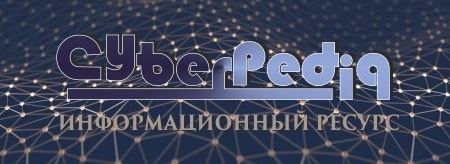
Особенности сооружения опор в сложных условиях: Сооружение ВЛ в районах с суровыми климатическими и тяжелыми геологическими условиями...
История развития хранилищ для нефти: Первые склады нефти появились в XVII веке. Они представляли собой землянные ямы-амбара глубиной 4…5 м...
Топ:
Комплексной системы оценки состояния охраны труда на производственном объекте (КСОТ-П): Цели и задачи Комплексной системы оценки состояния охраны труда и определению факторов рисков по охране труда...
Основы обеспечения единства измерений: Обеспечение единства измерений - деятельность метрологических служб, направленная на достижение...
Теоретическая значимость работы: Описание теоретической значимости (ценности) результатов исследования должно присутствовать во введении...
Интересное:
Влияние предпринимательской среды на эффективное функционирование предприятия: Предпринимательская среда – это совокупность внешних и внутренних факторов, оказывающих влияние на функционирование фирмы...
Отражение на счетах бухгалтерского учета процесса приобретения: Процесс заготовления представляет систему экономических событий, включающих приобретение организацией у поставщиков сырья...
Искусственное повышение поверхности территории: Варианты искусственного повышения поверхности территории необходимо выбирать на основе анализа следующих характеристик защищаемой территории...
Дисциплины:
![]() |
![]() |
5.00
из
|
Заказать работу |
|
|
Основные свойства и классификация металлов.
2. Основные виды кристаллических решеток.
А. Свойства присущие металлам.
1. Повышенная тепло и электропроводность.
2. Положительный температурный коофициент электросопротивления.
3.Термоэлектронная эмиссия (способность испускать электроны при нагреве).
4. Хорошая отражающая способность.
5. Повышенная пластичная деформация.
6. В строении все металлы и сплавы тела кристаллические, т.е. в узлах кристаллической решетки расположены положительные ионы, а между ними отрицательные ионы (электронный газ).
Б. Классификация металлов.
Черные металлы.
К ним можно отнести: железо, марганец, хром и т.д.
2. Цветные металлы можно разделить на подгруппы:
а) Тяжелые: имеют плотность более 5гр. на см. куб. К ним относятся: цинк; медь; олово; свинец; серебро; золото.
б) Легкие: имеют плотность менее 5гр. на см. куб. К ним относятся: литий, натрий, магний, калий, алюминий, титан.
в) Тугоплавкие: температура плавления превышает температуру плавления железа (1539*С). К ним относятся: ниобий, молибден, вольфрам.
г) Легкоплавкие: температура плавления менее температуры плавления железа (1539*С). К ним относятся: цезий, литий, калий, натрий, олово, свинец, алюминий, медь, ртуть.
д) Редкие: молибден, вольфрам, ванадий.
е) Рассеянные: кадмий, титан, индий.
ж) Радиоактивные: радий, уран, криптон.
з) Благородные: серебро; золото, платина, палладий.
Атомно – кристаллическое строение металлов.
1. Под ним понимают взаимное расположение атомов в кристалле, которые располагаются в определенном порядке, повторяющемся в трех измерениях.
|
2. Основные виды кристаллических решеток:
2.1. Ионная. 2.2.Атомная. 2.3.Молекулярная. 2.4. Металлическая.
3. Основные виды металлических решеток. графит (слоистая)
3.1. КУБИЧЕСКАЯ ОБЪЕМНО ЦЕНТРИРОВАННАЯ (КОЦ).
.
Атомы расположены в узлах ячейки и один атом в центре куба.
Встречается в: альфа железо (при температуре до 768*С), хром, вольфрам, ванадий, молибден.
3.2. КУБИЧЕСКАЯ ГРАНЕ ЦЕНТРИРОВАННАЯ (КГЦ).
Атомы расположены в углах куба и в центре каждой грани.
Встречаются в :
Гамма железо (при температуре от 910 до 1392*С), никель, медь, золото, серебро, свинец, алюминий.
