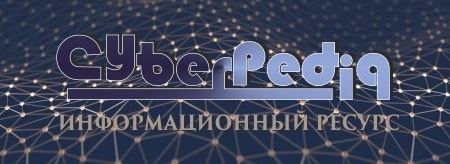
Механическое удерживание земляных масс: Механическое удерживание земляных масс на склоне обеспечивают контрфорсными сооружениями различных конструкций...
Типы оградительных сооружений в морском порту: По расположению оградительных сооружений в плане различают волноломы, обе оконечности...
Топ:
Установка замедленного коксования: Чем выше температура и ниже давление, тем место разрыва углеродной цепи всё больше смещается к её концу и значительно возрастает...
Эволюция кровеносной системы позвоночных животных: Биологическая эволюция – необратимый процесс исторического развития живой природы...
Теоретическая значимость работы: Описание теоретической значимости (ценности) результатов исследования должно присутствовать во введении...
Интересное:
Наиболее распространенные виды рака: Раковая опухоль — это самостоятельное новообразование, которое может возникнуть и от повышенного давления...
Национальное богатство страны и его составляющие: для оценки элементов национального богатства используются...
Уполаживание и террасирование склонов: Если глубина оврага более 5 м необходимо устройство берм. Варианты использования оврагов для градостроительных целей...
Дисциплины:
![]() |
![]() |
5.00
из
|
Заказать работу |
|
|
Содержание
1. История ОАО «ПО АМЗ»
2. Схема технологического процесса изготовления шкива
3. Техническая характеристика, устройство токарного станка
4. Режущий инструмент
5. Контрольный и мерительный инструмент
6. Практическая часть технологической производственной практики
Литература
Приложение А
Приложение Б
1. История ОАО "ПО АМЗ"
Возникновение ОАО "ПО АМЗ" относится к первой половине 50-х годов, когда начиналось наступление на целинные просторы Урала и Казахстана. Было принято решение о выпуске в Западной Сибири партии прицепных комбайнов С-6 на началах кооперации группы машиностроительных и металлообрабатывающих заводов. В эту группу вошли действующие заводы Омской, Новосибирской, Кемеровской областей и вновь созданный Барнаульский комбайносборочный завод.
Предприятие непродолжительное время, с 1955 года по 1958,производило жатки и копнители. В 1956 году по решению правительства комбайносборочный завод преобразован в завод по выпуску двигателей и топливной аппаратуры - Алтайский моторный завод.
В 1959 году начат выпуск тракторного двигателя СМД-7 мощностью 55 л.с. по чертежам Харьковского завода "Серп и Молот". Одновременно конструкторским бюро завода разрабатывается новый двигатель собственной конструкции А-01 мощностью 110 л.с. А в 1963 году уже успешно прошли государственные испытания этого двигателя, и с 1965 года завод приступил к его выпуску, параллельно с ним - к выпуску собственного же двигателя А-41. Модели А-01 и А-41 стали базовыми.
Этим было положено начало созданию двигателей собственной конструкции с большим количеством оригинальных инженерных решений, как в самой конструкции двигателя, так и в технологии его производства.
|
В 1990-91 г.г. освоены двигатели второго поколения - это двигатели с турбо наддувом без промежуточного охлаждения воздуха мощностью 127 л.с. в четырехцилиндровом исполнении и 160 л.с. - в шестицилиндровом. А уже в 1993 году начато производство двигателей третьего поколения с турбо наддувом и промежуточным охлаждением надувочного воздуха мощностью 145-160 л.с. для четырехцилиндровой модели и 180-240 л.с. для шестицилиндровой.
В декабре 1992 года производственное объединение "Алтайский моторный завод", сменив форму собственности, стало акционерным обществом "Алтайдизель".
На сегодняшний день "Алтайдизель" является одним из крупнейших в России производителей дизельных двигателей мощностью от 45 до 240 кВт.
