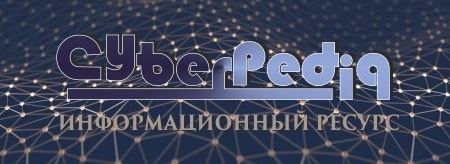
История развития хранилищ для нефти: Первые склады нефти появились в XVII веке. Они представляли собой землянные ямы-амбара глубиной 4…5 м...
Состав сооружений: решетки и песколовки: Решетки – это первое устройство в схеме очистных сооружений. Они представляют...
Топ:
Проблема типологии научных революций: Глобальные научные революции и типы научной рациональности...
Генеалогическое древо Султанов Османской империи: Османские правители, вначале, будучи еще бейлербеями Анатолии, женились на дочерях византийских императоров...
Интересное:
Подходы к решению темы фильма: Существует три основных типа исторического фильма, имеющих между собой много общего...
Уполаживание и террасирование склонов: Если глубина оврага более 5 м необходимо устройство берм. Варианты использования оврагов для градостроительных целей...
Наиболее распространенные виды рака: Раковая опухоль — это самостоятельное новообразование, которое может возникнуть и от повышенного давления...
Дисциплины:
![]() |
![]() |
5.00
из
|
Заказать работу |
|
|
В. П. Добровольский
ПРИВОДЫ КОНВЕЙЕРОВ
С ГИБКИМ ТЯГОВЫМ ЭЛЕМЕНТОМ
Учебное пособие
по курсовому проектированию
Омск
Издательство ОмГТУ
2009
УДК 62–8(075)
ББК 34.447я73
Д56
Рецензенты:
А. А. Еремеев, канд. техн. наук, доц. каф. «Детали машин» ОмГАУ
В. Н. Никитин, канд. техн. наук, доц. каф. «Прикладная механика» СибАДИ
Добровольский, В. П.
Д56 Приводы конвейеров с гибким тяговым элементом: учеб. пособие /
В. П. Добровольский. – Омск: Изд-во ОмГТУ, 2009. – 112 с.
ISBN 978-5-8149-0792-9
Печатается по решению редакционно-издательского совета
Омского государственного технического университета
УДК 62–8(075)
ББК 34.447я73
© ГОУ ВПО «Омский государственный
|
СОДЕРЖАНИЕ
ВВЕДЕНИЕ......................................................................................................... 5
1. ПРЕДВАРИТЕЛЬНЫЙ РАСЧЁТ ПРИВОДА............................................... 6
1.1 Определение частоты вращения вала рабочего органа.......................... 7
1.2 Определение потребной мощности электродвигателя............................ 7
1.3 Выбор электродвигателя по мощности.................................................... 8
1.4 Выбор электродвигателя по частоте вращения его вала...................... 10
1.5 Рекомендации по проектированию дополнительных передач привода 12
1.6 Выбор стандартного редуктора............................................................. 15
2. ЭСКИЗНОЕ ПРОЕКТИРОВАНИЕ УЗЛА ВАЛА РАБОЧЕГО ОРГАНА. 26
Таблица параметров на валах привода....................................................... 29
3. ОПРЕДЕЛЕНИЕ СИЛЫ НА ВАЛ РАБОЧЕГО ОРГАНА КОНВЕЙЕРА
ИЗ-ЗА ВОЗМОЖНОГО СМЕЩЕНИЯ СОЕДИНЯЕМЫХ МУФТОЙ
ВАЛОВ........................................................................................................... 37
|
4. КОНСТРУИРОВАНИЕ РАБОЧЕГО ОРГАНА ЛЕНТОЧНОГО
КОНВЕЙЕРА................................................................................................ 38
4.1 Определение силы на приводной барабан со стороны тяговой ленты 38
4.2 Выбор тяговой ленты.............................................................................. 39
4.3 Конструирование приводных барабанов.............................................. 41
4.4 Расчёт вала барабана на статическую прочность.................................. 43
4.5 Расчёт подшипников вала барабана по динамической
грузоподъёмности................................................................................... 46
4.6 Конструирование отклоняющего барабана (ролика)........................... 47
