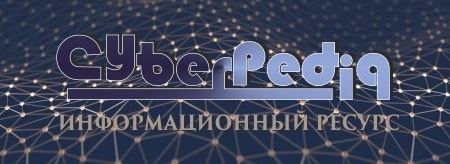
Типы оградительных сооружений в морском порту: По расположению оградительных сооружений в плане различают волноломы, обе оконечности...
Общие условия выбора системы дренажа: Система дренажа выбирается в зависимости от характера защищаемого...
Топ:
Комплексной системы оценки состояния охраны труда на производственном объекте (КСОТ-П): Цели и задачи Комплексной системы оценки состояния охраны труда и определению факторов рисков по охране труда...
Основы обеспечения единства измерений: Обеспечение единства измерений - деятельность метрологических служб, направленная на достижение...
Генеалогическое древо Султанов Османской империи: Османские правители, вначале, будучи еще бейлербеями Анатолии, женились на дочерях византийских императоров...
Интересное:
Искусственное повышение поверхности территории: Варианты искусственного повышения поверхности территории необходимо выбирать на основе анализа следующих характеристик защищаемой территории...
Финансовый рынок и его значение в управлении денежными потоками на современном этапе: любому предприятию для расширения производства и увеличения прибыли нужны...
Средства для ингаляционного наркоза: Наркоз наступает в результате вдыхания (ингаляции) средств, которое осуществляют или с помощью маски...
Дисциплины:
![]() |
![]() |
5.00
из
|
Заказать работу |
|
|
Смятие цилиндра, нагруженного внешним давлением, может произойти
в результате нарушения прочности цилиндра или потери устойчивости формы.
Нарушение прочности цилиндра происходит, когда расчетные напряжения в стенке достигают предела текучести металла стенки. Это характерно для цилиндров с достаточной толщиной стенки, у которых отношение толщины стенки к диаметру больше определённой заданной величины (например,
при S ' / D > 0,04).
Явление потери устойчивости формы происходит при расчетных напряжениях меньше предела текучести металла стенки, но когда внешнее давление достигает определенной критической величины. Величина критического давления зависит от геометрической формы, размеров аппарата, механических свойств материала его стенок. Явление потери устойчивости формы цилиндра аналогично явлению потери устойчивости при продольном изгибе стержней. Цилиндр идеальной формы, выполненный из однородного материала, теряет форму, если внешнее давление достигает критического значения. Первоначальные отклонения от цилиндрической формы, являющиеся следствием неточности изготовления, могут оказать влияние на прочность и устойчивость формы аппарата. Это необходимо учитывать при выборе коэффициентов запаса прочности и устойчивости.
Предельное состояние обечайки под внешним давлением зависит также от способа и конструкции закрепления ее концов, что проявляется в большей степени для сравнительно коротких обечаек с небольшим отношением длины к диаметру L / Dk, поэтому при расчете рассматривают два случая:
1. Гладкие обечайки при .
Допускаемое давление из условия устойчивости формы
. (12)
|
Формула (12) применима для обечаек с S ' / D В ≤ 1,1· при больших S ' / D В допускаемое давление определяют из условия прочности
по формуле:
, (13)
где n т – коэффициент запаса прочности по пределу текучести:
. (14)
2. Гладкие обечайки при . Критическое давление из условия устойчивости формы:
. (15)
Формула (15) применима для обечаек с при больших S ' / D В допускаемое давление определяют из условия прочности по формуле (13) при коэффициенте запаса прочности:
. (16)
При расчете допускаемого давления по формуле (12) коэффициент запаса устойчивости по отношению к критическому давлению принят равным 2,6, при расчете по формуле (15) равным 2,6–4,0; при расчете по формулам (13), (14) и (16) коэффициент запаса прочности n = 1,5–2,6.
Для укрепления цилиндров, работающих под внешним давлением р, применяют кольца жесткости (рис. 22). При расчете устойчивости цилиндра на участке длиной l между кольцами жесткости наряду с формулами (12) и (15) может быть использовано уравнение Мизеса, определяющее критическое давление:
, (17)
где R в – внутренний радиус цилиндра; n – число волн, образующихся в результате смятия цилиндра.
