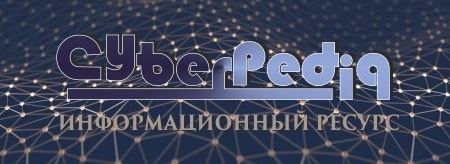
Индивидуальные и групповые автопоилки: для животных. Схемы и конструкции...
Особенности сооружения опор в сложных условиях: Сооружение ВЛ в районах с суровыми климатическими и тяжелыми геологическими условиями...
Топ:
Марксистская теория происхождения государства: По мнению Маркса и Энгельса, в основе развития общества, происходящих в нем изменений лежит...
Отражение на счетах бухгалтерского учета процесса приобретения: Процесс заготовления представляет систему экономических событий, включающих приобретение организацией у поставщиков сырья...
Техника безопасности при работе на пароконвектомате: К обслуживанию пароконвектомата допускаются лица, прошедшие технический минимум по эксплуатации оборудования...
Интересное:
Мероприятия для защиты от морозного пучения грунтов: Инженерная защита от морозного (криогенного) пучения грунтов необходима для легких малоэтажных зданий и других сооружений...
Берегоукрепление оползневых склонов: На прибрежных склонах основной причиной развития оползневых процессов является подмыв водами рек естественных склонов...
Наиболее распространенные виды рака: Раковая опухоль — это самостоятельное новообразование, которое может возникнуть и от повышенного давления...
Дисциплины:
![]() |
![]() |
5.00
из
|
Заказать работу |
|
|
Разработка участка механической обработки детали зубчатого колеса со шпоночным пазом
Анализ служебного назначения и технологичности конструкции детали изготавливаемой на проектируемом участке
Деталь зубчатого колеса со шпоночным пазом представляет собой тело вращения и входит в состав редуктора.
Редукторы - основные элементы механизмов в зависимости от назначения, к редукторам и ко всему механизму могут предъявляться различные требования.
Шестерня коническая относится к ответственным деталям машин и служит для изменения ряда частот вращения и передачи их с одного вала на другой, по средствам зубчатых секторов расположенных на наружной поверхности. Шестерня коническая устанавливается на валу с помощью шлицевого соединения и воспринимает осевые и радиальные (поперечные) силы, вызывающие изгиб. К зубчатым секторам предъявляются высокие требования, как по точности изготовления, так и по прочности, жесткости, устойчивости к колебаниям.
Деталь, рассматриваемая в данном дипломном проекте, изготовлена из материала сталь 45 ГОСТ 1050-88. Материал допускает применение высоко производительных режимов резания. Химические свойства материала представлены в таблице 1.1 [1, с. 240.]. Физико-механические свойства материала, показаны в таблице 1.2 [1, с. 255.].
Таблица 1.1 - Химический состав
В процентах
Угле-род, С | Хром, Сr | Крем-ний, Si | Марганец, Мn | Фосс-фор, Р | Медь, Сu | Никель, Ni | Мышьяк, As | Азот, N | Сера, S |
0,42 - 0,50 | £ 0,25 | 0,17- 0,37 | 0,5 - 0,8 | £ 0,035 | £ 0,3 | £ 0,3 | £ 0,08 | £ 0,008 | £ 0,04 |
Таблица 1.2 - Механические свойства
Предел текучести материала, dт | Предел прочности материала при его растяжении, dв | Относительное удлинение после разрыва, d | относительное сужение после разрыва, y | |
Н/мм2
| % | |||
315 | 570 | 17 | 38 |
Анализ технологичности детали имеет целью установление возможности воспроизведения детали. Он осуществляется исходя из возможности обеспечения конструктивной формы детали её габаритов простановки размеров, заданных на размеры допусков, квалитета шероховатости поверхностей известными методами обработки на существующем оборудовании.
Рассмотрим наиболее ответственные поверхности детали: их обработку, точность, шероховатость.
Размер Æ40Н11 (+0.16) выполнен по 11 квалитету в системе отверстия. Шероховатость Ra 12.5 мкм.
Размер Æ32Н7 (+0.025) выполнен по 7 квалитету в системе отверстия. Шероховатость Ra 1.25 мкм.