5. КОНСТРУИРОВАНИЕ РАБОЧЕГО ОРГАНА ЦЕПНОГО КОНВЕЙЕРА 50
5.1 Определение силы на вал тяговой звёздочки со стороны тяговой цепи 50
5.2 Выбор тяговой цепи................................................................................ 50
5.3 Конструирование тяговых звёздочек..................................................... 52
5.4 Проектирование предохранительного устройства................................ 53
5.5 Расчёт валов тяговых звёздочек на статическую прочность................. 55
5.6 Расчёт подшипников вала тяговых звёздочек по динамической
грузоподъёмности................................................................................... 57
6. ПРОЕКТИРОВАНИЕ ШПОНОЧНЫХ СОЕДИНЕНИЙ............................ 59
7. ВЫБОР МУФТЫ ДЛЯ СОЕДИНЕНИЯ ВАЛОВ РЕДУКТОРА
И ДВИГАТЕЛЯ............................................................................................. 62
ПРИЛОЖЕНИЕ I. Цепи приводные роликовые.............................................. 63
ПРИЛОЖЕНИЕ II. Подшипники шариковые радиальные............................ 65
ПРИЛОЖЕНИЕ III. Корпуса подшипников качения и крышки..................... 68
ПРИЛОЖЕНИЕ IV. Шайбы концевые............................................................. 83
ПРИЛОЖЕНИЕ V. Основные параметры и размеры тяговых 85
пластинчатых цепей.......................................................................................... 85
ПРИЛОЖЕНИЕ VI. Конструкции предохранительных устройств................ 87
ПРИЛОЖЕНИЕ VII. Муфты упругие............................................................. 90
ПРИЛОЖЕНИЕ VIII. Рекомендации по оформлению документации
курсового проекта............................................................................................. 94
|
ПРИЛОЖЕНИЕ IX. Сборочный чертёж привода ленточного конвейера... 102
ПРИЛОЖЕНИЕ X. Образцы заданий на курсовое проектирование........... 108
ПРИЛОЖЕНИЕ XI. Исходные данные на курсовое проектирование.......... 110
БИБЛИОГРАФИЧЕСКИЙ СПИСОК............................................................ 111
ВВЕДЕНИЕ
Конвейеры (транспортёры) – машины непрерывного действия применяются для перемещения массовых грузов, при сборке машин и в других случаях.
По типу грузонесущего элемента конвейеры разделяются на ленточные, цепные, роликовые (рольганги), скребковые, ковшовые и винтовые (шнеки).
По принципу действия конвейеры бывают гравитационные и приводные (тяговые).
Предметом проектирования при выполнении курсового проекта по дисциплинам кафедры «Детали машин» является привод ленточного или цепного конвейера, который состоит из электродвигателя, передаточного механизма и рабочего органа.
В курсовых проектах рекомендуется использовать асинхронные двигатели единой серии АИР.
Обозначения типов двигателей в большинстве случаев не определены стандартами. Различают условное, базовое, основное и полное обозначения двигателей. В курсовых проектах достаточно привести базовое обозначение двигателя, например: двигатель АИР100L 4. Здесь АИ обозначение серии;
Р вариант привязки мощности к установочным размерам; 100
высота оси вращения; L
установочный размер по длине станины; 4
число полюсов обмотки статора.
Передаточный механизм привода, располагающийся между двигателем и рабочим органом конвейера, предназначен для снижения частоты вращения вала рабочего органа и повышения крутящего момента на нём. Он может включать в себя редуктор и дополнительную передачу. Тип редуктора и наличие дополнительной передачи оговаривается заданием на курсовое проектирование.