Рис. 22. Цилиндрическая оболочка под внешним давлением
При определении критического давления число волн подбирают так, чтобы величина р кр была минимальной. Например, для вакуумных колонн число волн, соответствующее минимальному значению р кр лежит обычно в пределах n = 6–20. Предварительно число волн находят по графику (рис. 23). Коэффициент запаса устойчивости при расчете с использованием (17) принимают равным .
Рис. 23. График для определения числа волн,
образующихся при смятии оболочки
Расчет аппаратов на устойчивость имеет смысл при условии, что напряжения сжатия в стенке аппарата от действия р кр = n [ p ] не превышают предел текучести при рабочей температуре, т. е.:
|
. (18)
Рассчитывая аппарат при повышенных температурах стенок, значения предела текучести и модуля упругости следует принимать при рабочей температуре.
Цилиндрический корпус закрытого аппарата работает под одновременным воздействием наружного давления р, осевой сжимающей силы Q (результата действия давления р на днища и весовых нагрузок) и изгибающего момента М (например, от ветровых сил); при этом устойчивость корпуса в поперечных сечениях проверяют по формуле:
, (19)
где q доп, М доп, р доп, – допускаемые значения осевой сжимающей силы [см. формулу (20)], изгибающего момента [см. формулы (21), (22)] и внешнего давления.
Допускаемая осевая сжимающая сила:
. (20)
Здесь коэффициент уменьшения допускаемого напряжения φс определяют по следующим зависимостям:
– при
;
– при
,
где k с – коэффициент, принимаемый по приведенным ниже данным:
Допускаемый изгибающий момент рассчитывают по формулам:
– при
; (21)
– при
, (22)
где φн, k н – коэффициенты. Значения k н принимают по указанным выше данным,
а φн определяют по формуле:
.
В формулах (19)–(22): D – внутренний диаметр обечайки; [σ] – нормативное допускаемое напряжение. При расчете опорной части прибавку yа коррозию С принимают равной нулю.
Лекция № 11
Тема: «Теплообменные аппараты»
В пищевой промышленности широко применяют аппараты для нагревания, охлаждения или выпаривания многих видов сырья, полуфабрикатов и продуктов.
Современные теплообменные аппараты должны обеспечивать передачу требуемого количества тепла от одной среды к другой с получением необходимых конечных температур и при возможности большой интенсивности теплообмена.
Для осуществления длительной работоспособности в процессе эксплуатации при обработке среды, загрязнённой или выделяющей отложения на стенках аппарата, необходимо производить периодические осмотры и очистку поверхностей.
Аппараты должны обладать достаточной прочностью и иметь возможно малые габаритные размеры. При конструировании необходимо находить оптимальные решения, учитывающие требования обеспечения возможности разборки рабочей части аппарата и герметичности системы каналов, возможно высоких коэффициентов теплопередачи за счёт повышения скорости движения рабочей среды при минимальных гидравлических потерях в аппарате. В пищевых и химических производствах до 70 % теплообменных аппаратов применяют для сред жидкость–жидкость и пар–жидкость при давлении до 1 МПа и температуре до 200 °С.
Для указанных условий разработаны и серийно изготовлены теплообменные аппараты общего назначения кожухотрубчатого и спирального типов.
|
В пищевой и смежных отраслях промышленности нашли широкое применение горизонтальные кожухотрубчатые теплообменники (рис. 24).
Рис. 24. Кожухотрубчатый теплообменник
К основным элементам теплообменников относятся трубные решетки, представляющие собой перегородки, которыми трубное пространство отделяется от межтрубного. В трубных решетках закрепляют трубки теплообменника.
На рис. 25 приведены варианты крепления трубных решеток. Конструкция узла соединения трубок с трубными решетками должна обеспечивать достаточную плотность и прочность соединения.
Рис. 25. Трубные решетки: а – приварная к корпусу; б – зажатая между фланцами;
в – присоединенная к фланцу кожуха на болтах
По одному из вариантов соединения концы трубок и отверстия в трубных решетках тщательно обрабатывают. После того как трубки вставляют в отверстия, концы трубок подвергают внутренней обкатке роликами вальцовки; в результате в стенках трубки создаются остаточные пластические, а в трубной решетке – упругие деформации. Благодаря этому после развальцовки материал трубной решетки плотно сжимает концы трубок. Для увеличения прочности соединения применяют развальцовку на конус или с канавками в отверстиях трубной решетки. Стальные трубки можно и приваривать. В этом случае достигается высокая прочность соединения, но при выходе трубки из строя ее замена исключена. В охлаждающих медных и латунных аппаратах трубки припаивают к трубной решетке. В некоторых случаях применяют сальниковое крепление трубок, обеспечивающее компенсацию температурных удлинений.
|
Основные способы соединения труб с трубными решетками схематически показаны на рис. 26.
