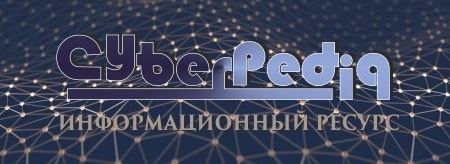
История развития хранилищ для нефти: Первые склады нефти появились в XVII веке. Они представляли собой землянные ямы-амбара глубиной 4…5 м...
Особенности сооружения опор в сложных условиях: Сооружение ВЛ в районах с суровыми климатическими и тяжелыми геологическими условиями...
Топ:
Методика измерений сопротивления растеканию тока анодного заземления: Анодный заземлитель (анод) – проводник, погруженный в электролитическую среду (грунт, раствор электролита) и подключенный к положительному...
Особенности труда и отдыха в условиях низких температур: К работам при низких температурах на открытом воздухе и в не отапливаемых помещениях допускаются лица не моложе 18 лет, прошедшие...
Техника безопасности при работе на пароконвектомате: К обслуживанию пароконвектомата допускаются лица, прошедшие технический минимум по эксплуатации оборудования...
Интересное:
Как мы говорим и как мы слушаем: общение можно сравнить с огромным зонтиком, под которым скрыто все...
Мероприятия для защиты от морозного пучения грунтов: Инженерная защита от морозного (криогенного) пучения грунтов необходима для легких малоэтажных зданий и других сооружений...
Национальное богатство страны и его составляющие: для оценки элементов национального богатства используются...
Дисциплины:
![]() |
![]() |
5.00
из
|
Заказать работу |
|
|
Цель работы
1. Изучение микроструктуры различных цветных сплавов.
2. Изучение влияния термической обработки на структуру и свойства алюминиевых сплавов типа дуралюминов.
Оборудование, приборы и материалы
При выполнении работы используют муфельные печи с термопарами и приборами для измерения температуры, твердомер, наждак и образцы из алюминиевых сплавов для проведения термической обработки.
Охрана труда
Загрузку и выгрузку образцов производить при выключенной электропечи с использованием клещей и рукавиц.
Во время работы на наждаке соблюдать правила техники безопасности: не работать на выбитом шлифовальном круге, не работать без защитного стекла и при неисправной блокировке. Нагретые образцы охлаждать на теплоизоляционных подкладках.
Краткие сведения из теории
В промышленности широко применяются цветные сплавы на основе алюминия, меди, титана, магния и др., которые подразделяются на деформируемые и литейные.
Из деформируемых сплавов методами горячей или холодной пластической деформации (прокатки, штамповки и др.) получают прутки, листы и др.
Детали из литейных сплавов давлением не обрабатывают. Эти сплавы должны обладать высокой жидкотекучестью, обеспечивающей хорошее заполнение литейной формы, малой усадкой, низкой склонностью к образованию горячих и холодных трещин и др. Лучшими литейными свойствами обладают сплавы, имеющие химический состав, близкий к эвтектическому.
Изучение микроструктуры цветных сплавов
Микроструктуру различных цветных сплавов студенты изучают по готовым микрошлифам. Описание микрошлифов приведено в табл. 4.1, а микроструктура цветных сплавов - на рис. 4.1.
|
Алюминиевые сплавы
Алюминиевые сплавы подразделяются на литейные и деформируемые.
Деформируемые алюминиевые сплавы подразделяются на термически неупрочняемые и термически упрочняемые.
К термически неупрочняемым деформируемым сплавам относятся алюминиевые сплавы, легированные марганцем (типа АМЦ), магнием (типа АМгЗ) и др.
К термически упрочняемым деформируемым сплавам относятся дуралюмины, например, марки Д16 (шлиф 42), высокопрочный сплав В95 и др.
В маркировке дуралюминов число – условный номер.
