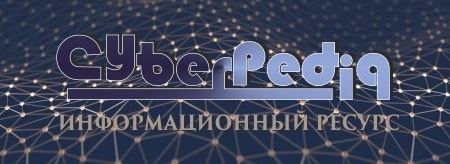
Состав сооружений: решетки и песколовки: Решетки – это первое устройство в схеме очистных сооружений. Они представляют...
Общие условия выбора системы дренажа: Система дренажа выбирается в зависимости от характера защищаемого...
Топ:
Устройство и оснащение процедурного кабинета: Решающая роль в обеспечении правильного лечения пациентов отводится процедурной медсестре...
Когда производится ограждение поезда, остановившегося на перегоне: Во всех случаях немедленно должно быть ограждено место препятствия для движения поездов на смежном пути двухпутного...
Интересное:
Принципы управления денежными потоками: одним из методов контроля за состоянием денежной наличности является...
Средства для ингаляционного наркоза: Наркоз наступает в результате вдыхания (ингаляции) средств, которое осуществляют или с помощью маски...
Что нужно делать при лейкемии: Прежде всего, необходимо выяснить, не страдаете ли вы каким-либо душевным недугом...
Дисциплины:
![]() |
![]() |
5.00
из
|
Заказать работу |
|
|
РЕМОНТ РЕДУКТОРА ЗАДНЕГО МОСТА АВТОМОБИЛЯ ВАЗ
ВОССТАНОВЛЕНИЕ ВАЛА ВЕДУЩЕГО
К У Р С О В О Й П Р О Е К Т
КП 1705.199.03.000.ПЗ
Руководитель
МИНЬКО А.М.
Учащийся
КАМЕНЩИКОВ В.А.
г.Ангарск-2003 год
УТВЕРЖДЕНО:
на цикловой комиссии
Председатель ______________
«_____» ____________ 200___г.
ЗАДАНИЕ
для курсового проектирования по учебной дисциплине
«Ремонт автомобилей и двигателей»
Студенту ______________ курса ___________________________группы
Ангарского промышленного политехнического колледжа
КАМЕНЩИКОВУ Владлену Александровичу
Тема задания Ремонт редуктора заднего моста автомобиля ВАЗ. Восстановление вала ведущего.
Введение: Краткое описание вопросов, разработанных в проекте.
Обоснование целесообразности восстановления.
Организация ремонта.
1.1. Описание устройства и последовательности разборки сборочной единицы редуктора заднего моста
1.2. Очистка и мойка деталей редуктора заднего моста
1.3. Дефектация и сортировка деталей сборочной единицы редуктора заднего моста
2. Расчетно-технологическая часть проекта: ___________________________
2.1 последовательность операции для устранения дефектов
2.2 Выбор оборудования
|
2.3 Выбор рабочего (режущего) и измер. инстр.
2.4 Расчет режим работы по операциям
2.4.1 Операция токарная
2.4.2 Операция наплавочная
2.4.3 Операция токарная
2.4.4 Операция шлифовальная
2.5 Техническое нормирование станочных работ
3. Техника безопасности и противопожарные мероприятия при выполнении ремонта сборочной единицы и восстановления детали______________
____________________________________________________________________
Графическая часть проекта выполняется на двух листах формата А1 (594-841).
Сборочный чертеж ремонтируемой сборочной единицы.
Формат А1 (594-841)
Допускается выполнение сборочного чертежа на формате А2 (420-597)
____________________________________________________________________
Технологическая карта.
4.2.1. Рабочий или ремонтный чертеж восстанавливаемой детали А3 (297-420) __________________________________________________________
Маршрутная карта на восстановление детали формат А3 (297-420).