Размер Æ10Н11 (+0.09) выполнен по 11 квалитету в системе отверстия. Шероховатость Ra 12.5 мкм.
Остальные размеры выполнены по 14 квалитету.
Количественная оценка технологичности конструкции детали характеризуется показателями технологичности. В дипломном проекте количественную оценку конструкции детали производят по следующим вспомогательным коэффициентам.
Коэффициент точности обработки КТО определяем по формуле [2, с. 23.]
КТО = 1 - 1 / АСР, (1.1)
где АСР - средний квалитет обработки изделия.
КТО = 1 - 1 / 12 = 0,9.
Средний квалитет обработки изделия АСР определяем по формуле
АСР = ΣАni / Σni, (1.2)
где ni- число размеров соответствующего квалитета;
А - квалитет обработки.
АСР = 7 × 2 + 11 × 2 + 14 × 7 / 12 = 12,3 ≈ 12,
Так как Кто = 0,9 > 0,8, то деталь является технологичной
Коэффициент шероховатости поверхности КШ определяем по формуле [2, с. 23.]
КШ = 1 - 1 / БСР, (1.3)
где БСР - среднее числовое значение параметра шероховатости.
Среднее числовое значение параметра шероховатости БСР, мкм определяем по формуле
БСР = ΣБni / Σni, (1.4)
|
КШ = 1 - 1 / 12.5 = 0,92 мкм.
где Б - числовое значение параметра шероховатости;
ni - число поверхностей с соответствующим числовым значением параметра шероховатости.
БСР = 1.25 × 1 + 0.63 × 1 + 12.5 × 10 / 12 = 10.5 ≈ 12.5,
Так как КШ = 12.5 =12.5, то деталь является технологичной
Все поверхности детали открыты для доступа к ним режущего инструмента. Отсюда делается вывод, деталь изготавливается из материала, сталь 45 ГОСТ 1050-88. С точки зрения механической обработки деталь можно считать технологичной так как все элементы конструкции детали легко обработать без затруднений, как на универсальном так и на специальном оборудовании.
Анализ типа оборудования предусмотренного технологическим процессом
Металлорежущие станки в соответствии с видами обработки делятся на десять групп: каждую группу подразделяют на десять типов, а также каждый тип – на десять типоразмеров.
Группы станков определяются технологическим назначением станка (токарные, сверлильные и т. д.); типы – расположением рабочих органов, количеством главных рабочих органов, степенью автоматизации.
Абразивно-отрезной станок
Основное назначение абразивно-отрезного станка - поперечная резка различного металлопроката. Такие станки способны работать с заготовками, как из чёрного, так и цветного металла, практически любой формы, что делает их достаточно универсальными.
Современная строительная и промышленная отрасли требуют использования сложных металлоконструкций, а также разнообразных материалов - композитных, конструкционных, отделочных, теплоизоляционных и т.д. Нарезка с помощью абразивно-отрезных станков является одним из основных видов формообразующей обработки. Она позволяет получать без особых трудностей детали достаточно высокой точности с соблюдением необходимых размеров и прочих параметров.
Технические характеристики станка 8В262
8В262 - Автомат абразивно-отрезной
Станки 8в262 применяются для разрезки дисковыми пилами черных металлов в заготовительных цехах машиностроительных предприятий.
Начало производства: 1981
Точность: Н
Максимальный диаметр заготовки, мм 150
Длина отрезаемой заготовки максимальная, мм 1000
Потребляемая мощность, кВт: 55
Размеры (Д_Ш_В), мм: 2270_1992_2100
Вес станка с выносным оборудованием, кг: 3680
|
Токарный полуавтомат
Токарный станок — станок для обработки резанием (точением) заготовок из металлов и др. материалов в виде тел вращения. На токарных станках выполняют обточку и расточку цилиндрических, конических и фасонных поверхностей, нарезание резьбы, подрезку и обработку торцов, сверление, зенкерование и развёртывание отверстий и т. д. Заготовка получает вращение от шпинделя, резец — режущий инструмент — перемещается вместе с салазками суппорта от ходового вала или ходового винта, получающих вращение от механизма подачи.
В состав токарной группы станков входят станки выполняющие различные операции точения: обдирку, снятие фасок, растачивание и т. д.