3.3. ГЕКСАГОНАЛЬНАЯ (ПЛОТНОУПАКОВАННАЯ).
Атомы расположены в углах и в центре шестигранных оснований призмы, плюс три атома в средней плоскости призмы.
Встречается в: магний, цинк, кадмий, кобальт, селен.
4. Размеры решетки характеризуется периодами
Период это расстояние между двумя ближними параллельными атомными плоскостями.
Еденица измерения АНГСТРЕМ. 1А=10 в -8см.
Период решетки металлов находится в пределах от 1 до 7А.
У. Коррозия металлов.
1. Самопроизвольное разрушение металлических материалов, происходящее под химическим воздействием окружающей среды называется коррозией.
2. Коррозия в газах:
- происходит при высоких температурах, когда влаги на поверхности быть не может. Образуются оксиды, сульфиды (окалина).
- Газовой коррозии подвергаются: ДВС, арматура печей, металл при термообработке.
3. Коррозия в растворах (электрохимическая коррозия)
- происходит в водных растворах или влажной среде.
- образуются нерастворимые продукты (ржавчина) и переход металла в раствор в виде ионов.
4. Методы защиты о т коррозии:
- Применение химических стойких сплавов(коррозийно стойких и жаростойких).
|
- защита поверхности металла покрытиями (хром, никель, цинк).
- покрытие неметаллов лаками и красками.
- обработка внешней среды (удаление 02 из растворов).
Тема № 2. Свойства металлов.
1. Физические свойства металлов.
1. Плотность – количество вещества, содержащегося в единице объема (г/см.куб).
2. Температура плавления (*С) – температура, при которой металл полностью переходит из твердого в жидкое состояние.
3. Теплопроводность это способность тела передавать с той или иной скоростью тепло при нагревании или охлаждении. (кал/см*мин*град.)
4. Тепловое расширение – металлы при нагревании расширяются, а при охлаждении сжимаются.
4.1. Линейное расширение – изменение линейного размера при нагреве или расширении.
4.2. Объемное расширение – это изменение объема тела при нагреве или расширении.
5. Удельная теплоемкость – это количество электричества, необходимого для повышения температуры 1г.вещества на 1*С.
6. Электропроводность – это способность металлов проводить электрический ток.
- зависит от удельного сопротивления. P=L*S/R. (Ом*мм/м.)
7. Способность намагничивания – это способность металла создавать собственное м магнитное поле: самостоятельно или под действием внешнего магнитного поля.
- оно зависит от магнитной проницаемости вещества.
-за единицу принята магнитная проницаемость вакуума М=4*10-7 ом*м/сек(гн/м).
7.1. Парамагниты М=1. (воздух, дерево. Бумага, стекло, пластмасса и т. д.)
7.2. Диамагниты М меньше 1. (медь. Бронза, олово, свинец, латунь).
7.3. Ферромагниты М больше 1. Железо(М=800), чугун(М=240), сталь Ст3(М=3500), трансформаторная сталь(М=7500). Ферриты(М=60000).
11. Химические свойства металлов.
1. Это свойство металлов и сплавов, определяющие отношение их к химическим воздействиям различных сред.
2. Воздействие этих сред проявляется в различных формах:
2.1. Атмосферная коррозия (ржавчина).
2.2.Коррозия в газах (окалина).
2.3. В кислотах металлы растворяются.
111. Деформации и разрушения.
1. Изменение формы твердого тела под действием внешних сил называется деформацией.
2. По характеру действия сил нагрузки они делятся на статические и динамические.
2.1. Статические возрастают медленно о «0» значения до некоторого максимального значения и далее остаются неизменными.
|
2.2. Динамические возрастают в результате удара, действие нагрузки исчисляются секунды.
ВИДЫ ДЕФОРМАЦИИ.
Сжатие.
Это деформация, где уменьшается объем тела под действие сдавливающих сил.
- сжатию подвергаются: колонны, фундаменты, амортизаторы.
2. Растяжение.
Это деформация с увеличением длины тела под действием сил, приложенных к его концам (тросы. фаркоп. ремни. болты).
Сдвиг (срез).