____________________________________________________________________
Эскизы к операциям 4 шт. формат А4 (210-297)
|
Дата выдачи ______________________
Срок окончания____________________
Зав. отделением____________________
Преподаватель ____________________
СОДЕРЖАНИЕ
Введение................................................................................................ - 5
1.1. Схема разборки вала ведущего..................................................... - 6
1.2. Очистка и мойка деталей входящих в К.П. с описанием применяемого оборудования, процесса мойки, современных моющих средств и режимов мойки............................................................................... - 8
1.3. Дефектация...................................................................................... - 11
2 Расчетно-технологическая часть........................................................ - 12
2.1. Последовательность операций, выполняемых для устранения дефектов......................................................................................................... - 12
2.2. Выбор оборудования..................................................................... - 14
2.3. Выбор инструментов...................................................................... - 15
2.4. Расчет режимов работы по операциям......................................... - 16
2.4.1 Операция токарная предварительная......................................... - 16
2.5. Техническое нормирование станочных работ.............................. - 19
2.6. Операция токарная окончательная (чистовая)............................. - 21
2.7. Операция шлифовальная............................................................... - 21
2.8. Техническое нормирование........................................................... - 23
2.9. Операция наплавочная................................................................... - 25
2.10. Техническое нормирование шлифовальных работ.................... - 25
Литература........................................................................................... - 27
| ||||
|
В процессе эксплуатации автомобиля его рабочие свойства постепенно ухудшаются из-за изнашивания деталей. Исправным считают автомобиль, который соответствует всем требованиям нормативно-технологической документации. Работоспособный автомобиль в отличии от исправного должен удовлетворять лишь тем требованиям выполнение которых позволяет использовать его по назначению без угрозы безопасности движения.
Повреждением называют переход авто в неисправные, но работоспособные состояния. Отказом называют переход автомобиля в неработоспособное состояние.
Текущий ремонт автомобилей производят на АТП. Он должен обеспечивать гарантированную работоспособность автомобиля на пробеге другого очередного планового ремонта но не менее пробега другого очередного ТО-2. При длительной эксплуатации автомобилей достигают такого состояния когда их ремонт в условиях АТП становится невозможным или экономически нецелесообразным, в этом случае они направляются на авторемонтные предприятия (АРП).
|
Основными источниками экономически эффективными и КР автомобилей является использование оснащенного ресурса их деталей.
Формулировка.
Около 70-75% деталей автомобилей поступивших в КР могут быть использованы повторно, либо без ремонта, либо после их восстановления. К ним относятся большинство наиболее сложных и дорогостоящих деталей, а так же валы, оси, цапфы и другие.
Стоимость восстановления этих деталей не превышает 10-50% стоимости их изготовления. Это достигается только при наличии, централизованного ремонта в условиях АРП с специально оборудованными производственными цехами участками и отделениями. При этом достигается большая экономия металла и энергетических ресурсов. В последнее время АРП либо закрываются, либо перепрофилируются из-за малой эффективности или неконкурентоспособности с автомобильными заводами и автомобильными иностранными производствами.
Целенаправленная работа завода изготовителя по повышению ресурса рам и кабин и доведению их до срока службы а/м способствует резкому сокращению сферы применению КР полнокомплектным автомашинам (Камаз, ЗиЛ). Это тенденция развития авторемонтного производства вызывает изменения функции АРП, которая становится преимущественно предприятием по капитальному ремонту агрегатов.
Рабочее место дефектовщика
1 - Контейнер; 2 - рольганг; 3 - слесарный стол; 4 – пресс; 5 – стол дефектовщика; 6 – пуль управления; 7 – шкаф с контрольно-измерительным инструментом; 8 – монорельс; 9 – поворотно-консольный кран; 10 – тележка с подъемным столом; 11 – направляющая; 12 – приводная станция тележки; 13 – контейнер для металлолома; 14,15 – подвижные захваты; 16 – пишущая машинка; 17 – стол для инструмента.
На обработку деталей
![]() ![]() ![]() ![]() ![]() ![]() ![]() ![]() |
Рис. Схема расположения припусков и допусков на обработку детали.
|
Номинальный припуск для шлифования складывается из основного припуска и величины допуска для чистового обтачивания, т.е.
Z3=Z3+S2; мм,
где Z3 – основной припуск на шлифование (0,1-0,2) мм. на сторону.
Принимаю 0,15мм.
S2 – допуск для чистового обтачивания равен (0,3-0,4)Z2,
где Z2 – основной припуск на чистовое обтачивание равен 0,2мм., отсюда
Z3=0,15+0,6=0,21
Номинальный припуск на чистовое обтачивание складывается из основного припуска и допуска на черновое обтачивание.
