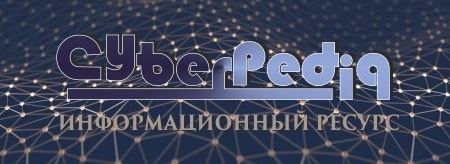
Адаптации растений и животных к жизни в горах: Большое значение для жизни организмов в горах имеют степень расчленения, крутизна и экспозиционные различия склонов...
Папиллярные узоры пальцев рук - маркер спортивных способностей: дерматоглифические признаки формируются на 3-5 месяце беременности, не изменяются в течение жизни...
Топ:
Основы обеспечения единства измерений: Обеспечение единства измерений - деятельность метрологических служб, направленная на достижение...
Отражение на счетах бухгалтерского учета процесса приобретения: Процесс заготовления представляет систему экономических событий, включающих приобретение организацией у поставщиков сырья...
Интересное:
Средства для ингаляционного наркоза: Наркоз наступает в результате вдыхания (ингаляции) средств, которое осуществляют или с помощью маски...
Влияние предпринимательской среды на эффективное функционирование предприятия: Предпринимательская среда – это совокупность внешних и внутренних факторов, оказывающих влияние на функционирование фирмы...
Что нужно делать при лейкемии: Прежде всего, необходимо выяснить, не страдаете ли вы каким-либо душевным недугом...
Дисциплины:
![]() |
![]() |
5.00
из
|
Заказать работу |
|
|
Червячные фрезы в ИП производстве изготавливаются из следующих марок быстрорежущих сталей: Р6М5, Р6М5К5, Р6М5Ф3-Ш, Р6М5Ф3-МП.
Наиболее ответственная операция с точки зрения влияния на дальнейшую стойкость червячной фрезы – это заточка по передней поверхности. Заточка производится следующими абразивными кругами:
1) 12 300х20х50,8 24А 25Н СМ1 12 К11
2) 12 300х20х50,8 25А 25Н СМ1 11 КФ-40
Проводились производственные испытания по заточке выше названными кругами на двух параллельно работающих станках ф. Карр мод. As-305, червячных фрез, выбранных случайным образом, выполненных из всех выше перечисленных сталей. При этом стоит отметить, что в основном это были стали Р6М5Ф3-МП и Р6М5Ф3-Ш – отличием этих сталей является лишь то, что первая выполнена путем спекания мелкодисперсных частиц, по технологии порошковой металлургии, вторая же сталь получена методом электрошлакового переплава. Шероховатость поверхности замерена 38 раз на шлифованной поверхности. Расположим замеры шероховатости Ra в порядке возрастания:
0,175; 0,182; 0,185; 0,187; 0,192; 0,195; 0,195; 0,198; 0,202; 0,203; 0,206; 0,208; 0,209; 0,210; 0,212; 0,215; 0,216; 0,218; 0,221; 0,224; 0,227; 0,228; 0,229; 0,231; 0,232; 0,232; 0,235; 0,238; 0,241; 0,244; 0,246; 0,247; 0,251; 0,252; 0,257; 0,259; 0,263; 0,266; 0,276.
На основании этих данных заполним таблицу 4.1.
Таблица 4.1. Данные для построения кривой распределения
Интервалы | значения середин | Обычная правка | ||
свыше | До | интервалов | частота | частость |
0,17 | 0,18 | 0,175 | 1 | 0,026 |
0,18 | 0,19 | 0,185 | 3 | 0,052 |
0,19 | 0,20 | 0,195 | 4 | 0,105 |
0,20 | 0,21 | 0,205 | 5 | 0,132 |
0,21 | 0,22 | 0,215 | 5 | 0,132 |
0,22 | 0,23 | 0,225 | 4 | 0,158 |
0,23 | 0,24 | 0,235 | 5 | 0,132 |
0,24 | 0,25 | 0,245 | 4 | 0,105 |
0,25 | 0,26 | 0,255 | 4 | 0,079 |
0,26 | 0,27 | 0,265 | 2 | 0,052 |
0,27 | 0,28 | 0,275 | 1 | 0,026 |
Используя данные таблицы 4.1. построим кривую распределения.
