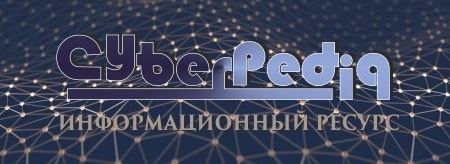
Типы оградительных сооружений в морском порту: По расположению оградительных сооружений в плане различают волноломы, обе оконечности...
Архитектура электронного правительства: Единая архитектура – это методологический подход при создании системы управления государства, который строится...
Топ:
Оснащения врачебно-сестринской бригады.
Отражение на счетах бухгалтерского учета процесса приобретения: Процесс заготовления представляет систему экономических событий, включающих приобретение организацией у поставщиков сырья...
Интересное:
Национальное богатство страны и его составляющие: для оценки элементов национального богатства используются...
Наиболее распространенные виды рака: Раковая опухоль — это самостоятельное новообразование, которое может возникнуть и от повышенного давления...
Отражение на счетах бухгалтерского учета процесса приобретения: Процесс заготовления представляет систему экономических событий, включающих приобретение организацией у поставщиков сырья...
Дисциплины:
![]() |
![]() |
5.00
из
|
Заказать работу |
|
|
РЕМОНТ ТРУБОПРОВОДНОЙ АРМАТУРЫ
Уважаемые студенты! Предлагаю Вам внимательно изучить представленный материал по организации ремонта трубопроводной арматуры. Многие понятия Вам уже знакомы: дефектация деталей, сортировка, промывка, методы контроля. Эта информация представляется в контексте с ремонтом ТА (трубопроводной арматуры).
На производственной практике многие из вас занимались ремонтными работами ТА, на учебной практике выполнялся разбор и дефектация узлов и деталей.
Внимательно прочитав материал Вам необходимо:
Найти спрятанные в тексте 2 ошибки (мотивацию не озвучиваю, бунус будет достойный)
2. Составить тестовые задания по организации ремонта ТА, включающие 8 заданий: 5 – с одним вариантом ответа, 3- с несколькими верными ответами. Количество вариантов ответов – три.
Указания по организации ремонта
Ремонт арматуры должен выполняться по ремонтной документации, разработанной по ГОСТ 2.602, и утвержденной в установленном порядке.
Исходя из транспортируемых по трубопроводам рабочих сред и их параметров, трубопроводная арматура подвергается износу различной степени.
В зависимости от степени износа узлы и детали трубопроводной арматуры могут ремонтироваться непосредственно на месте установки или в ремонтном цехе (на ремонтном предприятии), или на другом предприятии, располагающим возможностями для ремонта.
До начала ремонта составляется и утверждается следующая документация:
- ремонтная документация, включающая:
а) технические условия на ремонт;
б) ремонтные чертежи на ремонтируемые узлы и детали;
в) ведомость документов для ремонта (ВРК, ВРС).
Необходимость разработки других документов по ГОСТ 2.602 устанавливает разработчик. Для арматуры, ремонтируемой по заказу МО РФ, номенклатура РД согласовывается с ним;
|
- график подготовительных работ;
- ведомость объема работ;
- технологические процессы ремонта.
Подготовка производства к ремонту включает:
- составление плана организации ремонта, включающего методы обеспечения выполнения основных ремонтных работ (установка такелажных приспособлений, способы подачи сжатого воздуха, приспособления для сварочных работ, обеспечение ремонта транспортными средствами и т.д.).
- подготовку режущего и мерительного инструмента, приспособлений;
- заготовку материалов;
- определение объема работ;
- разработку технологии ремонта.
В графике подготовительных работ указываются сроки изготовления приспособлений, инструмента, сроки заготовки материалов и запасных частей.
Технологический процесс на ремонт может разрабатываться как на каждое изделие, так и на типового представителя арматуры.
Технологический процесс на ремонт должен содержать:
- сведения о технологической последовательности выполнения ремонта;
- сведения о технологической оснастке и инструментах;
- нормы времени;
- приемы выполнения ремонта;
- методы контроля.