Значительную долю станочного парка составляют станки токарной группы. Она включает, согласно классификации Экспериментального НИИ металлорежущих станков, девять типов станков, отличающихся по назначению, конструктивной компоновке, степени автоматизации и другим признакам. Станки предназначены главным образом для обработки наружных и внутренних цилиндрических, конических и фасонных поверхностей, нарезания резьб и обработки торцовых поверхностей деталей типа тел вращения с помощью разнообразных резцов, свёрл, зенкеров, разверток, метчиков и плашек.
Применение на станках дополнительных специальных устройств (для шлифования, фрезерования, сверления радиальных отверстий и других видов обработки) значительно расширяет технологические возможности оборудования.
Токарные станки, полуавтоматы и автоматы, в зависимости от расположения шпинделя, несущего приспособление для установки заготовки обрабатываемой детали, делятся на горизонтальные и вертикальные. Вертикальные предназначены в основном для обработки деталей значительной массы, большого диаметра и относительно небольшой длины.
Моечная машина
Моечная машина не только экономит время, которое необходимо уделять мойке посуды, но и уберегает руки от воздействия вредных химических веществ, которые содержатся в моющих средствах. Такие устройства бывают самых разных типов и моделей. Есть техника, которая предназначена для ресторанов, школ и детских садиков, для дома или промышленных предприятий. Среди ее преимуществ стоит выделить невысокую стоимость, компактность и удобство в использовании.
|
Моечная машина считается профессиональной бытовой техникой, которая есть практически в каждом доме. Перед выбор такого оборудования необходимо подумать, на какое количество посуды вы рассчитываете. Есть машины, которые предназначены для большого количества посуды, а есть – для маленького. Каждая домохозяйка сможет выбрать себе красивую и компактную технику, которая позволит тратить меньше времени на уборку и мытье.
Надо обращать также внимание на тип установки: есть машины, для которых необходимо много воды или высокое давление потока. Не стоит забывать и про функциональность этой техники, с помощью которой можно мыть посуду при разной температуре и с различной скоростью.
Моечная машина для деталей
Применяется на многих предприятиях. Такое оборудование помогает сэкономить время и силы. Часто в сервисах или на предприятиях появляется необходимость помыть какие-то детали. Для этого лучше всего использовать такую машину. Моечная машина для деталей стоит не дорого и прекрасно справляется со своим предназначением.
Машины промывают детали в горячем растворе технических моющих средств. С помощью такой техники возможны следующие методы обработки: пассивация, обычное или фосфатное обезжиривание, подготовка к окраске, антикоррозийная защита.
Моечные машины высокого давления
Моечные машины высокого давления используются для того, чтобы вымывать поверхности или различные детали с помощью давления струи воды. Они могут относиться к высокому и среднему классу. Моечная машина среднего класса применяется, как правило, в бытовых целях. Эта универсальная техника помогает содержать в чистоте автомобиль, гараж или мастерскую, сад и его дорожки, дом и внутренний двор. В ней есть полезная функция, с помощью которой производится забор воды из специальных емкостей или открытых водоемов.
Она предназначена для того, чтобы профессионально вымывать территорию автомастерских или производств. С помощью такой техники можно эффективно вымыть разнообразные поверхности и детали, к тому же данная машина имеет множество насадок и режимов работы. С её помощью можно осуществить грубую очистку поверхности с приевшейся грязью или аккуратную очистку поверхности, которая просто нуждается в деликатном уходе.
Моечная машина высокого давления используется в самых разнообразных сферах деятельности. Она помогает избавиться от цемента, мела, строительного раствора, мазута, водорастворимой краски и других веществ. Такое оборудование может подавать напор воды с давлением около 160 бар.
|
Ее производительность составляет около 600 литров воды в час.
Такие машины отличаются удобной и компактной конструкцией, в которой предусмотрены колеса для легкого передвижения по территории. К тому же это устройство обладает небольшим весом и компактными размерами.
В этой машине есть также специальная секция сушки, в которой стекла высыхают. На них через специальные воздушные сопла подается под высоким давлением воздух с помощью мощных вентиляторов. После окончания всех этапов мойки стекла попадают на выходной стенд, откуда их достает оператор.
