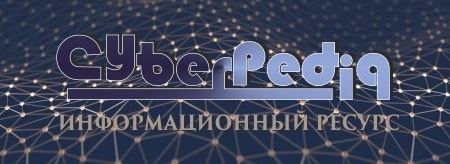
Индивидуальные очистные сооружения: К классу индивидуальных очистных сооружений относят сооружения, пропускная способность которых...
Типы оградительных сооружений в морском порту: По расположению оградительных сооружений в плане различают волноломы, обе оконечности...
Топ:
Характеристика АТП и сварочно-жестяницкого участка: Транспорт в настоящее время является одной из важнейших отраслей народного хозяйства...
Теоретическая значимость работы: Описание теоретической значимости (ценности) результатов исследования должно присутствовать во введении...
Интересное:
Отражение на счетах бухгалтерского учета процесса приобретения: Процесс заготовления представляет систему экономических событий, включающих приобретение организацией у поставщиков сырья...
Лечение прогрессирующих форм рака: Одним из наиболее важных достижений экспериментальной химиотерапии опухолей, начатой в 60-х и реализованной в 70-х годах, является...
Подходы к решению темы фильма: Существует три основных типа исторического фильма, имеющих между собой много общего...
Дисциплины:
![]() |
![]() |
5.00
из
|
Заказать работу |
|
|
ЭКОНОМИЧЕСКИЙ УНИВЕРСИТЕТ»
(СПбГЭУ)
ПОЛИТЕХНИЧЕСКИЙ УНИВЕРСИТЕТ
Специальность 15.02.07
«Автоматизация технологических процессов и производств (по отраслям)»
Контрольная работа
по дисциплине
«МДК.03.02 Приборы энергосбережения и
безопасности»
КР 15.02.07 09 00 00 ПЗ
Проверила преподаватель: | Выполнил(а): |
Иванова В.А. | Синякина Г. Е. |
Группа: 332-з |
2016
Рис. 2.5. Схема термоэлектрического пирометра:
1,2 — свободные (холодные) концы термопары; 3 — рабочий конец термопары (голый спай); А, В — термоэлектроды; С— соединительные провода; ЭП — вторичный электроизмерительный прибор; to — температура холодных концов термопары; t — температура горячего спая
Наибольшее распространение для промышленных термопар получили следующие материалы: платина, платинородий, хромель, алюмель и копель. Соответственно термопары получили названия: платинородий-платиновая, платинородиевая, хромель-алюмелевая, хромель-копелевая (табл. 1.1).
Таблица 1.1. Пределы измерения температур наиболее распространенными термопарами
Наименование термопары | Тип | Градуировка | Пределы измерения температур при длительном измерении, °С |
Платинородий-платиновая (10 % родия) | ТПП | ПП-1 | -20...+1 300 |
Платинородиевая (30 и 6 % родия) | ТПР | ПР-30/6 | +300...+1600 |
Хромель-алюмелевая | ТХА | ХА | -50...+1 000 |
Хромель-копелевая | ТХК | ХК | -50...+600 |
Рис. 1.6. Рабочие концы термопар:
а, б — термоэлектроды, соединенные сваркой; в — термоэлектроды, приваренные к дну защитного чехла
Термопары типов ТПП и ТПР из драгоценных металлов и сплавов применяются главным образом для измерения высокой температуры (выше 1000 °С), так как они обладают большой термостойкостью. Термопары типов ТХА и ТХК применяют для измерения температуры до 1 ООО °С. Эти термопары развивают значительные ТЭДС, что является их большим достоинством.
|
Термоэлектроды термопар из драгоценных металлов изготовляются обычно из проволоки диаметром 0,5 мм, а диаметр проволоки из недрагоценных металлов — 1,2...3,2 мм.
Рабочий конец термопары из тонких термоэлектродов образуется сваркой их концов (рис. 1.6, а, б), а из толстых — их скруткой и сваркой. Иногда для улучшения условий теплопередачи рабочий конец термопары из недрагоценных металлов приваривают к дну защитного металлического чехла (рис. 1.6, в).
Термоэлектроды термопары от спая до зажимов тщательно изолируются. В качестве изоляции применяют одно- и двухканальные фарфоровые трубки или бусы, надеваемые на термоэлектроды.