В качестве дополнительной передачи может использоваться ременная, цепная или открытая зубчатая передача. При этом ременная передача располагается между двигателем и редуктором, а цепная и открытая зубчатая – между редуктором и рабочим органом конвейера. В зависимости от времени, выделяемого учебным планом на курсовой проект, редуктор передаточного механизма или выбирается стандартный, или проектируется оригинальный. Дополнительная передача всегда проектируется.
Рабочим органом ленточного конвейера является тяговый барабан. Рабочим органом цепного конвейера может быть одна или две тяговые звёздочки
(в зависимости от задания на проект), закреплённые на валу. Валы рабочих органов конвейеров через сферические подшипники качения, смонтированные в стандартных корпусах, устанавливаются и закрепляются болтами на раме конвейера.
|
ПРЕДВАРИТЕЛЬНЫЙ РАСЧЁТ ПРИВОДА
Целью предварительного расчёта привода конвейера является выбор электродвигателя и решение вопроса о структуре передаточного механизма.
Начинать расчёт следует с составления кинематической схемы привода, на которой нужно отразить все его элементы от электродвигателя до рабочего органа конвейера.
Кинематическая схема привода с передаточным механизмом, состоящим только из цилиндрического зубчатого редуктора, представлена на рисунке 1а,
с передаточным механизмом, состоящим из цилиндрического зубчатого редуктора и ременной передачи – на рисунке 1б, с передаточным механизмом, состоящим из червячного редуктора и цепной передачи – на рисунке 1в. В целях экономии места на рисунках представлены схемы приводов при одинаковом передаточном механизме ленточного (I) и цепных (II, III) конвейеров с разным числом тяговых звёздочек. В дальнейших расчётах отношение формул к тому или иному типу конвейера будет отражаться указанием его номера.
а) б)
в)
Рис. 1. Кинематические схемы приводов конвейеров с передаточным механизмом,
включающим: а) редуктор цилиндрический зубчатый; б) редуктор цилиндрический зубчатый и ременную передачу; в) редуктор червячный и цепную передачу
На рисунке обозначено: 1 электродвигатель; 2 – редуктор цилиндрический; 2'
редуктор червячный; 3
муфта упругая компенсирующая; 3' – передача ременная; 4 – муфта жесткая компенсирующая; 4'
передача цепная; 5
подшипник качения сферический; 6
барабан тяговый; 7
звёздочка тяговая.
1. 1 Определение частоты вращения n вала рабочего органа, об/мин
барабана для схемы :
;
звёздочек для схем ,
|
где
скорость тяговой ленты или тяговой цепи, м/с;
диаметр тягового барабана, мм;
p шаг тяговой цепи, мм;
z число зубьев тяговой звёздочки.
1.2 Определение потребной (расчётной) мощности
электродвигателя, кВт
для схемы ;
для схемы ;
для схемы ,
где
окружное усилие на тяговом барабане или тяговой звёздочке, кН;
коэффициент полезного действия (кпд) привода;
Кб коэффициент безопасности, значение которого принимается в пределах 1,1
1,2 для учёта возможного изменения коэффициента трения между лентой и барабаном.
Для схемы привода (рис. 1а)
. (1)
Здесь
кпд редуктора;
кпд муфты;
кпд подшипников вала рабочего органа конвейера.
Коэффициент полезного действия редуктора определяется типом ре-дуктора. Стандартный цилиндрический зубчатый редуктор одноступенчатый ЦУ и двухступенчатый соосный Ц2С имеют = 0,98, двухступенчатый Ц2У
= 0,97. Значение кпд стандартного червячного редуктора зависит от его передаточного числа и частоты вращения вала червяка и изменяется в пределах от 0,54 до 0,94. На предварительной стадии расчётов рекомендуется принимать кпд червячного редуктора равным 0,80 с уточнением расчётов после выбора редуктора и определения точного значения его кпд.
Кпд компенсирующих муфт колеблется в пределах 0,985 0,995
.
В формуле (1) предполагаются значения обеих муфт привода одинаковыми.
