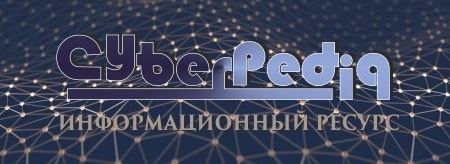
Таксономические единицы (категории) растений: Каждая система классификации состоит из определённых соподчиненных друг другу...
Индивидуальные и групповые автопоилки: для животных. Схемы и конструкции...
Топ:
Комплексной системы оценки состояния охраны труда на производственном объекте (КСОТ-П): Цели и задачи Комплексной системы оценки состояния охраны труда и определению факторов рисков по охране труда...
Когда производится ограждение поезда, остановившегося на перегоне: Во всех случаях немедленно должно быть ограждено место препятствия для движения поездов на смежном пути двухпутного...
Интересное:
Берегоукрепление оползневых склонов: На прибрежных склонах основной причиной развития оползневых процессов является подмыв водами рек естественных склонов...
Инженерная защита территорий, зданий и сооружений от опасных геологических процессов: Изучение оползневых явлений, оценка устойчивости склонов и проектирование противооползневых сооружений — актуальнейшие задачи, стоящие перед отечественными...
Уполаживание и террасирование склонов: Если глубина оврага более 5 м необходимо устройство берм. Варианты использования оврагов для градостроительных целей...
Дисциплины:
![]() |
![]() |
5.00
из
|
Заказать работу |
|
|
УЧЕБНОЕ ПОСОБИЕ
ОП.03 ТЕХНИЧЕСКОЕ ОСНАЩЕНИЕ ПРЕДПРИЯТИЙ ОБЩЕСТВЕННОГО ПИТАНИЯ
основной профессиональной образовательной программы по специальности
ТЕХНОЛОГИЯ ПРОДУКЦИИ ОБЩЕСТВЕННОГО ПИТАНИЯ
СОДЕРЖАНИЕ
Стр. | |
Раздел 1. Общие сведения о структуре машин и механизмов | 4 |
Тема 1.1 Детали машин | 4 |
Тема 1.2 Детали передач | 8 |
Тема 1.3 Электроустановки | 13 |
Раздел 2 Механическое оборудование | 18 |
Тема 2.1. Классификация механического оборудования | 18 |
Тема 2.2... Универсальные приводы общего и специального назначения | 22 |
Тема 2.3.. Машины для обработки овощей | 25 |
Тема 2.4. Машины и механизмы для нарезки и протирания овощей | 27 |
Тема 2.5.. Машины и механизмы для обработки мяса и рыбы | 29 |
Тема 2.6. Машины и механизмы для обработки муки. | 33 |
Лекция 2.7. Машины, приготовления и раскатки теста. | 34 |
Тема 2.8 Взбивальные машины и механизмы | 36 |
Тема 2.9 Машины для нарезки хлеба и гастрономических продуктов. | 38 |
Тема 2.10.Подъемно- транспортное оборудование | 43 |
Тема 2.11.Весоизмерительное оборудование. | 49 |
Тема 2.12. Контрольно- кассовые машины, значение и классификация. | 59 |
Раздел 3 Тепловое оборудование | 70 |
Тема 3.1. Основы теплотехники | 70 |
Тема 3.2.Теплогенерирующие устройства | 78 |
Тема 3.3.Общие сведения о тепловом оборудовании | 88 |
Тема 3.4Варочное оборудование | 96 |
Тема 3.5. Жарочно- пекарское оборудование Электросковороды | 102 |
Тема 3.6. Электрофритюрницы | 103 |
Тема 3.7. Жарочные и пекарские шкафы | 104 |
Тема 3.8.Универсальное оборудование | 106 |
Тема 3.9.Специализированные аппараты. | 111 |
Тема 3.10 Многофункциональное оборудование, тепловые линии. | 113 |
Тема 3.11Многофункциональное оборудование: пароконвектомат | 115 |
Тема 3.12Водогрейное оборудование | 117 |
Тема 3.13Оборудование для раздачи пищи. | 118 |
Раздел 4 Холодильное оборудование | 120 |
Тема 4.1 Основы холодильной техники. | 120 |
Тема 4.2. Холодильные машины | 122 |
Тема 4.3. Торгово-технологическое холодильное оборудование | 124 |
Раздел 1. Общие сведения о структуре машин и механизмов
|
Тема 1.1 Детали машин
Машиной называется техническое устройство, в котором разные виды энергии (электрическая, мускульная и др.) превращаются в механическую энергию. Машина, которая выполняет все необходимые операции по заданной программе без непосредственного участия человека, — это уже автомат.