Две силы направлены навстречу, но не по одной прямой, а близко друг к другу. (заклепки, болты, шпильки).
4. Кручение.
Это деформация тела с одним неподвижным концом, под действием пары равных противоположных сил. (валы ДВС).
5. Изгиб.
Это деформация тела, сопровождающая изменением кривизны его под действием внешних сил (рессоры, валы, балки).
1У. Механические свойства металлов.
Прочность.
Это способность тела сопротивляться разрушению под действием внешних сил.
- в зависимости от характера внешних сил различают:
1.1. Прочность на растяжение. 1.2. Прочность на сжатие. 1.3. Прочность на изгиб.
1.4. Прочность на кручение. 1.5. Усталость металлов.
Б. Усталость металлов.
1. Это явление их разрушения при многократных, часто повторяющихся нагрузках.
- причина – появление микротрещин при охрупчивании.
- усталости подвержены: поршни, шатуны, к. валы.
Пластичность.
2.1.Это способность металла не разрушаясь, не разрушаясь, изменять форму под действием нагрузки, и сохранять измененную форму после снятия нагрузки.
2.2.Пластичность определяется при испытании на растяжение: - чем больше удлиняется образец, тем более пластичен металл и хорошо обрабатывается давлением.
2.3. Характеризуется: - относительным удлинением и относительным сужением.
А. Относительное удлинение (б). б= L 1- L 2 / Lo *100%.
1.Это отношение длины образца после разрыва к его первоначальной длине.
L 1 – длина после разрыва (мм). L 2 – первоначальная длина (мм).
|
Б. Относительное сужение ( )
= F o – F 1 / Fo *100%.
1.Это отношение уменьшения площади поперечного сечения образца после испытания, к первоначальной площади.
- F o – площадь образца до начала испытания. (мм2)
- F 1 – площадь в месте разрыва (мм2).
Ударная вязкость.
3.1. Это способность металлов и сплавов оказывать сопротивление действию ударных нагрузок.
3.2. Изготовляют стандартные образцы с надрезом.(бруски).
3.3. Устанавливают образец в маятниковом копере и наносят удар со стороны противоположной надрезу.
3.4. Хрупкие металлы разрушаются без изменения формы.
3.5. Вязкие изгибаются в местах излома.
Твердость.
4.1. Это свойство металла оказывать сопротивление проникновению в него, более твердого тела, не получающего остаточных деформаций.
4.2. Твердость связана с прочностью и износоустойчивостью.
4.3 Методы определения твердости:
а) Метод Бринелля – шарик из закаленной стали вдавливают в образец, и специальной лупой с ценой деления 0.1мм замеряют диаметр отпечатка.
б) Метод Роквелла – алмазный конус или закаленный стальной шарик малого диаметра (1.6мм) вдавливают в образец и замеряют глубину отпечатка.
в) Метод Виккерса – алмазную пирамиду вдавливают в образец и измеряют диагональ отпечатка.
метод применяется для испытания:
- металлов и сплавов очень высокой твердости.
-деталей малых размеров.
- тонких твердых поверхностных слоев, полученных ХТО.
Метод Роквелла Бринелля Виккерса
г) Метод Шора
- Как правило, используется для измерения твердости низкомодульных материалов. Обычно — полимеров: пластмасс, эластомеров, каучуков и продуктов их вулканизации.
- Называется аппарат дюрометром.
У него есть опорная площадка с отверстием по центру, индентор, то есть вдавливатель, и калиброванная пружина, прилагающая к нему определенную силу.
-Последний элемент машины – индикатор. Он определяет степень выдвижения «носика» индентора за пределы опорной поверхности.
- Измерительных шкал у прибора несколько. Основных две, это A и D. Разбивка необходима для точности опытов, ведь испытуемыми становятся материалы с разной твердостью. Мягкие проверяют по шкале А, а более упругие – по D.
- Чтобы определить, к примеру, твердость полиуретана по Шору, дюрометр устанавливают вертикально. «Носик» индентора, при этом, должен отстоять от края образца на те самые 12 миллиметров.
- Прижать опорную поверхность к образцу нужно как можно быстрее, без толчка, держа параллель между плоскостями.