Рис. 4.1. Кривая распределения при шлифовании червячных фрез из сталей Р6М5, Р6М5К5, Р6М5Ф3-Ш, Р6М5Ф3-МП
|
Из общего вида кривой распределения рис. 4.1 можно говорить о том, что, во-первых, данная технологическая операция не позволяет производить годную продукцию и требуются срочные меры по улучшению качества, во-вторых, очень большой разброс шероховатости (почти 0,1мкм по Ra). То есть в данном случае возникает две проблемы требующие решений:
1. Слишком высокая высота микронеровностей шлифованной поверхности, вероятность получения негодной продукции более 50%.
2. Низкая степень прогнозируемости процесса.
Причина возникновения первой проблемы заключается или в неправильном выборе абразивного материала или же в неправильном выборе режимов резания. Возможная причина второй проблемы заключается в том, что у обрабатываемых сталей несколько разная шлифуемость.
Для решения первой проблемы существуют несколько стандартных решений:
1) Выбор другого абразивного круга
а) с меньшей твердостью
б) с меньшей зернистостью
2) Выбор других режимов резания
а) уменьшение подачи
б) увеличение скорости резания
в) увеличение времени выхаживания.
Рассмотрим все решения по порядку.
Выбор абразивного материала с меньшей твердостью.
При уменьшении твердости абразивного материала происходит снижение прочности удержания абразивных зерен в круге, затупившиеся зерна быстрее вылетают из круга. При шлифовании это приводит к улучшении стабильности и некоторому снижению шероховатости. Помимо прочего это приводит к тому, что абразивный круг хуже «держит профиль», то есть зерна быстрее осыпаются быстрее, переточки приходиться производит чаще. В нашем случае данное решение неприемлемо, так как будет ухудшаться важный параметр червячной фрезы – отклонение от номинального положения образующей передней поверхности.
Выбор абразивного материала с меньшей зернистостью.
При уменьшении размера зерен абразива, соответственно и уменьшаются размеры рисок им оставленном на шлифуемой поверхности, в этом случае значения шероховатости снижаются значительно. Но при этом значительно увеличивается повышается теплонапряженность процесса резания, что потребует снижение подачи, и как следствие снижение производительности. Примем данное решение.
|
Изменение режимов резания – уменьшение подачи.
В данном случае это не актуально, так как окончательная шероховатость формируется при выхаживании, которое включено в данный техпроцесс.
Изменение режимов резания – увеличение скорости резания.
Скорость резания несколько снижает величину микронеровностей на шлифованной поверхности, но при этом значительно повышается теплонапряженность процесса резания, а следовательно увеличивается вероятность появления шлифовочных прижогов, что недопустимо. Также, фактические режимы резания – скорость резания 25–30 м/с, что близко к критической величине, на которой предназначены работать применяемые абразивные круги (35 м/с). Также в данном случае нас ограничивают возможности самого станка, скорость вращения шлинделя станка не позволяет повышать скорость резания выше 35 м/с.
Изменение режимов резания – увеличение времени выхаживания.
Время выхаживания подобрано экспериментально, и увеличение этой величины обычно приводит к появлению шлифовочных прижогов. Данное решение не приемлемо.
Для решения второй проблемы воспользуемся [12], коэффициенты шлифуемости сталей К1:
Для Р6М5 КR=0,94
Для Р6М5К5 КR=1,1
Для Р6М5Ф3-МП КR=0,94
Для Р6М5Ф3-Ш КR=1,2
Из общего вида кривой распределения, наличие почти плоской площадки на вершине, можно сделать предположение, что данная кривая является кривой суммарного распределения шероховатости по шлифованию каждой стали в отдельности, и что эти распределения могут подчинятся закону Гаусса. Тогда, одним из возможных путей решения этой проблемы заключается в том, чтобы изготавливать червячные фрезы только из одного материала и применять на заточной операции лишь одну марку абразивного круга. Данные меры должны сузить разброс шероховатостей. Исходя из представленных данных и данных по стойкости червячных фрез из различных материалов наиболее целесообразным представляется изготавливать червячные фрезы из материала – Р6М5Ф3-МП.
Теперь просуммируем все решения по данным проблемам:
|
1. Выбор абразивного круга с меньшей зернистостью.
2. Изготавливать все червячные фрезы из одного материала и применять один абразивный круг.
Так как первое решение предполагает снижение производительности – воспользуемся вторым решением.