Кпд подшипников качения вала рабочего органа привода рекомендуется принимать 0,99.
Для схемы привода (рис. 1б) ,
где кпд ременной передачи.
Для повышения компактности привода из ременных передач в передаточном механизме следует отдавать предпочтение передачам клиновыми ремнями. Для этих передач кпд изменяется в пределах = 0,96 – 0,97.
Для схемы привода (рис. 1в) ,
где кпд цепной передачи.
Для открытой цепной передачи роликовой или втулочной цепью рекомендуется принимать кпд = 0,92 – 0,94.
Муфта 500 – 1 – 55 – 2 – 48 – 1 У3 ГОСТ 20742-93.
Таблица параметров на валах привода
Вал | Частота вращения, об/мин | Момент крутящий, Н · м | Мощность, Вт |
электро-двигателя редуктора быстроходный (входной) редуктора тихоходный (выходной) рабочего органа |
![]() ![]() ![]() ![]() ![]() ![]() ![]() ![]() ![]() ![]() | А: ![]() ![]() ![]() ![]() ![]() ![]() ![]() ![]() ![]() | А: ![]() ![]() ![]() ![]() ![]() ![]() ![]() ![]() ![]() ![]() ![]() ![]() |
А – схема привода (рис. 1а);
Б – схема привода (рис. 1б);
В – схема привода (рис. 1в).
Таблица 11
Цепные муфты (по ГОСТ 20742-93)
Размеры, мм
Номинальный крутящий момент Т, Нм |
| D, не более | L не для исполнений | для испол-нений | Компенси-
рующие свойства | Частота вращения, 1/с-1 | Цепь, ГОСТ 13568 – 97 | Число звеньев цепи | | |||||
Смещение | ||||||||||||||
Ряд 1 | Ряд 2 | 1 | 2 | 1 | 2 | Угловое | Радиальное | |||||||
500 | 40 | - | 200
200 | 222
| 172 |
82 |
57 |
|
0,32 |
18 | ПР-31,75-8900 |
14 |
2,0 | |
- | 42 | |||||||||||||
45 | - | |||||||||||||
- | 48 | |||||||||||||
50 | - | |||||||||||||
- | 53 | |||||||||||||
55 | - | |||||||||||||
- | 56 | |||||||||||||
1000 | 50 | - | 210
|
0,40
|
16 | ПР-38,1-12700 |
12 |
3,5 | ||||||
- | 53 | |||||||||||||
55 | - | |||||||||||||
- | 56 | |||||||||||||
60 | - | 284 | 220 | 105 |
73 | ПР-50,8-22700 | ||||||||
63 | - | |||||||||||||
- | 65 | |||||||||||||
70 | - | |||||||||||||
71 | - |
Окончание табл. 11
Номинальный крутящий момент Т, Нм |
| D, не более | L не более для исполнений | для испол-нений | Компенси- рующие свойства | Частота вращения, 1/с-1 | Цепь, ГОСТ 13568 – 97 | Число звеньев цепи |
| ||||
Смещение
| |||||||||||||
Ряд 1 | Ряд 2 | 1 | 2 | 1 | 2 | Угловое | Радиальное | ||||||
2000 | 63 | - | 280 | 284 | 220 | 105 |
73
|
|
0,50 |
14 | ПР-50,8-22700 |
12
|
3,8 |
- | 65 | ||||||||||||
70 | - | ||||||||||||
71 | - | ||||||||||||
- | 75 | ||||||||||||
80 | - | 344 | 272 | 130 |
94 | ||||||||
- | 85 | ||||||||||||
90 | - |
По диаметру вала 50 мм выбираем подшипник радиальный шариковый двухрядный сферический средней серии 1310, имеющий диаметр наружного кольца 110 мм и ширину 27 мм (прил. II). По диаметру 110 мм с учётом рекомендаций ГОСТ 1328.3–80 выбираем корпус УМ 110 (прил. III).