- Остается приложить к опорной поверхности давление, обеспечивающее надежный контакт с испытуемым материалом. Для этого используют груз. Но, допускается и ручной жим.
|
- Мгновенное измерение проводят за 1 секунду. Однако, обычно, показатели снимают через 15 секунд. Для верности, проводят 5 замеров в разных местах поверхности.
- Среднее значение – и есть число твердости. Оно может быть от 0-ля до 100-та. Такова шкала твердости Шора
- на среднем рисунке показан прибор в котором шарик отскакивает от образца и замеряется высота отскока и сила отскока.
д) Метод тарированных (сравнительных) напильников.
- имеется набор напильников с маркировкой твердости.
- если выбранный напильник снимает с образца стружку, то твердость образца меньше твердости выбранного напильника.
У. ТЕХНОЛОГИЧЕСКИЕ И ЭКСПЛУАТАЦИОННЫЕ СВОЙСТВА.
Пластинчатый – серый чугун.
А. БЕЛЫЙ ЧУГУН. (БЧ)
1. Это такой чугун, в котором большая часть углерода химически соединена с железом в виде цементита Fe3C.(карбид железа).
2. Цементит имеет светлый цвет, обладает большой твердостью (800 НВ) и хрупкостью.
3.Поэтому белый чугун также имеет в изломе светло-серый, почти белый цвет, очень тверд, не поддается механической обработке и сварке, поэтому ограниченно применяется в качестве конструкционного материала.
4. Общие сведения используются для:
а) получения ковких чугунов. (При длительном обжиге белого чугуна цементит в нем распадается и углерод выделяется в свободное состояние.),
б) на переплавку в сталь.
5. Удельный вес 7,4 – 7,7г/смз;
6. Температура плавления 1100 – 1150*С.
Б. Серый чугун (СЧ).
1.Это литейный чугун поступает в виде заготовок, в котором большая часть углерода находится в свободном состоянии в виде графита(пластинчатого типа).
2. Серый чугун мягок, хорошо сопротивляется износу, хорошо обрабатывается режущим инструментом, имеет хорошие демпфирующие свойства(гасит вибрации в 2-4 раза лучше стали) – поэтому применяется для изготовления фундаментов, рам кузнечных прессов, крупных эл. машин, к. валов.
3. В изломе имеет темно-серый цвет (чем темнее тем мягче).
4. Температура плавления серого чугуна 1200-1250°С. Удельный вес 6,6 -7,4г/см3.
- Чем больше в чугуне углерода, тем ниже температура его плавления и выше жидкотекучесть.
5. Прочность серого чугуна с пластинчатым графитом при растяжении находится в пределах 120...440 МПа, твердость 140...290 НВ.
6. Структура серых чугунов в зависимости от состава и условий охлаждения может быть с перлитной, перлитно-ферритной и ферритной основой.
7. По ГОСТ 1412-79 марку серого чугуна обозначают буквами СЧ и двумя числами СЧ – 35 - 46 из которых первое обозначает величину временного сопротивления чугуна при растяжении в МН/м2(например 35=35кг/мм2 = 350МПа =3500кг/см2) второе - то же, при изгибе (46= 46кг/мм2=460МПа=4600кг/см2).
В. Ковкий чугун (кч)
1. Получают из белого чугуна термической обработкой - длительной выдержкой при температуре 800-850°С.(отжиг).
1.1. Отливку медленно нагревают (в течении 20-25часов)до температуры 950-1000*С.
1.2. Выдерживают при этой температуре 10-15часов.
1.3. Снижают до температуры 720-740*С и выдерживают 25-30 часов.
2. При этом углерод в чугуне выделяется в виде хлопьев свободного углерода, располагающихся между кристаллами чистого железа.
3. В зависимости от режима термической обработки получают ковкий чугун ферритной или перлитной структур
4. Ковкий чугун обозначают буквами КЧ и двумя числами: первое - указывает временное сопротивление при растяжении, МН/м, второе - относительное удлинение, %.