Рис. 26. Варианты крепления труб в трубных решетках:
а, б – развальцовкой; в – сваркой; г – пайкой; д – склейкой
При проектировании теплообменной трубчатой аппаратуры
необходимо рассчитать толщину трубной решетки с учетом напряжений, возникающих вдоль оси трубок и корпуса, в местах крепления трубок в трубных решетках, а также в самих трубных решетках.
В пачке труб теплообменных устройств жесткой конструкции возникают напряжения под действием давления среды и вследствие наличия разности температур в аппарате.
Обозначим: D (рис. 27) – внутренний диаметр корпуса аппарата; d н и d в –
соответственно наружный и внутренний диаметры трубок; п – число трубок;
р k – давление среды в межтрубном пространстве; р т – давление среды в трубном пространстве.
Рис. 27. Схема к расчету теплообменника
Осевые усилия, вызванные действием давления среды в пучке труб
и стремящиеся оторвать трубки от трубных решеток:
Q ' = 0,285 (D 2 – nd н ) р k + 0,285 nde 2 p т. (23)
Часть Q ' к усилия Q ' воспринимается корпусом аппарата, а другая часть Q ' т – трубками, т. е.:
Q '= Q ' к + Q ' т . (24)
На основании закона Гука изменение длины трубок:
,
где L – длина трубок, равная длине корпуса; F т – площадь сечения трубок;
Е т– модуль упругости материала трубок.
Изменение длины корпуса:
,
где F к— площадь сечения обечайки корпуса; Е к – модуль упругости материала корпуса.
Так как ,то
.
Подставим в последнее равенство значение Q ' т из уравнения (24) и решим полученное равенство относительно Q ' к тогда
.
Аналогично находим
.
Соответственно осевые напряжения в корпусе аппарата и трубках:
Толщина трубной решетки зависит не только от требований кпрочности, но и от условий закрепления труб при развальцовке, сохранения формы решетки после вальцовки труб. Толщина у стальных трубных решеток s тиз условия завальцовки должна быть не менее 10 мм:
,
где – наружный диаметр трубок.
Толщина медной трубной решетки из условия завальцовки:
.
Согласно отраслевой нормали Министерства химического и нефтяного машиностроения для теплообменника со средней разностью температур труб и кожуха, равной или больше 15 °С, при давлении в трубном или межтрубном пространствах р т> 5 мн/м2или р к> 5 мн/м2, а также для теплообменников с диаметром кожуха более 1,5 м(при давлении р к> 1 мн/м2 ) толщину трубной решетки определяют по формуле:
где – толщина стенки кожуха в м;
– приведённое давление;
– допускаемое напряжение;
– половина длины пучка труб.
|
Лекция № 12
Тема: «Составление алгоритма расчёта аппарата,
на примере выпарного»
Произвести прочностной расчёт выпарного аппарата на рабочий режим, по данным теплового и конструктивного расчётов.
Исходные данные:
D = 2 a = 1 800 мм – внутренний диаметр кожуха;
a 1 = 870 мм – расстояние от оси кожуха до оси наиболее удаленной теплообменной трубы;
L = 2 l = 2 500 мм – длина теплообменных труб;
d т = 38 мм – наружный диаметр труб;
s т = 2,5 мм – толщина стенок труб;
i = 740 – число труб;
t р – шаг расположения отверстий в решетке;
d о = 39 мм – диаметр отверстий в решетке;
G = 8 700 кг – масса аппарата;
N = 10 000 – число теплосмен, которое может иметь место в течение всего срока службы аппарата;
р м = 1,18 МПа – расчетное давление в межтрубном пространстве;
р т = 0,5 МПа – расчетное давление в трубном пространстве;
Δ t = 25 °С – разность температур кожуха греющей камеры и трубок;
αт = αк = 1,2 · 10–6 1/град. – коэффициент линейного расширения материалов труб и кожуха;
Е р = Е р = Е р = 1,9 · 103 МПа – модули продольной упругости материалов решетки, труб и кожуха (углеродистая сталь при температуре до 100 °С);
[σ] = 134 МПа – допускаемое напряжение для углеродистой стали ВСт3 при температуре до 100 °С;
D Е = 100 мм – диаметр окружности, вписанной в максимальную беструбную площадь;
φ = 0,9 – коэффициент прочности сварных швов;
с = 1 мм и с = 4 мм – прибавка к толщине на компенсацию коррозии для стенки цилиндрической обечайки греющей камеры, а также конического днища и обечайки и крышки аппарата;
σт = 200 МПа.