Проводились производственные испытания по заточке абразивным кругом 12 300х20х50,8 24А 25Н СМ1 12 К11 на двух параллельно работающих станках ф. Карр мод. As-305, червячных фрез, выбранных случайным образом, выполненных из быстрорежущей стали марки Р6М5Ф3-МП. Шероховатость поверхности замерена также 38 раз на шлифованной поверхности. Расположим замеры шероховатости Ra в порядке возрастания: 0,168; 0,174; 0,177; 0,179; 0,181; 0,183; 0,185; 0,186; 0,187; 0,188; 0,189; 0,190; 0,190; 0,191; 0,192; 0,192; 0,193; 0,194; 0,194; 0,194; 0,195; 0,195; 0,196; 0,197; 0,198; 0,198; 0,199; 0,199; 0,201; 0,202; 0,203; 0,204; 0,206; 0,207; 0,210; 0,212; 0,216; 0,222.
На основании этих данных заполним таблицу 4.2.
Таблица 4.2. Данные для построения кривой распределения
Интервалы | значения середин | Обычная правка | ||
свыше | До | интервалов | частота | частость |
0,167 | 0,172 | 0,1695 | 1 | 0,026 |
0,172 | 0,177 | 0,1745 | 2 | 0,052 |
0,177 | 0,182 | 0,1795 | 2 | 0,052 |
0,182 | 0,187 | 0,1845 | 4 | 0,105 |
0,187 | 0,192 | 0,1895 | 7 | 0,184 |
0,192 | 0,197 | 0,1945 | 8 | 0,211 |
0,197 | 0,202 | 0,1995 | 6 | 0,158 |
0,202 | 0,207 | 0,2045 | 4 | 0,105 |
0,207 | 0,212 | 0,2095 | 2 | 0,052 |
0,212 | 0,217 | 0,2145 | 1 | 0,026 |
0,217 | 0,222 | 0,2195 | 1 | 0,026 |
Используя данные таблицы 4.2. построим кривую распределения.
Рис. 4.2. Кривая распределения при шлифовании червячных фрез из стали Р6М5Ф3-МП
Общей вид кривой распределения рис. 4.2, с некоторым приближением, можно отнести к кривой нормального Гауссового распределения, а это дает возможность рассчитать процент появления вероятного брака. Расчет произведем, как показано в [15]. Для этого рассчитаем среднеквадратичное отклонение:
,
где
r - частость в интервале
D – остаточная погрешность, вычисляется по формуле:
, где
li – середина интервала
- среднее арифметическое
В нашем случае остаточная погрешность в каждом интервале:
D1=0,1695–0,169=0,0005
D2=0,1745 – (0,174+0,177)/2=-0,001
D3=0,1795 – (0,179+0,181)/2=-0,0005
D4=0,1845 – (0,183+0,185+0,186+0,187)/4=-0,00075
D5=0,1895 – (0,188+0,189+0,190+0,190+0,191+0,192+0,192)/7=-0,00079
D6=0,1945 – (0,193+0,194+0,194+0,194+0,195+0,195+0,196+0,197)/8=
=-0,00025
D7=0,1995 – (0,198+0,198+0,199+0,199+0,201+0,202)/6=0
D8=0,2045 – (0,203+0,204+0,206+0,207)/4=-0,0005
|
D9=0,2095 – (0,210+0,212)/2=-0,0015
D10=0,2145–0,216=-0,0015
D11=0,2195–0,221=-0,0015
Тогда среднеквадратичное отклонение:
s1=0,0035 мкм
Коэффициент точности вычисляется по формуле:
ТП=d/6s,
где
d – допуск на изготовление детали. В нашем случае т. к. допуска как такового нет, величину заменяющую допуск можно найти по формуле:
,
где
А=0,2 – критическая шероховатость, определяемая по чертежу.
Тогда:
d=2*(0,2–0,194)=0,012 мкм
Отсюда, коэффициент точности:
ТП.1=0,012/0,0035*6=0,57
Далее необходимо рассчитать коэффициент смещения:
,
где
lcp=(Анаиб.+ Анаим.)/2, где
Анаиб. и Анаим. – соответственно наибольший и наименьший размер в выборке
lcp.=(0,221+0,169)/2=0,195
Тогда коэф. Смещения:
Е=|,193–0,196|/0,012=0,25
Теперь по табл. 2 в [15] определим вероятность появления брака.