5. Ковкий чугун по сравнению с серым чугуном обладает более высокой прочностью (300... 630 МПа), пластичностью и ударной вязкостью. Ковкий чугун имеет однородные свойства по сечению, в его отливках отсутствуют напряжения, ему присущи высокие механические свойства, он хорошо обрабатывается и применяется в автомобильной. с/х, текстильной промышленности
6. Состав основных элементов в ковком чугуне (в %): 2,3...3 С; 0,9... 16 Si; 0,3... 1,2 Мn; >0,15 Р и S
Г. Высокопрочный чугун (вч)
1. Получают из серого чугуна специальной обработкой - введением в жидкий чугун в электрической печи при температуре не ниже 1400°С чистого магния (Mg) или его сплавов.
2.В высокопрочном чугуне (ГОСТ 7293-85) углерод находится в виде шаровидного графита.
3. Содержание основных элементов в таких чугунах составляет (в %): до 38 С; 2.9 Si; 0,9 Мn; 0,1 Сг; 0,02 S; 0,1 Р; 0,08 Mg.
4. Чугуны с шаровидным графитом значительно превосходят по характеристикам серые чугуны. в частности по износо-, жаро- и коррозионной стойкости.
5.Применяется для деталей прокатных станов, кузнечно – прессового обордования, к. валов.
6. Предел прочности до 650 МПа. Б=12%.(относительное удлинение)
7 Высокопрочный чугун обозначают буквами ВЧ и двумя числами: первое - указывает временное сопротивление при растяжении, МН/м, второе - относительное удлинение, %.
Д. Легированные чугуны
1. Имеют специальные примеси Сr, Ni, благодаря которым повышаются его кислотостойкость, прочность при ударных нагрузках и др.
2. Классификация чугунов легированных:
2.1. жаростойкие хромовые чугуны, (алюминий, титан, молибден, вольфрам, хром).
2.2. коррозионно-стойкие чугуны, (хром, никель, медь).
2.3.износостойкие чугуны (кремний, титан, молибден. вольфрам)
2.4.другие.
3. Такие чугуны легируются хромом, никелем, кремнием, магнием, медью и другими элементами.
4. В легированных чугунах с содержанием до 10 % Ni, Сr и Мn и более имеют место перлитно-карбидные, бейнитные, мартенситные и аустенитные основы.
5. Магнитные чугуны: -
Применяют для изготовления корпусов эл. машин, рам, щитов,;
4. Немагнитный чугун
Применяют для изготовления кожухов и бондажей эл. машин. Состав (7-10% Мп +7-9% никеля)
5. Аустенитный чугун – кислотостойкий, жаропрочный, легируют никелем, хромом, медью, молибденом, ванадиеим.
6. НИРИЗИТ = 14% никеля + 2%хрома + 7% меди. – кислотостойкий.
7. Чугаль – жаростойкий = 20-25% алюминия.
Тема №5. СТАЛИ.
1. Общие сведения.
1. Сталь представляет собой сплав железа и углерода с незначительным содержанием кремния, марганца, фосфора и серы.
2. В углеродистой стали, в отличие от нержавеющей, отсутствуют легирующие элементы (молибден, хром, марганец, никель, вольфрам)
3. Свойства углеродистой стали сильно изменяются в зависимости от незначительного изменения содержания углерода. С ростом содержания углерода растут твердость и прочность стали, а ударная вязкость и пластичность снижаются. Содержание углерода от 0,02 до 2.14%. При содержании углерода более 2,14% сплав называется чугуном. Эвтектика стали =0,8%.
11. Классификация углеродистых сталей
А. В зависимости от химического состава сталь бывает углеродистая и легированная.
1. Углеродистая сталь делится на:
Сталь, в составе которой кроме углерода имеются легирующие компоненты (хром, никель, вольфрам, ванадий и т. д.), называется легированной.
2. Легированные сталибывают:
Б. По способу производства (ПО КАЧЕСТВУ).
1. Обыкновенного качества с содержанием серы до 0,6 % и фосфора до 0,7%.
Существует 3 группы сталей обыкновенного качества:
· Группа А. Поставляется по механическим свойствам без регламентации состава сталей. Стали эти обычно используются в изделиях без последующей обработки давлением и сваркой. Чем больше число условного номера, тем выше прочность и меньше пластичность стали.