Решение:
Рис. 28. Схема к расчету прочности выпарного аппарата
По формуле (11) определяем толщину стенки цилиндрической обечайки греющей камеры:
.
Предполагаем, что обечайка с жёстким фланцем, определим местное меридиональное напряжение у заделанного её края.
(Мпа).
Полученное местное напряжение превышает допустимое напряжение для данного материала: 221,9 МПа > 134 МПа.
Имеются сведения о возможности повышения значений допускаемых напряжений для местного напряжения в 1,3 раза. В данном примере можно принять [σт] 134 · 1,3 = 174 МПа, и при этом значении допускаемого напряжения толщина стенки обечайки греющей камеры является недостаточной.
Опуская определение местного окружного напряжения, которое по значению меньше меридионального, и применяя гипотезу наибольших касательных напряжений, устанавливаем, что σ1 = σэкв. Приравнивая σ1 к допускаемому напряжению и решая полученное равенство относительно толщины стенки и вводя в уравнение коэффициент прочности и прибавку к толщине стенки на коррозию, получаем
Толщину стенки цилиндрической обечайки аппарата определяем по той же формуле, но при другом значении прибавки к толщине стенки на коррозию:
Для аппарата используем эллиптическую крышку, толщину стенки которой находим по формуле:
Толщину стенки конического днища определяем по формуле:
Коническое днище целесообразно применить с торообразным переходом. Исполнительную толщину стенки тороидального перехода конической обечайки определяем по формуле
,
Производим расчёт трубной решётки. Определяем вспомогательные величины: коэффициенты влияния давления на трубную решётку.
,
.
Модуль упругости основания (системы труб):
.
Приведённое отношение жёсткости труб к жёсткости кожуха:
Относительная характеристика беструбного края:
Приведённое давление:
Коэффициент ослабления трубной решётки:
По данным [11] при φ0 = f (ηт) находим значение φ0 = 0,49 при ηт = 0,734.
Тогда коэффициенты:
,
Толщину трубной решётки определяем по формуле:
.
Толщину трубной решётки проверяем по формуле:
Осевое усилие в кожухе по формуле:
Осевое усилие в трубе может быть определено после нахождения коэффициента f 2 и z:
,
тогда
Осевое усилие в трубе:
Проверяем прочность трубы по формуле:
МПа.
Рассчитываем опоры (лапы).
По требованиям монтажа необходимо установить опоры с вылетом
b = 230 мм. В соответствии с условиями монтажа и эксплуатации аппарата принимаем число лап n = 4. Предварительно выбираем опору по ОСТ 26-665-79, имеющую размеры b = 230 мм; h = 360 мм; f max = 60 мм; G = 87 000 Н.
Определяем плечо нагрузки по формуле:
см.
Нагрузка на одну опору:
Н.
Нагрузка допустимая для данной опоры равна 6300 Н.
Определяем соотношение параметров аппарата и опоры:
,
.
Напряжение от действия внутреннего давления:
МПа.
Максимальное мембранное напряжение от основных нагрузок и реакции опоры определяем по формуле:
Н/м,
МПа,
МПа.
Максимальное напряжение при изгибе от реакции опоры определяют по формуле:
МПа.
Условие прочности по формуле:
.
Таким образом, условие выполнено и, следовательно, опора выбрана правильно.
Лекция № 13
Тема: «Опоры»
Важными конструктивными элементами емкостей и тепловой аппаратуры являются опоры, например лапы (рис. 29). Конструкция и размеры лап стандартизированы, их выбирают в соответствии с ОСТ 26-665–79.