Приложение Б
(Рекомендуемое)
Определение общего объема ремонтных работ, потребности в запасных частях и материалах
Требования, предъявляемые к инструменту, используемому при разборке, ремонте, сборке и испытаниях арматуры:
а) съемники, ключи с изношенной рабочей поверхностью, трещинами, сколами, изношенной и помятой резьбой винтов использовать запрещается;
б) использование удлинителей рукояток ключей при разборке и затяжке крепежных деталей запрещается;
в) отвертки должны быть с исправной рабочей поверхностью и удобной рукояткой;
г) ручной инструмент с злектро – или пневмоприводом перед использованием должен быть проверен и исправен;
д) при разборке сопрягаемые узлы и детали не должны самопроизвольно падать;
|
При механической обработке узлов и деталей арматуры должны соблюдаться требования безопасности в соответствии с ГОСТ 12.3.025.
Дефектация
Дефектацию узлов и деталей проводят с целью выявления имеющихся дефектов и рассортировки на исправные, требующие ремонта и не подлежащие ре-монту, а также для уточнения объема работ, потребности в запасных частях и мате-риалах.
Методы дефектации:
- визуальный контроль;
- измерительный контроль;
- неразрушающий контроль.
Методы дефектации и нормы дефектов конкретизируются в РЭ,РД, УК (УС) на конкретное изделие.
Визуальный контроль арматуры рекомендуется проводить по ПНАЭ Г-7-016, РД 03-606-03 для выявления видимых наружных (поверхностных) дефектов: трещин, поломок, выкрашивания металла и т.д. Визуальный контроль должен проводиться с использованием лупы не менее семикратного увеличения по ГОСТ 25706. При визуальном контроле необходимо особое внимание уделять местам, наиболее подверженным коррозионному, эрозионному и механическому износам. Места наибольшего износа должны быть указаны в РЧ.
Измерительный контроль предусматривает измерение рабочих поверхностей с целью установления величины износа и определения пригодности узлов и деталей к дальнейшей работе, а также контролируется взаимное расположение поверхностей с помощью специальных приборов и мерительного инструмента для определения величины возможного изгиба, коробления и т.п.
Измерение твердости проводится по ГОСТ 9012 и ГОСТ 9013 с целью определения механических характеристик металла неразрушающими методами, в том числе предела прочности σв, предела текучести σ0,2, ударной вязкости KCU (КCV), относительного удлинения δ, относительного сужения φ в соответствии с СТ ЦКБА 091.
Контроль и измерение прямолинейности и круглости при визуальном и измерительном контроле следует проводить:
- круглости – с помощью микрометров по ГОСТ 6507 и индикаторов по ГОСТ 577;
- отклонения от плоскостности поверхности – с помощью плит по ГОСТ 10905 класса точности 1 или 2 «по краске». При применении методов «по краске» пятна краски должны равномерно располагаться по всей контролируемой поверхности.
Неразрушающие методы контроля с применением технических средств:
- капиллярный контроль - по ГОСТ 18442, ПНАЭ Г-7-018;
|
- магнитопорошковая дефектоскопия - по ГОСТ 21105;
- ультразвуковой контроль внутренних дефектов - по ГОСТ 14782, ПНАЭ Г-7-014;
- ультразвуковая толщинометрия - по ПНАЭ Г-7-031;
- радиографический контроль - по ГОСТ 7512, ПНАЭ Г-7-017;
- гидравлические испытания;
- пневматические испытания.
Капиллярный контроль проводится для выявления дефектов, выходящих на поверхность деталей как в основном металле, так и трещин в наплавках.
Магнитопорошковая дефектоскопия проводится с целью выявления как поверхностных, так и подповерхностных (скрытых) дефектов на глубине до двух миллиметров на деталях и сварных швах из углеродистых сталей. Он основан на свойстве магнитных порошков, помещенных в магнитное поле, ориентироваться в направлении наибольшего увеличения плотности магнитного потока, возникающего в местах расположения дефектов детали при его намагничивании.