Машина представляет собой совокупность нескольких механизмов (узлов), при приведении в действие одного из которых приходит в действие вся машина.
Механизм — совокупность нескольких деталей. Деталь — наименьшая часть, предел делимости машины. Механизмы и детали машин изготавливаются из различных материалов: металлов, пластмасс, оргстекла, дерева, теплоизоляционных материалов, пластика и композиционных материалов. Наибольшее применение в машиностроении нашли металлы, используемые либо в чистом виде, либо в виде сплавов. Черные и цветные металлы в чистом виде применяются редко, так как в них отсутствует комплекс необходимых свойств. Из чистых металлов в основном применяются алюминий, медь, олово, хром, никель. Сплавы же по своим характеристикам значительно превосходят многие чистые металлы, поэтому большинство деталей изготавливается из сплавов металлов друг с другом н сплавов нескольких металлов и металлов с неметаллами Из сплавов черных металлов наиболее часто применяются сталь и чугун, представляющие собой соединение железа с углеродом. В стали углерода содержится до 2 %, в чугуне — 2—4 %.
Наличие в чугуне углерода свыше 2 % позволяет ему выдерживать намного большие нагрузки, чем сталь, но при этом повышается хрупкость.
На свойства стали значительное влияние оказывают различные примеси и добавки металлов, а также термическая обработка — закаливание, отпуск, отжиг. Закаливание — нагрев стали до определенной температуры, а затем быстрое ее охлаждение, что приводит к увеличению хрупкости, прочности, твердости. Отпуск и отжиг — нагрев до определенной температуры с последующим постепенным охлаждением. Отпуск и отжиг стали уменьшают действие закаливания, твердость и хрупкость, повышают пластичность.
|
Из сплавов цветных металлов чаще применяются латуни, бронза, баббиты, алюминиевые сплавы.
Латунями называются сплавы меди с цинком; в некоторые латуни добавляют другие легирующие компоненты, улучшающие их свойства. Латуни тверже и прочнее самой меди, более коррозионностойкие.
Бронза — сплав меди с любыми металлами, кроме цинка. Данные сплавы обладают высокой коррозионной стойкостью, высокими антифрикционными свойствами.
Баббиты представляют собой сплавы олова или свинца с различными добавками, антифрикционные свойства которых позволяют использовать их для изготовления вкладышей подшипников.
Алюминиевые сплавы — соединения алюминия с медью, марганцем, кремнием и магнием.
Машиностроительные материалы обладают следующими механическими характеристиками: твердостью, упругостью, пластичностью, хрупкостью.
Твердость — способность материала противостоять проникновению в него другого тела.
Упругость — свойство материала изменять свою форму под воздействием внешних сил и восстанавливать ее после прекращения такого воздействия.
Пластичность - свойство материала деформироваться под действием нагрузки и сохранять приобретенную форму после прекращения нагрузки.
Хрупкость — свойство материала разрушаться под действием быстродействующих сил.
В последнее время в оборудовании для предприятий общественного питания много деталей изготавливается из пластмасс (соединение органических смол с различными добавками). Такие детали легче, не проводят электроток, не горят, дешевле, но с теми же механическими характеристиками, что и детали из металлов или сплавов.
Классификация деталей машин
Все детали машин делятся на две группы: детали соединений И детали передач. Детали соединений служат для скрепления узлов И механизмов друг с другом, а детали передач — для передачи движения, изменения направления и скорости движения
|
Детали соединений
Жесткое соединение деталей машин может быть двух видов: p;i п.емное и неразъемное.
Неразъемные соединения позволяют выдерживать большие нагрузки, чем разъемные, они проще и дешевле, но при необходимости разъединения деталей приходится нарушать их целостность. Как видно из рис. 1.2, к неразъемным относятся сварные, заклепочные, клеевые соединения, а также соединения пайкой (паяные) и посадка с натягом.
Сварные соединения образуются путем сварки деталей. При этом различают сварку давлением, плавлением, контактную, трением, ультразвуком, электронно-лучевую и т. д.