Термопара имеет стальной защитный чехол 5 (рис. 1.7), на который насажен подвижный фланец 6 со стопорным винтом для ее закрепления. Рабочий конец термопары 7 помещен в фарфоровый стаканчик 8. Оба термоэлектрода изолированы по длине фарфоровыми бусами 9. Головка состоит из литого корпуса 10, крышки 1 и сальника 2 с уплотнением для вывода проводов. Внутри головки расположена колодка 4 с двумя зажимами 3, несущими на себе две пары винтов 11 и 12 для закрепления термопроводов и соединительных проводов.
В качестве электроизмерительных приборов в термоэлектрических пирометрах применяются пирометрические милливольтметры и потенциометры.
Рис 2.7. Общий вид термопары:
1 — крышка; 2 — сальник с уплотнением для вывода проводов; 3 — зажимы;
4 — колодка; 5 — защитный чехол; 6 — подвижный фланец; 7 — рабочий конец термопары; 8 — фарфоровый стаканчик; 9 — фарфоровые бусы; 10 — корпус головки; 11,12 — винты
Рис. 1.10. Показывающий мембранный тягомер типа ТМ-П1 с профильной шкалой:
1 — мембранная коробка; 2 — фасонный рычаг; 3,12 — оси; 4 — поводок;
5 — пружина; 5 — корректор нуля; 7 — соединительная трубка; 8 — штуцер; 9 — рычаг; 10 — стопорный винт, противовес; 13 — стрелка; 14 — тяга, 15 — волосок
|
Пружинные манометры. Наиболее широкое применение для измерения избыточного давления жидкости, газа и пара получили пружинные манометры.
Принцип действия пружинных манометров основан на использовании упругой деформации специальных пружин, возникающей под влиянием измеряемого давления. По роду применяемых пружин манометры подразделяют на трубчатые (с одновитковой и многовитковой трубчатыми пружинами) и мембранные (с гармониковой мембраной — сильфоном).
Рис. 1.11. Показывающий манометр с одновитковой трубчатой пружиной:
1 — трубчатая пружина; 2 — стрелка; 3 — зубчатый сектор; 4 — пробка; 5 — поводок; б — корпус; 7 — штуцер; 8 — держатель; 9 — шкала; 10 — спиральная пружина; li — шестеренка
Показывающий манометр с одновитковой трубчатой пружиной приведен на рис. 1.11. Трубчатая пружина 1 эллиптического сечения одним концом жестко соединена с держателем 8, укрепленным в корпусе 6 манометра. Держатель имеет штуцер 7 с резьбой, служащей для сообщения прибора с измеряемой средой. Свободный конец пружины закрыт запаянной пробкой 4 с шарнирной осью. Посредством поводка 5 он связан с передаточным механизмом, состоящим из зубчатого сектора 3, сцепленного с шестеренкой 11, сидящей неподвижно на оси вместе с указывающей стрелкой 2. Спиральная пружина 10 прижимает зубцы шестеренки к зубцам сектора и устраняет «мертвый ход».
Под действием измеряемого давления трубчатая пружина частично раскручивается и тянет за собой поводок, приводящий в движение зубчатосекторный механизм и стрелку манометра, показывающую по шкале 9 величину этого давления.
По функциям различают технические, контрольные и образцовые манометры. Контрольные манометры типа МКО являются переносными приборами, служащими для периодических точных измерений давления, а также для поверки технических манометров на рабочем месте. Образцовые пружинные манометры типа МО применяются для поверки технических и контрольных манометров.
Электроконтактные манометры. В системах автоматического регулирования технологических процессов, в схемах сигнализации, устройствах тепловой защиты нашли применение электроконтактные манометры. На рис. 1.12 показаны внешний вид и принципиальная схема электроконтактного манометра. В приборе типа ЭКМ в качестве упругого чувствительного элемента используется одновитковая трубчатая пружина. По устройству прибор типа ЭКМ отличается от рассмотренного на рис. 1.11 пружинного манометра лишь наличием специальных электрических контактов i, 2 и 5. Установка контактов 1 и 2 может быть выполнена на любые отметки рабочей шкалы манометра вращением винта в головке 3, расположенной на наружной стороне стекла.
|
Если измеряемое давление среды в объекте уменьшится и достигнет нижнего значения, заданного на шкале с помощью контакта 1, то стрелка 4 посредством контакта 5 замкнет цепь и включится лампа определенного цвета, например, зеленого JI3.