Внутришлифовальный 3А227АФ2
Внутришлифовальные станки предназначены для шлифования внутренних поверхностей вращения. Применение внутришлифовального станка является одним из прогрессивных методов обработки металлов резанием. Само по себе шлифование означает процесс обработки заготовок резанием с помощью инструментов - кругов, состоящих из абразивного материала. В машиностроении наиболее часто применяют следующие виды шлифования:
круглое наружное,
круглое внутреннее
плоское.
Над круглым внутренним работает внутришлифовальный станок. Действие осуществляется благодаря продольной подачи шлифовального круга, возможно, заготовки, а также обработка врезанием.
Внутришлифовальный станок относится к шлифовальной группе станков, которые предназначены для изготовления деталей с малыми отклонениями формы, размеров, малыми параметрами шероховатости поверхности и отличаются высокой производительностью.
Данный вид оборудования применяются для обработки внутренних поверхностей вращения. Подобный вид станка используется в работе по шлифовке отверстий.
Тиски
Тиски представляет собой пару параллельных губок, одна из которых обычно неподвижна, а вторая прижимается к детали при помощи винта. Тиски изготавливаются из различных материалов, слесарные чаще всего из металла, столярные из дерева.
Основные типы тисков:
слесарные,
станочные с ручным и механизированным приводом,
ручные (применяются, например, в ювелирном деле удерживаемые одной рукой и предназначенные для фиксации маленьких предметов,
столярные (часть столярного верстака).
Трехкулачковый патрон
Трехкулачковый самоцентрирующий патрон с ручным зажимом самое
распросраненное устройство для крепления деталей на токарных
станках. С многообразием токарных патронов можно ознакомится на
сайтах их производителей и дилеров.
Мы будем рассматривать лишь небольшим размерный ряд трехкулачковых самоцентрирующих патронов от разных производителей.
Обладая мощным, но чувствительным механизмом, патрон позволяет
надежно крепить детали с высокой точностью их центрирования,
как для выполнения высокорежимной обработки, так для более тонких
работ. Основные детали трехкулачкового патрона с ручным зажимом:
корпус из чугуна или стали, который у этого патрона состоит из двух частей, а данной конструкции из одной. Во внутренней части корпуса патрона находится деталь один торец которой выполнен в форме конической шестерни, а на другом торце нарезана архимедова спираль. Эта деталь называется спиральный диск, который еще называют технически-жаргонно -
архимедовой спиралью, спиралью, улиткой, планетаркой.
Малых конических шестерен с гнездом для ключа в патроне может быть от одной до нескольких.
Как правило комплектов кулачков у патрона два - прямые кулачки для крепления деталей на сжим и разжим и обратные кулачки для крепления на сжим деталей с большими диаметрами. Многие производители вводят в стандартный набор патрона, или поставляют отдельно еще и комплект кулачковых реек на которые могут крепиться произвольные по формам насадки из незакаленной стали.
Эти сменные насадки принято называть сырыми кулачками.
По точности центрирования патроны могут быть разных классов. Класс 1 по стандартам DIN или класс "А" по ГОСТу самый высокие по точности. Кроме трехкулачковых самоцентрирующих патронов, существуют патроны,также самоцентрирующие, но с двумя, четырьмя и шестью кулачками. Около одного из гнезд для ключа на патроне стоит метка "0". Для бОльшей видимости это гнездо обычно метится станочником дополнительно. Чтобы центрирование патрона было более стабильным, зажим патрона выполняется только одним этим гнездом для ключа. Другие гнезда могут использоваться для менее ответственных по точности центрирования зажимов. Кулачки патрона, например, диаметром 250мм при максимальном усилии рук развивают давление до 4,5 тн. Несоразмерное усилие зажима патрона может привести к браку детали, выраженному в смятии ее чистовой поверхности, деформации тонкостенной детали, а может и просто сломать хрупкий материал детали.
Другая сторона несоразмерности усилия, а именно недостаточно надежный зажим может привести к вырыванию детали из кулачков силами резания или к провороту детали в кулачках.
Поэтому следует применять различные усилия зажатия деталей в зависимости от условий их обработки.