Сварка — соединение деталей посредством их местного нагрева до пластичного состояния и использования сил молекулярного взаимодействия на месте стыка, где образуется сварной шов. Для местного нагрева используется энергия электрической дуги (электросварка), энергия горящего газа (газосварка), нагрев тел при трении. Для сварки тугоплавких металлов и получения высококачественных швов применяют электронно-лучевую сварку, при которой нагрев производится электронным лучом в вакууме.
По назначению различают сварные швы: прочные, способные выдерживать большие нагрузки; плотные, обеспечивающие герметичность; прочно-плотные, например для изготовления сосудов, работающих под повышенным давлением.
В зависимости от расположения в пространстве соединяемых деталей швы бывают стыковые, когда детали находятся в одной плоскости (рис. 1.3, а, б), и угловые, когда детали соединяются внахлестку (в), в тавр (г) и под углом (д).
Соединения пайкой выполняются тогда, когда невозможно и (или) нежелательно применять сварку. В этом случае до температуры плавления нагревают не соединяемые детали, а припой — специальный металл или сплав, который плавится при более низкой температуре, чем металл соединяемых деталей. С помощью паяльника расплавленным припоем обрабатывают поверхности соединяемых деталей, и они скрепляются силами молекулярного сцепления. После остывания припоя детали жестко соединяются друг с другом.
|
Заклепочные соединения. В случаях когда невозможно применить самый дешевый способ соединения — сваркой, детали соединяют специальным элементом — заклепкой (рис. 1.4).
Заклепка — стержень цилиндрической формы с закладной головкой, которая может быть различной формы: полусферической, потайной, полупотайной и плоскоконической.
Заклепки изготавливаются из алюминия, меди, их сплавов, реже из стали. Размеры заклепок и их форма стандартизированы. Для соединения деталей в них просверливаются сквозные; отверстия совмещают и снизу вставляют заклепку, под которую устанавливают поддержку. На выступающий конец заклепки воздействует обжимкой (молотком, кувалдой), в результате чего
конец превращается в замыкающую головку, а заклепка становится короче, но толще, заполняя пространство между деталями. Расположенные в ряд заклепки образуют заклепочные швы, которые по назначению бывают: прочные, плотные и прочно-плотные. При соединении деталей встык применяют одну или две накладки, которые располагают над и(или) под соединяемыми деталями.
Посадка с натягом применяется значительно реже, чем сварные и заклепочные соединения. Для этого одну из соединяемых деталей со сквозным отверстием или углублением нагревают до высокой температуры, при этом диаметр отверстия увеличивается, деталь натягивают на другую. При остывании отверстие принимает первоначальный размер и происходит жесткое соединение деталей. При необходимости аналогичным образом детали можно рассоединить.
Клеевые соединения. Промышленность стала выпускать новые виды клея, способного скреплять различные материалы: дерево с металлом, пластик с металлом, металлы с металлами и т. п. Новые виды клея позволяют соединяемым деталям выдерживать определенные нагрузки, что расширяет возможности использования клеевых соединений в машиностроении
Разъемные соединения
В отличие от неразъемных разъемные соединения позволяют производить многократную сборку и разборку деталей без нарушения их целостности. К разъемным относятся резьбовые, клиновые, шпоночные, шлицевые, штифтовые и профильные соединения.
Резьбовое соединение деталей происходит путем завинчивания одной детали внутрь другой с помощью резьбовой (винтовой) поверхности.
В таких соединениях резьба у одной детали нарезается снаружи, а у другой внутри. При этом завинчиваемая деталь совершает вращательное движение вокруг своей оси и одновременно поступательное движение вдоль нее.
В торговом машиностроении для соединения деталей и агрегатов широко применяются различнхые крепежные детали с резьбой: болты, винты, шпильки, гайки и шайбы.
|
Болты и винты по конструкции схожи между собой — цилиндрической формы стержень с головкой на одном конце и резьбой на другом. Головки болтов бывают различной формы: шестигранной, шестигранной с отверстием полукруглой и с квадратным подголовником или с усом, потайной. Соединение болтом наиболее простое и распространенное. В соединяемых деталях просверливаются сквозные отверстия; отверстия совмещают и вставляют в них болт, а на выступающий конец с резьбой навинчивают гайку.
Гайка — деталь различной формы со сквозным отверстием и внутренней резьбой Иногда при вибрациях и динамических нагрузках происходит самовывинчивание гаек. Для предотвращения этого и увеличения силы трения применяют гаечный замок — вплотную к основной гайке навинчивают контргайку ли используют пружинные шайбы, имеющие срез, загнутые концы которого предотвращают самовывинчивание.
