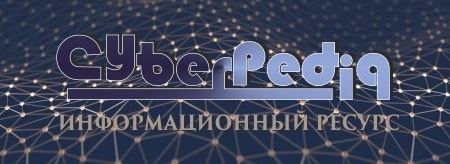
Наброски и зарисовки растений, плодов, цветов: Освоить конструктивное построение структуры дерева через зарисовки отдельных деревьев, группы деревьев...
Индивидуальные очистные сооружения: К классу индивидуальных очистных сооружений относят сооружения, пропускная способность которых...
Топ:
Методика измерений сопротивления растеканию тока анодного заземления: Анодный заземлитель (анод) – проводник, погруженный в электролитическую среду (грунт, раствор электролита) и подключенный к положительному...
Выпускная квалификационная работа: Основная часть ВКР, как правило, состоит из двух-трех глав, каждая из которых, в свою очередь...
Организация стока поверхностных вод: Наибольшее количество влаги на земном шаре испаряется с поверхности морей и океанов...
Интересное:
Национальное богатство страны и его составляющие: для оценки элементов национального богатства используются...
Влияние предпринимательской среды на эффективное функционирование предприятия: Предпринимательская среда – это совокупность внешних и внутренних факторов, оказывающих влияние на функционирование фирмы...
Инженерная защита территорий, зданий и сооружений от опасных геологических процессов: Изучение оползневых явлений, оценка устойчивости склонов и проектирование противооползневых сооружений — актуальнейшие задачи, стоящие перед отечественными...
Дисциплины:
![]() |
![]() |
5.00
из
|
Заказать работу |
|
|
Кафедра «Подвижной состав железных дорог»
КУРСОВОЙ ПРОЕКТ
по дисциплине: «ПОДВИЖНОЙ СОСТАВ ЖЕЛЕЗНЫХ ДОРОГ»
на тему: «Исследование экипажной части локомотива»
Выполнил: студент II курса
Специальности 23.05.03 «Подвижной состав Железных дорог»
Борзенко Е.В.(176833)______________
Руководитель: Кривошея Ю.В.
Национальная шкала:_________
Количество баллов:___________
Оценка: ECTS:_______________
Члены комиссии: __________ Гончарова Д.С.
__________ Кривошея Ю.В.
__________ Слепокуров Д.А.
Г. Донецк- 2019г.
Содержание
ВВЕДЕНИЕ
Экипажная часть локомотива — часть конструкции тяговой единицы подвижного состава, обеспечивающая её движение в рельсовой колее, представляет собой кузов с колёсными парами, в котором располагается необходимое энергетическое и вспомогательное оборудование. Экипажная часть является основой локомотива, непосредственно обеспечивающей движение.
При использовании кузова вагонного типа локомотивная бригада имеет доступ к силовому оборудованию во время движения без выхода из кузова, что улучшает условия работы бригады; кроме того, кузов вагонного типа имеет хорошую аэродинамику. Кузов капотного типа боковыми стенками и крышей закрывает лишь силовые агрегаты, что обеспечивает хороший обзор пути из кабины машиниста.
К экипажной части локомотива относятся кузов, главная рама, автосцепное устройство, тележки, рессорное подвешивание и др.
К экипажной части предъявляется ряд обязательных конструктивных требований и условий содержания при эксплуатации, к которым относятся:
- прочность и надёжность эксплуатации, как в целом, так и отдельных узлов;
- выдерживать нагрузки статического, динамического и ударного характера;
|
- обеспечивать определённые, научно-обоснованные показатели динамического качества локомотивов;
- обеспечивать удобство эксплуатации и ремонта отдельных элементов;
- обеспечивать заданный срок службы как верхнего строения пути, так и отдельных своих элементов;
- её конструкция не должна быть чрезмерно сложной и дорогой.
Подвижной состав железнодорожного транспорта не имеет рулевого управления. Траекторию его движения определяет рельсовая колея. Этим определяются и особенности ходовых частей: наличие гребней у бандажей колес; глухая насадка колёс на оси; параллельное расположение осей у тележек локомотивов и вагонов; коничность бандажей колёс; возможность поворота тележек и отдельных осей. Постоянство рельсовой колеи требует и постоянства расстояния между колёсами, для этого их запрессовывают так, чтобы они не могли ни смещаться на оси, ни поворачиваться относительно неё. Это называется глухой насадкой колёс. Ось с насаженными на неё двумя колёсами называют колесной парой.