Таблица 4.1. Описание микрошлифов некоторых цветных сплавов
№ шлифа | Наименова- ние | Марка | Химический состав | Обработка | Структура |
Деформируемые сплавы
Литейные сплавы
Антифрикционные сплавы
42. Дуралюмин Д16 после отжига 42'. Дуралюмин Д16 после закалки (α-фаза и частицы θ-фазы) и искусственного старения
|
![]() | ![]() | ||
А б в
Рис. 4.3. Типы выделений при распаде пересыщенного твердого раствора:
а- зона ГП1; б- полукогерентную θ'- фаза; в - кристаллы θ - фазы (1-Al, 2-Cu)
Повышение температуры старения до 100-150 ОС приводит к утолщению зон ГП1 и обогащению их медью до стехиометрического соотношения СuАl2. Такие когерентные зоны обозначаются как ГП 2 (θ ''-фаза).
При температурах старения 150-200ОС образуется метастабильная θ'-фаза (CuAI2), имеющая полукогерентную связь с кристаллами α'- фазы (рис. 4.3, б).
При температурах старения свыше 200 ОС происходит нарушение когерентности θ'-фазы, образование некогерентных (обособленых) частиц θ-фазы (рис. 4.3, в), их коагуляция (укрупнение), приводящая к снижению твердости и прочности сплава, называемому перестариванием.
Объект исследования: металлографические образцы из цветных сплавов.
Таблица Результаты испытаний
Тип сплава и марка | До Т.О. | Вид Т.О. | Режим Т.О. | После Т.О. | ||||||
состояние | твердость | структура | tнагрева,°С | τвыдержки, мин. | Охл-ние | твердость | структура | |||
Л90 | литое | 44 HRF | дендритная | |||||||
х/д (холодно-деформиро-ванное) ε=50% | 78HRF | α-тв. раствор, волокнист. строение | Рекристал-лизационный отжиг | 300 | 30 | Возд. | 72 HRF | |||
500 | 30 | Возд. | 45 HRF | Мелкие равноосные зерна | ||||||
700 | 30 | Возд. | 38 HRF | Крупные зерна с двойниками | ||||||
ЛС59-1 | х/д | 100HRF | α+β' | Отжиг | 800 | 60 | Печь | 89 HRF | α+β | |
Закалка | 800 | 60 | Вода | 98 HRF | Пересыщ. α-тв. раствор | |||||
БрАЖН10-4-4 | Отожженное (литое) | 77 HRB |
| Закалка | 950 | 180 | Вода | 82 HRB | β'-игольчатый мартенсит | |
Закалка + отпуск | 950/400 | 180/120 | Вода/ возд. | 84 HRB | α+γ -эвтектоид | |||||
БрБ2 | Отожженное | 81 HRB (150 HB) | α+γII
| Закалка | 800 | 60 | Вода | 82HRF (85 HB) | α | |
Закалка + старение | 850/350 | 60/90 | Вода/ возд. | 42 HRС (390 HB) | α+ГП1 | |||||
АМг2М | Отожженное | 48 HRF | Закалка | 500 | 12 | Вода | 46 HRF |
| ||
х/д ε=30% | 82 HRF | |||||||||
Д16 | Литое | |||||||||
Отожженное | 62HRF |
| Закалка | 500 | Вода | 92 HRF | α'-пересыщ. тв. р-р | |||
Закалка 500+ искусств. старение | 100 | 60 | Возд. | 99 HRF | ||||||
200 | 60 | Возд | 91 HRF | |||||||
300 | 60 | Возд | 75 HRF | α+θ | ||||||
350 | 30 | Возд | 53 HRF | α+θ | ||||||
Закалка 500+ естеств. старение | 20 | 7 суток | 103 HRF | α'+ГП1 | ||||||
АЛ9
| Литое | 76HRF | α+эвтектика | Закалка | 70 HRF | |||||
Закалка+ старение | 200 | 57 HRF |
Твердость сплава Л90 имеет самую высокую прочность в холоднодеформированном состоянии и понижается с увеличением температуры нагрева.
Твердость сплава ЛС59-1 самая высокая в х/д состоянии и она выше при закалке, чем при отжиге.
Твердость сплаваБрАЖН10-4-4 самая высокая при закалке с отпуском и самая низкая в отожженном(литом) состоянии.
