,5,6 ® свеча.
Азот на ® К-9®С-6® Т-12 ® К-10
Прием ® К-11 ® трубопровод фракции (С3-С4) с установки®
Н-32,33 ® воздушник
® ® К-11 ® С-6® Т-12 ® К-10
® К-12 ® трубопровод фракции С3-С4 с установки®
® воздушник
® К-12 ® С-6® Т-12 ® К-10
Азот на К-10 ®ВХК-9 ®ХК-9®С-7® трубопровод сероводорода с
прием ® установки ® воздушник.
Н-24,25 К-10 ® Т-12 ®ВХ-4 ®Х-7®Ф-5,6®Е-8® свеча.
1. Опрессовать колонну К-9 азотом на 0,8 МПа (8 кгс/см2) через съемную катушку.
2. Опрессовать колонну К-10 и связанные с ней аппараты на 0,16 МПа (1,6 кгс/см2) азотом из общей линии.
3. Опрессовать колонну К-11 на 2,4 МПа (24 кгс/см2) азотом от компрессора ПК-5 по временному трубопроводу.
4. Опрессовать колонну К-12 на 1,4МПа (14 кгс/см2) азотом от воздушника компрессора по временному трубопроводу.
5. Продуть факельный трубопровод через ручные сбросы от ППК из всех аппаратов с выходом азота через воздушник и опрессовать его на 0,05 МПа (0,5 кгс/см2).
6. Продуть дренажный коллектор нефтепродуктов в Е-10 со всех аппаратов на факел через Е-24 в Е-10, коллектор МЭА в Е-11 из аппаратов связанных с МЭА на свечу из Е-11.
После продувки и опрессовки всех блоков, аппаратов и трубопроводов сбросить давление азота через свечи и воздушники в атмосферу и приступить к приему конденсата и водорода.
Пуск блока подготовки сырья, гидроочистки и ректификации производится одновременно, при необходимости - раздельно.
Прием газообразного топлива
При приеме газообразного топлива на установку необходимо:
1. Продуть линии топлива инертным газом.
2. Опрессовать линии топлива к печам до форсунок инертным газом.
3. При давлении инертного газа в топливной линии не менее 1МПа (10 кгс/см2) проверить герметичность вентилей форсунок.
4. Отглушить все форсунки паспортными заглушками.
5. Проверить работу регулирующих клапанов, приборов КИП и А.
6. Давление инертного газа сбросить до нуля, все воздушники отглушить.
7. Привести в рабочее состояние клапаны-регуляторы давления, температуры.
8. Поставить в известность диспетчера НПЗ о приеме топлива.
9. Сделать направление топливного газа к подогревателю Т-15.
10 Открыть постепенно общую задвижку на линии газа, принять газ к печам.
11. Продуть все участки топливной линии на факел у каждой печи в течение 15-20 мин.
12. Продуть все коллекторы печи П-1,2,5,6 на факел для подогрева коллекторов.
13. Розжиг форсунок печей производится в присутствии ИТР цеха, перед розжигом форсунок необходимо:
а) продуть печи паром в течение не менее 15 минут с момента появления пара из дымовой трубы.
б) снять заглушку на подаче топливного газа к форсунке печи, немедленно зажечь форсунку, розжиг остальных форсунок производить идентично, по необходимости.
Подготовка реакторного блока к сушке и прокалке катализатора
Перед сушкой и прокалкой катализатора тщательно продуть систему реакторного блока азотом до содержания кислорода до 0,5% объемных, подаваемого с компрессора ПК-5 на выкид турбокомпрессора ЦК-1.
Систему продуть по схеме: трубопровод азота в трубопровод подачи сырья на РБ ® Т-6(1) ® Т-7(1,2,3) ® Т-6 ® П-2 ® Р-1 ®Т-6 ®Т-18 ®
Х-14
®Т-7(3,2,1)®Т-6(1)®ВХК-3® С-1®К-8®С-5а®С-5® свеча.
Х-14а
При достижении содержания кислорода в продувочном азоте не более 0,5% объемных прекратить выдув.