Рис. 29. Схема опирания аппарат: а – на лапы; б – типы лап
Нагрузка на одну опору:
,
где G – сила тяжести аппарата, включая и находящуюся в нем среду; n – число лап, выбираемое по конструктивным соображениям; М – момент внешних
нагрузок, задаваемый перед расчетом, МН · м; λ1 и λ2 – коэффициенты, зависящие от числа лап; при n = 2 λ1 = λ2 = 1; при n = 3 λ1 = 1, λ2 = 1,3; при n = 4 λ1 = 2,
λ2 = 1; l 1 – плечо нагрузки Q относительно срединной поверхности корпуса:
где b – величина, показанная на рис. 29 б, м; f max – максимальный зазор между аппаратом и подпорной рамой, м (рис. 29 а); s 0 – толщина стенки аппарата в конце срока его службы.
В соответствии с РТМ 26-319–79 обязательным элементом проверки правильности выбора опор является определение максимальных значений мембранного напряжения σ т в стенке корпуса аппарата от действия основных нагрузок и реакции опоры и напряжения при изгибе от действия реакции опоры σи:
,
,
где σ т 0 – меридиональное напряжение в стенке аппарата, равное ; k 1и k 2 – коэффициенты, определяемые по рис. 30 а, б для лап типа I.
Затем проверяют условие прочности:
, (25)
где σт – значение предела текучести материала стенки при расчетной температуре; А = 1 для условий эксплуатации и А = 1,2 при транспортировании и гидроиспытаниях.
Если условие (25) не выполняется, то требуется применить накладной лист, располагаемый на корпусе аппарата под лапой и служащий для увеличения области местных нагрузок. В этом случае необходимо воспользоваться методом расчета, приведенным в РТМ 26-319–79.
Рис. 30. Кривые для расчета опор: а – k 1 = f (γ); б – k 2 = f (γ)
Наряду с рассмотренными выше лапами в промышленности широко применяют и другие виды опор (РТМ 26-111–77 и РТМ 26-110–77), например трубчатые, га которые опирается горизонтальная цистерна для жидкости (рис. 31).
Рис. 31. Горизонтальная цистерна для жидкости на трубчатых колесах
При конструировании опор горизонтальных аппаратов следует проверить стенку корпуса на устойчивость в местах опирания. Критическая нагрузка Р кр может быть приближенно найдена при рассмотрении опоры аппарата как круговой арки постоянного сечения с шарнирно опертыми концами, находящейся под действием равномерно распределенной нагрузки (рис. 32):
. (26)
Рис. 32. Схема к расчету стенки корпуса на устойчивость в местах расположения опор
В приведенном уравнение J – момент инерции поперечного сечения полоски листа шириной, равной ширине опоры и кольца жесткости, если последнее имеется. Момент инерции берется относительно оси, параллельной оси аппарата, проходящей через центр масс сечения.
Действительную нагрузку, приходящуюся на 1 см длины опорной поверхности, находят делением реакции опоры аппарата на проекцию дуги опорной поверхности на хорду:
; (27)
при
(28)
Действительная нагрузка должна быть меньше допустимой:
(29)
Лекция № 14
Тема: «Расчёт аппаратов на ветровую нагрузку и сейсмические силы»
При расчете на ветровые нагрузки аппарат рассматривают в трех состояниях:
– при рабочих условиях, когда аппарат имеет вес Q p;
– при гидроиспытании, когда аппарат заполнен водой и имеет максимальный вес Q max (с учетом воды, внутренних устройств и изоляции);
– после монтажа, когда аппарат имеет минимальный вес Q min (без учета веса изоляции и внутренних устройств).
Расчет цилиндрических аппаратов на действие ветровой нагрузки включает:
1. Выбор размеров площади опорной поверхности фундаментного
кольца 1 (рис. 33) и проверку фундамента на напряжения сжатия, возникающие на опорной поверхности.
Рис. 33. Схема к расчету напряжений на опорной поверхности аппарата
при весе аппарата: а – минимальном; б – максимальном
2. Определение толщины фундаментного кольца и других элементов опоры.
3. Расчет аппарата на устойчивость против опрокидывания (выбор числа и размеров фундаментных болтов).
4. Расчет сварного шва 2, соединяющего опорную часть 3 с аппаратом.