Заводские ключи имеют равноплечий рычаг. Многие станочники делают этот рычаг неравноплечим, а именно под левую руку более короткое плечо рычага, а более длинный рычаг - для правой руки. Это дает выигрыш в силе зажатия при меньшей нагрузке на руки.
Менять на ключе рычаг не более длинный и использовать для удлинения рычага трубу трубу не допустимо, так как это может к излому деталей патрона.
Эксплуатировать патрон, в диапазонах раствора кулачков, при которых спираль диска даже частично выходит из зацепления с гребенками кулачков, нельзя во избежании излома гребенок или спирали. При необходимости следует применить кулачки другого вида - обратные или специальные сырые.
Усилия руки или рук на ключ можно подразделить на такие уровни:
1. кистевое усилие без рычага- зажим одной рукой, с приложением ее у оси ключа.
2. кистевое усилие на рычаг ключа- одна рука на коротком плече ключа почти без усилия, вторая рука действует на длинный рычаг ключа усилием открытой кисти.
3. локтевое усилие - одна рука действует, как контр-опора, другая рука, согнутая в локте, воздействует на длинный рычаг ключа. Это усилие наиболее применяемое и имеет довольно большой силовой диапазон. Зажим- отжим может производится, как рывком, так и без рывка.
4. плечевой зажим - предельный по силе, когда одна рука действует, как контр-опора, а вторая, не согнутая в локте, прикладывается к длинной стороне рычага. Каждый из вышеизложенных уровней можно в свою очередь подразделить на легкие, умеренные или предельные. Плечевые зажимы производится силами только поворота торса, рывком или плавно. Отжимы следует делать не давлением рук, с участием сил своего веса, а коротким, энергичным толчком с использованием люфтов в ключе и механизме патрона для разгона движения. Особо ваше заострю внимание, что при зажатиях и отжатиях рывком и толчком использование веса также недопустимо, во избежании неконтролируемых потерь равновесия при срыве или поломке ключа. Рывки и толчки при зажиме и отжиме нужно делать только силами рук и поворота торса. Отжим толчком применяется, в частности, когда надо снять основной натяг зажима для того, чтобы оставшийся отжим выполнить одной рукой, когда вторая занята Технику вращения ключа одной левой рукой, нужно выработать, так как этот навык полезен при установке тяжелых деталей силами одного станочника.
Специальные оправки
Специальные оправки выгодны для обработки заготовок конкретного типоразмера в условиях массового и крупносерийного производств. Кулачки специальных оправок называют постоянными, их заменяют строго комплектно по мере изнашивания или в случае утраты части кулачков, центрирующий зажимной механизм (ЦЗМ) специальных кулачковых оправок сравнительно компактный.
Специальная оправка для насадных зенкеров и разверток, применяемая при обработке отверстий под шатунные болты (фиг. Этим достигается быстрое удаление стружки, образующейся при резании металла. Уплотнение подвижного соединения оправки с кольцом и фланцами производится мягкой набивкой.
Специальная оправка для насадных цековок, применяемая для обработки мест под головки шатунных болтов
Специальная оправка и стойка для контроля сборочного размера ведущей шестерни главной передачи.
При проектированииспециальных оправок следует предусматривать, чтобы длина оправки была минимально необходимой для оое. Фреза плотно насаживается на оправку. Перед тем кагс зажать фрезу, оправку устанавливают в подшипник поддерживающего кронштейна Количество установочных колец должно быть минимальным во избежание дополнительных погрешностей.
При отсутствииспециальной оправки для постановки вала ротора в сальники вал из сальников не вынимать.
Одновременно наспециальной оправке необходимо проверить взаимное расположение стрелки по отношению к рамке.
Шайбу с помощьюспециальной оправки шлифуют до диаметра 20 мм, затем на плоскошлифовальном станке в специальной призме симметрично оси наружной поверхности шайбы шлифуют паз с припуском на доводку, которую выполняют с учетом прессовой посадки выступа линейки. Сборку линейки с шайбой производят следующим образом. Снимают фаски по контуру выступа линейки, а также по контуру паза шайбы с обеих сторон, после чего шайбу насаживают на выступ линейки, выставляют на размер 100 мм между осями шайбы и отверстия линейки и место соединения запаивают третником.