Твердость сплава БрБ2 (по Бринеллю HB) самая высокая достигается при закалке со старением, наименьшая достигается при закалке.
Твердость сплава АМг2М наивысшее значение имеет в холоднодеформированном состоянии, наименьшее при закалке
Твердость сплава Д16 достигает максимума при закалке с естественным старением, при закалке с искусственным старением убывает с увеличением температуры и при температуре 350ᵒС имеет самую малую твердость.
Твердость сплава АЛ9 наивысшая в исходном литом состоянии, наименьшая при закалке со старением.
Вывод: Каждый из цветных сплавов индивидуально реагирует на разные виды термической обработки. Цветные металлы и сплавы образуют особую группу конструкционных материалов. Прочность и твердость цветных сплавов невелика, даже после термообработки (закалка + старение). Некоторые сплавы, например, на основе меди не подвергаются термической обработке из-за отсутствия должного эффекта.
Контрольные вопросы
Что такое старение?
Старение представляет собой упрочение сплава за счет дисперсионного твердения, которое вызывается при распаде пересыщенного твердого раствора образованием зон повышенной концентрации легирующих элементов, затрудняющих движение дислокаций, что приводит к повышению прочности и твердости сплав
14. Что представляют собой зоны ГП1, ГП2, θ'-, θ''- и θ - фазы?
ГП1 - неупорядоченные скопления атомов меди толщиной 1- 2 атомных слоя и диаметром 10-50 нм
Повышение температуры старения до 100-150 ОС приводит к утолщению зон ГП1 и обогащению их медью до стехиометрического соотношения СuАl2. Такие когерентные зоны обозначаются как ГП 2 (θ ''-фаза).
|
При температурах старения 150-200ОС образуется метастабильная θ'-фаза (CuAI2), имеющая полукогерентную связь с кристаллами α'- фазы.
15. Как влияет температура старения на твердость дуралюмина?
В дуралюминах процесс зонного старения протекает при комнатных температурах и приводит к максимальному упрочнению, при температурах 100–150 °С зонное старение переходит в фазовое, а оно не приводит к получению максимальной прочности. При еще более высоких температурах (200 °С) происходит перерождени θ. -фазы в θ-фазу, что дает еще меньшее упрочнение
Цель работы
1. Изучение микроструктуры различных цветных сплавов.
2. Изучение влияния термической обработки на структуру и свойства алюминиевых сплавов типа дуралюминов.
Оборудование, приборы и материалы
При выполнении работы используют муфельные печи с термопарами и приборами для измерения температуры, твердомер, наждак и образцы из алюминиевых сплавов для проведения термической обработки.
Охрана труда
Загрузку и выгрузку образцов производить при выключенной электропечи с использованием клещей и рукавиц.
Во время работы на наждаке соблюдать правила техники безопасности: не работать на выбитом шлифовальном круге, не работать без защитного стекла и при неисправной блокировке. Нагретые образцы охлаждать на теплоизоляционных подкладках.
Краткие сведения из теории
В промышленности широко применяются цветные сплавы на основе алюминия, меди, титана, магния и др., которые подразделяются на деформируемые и литейные.
Из деформируемых сплавов методами горячей или холодной пластической деформации (прокатки, штамповки и др.) получают прутки, листы и др.
Детали из литейных сплавов давлением не обрабатывают. Эти сплавы должны обладать высокой жидкотекучестью, обеспечивающей хорошее заполнение литейной формы, малой усадкой, низкой склонностью к образованию горячих и холодных трещин и др. Лучшими литейными свойствами обладают сплавы, имеющие химический состав, близкий к эвтектическому.
Изучение микроструктуры цветных сплавов
Микроструктуру различных цветных сплавов студенты изучают по готовым микрошлифам. Описание микрошлифов приведено в табл. 4.1, а микроструктура цветных сплавов - на рис. 4.1.
Алюминиевые сплавы
Алюминиевые сплавы подразделяются на литейные и деформируемые.
Деформируемые алюминиевые сплавы подразделяются на термически неупрочняемые и термически упрочняемые.