Традиционными потребителями двигателей ОАО "Алтайдизель" были и остаются такие промышленные гиганты, как Алтайский, Волгоградский, Павлодарский тракторные заводы, завод "Дорожные машины" (г. Орел), завод "Арсенал" (г. Брянск), АО "Амкодор" (г. Минск), завод "Компрессор" (г.Ташкент) и др. Среди новых: Липецкий тракторный завод, Красноярский завод комбайнов, ОАО "Ростсельмаш", г. Ростов-на-Дону, Тульский комбайновый завод, Юргинский машиностроительный завод, Донецкий экскаваторный завод.
Несмотря на общий экономический спад производства, новая продукция обеспечила расширение доли традиционных рынков сбыта и завоевание новых.
Освоен комбайновый рынок. Поставлен в кратчайшие сроки на производство дизель Д-442, который полностью обеспечил потребность Красноярского комбайнового завода в двигателях для зерноуборочного комбайна "Енисей". А недавно конструкторами предприятия разработан двигатель для нового перспективного комбайна "Руслан". Сейчас ОАО "Ростсельмаш" практически полностью комплектует серийные зерноуборочные комбайны "Нива" и "Дон-800" двигателями ОАО "Алтайдизель". Но "Ниву" уже в ближайшее время сменит комбайн нового поколения "Дон-091", на котором будет стоять алтайский двигатель Д-4405-53 с 2-х поточным редуктором. Ростсельмашевский зерноуборочный комбайн "Дон-1500" уступит место на полях новому комбайну "Дон-141", для которого у нас начато изготовление опытных образцов шестицилиндровых двигателей. Успешно прошёл испытания двигатель Д-4605-51 для кормоуборочного комбайна "Дон-680". Параллельно ведутся работы с Тульским и другими комбайностроительными предприятиями.
|
Такая политика предприятия позволила захватить рынок комбайновых двигателей, на котором раньше монопольно господствовал Харьковский завод "Серп и Молот". Доля наших дизелей на комбайновом рынке на сегодня составляет 60,3%, и она постоянно увеличивается. В 1999 году комбайновым заводам отгружено 1225 дизелей.
Первым из моторостроительных заводов в России "Алтайдизель" создал семейство двигателей с двумя уровнями мощности, охватывающее диапазон (100 -, 160) л.с. и запасы крутящего момента (15-40)%. Применение двигателя Д-442-24 с двумя уровнями мощности позволило повысить производительность трактора ВТ-100Д производства Волгоградского тракторного завода до 15% на различных видах работ при сокращении погектарного расхода топлива до 10% по сравнению с трактором ВТ-1 ООН с двигателем СМД-20ТА Харьковского завода "Серп и Молот", то есть повысился технический уровень нового поколения тракторов ВгТЗ за счёт улучшения их тяговых характеристик и топливной экономичности, обеспечения более полного использования мощности двигателя, возможности работы с не энергоёмкими машинами и орудиями, снижения утомляемости оператора за счёт меньшего числа переключений передач.
Вся эта работа позволила значительно расширить традиционные для завода рынки сбыта. Так, например, в 1994 году лишь 65,5% гусеничных тракторов для сельского хозяйства комплектовались алтайскими дизелями, а в настоящее время - 93,2%.
В рекордно короткие сроки был разработан двигатель Д-442-47 с двумя уровнями мощности для интегрального трактора ЛТЗ-155 производства Липецкого тракторного завода и выпущена опытно-промышленная партия таких двигателей. Применяющиеся ранее на этих тракторах двигатели СМД DEUTZ, показали себя ненадёжными или сложными в эксплуатации. В настоящее время Липецкий тракторный завод комплектует тракторы ЛТЗ-155 только двигателями ОАО "Алтайдизель". 127 штук их выпущено в 1999 году и 250 шт. запланировано на 2000 год.
|
В начале 90-х годов в России, кроме Москвы и Санкт-Петербурга, в эксплуатации находилось около 30 тысяч автобусов "Икарус" венгерского производства. Более 30% этих автобусов простаивало из-за неисправности установленных двигателей фирмы «RАВА-МАN», отсутствия запасных частей и валюты.
