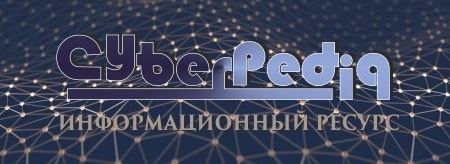
Семя – орган полового размножения и расселения растений: наружи у семян имеется плотный покров – кожура...
Биохимия спиртового брожения: Основу технологии получения пива составляет спиртовое брожение, - при котором сахар превращается...
Топ:
Установка замедленного коксования: Чем выше температура и ниже давление, тем место разрыва углеродной цепи всё больше смещается к её концу и значительно возрастает...
Организация стока поверхностных вод: Наибольшее количество влаги на земном шаре испаряется с поверхности морей и океанов...
Интересное:
Средства для ингаляционного наркоза: Наркоз наступает в результате вдыхания (ингаляции) средств, которое осуществляют или с помощью маски...
Распространение рака на другие отдаленные от желудка органы: Характерных симптомов рака желудка не существует. Выраженные симптомы появляются, когда опухоль...
Влияние предпринимательской среды на эффективное функционирование предприятия: Предпринимательская среда – это совокупность внешних и внутренних факторов, оказывающих влияние на функционирование фирмы...
Дисциплины:
![]() |
![]() |
5.00
из
|
Заказать работу |
|
|
Детали машин
ПЛАКАТ 3
Основы проектирования ДМ
Курс «Детали машин» посвящен изучению основ расчета и конструирования деталей и узлов общего назначения, встречающихся в различных механизмах и машинах.
Целью курса ДМ - является развитие инженерного мышления с точки зрения изучения современных методов, правил и норм расчета и конструирования деталей и сборочных единиц машин общего назначения (валы зубчатые колеса редуктора и т.д.).
Задачи курса ДМ - привить навыки расчета и конструирования типовых деталей и узлов машин, научить рационально, выбирать материал и форму деталей, выполнять расчеты на прочность жесткость, устойчивость, износостойкость и т.д. исходя из заданных условий работы машины.
Основной критерий, которому должны соответствовать все инженерные решения – здравый смысл. Решение не соответствующее данному критерию заведомо не верно.
Машина – устройство для преобразования энергии или движения, накопления и переработки информации.
Механизм – часть машины, в которой рабочий процесс реализуется путем выполнения определенных механических движений.
Деталь – элемент конструкции, изготовленный из материала одной марки без применения сборочных операций (болт, гайка, вал и т.д.).
Узел (сборочная единица) – совокупность деталей, соединенных на предприятии-изготовителе сборочными операциями и предназначенных для совместной работы (коробка передач, муфта, редуктор и т. д.).
Основные требования, которым должны удовлетворять детали и узлы, как и машины в целом:
1 Работоспособность; 2 Надежность; 3 Технологичность;
4 Экономичность; 5 Эстетичность.
Работоспособность - состояние объекта, при котором он способен выполнять заданные функции, сохраняя значения заданных параметров в пределах, установленных нормативно-технической документацией. (Феррари V< 320 км/час).
|
Надежность - свойство объектов сохранять работоспособность в течении заданного промежутка времени или требуемой наработки. Например: срок службы подшипников - 20 тыс. часов.
Технологичными называют детали и узлы, требующие минимальных затрат средств, времени и труда в производстве, эксплуатации и ремонте.
Работоспособность и надежность деталей машин оценивают следующими основными критериями:
1 Прочность; 2 Жесткость; 3 Износостойкость;
4 Устойчивость; 5 Теплостойкость; 6 Виброустойчивость.
Износостойкость - способность детали сохранять необходимые размеры трущихся поверхностей в течении заданного срока службы. (Она зависит от свойств выбранного материала, термообработки и шероховатости поверхностей, значения давлений или контактных напряжений, скорости скольжения и условий смазывания, режима работы и т.д. Износ уменьшает прочность деталей, изменяет точность и характер соединения.)