Сушка катализатора
Активность свежего катализатора, загруженного в реактор, не достигает максимальной своей величины в первые часы его работы, по причине высокой влажности и неподготовленности последнего к восприятию высоких температур. Поэтому после загрузки катализатора в реактор необходимо произвести его сушку.
Сушка катализатора производится азотом или водородсодержащим газом при удельном расходе газа не менее 200 нм3/ч на м3 катализатора и давлении до 1,5 МПа (15 кгс/см2).
На этой стадии температура повышается не выше чем до 200-230°С.
Повышение температуры ступенчатое, со скоростью не выше 10-15°С в час, длительность которых определяется скоростью выделения и дренирования воды из сепаратора С-1.
На всех этапах сушки и восстановления катализатора следует дренировать воду из сепаратора.
6.6.7 Осернение катализатора гидроочистки
Катализаторы гидроочистки достигают максимальной активности при переходе из окисной в сульфидную форму. Поэтому катализаторы гидроочистки, как свежие, так и регенерированные, необходимо подвергать осернению.
В качестве осерняющих агентов применяется сернистое сырье процесса гидроочистки, высокосернистые бензины, их смеси с гидрогенизатом с общим содержанием серы не менее 0,02% масс, растворы индивидуальных органических соединений (сероуглерод, меркаптаны, дисульфиды) в нефтепродуктах, сероводород (обычно смесь 10% об. сероводорода и 90% об. водорода) и элементарную серу (кусковую, чешуйчатую или порошковую по ГОСТ 127-76).
Взаимодействие активных компонентов катализаторов гидроочистки с элементарной серой протекает, в основном, по двум реакциям:
МоО3 + S2 + 3Н2 ® МоS2 + 3Н2О
NiМоО4 + 4S + 4Н2 ® МоS2 + NiS2 + 4Н2О
Дозировка серы зависит от типа катализатора и способа осернения. При использовании сероорганических соединений, высоко сернистых бензинов и сероводорода подача серы составляет 6-8% от массы катализатора. В соответствии с расчетным значением необходимого общего количества серы для осернения катализатора гидроочистки подбирается требуемая величина загрузки сырьем.
При использования для осернения раствора сероорганических соединений в бензине - осернение начинают при температуре не выше 230°С и проводят его примерно по следующему графику при расходе серы 50% от проектного.
Температура, °С | Давление, кгс/см2. | Концентрация серы в сырье, % масс | Контроль длительности операции. |
230 | 15 | 0,2-0,3 | Для стабилизации концентрации Н2S в газе.
|
230¸260 260 | 15 30 | 0,2 - 0,3 0,5 | |
260¸290 290 | 30 30 | 0,5 0,5 | |
290¸315 315 | 30 30 | 0,5 0,5 |
После завершения осернения с подачей расчетного количества серы повышается расход сырья до нормального уровня, и регулируются параметры процесса с целью достижения заданной степени очистки серы.
При осернении катализатора гидроочистки водородсодержащим газом используется газ при содержании сероводорода в том же газе не менее 0,5% об.
Общая дозировка серы и график осернения аналогичны выше изложенным.
В случае пуска катализатора АКМ или ГО-70 без стадии осернения сушка должна производиться в том же порядке, а прием сырья производится при температуре, не превышающей 210-250°С.
Подачу сырья на блок гидроочистки начинают при налаженной циркуляции водородсодержащего газа.
6.7 Прием стабильного Оренбургского конденсата и вывод колонны К-1 на режим
1. Через диспетчера НПЗ согласовать с работниками товарного парка площадки «Д» о готовности схемы приема конденсата.
2. Открыть задвижки на входе конденсата на установку и сделать направление его в емкость Е-25.
3. При появлении уровня в Е-25 принять конденсат на прием насосов Н-1,2, включить их в работу и подать конденсат по схеме:
Н-1,2 ® трубное пространство Т-1® Т-1а®Т-2 (или минуя их) ®К-1
4. Набрать уровень в колонне К-1, сделать направление конденсата на прием насосов Н-7,8 и пустить их на циркуляцию по схеме:
К-1 ® Н-7,8 ® параллельно по межтрубному пространству ®
Т-2®П-1®К-1
®
Т-1а® ВХ-1®Е-25.
Настроить холодную циркуляцию на блоке подготовки сырья.