Если же давление среды увеличится до верхнего значения, заданного с помощью контакта 2, то стрелка с помощью контакта 5 замкнет цепь красной лампы JIK.
Приборы типа ЭКМ имеют класс точности 2,5.
Рис. 1.12.
Рис. 1.13. Пружинный манометр электрический дистанционный типа МЭД:
1 — трубчатая пружина; 2 — сердечник (плунжер); 3 — дифференциально- трансформаторный преобразователь; R 1 и R 2 — электрические сопротивления; р — импульс давления; Е — выходной сигнал
Рис. 1.14 Конструкция датчика серии Метран-100
(модель 1411).
1 — фланец; 2 — корпусом; 3 — мембрана. 4 — жесткий центр; 5 — тяга; 6,7 — камеры; 8 — рычаг тензопреобразователя.
Между фланцем 1 и корпусом 2 крепится мембрана 3. К мембране приваривается жесткий центр 4. Жесткий центр с помощью тяги 5 соединен с рычагом тензопреобразователя 8. При измерении разности давлений (ДД) положительное давление подается в камеру 6, а отрицательное в камеру 7. Измеряемое давление, поданное в камеру 6 или 7, воздействует на мембрану и перемещает ее. Перемещение мембраны через жесткий центр 4 и тягу 5 передается на рычаг тензопреобразователя. Перемещение рычага вызывает деформацию мембраны тензопреобразователя, с которой жестко соединен рычаг. На мембране тензопреобразователя расположены тензорезисторы. Деформация мембраны тензопреобразователя вызывает изменение сопротивления тензорезисторов. Электронное устройство датчика преобразует изменение электрических сопротивлений в стандартный аналоговый сигнал.
|
В датчике Метран-150 в качестве одного из первичных преобразователей давления также используется новая емкостная ячейка Rosemount (рис. 1). Она образована двумя цилиндрическими основаниями 1, между которыми расположена плоская металлическая мембрана 2. На торцах цилиндрических оснований, обращенных к поверхности мембраны, имеются диэлектрические вкладыши 3 с тонкопленочными металлическими электродами 4. Цилиндрические основания и мембрана сварены между собой по наружному контуру, образуя симметричную и прочную конструкцию ячейки. Таким образом, между металлической мембраной и электродами, расположенными по обе стороны от нее, образованы две емкости конденсаторов.
При перемещении мембраны под действием измеряемого давления происходит увеличение емкости одного из конденсаторов и уменьшение емкости другого. Это дифференциальное изменение емкостей ячейки под действием давления преобразуется и обрабатывается в электронном устройстве датчика.
Рис. 1.15. Емкостная ячейка:
1 — цилиндрические основания; 2 — мембрана;
3 — диэлектрические вкладыши; 4 — электроды;
Емкостная ячейка – существенное, но недостаточное условие для успешной работы прибора, поэтому датчики давления Метран и Rosemount обладают следующими конструктивными особенностями:
· симметричность конструкции, которая обеспечивает одинаковое количество заполняющей жидкости с стороны камер высокого и низкого давления. Таким образом, при изменении температуры жидкость расширяется равномерно, что со стороны высокого давления, что со стороны низкого давления, обеспечивая взаимную компенсацию температурной погрешности;
· наиболее важным параметром конструкции является объем заполняющей жидкости: чем он меньше, тем меньше влияние заполняющей жидкости на точность показаний от расширения/сжатия под воздействием статического давления и температуры. Если в традиционной конструкции датчиков объем заполняющей жидкости равен ~ 5 см3, то в Метран-150 этот объем снижен до 0,2 см3, а в датчиках Rosemount он составляет всего лишь до 0,1 см3;
· следующим преимуществом конструкции является «свободно плавающий сенсор» – емкостная ячейка не имеет жесткой кинематической связи с корпусом модуля, ячейка всего лишь подвешена на двух капиллярах, данное решение снижает влияние механических напряжений в корпусе прибора при затяжке монтажных фланцев. Также оно снижает влияние вибрации, обеспечивая лучшие метрологические характеристики на таких применениях, ведь вибрации присутствуют практически во всех технологических процессах.
|
В начале 2010 года модельный ряд датчиков Метран-150 был расширен за счет новых моделей, которые обладают новыми опциями, такими, как:
· возможность применений в кислородных и кислородсодержащих средах;
· измерение уровня (гидростатического давления);
· возможность функционирования датчиков разности давлений при рабочем избыточном давлении до 40 МПа;
· использование новых материалов – Hastelloy® и тантал для применения в агрессивных средах;
· возможность перенастройки диапазонов измерений до 100:1.