Винты применяются в том случае, когда невозможно или экономически невыгодно применять соединение болтом. Винтовое соединение менее надежно, выдерживает меньшие нагрузки, чем болтовое. Для соединения винтом в одной из деталей просверливают сквозное отверстие, а в другой детали в углублении для стержня винта нарезается внутренняя резьба. Через деталь со сквозным отверстием вставляют стержень винта и вкручивают его во вторую деталь. Головки винтов могут быть различной формы: шестигранные и четырехгранные под гаечный ключ потайные полупотайные, полусферические со шлицей (прорезью) под отвертку, шестигранные и четырехгранные со шлиией для двойного применения, полукруглые, без головки со шлицей и под ключ, с головкой под ключ. Для облегчения подъема изделий применяются рым-болты (л), головка которых выполнена в виде большого кольца для захвата грузоподъемными машинами. Для закрепления на валах различных деталей применяют установочные винты с плоскими, коническими или цилиндрическими концами без головок, имеющие шлицы под отвертку обыкновенную либо с крестообразным шлицем под специальную отвертку.
Шпилька — цилиндрический стержень с резьбой на обоих концах. При соединении с помощью шпильки можно получать как болтовое соединение (реже), так и соединение винтом. Если в обе-. их деталях имеются сквозные отверстия, то в совмещенные отверстия вставляется шпилька, а на выступающие концы стержня с двух сторон навинчиваются гайки.
Если в одной из деталей есть резьбовое углубление, то в него до отказа завинчивается один конец шпильки, на стержень надевается вторая деталь, а затем на свободный конец шпильки навинчивается гайка. Для разборки соединения достаточно отвинтить гайку и удалить деталь, а шпильку можно не выворачивать.
Соединения с помощью шпилек более надежны, чем соединения винтом, а в некоторых случаях и надежнее, чем болтом.
Клиновые соединения. В соединениях данного типа для скрепления деталей используется клин, представляющий собой пластинку, ограниченную параллельными или непараллельными плоскостями Для скрепления деталей в них проделываются соответствующей формы отверстия, затем отверстия совмещают и вставляют клин. Если у клина параллельные плоскости, то он вставляется и вынимается свободно и соединение называется ненапряженным. В напряженных клиновых соединениях боковые стороны клина непараллельны, клин вставляют в пазы скрепляемых деталей и заколачивают. Благодаря малому углу между боковыми сторонами клин надежно удерживается в пазах деталей силой трения.
Штифтовые соединения. Штифт — крепежная деталь цилиндрической или конической формы с головками или без них. Для соединения в деталях просверливаются сквозные отверстия (например, на валу и в детали), отверстия совмещают и в них вставляют штифт. Штифтовые соединения бывают напряженными и ненапряженными. Иногда конец штифта снабжается пропилом и разводится после монтажа, а при необходимости демонтажа усики пропила сводятся и штифт легко удаляется. Конические штифты бывают с резьбой на конце или без нее. Штифты устанавливаются перпендикулярно оси вала
Шпоночные соединения. В торговом машиностроении шпоночные соединения применяются достаточно широко: для крепления к валам и передачи вращения шкивам, колесам, звездочкам и другим деталям, а также для жесткой фиксации деталей друг с другом, например в мясорубке для фиксации ножевых решеток внутри корпуса. Шпонка — клиновая деталь с параллельными или непараллельными гранями, в отличие от штифтов устанавливается параллельно оси вала.
По форме различают шпонки: обыкновенные призматические, призматические с плоскими торцами, направляющие и сегментные. Вышеперечисленные шпонки передают вращающий момент боковыми гранями и являются ненапряженными соединениями.
Напряженные соединения получают с помощью клиновых шпонок, которые забивают в шпоночное гнездо. Такие шпонки бывают с головками и без них, с закругленными или плоскими торцами. Клиновые шпоночные соединения обеспечивают передачу не только вращающего момента, но и осевых усилий. Однако они вызывают перекос и радиальное смещение вала, что ограничивает область их применения.