5. Проверка устойчивости цилиндрической формы стенки опорной части аппарата.
1. При расчете ветровых нагрузок и моментов аппарат делят по высоте на участки длиной не более 10 м. Для аппаратов с меняющимися по высоте формой и диаметром деление на участки целесообразно проводить так, чтобы границы участков соответствовали отметкам изменения этих параметров.
Ветровую нагрузку (силу) на i -й участок (на высоте х) определяют как сумму статической и динамической Р составляющих:
Р i = Р c i + Р д i,
где ,
. Здесь q н i – нормативное значение статической составляющей ветровой нагрузки; F 1 – площадь проекции i -го участка на плоскость, перпендикулярную направлению ветра (F 1 = Н i · Di для участка цилиндрического аппарата высотой Н i и диаметром Di; М i – масса i -го участка аппарата; ξ – коэффициент динамичности, определяемый по графику (рис. 34) в зависимости от параметра ε; η i – приведенное ускорение центра масс i- го участка, м/с2.
Рис. 34. График для определения коэффициента динамичности
Нормативное значение статической составляющей ветровой нагрузки:
q н i = q 0θ c,
где q 0 – скоростной вапор ветра для высоты над поверхностью земли до 10 м,
принимаемый по приведенным ниже данным в зависимости от района установки аппарата (например, города Москва, Минск расположены в 1 районе, Омск, Тобольск, Уфа — во II районе, Куйбышев, Оренбург — в ΙΙΙ районе); θ i – коэффициент, учитывающий возрастание скоростного напора с увеличением высоты х i над поверхностью земли; при выборе θ, по графику (рис. 35) учитывают высоту до середины i -го участка.
Рис. 35. График для определения коэффициентов θ i
Суммарный момент находят по формулам:
– при максимальном весе аппарата (Q max)
М = 0,6 М в + М э;
– при рабочем весе (Q р)
М = М в + М э;
– при минимальном весе (Q min)
М = М в1 + М э; М в1 = М в D н/ D и.
Максимальное напряжение на опорной поверхности фундаментного кольца (см. рис. 33) при максимальном весе (Q max) и при рабочем весе (Q р) аппарата и соответствующих изгибающих моментах М от действия ветровых и весовых сил:
;
,
где F – опорная площадь фундаментного кольца; W – момент сопротивления изгибу опорной площади фундаментного кольца.
Для цилиндрических аппаратов внутренний и наружный диаметры опорного фундаментного кольца обычно принимают равными соответственно:
;
,
где k – коэффициент, определяемый по графику (рис. 36) и равный отношению ширины кольца к D н.
Рис. 36. График для определения коэффициента k
Тогда
;
.
2. Толщину фундаментного кольца, не укрепленного ребрами (рис. 37), рассчитывают из условия изгиба выступающей части кольца длиной b под действием напряжения σmax.
Рис. 37. Схема к расчету нагрузки на фундаментное кольцо
Нагрузка на полоску шириной, равной единице, и длиной b:
q к = σmax b.
Изгибающий момент для полоски (как для консольной балки):
Момент сопротивления изгибу опасного сечения полоски:
.
Напряжение в кольце:
.
Отсюда находят толщину фундаментного кольца:
,
где σ – напряжение в кольце, которое можно принять равным нормативному допускаемому напряжению при 20 °С; φ – коэффициент, учитывающий увеличение жесткости конструкции при наличии ребер и возможность уменьшения при этом толщины кольца.
3. Минимальное напряжение на опорной поверхности фундаментного кольца при минимальном весе аппарата и соответствующем опрокидывающем моменте
.
Если минимальное напряжение σmin положительное или равно нулю, то следует определить коэффициент устойчивости аппарата:
,
где М Q – момент от собственного веса аппарата; R 1 – плечо силы Q min принимаемое равным примерно 0,42 D н.
При у > 1,5 устанавливать фундаментные болты не обязательно, но ох всегда необходимо предусматривать для фиксации аппарата. Число болтов принимают равным 4; 6; 8; 10 и далее кратным четырем.
Отрицательное значение свидетельствует об отрыве фундаментного кольца от фундамента. В этом случае фундаментные болты работают на растяжение.
Нагрузку на наиболее нагруженный болт Р σ приближённо можно определить
в зависимости от σmin, площади фундаментного кольца F и числа фундаментных болтов n по формуле:
.