5. При заполнении емкости Е-25 до 80% по шкале прибора и нормальном уровне в К-1 прием конденсата прекратить.
6. При устойчивой циркуляции через печь П-1 приступить к разогреву колонны К-1 и печи П-1, для чего необходимо:
а) продуть камеры сгорания печи П-1 водяным паром не менее 15 минут с момента появления пара из дымовой трубы.
б) принять топливный газ и разжечь форсунки.
7. По мере повышения температуры в колонне К-1, со скоростью 20-25°С в час, включить вентиляторы воздушных холодильников ВХ-1 и ВХК-1, а при появлении уровня в емкости Е-1 сдренировать воду и принять бензин на прием насосов Н-5,6 и подать орошение в колонну К-1, а избыток направить по схеме: Н-5,6 ® до Е-9, линии подачи в Е-9, в Е-25.
8. При устойчивой подаче орошения в колонну К-1 сделать вывод бокового погона из К-1 через межтрубное пространство теплообменника Т-1 на прием насосов Н-9,10, включить их и направить фракцию 105-180°С в сырьевую емкость реакторного блока Е-9 через фильтры поз.Ф-1,2 или по линии циркуляции в Е-25.
9. Постепенно, не прекращая циркуляции колонны довести температуру верха и низа колонны К-1 до нормальной.
10. Порядок пуска и остановки блока подготовки сырья при ремонте остальных блоков.
В случае необходимости пуска блока подготовки сырья при ремонте всей установки необходимо выполнить следующее:
а) отключить все блоки от факельной и дренажной систем (установить все ППК на всех блоках и отглушить все дренажи в подземную емкость с ремонтируемых аппаратов).
б) отключить от топливной системы блок очистки закрытием арматуры и отглушить.
Газ из печи П-2,5,6 отглушить на общих трубопроводах.
в) отключить линию циркуляции с блока ректификации в Е-25.
(от Х-3,4,5 в Е-25) перекрытием задвижки и установкой заглушки.
г) отглушить подачу сырья на реакторный блок.
Только после проведения мероприятий по 1¸4, пуск блока подготовки производить согласно раздела «Прием стабильного Оренбургского конденсата и вывод колонны К-1 на режим».
После вывода блока на нормальный технологический режим постепенно направить фр. НК-105°С и 105-180°С в Е-9 и с набором уровня в Е-9 направить на установки гидроочистки диз. топлива № 2,3 постепенно увеличивая её расход, зажимая циркуляцию в Е-25.
6.8 Циркуляция и пуск блока ректификации
1. Порядок пуска блоков стабилизации, ректификации, получения пентанов, очистки газов и котла-утилизатора при ремонте блоков подготовки сырья и реакторного блока.
При ремонте блоков подготовки сырья и реакторного блока, пуск блоков стабилизации, ректификации, получения пентанов, очистки газов и котла-утилизатора производится на нестабильном гидрогенизате с установки ГО-2,3 после проведения подготовительных работ.
- отключить блоки подготовки сырья и реакторного от системы факела и дренажного коллектора.
- установить заглушки на линии циркуляции после Х-3,4,5 в Е-25, на трубопроводе от С-1 в С-3, на трубопроводе топливного газа к печам П-1, П-2.
Пуск производить в следующей последовательности:
1. Набрать уровень в колонне К-3 по схеме:
бензин из линии 13 ® обратным ходом до холодильника Х-5 ® линия циркуляции блока ректификации ® трубопровод выхода гидрогенизата из С-3 ® Т-8(2) ® Т-3® Т-9 ®Т-11®К-3.
2. Пустить в работу насосы Н-38,39 и наладить циркуляцию горячей струи колонны К-3 по схеме: К-3® Н-38, Н-39® Т-18® П-5®К-3.
3. Зажечь форсунки печи П-5, предварительно продуть камеры сгорания паром не менее 15 мин. с момента появления пара из дымовой трубы и принять топливный газ и приступить к разогреву колонны К-3.
4. При разогреве колонны со скоростью 20-25°С в час и подъеме давления в ней со скоростью 0,3-0,4 МПа (3-4 кгс/см2) в час, открыть сброс избытка уровня в колонну К-4, включить воздушный холодильник- конденсатор ВХК-5.