Z2=Z2+S; S=(0,3-0,4)Z1,
где Z1 – припуск на черновое обтачивание равен 0,2-2мм. Принимаю 2мм., отсюда Z1=0,8мм. на сторону.
Общий припуск на механическую обработку на сторону
Zобщ=Z3+Z2+Z1=3,01мм.
Принимаю 3мм.
Тогда диаметр заготовки d3=46мм.
Диаметр заготовки принимается в соответствии с ГОСТ по справочнику Конструктора-Машиностроение ТОМ1, Ануфьев, с.130.
Если заготовка выбирается диаметром больше чем расчетный, то при черновой (предварительной) обработке снимается слой металла за 1 проход до номинального размера, под чистовое обтачивание.
Операция токарная
Для получения восстановленной поверхности детали более высокого качества и однородной по материалу рекомендуется перед наплавкой ее протачивать для устранения неровностей и задиров. Поверхности рекомендуется протачивать с уменьшением диаметра от номинального на 1-2мм. Принимаю 1мм, т.е. на сторону 0,5мм.
Назначаю режимы обработки. Глубина резания t=0,5мм., подача S принимается в зависимости от мощности станка, жесткости системы СПИД, прочности режущей пластины резца и державки, принимаю S=0,4мм/об [2], с.266, Табл.11. Подача корректируется по паспортным данным станка, т.к. для токарной операции принимаю токарно-винторезный станок 16К20, то S=0,4мм/об. Скорость резания рассчитывается по формуле:
где Сv – коэффициент резания и при наружном продольном точении проходными резцами с материалом режущей части резца Т15К6 (титана 15%, кобальта 6% и остальное карбид вольфрама). Принимаю Сv=350.
Принимаю m=0,2, х=0,15, у=0,35.
Кv – коэффициент учитывающий влияние материала заготовки, состояние поверхности, материала инструмента и т.д. В учебных целях принимаю равный 1.
Частота вращения детали рассчитывается по формуле:
При расчете получили n=2692
Расчетная частота вращения шпинделя корректируется с паспортными данными станка 16К20 и принимаю 1600.
Операция наплавочная
Автоматическая вибродуговая наплавка служит для восстановления изношенных поверхностей. Основным преимуществом является небольшой нагрев детали (около 1000С, малая зона термического влияния, возможность получения наплавленного металла с требуемой твердостью и износостойкостью без дополнительной термической обработки.
|
Рис. Автоматическая вибродуговая наплавка.
1. Обрабатываемая деталь. 2. Механизм подачи проволоки. 3. Барабан с проволокой. 4. Мундштук. 5. Схема двигателя для подачи проволоки.
Сущность процесса АВДН заключается в периодическом замыкании и размыкании находящейся под током электродной проволоки и поверхности детали. Каждый цикл вибрации поволоки включает в себя 4 последовательно протекающих процесса:
- короткое замыкание;
- отрыв электрода от детали;
- электрический разряд;
- холостой ход.
При отрыве электрода от детали на ее поверхности остается частичка приварившегося металла.
В качестве источника тока применяют низковольтные генераторы типа АНД 500/250 и АНД 1000/500.
В качестве наплавочных головок применяют УАНЖ – 5,6; ВДГ – 5 электромагнитные вибраторы, либо КУМА – 5 с механическим вибратором.
В качестве проволоки применяют Нn-60, 80, Св-08.
Скорость наплавки определяется опытным путем в зависимости от скорости подачи электродной проволоки.
v=(0,4-0,7)vn
либо по формуле:
где d – диаметр электродной проволоки (принимается в зависимости от толщины наплавочного слоя) при толщине 3,5мм. d=2,5
vn – скорость подачи l 3,5мм/мин. Принимаю 3м/мин – 50 мм/с.
К – коэффициент перехода электродной проволоки в наплавленный металл (0,8-0,9)
h – заданная толщина наплавки;
S – Шаг наплавки, зависит от d проволоки. Принимаю 2,8 мм/об.
По паспортным данным станка 16К20 максимальная подача 2,8мм/об.
а – коэффициент, учитывающий отклонения фактической площади сечения наплавленного слоя от площади прямоугольника с высотой h. Принимаю 1.
Это значение соответствует требованиям на наплавку, где значения в пределах от 5 до 20 мм/с.