Ультразвуковой контроль предназначен для выявления внутренних дефектов в разнообразных материалах на значительной глубине от 10 мм, но без определения внутренней формы дефекта. Ультразвуковая дефектоскопия применяется для контроля концов патрубков литой арматуры, для выявления раковин, рыхлот, шлаковых и земляных засорений, пор, трещин. Ультразвуковой контроль проводится также для выявления следующих внутренних дефектов сварных соединений из углеродистых и низколегированных сталей перлитного класса: трещин, непроваров, шлаковых включений, пор и других без расшифровки их характера, но с указанием количества дефектов, условной протяженности, координат расположения и оценкой их эквивалентной площади. Нормы оценки при контроле зоны, прилегающей ко шву, должны соответствовать требованиям НД на материал.
Радиографический контроль служит для выявления внутренних дефектов металлов.
Контролируемая зона должна включать весь объем металла шва, а также примыкающие к нему участки основного металла в обе стороны от шва:
а) для стыковых сварных соединений, выполненных дуговой сваркой, шириной:
- на менее 5 мм при номинальной толщине свариваемых деталей до 5 мм включительно;
- не менее номинальной толщины свариваемых деталей при номинальной толщине свариваемых деталей свыше 5 до 20 мм включительно;
|
- не менее 20 мм при номинальной толщине свариваемых деталей свыше 20 мм;
б) для угловых, тавровых, торцевых сварных соединений, выполненных дуговой сваркой, шириной не менее 3 мм независимо от толщины;
в) для сварных соединений, выполненных электрошлаковой сваркой, шириной 50 мм независимо от толщины.
В сварных соединениях различной номинальной толщины ширина контролируемых участков основного металла определяется отдельно для каждой из свариваемых деталей в зависимости от их номинальной толщины.
Гидравлические испытания проводятся для проверки прочности и плотности корпусных деталей, позволяют обнаружить наличие трещин, раковин и других неплотностей металла. Гидравлические испытания должны проводиться на специальных стендах водой пробным давлением.
Пневматические испытания проводятся воздухом давлением 0,6 МПа для проверки плотности материала деталей и сварных швов.
Дефектации подлежат:
- сварные соединения, наплавки и места утонений в объеме 100 %;
- литые, штампованные, кованные детали и детали из проката;
- покупные изделия и детали.
Дефектация сварных соединений, наплавок и мест утонений.
Дефектации подлежит шов с двух сторон на всей его протяженности и около-шовная зона (не менее 20 мм в каждую сторону от сварного шва). Виды возможных дефектов сварных швов, екомендуемые методы контроля и нормы разбраковки при-ведены в приложении Г, СТ ЦКБА 025, ПНАЭ Г-7-010 ли ОСТ 5Р 9634 в зависимости от заказа.
Дефектации подлежит вся поверхность наплавки, включая боковые поверхности и зона сплавления с основным металлом.
Виды возможных дефектов наплавок, выявленных в результате эксплуатации и дефектации и не соответствующих нормам СТ ЦКБА 053, ОСТ 5Р.9937, РД 2730.300.06 или СТ ЦКБА 098 в зависимости от заказа приведены в приложении Д.
К местам утонений относятся сварные швы с околошовной зоной основного металла и непосредственно основной металл корпусных деталей, находящийся под воздействием потока рабочей среды и окружающих условий эксплуатации. Допускаются только местные утонения, оговоренные в КД, в УК (УС) или в РД. Допустимость любых других утонений металла корпусных деталей рассматривается в каждом случае на основании прочностного расчета, выполненного с учетом конкретных условий эксплуатации арматуры.
При дефектации поверхностей, подверженных коррозионному, эрозионному и механическому износам особое внимание должно быть обращено на:
- замер толщины стенок в минимальном сечении;
- наличие и симметричность износа направляющих элементов резьбовых и направляющих втулок;
- отсутствие бронзовой пыли на стальных деталях (например, вследствие интенсивного износа бронзовых втулок);
|
- наличие задиров и рисок.
К поверхностям, подвергаемым коррозионному, эрозионному и механическому износам относятся внутренние поверхности корпусных деталей литой арматуры, сварные швы и околошовная зона сварных конструкций корпусных деталей штампосварной арматуры, патрубков в связи с воздействием потока рабочей среды при малых щелях открытия (закрытия) запирающего элемента, а также ходовая резьба втулок, направляющих втулок и т.д.
