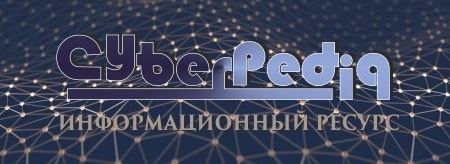
Археология об основании Рима: Новые раскопки проясняют и такой острый дискуссионный вопрос, как дата самого возникновения Рима...
Эмиссия газов от очистных сооружений канализации: В последние годы внимание мирового сообщества сосредоточено на экологических проблемах...
Топ:
Процедура выполнения команд. Рабочий цикл процессора: Функционирование процессора в основном состоит из повторяющихся рабочих циклов, каждый из которых соответствует...
Теоретическая значимость работы: Описание теоретической значимости (ценности) результатов исследования должно присутствовать во введении...
Интересное:
Инженерная защита территорий, зданий и сооружений от опасных геологических процессов: Изучение оползневых явлений, оценка устойчивости склонов и проектирование противооползневых сооружений — актуальнейшие задачи, стоящие перед отечественными...
Искусственное повышение поверхности территории: Варианты искусственного повышения поверхности территории необходимо выбирать на основе анализа следующих характеристик защищаемой территории...
Берегоукрепление оползневых склонов: На прибрежных склонах основной причиной развития оползневых процессов является подмыв водами рек естественных склонов...
Дисциплины:
![]() |
![]() |
5.00
из
|
Заказать работу |
Новосибирск 2020
Кафедра надежности и ремонта машин
УДК 631.372, 621.43
ББК 39.33
Рецензент: канд. техн. наук, доцент А.А. Малышко
Составитель: ст. преподаватель М.Л. Вертей
Технология ремонта машин. Восстановление деталей сваркой, наплавкой в среде защитного газа СО2: метод. указания по вып. лабор.-практ. работы / Новосиб. гос. аграр. ун-т. Инженер. ин-т; сост. М.Л. Вертей. – Новосибирск, 2020. – 16 с.
В методических указаниях представлены основные термины и определения. Представлена сущность процесса сварки и наплавки с среде защитного газа СО2. Описан технологический процесс наплавки цилиндрических поверхностей.
Методические указания предназначены для студентов очной формы обучения по направлениям: Агроинженерия; Эксплуатация транспортно-технологических машин и комплексов; Технология транспортных процессов.
Утверждены и рекомендованы к изданию учебно-методическим советом Инженерного института НГАУ (протокол №6 от 31.01.2020 г.)
© Новосибирский государственный аграрный университет, 2010
© Инженерный институт, 2010
Лабораторно-практическая работа
Сварка и наплавка в среде углекислого газа.
Цель работы: Изучить принципы сварки и наплавки в среде диоксида углерода; ознакомиться с применяемым оборудованием и материалами для наплавки; приобрести практические навыки восстановления деталей сваркой и наплавкой в среде диоксида углерода (углекислого газа).
Оборудование и инструмент:
- Углошлифовальная машинка интерскол 125/900;
- Аппарат МIG сварки «Аврора Динамика 200»;
- Стол сварочный;
- Линейка;
- Твердомер;
- Средства индивидуальной защиты;
Материалы:
- Лепестковый шлифовальный круг Р400;
- Пластины малоуглеродистой стали толщиной 3,0 -5,0 мм;
Задание к лабораторно-практической работе:
Ознакомиться с содержанием методических рекомендаций
1. Изучить технику безопасности при выполнении сварочных работ.
2. Ознакомиться с устройством и принципом сварочного аппарата фирмы Аврора модели «Динамика 200».
3. Исследовать влияние режимов наплавки на свойства наплавленного слоя.
4. Разработать технологию восстановления заданной детали.
5. Сдать рабочее место учебному мастеру (преподавателю).
6. Составить отчет о работе и сдать преподавателю.
Организация проведения
лабораторно-практической работы*
40 минут – работа с подгруппой. Вводная информация преподавателя: постановка задачи, ознакомление с общими вопросами по подготовке поверхности, инструменты и материалы, которыми она проводится.
Правила техники безопасности при использовании сварочного аппарата и инструмента для сварки и наплавки.
10 минут. Подготовка рабочего места. Подготовка деталей для наплавки поверхности.
10 минут. Получение навыка по настройке сварочного аппарата
60 минут. Получение навыков сварки и наплавки в среде углекислого газа.
20 минут. Разработка технологического процесса восстановления детали наплавкой в среде углекислого газа.
20 минут. Ответить на контрольные вопросы. Оформить отчет и защитить у преподавателя.
Основные термины и определения
Сварка – процесс получения неразъемного соединения деталей посредством установления межатомных связей при их нагревании и (или) пластическом деформировании.
Наплавка – процесс нанесения посредством сварки слоя металла на поверхность детали.
Общие сведения
Схема наплавки цилиндрических деталей плавящимся электродом показана на рисунке 1.