При улучшении конструкции и содержания пути и, следовательно, его состояния, уменьшатся динамические взаимодействия подвижного состава и пути и напряжения во всех элементах не только пути, но и подвижного состава.
Целью данной работы заключается конструктивные особенности и принципы расчёта отдельных элементов экипажа локомотивов и железнодорожного пути, взаимодействующего с подвижным составом.
Выбор серии локомотива и его технические характеристики
Табл.1: Выбор серии локомотива и его технические характеристики
Показатели технической характеристики локомотива | Исходные данные | Показательные данные |
Осевая характеристика | 2(3о-3о) | 2(3о-3о) |
Нагрузка колёсной пары на рельсы, Кн (тс) | 220 | 226 |
Конструкционная скорость, км/ч | 100 | 100 |
Мощность номинального режима, кВт | 2*2200 | 2*2210 |
Габаритные размеры: - высота от головки рельса - длина от осей автосцепок - Ширина локомотива | 4900 34000 3200 | 4948 33938 3080 |
Масса состава, т | 4000 | 5040 |
Расчётный подъём, % | 7 | 6 |
Минимальный радиус кривой, м | 125 | 125 |
Допустимая скорость движения в кривой, км/ч | 60 | 60 |
Радиус Кривой участка пути, м | 350 | 350 |
|
Исходя из исходных данных заданий в методических указаниях и при помощи литературы, был выбран грузовой тепловоз 2ТЭ10М.
Тепловозы типа ТЭ10М выпускаются производственным объединением «ПАО «Лугансктепловоз»» двухсекционные общей мощностью 4412 кВт —2ТЭ10М и трёхсекционные общей мощности 6618 кВт — 3ТЭ10М- Тепловоз 2ТЭ10М состоит из двух однокабинных секций (А и Б), одинаковых по конструкции Секции тепловоза соединяются между собой автосцепкой СА-3, а для обеспечения перехода членов локомотивной бригады из секции в секцию оборудованы переходными тамбурами.
Общая техническая характеристика тепловоза
Род службы:………………………..……………Грузовой, магистральный;
Тип передачи:…………………...………Электрическая, постоянного тока;
Мощность дизеля:…………………………………...…2210 кВт.(3000 л.с.);
Осевая формула:……………………………………………….………..3о-3о;
Масса тепловоза:………………………………………………….…….138*2;
Нагрузка от колёсной пары на рельсы:……………………….….…..226 кН;
Скорость длительного режима:……………………………...……....24 Км/ч.;
Конструкционная скорость:……………………………………….100 км/ч.;
Ширина колеи:………………………………………………………1520 мм.;
Диаметр колёс:……………………………………...……………….1050 мм.;
Минимальный радиус проходимых кривых:…………………………125 м.;
Длина:……………………………………………………………..16969*2мм.;
Ширина:……………………………………………………………...3080 мм.;
Высота:…………………………………………………...…………..4948 мм.;
Дизель 10Д100
Установленный на тепловозе дизель создан на базе дизеля 2Д100. По конструкции примерно 80% деталей и сборочных единиц дизеля 10Д100 аналогичны деталям и сборочным единицам дизеля 2Д100 Мощность дизеля увеличена до 2206 кВт путем повышения давления надувочного воздуха с 0,03 до 0,13 МПа, его промежуточного охлаждения и увеличения цикловой подачи топлива.[1]
Рис.1: Дизель-Генератор 10Д100: 1, 17—валы отбора мощности, 2—масляный насос, 3—регулятор частоты вращения, 4—выпускной патрубок, 5—тахометр, 6—компенсатор, 7—турбокомпрессор, 8—маслоотделитель, 9—блок цилиндров, 10—крышка блока, 11—трубопровод воздушный, 12—топливный насос, 13—форсунка, 14—верхний шатун, 15—верхний коленчатый вал, 16—вертикальная передача, 18—нагнетатель второй ступени, 19— воздухоохладитель, 20—валоповоротный механизм, 21—генератор, 22— муфта привода генератора, 23—нижний коленчатый вал, 24—нижний шатун, 25—поддизельиая рама, 26—антивибратор, 27—привод масляного насоса и регулятора, 28, 29—смотровые люки, 30—маслопровод, 31, 37—коренные подшипники, 32—распределительный вал, 33, 36— поршни верхний и нижний, 34—втулка цилиндра, 35—водяной патрубок, 38—сетка
|
Основные данные дизеля:
Марка:.......................................................................................................10Д100;
Тактность:...........................................................................................................2;
Расположение цилиндров:......................................однорядное, вертикальное;
Число цилиндров:........................................................................................10 шт;
Диаметр цилиндра:..................................................................................207 мм.;
Ход поршня:…………………………………………………..............2x254 мм;
Частота вращения коленчатого вала на номинальном режиме: ………………………………………………………….………….......850 об/мин.;
Масса дизеля:………………………………………………..………..…. 28,3 т.;
Удельный расход топлива:………………………….…..…...……217 г / кВт·ч;
Удельных расход масла:……………………………………………..…….1,7%.