· Группа Б. Поставляется с гарантией химического состава. Чем больше число условного номера, тем выше содержание углерода. В дальнейшем могут обрабатываться ковкой, штамповкой, температурным воздействием без сохранения начальной структуры и механических свойств.
· Группа В. Могут свариваться. Поставляются с гарантией состава и свойств. Эта группа сталей имеет механические свойства в соответствии с номерами по группе А, а химический состав – с номерами по группе Б с коррекцией по способу раскисления.
2. Качественную с содержанием серы до 0,030 % и фосфора до 0,035%. Сталь имеет повышенную чистоту и обозначается буквой А после марки стали.
3. Высококачественные содержание серы и фосфора не более 0,025%. Сталь имеет повышенную чистоту и обозначается буквой А после марки стали.
4. Особовысококачественные содержание серы и фосфора не более 0,015%. Сталь имеет повышенную чистоту и обозначается двойной буквой АА после марки стали.
В. По назначению стали могут быть:
1. Строительные для изготовления строительных конструкций.
2. Машиностроительные (конструкционные) – для изготовления конструкций, приборов, деталей машин, из них выделяют: -цементуемые; - автоматные (для ЧПУ); -улучшаемые; - высокопрочные; - рессорно-пружинные; - арматурные; - подшипниковые.
3. Инструментальные для изготовления измерительного и режущего инструмента (резец, сверло)
4.Стали с особыми физическими свойствами – коррозийностойкие, жаростойкие.
Г. По степени раскисления.
1. СП - спокойные. Раскисляются марганцем, алюминием, кремнием почти полностью, пластичные, застывают спокойно, без газовыделения.
2. КП – кипящие. Раскисляются только марганцем, но не полностью. Перед разливкой имеют много кислорода, который реагирует с углеродом, образуя окись углерода. При застывании слитка окись углерода выходит наружу в виде пузырьков (кипит). Свариваются плохо, идет на штамповку.
3. ПС – полуспокойные. Занимают среднее положение между КП и СП.
Д. Обозначение сталей по позициям.
1 -- 2 -- 3 -- 4 -- 5 - 6
В Ст3г ПС 5 Х2С А
1я позиция – группа стали по качеству.
2я позиция – символ стали,содержание углерода (0,3%) и 1% марганца.
3я позиция – степень раскисления.
4я позиция – категория стали (для группы А - 6 категорий; для группы Б – 2 категории; для группы В – 6 категорий).
5я позиция – дополнительные элементы - полезные примеси. (см. таблицу ниже.)
6я позиция – чистота по сере и фосфору.
Тема № 6. ТЕРМИЧЕСКАЯ ОБРАБОТКА МЕТАЛЛОВ.
1. Сущность Т.О.
1. Термической обработкой называется совокупность операций: - нагрева, - выдержки, - охлаждения металлов и сплавов, находящихся в твердом, подогретом состоянии, с целью получения заданных свойств за счет изменения внутреннего строения и структуры.
2. Т.О. используется в качестве:
2.1. Промежуточной операции для улучшения: - обрабатываемости резанием; - давлением.
2.2. Как окончательная операция: - для придания особых свойств (прочность, пластичность, коррозийностойкость, жаростойкость).
Факторы Т.О.
-температура, время выдержки, скорость нагрева и охлаждения, среда нагрева и охлаждения.
11. Виды Т.О.
Различают три основных вида Т.О. металлов: - Собственно Т.О. – Химико – термическая обработка; - Термомеханическая обработка.
1. Собственно термообработка: предусматривает только температурное воздействие на металл в обычной среде.
- К ней относятся: отжиг, отпуск, закалка, нормализация, старение.
2. Химико - термическая обработка: нагрев и охлаждение осуществляется в определенной среде (азот, углерод), в результате которой металл насыщается элементами среды и приобретает особые свойства.
- К ней относятся: цементация, азотирование, цианирование.
3. Термо-механическая обработка: металл подвергается температурной обработке и одновременно температурному воздействию.
111. Собственно термическая обработка.
А. ОТЖИГ.
1. Это т.о. при которой металл нагревается до определенной температуры (350-1100*С), выдерживается при ней, а затем медленно охлаждается в термопечи.
2. Цель–получение менее твердой структуры, свободной от остаточных деформаций.