К термически неупрочняемым деформируемым сплавам относятся алюминиевые сплавы, легированные марганцем (типа АМЦ), магнием (типа АМгЗ) и др.
К термически упрочняемым деформируемым сплавам относятся дуралюмины, например, марки Д16 (шлиф 42), высокопрочный сплав В95 и др.
|
В маркировке дуралюминов число – условный номер.
Таблица 4.1. Описание микрошлифов некоторых цветных сплавов
№ шлифа | Наименова- ние | Марка | Химический состав | Обработка | Структура |
Деформируемые сплавы
Литейные сплавы
Антифрикционные сплавы
42. Дуралюмин Д16 после отжига 42'. Дуралюмин Д16 после закалки (α-фаза и частицы θ-фазы) и искусственного старения
![]() | ![]() | ||
Латунь Л70 после отжига 44. Титановый сплав ВТ3-1
(светлые и темные кристаллы (α-твердый раствор + β-фаза) α-твердого раствора с двойниками)
45. Силумин немодифицированный 46. Силумин модифицированный (эвтектика (α +Si) и крупные (мелкозернистая эвтектика (α +Si)
кристаллы кремния Si) и кристаллы α-фазы)
48. Бронза оловянистая (литая) 49. Баббит Б83 оловянный (α-твердый БрО10Ф1 (дендриты α-твердого раствор-темный+кристаллы: крупные раствора и эвтектоид α+Cu31Sn8) β-фазы(SnSb), мелкие - Cu3Sn)
Рис. 4.1. Микроструктура некоторых цветных сплавов (указан номер микрошлифа согласно табл. 4.1)
Силумины
Силумины относятся к литейным сплавам системы алюминий - кремний. Силумин АК 12 (шлиф 45) в литом состоянии без модифицирования имеет структуру, состоящую из грубоигольчатой эвтектики Э(Al+Si) и крупных кристаллов кремния. После модифицирования силумина натрием, который в виде смеси фтористых NaF и хлористых NaCl солей в количестве 2–3% добавляют в жидкий сплав, структура становится доэвтектической, состоящей из мелкозернистой эвтектики и светлых зерен α-фазы-твердого раствора кремния в алюминии (шлиф 46), что обусловливает улучшение механических свойств - повышение прочности и пластичности.
В маркировке силуминов числа показывают содержание кремния и других легирующих элементов.
Медные сплавы
Медные сплавы подразделяются на латуни и бронзы.
Латуни – сплавы на основе меди и цинка. Микроструктура латуни Л70 (шлиф 43) состоит из α-фазы –твердого раствора Zn в Cu в виде светлых или с темным оттенком кристаллов с ГЦК решеткой, пронизанных полосками двойников. Растворимость Zn в Сu (α-фазе) достигает 39%. При содержании цинка в латуни до 39% ее структура состоит из α-фазы, а при более высоком - в ней дополнительно появляется черная β-фаза, представляющая собой электронное соединение CuZn с ОЦК решеткой. Латуни с (α + β) - структурой отличаются более высокой прочностью и пониженной пластичностью.
Маркировка деформируемых латуней начинается с буквы Л, за которой следуют буквы, обозначающие вид легирующего элемента (О – олово, Ц – цинк, К
– кремний, Мц – марганец, Ж – железо, Ф – фосфор, Б – бериллий и др.) и числа, показывающие в процентах содержание меди и легирующих элементов. Например, ЛК80-3- латунь, содержащая 80% Cu и 3% Si, остальное Zn.
В маркировке литейных латуней содержание компонентов сплава в процентах ставится после каждой обозначающей его буквы. Например, ЛЦ40Мц3Ж- латунь, содержащая 40% Zn, 3% Mn, 1% Fe, остальное Cu.
Бронзы представляют собой сплавы меди со всеми элементами, в которых цинк не является основным легирующим элементом. В зависимости от вида основного легирующего элемента бронзы подразделяются на оловянистые, алюминиевые, свинцовистые, бериллиевые и др. Бронзы обладают высокой жидкотекучестью и поэтому широко применяют в литом состоянии.