Тяговый генератор
Для преобразования механической энергии дизеля в электрическую и питания тяговых электродвигателей на тепловозах установлен тяговый генератор (рис. 2). При пуске дизеля генератор используется в качестве электродвигателя с последовательным возбуждением, получая питание от аккумуляторной батареи. Генератор представляет собой десятиполюсную электрическую машину постоянного тока с независимым возбуждением. Обмотка возбуждения питается от якоря возбудителя В-600 двухмашинного агрегата А-706Б и создает основной магнитный поток. Схема регулирования возбуждения генератора обеспечивает использование всей свободной мощности и автоматическое регулирование напряжения генератора в соответствии с током, потребляемым электродвигателями в диапазоне от продолжительного тока до максимального напряжения.
|
Рис.2: Тяговый генератор ГП-311Б (продольный и поперечный разрезы) 1—отверстия выброса охлаждающего воздуха, 2—лапа генератора, 3—роликоподшипник, 4— трубка подачи смазки, 5—коллектор, 6—подшипниковый щит, 7—щеткодержатели, 8—крышка кол лекторной камеры, 9—бракеты, 10—изоляторы, 11—поворотная траверса, 12—уравнители, 13— пусковая обмотка, 14—обмотка независимого возбуждения, 15—станина, 16—главный полюс, 17— добавочный полюс, 18—сердечник якоря, 19—обмотка добавочного полюса, 20—обмотка якоря, 21—воздухоподводящий патрубок, 22—корпус якоря, 23—электрошетки
Техническая характеристика генератора ГП-311Б тепловоза 2ТЭ10М
Мощность:..............................................................................................2000 кВт
Номинальная частота вращения:......................................................850 об/мин
Продолжительный ток:.............................................................................4320 А
Напряжение при продолжительном токе:.................................................465 В
Максимальный кратковременный ток:…................................................6600 А
Максимальное напряжение:........................................................................700 В
Ток при максимальном напряжении:......................................................2870 А
КПД в номинальном режиме:....................................................................94,3%
Расход охлаждающего воздуха:.............................................................4,16 м /с
Падение статического давления внутри генератора:..............................981 Па
Масса:.........................................................................................................8700 кг
Рис. 3. Электродвигатель постоянного тока тяговый типа ЭД-118Б: 1—трубка подачи смазки, 2—коллектор, 3—подшипник роликовый; 4—щит подшипниковый, 5—щеткодержатель; 6—кронштейн; 7—щетка; 8 — палец щеткодержателя; 9—катушка добавочного полюса; 10—остов; 11—шайба нажимная передняя, 12—сердечник добавочного полюса; 13—сердечник главного полюса; 14—якорь необмотанный; 15—катушка главного полюса, 16—катушка якорная; 17—шайба нажимная задняя, 18—дренажное отверстие; 19—лабиринтное кольцо, 20—вал якоря,21—подшипник; 22—щит подшипниковый
Магнитный поток главных полюсов, взаимодействуя с током якорной обмотки, создает на валу якоря тягового электродвигателя вращающий момент, передаваемый через редуктор колёсной паре. Добавочные полюсы служат для создания коммутирующего магнитного потока, способствующего обеспечению коммутации якорной обмотки без подгара коллекторных пластин и щеток. Для обеспечения широкого диапазона изменения частоты вращения вала якоря тягового электродвигателя в схеме тепловоза предусмотрены две ступени ослабления магнитного потока главных полюсов и гиперболическая форма внешней характеристики тягового генератора.