Доля вероятного брака: Р=22%
Также можно говорить о значительно более узком разбросе шероховатостей, но вероятность появления брака, тем не менее, достаточно высока. В данном случае можно воспользоваться первым решением, но это приведет к снижению производительности. Чтобы этого избежать предлагается выбрать шлифовальный круг из кубического нитрида бора. Эльборовые круги показали себя хорошо как раз там, где необходимо добиться высоких показателей стабильности процесса шлифования при высоких требованиях к обрабатываемой поверхности. При этом прочность удержания зерен в круге значительно выше, и твердость зерен также выше, что позволяет вести обработку на повышенных режимах.
По [8] предлагается эльборовый круг следующих характеристик:
Профиль круга тарельчатый – 12R4
Габариты круга, наружный диаметр х толщина х внутренний диаметр
Марка шлифовального материала для обработки быстрорежущей стали – ЛКВ40
Для получения шероховатости Ra 0,2 мкм принимаем зернистость – 80/63
Для получения стабильных показателей по размеру принимаем твердость – С1
Связку круга берем керамическую – К27
Концентрацию эльбора – 100%
Маркировка полная – 12R4 300х20х50,8 ЛКВ40 80/63 С1 К27 100%.
Теперь назначим некоторые режимы резания данным кругом.
По диаметру круга и паспортным данным станка назначаем скорость резания v=35 м/c
Определим частоту вращения круга:
n=1000*V*60/p*D
n=1000*35*60/3,14*300=2053 об/мин
Станок имеет бесступенчатое регулирование скорости вращения.
Далее найдём остальные параметры шлифования.
Назначаем подачу S =2 м /мин
Глубина шлифования t=0.003 мм/ход
Машинное время ТМ:
TM=(L+2lП)*i*z/S*1000
где:
L – длина фрезы, L=150 мм
lП – длина перебега круга, назначаем 30 мм
z – число зубьев фрезы
i=D/t,
где
D=0,15 мм – припуск под шлифовку
Отсюда находим: i=0.1/0.003=33
TM=(150+2*30)*33*14/2*1000=48 мин.
Штучное время Тшт найдём по формуле:
Тшт=Тв+Тп-з+Тм
ТВ=1,2 мин – вспомогательное время;
|
ТП-З = 0,5 мин – подготовительно–заключительное время;
Тшт=1,2+0,5+48=49,7 мин
Теперь по [8] рассчитаем ожидаемую шероховатость Ra при обработке червячной фрезы:
Ra=0,93*v-0.3*S0.06*t0.04*К1* К2* К3,
где
К2 – коэффициент, учитывающий концентрацию эльбора, при 100% – К2=1
К3 – коэффициент, учитывающий зернистость круга, при 80/63 – К3=1
Отсюда найдем показатель шероховатости: Ra=0,93*35-0.3*20.06*0,0030.04*0,94=0,18.
По чертежу 0,2, то есть приемлемо.
5. Расчет безопасности станка и его основных элементов
Общие положения
Понятие безопасности включает в себя такие понятия как, безопасные условия труда, безопасность производственного оборудования, безопасность производственного процесса. При рассмотрении безопасности мы рассматриваем как техническую систему, так и систему «человек – машина».
В качестве «человека» подразумевается персонал, непосредственно занятый выполнением работ, «машины» – технологическое оборудование, иногда с предметом труда, обеспечивающее изменение его свойств или состояния.
Безопасные условия труда – состояние условий труда, при которых воздействие на работающего опасных и вредных производственных факторов исключено или воздействие вредных производственных факторов не превышает предельно допустимых значений.
Безопасность производственного оборудования – свойство производственного оборудования соответствовать требованиям безопасности труда при монтаже (демонтаже) и эксплуатации в условиях установленных нормативно-технической документацией.
Безопасность производственного процесса – свойство производственного процесса соответствовать требованиям безопасности труда при проведении его в условиях, установленных нормативно-технической документацией.
При анализе безопасности системы следует разделять такие понятия как опасный фактор и вредный фактор. Опасным фактором является такое воздействие на человека, которое в определенных условиях приводит к травме или другому внезапному резкому ухудшению здоровья. Вредным фактором является такое воздействие на человека, которое в определенных условиях приводит к заболеванию или снижению работоспособности.