С учётом серии подшипника и его посадочного диаметра на вал выбираем по таблице 12 диапазон диаметра заплечика для установки подшипника. В рассматриваемом случае получается от 60 до 63 мм. По диаметру отверстия в корпусе с учётом диапазона диаметра заплечика подбираем крышку торцовую для корпуса. Крышки высокая (МВ) (табл. ПIII.7) и средняя (МС) (табл. ПIII.8)
не подходят, т.к. имеют отверстия под вал меньше значения диаметра запле-чика. Подходит крышка низкая (МН) с диаметром отверстия под вал 60 мм (табл. ПIII. 9):
Крышка МН 110 60 ГОСТ 13219.6 – 81.
С левой стороны корпуса устанавливаем такую же крышку. Для обеспечения совпадения диаметров вала и отверстия в крышке, ставим на валу втулку с наружным диаметром 60 мм, которая будет выполнять ещё и функцию буртика для полумуфты, насаживаемой на вал.
Таблица 12
Заплечики для установки подшипников качения (по ГОСТ 20226-82)
для подшипников по ГОСТ 28428-90
Лёгкой серии | |||||
d | D | ![]() | ![]() | ![]() | a, min |
35 | 72 | 42,0 | - | 65,0 |
2,0 |
40 | 80 | 47,0 | 48,0 | 73,0 | |
45 | 85 | 52,0 | 53,0 | 78,0 | |
50 | 90 | 57,0 | 58,0 | 83,0 | |
55 | 100 | 62,0 | 65,0 | 91,0 |
3,0 |
60 | 110 | 67,0 | 71,0 | 101 | |
65 | 120 | 72,0 | 77,0 | 111 | |
70 | 125 | 77,0 | 82,0 | 116 | |
75 | 130 | 82,0 | 85,0 | 121 | |
80 | 140 | 90,0 | 92,0 | 130 | |
Средней серии | |||||
D | ![]() | ![]() | ![]() | ![]() | a, min |
80 | 42,0 | 44,0 | 71,0 | - |
2,0 |
90 | 47,0 | 51,0 | 81,0 | 80,0 | |
100 | 52,0 | 56,0 | 91,0 | 89,0 | |
110 | 60,0 | 63,0 | 99,0 | 98,0 | |
120 | 65,0 | 67,0 | 110 | 109,0 |
3,0
|
130 | 72,0 | 75,0 | 118 | 115,0 | |
140 | 76,0 | 78,0 | 128 | 125,0 | |
150 | 81,0 | 85,0 | 138 | 136,0 | |
160 | 86,0 | 93,0 | 148 | 144,0 | |
170 | 91,0 | 99,0 | 158 | 155,0 |
Размеры даны в миллиметрах.
Конец вала рабочего органа можно принять коническим (рис. 9). При таком решении будет одно достоинство этой конструкции – обе полумуфты применяемой муфты одного исполнения.
Рис. 9. Конструкция вала с коническим концом
При этом будут иметь место следующие недостатки:
1) потребуется применить крышку подшипника со стороны конца вала, отличную от поставленной с другой стороны опоры, из-за различия диаметров вала, что увеличит номенклатуру заказываемых крышек;
2) для сохранения статуса неподвижности этой опоры вала закрепить подшипник на нём можно только с помощью пружинного упорного кольца, что потребует применения дополнительной детали в форме кольца, толщина которого подбирается при монтаже. Это удорожает конструкцию. Кроме того, паз под пружинное кольцо ослабляет сечение вала.
Размеры пружинных упорных плоских наружных колец концентрических (ГОСТ 13940-68) и эксцентрических (ГОСТ 13942-68), а также размеры канавок для них выбираются в зависимости от диаметра вала .