5. Испарившиеся пары бензина с верха К-3 через теплообменник Т-8 (минуя его) направить в ВХК-5, ХК-5 и далее в емкость Е-4.
6. При появлении уровня в емкости Е-4 сдренировать воду, сделать направление продукта на прием насосов Н-36,37, включить их в работу. Для исключения попадания воды из колонны К-3 на прием насосов Н-38,39 при выводе колонны К-3 на режим после ремонта, выпаривание воды производить через верх колонны без подачи орошения в колонну до прекращения попадания воды в Е-4. После удаления воды, включить Н-38,39, подать орошение в К-3. Избыток фракции С3-С5 направить в К-2 и далее на установку АГФУ-2 или в парк 700 об. Избыток уровня из Е-4 сбрасывать через клапан-регулятор уровня в Е-4 поз.281 в колонну К-2 для набора уровня и создания давления, а углеводородный газ через холодильник Х-15 в колонну К-9 и далее в топливную сеть.
7. При появлении уровня внизу К-4, подготовить и пустить насосы Н-34,35 по схеме: К-4® Н-34,35 ®П-6® К-4, а избыток уровня через клапан-регулятор уровня в колонне К-4 направить по схеме: Н-34,35® Т-9®Т-3 ® ВХК-8 ®Х-5®Т-8(2) ®Т-3®Т-9®Т-11®К-3.
8. Зажечь форсунки печи П-6, предварительно продуть камеры сгорания паром не менее 15 мин. с момента появления пара через дымовую трубу и принять топливный газ к форсункам печи.
9. Разогреть колонну К-4, включить ВХК-6 и с появлением уровня в емкости Е-5 сдренировать воду, включить насосы Н-42,43, подать орошение в колонну К-4, а избыток направить на загрузку в К-5.
10. Открыть паровое питание колонны К-5 из К-4.
11. Для разогрева колонны К-5 открыть небольшое количество пара в подогреватель Т-10.
12. Включить воздушные холодильники ВХК-7.
13. При появлении уровня в емкости Е-6 проверить наличие воды, включить в работу насосы Н-46,47 и подать орошение в К-5, а избыток фракции НК-62°С через Х-3 направить на загрузку К-3.
14. Избыток уровня из колонны К-5 насосами Н-48,49 через воздушный холодильник ВХ-3, Х-4 направить на загрузку К-3.
15. Температуру верха и низа колонн К-3,4,5 довести до нормальной.
16. Боковой погон К-5 выводится с 27 тарелки, затем проходит ВХ-25, откачивается с установки насосом Н-40,41 в ТСЦ.
Блоки подготовки сырья и ректификации находятся на циркуляции по вышеописанной схеме с одновременным разогревом системы до готовности к пуску блока гидроочистки.
При появлении избытка бутан-пентановой фракции открыть сброс её с установки, предварительно согласовав с диспетчером НПЗ.
Остановка блока стабилизации при ремонте реакторного блока:
- по мере уменьшения поступления нестабильного гидрогенизата в С-3 с ГО-2,3, уменьшается загрузка по блокам пентанов, стабилизации, ректификации, очистки газов.
- после прекращения приема нестабильного гидрогенизата с ГО-2,3 закрыть запорную арматуру на линии приема.
- дальнейшая остановка блока производится согласно раздела «Остановка установки».
6.9 Пуск блока очистки газов
1. Система должна быть заполнена и промыта конденсатом пара. Сброс конденсата из системы производится до тех пор, пока анализ не покажет отсутствие примесей.
Механические примеси, следы щелочи, наличие солей может привести к вспениванию раствора в процессе эксплуатации.
2. В целях сокращения потерь МЭА (ТЭА) пуск блока рекомендуется на конденсате водяного пара.
3. Подача в систему МЭА (ТЭА) и вывод на режим должны осуществляться до момента сушки и восстановления катализатора.
4. Для возможности снижения коррозии в верхней части отгонной колонны и конденсатора-холодильника в период пуска необходимо добавить в конденсат, подающий на орошение до 0,5% мас. МЭА(ТЭА) и поддерживать концентрацию на данном уровне. При этом на внутренних поверхностях формируется антикоррозионная пленка этаноламина.