Конечным следствием неблагоприятных условий труда являются производственный травматизм и профессиональные заболевания.
Травма – повреждение тканей организма и нарушение его функций внешними воздействиями.
Профзаболевание - либо на встречающееся в быту (специфическое), либо возникающее как на производстве, так и в быту устойчивое нарушение здоровья.
Производственная опасность – наблюдаемое в процессе выполнения технологических операций (функционирования человеко-машинных систем) свойство таких систем представлять в естественных условиях реально предсказуемую возможность причинения ущерба.
Ущерб – такое изменение состояния производственного процесса, которое характеризуется нарушениями целостности, работоспособности или потерей других свойств ее компонентов или окружающей среды в результате происшествий или вредного влияния на них неизбежных энергетических (тепло, шум,…) либо материальных (сажа, шлаки,…) выбросов.
Происшествие – событие, состоящее в воздействии производственной опасности на компоненты систем «человек-машина-среда» и повлекшее за собой ущерб, вследствие резкого изменения свойств системы или окружающей среды.
Обеспечение безопасности в рабочей зоне достигается тремя основными методами. В реальных условиях производства используется комбинация этих методов.
Метод А состоит в пространственном и (или) временном разделении рабочей зоны и опасного пространства: дистанционное управление, автоматизация, роботизация и др.
Метод Б состоит в нормализации опасного пространства путем исключения опасностей. Это совокупности мероприятий, защищающих человека от шума, газа, пыли, травм (средства коллективной защиты).
Метод В включает гамму приемов и средств, направленных на адаптацию человека к соответствующей среде и на повышение его защищенности: профотбор, обучение, психологическое воздействие, средства индивидуальной защиты.
Описание рабочего места, оборудования, выполняемых операций. Обработка внутреннего диаметра червячной фрезы ведётся на внутришлифовальном станке. Рабочий-оператор загружает заготовку и снимает обработанную деталь. На станке производятся операция шлифования внутреннего диаметра червячной фрезы.
Опасные и вредные производственные факторы разрабатываемого производственного объекта
Вибрация
В промышленности широкое применение получили машины и оборудование, создающие вибрацию, неблагоприятно воздействующую на человека. Увеличение производительности и, как следствие этого, рост мощностей и быстроходности технологического оборудования при одновременном снижении его материалоемкости, уменьшение статических нагрузок на человека сопровождаются нежелательным побочным эффектом–усилением вибраций. Воздействие вибраций не только ухудшает самочувствие работающего и снижает производительность труда, но часто приводит к тяжелому профессиональному заболеванию–виброболезни. Поэтому вопросам борьбы с вибрацией придается огромное значение.
В соответствии с ГОСТ 24346–80 (СТ СЭВ 1926–79) «Вибрация. Термины и определения» под вибрацией понимается движение точки или механической системы, при котором происходит поочередное возрастание, иубывание во времени значений, по крайней мере, одной координаты.
Причиной возбуждения вибраций являются возникающие при работе машин и агрегатов неуравновешенные силовые воздействия. В одних случаях источниками вибраций являются возвратно-поступательные движущиеся системы (кривошипно-шатунные механизмы, ручные перфораторы, вибротрамбовки, вращающиеся массы, ручные электрические и пневматические шлифовальные машины, режущий инструмент станков и т.п.). Иногда вибрации создаются ударами деталей (зубчатые зацепления, подшипниковые узлы и т.п.). Величина дисбаланса во всех случаях приводит к появлению неуравновешенных сил, вызывающих вибрацию. Причиной дисбаланса может явиться неоднородность материала вращающегося тела, несовпадение центра массы тела и оси вращения, деформация деталей от неравномерного нагрева при горячих и холодных посадках и т.п.
Воздействие вибраций на человека чаще всего связано с колебаниями, обусловленными внешним переменным силовым воздействием на машину либо на отдельную ее систему. Возникновение такого рода колебаний может: быть связано не только с силовым, но и с кинематическим возбуждением, например, в транспортных средствах при их движении по неровному пути.