Секция наматывается наспециальную оправку. Поэтому при номинальных напряжениях на конденсаторе в 15 - 20 кВ и выше конденсаторы составляют из нескольких последовательно соединенных секций или групп секций.
Шарошку устанавливают наспециальную оправку, которая крепится к неподвижному башмаку машины. Электрод коническим концом вставляют в подвижный башмак машины. В цилиндрическое отверстие электрода помещают армированный зубок. Приварка выполняется при постоянном усилии Р на электроде.
Деталь устанавливается наспециальную оправку и закрепляется, после чего подрезают торец буртика с внутренней стороны на размер 7 5 02лш; протачивают наружный диаметр вкладыша до размера 80С и подрезают второй внутренний торец бурта до размера 48А между ними.
Вкладыш надевается наспециальную оправку и закрепляется. Разметочная риска должна находиться по центру прореза диска приспособления. После разрезки вкладыша с одной стороны оправка поворачивается на 180 и производится разрезка его с другой стороны.
Грузоподъемные машины
Домкраты - простейшие грузоподъемные механизмы, применяемые в основном при ремонтных и монтажных работах. Высота подъема грузов составляет 0,15 - 0,7 м. Используются в виде толкателей, т.е. подъем грузов осуществляется без грузозахватных устройств. Некоторые домкраты могут производить горизонтальное перемещение поднятых средств на небольшое расстояние. В зависимости от конструкции домкраты делятся на реечные, винтовые, гидравлические.
Реечные домкраты с ручным приводом (грузоподъемностью 0,5 - 10 т) обладают существенным недостатком - невозможностью установки груза на высоте с большой точностью.
Винтовые домкраты имеют ручной привод и электрический. Винтовой домкрат состоит из корпуса, винта, головки, шарнирно соединенной с винтом, закрепленной в корпусе гайки и приводной рукоятки с собачкой кранового механизма. При качательных движениях рукоятки храповое колесо вместе с винтом поворачивается и винт выдвигается из корпуса. Самопроизвольное опускание груза предотвращается наличием самотормозящей резьбы.
Недостатки: 1) низкий КПД - 0,3 - 0,4; 2) малая скорость опускания груза.
Гидравлические домкраты. Привод - ручной или машинный. Преимущества - плавность хода и точная установка по высоте поднимаемого груза, КПД - 0,15 - 0,8, грузоподъемность - до 750 т. Недостаток - малая скорость подъема (0,001 - 0,002 м/с) при ручном приводе. Гидравлический домкрат с ручным приводом состоит из гидроцилиндра, плунжера, ручного поршневого насоса с приводной рукояткой и бачка для масла.
Подъем груза осуществляется поршнем, который перемещается за счет подачи масла. Опускание груза производится путем соединения полости гидроцилиндра с бачком с помощью вентиля. Скорость регулируется степенью открытия спускного вентиля.
Лебедки (тали). Лебедки - грузоподъемные устройства для подъема и перемещения грузов тяговым органом (канат или цепь), навиваемым на барабан. Привод - ручной или машинный. Они используются в грузоподъемных кранах и подъемниках как механизмы подъема груза и передвижения крановых тележек.
Тали - компактные подъемные лебедки, имеющие ручной и механический привод и подвешиваемые к балкам или специальным тележкам, перемещающимся по подвесному пути (монорельсу). Применение - внутри и межцеховое перемещение грузов, обслуживание станков, поточных и автоматических линий и т.п.
Рис. Таль с ручным приводом: 1 - пластинчатая шарнирная цепь; 2 - собачка тормоза; 3 - крюк; 4 - приводное колесо; 5 - дисковый тормоз; 6 - храповое колесо тормоза; 7 - сварная цепь
Грузоподъемные краны предназначены для подъема, перемещения, опускания груза с помощью грузозахватного устройства. Это универсальные грузоподъемные машины, состоящие из остова (в виде металлоконструкции) и крановых механизмов, грузозахватных устройств. Грузозахватные устройства применяются как универсальные - крюки, петли для непосредственного принятия груза, так и специальные. Для штучных грузов (ящиков, бочек, мешков, листов и т.д.) - клещевые, эксцентриковые и другие захваты, грейферы - для подачи сыпучих грузов, электромагниты - для транспортирования грузов из стали и чугуна, вакуумные захваты - для транспортирования листового материала, а также коробок, ящиков и т.п.