Шлицевые соединения иначе называют многошпоночными, так как у них несколько шпонок и они выполнены вместе с валом В зависимости от форм зуба шлицевые соединения бывают треугольные, трапецеидальные, прямоугольные, эвольвентные. Шлицевые соединения имеют некоторые преимущества по сравнению со шпоночными, так как они меньше ослабляют вал, могут передавать большие мощности и скорости, обеспечивают осевое перемещение деталей вдоль вала, а также лучшее центрирование соединяемых деталей; но они более дорогостоящие. Шлицевые соединения стандартизированы.
Профильные соединения свое название получили в связи с тем, что соединяемые с валом детали имеют отверстия, по форме соответствующие профилю конца вала (квадратные, треугольные и т. д.). Таким образом крепятся ножи мясорубок на валу, рукоятки на конце вала, вал сменного механизма с валом универсального привода и т. п. Преимущества и недостатки профильных соединений аналогичны шлицевым соединениям
Тема 1.2 Детали передач
Детали передач, как отмечалось, служат для передачи движения, изменения скорости, мощности и направления движения. К ним относятся: оси и валы; опоры осей и валов; муфты; передачи; передаточные механизмы; редукторы.
Оси и валы
Оси и валы поддерживают в пространстве вращающиеся детали и части машин. При этом оси только поддерживают вращающиеся части в пространстве, а валы не только поддерживают, но и придают им вращательное движение.
Оси проще по конструкции, могут быть неподвижными, подвижными, вращающимися вместе с деталями. Валы по конструкции, соответственно, сложнее и при работе всегда вращаются. Оси чаще имеют цилиндрическую форму. Валы же бывают прямые, коленчатые и, реже, гибкие. Прямые валы цилиндрической формы, в поперечнике имеют круглое, реже, кольцевое сечение. Различные части валов имеют разный диаметр и назначение. Опорными частями валов являются шип (при горизонтальном) и пята (при вертикальном) расположении вала Для закрепления деталей валы имеют шпоночные канавки, отверстия, протоки, заплечики, резьбовые участки, шлицы и т. п. Иногда вместе с валом изготавливаются червячные и зубчатые колеса.
Валы коленчатые бывают с одним или несколькими коленами Гибкие валы изготавливаются из стального проволочного сердечника и предохранительного рукава, внутри которого в пространстве, заполненном смазкой, вращается сердечник.
Опоры осей и валов
Опорные части валов и осей в зависимости от расположения называются шип и пята. Опорами для них являются соответственно подшипники и подпятники. Наиболее часто используются подшипники, которые по характеру силы трения подразделяются на подпипники трения скольжения и подшипники трения качения.
Подшипники скольжения представляют собой два диска: один внутри другого. На внутренний диск, который называется вкладыш, укрепляется вал, а наружный диск закрепляется внутри корпуса (станины). Подшипники данного типа подразделяются на глухие — неразъемные и разъемные Глухие подшипники не могут передавать большие мощности и не выдерживают больших скоростей.
Разъемные подшипники используют при больших скоростях и нагрузках в валах. Они состоят из корпуса /, крепящегося к станине, разъемного (состоящего из двух полуколец) вкладыша, крышки и болтов для стягивания крышки и корпуса. Для уменьшения силы трения используют масленки, из которых на вал периодически поступает смазка. Подпятники (г) устанавливаются под вертикальными валами.
|
а б в г д |
Подшипники качения более сложные по конструкции, чем подшипники скольжения. Они состоят из двух колец, между которыми находится тело качения: ролики, шарики или иглы (рис. 1).
Рис. 1. Подшипники качения
Для равномерного распределения тел качения по окружности их располагают внутри сепараторов. Шарикоподшипники (а, б), роликоподшипники {в, г) и иглоподшипники (д) в отличие от подшипников скольжения имеют меньше потерь на трение и нагрев, меньшие габариты, но боятся загрязнений и требуют смазки.
Муфты
Муфты применяются для соединения валов друг с другом или валов с деталями и передачи вращающего момента. Существует большое разнообразие конструкций муфт. В торговом машиностроении применяются втулочные, дисковые (фланцевые), упругие втулочно-пальцевые и сцепные муфты различных видов.
Самая простая по конструкции втулочная муфта представляет собой втулку, которая насаживается на концы валов и крепится к ним различными способами: шпонками, штифтами, винтами или с помощью шлицев.
Фланцевые муфты состоят из двух дисков (полумуфт), которые насаживаются на концы валов и крепятся к ним с помощью шпонок. Полумуфты стягиваются друг к другу болтами.