В отличие от обычных электрических машин постоянного тока тяговый электродвигатель имеет конструктивные особенности, связанные со специфическими условиями работы и монтажом его на тепловозе (габаритные размеры и форма из-за необходимости вписывания в пространство, ограниченное шириной колеи и диаметром колеса тепловоза и типом подвески электродвигателя; вибрация и удары на стыках рельсов, воздействие снега, дождя, пыли; температурный интервал окружающей среды от —50 до +40 °С). Вентиляция независимая, осевая, принудительная от вентилятора, приводимого валом дизеля через редуктор, вход охлаждающего воздуха в электродвигатель со стороны коллектора.
|
Техническая характеристика тягового электродвигателя ЭД-118Б:
Мощность:...............................................................................................305 кВт
Напряжение:........................................................................................ 463/691 В
Ток:........................................................................................................ 720/482 А
Частота вращения:...................................................................585/2230 об/мин
КПД:............................................................................................................91,6%.
Расход охлаждающего воздуха:................................................1,33—1,25 м /с
Статическое давление охлаждающего воздуха:………………........1570 Па
Момент на валу:..................................................................................4983 Н • м
Максимальное значение кратковременного тока:…………….........1100 А
Рис 7 Колесные пары для тяговых электродвигателей а — ЭД-118А; б — ЭД-118Б,ЭД-125Б. 1 — ось, 2 — колесный центр, 3 — зубчатое колесо, 4 — бандажное кольцо, 5 — бандаж, 6 — втулка, 7 — разъемный венец колеса привода насоса, 8 — лабиринтное кольцо
Унифицированная колёсная пара тепловозов (ТЭ10М, 2ТЭ116, 2ТЭ10В, 2М62 с бесчелюстными тележками) представлена на рис. 7, а. Ось 1 колесной пары изготовлена из осевой стали. Механические свойства её после термообработки должны соответствовать ГОСТ 3281—81. На поверхности оси различают: буксовые шейки А для установки подшипников букс; предподступичные части Б, служащие для установки лабиринтных колец уплотнения букс подступичные части В, на которые напрессовывают колёсные центры 2 и зубчатое колесо 3; шейки Г моторно-осевых подшипников и среднюю часть Д. Все переходы с одного диаметра оси на другой выполнены плавными переходными галтелями радиусом 20—60 мм с шероховатостью <0,63 во избежание концентрации напряжений. Все наружные поверхности оси упрочняют накаткой стальными роликами, создавая в поверхностном слое высокие остаточные напряжения сжатия, которые в 1,5—2 раза повышают предел выносливости оси в зонах неподвижных посадок и делают ось менее чувствительной к концентрации напряжений. Глубина упрочненного слоя после накатки достигает 6—7 мм, поверхностная твердость металла повышается на 25—30 %. Шейки осей накатывают сферическими роликами, затем шлифуют или подвергают обработке цилиндрическим роликом для сглаживания поверхности. На концах оси выполнены: кольцевая канавка Е для установки стопорного кольца, предохраняющего внутреннее кольцо роликового буксового подшипника от сползания с шейки; проточка Ж, на которую напрессовывают кольцо подшипника типа 8320 осевого упора буксы. В торцах оси выполнены центровые отверстия, позволяющие в процессе эксплуатации производить обточку колёс для восстановления профиля бандажей колёсных пар и устанавливать вкладыш и втулки привода скоростемера (сечение С — С). На пояске торца оси между проточкой Ж и фаской центрового отверстия наносят знаки маркировки и клейма приемки колёсных пар согласно ГОСТ 11018—76.