Замер толщины необходимо проводить после зачистки следов коррозии.
Неравномерность (асимметричность) износа, а также интенсивный износ, являются следствием несоосности изнашиваемых поверхностей, недостаточной смазкой или завышенной (против расчетной) нагрузки.
При дефектации должна быть установлена причина несоосности и величина прикладываемой нагрузки.
Дефектация литых, штампованных и кованых деталей и деталей из проката (корпус, крышка, стойка, шпиндель, запирающий элемент и т.д.).
Допустимые размеры дефектов (раковин), их размеры в плане, количество, расстояние между ними и глубина и количество участков для замера оговариваются в РЧ и УК (УС) для конкретного изделия.
Глубина раковин устанавливается контрольной зачисткой.
На механически необработанных поверхностях литых деталей допускаются без исправления видимые визуально несплошности (кроме трещин, надрывов, наплывов, несплавлений) округлой или удлиненной формы, размеры которых должны быть указаны в УК (УС) для конкретного изделия.
Поверхность литых деталей не должна иметь дефектов, снижающих прочность отливок.
Дополнительные указания по дефектации литых поверхностей по СТ ЦКБА 014 и СТ ЦКБА 089.
На штампованных и кованых деталях допускаются точечные поверхностные дефекты и площадь дефектов, размеры и расстояния между которыми должны быть указаны в УК (УС) для конкретного изделия.
Дефекты, превышающие допустимые, а также другие виды дефектов (поверхностные и сквозные трещины, коррозионные язвы и т д.) подлежат исправлению в соответствии с РД.
Дополнительные указания по дефектации штампованных и кованых поверхностей по СТ ЦКБА 010.
На обработанных поверхностях ходовых резьб не допускаются без исправления раковины диаметром более 2 мм в количестве не более 3.
На обработанных уплотнительных поверхностях фланцев, на обработанных трущихся поверхностях, на резьбовых поверхностях, в отверстиях под запрессовку втулок или сальниковой набивки, на обработанных поверхностях стоек без исправления не допускаются раковины, размеры в плане, глубина, количество и расстояние между ними, которые превышают указанные в РД для конкретного изделия.
На данных поверхностях деталей подлежат исправлению дефекты, превышающие допустимые, а также другие дефекты (следы коррозии, и трещины на всех поверхностях, риски и задиры на направляющих корпусов и запирающих элементах, риски на уплотнительных поверхностях под прокладочные соединения).
На сильфонных сборка не допускаются разрывы, трещины, смятие, следы кор-розии сильфонов и сопрягаемых с ними деталях.
При наличии разрывов, трещин, смятия или следов коррозии сильфонные сборки ремонту не подлежат и заменяются новыми.
На втулках и кольцах направляющих, поднабивочных, фланцах и втулках сальника не допускаются трещины, задиры.
При наличии трещин и задиров детали заменяются новыми.
При дефектации места с концентраторами напряжений должны быть проверены на отсутствие трещин методом магнитопорошковой дефектоскопии по ГОСТ 21105, капиллярного контроля по ГОСТ 18442 или лупой 7 – 10-кратного увеличения по ГОСТ 25706.
К концентраторам напряжения относятся:
- радиусы переходов от обечаек (цилиндрических частей) к фланцам, особенно без переходного конуса (средние и магистральные фланцы корпусов, фланцы крышек, сальника, стоек);
- сварные швы, особенно угловые без подварки или с конструктивным непроваром;
- места перехода от направляющих к телу корпусов;
- углы «Т» - образного паза в запирающих элементах;
- углы головки шпинделя под «Т» - образный паз;
- углы в резьбовых канавках шпинделей, шпилек, в основаниях кулачков ку-лачковых втулок.
На подшипниках не допускаются следы износа, коррозии, разрыв сепаратора, смятие сепаратора, трещины, разрушение шариков. При наличии дефектов подшипник должен быть заменен.
Прокладки, сальниковая набивка, пылезащитные кольца при ремонте должны быть заменены новыми. Прокладки и сальниковые набивки на основе асбеста должны быть заменены на прокладки и сальниковые набивки из материалов, не содержащих асбест.