Микроструктура литой бронзы БрО10Ф1 (шлиф 48), в соответствии с диаграммой состояния медь – олово (рис. 4.1) состоит из дендритов α-фазы и светлых включений эвтектоида (дисперсной смеси α-фазы и кристаллов δ-фазы интерметаллида Cu31Sn8). Бронзы широко применяют для изготовления пароводяной арматуры, подшипников скольжения и др.
Маркировка бронзы начинается с «Бр» и букв, обозначающих вид легирующего элемента и чисел, показывающих их содержание в процентах
Титановые сплавы
Титан – полиморфный металл серого цвета с температурой плавления 1668ОС, плотностью 4,5 г/см3, имеет две полиморфные модификации: α-фазу с ГПУ решеткой, существующую до 882ОС, и β-фазу с ОЦК решеткой, существующую при температурах свыше 882ОС, отличается высокой прочностью (σВ≈1000МПа).
В промышленности в основном применяют титановые сплавы, имеющие структуру α-фазы (ОТ 4-1 и др.) и (α + β) – фаз (ВТ 3-1, ВТ 16 и др.).
Титановые α-сплавы характеризуются высокой прочностью и хрупкостью, не упрочняются термической обработкой, изделия из них подвергают отжигу для снятия внутренних напряжений. Титановые (α + β) – сплавы, благодаря наличию в структуре β-фазы, отличаются достаточно высокой пластичностью. Изделия из них подвергают как разупрочняющей термообработке (отжигу), так и упрочняющей, состоящей из закалки и старения.
Титановый сплав ВТ3-1 (шлиф 44) в состоянии после отжига имеет структуру, состоящую из α-фазы (светлые зерна) и β-фазы (темные зерна).
В маркировке титановых сплавов число – условный номер.
Магниевые сплавы
Магниевые сплавы обладают низкой плотностью (1,8 г/см3), высокой прочностью, хорошо поглощают вибрацию и хорошо свариваются в среде инертных газов, контактной сваркой. Широко применяются сплавы магния с Al (до 10 %), Zn (до 5-6 %), Mn (до 2.5 %), Zr (до 1.5 %).
Из литейных магниевых сплавов наиболее широко применяют сплавы системы Mg-AI-Zn. Микроструктура сплава МЛ 5 (шлиф 47) состоит из α-фазы (твердого раствора алюминия и цинка в магнии) и включений хрупкого интерметаллида Мg4Аl3.
Маркировка магниевых сплавов: деформируемых - МА, литейных – МЛ, далее условный номер. Например, магниевые сплавы: деформируемый МА2-1, литейный - МЛ5.
Антифрикционные легкоплавкие сплавы – баббиты
Баббиты - мягкие, легкоплавкие, антфрикционные сплавы систем олово- сурьма-медь (рис. 4.1), свинец-сурьма и др., Они характеризуются низким коэффициентом трения и используются для изготовления вкладышей подшипников скольжения.
Микроструктура баббита Б83 (шлиф 49) системы Sn-Sb-Cu, содержащего 83% Sn, остальное Cu и Sb (см. табл. 4.1), состоит из темных зерен мягкой α- фазы (твердого раствора сурьмы и меди в олове) и светлых кристаллов высокой твердости: крупных квадратной формы β-фазы (интерметаллида SnSb) и удлиненных игл или звездочек γ-фазы (интерметаллида Cu3Sn).
Мягкая α-фаза обеспечивает прирабатываемость и сохранение смазки, а твердые частицы интерметаллидов - износостойкость.
Влияние термической обработки на структуру и свойства дуралюминов
Дуралюмин Д16 (шлиф 42) относится к деформируемым термически упрочняемым алюминиевым сплавам системы AI-Сu (рис. 4.2) с дополнительным легированием Mg и Mn.
Основным легирующим элементом в дуралюминах служит медь, поэтому структурные превращения при их термической обработке удобно анализировать по диаграмме состояния двойного сплава AI-Сu (рис. 4.1).
Из диаграммы состояния видно, что при температурах выше линии ВС
структура дуралюминов состоит из α-фазы -твердого раствора меди в алюминии.