В большинстве случаев расчеты деталей на износостойкость ведут по допускаемым давлениям [P], установленным практикой (расчеты подшипников скольжения, цепных передач и т.д.):
P ≤ [ P ].
Машиностроительные материалы
ПЛАКАТ 4
Выбор материала и термообработки деталей машин определяется конструктивными соображениями (обеспечение надежности), технологическими (единичное, серийное, массовое производство) и экономическими.
Для изготовления деталей применяют черные и цветные металлы, пластмассы и другие не металлические материалы.
Черные металлы являются основными машиностроительными материалами. К ним относятся: стали - железоуглеродистые сплавы с содержанием углерода до 2,14%. и чугуны - железоуглеродистые сплавы с содержанием углерода более 2,14%, обычно до 3,8%..
Стали подразделяются на углеродистые и легированные - содержащие специальные присадки (примеси): хром никель и другие.
|
Углеродистая сталь обыкновенного качества изготовляется по ГОСТ 380 - 88 обозначается буквами: Ст0,Ст1, Ст3,Ст5 и т.д. Применяют для термически не обрабатываемых деталей (прокатный профиль, корпуса, крепеж и т.д.)
Углеродистая качественная конструкционная сталь изготовляется по ГОСТ 1050 – 88 обозначается сталь 10, сталь 45 где числа 10 и 45 показывают содержание углерода в сотых долях процента 0,10% и 0,45% соответственно. Содержание серы в качественной стали S≤0,04%, фосфора Р≤0,035-0,04%.
Качественную углеродистую сталь применяют для деталей машин подвергаемых термообработке (зубчатые колеса, валы и т.д.)
ПЛАКАТ 5
Для улучшения свойств сталей применяют легирующие присадки:
В – вольфрам; Г – марганец; Д – медь; М – молибден;
Н – никель; Р – бор; С – кремний; Т – титан;
Х – хром; Ф – ванадий; Ю - алюминий.
Процентное содержание присадок указывают цифрами после буквы: 12Х2Н4А => 0,12% углерода 2% хрома, 4% никеля. Буква А обозначает высококачественную легированную сталь (содержание фосфора Р≤0,025% и серы S≤0,025%), 30ХГСА.
ПЛАКАТ 6
Для придания стали определенных механических свойств применяют термическую и химико-термическую обработку, а также механическое упрочнение.
Термическая обработка заключается в нагреве до требуемой температуры с определенной скоростью, выдержке при этой температуре в течение определенного времени и охлаждения с заданной скоростью
Основные виды ТО:
Отжиг, характеризуется медленным охлаждением вместе с печью, используют для понижения твердости и снятия остаточных напряжений в деталях получаемых литьем, сваркой и обработкой давлением.
Нормализация – характеризуется охлаждением на воздухе, применяют для улучшения механических свойств и обрабатываемости резанием.
Закалка – отличается высокой скоростью охлаждения (в воду, масло, растворы солей) применяют для получения однородной мелкозернистой структуры стали с высокой твердостью, прочностью, износостойкостью но пониженной пластичностью и более трудной обрабатываемостью резанием.
Улучшение – закалка и высокий отпуск, применяют для повышения, предела прочности, предела текучести, относительного сужения и особенно ударной вязкости.
|
Химико-термическая обработка – насыщение поверхностных слоев при высокой температуре: углеродом – цементация, углеродом и азотом – цианирование (нитроцементация), азотом – азотирование на глубину 0,2 – 1 мм. ХТО применяется для повышения твердости и износостойкости поверхности деталей.
Механическое (деформационное) упрочнение (наклеп) осуществляют дробеструйной обработкой, волочением, накатыванием роликами или шариками и другими способами.
ПЛАКАТ 7
Чугуны. Имеют высокие литейные и не высокие пластические свойства по сравнению со сталями. Различают серый чугун, белый и ковкий.