Измерители давления многопредельные (далее - измерители) АДН АДР КБ «Агава», предназначены для измерения избыточного давления (разрежения) воздуха, и других газов, неагрессивных к материалам контактирующих деталей.
Область применения: системы измерения давления в промышленности, энергетике, жилищно-коммунальном хозяйстве.
· непрерывного измерения значения избыточного давления воздуха, природных и других газов, неагрессивных кматериалам контактирующих деталей (кремний, сталь);
· низкочастотной фильтрации сигналов избыточного давления;
· формирования дискретных выходных сигналов при достижении давления заданных уровней (уставок);
· формирования токового выходного сигнала 4 - 20 мА, пропорционального измеряемому параметру;
· регулирования давления по ПИ-закону*;
· дистанционного управления уровнем давления*;
· стабилизация давления (поддержания уровня между двумя уставками);
· формирования ШИМ сигналов для управления исполнительным механизмом.
Принцип действия измерителя основан на преобразовании давления в изменение сопротивлений тензорезисторов и измерении напряжения, возникающего в диагонали моста тензорезисторного датчика давления.
Измерители обеспечивают вывод значения измеренного давления на цифровой индикатор, индикацию уровня измеренного давления при помощи светодиодной линейки, формирование сигналов при достижении заданных уровней измеряемого давления (уставка).
Измеритель состоит из датчика давления и электронного преобразователя, состоящего из узла усилителя, узла микропроцессорной обработки сигнала и узла питания.
Электронный преобразователь служит для преобразования выходного сигнала тензо-моста в показания трёхзначного семисегментного индикатора, вывода информации об уровне измеренного давления на светодиодную линейку и формирования сигнала соответствующего заданной уставке.
Узел микропроцессорной обработки сигнала работает под управлением программного обеспечения (ПО). При помощи ПО осуществляются необходимые математические преобразования, цифровая фильтрация, управление трёхзначным семисегментным индикатором и светодиодной линейкой. Настройка измерителя производится через пользовательское меню.
Габаритные размеры измерителя приведены на рисунке 1.16.
Рис. 1.16
Внутренний диаметр присоединительной трубки, по которой подается измеряемая среда, равен 6 мм. Рекомендуется использовать рукав I-6,3-0,63-У ГОСТ 9356-75 (рукава резиновые для газовой сварки и резки металлов).
Приборы для измерения расхода вещества
Расход вещества и методы его измерения. Количество вещества, перемещаемое в единицу времени по трубопроводу или каналу, называется расходом вещества. Расход вещества выражают в единицах измерения объема или массы. Наиболее распространенные единицы измерения объемного расхода — м3/с, м3/ч, а для массового расхода — кг/с, кг/ч, т/ч. Для перевода объемных единиц измерения расхода в массовые и обратно используют формулу
G = V r
где G — массовый расход вещества, кг/с; V — объемный расход вещества, м3/с; r — плотность вещества, кг/м3.
К приборам, измеряющим суммарное количество вещества, прошедшее за известный промежуток времени, относятся счетчики. С их помощью фиксируются показания прибора в начале и конце периода измерения и по разности определяют общее количество жидкости, газа или пара за какой-то период работы.
Приборы, измеряющие или записывающие мгновенное значение измеряемого количества, отнесенное к единице времени, называются расходомерами. В ряде случаев расходомер снабжается суммирующим счетным механизмом (интегратором).
Для определения количества и расхода жидкости, газа или пара обычно применяют скоростной, объемный и дроссельный методы измерений. Скоростным и объемным методами определяют количество жидкости, газа и пара, а дроссельным — их расход.