Линия ВС показывает уменьшение растворимости меди в α-фазе с 5, 7% при 547 ОС до 0,5% при комнатной температуре.
При этом в дуралюмине, содержащем ~ 4% Сu, после нагрева до Т = 500ОC (см. рис. 4.2) в случае медленного охлаждения (отжига) из α-фазы выделяются кристаллы частиц θ-фазы (интерметаллида CuAI2).
![]() |
Рис. 4.2. Диаграмма состояния сплавов Al - Cu: L – жидкий сплав;
α - твердый раствор меди в алюминии; θ – интерметаллическое соединение Си Al2; Э - эвтектика ( α + θ)
Для алюминиевых сплавов наибольшее распространение получили три вида термической обработки: отжиг, закалка и старение.
Отжиг
После отжига, состоящего из нагрева выше температуры фазового превращения (для дуралюмина 400-450 ОС), выдержки и медленного охлаждения с печью до ~200 ОС) и далее на воздухе, структура дуралюмина при содержании в
нем меди 3,8 - 4,8 % (см. рис. 4. 1) состоит из α-фазы, содержащей 0,5 % Сu, и частиц θ-фазы- интерметаллида CuAI2 с объемноцентрированной тетрагональной кристаллической решеткой, имеющей высокую твердость 530 HV или S-фазы- CuMgAI2 с ромбической кристаллической решеткой.
В равновесном состоянии все дуралюмины имеют двухфазную (α + θ) структуру.
Закалка
При закалке в воде с нагревом до температуры 495-505 ОС структура дуралюмина Д16 состоит из α'-фазы - пересыщенного твердого раствора меди в алюминии.
В свежезакаленном состоянии дуралюмины обладают высокой пластичностью и поэтому сразу после закалки могут быть подвергнуты холодной пластической деформации.
Старение
Старение представляет собой упрочение сплава за счет дисперсионного твердения, которое вызывается при распаде пересыщенного твердого раствора образованием зон повышенной концентрации легирующих элементов, затрудняющих движение дислокаций, что приводит к повышению прочности и твердости сплава
Старение подразделяется на естественное, происходящее при комнатной температуре, и искусственное, происходящее при нагреве.
В сплавах Al-Cu при естественном или низкотемпературном старении (ниже
50 ОС) образуются зоны Гинье-Престона ГП1 - неупорядоченные скопления атомов меди толщиной 1- 2 атомных слоя и диаметром 10-50 нм (рис. 4.3, а).
![]() |
А б в
Рис. 4.3. Типы выделений при распаде пересыщенного твердого раствора:
а- зона ГП1; б- полукогерентную θ'- фаза; в - кристаллы θ - фазы (1-Al, 2-Cu)
Повышение температуры старения до 100-150 ОС приводит к утолщению зон ГП1 и обогащению их медью до стехиометрического соотношения СuАl2. Такие когерентные зоны обозначаются как ГП 2 (θ ''-фаза).
При температурах старения 150-200ОС образуется метастабильная θ'-фаза (CuAI2), имеющая полукогерентную связь с кристаллами α'- фазы (рис. 4.3, б).
При температурах старения свыше 200 ОС происходит нарушение когерентности θ'-фазы, образование некогерентных (обособленых) частиц θ-фазы (рис. 4.3, в), их коагуляция (укрупнение), приводящая к снижению твердости и прочности сплава, называемому перестариванием.
Объект исследования: металлографические образцы из цветных сплавов.