Буксы. Буксы передают вертикальные и горизонтальные (силы тяги и торможения, поперечные от набегания на рельс) силы между рамой тележки и колёсными парами. Кроме того, буксы ограничивают продольные и поперечные перемещения колёсной пары относительно рамы тележки. Вертикальные статические нагрузки на буксы достигают 94—100 кН, а при движении тепловоза они возрастают в 1,3—1,5 раза. Одновременно на буксовые узлы действуют продольные тяговые и тормозные усилия 20—25 кН, удары колёс на стыках, вызывающие ускорения букс (7—25g), и рамные усилия до 50— 75 кН. Совокупностью этих действующих сил определяется конструкция буксового узла, которая должна обеспечить прежде всего безопасность движения, эксплуатационную долговечность подшипников не менее 2,5 млн. км пробега.
Рис. 8. Буксовый узел: а — крайней колесной пары; б — осевой упор средней колесной пары; 1 — лабиринтное кольцо; 2 — стопорный болт; 3 — шайба; 4 — задняя крышка; 5, 20 — шелковые шнуры; 6 — роликоподшипник; 7— корпус буксы; 8, 9 — дистанционные кольца; 10, 12—стопорные кольца; 11 — кронштейн; 13 — упорный подшипник; 14 — амортизатор; 15 — передняя крышка; 16 — пружина; 17 — упор; 18 — контровочная проволока; 19, 22— болты; 21 — коническая пробка; 23 — поводок
Корпус буксы 7 (рис.8) двумя поводками 23 соединен с рамой тележки. Соединение валиков поводков с корпусом буксы и рамой тележки производится посредством клиновых соединений. Литой корпус буксы имеет также и два боковых опорных кронштейна (крыла) для установки пружин рессорного подвешивания тележки и восприятия вертикальной нагрузки.
В корпусе буксы 7 в пространстве между задней крышкой 4 и передней 15 размещен блок из двух роликовых подшипников 30-32532 Л1М (160Х290Х Х80 мм) с дистанционными кольцами 8 и 9 между ними. Для повышения срока службы подшипники устанавливают в одном буксовом узле с разностью радиальных зазоров не более 0,03 мм. Кроме того, потолок корпуса буксы выполнен в виде свода переменного сечения увеличенной толщины в верхней части, что даёт не только более равномерное распределение нагрузки между роликами, но и увеличение числа роликов, находящихся в рабочей зоне.
На предподступичную часть оси до упора в галтель надевают с натягом лабиринтное кольцо 1. Температура нагрева кольца 120—150 °С. Лабиринтное кольцо образует с задней крышкой 4 четырёхкамерное лабиринтное уплотнение буксы. Внутренние кольца подшипников имеют натяг 0,035— 0,065 мм и насаживаются на шейку оси вместе с дистанционным кольцом 9, нагретым в масле индустриальном до температуры 100—120 °С. Для предотвращения сползания с шейки оси внутренних колец роликоподшипников в случае ослабления их посадки на оси установлено стопорное кольцо 10.
Опоры и возвращающие устройства. Опорно-возвращающее устройство тепловоза воспринимает массу всего надтележечного строения, обеспечивает устойчивое положение тележки под тепловозом при его движении, а также плавное вписывание в кривые и создание необходимых усилий, возвращающих кузов тепловоза в первоначальное положение при перемещении его относительно тележек при движении в кривых.
Взаимное расположение опор главной рамы и опор тележки показано на рис. 9. Для равенства нагрузок от колёсных пар тележек на рельсы передние опоры расположены вокруг шкворня на радиусе 1632 мм, задние — на радиусе 1232 мм. Надтележечное строение тепловоза опирается на раму тележки через четыре комбинированные опоры (рис. 9), состоящие каждая из двух ступеней: нижняя жесткая ступень — роликовая опора качения, верхняя упругая — блок, содержащий семь резинометаллических элементов (РМЭ).