Дроссельные расходомеры. Дроссельный метод измерения основан на использовании изменения статического давления среды, проходящей через искусственно суженное сечение трубопровода. Дроссельный расходомер состоит из сужающего устройства, устанавливаемого в трубопроводе в целях местного сжатия струи (первичный прибор), дифференциального манометра, предназначенного для измерения разности статических давлений протекающей среды до и после сужающего устройства (вторичный прибор), и соединительных линий — двух трубок, связывающих между собой первичный и вторичный приборы.
Сужающее устройство (диафрагма) имеет круглое отверстие, расположенное концентрично относительно стенок трубы, диаметр d которого меньше внутреннего диаметра D трубопровода.
Рис. 1.17. Характер потока в трубопроводе до и после сужающего устройства в виде диафрагмы:
D, d — диаметр трубопровода и сужающего устройства; F 0, F 1, F 2 — площади сечений соответственно трубопровода, сужающего устройства, максимально сжатого участка на схеме; v 1, v 2 — скорости потока в трубопроводе и максимально сжатом участке; —► — направление потока среды
При прохождении потока через сужающее устройство происходит изменение потенциальной энергии вещества, часть которой вследствие сжатия струи и соответствующего увеличения скорости потока преобразуется в кинетическую энергию. Изменение потенциальной энергии приводит к появлению разности статических давлений (перепад давления), которая определяется при помощи дифференциального манометра. По измеренному перепаду давления может быть определена кинетическая энергия потока при дросселировании, а по ней — средняя скорость и расход вещества.
На схеме установки диафрагмы в трубопроводе тонкими линиями показан характер потока до и после сужающего устройства (рис. 1.17).
По способу отбора статического давления к дифференциальному манометру стандартные измерительные диафрагмы подразделяют на камерные (I) и бескамерные (II) (рис. 1.18). В камерной диафрагме импульсы давления к дифференциальному манометру передаются через две кольцевые уравнительные камеры, позволяющие усреднить давление по окружности трубопровода и обеспечивающие более точное измерение перепада давления в камере.
Для установки диафрагм необходимо соблюдение определенных требований. Тщательно проводить центровку отверстия сужающего устройства относительно оси трубы. Не допускать наличия на внутренней поверхности трубопровода перед сужающим устройством больших неровностей (уступов, сварных швов, выступающих внутрь уплотнительных прокладок и др.). До и после сужающего устройства необходимо иметь прямые «успокоительные» участки трубопровода постоянного диаметра, так как разные местные сопротивления (колена, угольники, вентили, задвижки и др.) приводят к искажению профиля скоростей потока по сечению и увеличению погрешности измерения.
Наименьшие относительные (кратные по отношению к диаметру трубопровода D числа) длины прямых участков перед сужающим устройством (l 1) и после него (12) зависят от модуля диафрагмы т= d 2 / D 2 и характера местных сопротивлений и составляют:
· для участков до диафрагмы l 1 / D = 10... 80;
· для участков после диафрагмы l 2 / D = 4...8.
Рис. 1.18. Камерная (I) и бескамерная (II) стандартные измерительные диафрагмы:
D, d — диаметр трубопровода и сужающего устройства; f — угол скоса; «+», «-» — импульс давления соответственно до и после диафрагмы;
—► — направление потока
При правильно установленных диафрагмах основная погрешность измерения не превышает ±0,5... 1 %.
Объемные счетчики для газа. Для измерения объема горючего газа используются объемные ротационные счетчики. Ротационный счетчик содержит измерительную камеру 1 (рис. 1.19, а), в которой размещены две широкие вращающиеся в разные стороны лопасти 2 и 3 восьмеричной формы.
Действие ротационного счетчика основано на вытеснении определенных объемов газа, заключенных между стенками измерительной камеры и лопастями, при вращении последних под влиянием разности давлений газа до счетчика и после него. Величина зазоров между шестернями и стенками измерительной камеры не превышает 0,03...
0,06 мм, вследствие чего погрешность измерения из-за перетекания газа через них невелика.
В приборе РС-100М роликовый счетный механизм 4 (рис. 1.19, б) связан с одной из лопастей при помощи магнитной муфты или непосредственно с выходной осью, пропущенной через сальниковое уплотнение. Для контроля за степенью засоренности счетчика в него встроен водяной двухтрубный дифференциальный манометр 5, измеряющий перепад давления в приборе.