Серый чугун ГОСТ 1412–85 основной литейный машиностроительный материал из него изготавливают (корпуса редукторов, станины и т.д.). Марки СЧ 12-28, СЧ 15-32, СЧ 28-48. СЧ 15-32 – первые две цифры это σвр=15 кгс/мм2 (150 МПа) – предел прочности при растяжении, σви=32 кгс/мм2 (320 МПа) – предел прочности при изгибе.
Серый (модифицированный) высокопрочный чугун по ГОСТ 7293 – 85. Применяют для более ответственных деталей. Марки ВЧ 38-17, ВЧ 42-12, ВЧ 50-2. ВЧ 38-17 первые две цифры это σвр=38 кгс/мм2 (380 МПа) – предел прочности при растяжении, вторые δ=17% - остаточное удлинение при разрыве.
Ковкий чугун (ГОСТ 1215-79) – применяют для литых деталей, на которые могут действовать ударные нагрузки. Например, в текстильном, сельском хозяйстве и железнодорожном машиностроении. КЧ 30-6, КЧ 38-8, КЧ 37-12, первые две цифры это это σвр=37 кгс/мм2 (370 МПа) – предел прочности при растяжении, вторые δ=12% - остаточное удлинение при разрыве.
Белый чугун (ГОСТ 7769-75) – применяют редко для деталей работающих при высоких температурах (колосники) и в химически агрессивных средах.
ПЛАКАТ 9
Сплавы цветных металлов.
Наибольшее применение имеют сплавы на основе меди, алюминия, цинка. Медные сплавы разделяют на латуни и бронзы.
Латунь – сплав меди и цинка (+ дополнительные компоненты) Обозначение Л – латунь: Л68 (68% меди, остальное –цинк), ЛК 80-3 (кремнистая латунь – 80% меди, 3% кремния, остальное –цинк).
Латунь обладает хорошим сопротивлением коррозии, антифрикционными свойствами, электропроводностью, хорошими технологическими свойствами (хорошо отливается и штампуется). Применяют для изготовления проволоки, гильз, труб, арматуры. Стоимость латуни в 5 раз больше стали.
|
Бронза – все медные сплавы кроме латуни. Они бывают оловянистые, свинцовые, алюминиевые, бериллиевые и другие. Маркируют бронзы буквами «Бр», затем обозначают входящие в нее элементы (кроме меди) и их содержание в процентах. Например, БрОЦ4-3 (4% олова, 3% цинка); БрАЖ 9-4Л (9% алюминия, 4% железа, Л – литейная).
Бронза обладает высокими антифрикционными свойствами. Ее используют в подшипниках скольжения, червячных и винтовых колесах.
Кроме вышеуказанных материалов в машиностроении используют:
Алюминиевые сплавы
– литейные АЛ7; АЛ8; АЛ21;
– деформируемые АМц; АМг6.
– дуралюмин Д1, Д16 (медь 3,8 –4,9 %);
– силуминыАЛ 2, АЛ 4 (кремний 8-13%).
Магниевые сплавы
МЛ5, МЛ6 - литейные;
МА1, МА14 - деформируемые.
Титановые сплавы
ВТ5, ОТ4, ВТ6, ВТ14, ВТ22.
Не металлические материалы:
пластмассы, композиционные материалы (стеклопластик), резина, стекло керамика.
ПЛАКАТ 9
ПЛАКАТ 10
Допуски и посадки.
Для изготовления и ремонта машин большое значение имеет взаимозаменяемость деталей и узлов. Взаимозаменяемыми называются такие детали, которые могут занимать свои места в машине без дополнительной обработки (например, подшипники).
Взаимозаменяемость ДМ обеспечивается системой допусков и посадок. ЕСДП (ГОСТ 25346 - 82 и ГОСТ 25347 - 82).
Основные термины и обозначения ЕСДП.
Номинальным размером называют размер изделия, полученный по расчету или выбранный по конструктивным соображениям. Изготовленные изделия всегда имеют некоторые отклонения от номинальных размеров. Для того чтобы изделие отвечало своему целевому назначению, его размеры должны выдерживаться между двумя допустимыми предельными размерами, разность которых образует допуск. Зону между наибольшим и наименьшим предельными размерами называют полем допуска.