Для предотвращения деформации валов и компенсации небольших смещений соединяемых валов, смягчения ударных нагрузок,
Рис. 2 .. Муфты
например у вибрационных машин, применяют компенсирующие муфты. Однако наибольшее распространение среди них получили упругие втулочно-палъцевые муфты (б), которые, как и фланцевые, крепятся на валах. Вместо болтов расположены пальцы, на концы которых надеты резиновые втулки. Такие муфты более бесшумные.
Часто в машинах необходимо без остановки соединять или отсоединять валы друг от друга. Для этой цели применяет сцепные муфты различных видов. Наибольшее распространение получила кулачковая муфта {в, г), состоящая из двух полумуфт, имеющих на поверхности кулачки прямоугольного или трапецеидального профиля. Одна полумуфта жестко крепится с помощью шпонки на ведущем валу, а другая полумуфта — с помощью направляющей шпонки на ведомом валу и может перемещаться вдоль него посредством отводки.
Обгонные муфты позволяют передавать вращающий момент с ведущего вала на ведомый только в одном направлении и вращаться ведомому валу с большей скоростью, чем ведущий.
Передачами называются механизмы, передающие движение (механическую энергию) от ведущего вала к ведомому, при необходимости изменяя скорость вращения и направление движения. Передачи характеризуются передаточным числом, которое можно определить как отношение скоростей вращения валов, диаметров колес (валов) или числа зубьев колес (звездочек) по одной из следующих формул:
Как правило, передаточное число имеет постоянное значение.
Передачи, где возможно плавное регулирование скоростей на ходу, называются вариаторами.
Различают следующие виды передачи: с гибкой и жесткой связью; трением и зацеплением. К передачам с гибкой связью относятся ременные и цепные, с жесткой связью — фрикционные, зубчатые, червячные; к передачам трением — фрикционные и ременные, к передачам зацеплением — зубчатые, червячные и цепные.
Ременные передачи состоят из двух шкивов и надетого на них •бесконечного ремня. Передача движения происходит за счет силы трения, которая возникает между поверхностями ремня и шкива.
По виду ремня различают плоскоременные, клиноременные, поликлиновые и круглоременные передачи. В подавляющем большинстве ременные передачи передают движение параллельным валам. Натяжение ремня можно регулировать увеличением расстояния между шкивами или с помощью натяжного ролика.
Преимущества ременных передач — простота изготовления, бесшумность и плавность хода, возможность передавать движение на большое расстояние, самопредохранения (при перегрузках — пробуксовывание ремня), а также возможность одним ремнем привести в действие несколько валов
Недостатками являются: невозможность передачи больших мощностей, непостоянство передаточного числа (при пробуксовывании, пониженный КПД (92—95 %), растяжение (провисание) ремня, соскальзывание ремня со шкива.
Цепные передачи состоят из двух зубчатых колес (звездочек), на которые надета гибкая бесконечная цепь Передача движения осуществляется за счет зацепления зубьев звездочки со звеньями шарнирной цепи.
Цепная передача вращает только параллельные валы. Цепь бывает двух видов: роликовая и зубчатая Наиболее распространена роликовая цепь. Преимущества цепной передачи — возможность передавать движение на большое расстояние, одной цепью приводить в действие несколько валов (г), при необходимости вращать их в разные стороны, достаточно высокий КПД (97—98 %). Недостатки — сложность изготовления, большой шум при работе по сравнению с ременной передачей, растяжение цепи из-за износа шарниров и поэтому необходимость периодического натяжения цепи, а также необходимость смазки.
Зубчатые передачи состоят из двух зубчатых колес, зубья которых входят в зацепление друг с другом; при вращении зубья ведущего толкают зубья ведомого колеса.
Различают зубчатые передачи с внешним зацеплением, в которых зубья расположены снаружи колеса, что позволяет изменять направление движения на противоположное, и с внутренним зацеплением, сохраняющим направление движения. По форме зубьев передачи бывают прямозубые), у которых зубья расположены параллельно оси колеса, косозубые, у которых зубья расположены под углом к оси колес; шевронные, у которых зуб имеет форму угла; круговые; винтовые).
Шевронные зубья имеют наибольший КПД, но они более сложны в изготовлении; используются в основном при передаче очень больших мощностей.