Наибольшее применение получили стационарные рельсовые мостовые и поворотные стреловые краны, краны-штабелеры.
Мостовые краны применяются для внутрицеховых и внутрискладских погрузочно-разгрузочных работ. Схема двухбалочного мостового крана опорного типа состоит из главных и концевых балок, составляющих мост крана. В концевых балках моста укреплены ходовые колеса крана на рельсы, которые закреплены на подкрановых балках, установленных на колоннах цеха или эстакадах, механизмы подъема груза и передвижения тележки смонтированы на крановой тележке. К мосту прикреплена кабина крановщика. Питание электроэнергией механизмов крана производится с помощью специальных токоведущих шин. Основная характеристика двухбалочных мостовых кранов - пролет, он составляет 10,5 - 34,5 м; грузоподъемность - 5 - 100 т. При грузоподъемности 1 - 5 т применяют однобалочные краны (кран-билки) с электроприводом. Применяются также опорные однобалочные и двухбалочные мостовые краны с ручным приводом грузоподъемностью от 3,2 до 20 т.
В стреловых (консольных) кранах груз подвешен к балкам на концевой части стрелы или на грузовой тележке, перемещающейся по стреле, и находится вне опорного контура крана, что обуславливает возникновение опрокидывающего момента.
Кран закреплен к стене с помощью двух опор - верхней и нижней, воспринимающих горизонтальные и вертикальные нагрузки. Металлоконструкция крана имеет Г-обрязную форму, на которой расположены механизмы подъема груза, передвижения тележки и попорота крана. По стреле перемещается тележка, установленная на ролики с грузозахватным устройством с помощью каната, наматываемого на барабан перемещения тележки. При применении электротали в качестве верхней балки используется монорельс.
Штабелеры. Штабелеры являются разновидностью подъемно-транспортного оборудования, и предназначены исключительно для работы в условиях складских помещений. В соответствии с этим целевым назначением к этой технике предъявляется ряд специфических требований:
· минимальные размеры, позволяющие работать в стесненных условиях (узкие проходы);
· высокая маневренность, способность разворачиваться на месте, обеспечивая минимальные радиус поворота и размеры рабочего коридора;
· способность работать с грузом на большой высоте, высокая остаточная грузоподъемность.
Подобные требования приводят к очень специфичной компоновке этих складских машин. Например, при отсутствии необходимости работы на неровном грунте колеса, как правило литые, имеют небольшой диаметр, дорожный просвет также очень мал. Для достижения высокой маневренности и упрощения конструкции ходовой части обычно используется одно-единственное ведущее колесо, являющееся также и управляемым. Располагается оно под корпусом так, чтобы исключить возможность травмирования персонала, что важно при работе в тесноте. Благодаря такой конструкции машина буквально ходит за ведущим колесом в любую сторону и может разворачиваться с минимальным радиусом почти в пределах собственных габаритов.
Кроме того, условия эксплуатации позволили вынести опорные колеса далеко вперед, за мачту, что дало возможность принципиально освободиться от противовеса. Благодаря этому проекция центра тяжести груза находится на минимальном расстоянии от опорных точек машины (практически в пределах треугольника устойчивости).
Погрузчики. Погрузчик -- специальное транспортное средство, предназначенное для поднятия, переноса и складирования различных грузов с помощью вил или других рабочих приспособлений, -- продолжает рассказ Максим Лебедев.
Погрузчики с противовесом классифицируются по следующим признакам:
· грузоподъемность;
· расположение подъемного устройства;
· тип привода;
· число опорных колес.
По грузоподъемности вилочные погрузчики могут быть от 500 кг до 16 т.
Портовые погрузчики могут поднимать груз даже до 52 т.
