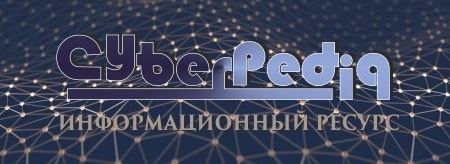
Индивидуальные и групповые автопоилки: для животных. Схемы и конструкции...
Индивидуальные очистные сооружения: К классу индивидуальных очистных сооружений относят сооружения, пропускная способность которых...
Топ:
Оснащения врачебно-сестринской бригады.
Выпускная квалификационная работа: Основная часть ВКР, как правило, состоит из двух-трех глав, каждая из которых, в свою очередь...
Интересное:
Как мы говорим и как мы слушаем: общение можно сравнить с огромным зонтиком, под которым скрыто все...
Влияние предпринимательской среды на эффективное функционирование предприятия: Предпринимательская среда – это совокупность внешних и внутренних факторов, оказывающих влияние на функционирование фирмы...
Национальное богатство страны и его составляющие: для оценки элементов национального богатства используются...
Дисциплины:
![]() |
![]() |
5.00
из
|
Заказать работу |
|
|
Гидропривод применяется в долбёжных станках для обеспечения рабочих движений резца, а так же подачи стола.
Гидравлический привод этого станка обеспечивает следующий цикл работы:
1. возвратно - поступательное движение долбяка, приводимого в движение гидроцилиндром ЦД;
2. подачу стола на каждый ход долбяка гидроцилиндром ЦП;
. пуск и остановка долбяка в любом положении. При остановке долбяка, его положение фиксируется гидросистемой.
Исходное положение: в начале цикла долбяк находится в положении, которое соответствует концу его обратного хода. Распределитель Р1 находится в положении II, сообщая каналы нагнетания насосов Н1 и Н2 со сливом при любом положении распределителя диапазона скоростей РДС.
Рабочий ход долбяка: при переключении распределителя Р1 в положение I рабочая жидкость от насосов через распределитель РДС поступает к распределителю реверса РР, который находится в положении I. От распределителя РР рабочая жидкость поступает в поршневую полость гидроцилиндра ЦД, из штоковой полости рабочая жидкость через гидроклапаны К3, К5, распределитель РДС поступает на слив.
Распределитель РДС имеет четыре фиксированных положения. В положении I рабочая жидкость от насоса Н1 поступает в гидросистему, а от насоса Н2 идет на слив. В положении II - наоборот. В положении III оба насоса нагнетают рабочую жидкость в гидросистему одновременно. Но в положении IV также как и в положении III, но рабочая жидкость поступает одновременно в обе полости гидроцилиндра ЦД. Таким образом обеспечивается получение четырёх диапазонов скоростей. Внутри каждого из этих диапазонов дросселем ДР1 обеспечивается бесступенчатое регулирование скорости движения долбяка.
|
Обратный ход долбяка: при крайнем переднем положении долбяка упор перемещает распределитель РУ в положение II. Из распределителя РУ рабочая жидкость поступает под левый торец распределителя РР и он переходит в положение II. Рабочая жидкость под давлением начинает поступать в штоковую полость гидроцилиндра ЦД, поршневая полость соединяется со сливом. Происходит движение долбяка в обратном направлении. В конце обратного хода долбяка другой упор снова перемещает распределитель РУ в положение I и цикл повторяется.
Во время обратного хода рабочая жидкость из поршневой полости сливается через фильтр Ф. при засорении фильтра рабочая жидкость сливается через предохранительный клапан К1.
Подача стола: одновременно со сменой положения распределителя РР приходит смена положения распределителя Р3. В момент реверсирования распределителя РР на рабочий ход рабочая жидкость под давлением поступает под левый торец распределителя Р3 и он занимает положение I. Пропуская рабочую жидкость в поршневую полость гидроцилиндра ЦП. Происходит подача стола. В момент реверсирования распределителя РР на обратный ход распределитель Р3 перейдёт в положение II, пропуская рабочую жидкость в штоковую полость гидроцилиндра ЦП. Происходит подготовка к последующей подаче. Величина подачи устанавливается регулируемым жёстким упором (на схеме не показан), ограничивающим ход поршня гидроцилиндра ЦП.
Остановка долбяка: в любом положении обеспечивается гидроклапаном К5. Во время работы под давлением рабочей жидкости клапан К5 поддерживается в открытом положении. При переводе распределителя Р1 в положение II, давление резко снижается и, под действием пружины, клапан К5 закрывается, запирая выход рабочей жидкости из штоковой полости гидроцилиндра ЦД. Гидроклапаны К2 и К4 ограничивают соответственно давление рабочего и обратного хода.