Рисунок 1. Схема наплавки цилиндрических деталей:
1 - плавящийся электрод; 2 - мундштук; 3 - корпус горелки; 4 - зона горения дуги; 5 - сварочная ванна; 6 - наплавленный металл; 7 - деталь; Н- вылет электрода; Vэ- скорость подачи электродной проволоки; Vн- скорость наплавки; а- смешение электрода с зенита; п - частота вращения детали.
Через мундштук 2 подается плавящийся электрод 1. В зону горения дуги 4 через корпус горелки 3 поступает диоксид углерода. Между кончиком плавящегося электрода 1 и деталью 7 возбуждается электрическая дуга. В качестве плавящегося электрода используют наплавочную проволоку или ленту. Дуга горит между деталью и электродом, расплавляя последний. Под действием гравитационной силы расплавленный металл переносится на поверхность детали и образует сварочную ванну 5, после остывания которой формируется слой наплавленного металла 6.
При наплавке в среде диоксида углерода защита расплавленного металла осуществляется в процессе ряда химических реакций.
Под действием высокой температуры происходит диссоциация диоксида углерода
2СО2 <=> 2СО + О2,
и окисление железа (в скобках: ж - жидкое состояние; г - газообразное состояние)
Fе (ж) + О(г) = FеО(ж).
Нейтрализация (связывание) кислорода происходит в результате взаимодействия химических элементов, входящих в состав стали:
С(ж) + О(г) = СО(г);
Si (ж) + 2О(г) = Si02(ж);
Мn (ж) + О(г) = МnО(ж).
Для восстановления железа из оксидов необходимо повышенное содержание мощных раскислителей, в первую очередь кремния и марганца:
FеО (ж) + С(ж) = Fe(x) + СО(г);
2FеО(ж) + Si(ж) = 2Fе(ж) + SiO2(ж);
FеО (ж) + Мn(ж) = Fе(ж) + МnО(ж).
Оксиды кремния и марганца, обладая меньшей массой, чем железо, всплывают на поверхность жидкого металла и после охлаждения образуют тончайшую шлаковую корку.
Нейтрализация (связывание) действия водорода и азота протекает по следующим химическим реакциям:
СO2(г) + 2H <=> СО(г) + Н2O(г);
2СO2(г) + N2<=> 2СО(г) + 2NO(г).
Преимущества
· Эффективное использование тепла сварочной дуги обеспечивает высокую производительность процесса, достигающую 18 кг наплавленного металла в 1 ч.
· Производительность сварки в среде диоксида углерода в 2,5...4 раза выше, чем производительность ручной сварки штучным электродом, и в 1,5 раза — чем при сварке под слоем флюса.
· Уменьшение зоны термического влияния (ЗТВ) обеспечивает высокое качество сварочных швов, возможность восстановления деталей малого диаметра (начиная с 10... 12 мм), а также сварки металла небольшой толщины.
Недостатки
· Большие потери электродного материала (8... 12 %).
· Снижение (на 10...50%) усталостной прочности восстанавливаемых деталей.
Область применения
Сварку и наплавку в среде диоксида углерода плавящимся электродом широко применяют в ремонтном производстве (для устранения трещин, приварки усилителей, сварки и приварки тонколистовых деталей, особенно при ремонте рам, кабин, элементов оперения и т. д.), что обусловлено рядом преимуществ перед наплавкой под слоем флюса и ручной сваркой штучным электродом.
Оборудование
Сварку плавящимся электродом в среде диоксида углерода проводят с помощью шланговых полуавтоматов Динамика 200, ПДА-300, ПДГ-312-4 и др. (рисунок 2).
Газовый баллон 1 предназначен для хранения диоксида углерода. В стандартный баллон вместимостью 40 л вмещается 25 кг жидкого СО2, после испарения которой образуется около 12,5 м3газа. Баллоны окрашивают в черный цвет и маркируют надписью желтого цвета — «диоксид углерода».
При испарении диоксида углерода поглощается большое количество теплоты. Поэтому влага, которая может содержаться в баллоне, приводит к обмерзанию понижающего газового редуктора 4 и выходу его из строя. Для предотвращения этого применяют электрический подогреватель газа 2 и осушитель газа 3.
Рисунок 2. Схема установки для сварки (наплавки) в среде диоксида углерода: 1 - баллон с диоксидом углерода; 2 - электрический подогреватель газа; 3 - осушитель газа; 4 - газовый редуктор; 5 - ротаметр (расходомер газа); 6, 7 - электромагнитный газовый клапан; 8 - аппаратный ящик; 9 - механизм подачи проволоки с катушкой; 10 - сварочная горелка; 11 - восстанавливаемая деталь; 12 - источник сварочного тока
Газ, проходя по змеевику подогревателя, нагревается с помощью электрического нагревательного элемента и попадает в осушитель, где при взаимодействии с поглотителем влаги обезвоживается. В качестве поглотителя влаги используют силикагель или медный купорос. Осушитель периодически разбирают, и работоспособность поглотителя влаги восстанавливают путем его прокаливания.