Различают общую и локальную вибрации. Общая вибрация вызывает сотрясение всего организма, местная вовлекает в колебательное движение отдельные части тела. Общей вибрации подвергаются транспортные рабочие, операторы мощных штампов, грузоподъемных кранов и некоторых других видов оборудования. Локальной вибрации подвергаются работающие с ручным электрическим и пневматическим механизированным инструментом (зачистка сварных швов, обрубка отливок, клепка, шлифование и т. п.). В ряде случаев работник может подвергаться одновременно воздействию общей и локальной вибрации (комбинированная вибрация), например, при работе на строительно-дорожных машинах и транспорте.
Общая вибрация с частотой менее 0,7 Гц (качка) хотя и неприятна, но не приводит к вибрационной болезни. Следствием такой вибрации является морская болезнь, происходящая из-за нарушения нормальной деятельности органов равновесия (вестибулярного аппарата) по причине резонансных явлений.
Различные внутренние органы и отдельные части тела (например, голову и сердце) можно рассматривать как колебательные системы с определеннойI массой, соединенные между собой «пружинами» с определенными упругими свойствами и параллельно включенными сопротивлениями. Очевидно, что такая система обладает рядом резонансов, частоты которых, определяющие субъективное восприятие вибраций, зависят также от положения тела работающего (работа в положении стоя или сидя). Собственные частоты плечевого пояса, бедер и головы относительно опорной поверхности (положение «стоя») составляют 4–6Гц, головы относительно плеч (положение «сидя») – 25–30 Гц. Для большинства внутренних органов собственные частоты лежат в диапазоне 6–9 Гц. Колебания рабочих мест с указанными частотами весьма опасны, т.к. могут вызвать механическое повреждение или даже разрыв этих органов. Систематическое воздействие общих вибраций, характеризующихся высоким уровнем виброскорости, может быть причиной вибрационной болезни – стойких нарушений физиологических функций организма, обусловленных преимущественно воздействием вибраций на центральную нервную систему. Эти нарушения проявляются в виде головных болей, головокружения, плохого сна, пониженной работоспособности.
Вибрация может не вызывать болезненных ощущений, но затруднить проведение производственных процессов.
Локальная вибрация вызывает спазмы сосудов, которые начинаются с концевых фаланг пальцев и распространяются на всю кисть, предплечье, захватывают сосуды сердца. Вследствие этого происходит ухудшение снабжения конечностей кровью. Одновременно наблюдается воздействие вибрации на нервные окончания, мышечные и костные ткани, выражающееся в нарушении чувствительности кожи, окостенении сухожилий мышц и отложениях солей в суставах кистей рук и пальцев, что приводит к болям, деформациям и в холодный и уменьшаются в теплый период года. При локальной вибрации наблюдаются нарушения деятельности центральной нервной системы, как и при общей вибрации.
Виброболезнь относится к группе профзаболеваний, эффективное лечение которых возможно лишь на ранних стадиях. Восстановление нарушенных функций протекает очень медленно, а в особо тяжелых случаях в организме наступают необратимые изменения, приводящие к инвалидности.
Шум
Вопросы борьбы с шумом в настоящее время имеют большое значение во всех областях техники, особенно в машиностроении, на транспорте, в энергетике.
Шум на производстве наносит большой ущерб, вредно действуя на организм человека и снижая производительность труда. Утомление рабочих и операторов из-за сильного шума увеличивает число ошибок при работе, способствует возникновению травм. Нередко и в быту человек подвергается воздействию шума недопустимо высоких уровней. Поэтому борьба с шумом является важной задачей.
Часто возникает необходимость защиты не только от шума, но и от инфразвука и ультразвука.
Шумом является всякий нежелательный для человека звук. В качестве звука мы воспринимаем упругие колебания, распространяющиеся волнообразно нетвердой, жидкой или газообразной среде. Звуковые волны возникают при нарушении стационарного состояния среды вследствие воздействия на нее какой-либо возмущающей силы. Частицы среды при этом начинают колебаний (колебательная скорость υ), значительно меньше скорости распространения волны (скорости звука с).