Разновидностью зубчатой передачи является зацепление типа рейка—шестерня (к) — реечная передача, которая может превращать один вид движения в другой в зависимости от того, какая деталь является ведущей. Если шестерня ведущая и совершает вращательное движение, то рейка совершает поступательное движение. Если шестерня совершает реверсивное вращение, то рейка — возвратно-поступательное, и наоборот. Если ведущей является рейка, совершающая возвратно-поступательное движение, то шестерня будет совершать реверсивное движение.
Преимущества зубчатых передач — самый высокий КПД из всех передач (до 99 % при хорошей смазке), компактность, долговечность, надежность, возможность передавать движение в разных направлениях. Недостатки — сложность в изготовлении, шум при работе, невозможность плавного изменения скорости движения, необходимость смазки.
Червячные передачи состоят из червяка и червячного колеса. Червяк имеет форму винта и является только ведущим, зубья червячного колеса входят во впадины резьбы червяка. Червячная передача позволяет передавать вращательное движение валам со скрещивающимися осями (чаще под прямым углом).
Преимущества данного типа передач — большое передаточное число (100 и более), что позволяет выиграть в силе, компактность, плавность, возможность самоторможения. Недостатки — сложность и трудоемкость в изготовлении, невысокий КПД (до 70 %; а у самотормозящихся — менее 50 %), повышенный нагрев, необходимость смазки.
Фрикционные передачи состоят из двух колес (катков), прижатых друг к другу и передающих движение за счет силы трения Цилиндрические катки передают движение параллельным валам, а конические — пересекающимся.
Преимущества — просты по конструкции, бесшумны, самопредохраняющиеся. Недостатки — малый КПД (до 80—90 %), непостоянство передаточного числа, быстрый износ катков, необходимость в постоянном прижатии катков, поэтому практически в торговом машиностроении не применяются Передаточные механизмы
К передаточным относятся планетарный и кривошипно-шатунный механизмы. Эти механизмы в отличие от вышеперечисленных передач позволяют осуществлять сложное движение.
В планетарном механизме вращательное движение превращается в планетарное, при котором деталь вращается вокруг своей оси и одновременно вокруг другой оси (так движутся планеты в пространстве — отсюда и название механизма).
Планетарный механизм состоит из двух зубчатых колес: ведущего /, которое называется солнечным, и ведомого, которое называется сателлитом (их может быть несколько). Необходимым условием работы данного механизма является жесткое соединение этих колес с помощью рычага — водила, который придает движение сателлиту и неподвижность солнечному колесу. Планетарный механизм может быть выполнен на базе двух передач: зубчатой с наружным или внутренним зацеплением или цепной ). На базе цепной передачи можно передавать планетарное движение на большее расстояние, чем на базе зубчатой.
Кривошипно-шатунный (кривошипно-ползунный, кривошип-но-кулисный) механизм служит для превращения вращательного движения в возвратно-поступательное). Механизм состоит из ведущего органа кривошипа /, который на валу совершает вращательное движение, и шатуна, ползуна или кулисы, которые совершают возвратно-поступательное движение. Шатун соединятся с помощью пальца с рабочим органом — поршнем.
Редукторы
Редукторы, как и передачи, служат для изменения скорости и направления движения. Редуктор — одна или несколько передач, заключенных в один общий корпус, называемый картером. Наличие картера позволяет компактно расположить детали передач, защищает детали от механических повреждений и загрязнений, обеспечивает необходимую смазку. В картере находятся три отверстия с пробкой: верхнее — для заливки масла, нижнее — для слива отработанного масла, среднее — для контроля за уровнем масла. В зависимости от числа ступеней передач различают редукторы одноступенчатые, двухступенчатые, трехступенчатые и т. д. Ступенями являются зубчатые или червячные передачи, планетарные и кривошипно-шатунные механизмы, реже — цепные передачи. Валы редукторов называются входными, промежуточными и выходными.
Виды редукторов: зубчатый цилиндрический одноступенчатый, зубчатый цилиндрический двухступенчатый, одноступенчатый зубчатый конический, зубчатый конический цилиндрический двухступенчатый и червячный одноступенчатый. Редукторы, у которых входной и выходной валы лежат в одной плоскости, называются соосными.
Редуктор или его часть, позволяющие ступенчато изменять передаточное число, называются коробкой скоростей, а те, в которых происходит плавное бесступенчатое изменение передаточного числа, — вариатором скоростей.
Коробка скоростей выполняется на базе зубчатых передач, и для перекдючения скорости двигатель надо отключать; вариатор скоростей — на базе клиноременной передачи, и скорость регулируется на ходу без выключения двигателя.