Методы контроля антикоррозионных покрытий деталей, узлов и арматуры в целом следует проводить в соответствии с ГОСТ 9.302 и СТ ЦКБА 042.
Сортировка сборочных единиц и деталей арматуры по результатам дефектации.
По результатам дефектации узлов и деталей арматуры отдефектованные сборочные узлы и детали должны быть рассортированы по группам:
1 группа – узлы и детали, не имеющие отклонений геометрических параметров от значений, предусмотренных КД.
2 группа – узлы и детали, требующие ремонта, имеющие износ или повреждения, устранить которые возможно.
3 группа – узлы и детали, имеющие износ и повреждения, устранить которые невозможно.
Узлы и детали 3 группы подлежат изъятию и замены на вновь изготовленные.
Узлы и детали каждой группы необходимо маркировать:
- одним клеймом – узлы и детали не имеющие отклонений от значений, указанных в КД и не требующих ремонта;
- двумя клеймами – узлы и детали, требующие ремонта;
- тремя клеймами – узлы и детали, имеющие износ и повреждения, которые устранить невозможно и которые подлежат изъятию и заменой на вновь изготовленные.
Маркировку следует выполнять на нерабочих поверхностях деталей и арматуры в целом по ГОСТ 25726.
Дефекты, не устранимые путем ремонта (окончательный брак):
- коррозионный, эрозионный, механический износ деталей (достижение местных износов стенки более 20 % от величины, указанной на ремонтном чертеже, суммарной площадью более 10 % от общей площади поверхности узла или детали).
- деформация деталей, которая может привести к нарушению герметичности в затворе и заклиниванию подвижных деталей (деформация корпуса, крышки, стойки);
- свойства металла деталей ниже стандартных.
- дефекты сильфонных сборок.
Перечень деталей и узлов, которые в обязательном порядке подлежат замене при ремонте на новые, должны быть указаны в РД.
Методы контроля антикоррозионных покрытий деталей, узлов и арматуры в целом следует проводить в соответствии с ГОСТ 9.302 и СТ ЦКБА 042.
По результатам дефектации узлов и деталей должна быть составлена карта дефектации и ремонта по форме, приведенной приложении Е, в которой подробно перечисляются дефекты арматуры в целом, каждого узла в отдельности и каждой детали, подлежащей восстановлению или изготовления вновь.
Карта дефектации и ремонта является дополнением к технологическим процессам на ремонт.
Требования к сборке и отремонтированной арматуре
Сборку отремонтированной арматуры следует проводить в соответствии с требованиями ремонтной РД для конкретного изделия, а также настоящего стандарта.
К сборке допускаются узлы и детали, удовлетворяющие требованиям РД.
Все узлы и детали, отремонтированные или вновь изготовленные, снятые с ремонтируемой арматуры и признанные годными к установке на арматуру без ремонта, а также полученные как запасные части, должны удовлетворять требованиям РД на конкретное изделие и пройти входной контроль в соответствии с СТ ЦКБА 082.
После ремонта, перед сборкой, все узлы и детали должны быть очищены от загрязнения, промыты и, при необходимости, обезжирены по СТ ЦКБА 046.
Зазоры между подвижными и сопрягаемыми узлами и деталями арматуры должны удовлетворять требованиям РД на конкретное изделие.
Размеры, допуски и шероховатость поверхности узлов и деталей арматуры после восстановления или изготовления должны соответствовать требованиям РД на конкретное изделие.
Все трущиеся поверхности деталей арматуры, кроме уплотнительных поверхностей запирающего элемента, должны быть смазаны смазкой в соответствии с требованиями РД на конкретное изделие.
Концы магистральных патрубков с разделкой «под приварку» на расстоянии 100 мм от разделки и поверхности разделки не окрашиваются, а покрываются консервационной смазкой. Посадочные поверхности магистральных фланцев и посадочная поверхность для присоединения привода не окрашиваются, а покрываются консервационной смазкой.