С учётом создавшейся ситуации конструкторами ОАО "Алтайдизель" был разработан отечественный автобусный двигатель с технико-экономическими показателями, не уступающими зарубежным. Первые горизонтальные двигатели были выпущены в 1993 году. С момента их освоения заводом выпущено 1570 двигателей Д-463-10, Д-463-11 - для городских автобусов "Икарус", Д-463-20 - для междугородного автобуса. Икарусы с двигателями производства ОАО "Алтайдизель" перевозят пассажиров по всей России от Калининграда до Хабаровска.
На основе накопленного опыта создан двигатель нового поколения Д-46053, соответствующий стандартам ЕВРО. Начаты работы на двигателях Д-46053 по освоению рабочего процесса с газодизельным циклом.
Освоено мелкосерийное производство судового двигателя для речных и морских судов малого водоизмещения.
Выявив неудовлетворенную потребность в дизель-генераторных установках, предприятие организовало их производство. Выпускается семейство стационарных электростанций мощностью от 30 до 100 кВт, пользующихся устойчивым спросом.
ОАО "Алтайдизель" активно работает с иностранными фирмами. Были реализованы совместные проекты с фирмами Lister-Petter, Gerqules, AVL,Фирме Gerqules(США) завод и сейчас осуществляет поставку деталей 40 наименований.
Учитывая возрастающую конкуренцию на рынке в отношении технического уровня и экологических показателей двигателей, ОАО" Алтайдизель" совместно с немецкой фирмой "МАМ" разработало многоцелевой дизель современного уровня Д-4601, экологические параметры которого дымность, токсичность подтверждены сертификатами соответствия.
Технические решения, заложенные в конструкции двигателя Д-4601, соответствуют современным тенденциям двигателестроения. Выпущена опытная партия дизелей в количестве 60 штук. Эти двигатели прошли испытания на тракторах Т-250 Алтайского тракторного завода, Т-170 ОАО "Челябинский тракторный завод" и других машинах. Максимальная наработка двигателей Д-4601 составляет 10-12 тысяч моточасов. В 1993-1996 годах в МИС проводились сравнительные испытания трактора Т-250 с двигателем Д-4601 и трактора "Challenger-65" американской фирмы Саterpilan. Испытания показали, что Aлтайский трактор может реально конкурировать с американским по тяговым усилиям, тракторы имеет практически равную производительность при меньшем расходе топлива у Т-250.
|
Не останавливаясь на достигнутом, технические службы завода на базе дизеля Д-4601 разработали двигатели многоцелевого применения Д-4605 мощностью 310 л.с, Д-46053 мощностью 300 л.с. и Д-4405 мощностью 210 л.с. Эти двигатели отличаются высокой экономичностью (удельный расход топлива 150 г/л.с.ч.), надёжностью, большим запасом крутящего момента, экологическими параметрами, соответствующими современным требованиям.
Одной из основных проблем освоения производства этих двигателей остаётся отсутствие на российском рынке некоторых комплектующих соответствующего технического уровня (турбокомпрессор, поршневая группа, топливная аппаратура). Предприятие ведёт активную работу с предприятиями-смежниками для обеспечения собственного производства и рынка России комплектующими с высокими технико-экономическими показателями.
Специалистами предприятия разработан бизнес-план "Организация производства новых 4-х и 6-ти цилиндровых дизелей для тракторов, комбайнов и других машин путем технического перевооружения".
Бизнес-план, ТЭО технического перевооружения и другие документы переданы в Минэкономики РФ для рассмотрения в комиссии по инвестиционным конкурсам.
Программа развития ОАО "Алтайдизель" в представленном бизнес-плане получила одобрение Минсельхозпрода РФ, Департамента экономики машиностроения Минэкономики РФ и подтверждение, что для ее реализации требуется государственная поддержка.
Необходимо отметить, что наряду с техническими разработками на предприятии проведены и организационные мероприятия. Кардинально изменена структура управления: она приведена в соответствие с новыми экономическими требованиями и базируется на опыте работы многих зарубежных динамично развивающихся предприятий.