Диаметр болта, с помощью которого прижимаются торцовые крышки к корпусу подшипника, определяется диаметром отверстий в крышках и корпусе (в данном случае – 11 мм), а его длина обусловлена шириной корпуса, толщиной фланцев крышек и прокладок между корпусом и крышками, высотой гайки и толщиной шайбы пружинной (см. рис. 11). В рассматриваемой конструкции опоры применены болты нормальной точности класса прочности 5.8
Болт М 10 75. 58 ГОСТ 7798
70.
Для упрощения процесса замены болта левой опоры вала при случайном повреждении на нём резьбы устанавливаем эти болты со стороны рабочего органа конвейера. В противном случае для замены болта потребовалось бы снимать с вала полумуфту, что без разборки всего узла невозможно.
Положение торца резьбовой части болта определяет положение левого торца втулки, а, следовательно, её длины. Чтобы за болт не зацеплялась при вращении вала насаженная на него деталь, торец втулки (по рис. 8) должен быть левее торца резьбовой части болта.
Рабочий орган на валу относительно опоры располагаем с учётом возможности постановки этих болтов при сборке подшипникового узла.
|
|
Рис. 10. Вид на опору вала слева
Для предотвращения вытекания смазки из подшипникового узла между торцами корпуса и крышками устанавливаются прокладки толщиной около
1 мм, изготавливаемые из картона прокладочного (ГОСТ 9347-74) или паронита (ГОСТ 481-80), а в крышки вставляются резиновые армированные манжеты (ГОСТ 8752-79). В рассматриваемом примере применены манжеты типа 1 (однокромочные) исполнения 1 (с механически обработанной кромкой) для вала диаметром 60 мм с наружным диаметром 85 мм из резины группы 1 (пригодной для работы при скорости скольжения до 10 ) (табл. 13):
Манжета 1. 1– 60 85 – 1 ГОСТ 8752-79
Для обеспечения осевой неподвижности подшипника относительно корпуса опоры вала между торцами наружного кольца подшипника и крышек устанавливаются стальные кольца толщиной, равной зазору между этими поверхностями. Для обеспечения осевой неподвижности вала относительно подшипника применяем концевую шайбу (ГОСТ 14734–69), которая после установки на вал полумуфты будет прижимать полумуфту, втулку и внутреннее кольцо подшипника к заплечику вала при завинчивании в вал болта. Размеры концевой шайбы выбираются по диаметру вала. В данном случае с учётом диаметра конца вала (48 мм) применена шайба 2 исполнения (прижимаемая болтом)
Шайба 7019-0633 ГОСТ 14734-69.
Таблица 13
Основные размеры резиновых армированных манжет, мм (ГОСТ 8752 – 79)
Диаметр вала | 30; 32 | 35; 36 | 38 | 38 | 40 | 42 | 45 | 48; 50 | 52 | 55; 56; 58 | 60 | 63; 65 | 70; 71 | 75 |
D | 52 | 58 | 52 | 58 | 60; 62 | 62 | 65 | 70 | 75 | 80 | 85 | 90 | 95 | 100 |
h | 10 | 10 | 7 | 10 | 10 | 10 | 10 | 10 | 10 | 10 | 10 | 10 | 10 | 10 |
![]() | 14 | 14 | 10 | 14 | 14 | 14 | 14 | 14 | 14 | 14 | 14 | 14 | 14 | 14 |
Продолжение табл. 13
Диаметр вала | 80 | 85 | 90; 92; 95 | 100 | 105 | 110 | 115 | 120 | 125 | 130 | 140 |
D | 105 | 110 | 120 | 125 | 130 | 135 | 145 | 145; 150 | 155 | 160 | 170 |
h | 10 | 12 | 12 | 12 | 12 | 12 | 12 | 12 | 12 | 15 | 15 |
![]() | 14 | 16 | 16 | 16 | 16 | 16 | 16 | 16 | 16 | 20 | 20 |
В правой опоре вала (рис. 11), в отличие от левой, одна из крышек глухая и для обеспечения возможности осевого перемещения подшипника относительно корпуса не ставятся кольца между торцами наружного кольца подшипника и крышек. Для исключения случайного сползания подшипника с вала при работе привода применена концевая шайба, размеры которой определились посадочным на вал диметром подшипника и диаметром заплечика для него.