Допуск параллельности уплотнительных поверхностей присоединительных фланцев арматуры на каждые 100 мм диаметра должен находиться в пределах от 0,1 до 0,22 мм. Шероховатость уплотнительной поверхности должна соответствовать РД на конкретное изделие.
При сборке необходимо обеспечить плавность хода подвижных частей арматуры, а также сопряжение отдельных узлов, деталей и сборочных единиц с целью проверки зазоров и установочных размеров.
Затяжка резьбовых соединений должна проводиться равномерно последовательным затягиванием противоположно расположенных гаек.
Затяжка гаек должна выполняться крутящим моментом в три этапа: на первом этапе – 30 % от расчетного; на втором – 60 % и на третьем этапе – до полного, указанного в РД на конкретное изделие.
Зазор во фланцевых соединениях должен контролироваться в шести – восьми точках по окружности набором щупов.
Набивка и подтяжка сальника должна проводиться без перекосов, не повреждая рабочей поверхности шпинделя.
При набивке сальникового уплотнения кольца должны располагаться замками «в разбежку», причем разрезы соседних колец должны быть смещены на угол 90 ⁰ с обязательным обжатием каждого кольца. Диффузор сальникового уплотнения стыкуется с каждым кольцом.
Набивка сальника должна проводиться так, чтобы фланец сальника углубился в сальниковую камеру в пределах от 3 до 5 мм, обеспечивая легкое перемещение шпинделя или штока при управлении маховиком без применения дополнительных рычагов.
При затяжке сальника с установленным в сальниковой камере фланцем сальника необходимо внутренний диаметр фланца сальника располагать концентрично относительно наружного диаметра шпинделя или штока.
В процессе затягивания гаек откидных болтов должно контролироваться наличие зазора между внутренним диаметром фланца сальника и наружным диаметром шпинделя или штока.
После окончания затяжки сальника, опуская и поднимая шпиндель (шток) должны быть проверены наличие зазора между шпинделем (штоком) и внутренним диаметром фланца сальника и отсутствие трения между рабочей поверхностью шпинделя (штока) и внутренней поверхностью фланца сальника. Визуальным контролем должна быть проверена рабочая поверхность шпинделя (штока) на отсутствие каких-либо следов повреждения.
При сборке арматуры должно быть проверено прилегание запирающих элементов к седлу корпусов в соответствии с требованиями РД на конкретное изделие.
Правила приемки
Общие требования
Правила приемки отремонтированной арматуры должны соответствовать требованиям настоящего стандарта, РД на конкретное изделие.
Испытания отремонтированной арматуры проводятся на стендах ремонтного предприятия с использованием контрольно-измерительных приборов, обеспечивающих заданные параметры испытаний и погрешности измерений параметров.
Отремонтированная арматура должна быть испытана в объеме приемо-сдаточных испытаний, которые включают в себя:
- на прочность и плотность материала деталей и сварных швов, находящихся под давлением рабочей среды;
- на герметичность относительно внешней среды по подвижным и неподвижным соединениям (сальникового уплотнения, прокладочных соединений):
- на герметичность затвора;
- на работоспособность (проверку функционирования).
Приемо-сдаточные испытания проводит ОТК предприятия, проводившего ремонт, с целью проверки параметров отремонтированной арматуры на соответствие требованиям настоящего стандарта, РД на конкретное изделие.
Испытания проводятся по УК (УС) на конкретное изделие или по программе приемо-сдаточных испытаний.
К испытаниям допускается отремонтированная арматура, принятая ОТК предприятия, проводившего ремонт.
Отремонтированная арматура должна проходить испытания до окраски.
Испытательное оборудование, измерительные средства, а также испытательные среды (пробные вещества) должны удовлетворять требованиям ГОСТ Р 53402.
Методы контроля
Общие требования
Контрольно-измерительная аппаратура и испытательные стенды должны быть проверены на соответствие паспортам или другим техническим документам, содержащим основные параметры этого оборудования.
Помещения, в которых проводятся испытания, должны исключать возможность загрязнения отремонтированной арматуры, стендов и приборов.
Технический персонал, проводящий испытания, должен:
- пройти инструктаж по технике безопасности;
- знать устройство стендов, на которых проводятся испытания;
- изучить руководство по эксплуатации испытываемой отремонтированной арматуры.