Режущий инструмент
Для изготовления шкива на токарно-винторезном станке из режущего инструмента применяется резцы и протяжка шпоночная,о которой поговорим немного поподробнее.
Протяжка - многолезвийный металлорежущий инструмент для обработки сквозных отверстий и наружных поверхностей деталей на протяжных станках. В зависимости от формы обрабатываемой поверхности протяжки различают:
|
v цилиндрические
v гранёные (квадратные, шестигранные и др.),
v шлицевые
v шпоночные
v наружные
v плоские
v наружные
v фасонные
У протяжек для внутреннего протягивания(рис.a.) зубья, расположенные на режущей части (постепенно возвышающиеся), выполняют основную работу по срезанию припуска. Калибрующая часть протяжки имеет от 3 до 8 зубьев; первый из них срезает очень малый слой металла и придаёт отверстию окончательную форму, остальные являются запасными (работают после переточек протяжки). Протяжка для наружного протягивания (рис. b.) изготовляются в виде прямоугольного бруска; имеют режущую и калибрующие части. Кроме режущих, применяют выглаживающие протяжки, которые не режут, а выравнивают и уплотняют металл; уплотнённый слой обладает высокой износостойкостью. Зубья выглаживающих протяжек не имеют углов резания; такие зубья делают иногда на калибрующей части режущей протяжки.
Рис.5.
Металлорежущий инструмент- орудие производства для изменения формы и размеров обрабатываемой металлической заготовки путём удаления части материала в виде стружки с целью получения готовой детали или полуфабриката. Различают станочный и ручной металлорежущий инструмент. Основные части Металлорежущий инструмента: рабочая, которая может иметь режущую и калибрующие части, и крепёжная. Режущей называется часть металлорежущего инструмента, непосредственно внедряющаяся в материал заготовки и срезающая часть его. Она состоит из ряда конструктивных элементов: одного или нескольких лезвий; канавок для отвода стружки, стружколомателей, стружкозавивателей; элементов, являющихся базовыми при изготовлении, контроле и переточках инструмента; каналов для подвода смазочно-охлаждающей жидкости. Назначение калибрующей части — восполнение режущей части при переточках, окончательное оформление обработанной поверхности и направление металлорежущего инструмента при работе. Крепёжная часть служит для закрепления металлорежущего инструмент а на станке в строго определённом положении или для удержания его в руках и должна противодействовать возникающим в процессе резания усилиям. Крепёжная часть может выполняться в виде хвостовиков (вставной металлорежущий инструмент) или иметь отверстие для крепления на оправках (насадной металлорежущий инструмент). В зависимости от технологического назначения станочный металлорежущий инструмент делится на следующие подгруппы: резцы, фрезы, протяжки, зуборезный, резьбонарезной, для обработки отверстий, абразивный и алмазный инструмент. Резцы, применяемые на токарных, токарно-револьверных, карусельных, расточных, строгальных, долбёжных и др. станках (за исключением резьбовых и зуборезных резцов), служат для обточки, расточки отверстий.
Литература
1. Егоров М.Е. и др. Технология машиностроения. Учебник для вузов. Изд. 2-е, доп. М., «Высшая школа», 1976. 534 с. с ил.
2. Технология машиностроения (специальная часть): Учебник для машиностроительных специальностей вузов/ А.А.Гусев, Е.Р.Ковальчук, И.М.Колесов и др. - М: Машиностроение, 1985. - 480 с.: ил.
3. Основы технологии машиностроения: Учеб. Для машиностроит. спец. вузов. - 3-е изд., стер. - М.: Высш. шк., 2001. - 591 с: ил.
Содержание
1. История ОАО «ПО АМЗ»
2. Схема технологического процесса изготовления шкива
3. Техническая характеристика, устройство токарного станка
4. Режущий инструмент
5. Контрольный и мерительный инструмент
6. Практическая часть технологической производственной практики
Литература
Приложение А
Приложение Б
1. История ОАО "ПО АМЗ"
Возникновение ОАО "ПО АМЗ" относится к первой половине 50-х годов, когда начиналось наступление на целинные просторы Урала и Казахстана. Было принято решение о выпуске в Западной Сибири партии прицепных комбайнов С-6 на началах кооперации группы машиностроительных и металлообрабатывающих заводов. В эту группу вошли действующие заводы Омской, Новосибирской, Кемеровской областей и вновь созданный Барнаульский комбайносборочный завод.