Тема 1.3 Электроустановки
Электроустановки обеспечивают подачу электрического тока к приемникам, приводят машины в действие, включают или отключают их от электросети, регулируют режим работы, осуществляют их защиту и обеспечивают дистанционное управление ими. К электроустановкам относятся электроприводы, аппараты ручного и дистанционного управления, аппараты защиты.
Электроприводы
Электропривод служит для приведения машины в действие и состоит из электродвигателя, передаточных механизмов и аппаратуры управления. Электродвигатель превращает электрический ток в механическую энергию, т. е. позволяет получить вращательное движение. В торговом машиностроении чаще всего используются электродвигатели трехфазного тока с короткозамкнутым ротором, реже — двигатели однофазного тока.
Трехфазные двигатели выпускаются на напряжение 220—380 В, подсоединяются в электросеть в звезду или треугольник в зависимости от напряжения.
Однофазные двигатели выпускаются на напряжение 220 В. При включении в трехфазную сеть напряжением 3N~220 В их подключают к двум линейным проводам, в трехфазную сеть напряжением 3N~380 В — к линейному и нулевому проводам.
Трехфазные и однофазные двигатели предназначены для промышленной частоты 50 Гц и имеют частоту вращения вала не более 3000 об/мин.
В машинах, требующих изменения частоты вращения во время работы, применяют многоскоростные электродвигатели или редукторы с коробкой скоростей (например, во взбивальных машинах).
По числу электродвигателей различают одиночные и многодвигательные приводы.
При одиночном приводе рабочая машина приводится в движение от одного электродвигателя (мясорубка, вентилятор, насос). Для передачи движения от двигателя к машине используют
зубчатый редуктор. При непосредственной передаче движения от двигателя к машине (насос, вентилятор) скорость двигателя должна соответствовать скорости машины. Для удобства обслуживания машины и уменьшения ее габаритов двигатель, как правило, устанавливают внутри машины (картофелечистки, мясорубки).
При многодвигателъном приводе рабочая машина приводится в движение несколькими двигателями, например машина для мытья столовой посуды ММУ-2000. Однако механизм этой машины можно привести в движение и от одного двигателя, но для этого потребуется сложное передаточное устройство.
По числу приводимых в действие машин различают индивидуальные и универсальные электроприводы. Индивидуальный электропривод служит для приведения в действие одной машины (картофелечистка, мясорубка и др.). Универсальный электропривод поочередно приводит в действие несколько сменных механизмов, входящих к нему в комплект.
Аппараты ручного управления
Аппараты ручного управления служат для включения в сеть и отключения от сети приемников электроэнергии, а также для регулирования режимов их работы. Принцип действия аппаратов включения основан на замыкании или размыкании электрической цепи с помощью подвижных и неподвижных контактов. При замыкании подвижных контактов с неподвижными происходит подача электрического тока от источника к приемнику, а при размыкании этих контактов приемник обесточивается. Перемещение подвижных контактов производится механическим воздействием, поэтому большая их часть находится на самом оборудовании. К аппаратам ручного управления относятся: рубильники, кулачковые теплостойкие переключатели для кухонных плит, штепсельные разъемы, пакетные выключатели и переключатели, кнопочные пускатели.
Корпус аппаратов ручного управления выполняются из диэлектрика и имеют маркировку, где указаны номинальные сила тока и напряжение. Провода от электросети подключаются к клеммам неподвижных контактов, а от клемм подвижных контактов — к приемнику энергии.
Рубильники служат для включения и отключения различных приемников электроэнер
|
|
Автоматическое растормаживание колес: Тормозные устройства колес предназначены для уменьшения длины пробега и улучшения маневрирования ВС при...
Биохимия спиртового брожения: Основу технологии получения пива составляет спиртовое брожение, - при котором сахар превращается...
Особенности сооружения опор в сложных условиях: Сооружение ВЛ в районах с суровыми климатическими и тяжелыми геологическими условиями...
Архитектура электронного правительства: Единая архитектура – это методологический подход при создании системы управления государства, который строится...
© cyberpedia.su 2017-2024 - Не является автором материалов. Исключительное право сохранено за автором текста.
Если вы не хотите, чтобы данный материал был у нас на сайте, перейдите по ссылке: Нарушение авторских прав. Мы поможем в написании вашей работы!