Проектирование вспомогательных систем станка
Системы смазки
|
Системы смазки предназначены для уменьшения потерь на трение, повышение износостойкости и обеспечения нормально допустимой рабочей температуры трущихся поверхностей. Правильно спроектированная система смазки способствует нормальной эксплуатации станка и длительному сохранению его точности.
Существуют индивидуальный и централизованный способы смазки.
Первый осуществляется независимыми устройствами для каждой трущейся пары, второй - несколькими устройствами, управляемыми с одного места.
По времени действия смазка делится на периодическую и непрерывную. По способу подачи масла к трущимся поверхностям различают смазку без принудительного давления (смазка поливом) и под давлением. По виду циркуляции различают следующие виды систем смазки: проточную, циркуляционную и смешанную. В проточной системе отработанное масло не возвращается в систему; в циркуляционной - оно многократно циркулирует; смешанная - сочетает в себе одновременно проточную и циркуляционную систему.
Наибольшее распространение получила централизованная непрерывная циркуляционная смазка поливом. Индивидуальная непрерывная циркуляционная смазка под давлением используется, главным образом, для подшипников скольжения.
В систему смазки входят: насос, система распределения, уплотняющие средства, устройства для очистки, контроля и сигнализации. В качестве смазочного материала применяют жидкие минеральные масла, а в некоторых случаях густые (консистентные) смазки. Для очистки масла используют пластинчатые, сетчатые, войлочные и магнитные фильтры.
Качество подводимой смазки (производительность насоса) определяют из условия теплового баланса.
Работа сил трения, а, следовательно, и количество теплоты, определяют выражением:
W1 = N (1 - J), Дж/с (7.1)
где N - мощность станка, Вт;
J - КПД соответствующего узла.
Количество теплоты, отводимого смазочной жидкостью равно:
W2 = Q. ρ. C. Δt, Дж/с (7.2)
где Q - объем протекающей смазки, м3/с;
ρ - плотность масла (ρ ≈ 0,9. 103) кг/м3;
С - удельная теплоемкость масла (С ≈ 1700), дж/кг. град;
Δt - температура нагрева масла, град.
По опытным данным: для зубчатых колес и подшипников качения Δt = 5…8о, для подшипников скольжения Δt = 30…40о.
Приравнивая выражения (7.1) и (7.2) и решая относительно Q получим
|
, м3/с (7.3)
Общую емкость системы смазки обычно принимают равной 5…6 минутной производительности насоса.
Принимаем по стандартному ряду .
Система охлаждения
Подача смазочно-охлаждающей жидкости (СОЖ) к режущим кромкам инструмента в процессе резания увеличивает стойкость инструмента, улучшает обрабатываемость и, в конечном счете, способствует повышению производительности. Кроме того, СОЖ отводит из зоны резания мелкую стружку и охлаждает обрабатываемую деталь.
В современном машиностроении в основном применяют охлаждение инструмента поливом его СОЖ.
В качестве СОЖ применяют чаще всего водные (5% раствор соды в воде) и масляные (взвесь масла в воде) эмульсии, а также осерненные масла (для тяжелых условий работы).
Количество подводимой СОЖ определяют из условия теплового баланса
, м3/с (7.4)
Для обычных условий Δt = 15…25о, плотность водных эмульсий ρ = 1.103 кг/м3, масляных ρ ≈ 9.103 кг/м3, удельная теплоемкость соответственно 4000 и 1600 дж/кг. град.
Общую емкость системы охлаждения принимают равной 10…12 минутной производительности насоса.
|
|
Состав сооружений: решетки и песколовки: Решетки – это первое устройство в схеме очистных сооружений. Они представляют...
Двойное оплодотворение у цветковых растений: Оплодотворение - это процесс слияния мужской и женской половых клеток с образованием зиготы...
Организация стока поверхностных вод: Наибольшее количество влаги на земном шаре испаряется с поверхности морей и океанов (88‰)...
Типы сооружений для обработки осадков: Септиками называются сооружения, в которых одновременно происходят осветление сточной жидкости...
© cyberpedia.su 2017-2024 - Не является автором материалов. Исключительное право сохранено за автором текста.
Если вы не хотите, чтобы данный материал был у нас на сайте, перейдите по ссылке: Нарушение авторских прав. Мы поможем в написании вашей работы!