Предприятие непродолжительное время, с 1955 года по 1958,производило жатки и копнители. В 1956 году по решению правительства комбайносборочный завод преобразован в завод по выпуску двигателей и топливной аппаратуры - Алтайский моторный завод.
В 1959 году начат выпуск тракторного двигателя СМД-7 мощностью 55 л.с. по чертежам Харьковского завода "Серп и Молот". Одновременно конструкторским бюро завода разрабатывается новый двигатель собственной конструкции А-01 мощностью 110 л.с. А в 1963 году уже успешно прошли государственные испытания этого двигателя, и с 1965 года завод приступил к его выпуску, параллельно с ним - к выпуску собственного же двигателя А-41. Модели А-01 и А-41 стали базовыми.
Этим было положено начало созданию двигателей собственной конструкции с большим количеством оригинальных инженерных решений, как в самой конструкции двигателя, так и в технологии его производства.
В 1990-91 г.г. освоены двигатели второго поколения - это двигатели с турбо наддувом без промежуточного охлаждения воздуха мощностью 127 л.с. в четырехцилиндровом исполнении и 160 л.с. - в шестицилиндровом. А уже в 1993 году начато производство двигателей третьего поколения с турбо наддувом и промежуточным охлаждением надувочного воздуха мощностью 145-160 л.с. для четырехцилиндровой модели и 180-240 л.с. для шестицилиндровой.
В декабре 1992 года производственное объединение "Алтайский моторный завод", сменив форму собственности, стало акционерным обществом "Алтайдизель".
На сегодняшний день "Алтайдизель" является одним из крупнейших в России производителей дизельных двигателей мощностью от 45 до 240 кВт.
Традиционными потребителями двигателей ОАО "Алтайдизель" были и остаются такие промышленные гиганты, как Алтайский, Волгоградский, Павлодарский тракторные заводы, завод "Дорожные машины" (г. Орел), завод "Арсенал" (г. Брянск), АО "Амкодор" (г. Минск), завод "Компрессор" (г.Ташкент) и др. Среди новых: Липецкий тракторный завод, Красноярский завод комбайнов, ОАО "Ростсельмаш", г. Ростов-на-Дону, Тульский комбайновый завод, Юргинский машиностроительный завод, Донецкий экскаваторный завод.
Несмотря на общий экономический спад производства, новая продукция обеспечила расширение доли традиционных рынков сбыта и завоевание новых.
Освоен комбайновый рынок. Поставлен в кратчайшие сроки на производство дизель Д-442, который полностью обеспечил потребность Красноярского комбайнового завода в двигателях для зерноуборочного комбайна "Енисей". А недавно конструкторами предприятия разработан двигатель для нового перспективного комбайна "Руслан". Сейчас ОАО "Ростсельмаш" практически полностью комплектует серийные зерноуборочные комбайны "Нива" и "Дон-800" двигателями ОАО "Алтайдизель". Но "Ниву" уже в ближайшее время сменит комбайн нового поколения "Дон-091", на котором будет стоять алтайский двигатель Д-4405-53 с 2-х поточным редуктором. Ростсельмашевский зерноуборочный комбайн "Дон-1500" уступит место на полях новому комбайну "Дон-141", для которого у нас начато изготовление опытных образцов шестицилиндровых двигателей. Успешно прошёл испытания двигатель Д-4605-51 для кормоуборочного комбайна "Дон-680". Параллельно ведутся работы с Тульским и другими комбайностроительными предприятиями.
Такая политика предприятия позволила захватить рынок комбайновых двигателей, на котором раньше монопольно господствовал Харьковский завод "Серп и Молот". Доля наших дизелей на комбайновом рынке на сегодня составляет 60,3%, и она постоянно увеличивается. В 1999 году комбайновым заводам отгружено 1225 дизелей.