Частота вращения детали рассчитывается по формуле
и равна 13 об/мин.
Т.к. nmin шпинделя станка 16К20 составляет 12,5 об/мин, то близкие к этой величине расчетные частоты вращения округляются до 12,5 об/мин, либо станок оборудуется дополнительным редуктором снижающим частоту вращения шпинделя до 1-20 об/мин, либо до расчетного значения.
2.5 Операция токарная предварительная (черновая)
Режим обработки t=Z1=2мм.
Скорость подачи рассчитывается по формуле:
Считаем
тогда частота вращения шпинделя будет равна (dн/4 мм)
Частота вращения будет равна n=1618. Принимаю n=1600.
Тогда действительная скорость v будет равна
Действительная скорость равна v=101 м/мин
Сила резания. Принято раскладывать на составные по осям координат станка (см. рис.).
FZ – тангенциальная (окружная)
FY – радиальная
FX – осевая
FZ=10 Cр tx Sy vn Кр; Н
где Ср – коэффициент резания [2] Табл.22 с.273
Ср=300, х=1, y=0,75, n=-0,15, Кр=1
![]() |
FZ=10 300 21 0,50,75 161-0,15 1= 1664 Н
Тогда мощность резания рассчитывается по формуле:
Мощность электродвигателя р.n.ф.
Рdв = Рр/h=4,3/0,75=57 кВт.
По паспортным данным мощность двигателя токарно-винторезного станка 16К20 8 кВт.
Если нагрузка станка 75% и более, то станок выбран правильно. При меньшей загрузке необходимо принять станок меньшей мощности двигателя, в противном случае увеличивается потребление реактивной энергии, т.е. уменьшается СОS.
Операция шлифовальная
Наружное круглое шлифование выполняется тремя способами:
- способом продольной подачи
Рис..Продольная подача
При наружном круглом шлифовании способом продольной подачи припуск на обработку снимается за несколько проходов. Шлифовальный круг вращательное движение вокруг своей оси и поступательное в направлении обрабатываемой детали. Поступательное движение шлифовального круга.
- способом поперечной подачи
При наружном круглом шлифовании методом поперечной подачи шлифовальный круг обрабатывает одновременно всю длину вращаемой детали без продольного перемещения круга.
- способом глубинного шлифования
При глубинном шлифовании круг, установленный на полную глубину шлифования имеет вращательное движение и поступательное вдоль вращения детали.
Весь припуск при глубинном шлифовании (0,1-0,3мм) снимается за один проход.
Техническое нормирование
В нормируемое время входят все затраты рабочего времени включая в состав технико-обоснованной нормы на операцию (То) и необходимую для работы в соответствии с технологическим процессом (тв1 Тdon Tn.з).
Техническая норма штучно-калькуляционного времени рассчитывается по формуле
Тшк=То+Тв+Тdon+Тnз/П, мин
Тш=То+Тв+Тdon,
где То – основное (машинное время) – это время в течении которого происходит изменение формы, размеров, внутренних свойств детали (мин).
Тв – вспомогательное время – это время затрачиваемое действия обеспечивающее выполнение данное работы. К нему относятся: установка, закрепление, снятие детали, наладка оборудования, перестановка инструмента, обмер детали.
Тon=То+Тв
Оперативное время – это время в течение которого выполняется работа, непосредственно направленная на выполнение данной операции.
Тdon – дополнительное время состоит из времени на организационно-техническое обслуживание рабочего места и времени на отдых и личные надобности.
В организационно-техническое обслуживание рабочего места входят следующие работы: заточка инструмента, смазка станка, правка шлифовального круга … ….
Тdon=(То+Тв)к/100мин,
где К – отношение Тdon к То (%) устанавливается для каждой операции
Тnз – подготовительно заключительное время, затрачиваемое рабочим на подготовку к работе. Его продолжительность зависит от организации.
Техническое нормирование
Операция – токарная предварительная
То=l*i/s*n.мин,
где l=l+y
Y – величина прохода резца на врезание и перебег, для токарных работ y=5, мм
L=30+5=35, мм
То=35*1/0,5*1600=35/800=0,04мм
Тв – рассчитывается по формуле:
Тв=Тв.уст+Тв.пр+Тв.изм.(мин),
где Тв.уст – время на установку детали в основном зависит от массы и способов крепления. Тв.уст=0,5-1. мин. Принимаем Тв.уст=1. мин.