Внутренний диаметр резьбы фундаментного болта из условия прочности на растяжение:
,
где [σ] – допускаемое напряжение на растяжение при температуре 20 °С (для болтов выбирают по ГОСТ 14249–73); С ≈ 0,3 см – прибавка на атмосферную коррозию.
4. Напряжение в сплошном сварном шве, крепящем корпус аппарата
к цилиндрической опорной части (см. рис. 1), определяют в опасном сечении
(линия АА) по формулам:
;
где f c – площадь опасного сечения сварного шва; W c – момент сопротивления сварного шва изгибу; М' – изгибающий момент относительно сечения сварного шва от ветровых и эксцентрично приложенных массовых нагрузок, действующих выше сварного шва.
Если опора приварена к днищу, то сварной шов работает на сжатие
и σс ≤ φ [σ].
Если аппарат работает при высоких температурах, то следует проверять напряжения в сварном шве в сечении по линии АА в рабочих условиях, учитывая вес Q p аппарата в эксплуатационных условиях и допускаемое напряжение при рабочей температуре стенки.
5. При расчете аппарата на ветровую нагрузку стенки цилиндрической опорной части и корпуса проверяют на устойчивость формы в сжатой зоне.
Явление потери устойчивости формы цилиндрической стенки в сжатой зоне аналогично по своей сущности продольному изгибу сжатых стержней.
Нарушение формы вмятие (см. рис. 38) может произойти при напряжениях меньше предела текучести материала стенки.
Устойчивость формы опорной части проверяют, как для цилиндрической обечайки, под действием осевой сжимающей силы Q = Q max и изгибающего момента. Для обеспечения устойчивости должно быть выполнено условие:
,
где Q доп – допускаемая осевая сжимающая сила; М доп – допускаемый изгибающий момент.
Рис. 38. Схема нагрузок, действующих на вертикальный аппарат
Допускаемая осевая сжимающая сила:
.
Допускаемый изгибающий момент рассчитывают по формулам:
– при
;
– при
.
Список литературы
1. Основы конструирования и расчета химико-технологического оборудования. Справочник в 3-х томах. Тимонин А.С. – Калуга, 2002 г.
2. Остриков А.Н., Игнатов В.Е.и др. Практикум по курсу расчёт и конструирование машин и аппаратов пищевых производств-Воронеж, 1997. – 327 с.
3. Скобло А.И., Молоканов Ю.К., Владимиров А.И., Щелкунов В.А. Процессы и аппараты нефтегазопереработки и нефтехимии: Учебник для вузов. – 3-е изд., пеерераб. и доп – М.: ООО «Недра – Бизнесцентр», 2000. – 677 с.
4. Вихман Г.Л., Круглое С.А. Основы конструирования аппаратов и машин нефтеперерабатывающих заводов. – 2-е изд. – М.: Машиностроение, 1978. – 328 с.
5. Владимиров А.И., Щелкунов В.А., Круглов С.А. Основные процессы и аппараты нефтегазопереработки: Учеб. Пособие для вузов. – М.: ООО «Недра – Бизнесцентр», 2002. – 227 с.
6. Расчёт и конструирование машин и аппаратов химических производств: примеры и задачи: Учебное пособие для студентов втузов. Под ред. М.Ф. Михалева. – Л.: Машиностроение, 1984. – 301 с.
7. Методические указания по курсу: Расчет и конструирование машин и аппаратов химических производств. Расчет укрепления отверстий в ап
|
|
История создания датчика движения: Первый прибор для обнаружения движения был изобретен немецким физиком Генрихом Герцем...
История развития хранилищ для нефти: Первые склады нефти появились в XVII веке. Они представляли собой землянные ямы-амбара глубиной 4…5 м...
Общие условия выбора системы дренажа: Система дренажа выбирается в зависимости от характера защищаемого...
Организация стока поверхностных вод: Наибольшее количество влаги на земном шаре испаряется с поверхности морей и океанов (88‰)...
© cyberpedia.su 2017-2024 - Не является автором материалов. Исключительное право сохранено за автором текста.
Если вы не хотите, чтобы данный материал был у нас на сайте, перейдите по ссылке: Нарушение авторских прав. Мы поможем в написании вашей работы!