Область слышимых звуков ограничивается не только определенными частотами (20–20000 Гц), но и определенными предельными значениями звуковых давлений и их уровнями
Уместно напомнить, что логарифмическая шкала уровней звукового давления построена таким образом, что пороговое значение звукового давления Ро соответствует порогу слышимости (1= 0 дБ) только на частоте 1000 Гц, принятой в качестве стандартной частоты сравнения в акустике. Порог слышимости различен для звуков разной частоты. Если в диапазоне частот 800–4000 Гц величина порога слышимости минимальна, то по мере удаления от этой области вверх и вниз по частотной шкале его величина растет; особенно заметно увеличение порога слышимости на низких частотах. По этой причине высокочастотные звуки более неприятны для человека, чем низкочастотные (при одинаковых уровнях звукового давления).
В зависимости от уровня и характера шума, его продолжительности, а также от индивидуальных особенностей человека шум может оказывать на него различное действие.
Шум, даже когда он невелик (при уровне 50–60 дБ), создает значительную нагрузку на нервную систему человека, оказывая на него психологическое воздействие. Это особенно часто наблюдается у людей, занятых умственной деятельностью. Слабый шум различно влияет на людей. Причиной этого могут быть: возраст, состояние здоровья, вид труда, физическое и душевное состояние человека в момент действия шума и другие факторы. Степень вредности того или иного шума зависит также от того, насколько он отличается от привычного шума. Неприятное воздействие шума зависит и от индивидуального отношения к нему. Так, шум, производимый самим человеком, не беспокоит его, в то время как небольшой посторонний шум может вызвать сильный раздражающий эффект.
Известно, что ряд таких серьезных заболеваний, как гипертоническая и язвенная болезни, неврозы, в ряде случаев желудочно-кишечные и кожные заболевания, связаны с перенапряжением нервной системы в процессе труда и отдыха. Отсутствие необходимой тишины, особенно в ночное время, приводит к преждевременной усталости, а часто и к заболеваниям. В этой связи необходимо отметить, что шум в 30–40 дБ в ночное время может явиться серьезным беспокоящим фактором. С увеличением уровней до 70 дБ и выше шум может оказывать определенное физиологическое воздействие на человека, приводя к видимым изменениям в его организме.
Под воздействием шума, превышающего 85–90 дБ, в первую очередь снижается слуховая чувствительность на высоких частотах.
Сильный шум вредно отражается на здоровье и работоспособности людей. Человек, работая при шуме, привыкает к нему, но продолжительное действие сильного шума вызывает общее утомление, может привести к ухудшению слуха, а иногда и к глухоте, нарушается процесс пищеварения, происходят изменения объема внутренних органов.
Воздействуя на кору головного мозга, шум оказывает раздражающее действие, ускоряет процесс утомления, ослабляет внимание и замедляет психические реакции. По этим причинам сильный шум в условиях производства может способствовать возникновению травматизма, так как на фоне этого шума не слышно сигналов транспорта, автопогрузчиков и других машин.
Эти вредные последствия шума выражены тем больше, чем сильнее шум и чем продолжительнее его действие.
Таким образом, шум вызывает нежелательную реакцию всего организма человека. Патологические изменения, возникающие под влиянием шума, рассматривают как шумовую болезнь.
Звуковые колебания могут восприниматься не только ухом, но и непосредственно через кости черепа (так называемая костная проводимость). Уровень шума, передаваемого этим путем, на 20–30 дБ меньше уровня, воспринимаемого ухом. Если при невысоких уровнях передача за счет костной проводимости мала, то при высоких уровнях она значительно возрастает и усугубляет вредное действие на человека.
При действии шума очень высоких уровней (более 145 дБ) возможен разрыв барабанной перепонки.
|
|
Наброски и зарисовки растений, плодов, цветов: Освоить конструктивное построение структуры дерева через зарисовки отдельных деревьев, группы деревьев...
Общие условия выбора системы дренажа: Система дренажа выбирается в зависимости от характера защищаемого...
Механическое удерживание земляных масс: Механическое удерживание земляных масс на склоне обеспечивают контрфорсными сооружениями различных конструкций...
Биохимия спиртового брожения: Основу технологии получения пива составляет спиртовое брожение, - при котором сахар превращается...
© cyberpedia.su 2017-2024 - Не является автором материалов. Исключительное право сохранено за автором текста.
Если вы не хотите, чтобы данный материал был у нас на сайте, перейдите по ссылке: Нарушение авторских прав. Мы поможем в написании вашей работы!