Крышки глухие (табл. П III. 8).
Шайбы концевые (прил. IV, табл. ПIV.1)
Крышка ГН 110 ГОСТ 13219.2 – 81
Шайба 7019 – 0634 ГОСТ 14734 – 69.
3. ОПРЕДЕЛЕНИЕ СИЛЫ НА ВАЛ РАБОЧЕГО ОРГАНА КОНВЕЙЕРА
ИЗ-ЗА ВОЗМОЖНОГО СМЕЩЕНИЯ СОЕДИНЯЕМЫХ
МУФТОЙ ВАЛОВ
Кроме крутящего момента, числовое значение которого определено в п. 2, на вал рабочего органа действует сила от натяжения ветвей ленты в приводе ленточного конвейера или от натяжения ветвей тяговой цепи в приводе цепного конвейера. В обоих случаях при соединении валов редуктора и рабочего органа муфтой на валы будут действовать силы, обусловленные возможным относительным смещением валов при монтаже.
Для выбранной в п. 2 цепной муфты получаем делительный диаметр звёз-дочки полумуфты ,
где
шаг цепи муфты; z
число звеньев цепи муфты.
В нашем случае = 31,75 мм; z = 14. Тогда
142,683 мм.
Окружное усилие на звёздочке полумуфты в ньютонах ,
где Т крутящий момент, подводимый к валу рабочего органа, Н·м.
По расчетам в п. 2 Т = 490 Н·м. Тогда 6868,4 Н.
Усилие на вал от муфты определяется по формуле
, т.е.
(1030,3
1717,1) Н.
Максимальное значение усилия (1717 Н) нужно сравнить с допускаемой радиальной силой на конец тихоходного вала выбранного редуктора
(см. табл. 3–5, 14) и тем самым убедиться в пригодности выбранного редуктора по этому параметру.
Для расчёта вала рабочего органа и его подшипников принимаем усреднённое значение силы = 1400 Н. Эта сила считается приложенной в точке, совпадающей с серединой длины конца вала.
Таблица 14
Наибольшие радиальные консольные силы на концы валов
червячных одноступенчатых редукторов типа Ч, кН
Вал | Т и п о р а з м е р р е д у к т о р а | |||||
Ч-50 | Ч-63 | Ч-80 | Ч-100 | Ч-125 | Ч-160 | |
Входной Выходной | 250 2000 | 345 2800 | 500 4000 | 600 5600 | 875 8000 | 1180 11200 |
4. КОНСТРУИРОВАНИЕ РАБОЧЕГО ОРГАНА
ЛЕНТОЧНОГО КОНВЕЙЕРА
В ленточном конвейере движущая сила передаётся на ленту силой трения между лентой и барабаном. Различают приводы однобарабанные, двухбарабанные и трёхбарабанные. При небольшой производительности конвейера применяются в основном однобарабанные приводы. Для повышения силы трения между лентой и барабаном увеличивают угол обхвата барабана лентой установкой в приводе отклоняющего барабана (ролика).
Выбор тяговой ленты
В конвейерах применяют резинотканевые, резинотросовые и стальные ленты.
1 – тканая прокладка; 2 – резиновая обкладка
Наибольшее распространение находят резинотканевые ленты, имеющие резинотканевый послойный тяговый каркас (1) и наружные резиновые обкладки (2), предохраняющие каркас от механических повреждений и от воздействия влаги и агрессивных сред по ГОСТ 20–85. В зависимости от назначения ленты разделяют на следующие виды: общего назначения, морозостойкие, теплостойкие, пищевые и негорючие.