Ротационные счетчики устанавливают на вертикальных участках газопровода с нисходящим потоком газа. Входной патрубок счетчика снабжен сетчатым фильтром для очистки газа от механических примесей.
Ротационные счетчики типа PC выпускаются на номинальный расход газа 40... 1 000 м3/ч. Сопротивление счетчиков при номинальном расходе газа составляет 300 Па (30 мм вод. ст.).
Рис. 1. 19. Ротационный счетчик:
a - схема; б - счетчик РС-100М; 1 - измерительная камера; 2,3- лопасти;
4 - счетный механизм; 5 — дифференциальный манометр; ---► — направление потока среды; —► направление вращения лопастей
Турбинные (скоростные) счетчики. Тахометрический турбинный газовый счетчик (рис. 1.20) состоит из чугунного корпуса 1 с фланцами для присоединения к трубопроводу, турбины 2, счетчика 3, обтекателей 5, расположенных с обеих сторон турбины. Лопатки турбины размещены в кольцевом зазоре между гильзой 7 и обтекателями 5 и имеют наклон примерно 45°. Спереди и сзади турбины установлены неподвижные направляющие лопатки 6, выравнивающие поток газа. Турбина связана посредством червячной передачи 4 со счетчиком 3. Частота вращения турбины пропорциональна скорости течения газа, а следовательно, и его расходу.
Рис. 1.20. Турбинный (тахометрический) гиоаый сметчик:
1 — корпус; 2 — турбина; 3 — счетчик;
4 — червячная передача; 5 — обтекатель;
6 — неподвижная направляющая лопатка;
7 — гильза; —► — направление потока среды
Рис. 1.21. Гидростатические уровнемеры паровых котлов:
а — с жидкостным однотрубным дифференциальным манометром;
б — с мембранным дифференциальным манометром;
1, 3, 11,12 — соединительные трубки;
2 — уравнительный сосуд;
4,10 — грязеуловители;
5 — вентиль;
6 — лампа с рефлектором;
7 — измерительная трубка;
8 — пробка; 9 — широкий сосуд;
13 — дифференциальный манометр
Сигнализатор уровня жидкости САУ-M6 «ОВЕН». Сигнализатор уровня жидкости трехканальный ОВЕН САУ-М6 – предназначен для автоматизации технологических процессов, связанных с контролем и регулированием уровня жидкости.
![]() |
Контроль уровня осуществляется при помощи 4-х электродного кондуктометрического датчика, три сигнальных электрода которого расположены в резервуаре на заданных по условиям технологического процесса отметках: уровень 1, уровень 2, уровень 3 – и подключаются ко входам прибора 1–3. Питание датчика уровня осуществляется переменным напряжением.
САУ-М6 включает в себя три независимых канала контроля, в состав каждого канала входят:
· вход для измерения сопротивления кондуктометрического датчика на переменном токе;
· регулятор чувствительности, позволяющий изменять чувствительность канала контроля уровня к электропроводности жидкости;
· пороговое устройство (ПУ), фиксирующее достижение рабочей жидкостью заданного уровня, а также формирующее сигналы управления выходным реле;
· коммутатор для переключения канала в инверсный режим работы;
· выходное реле для управления внешним оборудованием; срабатывание реле происходит при контакте соответствующего электрода с жидкостью.
Рис. 1.22.
Функциональная схема
САУ-М6
Рис. 1.23. Пример временной диаграммы работы реле
Режим работы реле в любом из каналов может быть изменен пользователем при помощи соответствующего коммутатора.
При соприкосновении электрода датчика с жидкостью выходное реле в зависимости от положения его коммутатора может переводиться в состояние «выключено» (см. рис.) или, наоборот, в состояние «включено».
Комплект поставки
· Блок индикации;
· Блок(и) датчиков;
· Блок(и) коммутации.