После промывки системы конденсат сбрасывается в сернисто-щелочную
канализацию.
6.10 Пуск блока очистки газов после промывки конденсатом
1. Приготовить раствор МЭА (ТЭА) в Е-8,12 с концентрацией не более 15% мас.
2. Включить насосы Н-32,33 и подать раствор МЭА (ТЭА) по схеме:
Е-8®Н-32,33®К-9, набрать давление в К-9 из сети топливного газа, уровень МЭА (ТЭА) на глухой тарелке и открыть сброс МЭА (ТЭА) из К-9 через Т-12 в К-10.
3. Набрать уровень в К-10, включить подогреватель Т-13 и приступить к разогреву колонны.
4. При разогреве колонны К-10 включить воздушные конденсаторы ВХК-9, а сконденсировавшиеся пары направить через водяной холодильник ХК-9 в сепаратор С-7.
5. По мере накопления конденсата в С-7 подать орошение в колонну К-10, включить насосы Н-24,25.
6. При достижении давления в К-10 и С-7 - 0,07МПа (0,7 кгс/см2) открыть сброс сероводорода на факел до получения заданного качества, а затем в общекомбинатовскую систему, согласовав с диспетчером завода и объединения.
7. Регенерированный МЭА (ТЭА) из К-10 через теплообменник Т-12, ВХ-4, холодильник Х-7 и фильтры Ф-5,6 направить в емкость Е-8.
8. При наличии давления в экстракторах К-11,12 подать по 4-5 м3/ч МЭА (ТЭА) в каждую колонну, набрать уровень в низу экстракторов. Включив клапана раздела фаз, начать перепускать МЭА (ТЭА) в сепаратор С-6 и далее через Т-12 на регенерацию в К-10.
9. Включить регуляторы давления на сепараторе С-6.
10. Включить насосы Н-26,27 и подать небольшое количество 10-12 м3/ч МЭА (ТЭА) в К-8 по схеме: Е-8®Н-26,27®К-8 при появлении уровня на глухой тарелке К-8 открыть сброс МЭА (ТЭА) через клапан-регулятор уровня в сепараторе С-6 и далее через Т-12 на регенерацию в К-10. Довести расход МЭА (ТЭА) не менее 25 м3/ч.
При циркуляции МЭА по всей системе режим по К-10 держать в пределах установленных норм.
После окончания сушки катализатора в Р-1 и накопления сырья в емкости Е-9 увеличить количество циркулирующего продукта, а при снижении уровня в Е-25 принять конденсат с таким расчетом, чтобы режим в колоннах К-1,2,3,4,5 поддерживался в соответствии с нормами технологического режима.
6.11 Пуск реакторного блока
1. Подготовить к пуску насосы Н-13¸18.
2. Поднять давление и температуру в системе гидроочистки до рабочего.
3. Включить насосы Н-13¸18 и начать подачу сырья в тройник смешения с водородом с минимальной скоростью 15-20м3/ч.
4. При подаче сырья увеличить температуру нагрева в печи П-2 для поддержания заданной температуры на входе в реактор.
5. При появлении уровня в сепараторе С-1 открыть сброс гидрогенизата через теплообменник Т-8 в сепаратор С-3, включив клапан-регулятор уровня в С-1 и давления в С-3.
6. При возрастании давления в С-3 сброс газа направить в К-9 на очистку.
7. Открыть сброс нестабильного гидрогенизата из С-3 в К-3 через теплообменник Т-8(2),3,9,11, установку перевести на циркуляцию по схеме:
Е-25®К-1®Е-9®Р-1®С-1®Т-8(1) ® C-3®К-3®К-4®Е-25
¯
К-5®Е-25
8. При получении удовлетворительных анализов фракции НК-62°С, 62-85°С, 85-180°С поочередно перевести сброс их с установки, приняв Оренбургский конденсат в Е-25 для поддержания уровня.
9. Фракцию 180-КК вывести с установки после получения её в соответствии с СТП.