Литой корпус роликовой опоры установлен на боковине рамы тележки по касательной к радиусу ее поворота, обеспечивая поворот тележки на опорах качения нижней опорной плиты 2. Ролики 3 связаны между собой обоймами и вращаются в неметаллических втулках 4, которые являются подшипниками для роликов. Вся подвижная система опоры: ролики с обоймами, верхняя опорная плита 6 при перемещениях направляются приваренными к боковым стенкам корпуса износостойкими накладками 5, изготовленными из стали 65Г. На поверхности качения роликов и опорных плит возникают высокие контактные напряжения, поэтому ролики изготовлены из стали 40Х и закалены на глубину 1,5—3 мм до твердости HRC 54—60.
Рис. 9 Расположение опор на раме тележки 1 — комбинированная опора, 2 — шкворневой узел, А — положение средней колесной пары относительно шкворня
Поверхности качения опорных плит выполнены наклонными: угол наклона составляет 2 °. На прямом участке пути ролики занимают среднее положение между наклонными плоскостями. При повороте тележки относительно кузова ролики накатываются на наклонные поверхности опор. При этом возникают горизонтальные силы, создающие на радиусе опор возвращающий момент. Кроме возвращающих сил, при повороте тележек в опоре возникают силы трения и момент сил трения, который способствует уменьшению колебаний виляния тележек.
Рессорное подвешивание. Рессорное подвешивание тепловоза предназначено для уменьшения динамического воздействия колёс на рельсы при движении по неровностям пути и обеспечения плавности хода тепловоза, передачи массы кузова и тележек на колёсные пары. Рессорное подвешивание позволяет правильно распределить нагрузки от массы тепловоза между колесными парами, а также обеспечивает частичную передачу горизонтальных сил со стороны колёс на раму тележки.
Подвешивание (рис. 10) тепловоза выполнено одноступенчатым, одинарным (только пружины) и индивидуальным для каждого буксового узла колёсной пары. Оно состоит из 12 одинаковых групп пружин (по шесть групп пружин для каждой тележки). Каждая группа имеет два одинарных пружинных комплекта 4, установленных между опорными кронштейнами корпуса буксы 1 и кронштейнами 2 рамы тележки. Параллельно каждой группе рессорного подвешивания устанавливается фрикционный гаситель колебаний 3.
Рис 10 Рессорное подвешивание: 1 — корпус буксы 2 — кронштейн рамы тележки, 3 — фрикционный гаситель колебаний, 4 — пружинный комплект В Г—вертикальный зазор между рамой тележки и неподрессореииыми частями экипажа
Пружинный комплект составляют три пружины: наружная 2, средняя 4, внутренняя 3; две опорные плиты 1 и 5 и регулировочные прокладки 6. Чтобы исключить касание и заскакивание витков одной пружины между витками другой при их концентрическом расположении, внутреннюю пружину размещают в наружной с зазором не менее 5 мм на сторону, причем пружины должны быть навиты в разные стороны. Пружины изготавливают из круглого калиброванного проката горячекатаной пружинной стали 60С2А диаметром: для наружных пружин —36 мм, для средних —23 мм, для внутренних —16 мм. Твердость пружин в термообработанном состоянии HRC 40— 47. После термообработки пружины упрочняют наклёпом дробью.
Статическая нагрузка на пружинный комплект воспринимается пружинами: наружной 63 %, средней 25 %, внутренней 12 %. Предельная нагрузка с учётом 7 % перегруза и динамического прогиба составляет для наружной пружины 40 кН, средней 15 кН, внутренней 8 кН. При действии этих нагрузок в витках при их полном смыкании напряжения не превышают предела текучести материала пружин при кручении, равного 750 МПа.
Для обеспечения постоянной высоты пружинного комплекта под статической нагрузкой пружины по высоте в свободном состоянии разграничивают на группы и формируют комплект из пружин и регулировочных прокладок 6.
Пружинные комплекты собирают и стягивают специальными технологическими болтами 9, которые после окончательной сборки тележки снимают. На одной тележке устанавливают пружинные комплекты только одной из групп. Секция тепловоза может иметь тележки с пружинными комплектами рессорного подвешивания только одной группы или только I и II или II и III. Номер группы жёсткости пружинных комплектов указан в паспорте тепловоза для каждой секции. Колебания надрессорного строения, возникающие при движении тепловоза, гасятся с помощью фрикционных гасителей, включенных параллельно пружинным комплектам.