ПЛАКАТ 11
Поля допусков
ПЛАКАТ 12
К различным деталям и их соединениям предъявляют неодинаковые требования в отношении точности. Поэтому система допусков содержит 19 квалитетов: 01, 0, 1, 2...17 расположенных в порядке убывания точности. Например, для размера 100 мм допуск по квалитету 01 составляет – 1 мкм, по 7 квалитету – 35 мкм, а по 14 квалитету 1000 мкм. Квалитеты 6, 7, 8 - основные в современном производстве.
Характер соединения деталей называют посадкой. Характеризует посадку разность размеров деталей до сборки. Посадки могут обеспечивать в соединении зазор S или натяг N. Переходные посадки могут иметь или зазор S, или натяг N: они характеризуются наибольшим зазором Sмакс и наибольшим натягом Nмакс
|
Разнообразные посадки удобно получать, изменяя положение поля допуска или вала, или отверстия, оставляя для всех посадок поле допуска одной детали неизменным. Деталь, у которой положение поля допуска остается без изменений и не зависит от вида посадки, называют основной деталью системы. Если этой деталью является отверстие, то соединение выполнено в системе отверстия, а если основной деталью является вал - в системе вала. У основного отверстия нижнее отклонение ЕJ=0, а у основного вала верхнее отклонение es=0. Поле допуска направленно в тело деталей. Основные отклонения обозначают буквами латинского алфавита: для отверстий прописными A, B, C … Z, для валов строчными a, b, c, … z.
Преимущественно назначают посадки в системе отверстия с основным отклонением Н у которого EJ=0.(нижнее отклонение).
Для посадок с зазором рекомендуют применять неосновные валы f, g, h; для переходных посадок Js, k, m, n; для посадок с натягом p, r, s.
Посадки обозначаются комбинациями условных обозначений полей допусков отверстия и вала: Ø40 H7/f7; Ø 35 H7/k6; Ø 22 H7/p6.
В посадках больший допуск (квалитет) должен быть у отверстия H7/m6; допуски отверстия и вала могут отличаться не более чем на 2 квалитета. Основные квалитеты в современном производстве - 6, 7, 8.
Посадки выбирают на основании расчетов или предыдущего опыта по таблицам рекомендуемых посадок. Чернавский таб. 10.13.
ПЛАКАТ 131
ПЛАКАТ 14
Шероховатость поверхностей – совокупность неровностей с относительно малым шагом.
Обозначается знаками:
Основные параметры шероховатости:
R а – среднее арифметическое отклонение профиля в пределах базовой длины в мкм, обозначается:
Rz – высота неровностей профиля по десяти точкам мкм обозначается:
В каждом конкретном случае шероховатость должна быть выбрана в соответствии с назначением поверхности.
Рекомендации по назначению параметров шероховатости Чернавский стр. 266, табл. 10.17.
ПЛАКАТ 15
Пример рабочего чертежа вала-шестерни
Детали машин
ПЛАКАТ 3
Основы проектирования ДМ
Курс «Детали машин» посвящен изучению основ расчета и конструирования деталей и узлов общего назначения, встречающихся в различных механизмах и машинах.
Целью курса ДМ - является развитие инженерного мышления с точки зрения изучения современных методов, правил и норм расчета и конструирования деталей и сборочных единиц машин общего назначения (валы зубчатые колеса редуктора и т.д.).
Задачи курса ДМ - привить навыки расчета и конструирования типовых деталей и узлов машин, научить рационально, выбирать материал и форму деталей, выполнять расчеты на прочность жесткость, устойчивость, износостойкость и т.д. исходя из заданных условий работы машины.
Основной критерий, которому должны соответствовать все инженерные решения – здравый смысл. Решение не соответствующее данному критерию заведомо не верно.
Машина – устройство для преобразования энергии или движения, накопления и переработки информации.
Механизм – часть машины, в которой рабочий процесс реализуется путем выполнения определенных механических движений.