Б. ОТПУСК.
1. Это заключительная операция т.о.
2. Заключается в нагреве до 150 – 727*С, выдержке и охлаждении.
3. Цель: снятие остаточных деформаций после закалки или сварки.
В. ЗАКАЛКА.
1. Нагрев до температуры, выше фазовых превращений(1147*С). Выдержка при ней и быстрое охлаждение.
2. Цель: получение высокой твердости.
Г. НОРМАЛИЗАЦИЯ.
1. Это разновидность отжига с охлаждением на свободном воздухе.
2. Скорость охлаждения чуть больше обычного отжига.
3. Цель: устранение части крупно - зернистой структуры.
4. Применяется для: - в низкоуглеродистых сталях вместо отжига.
- для среднеуглеродистых сталей вместо улучшения (закалка + глубокий отпуск).
Д. СТАРЕНИЕ.
1. Это отпуск при невысоком нагреве.
2. Нагревают до 120 – 150*С, выдерживают при ней 10 – 35 часов.
3. Цель – не снижая твердости закаленной стали, стабилизировать размеры деталей. (это искусственное старение).
4. Естественное старение – это выдержка деталей и инструмента при комнатной температуре три и более месяца.
1У. Термо-механическая обработка.
А. Термо-механическая обработка.
1. Это сочетание пластической деформации стали в аустенитном состоянии (727-1239*С) с закалкой.
2. После закалки низкотемпературный отпуск при температуре 150-200*С.
3. Цель – получение очень высокой прочности при хорошей пластичности и вязкости.
4. Последовательность операций: деформация, закалка, отпуск.
Б. Механо-термическая обработка.
1. 1. Сочетает сначала закалку, потом деформирование.
2. Один из видов МТО это патентирование.
3. Патентирование – это термичекая обработка на троостит с последующей деформацией на 90-95%.
- она позволяет достичь предела прочности тонкой проволоки из высокоуглеродистой стали до 5000МПа.
У. Поверхностное упрочнение стали.
1. Поверхностная закалка – это вид Т.О. при которой закаливается только поверхностный слой изделия на заданную глубину, а сердцевина остается незакаленной.
2.Поверхностный слой обладает высокой твердостью или износостойкостью.
3. Методы поверхностной закалки:
3.1.Индукционный нагрев ТВЧ. 3.2. Нагрев газовым пламенем.
3.3.Закалка в электролите. 3.4. Лазерная закалка.
4. Толщина закаленного слоя чаще 1-3мм. но можно и 5-10мм.
У1. Химико – Термическая Обработка. (Х.Т.О.)
А. Общие положения.
1.ХТО – это тепловая обработка металла в химически активной среде.
2. Цель – изменение химических и физических свойств поверхностных слоев
.
3. ХТО основана на диффузии (переходе) атомов различных химических элементов в кристаллическую решетку железа, при нагреве в химической среде.
4.Глубина проникновения атомов зависит от: -состава стали; - температуры и времени насыщения.
5. Различают виды ХТО:
5.1. Цементация – насыщение углеродом.
5.2. Азотирование – насыщение азотом.
5.3. Цианирование (нитроцементация) – насыщение углеродом и азотом одновременно.
5.4.Диффузионная металлизация – насыщение поверхностного слоя металлами.
Б. Цементация.
1. Это процесс насыщения поверхностного слоя стали углеродом при температуре 920-950*С. Содержание углерода =0,8-1.0%.
2. Далее закалка и низкий отпуск при температуре 150*С.
3. Цель – получение твердой, износостойкой поверхности в сочетании с мягкой серцевиной.
4. Толщина (глубина) цементуемого слоя 0,5 -2,5мм.
5. Науглероживающая среда: - древесный уголь, раствор солей, природный газ.
В. Азотирование.
1. Это процесс насыщения поверхностного слоя стали азотом в течении 60 часов при температуре 500-600*С. Глубина насыщения 0.3-0.6мм.
2. Цель – придание поверхностному слою высокой твердости, коррозийностойкости, износостойкости.
3. Азот получают при нагреве аммиака (нашатырный спирт).
4. Азотируют только легированные хромом, молибденом, алюминием, титаном стали.