Первым из моторостроительных заводов в России "Алтайдизель" создал семейство двигателей с двумя уровнями мощности, охватывающее диапазон (100 -, 160) л.с. и запасы крутящего момента (15-40)%. Применение двигателя Д-442-24 с двумя уровнями мощности позволило повысить производительность трактора ВТ-100Д производства Волгоградского тракторного завода до 15% на различных видах работ при сокращении погектарного расхода топлива до 10% по сравнению с трактором ВТ-1 ООН с двигателем СМД-20ТА Харьковского завода "Серп и Молот", то есть повысился технический уровень нового поколения тракторов ВгТЗ за счёт улучшения их тяговых характеристик и топливной экономичности, обеспечения более полного использования мощности двигателя, возможности работы с не энергоёмкими машинами и орудиями, снижения утомляемости оператора за счёт меньшего числа переключений передач.
Вся эта работа позволила значительно расширить традиционные для завода рынки сбыта. Так, например, в 1994 году лишь 65,5% гусеничных тракторов для сельского хозяйства комплектовались алтайскими дизелями, а в настоящее время - 93,2%.
В рекордно короткие сроки был разработан двигатель Д-442-47 с двумя уровнями мощности для интегрального трактора ЛТЗ-155 производства Липецкого тракторного завода и выпущена опытно-промышленная партия таких двигателей. Применяющиеся ранее на этих тракторах двигатели СМД DEUTZ, показали себя ненадёжными или сложными в эксплуатации. В настоящее время Липецкий тракторный завод комплектует тракторы ЛТЗ-155 только двигателями ОАО "Алтайдизель". 127 штук их выпущено в 1999 году и 250 шт. запланировано на 2000 год.
В начале 90-х годов в России, кроме Москвы и Санкт-Петербурга, в эксплуатации находилось около 30 тысяч автобусов "Икарус" венгерского производства. Более 30% этих автобусов простаивало из-за неисправности установленных двигателей фирмы «RАВА-МАN», отсутствия запасных частей и валюты.
С учётом создавшейся ситуации конструкторами ОАО "Алтайдизель" был разработан отечественный автобусный двигатель с технико-экономическими показателями, не уступающими зарубежным. Первые горизонтальные двигатели были выпущены в 1993 году. С момента их освоения заводом выпущено 1570 двигателей Д-463-10, Д-463-11 - для городских автобусов "Икарус", Д-463-20 - для междугородного автобуса. Икарусы с двигателями производства ОАО "Алтайдизель" перевозят пассажиров по всей России от Калининграда до Хабаровска.
На основе накопленного опыта создан двигатель нового поколения Д-46053, соответствующий стандартам ЕВРО. Начаты работы на двигателях Д-46053 по освоению рабочего процесса с газодизельным циклом.
Освоено мелкосерийное производство судового двигателя для речных и морских судов малого водоизмещения.
Выявив неудовлетворенную потребность в дизель-генераторных установках, предприятие организовало их производство. Выпускается семейство стационарных электростанций мощностью от 30 до 100 кВт, пользующихся устойчивым спросом.
ОАО "Алтайдизель" активно работает с иностранными фирмами. Были реализованы совместные проекты с фирмами Lister-Petter, Gerqules, AVL,Фирме Gerqules(США) завод и сейчас осуществляет поставку деталей 40 наименований.
Учитывая возрастающую конкуренцию на рынке в отношении технического уровня и экологических показателей двигателей, ОАО" Алтайдизель" совместно с немецкой фирмой "МАМ" разработало многоцелевой дизель современного уровня Д-4601, экологические параметры которого дымность, токсичность подтверждены сертификатами соответствия.