По расположению подъемного устройства погрузчики бывают фронтальные и боковые. У фронтальных погрузчиков рабочее приспособление расположено спереди. По типу рабочего приспособления фронтальные погрузчики разделяют на вилочные и ковшовые. У боковых погрузчиков подъемное устройство расположено сбоку. Такие погрузчики широко используются на складах с небольшими межстеллажными расстояниями и при складировании длинномерных грузов.
По типу привода вилочные погрузчики с противовесом бывают дизельными, газобензиновыми (газовые, бензиновые) и электрическими.
Электрические погрузчики различаются также по числу опорных колес: бывают четырех- и трехопорные электропогрузчики. Четырехопорные погрузчики более устойчивы, а характеристики их остаточной грузоподъемности выше, чем у трехопорных. Трехопорные электропогрузчики более маневренны: они способны передвигаться в более узких рабочих коридорах, чем четырехопорные.
Лифты грузовые - это подъемники стационарного типа, предназначенные для вертикального перемещения тарно-штучных грузов между этажами на предприятиях оптово-розничной торговли и общепита. Они выпускаются следующего типа: малые грузоподъемностью 40, 100 и 250 кг, грузовые выжимные грузоподъемностью от 500 до 3200 кг, и грузовые тротуарные грузоподъемностью 500 и 630 кг.
Выжимные - это лифты, у которых привод расположен внизу и перемещение кабины осуществляется за счет действия силы снизу вверх. Тротуарные лифты предназначены для установки в подвальном помещении, находящемся под тротуаром хозяйственных дворов, складов, магазинов, предприятий общепита.
Автопогрузчики предназначены для работы на открытых площадках в целях экологической безопасности и техники безопасности, так как они имеют привод от двигателя внутреннего сгорания. Конструкция основных узлов автопогрузчика выполнена на базе узлов автомобиля.
Электропогрузчики имеют привод от электродвигателя с питанием от аккумуляторной батареи. Они более экологичны, поэтому применяются для выполнения работ и в закрытых помещениях - цехах, складах.
Рабочее оборудование погрузчиков однотипно - грузоподъемник с набором грузозахватных органов (вилы, челюстные захваты, ковши и др.). Грузоподъемник имеет раму, по которой перемещается каретка с грузозахватным органом, имеющим поворот вокруг горизонтальной оси на угол 90 - 360 градусов. Привод грузовой каретки обычно гидравлический (от гидроцилиндров). Грузоподъемность погрузчиков составляет 0,63 - 45 т, максимальная высота подъема 4,5 м.
наибольшей компактностью, так как имеют возможность складываться в пределах своего основания.
По способу управления роботы делятся на программные, адаптивные и интеллектуальные.
Программные - работают по заранее заданной программе - роботы первого поколения.
Адаптивное управление - работа по заранее заданному алгоритму управления. Роботы второго поколения. Они имеют средства очувствления (техническое зрение, устройство ориентации, датчики усилий и т.д.), реагируют на изменение обстановки и меняющиеся работы, разрабатывают программу управления по обходу препятствий, выбору необходимых деталей и т.д.
Интеллектуальное управление - наряду с вышеприведенными качествами имеют внутреннюю систему самообучения, которая выбирает и запоминает наиболее эффективные программные приемы выполнения рабочих действий, т.е. такая развитая система управления наделяет робот искусственным интеллектом. Это роботы 3-го поколения.
Разработка участка механической обработки детали зубчатого колеса со шпоночным пазом
|
|
Адаптации растений и животных к жизни в горах: Большое значение для жизни организмов в горах имеют степень расчленения, крутизна и экспозиционные различия склонов...
Особенности сооружения опор в сложных условиях: Сооружение ВЛ в районах с суровыми климатическими и тяжелыми геологическими условиями...
Опора деревянной одностоечной и способы укрепление угловых опор: Опоры ВЛ - конструкции, предназначенные для поддерживания проводов на необходимой высоте над землей, водой...
История развития пистолетов-пулеметов: Предпосылкой для возникновения пистолетов-пулеметов послужила давняя тенденция тяготения винтовок...
© cyberpedia.su 2017-2024 - Не является автором материалов. Исключительное право сохранено за автором текста.
Если вы не хотите, чтобы данный материал был у нас на сайте, перейдите по ссылке: Нарушение авторских прав. Мы поможем в написании вашей работы!