Закалка и отпуск не требуются.
Г. Цианирование (нитроцементация).
1. Это процесс совместного насыщения поверхностного слоя стали азотом и углеродом.
2. Цель – повышение твердости, износостойкости, коррозийностойкости при температуре 500 – 950*С.
2.1. При температуре 500*С, повышается коррозийностойкость.
2.2. При температуре 900*С повышается твердость.
Д. Диффузионная металлизация.
1. Это процесс диффузионного насыщения поверхностного слоя материала различными металлами. Для придания: корозийностойкости и износостойкости.
2. Различают виды металлизации:
2.1. Алитирование: насыщение поверхности алюминием, для придания коррозийностойкости и жаростойкости. Толщина слоя 0.2 – 1,0мм.
2.2.Хромирование: насыщение хромом для коррозийностойкости. Толщина слоя 0.2мм.
2.3. Борирование: насыщение бором для твердости. Толщина слоя 0.1мм.
2.4. Силицирование: насыщение кремнием для повышения износостойкости и корозийностойкости. Толщина слоя 0.3 – 1.0мм.
Тема № 7. ЦВЕТНЫЕ МЕТАЛЛЫ И СПЛАВЫ.
Раздел А. Алюминий и его сплавы.
Чистый алюминий.
1. Алюминий - один из самых лёгких металлических конструкционных материалов, его плотность составляет 2,7 г/см3.
2. Чистый алюминий имеет невысокую температуру плавления (660ºС), низкую твёрдость, высокую пластичность, хорошую электропроводность (60% от электропроводности меди)
3. Алюминий обладает высокой коррозионной стойкостью к воздействию воды и кислот. Коррозионные свойства объясняются высокой химической активностью алюминия, он быстро окисляется с образованием поверхностной плёнки Al2O3, которая имеет высокую плотность, твёрдость и температуру плавления 2050 градусов.
4. Одним из наиболее ценных свойств алюминия - высокая пластичность и хорошая деформируемость; он хорошо подвергается обработке давлением в холодном и горячем состоянии.
5. В связи с этим его используют в сосудах для транспортировки и получения азотной кислоты и т.п.
6. Чистый алюминий редко применяется как конструкционный материал (за исключением использования в качестве электропроводного материала в электротехнической промышленности и в отдельных случаях в химической и пищевой промышленности), что связано с его низкой прочностью.
7. Но в результате сплавления с магнием, медью, цинком, кремнием и другими элементами алюминий способен образовывать разнообразные сплавы, обладающие достаточной прочностью и хорошими технологическими свойствами.
8. Обозначение алюминевых сплавов: Л – литейный; Мг – магниевые. Д – дуралюминевые. К – для ковки и штамповки. Мц – марганцевые. Ав – авиали.
Характеристика сплавов |
Маркировка
Сплавы низкой прочности
И высокой пластичности,
свариваемые, коррозионносойкие
Al – Mn
Также
ММ (3005)
Сплавы средней прочности
И высокой пластичности,
свариваемые, коррозионносойкие
Al – Mg
(Магналии)
Также АМг0.5, АМг1, АМг1.5АМг2.5
АМг4 и т.д.
ТЕРМОУПРОЧНЯЕМЫЕ СПЛАВЫ
Al-Zn-Mg
|
|
Опора деревянной одностоечной и способы укрепление угловых опор: Опоры ВЛ - конструкции, предназначенные для поддерживания проводов на необходимой высоте над землей, водой...
Адаптации растений и животных к жизни в горах: Большое значение для жизни организмов в горах имеют степень расчленения, крутизна и экспозиционные различия склонов...
История развития пистолетов-пулеметов: Предпосылкой для возникновения пистолетов-пулеметов послужила давняя тенденция тяготения винтовок...
Индивидуальные очистные сооружения: К классу индивидуальных очистных сооружений относят сооружения, пропускная способность которых...
© cyberpedia.su 2017-2024 - Не является автором материалов. Исключительное право сохранено за автором текста.
Если вы не хотите, чтобы данный материал был у нас на сайте, перейдите по ссылке: Нарушение авторских прав. Мы поможем в написании вашей работы!