Хоббит-Т-CO-CH4 | с цифровой индикацией | 16 | СО | 0 - 150 мг/м3 | 20 - 120 мг/м3 |
с креплением на DIN-рейку без цифровой индикации показаний | 2 | СН4 | 0 - 2,55 об.% | 0,22 – 2,20 об.% | |
с креплением на DIN-рейку с цифровой индикацией показаний | 2 |
ТЕХНИЧЕСКИЕ ХАРАКТЕРИСТИКИ
Конструкция удовлетворяет требованиям ГОСТ 13320-81 | |
число датчиков [каналов] на один блок индикации | до 16 |
диапазон показаний | CH4: 0 – 2,55 об.%; CO: 0 – 150 мг/м3 |
диапазон измерения концентраций | CH4: 0,22 – 2,20 об.%; CO: 20 – 120 мг/м3 |
относительная погрешность измерений | 25% |
индикация показаний | ЖК-дисплей, токовый выход |
пороги срабатывания сигнализации по каналам | СH4: 10%НКПР, до 50%НКПР CO: 20 и 100 мг/м3 |
длина кабеля между датчиком и блоком индикации | до 1200 м |
напряжение питания | 220 В, 50 Гц |
потребляемая мощность | 60 Вт |
время установления показаний по уровню 0.9, не более | 10 с |
рабочий диапазон температур | от -40° С до +50° С |
масса: блока индикации блока датчика | 3500 г 700 г |
габариты: блока индикации блока датчика | 260x240x120мм мм 50x165мм |
обладает токовым и релейным выходом для управления внешними устройствами - включением аварийной вентиляции, сирены, клапана и т.п. |
Газоанализатор ЭССА-CO-CH4 исполнение МБ (моноблок). Газоанализатор стационарный ЭССА-CO-CH4 исп. МБ (моноблок) предназначена для контроля содержания оксида углерода (CO) и метана в воздухе рабочей зоны. При превышении установленных порогов по обоим каналам, система способна включать внешние устройства при помощи релейных выходов. Широкое применение данная двухгазовая система нашла в котельном хозяйстве.
Система представляет собой 2 блока: блок измерения и сигнализации (БИС) со встроенным в него сенсором на оксид углерода (электрохимия), измерительный преобразователь (ИП) метана. ИП на метан в зависимости от модификации может быть 1 или 2. Модификаций у газоанализатора ЭССА-CO-CH4 МБ две:
1) С одним выносным датчиком на метан;
2) С двумя выносными датчиками на метан.
Отбор: диффузионный
Минимальная канальность и количество контролируемых газов: 1
Максимальная канальность: 3
Максимальное количество контролируемых газов: 2
Тип сенсора: электрохимический, термохимический
Газы: оксид углерода, метан,
Пыле-влагозащита: IP40 (блок индикации и сигнализации), IP54 (датчик)
Взрывозащита: не предусмотрена
Выходные сигналы: «сухие» контакты реле по каждому из 2х порогов
Индикация: световая, звуковая
Единицы измерения: СО в мг/м3, СН4 в % об
Рабочий диапазон температур: от 0°С до 45°С
Питание: от сети переменного тока 220 В
Габариты: 160х130х90 мм (блок измерения и сигнализации ЭССА-СО), 210х182х90 мм (БИС для ЭССА-СО-СН4, ЭССА–СО–СН4/2), 235х184х90 мм (БИС ЭССА-СО-СН4 с БУК), 110х100х55 (измерительный преобр.)
Масса: 1,0 кг (блок измерения и сигнализации), 1,25 кг (БИС ЭССА-СО-СН4 с БУК), 0,4 кг (измерительный преобразователь)
Гарантийный срок: 1,5 года
Межповерочный интервал: 1 год
Газоанализатор ЭССА-СО-СН4 состоит из БИС со встроенным в него электрохимическим детектором оксида углерода (измерительный канал СО) и одного измерительного преобразователя (ИП) метана.
Газоанализатор ЭССА-СО-СН4/2 состоит из БИС со встроенным в него электрохимическим детектором оксида углерода (измерительный канал СО) и 2-х ИП метана.
БИС соединяется с ИП метана измерительным кабелем (экранированным, 3-х жильным), образуя измерительный канал СН4.
Газоанализатор ЭССА-CO-CH4 имеет два порога сигнализации для каждого измеряемого компонента. Конструкция газоанализатора предназначена для настенного монтажа.