Таблица Результаты испытаний
Тип сплава и марка | До Т.О. | Вид Т.О. | Режим Т.О. | После Т.О. | |||||
состояние | твердость | структура | tнагрева,°С | τвыдержки, мин. | Охл-ние | твердость | структура | ||
Л90 | литое | 44 HRF | дендритная | ||||||
х/д (холодно-деформиро-ванное) ε=50% | 78HRF | α-тв. раствор, волокнист. строение | Рекристал-лизационный отжиг | 300 | 30 | Возд. | 72 HRF | ||
500 | 30 | Возд. | 45 HRF | Мелкие равноосные зерна | |||||
700 | 30 | Возд. | 38 HRF | Крупные зерна с двойниками | |||||
ЛС59-1 | х/д | 100HRF | α+β' | Отжиг | 800 | 60 | Печь | 89 HRF | α+β |
Закалка | 800 | 60 | Вода | 98 HRF | Пересыщ. α-тв. раствор | ||||
БрАЖН10-4-4 | Отожженное (литое) | 77 HRB |
| Закалка | 950 | 180 | Вода | 82 HRB | β'-игольчатый мартенсит |
Закалка + отпуск | 950/400 | 180/120 | Вода/ возд. | 84 HRB | α+γ -эвтектоид | ||||
БрБ2 | Отожженное | 81 HRB (150 HB) | α+γII
| Закалка | 800 | 60 | Вода | 82HRF (85 HB) | α |
Закалка + старение | 850/350 | 60/90 | Вода/ возд. | 42 HRС (390 HB) | α+ГП1 | ||||
АМг2М | Отожженное | 48 HRF | Закалка | 500 | 12 | Вода | 46 HRF |
| |
х/д ε=30% | 82 HRF | ||||||||
Д16 | Литое | ||||||||
Отожженное | 62HRF |
| Закалка | 500 | Вода | 92 HRF | α'-пересыщ. тв. р-р | ||
Закалка 500+ искусств. старение | 100 | 60 | Возд. | 99 HRF | |||||
200 | 60 | Возд | 91 HRF | ||||||
300 | 60 | Возд | 75 HRF | α+θ | |||||
350 | 30 | Возд | 53 HRF | α+θ | |||||
Закалка 500+ естеств. старение | 20 | 7 суток | 103 HRF | α'+ГП1 | |||||
АЛ9 | Литое | 76HRF | α+эвтектика | Закалка | 70 HRF | ||||
Закалка+ старение | 200 | 57 HRF |
Твердость сплава Л90 имеет самую высокую прочность в холоднодеформированном состоянии и понижается с увеличением температуры нагрева.
Твердость сплава ЛС59-1 самая высокая в х/д состоянии и она выше при закалке, чем при отжиге.
Твердость сплаваБрАЖН10-4-4 самая высокая при закалке с отпуском и самая низкая в отожженном(литом) состоянии.
Твердость сплава БрБ2 (по Бринеллю HB) самая высокая достигается при закалке со старением, наименьшая достигается при закалке.
Твердость сплава АМг2М наивысшее значение имеет в холоднодеформированном состоянии, наименьшее при закалке
Твердость сплава Д16 достигает максимума при закалке с естественным старением, при закалке с искусственным старением убывает с увеличением температуры и при температуре 350ᵒС имеет самую малую твердость.
Твердость сплава АЛ9 наивысшая в исходном литом состоянии, наименьшая при закалке со старением.
Вывод: Каждый из цветных сплавов индивидуально реагирует на разные виды термической обработки. Цветные металлы и сплавы образуют особую группу конструкционных материалов. Прочность и твердость цветных сплавов невелика, даже после термообработки (закалка + старение). Некоторые сплавы, например, на основе меди не подвергаются термической обработке из-за отсутствия должного эффекта.
Контрольные вопросы
|
|
Автоматическое растормаживание колес: Тормозные устройства колес предназначены для уменьшения длины пробега и улучшения маневрирования ВС при...
Механическое удерживание земляных масс: Механическое удерживание земляных масс на склоне обеспечивают контрфорсными сооружениями различных конструкций...
Типы оградительных сооружений в морском порту: По расположению оградительных сооружений в плане различают волноломы, обе оконечности...
Эмиссия газов от очистных сооружений канализации: В последние годы внимание мирового сообщества сосредоточено на экологических проблемах...
© cyberpedia.su 2017-2024 - Не является автором материалов. Исключительное право сохранено за автором текста.
Если вы не хотите, чтобы данный материал был у нас на сайте, перейдите по ссылке: Нарушение авторских прав. Мы поможем в написании вашей работы!