Деталь – элемент конструкции, изготовленный из материала одной марки без применения сборочных операций (болт, гайка, вал и т.д.).
Узел (сборочная единица) – совокупность деталей, соединенных на предприятии-изготовителе сборочными операциями и предназначенных для совместной работы (коробка передач, муфта, редуктор и т. д.).
Основные требования, которым должны удовлетворять детали и узлы, как и машины в целом:
1 Работоспособность; 2 Надежность; 3 Технологичность;
4 Экономичность; 5 Эстетичность.
Работоспособность - состояние объекта, при котором он способен выполнять заданные функции, сохраняя значения заданных параметров в пределах, установленных нормативно-технической документацией. (Феррари V< 320 км/час).
Надежность - свойство объектов сохранять работоспособность в течении заданного промежутка времени или требуемой наработки. Например: срок службы подшипников - 20 тыс. часов.
Технологичными называют детали и узлы, требующие минимальных затрат средств, времени и труда в производстве, эксплуатации и ремонте.
Работоспособность и надежность деталей машин оценивают следующими основными критериями:
1 Прочность; 2 Жесткость; 3 Износостойкость;
4 Устойчивость; 5 Теплостойкость; 6 Виброустойчивость.
Износостойкость - способность детали сохранять необходимые размеры трущихся поверхностей в течении заданного срока службы. (Она зависит от свойств выбранного материала, термообработки и шероховатости поверхностей, значения давлений или контактных напряжений, скорости скольжения и условий смазывания, режима работы и т.д. Износ уменьшает прочность деталей, изменяет точность и характер соединения.)
В большинстве случаев расчеты деталей на износостойкость ведут по допускаемым давлениям [P], установленным практикой (расчеты подшипников скольжения, цепных передач и т.д.):
P ≤ [ P ].
Машиностроительные материалы
ПЛАКАТ 4
Выбор материала и термообработки деталей машин определяется конструктивными соображениями (обеспечение надежности), технологическими (единичное, серийное, массовое производство) и экономическими.
Для изготовления деталей применяют черные и цветные металлы, пластмассы и другие не металлические материалы.
Черные металлы являются основными машиностроительными материалами. К ним относятся: стали - железоуглеродистые сплавы с содержанием углерода до 2,14%. и чугуны - железоуглеродистые сплавы с содержанием углерода более 2,14%, обычно до 3,8%..
Стали подразделяются на углеродистые и легированные - содержащие специальные присадки (примеси): хром никель и другие.
Углеродистая сталь обыкновенного качества изготовляется по ГОСТ 380 - 88 обозначается буквами: Ст0,Ст1, Ст3,Ст5 и т.д. Применяют для термически не обрабатываемых деталей (прокатный профиль, корпуса, крепеж и т.д.)
Углеродистая качественная конструкционная сталь изготовляется по ГОСТ 1050 – 88 обозначается сталь 10, сталь 45 где числа 10 и 45 показывают содержание углерода в сотых долях процента 0,10% и 0,45% соответственно. Содержание серы в качественной стали S≤0,04%, фосфора Р≤0,035-0,04%.
Качественную углеродистую сталь применяют для деталей машин подвергаемых термообработке (зубчатые колеса, валы и т.д.)
|
|
Типы сооружений для обработки осадков: Септиками называются сооружения, в которых одновременно происходят осветление сточной жидкости...
Организация стока поверхностных вод: Наибольшее количество влаги на земном шаре испаряется с поверхности морей и океанов (88‰)...
История создания датчика движения: Первый прибор для обнаружения движения был изобретен немецким физиком Генрихом Герцем...
Общие условия выбора системы дренажа: Система дренажа выбирается в зависимости от характера защищаемого...
© cyberpedia.su 2017-2024 - Не является автором материалов. Исключительное право сохранено за автором текста.
Если вы не хотите, чтобы данный материал был у нас на сайте, перейдите по ссылке: Нарушение авторских прав. Мы поможем в написании вашей работы!