Технические решения, заложенные в конструкции двигателя Д-4601, соответствуют современным тенденциям двигателестроения. Выпущена опытная партия дизелей в количестве 60 штук. Эти двигатели прошли испытания на тракторах Т-250 Алтайского тракторного завода, Т-170 ОАО "Челябинский тракторный завод" и других машинах. Максимальная наработка двигателей Д-4601 составляет 10-12 тысяч моточасов. В 1993-1996 годах в МИС проводились сравнительные испытания трактора Т-250 с двигателем Д-4601 и трактора "Challenger-65" американской фирмы Саterpilan. Испытания показали, что Aлтайский трактор может реально конкурировать с американским по тяговым усилиям, тракторы имеет практически равную производительность при меньшем расходе топлива у Т-250.
Не останавливаясь на достигнутом, технические службы завода на базе дизеля Д-4601 разработали двигатели многоцелевого применения Д-4605 мощностью 310 л.с, Д-46053 мощностью 300 л.с. и Д-4405 мощностью 210 л.с. Эти двигатели отличаются высокой экономичностью (удельный расход топлива 150 г/л.с.ч.), надёжностью, большим запасом крутящего момента, экологическими параметрами, соответствующими современным требованиям.
Одной из основных проблем освоения производства этих двигателей остаётся отсутствие на российском рынке некоторых комплектующих соответствующего технического уровня (турбокомпрессор, поршневая группа, топливная аппаратура). Предприятие ведёт активную работу с предприятиями-смежниками для обеспечения собственного производства и рынка России комплектующими с высокими технико-экономическими показателями.
Специалистами предприятия разработан бизнес-план "Организация производства новых 4-х и 6-ти цилиндровых дизелей для тракторов, комбайнов и других машин путем технического перевооружения".
Бизнес-план, ТЭО технического перевооружения и другие документы переданы в Минэкономики РФ для рассмотрения в комиссии по инвестиционным конкурсам.
Программа развития ОАО "Алтайдизель" в представленном бизнес-плане получила одобрение Минсельхозпрода РФ, Департамента экономики машиностроения Минэкономики РФ и подтверждение, что для ее реализации требуется государственная поддержка.
Необходимо отметить, что наряду с техническими разработками на предприятии проведены и организационные мероприятия. Кардинально изменена структура управления: она приведена в соответствие с новыми экономическими требованиями и базируется на опыте работы многих зарубежных динамично развивающихся предприятий.
Схема технологического процесса изготовления шкива
Так как основной продукцией является производство двигателей внутреннего сгорания, то неотъемлемой частью производства является изготовление отдельной детали. Ниже приведена блок схема технологического процесса изготовления детали (шкива).
Материал, из которого изготовлена деталь, является Чугун СЧ20 ГОСТ 1412. Твёрдость 170…240HB(по Бринеллю)
Заготовка
![]() |
Принятие заготовки
![]() |
Обработка на токарно-винторезном станке с ЧПУ (Горизонтально протяжной станок) |
Балансировка
![]() ![]() |
![]() |
Рис.1. Блок – схема технологического процесса изготовления шкива.
Обработка на токарно-винторезном станке с ЧПУ производится в следуюем порядке:
Ø 1.Установка детали на адаптер до упора.
Ø 2.Ввести хвостовик протяжки через деталь в патрон
Ø 3.Протянуть шпоночный паз, выдержав размеры
Ø 4.Очистить протяжку от стружки
Ø 5.Сняь деталь с адаптера и уложить на стол
Ø 6.Зачистить заусеницы на кромках паза
Ø 7.Очистить деталь от стружки
Ø 8.Проверить размер
Подробнее о техническом процессе смотрите Приложение А.
|
|
История создания датчика движения: Первый прибор для обнаружения движения был изобретен немецким физиком Генрихом Герцем...
Историки об Елизавете Петровне: Елизавета попала между двумя встречными культурными течениями, воспитывалась среди новых европейских веяний и преданий...
Двойное оплодотворение у цветковых растений: Оплодотворение - это процесс слияния мужской и женской половых клеток с образованием зиготы...
Индивидуальные и групповые автопоилки: для животных. Схемы и конструкции...
© cyberpedia.su 2017-2024 - Не является автором материалов. Исключительное право сохранено за автором текста.
Если вы не хотите, чтобы данный материал был у нас на сайте, перейдите по ссылке: Нарушение авторских прав. Мы поможем в написании вашей работы!