Газоанализаторы ЭССА-СО-СН4/(2) имеют реле НЕИСПРАВНОСТЬ, сраба-тывающее при обрыве, коротком замыкании измерительного кабеля, а также при некоторых неисправностях ИП метана и при обесточивании БИС. Каждое реле, кроме реле НЕИСПРАВНОСТЬ, имеет пару замыкающих и пару размыкающих контактов. Реле НЕИСПРАВНОСТЬ имеет только пару замыкающих контактов. Контакты реле не имеют гальванической связи с электрическими цепями газоанализатора – «сухие» контакты. Контакты реле предназначены для коммутации электрических цепей постоянного и переменного тока частотой до 50 Гц. Коммутируемый ток контактами реле может иметь значения от 0,1 до 3,0 А при напряжении от 12 до 220 В.
Рис. 1.27. Внешний вид газоанализатора ЭССА-СО-СН4/(2) исп. МБ
1 - монтажное отверстие; 2 - светодиоды 1-го измерительного канала СН4; 3*- светодиоды 2-го измерительного канала СН4; 4 - светодиоды измерительного канала СО; 5 - детектор СО; 6 - кнопка СБРОС; 7 - предохранитель; 8 - кабельный ввод сетевого кабеля; 9 - гнездо «общий»; | 10 - гнездо контрольной точки 1-го измерительного канала СН4; 11* - гнездо контрольной точки 2-го измерительного канала СН4; 12 - гнездо контрольной точки измерительного канала СО; 13 - разъем для подключения ИП СН4; 14 - разъем для подключения внешних исполнительных устройств; 15**- резистор установки чувствительности измерительного канала СО; 16**- резистор установки нуля измерительного канала СО. |
* - только для ЭССА-СО-СН4/2 |
![]() |
Техические харатеристики
Параметр
Принцип измерения
Диапазон измерения, % об
Основная приведенная погрешность измерения, %
Число каналов
Число порогов срабатывания сигнализации
Пороги сигнализации, % об
Число ИП (N)
Сигнализация
Срок службы сенсора, месяцев
Максимальное расстояние (м) между БС и ИП при сечении жил кабеля
Рабочие условия эксплуатации:
Межповерочный интервал, месяцев
Гарантийный срок, месяцев
Рис. 1.28. Принципиальная схема работы запально-защитного устройства:
1 — управляющий импульс от автомата контроля пламени; 2 — подача топлива в основную горелку; 3 — основная горелка; 4 — подача воздуха в основную горелку; 5 — электромагнитный вентиль; б — газовая линия запальника;
7 — центральный (высоковольтный) электрод;
8 — высоковольтный трансформатор;
9 — промежуточное реле; 10 — управляющий прибор АКП; 11 — фотодатчик
Рис. 1.29. Фотодатчик:
1 — стекло; 2 — фоторезистор;
3 — корпус; 4 — крышка;
5 — штепсельный разъем
При розжиге котла, оснащенного автоматикой, полностью сохраняется порядок работ при розжиге котла без автоматики, но дополнительно необходимо выполнить следующие операции.
При подготовке котла к работе:
· все ключи управления на щите котла перевести в положение «Отключено», регуляторы перевести на дистанционное (ручное) управление;
· подать напряжение на щит управления;
· проверить работу каждого ИМ и регулирующего органа. При нажатии на кнопку (тумблер) «Больше» рычаг изменяет положение, открывая регулирующий орган. При нажатии на кнопку «Меньше» рычаг возвращается в исходное положение, закрывая регулирующий орган. Котлы с автоматикой «Контур» могут быть оснащены переносными
· запальниками и электрозапальниками, входящими в ЗЗУ.
· При розжиге горелок запально-защитным устройством:
· повернуть ключ управления котлом в положение «Розжиг». При этом срабатывает
|
|
Индивидуальные очистные сооружения: К классу индивидуальных очистных сооружений относят сооружения, пропускная способность которых...
Опора деревянной одностоечной и способы укрепление угловых опор: Опоры ВЛ - конструкции, предназначенные для поддерживания проводов на необходимой высоте над землей, водой...
Наброски и зарисовки растений, плодов, цветов: Освоить конструктивное построение структуры дерева через зарисовки отдельных деревьев, группы деревьев...
Механическое удерживание земляных масс: Механическое удерживание земляных масс на склоне обеспечивают контрфорсными сооружениями различных конструкций...
© cyberpedia.su 2017-2024 - Не является автором материалов. Исключительное право сохранено за автором текста.
Если вы не хотите, чтобы данный материал был у нас на сайте, перейдите по ссылке: Нарушение авторских прав. Мы поможем в написании вашей работы!