Давление газа понижается, а расход регулируется с помощью газового редуктора 4. Расход газа контролируют ротаметром (расходомером) 5. Перед началом сварочного цикла газовую магистраль продувают для удаления из нее воздуха. Для этого заблаговременно открывают электромагнитный клапан 6, 7. После окончания цикла сварки клапан закрывается с некоторым запаздыванием, обеспечивая защиту сварочной ванны до ее охлаждения. После открытия электромагнитного клапана газ по шлангу через сварочную горелку 10 поступает в зону горения дуги.
Механизм подачи наплавочного материала 9 состоит из кассеты со сварочной проволокой, редуктора с подающими роликами, приводимого электрическим двигателем. Скорость подачи проволоки может изменяться как ступенчато за счет изменения передаточного числа шестерен в редукторе, так и бесступенчато за счет изменения частоты вращения двигателя.
В качестве источников сварочного тока 12 можно применять сварочные преобразователи ПСГ-300, ПСУ-500 или сварочные выпрямители ВДГ-502, ВСЖ-303 с жесткой внешней характеристикой.
Для наплавки можно применять универсальные вращатели (ТОМ-12м) в сочетании со шланговыми сварочными полуавтоматами или изношенные токарные станки. (рис. 2.18). Вращатель позволяет наплавлять детали диаметром от 20 до 350 мм, длиной 50...400 мм и массой до 50 кг. Частота вращения детали двухступенчатая: 5...10 и 12,5...250 мин-1. Скорость продольного перемещения горелки: 2...26 и 24...290 мм/мин. В наплавочной установке используют сварочный полуавтомат ПДГ-312-4. Источник питания дуги — сварочный выпрямитель ВДГ-502, регулирующий сварочный ток в пределах 60...500 А при напряжении на дуге 16...40 В.
Материалы
Для сварки и наплавки применяют проволоки (диаметром 5...3 мм), ленты сплошного сечения, а также порошковые проволоки. Кроме того, используют сварочные (Св-08Г2, Св-18ХГН и др.) и наплавочные (Нп-30ХГСА, Нп-50ХГНТ и др.) легированные и высоколегированные проволоки с содержанием кремния и марганца не менее 1 %.
Режимы сварки
В зависимости от типа соединения, толщины свариваемых деталей выбирают диаметр электрода, силу сварочного тока и другие режимы сварки (таблица 1). Сварку проводят на постоянном токе, как правило, обратной полярности (деталь «-», электрод «+»).
Процесс сварки начинается с включения подачи газа, после небольшой задержки включается подача электрода и включается сварочный ток. Легким касанием кончика электрода детали возбуждается электрическая дуга, и начинается процесс сварки.
При сварке в нижнем положении электроду сообщают поступательное движение вдоль оси шва, возвратно-поступательное, по спирали или змейкой. Электрод перемещают слева направо «углом назад» или справа налево «углом вперед».
Таблица 1. Режимы сварки углеродистых сталей в диоксиде углерода
Вертикальные швы при толщине металла до 4 мм сваривают сверху вниз без колебаний электрода. При толщине металла более 4 мм сварку проводят снизу вверх с поперечными колебаниями электрода.
Заканчивая сварку, кратер необходимо заполнить металлом, отключить подачу электродного материала и выключить электроток, не отводя горелку и не прекращая подачу газа до остывания металла.
Режимы сварки и наплавки влияют на интенсивность металлургических процессов и состав металла шва. Ток в сварочной цепи определяется напряжением на дуге, скоростью подачи и сечением электрода. С повышением напряжения и уменьшением силы тока потери углерода, марганца и кремния растут. Увеличение силы тока значительно влияет на глубину проплавления. Расход газа влияет на коэффициент расплавления, химический состав шва и наличие пор.
При повышении скорости наплавки уменьшаются потери металла на угар, уменьшается глубина проплавления и несколько улучшаются прочностные свойства наплавленного металла. Рекомендуемые режимы наплавки приведены в таблице 2.7.
Шаг наплавки выбирают с учетом ширины и перекрытия валиков для достижения минимальной волнистости наплавленного металла.
Электрод с зенита смещают в сторону, противоположную направлению вращения детали, что необходимо для достижения оптимальных условий формирования шва.
Порядок проведения работ
Типы сооружений для обработки осадков: Септиками называются сооружения, в которых одновременно происходят осветление сточной жидкости...
Индивидуальные очистные сооружения: К классу индивидуальных очистных сооружений относят сооружения, пропускная способность которых...
Адаптации растений и животных к жизни в горах: Большое значение для жизни организмов в горах имеют степень расчленения, крутизна и экспозиционные различия склонов...
Особенности сооружения опор в сложных условиях: Сооружение ВЛ в районах с суровыми климатическими и тяжелыми геологическими условиями...
© cyberpedia.su 2017-2024 - Не является автором материалов. Исключительное право сохранено за автором текста.
Если вы не хотите, чтобы данный материал был у нас на сайте, перейдите по ссылке: Нарушение авторских прав. Мы поможем в написании вашей работы!