Защитные покрытия и смазка
На поверхностях деталей и узлов арматуры, подлежащих покрытию, не должно быть окалины, ржавчины, грязи, влаги, жировых пятен.
Для исключения коррозии деталей и узлов арматуры из углеродистых сталей, в случае длительного перерыва между ремонтными операциями, они должны быть покрыты масляной пленкой.
В случае разрушения лакокрасочного покрытия вследствие коррозии, эрозии, механического или другого воздействия, арматура должна быть после ремонта и испытаний окрашена.
Покрытия должны удовлетворять требованиям ГОСТ 9.301 и ГОСТ 9.303.
Полная окраска поверхности арматуры должна проводиться в случае, когда дефекты покрытия занимают более 50 % поверхности. Перед окраской старое лакокрасочное покрытие должно быть удалено, а поверхность обезжирена по СТ ЦКБА 046.
Подготовка поверхности арматуры под окраску должна проводиться по ГОСТ 9.402.
Окрашенная поверхность должна удовлетворять требованиям ГОСТ 9.032, класс покрытия VII.
Внешние поверхности деталей арматуры, изготовленных из коррозионностойкой стали и детали из углеродистой стали, имеющие антикоррозионное покрытие, не окрашивать.
Все трущиеся поверхности деталей арматуры должны быть смазаны смазкой ЦИАТИМ-201 по ГОСТ 6267 или по СТ ЦКБА 059.
Перед сборкой все резьбовые соединения должны быть смазаны графитовой смазкой по ГОСТ 3333 или по СТ ЦКБА 075.
Маркировка и консервация
На фланце отремонтированной арматуры, в местах, указанных в ремонтных чертежах и свободных от имеющейся маркировки предприятия - изготовителя, ремонтным предприятием должна быть нанесена маркировка ударным или любым другим способом, которая должна содержать:
- наименование или товарный знак ремонтного предприятия;
- номер ремонтного чертежа арматуры;
- порядковый номер отремонтированной арматуры;
- дата ремонта.
Маркировка должна отвечать требованиям РД и ГОСТ Р 52760.
Консервацию отремонтированной арматуры следует выполнять в соответствии с требованиями ГОСТ 9.014, СТЦКБА 061. Вариант защиты, вариант внутренней упаковки арматуры и срок консервации – в соответствии с РД.
Качество консервационных смазок должно быть подтверждено сертификатами предприятия-изготовителя.
Слой смазки на поверхности деталей не должен иметь разрывов, трещин, пропусков, должен быть однородным по толщине, не должен содержать пузырьков, комков и инородных включений, видимых при внешнем осмотре.
Антикоррозионное покрытие, консервация должны обеспечивать хранение и транспортирование в условиях, заданных в соответствии с ГОСТ 15150.
Консервация отремонтированной арматуры должна быть принята отделом технического контроля предприятия, выполнившим ремонт.
Приложение A
РЕМОНТ ТРУБОПРОВОДНОЙ АРМАТУРЫ
Уважаемые студенты! Предлагаю Вам внимательно изучить представленный материал по организации ремонта трубопроводной арматуры. Многие понятия Вам уже знакомы: дефектация деталей, сортировка, промывка, методы контроля. Эта информация представляется в контексте с ремонтом ТА (трубопроводной арматуры).
|
|
Индивидуальные и групповые автопоилки: для животных. Схемы и конструкции...
Наброски и зарисовки растений, плодов, цветов: Освоить конструктивное построение структуры дерева через зарисовки отдельных деревьев, группы деревьев...
Двойное оплодотворение у цветковых растений: Оплодотворение - это процесс слияния мужской и женской половых клеток с образованием зиготы...
История создания датчика движения: Первый прибор для обнаружения движения был изобретен немецким физиком Генрихом Герцем...
© cyberpedia.su 2017-2024 - Не является автором материалов. Исключительное право сохранено за автором текста.
Если вы не хотите, чтобы данный материал был у нас на сайте, перейдите по ссылке: Нарушение авторских прав. Мы поможем в написании вашей работы!