Конвейерные ленты, согласно ГОСТ 20–85, могут быть шириной от 100 до 3000 мм с числом прокладок от 1 до 8. Толщина наружных резиновых обкладок в зависимости от вида ленты и вида транспортируемого груза составляет 1–3,5 мм и 1–10 мм соответственно для нерабочей (нижней) и рабочей (верхней) сторон ленты. Толщина тканевых прокладок каркаса ленты принята
1,15–2,0 мм. Тканевые прокладки изготавливают из полиамидных или полиэфирных нитей или из комбинированных (полиэфирных и хлопчатобумажных) нитей. В зависимости от вида ткани каркаса изменяется номинальная прочность тканевой прокладки.
С учётом сложности точного определения действительного напряжения в слоях ленты при совместном действии растяжения и изгиба расчёт ленты ведут только на растяжение по наибольшему рабочему усилию в ленте.
Необходимое по условию прочности ленты число прокладок зависит от растягивающего ленту усилия и прочности материала прокладок. Наибольшее допустимое число прокладок ленты ограничивается диаметром барабана, т.к. увеличение числа прокладок повышает жёсткость ленты и напряжение изгиба в ленте при огибании ею барабана. Нужно подобрать материал прокладок ленты, который удовлетворял бы условию прочности ленты и соответствовал бы заданному диаметру приводного барабана.
С учётом этих условий получаем для горизонтальных конвейеров
,
где D – диаметр барабана, мм;
F1 – натяжение ведущей ветви ленты, Н;
В – ширина ленты, мм;
SP1 – прочность ткани прокладки, Н/мм ширины ленты (табл. 16);
К1 – коэффициент, учитывающий свойство ткани прокладок;
КН – коэффициент неравномерности работы прокладок;
КСТ – коэффициент прочности стыкового соединения концов ленты (для вулканизированного стыка КСТ = 0,90 – 0,85);
КР – коэффициент режима работы конвейера.
Полученное расчётом число прокладок округляется до ближайшего целого значения.
Значения коэффициентов К1, Кн, Кр берутся из следующей таблицы.
Прочность прокладки
![]() | 65 | 100 | 150 | 200 | 300 | 400 |
Коэффициент К1* | 125–140 | 141–160 | 161–170 | 171–180 | 181–190 | 191–200 |
Число прокладок | 3 | 4 | 5 | 6 | 7 | 8 |
Коэффициент КН | 0,95 | 0,90 | 0,88 | 0,95 | 0,82 | 0,80 |
Режим работы | Весьма легкий | Легкий | Средний | Тяжелый | Весьма тяжелый | |
Коэффициент режима КР | 1,2 | 1,1 | 1,0 | 0,95 | 0,85 |
* Меньшие значения коэффициента К1 принимают для лент меньшей ширины.
Таблица 16
Материал тканевых прокладок конвейерных лент
Ткань | Марка ткани | Номинальная прочность ткани по основе SP1, Н/мм ширины прокладки |
С нитями основы и утка из полиамидных волокон | ТА–400; ТК–400; МК–400/120 | 400 |
ТА–300; ТК–300; А–10–2–3Т К–10–2–3Т; МК–300/100 | 300 | |
ТК–200–2 | 200 | |
ТА–150; ТК–150 | 150 | |
ТА–100; ТК–100 | 100 | |
С нитями основы | МЛК–400/120 | 400 |
ТЛК–300; МЛК–300/100 | 300 | |
ТЛК–200 | 200 | |
С нитями |
|
|
Индивидуальные и групповые автопоилки: для животных. Схемы и конструкции...
История создания датчика движения: Первый прибор для обнаружения движения был изобретен немецким физиком Генрихом Герцем...
Кормораздатчик мобильный электрифицированный: схема и процесс работы устройства...
Семя – орган полового размножения и расселения растений: наружи у семян имеется плотный покров – кожура...
© cyberpedia.su 2017-2024 - Не является автором материалов. Исключительное право сохранено за автором текста.
Если вы не хотите, чтобы данный материал был у нас на сайте, перейдите по ссылке: Нарушение авторских прав. Мы поможем в написании вашей работы!