10. При возрастании давления в барабане котла и увеличения температуры пара довести давление на выходе из пароперегревателя до 1,6 МПа (16 кгс/см2), прогреть паропровод от котельной до врезки в магистраль объединения и подключиться к ней.
Остановка установки
Нормальная остановка установки производится по письменному распоряжению начальника цеха или его заместителя под непосредственным руководством начальника установки в следующих случаях:
а) при регенерации катализатора;
б) при остановке на ремонт;
в) при заранее известном прекращении подачи сырья, водорода, оборотной воды и т.д.
Для остановки установки необходимо предупредить:
а) диспетчера НПЗ, НХЗ и объединения.
б) работников товарной группы площадки «Д».
в) цеха № 32,33,9,51 о прекращении приема водорода.
г) работников установок Л-35/6, Л-35/11-1000, гидроочистки дизтоплива, Л-16-1 о прекращении приема водородсодержащего газа и прекращении сдувок отработанного, работников 35/6, СЖГ, ТК-2, 35-11-1000, парк АВТ, Л-16-1, ЭЛОУ-АВТ-4, ГО-2,3.
д) установку элементарной серы о прекращении подачи сероводорода
е) факельное хозяйство об. 645 и НХЗ о возможных сбросах.
ж) цех КИП и электроцех.
з) цех водоснабжения и работников оперативной службы по теплоснабжению.
и) лабораторию.
1. Отключить технологические блокировки.
2. Снизить загрузку по Оренбургскому конденсату со скоростью 15-20 м3/ч до 40% производительности с одновременным снижением загрузки на гидроочистку.
3. Продолжать циркуляцию по змеевикам печей П-1,5,6, с плавным снижением температуры в кубах колонн К-1,3,4.
4. Дальнейшее уменьшение загрузки на реакторный блок производить с переводом сырья помимо Е-9 в Е-25.
5. При достижении загрузки на реакторном блоке 20 м3/ч остановить насосы Н-13¸18, сырье из К-1 перевести помимо Е-9 в Е-25 полностью, перевести откачку фракции НК-62, 62-85, 85-180 в К-3, 180-КК в Е-25, прекратив прием Оренбургского конденсата.
6. Продолжить циркуляцию продукта по блоку подготовки сырья и ректификации с одновременным снижением температур низа и верха колонн.
7. Циркуляцию водородсодержащего газа по системе реакторного блока продолжить в течение 5-8 часов для удаления адсорбированного продукта с поверхности катализатора при рабочих условиях процесса.
8. Снизить подпитку свежего водорода в систему и сдув отработанного водорода из системы.
9. Уменьшить подачу фракции С3-С5 в К-2, снизить температуру К-2 уменьшением количества подачи пара в подогреватели Т-5(1,2) и Т-22. Откачку фракции С3-С5 полностью перевести в колонну К-3 на орошение, вывод фракции С5 с установки закрыть.
Для дальнейшего охлаждения колонны К-2 включить в работу схему циркуляции колонны К-2: Х-6 ®Н-29® Т-4®Т-22® К-2®Т-4®Х-6.
10. Откачать оставшийся продукт из Е-3 в К-11, остановить насосы Н-11,12.
11. Перепустить насыщенный раствор МЭА из К-11 в К-10 на регенерацию и отключить колонну К-11 задвижками.
12. Прекратить вывод бокового погона из колонны К-1, остановить насосы Н-9,10.
13. Отключить теплообменники Т-1а, Т-2 по меж
|
|
Эмиссия газов от очистных сооружений канализации: В последние годы внимание мирового сообщества сосредоточено на экологических проблемах...
Особенности сооружения опор в сложных условиях: Сооружение ВЛ в районах с суровыми климатическими и тяжелыми геологическими условиями...
Таксономические единицы (категории) растений: Каждая система классификации состоит из определённых соподчиненных друг другу...
Двойное оплодотворение у цветковых растений: Оплодотворение - это процесс слияния мужской и женской половых клеток с образованием зиготы...
© cyberpedia.su 2017-2024 - Не является автором материалов. Исключительное право сохранено за автором текста.
Если вы не хотите, чтобы данный материал был у нас на сайте, перейдите по ссылке: Нарушение авторских прав. Мы поможем в написании вашей работы!