Тв.пр – время на проход 0,5-1мм беру 1 мин.
Тв.изм – время на измерение 0,5-1 мин. Принимаю 1 мин.
Тв=1+1+1=3мин.
Дополнительное время:
Тdon=((То+Тв)*К)/100;мин
К=8%
Тdon-((0,4+3)*8)/100-0,24часа-14секунд
Время штучное на одну операцию
Тш=То+Тв+Тdon
Тш=0,04+3+0,24=3,28 (3мин 16 сек.)
Штучное время на восстановление детали определяется по формуле
Тш=То+Тв+Тdon=0,9+3,5+0,39=4,79 мин.
Общее штучное время
Тш.общ=Тш1+Тш2+Тш3+Иш4=
=3,28+2,93+3,28+4,79==14,28 мин.
Литература
1. С.И.Румянцев и другие, Ремонт автомобилей, м., Транспорт, 1988-327с.
2. Ю.А.абрамов и другие, Справочник технолога машиностроителя Том 2, М., Машиностроение, 1986-496с.
3. Г.А.Броневич, Курсовое и дипломное проектирование, М., Стройиздат, 1973-240с.
4. И.Я.Корчанов, Технология и организация ремонта и строительных машин и оборудования, М., Стройиздат, 1990-351с.
РЕМОНТ РЕДУКТОРА ЗАДНЕГО МОСТА АВТОМОБИЛЯ ВАЗ
ВОССТАНОВЛЕНИЕ ВАЛА ВЕДУЩЕГО
К У Р С О В О Й П Р О Е К Т
КП 1705.199.03.000.ПЗ
Руководитель
МИНЬКО А.М.
Учащийся
КАМЕНЩИКОВ В.А.
г.Ангарск-2003 год
УТВЕРЖДЕНО:
на цикловой комиссии
Председатель ______________
«_____» ____________ 200___г.
ЗАДАНИЕ
для курсового проектирования по учебной дисциплине
«Ремонт автомобилей и двигателей»
Студенту ______________ курса ___________________________группы
Ангарского промышленного политехнического колледжа
КАМЕНЩИКОВУ Владлену Александровичу
Тема задания Ремонт редуктора заднего моста автомобиля ВАЗ. Восстановление вала ведущего.
Введение: Краткое описание вопросов, разработанных в проекте.
Обоснование целесообразности восстановления.
Организация ремонта.
1.1. Описание устройства и последовательности разборки сборочной единицы редуктора заднего моста
1.2. Очистка и мойка деталей редуктора заднего моста
1.3. Дефектация и сортировка деталей сборочной единицы редуктора заднего моста
2. Расчетно-технологическая часть проекта: ___________________________
2.1 последовательность операции для устранения дефектов
2.2 Выбор оборудования
2.3 Выбор рабочего (режущего) и измер. инстр.
2.4 Расчет режим работы по операциям
2.4.1 Операция токарная
2.4.2 Операция наплавочная
2.4.3 Операция токарная
2.4.4 Операция шлифовальная
2.5 Техническое нормирование станочных работ
3. Техника безопасности и противопожарные мероприятия при выполнении ремонта сборочной единицы и восстановления детали______________
____________________________________________________________________
|
|
Наброски и зарисовки растений, плодов, цветов: Освоить конструктивное построение структуры дерева через зарисовки отдельных деревьев, группы деревьев...
Биохимия спиртового брожения: Основу технологии получения пива составляет спиртовое брожение, - при котором сахар превращается...
Своеобразие русской архитектуры: Основной материал – дерево – быстрота постройки, но недолговечность и необходимость деления...
История создания датчика движения: Первый прибор для обнаружения движения был изобретен немецким физиком Генрихом Герцем...
© cyberpedia.su 2017-2024 - Не является автором материалов. Исключительное право сохранено за автором текста.
Если вы не хотите, чтобы данный материал был у нас на сайте, перейдите по ссылке: Нарушение авторских прав. Мы поможем в написании вашей работы!