Подвеска тяговых электродвигателей. Колесно-моторный блок (КМБ) осуществляет кинематическую и силовую связь между тяговым электродвигателем и колёсной парой тепловоза. Блок тепловоза выполнен с опорно-осевой подвеской тягового электродвигателя и односторонней зубчатой передачей. Тяговый электродвигатель одной стороной жёстко опирается на ось колёсной пары через моторно-осевые подшипники, а другой стороной — опорным приливом упруго через пружинную подвеску на раму тележки. При такой подвеске практически половина массы ТЭД жёстко связана с необрессоренными массами колёсной пары и составляет на одном КМБ около 4250 кг. Вращающий момент ТЭД передаётся на колёсную пару через одноступенчатую зубчатую передачу: шестерню, напрессованную на вал якоря и находящуюся в постоянном зацеплении с упругим зубчатым колёсом колесной пары. Шестерня и зубчатое колесо закрыты кожухом, который крепится болтами М42 в трёх точках к корпусу ТЭД. От попадания пыли и влаги торец моторно-осевого подшипника со стороны коллектора ТЭД закрыт хомутом, который выполнен в виде двух полуколец, армированных войлоком. Торец моторно-осевого подшипника со стороны зубчатой передачи находится в контакте со ступицей зубчатого колеса. Для улучшения смазывания поверхностей на торцах передних половин вкладышей имеются по две прорези, в которые при сборке устанавливают войлочные полосы 6X10X160 мм (ГОСТ 288—72). Общее перемещение тягового электродвигателя относительно оси не более 1,2 мм при новом изготовлении.
Рис 11. Подвешивание ТЭД 1 — направляющий стержень, 2,7 — накладки, 3, 6 — нижняя и верхняя балочки, 4 — пружина, 5 — стяжной болт, 8 — тяговый электродвигатель, 9 — кронштейн рамы тележки, 10 — трубчатый выступ, 11—валик, В — рабочая поверхность накладки
Рис12 Колесно моторный блок
1 — тяговый электродвигатель, 2 — кожух тягового редуктора, 3 — шестерня, 4 — колесная пара 5 — упругое зубчатое колесо, 6 — хомут уплотнения, 7 — пружинная подвеска, 8 — моторно осевой подшипник, 9 — опорный прилив
Рис.1 Положение экипажа в кривой с возвышением наружного рельса
Особенностью рельсовой колеи в кривых является возвышение наружного рельса над внутренним, что обеспечивает равномерный износ рельсов обеих нитей, снижение бокового давления на рельсы наружной нити, устойчивость движения экипажа против опрокидывания центробежной силой и ветром, комфортное состояние пассажиров в вагоне.
Величина центробежной силы вычисляется по формуле 3.1
, (3.1)
где Скорость движения экипажа в кривой; м/с
сила давления экипажа (вес локомотива), Н;
ускорение силы тяжести; м/с2;
радиус кривой, м;
Н
При движении экипажа в кривой появляется центробежная сила, которая создаёт дополнительное давление колёс на наружную рельсовую нить. (рис.1). Рассчитаем возвышение наружного рельса
;
, мм
где расстояние между осями рельсов; м
сила давления экипажа (вес локомотива), Н;
Величина центробежной силы, Н
возвышение наружного рельса, мм.
мм.
Из рис.1 можно принять
(3.3)
По малости угла примем
, а
. Подставив значение
из выражения 3.1 получим
(3.4)
мм
Подставив значения и
в выражение 3.3 получим
Подставив в выражение 3.4 м.,
м/с2 и вводя переводные коэффициенты, для того чтобы подставить
в км/ч,
в м., получим выражение 3.5
(3,5)
Где Скорость движения экипажа в кривой, км/ч;
радиус кривой, м;
12,5- постоянная величина
мм.
Для учёта влияния эксцентриситетов расположения экипажа в колее, неподрессоренного и подрессоренного строения экипажа необходимо плюсовать добавку . Для высокоскоростных линий
мм, для линий с преимущественным пассажирским движением
мм. Так как Vmax<100 км/ч, то
.
Если расчёт производится для кривых R<600 м. или Vmax> 70 км/ч, то возвышение вычисляется по формуле 3.6
(3.5)
где допустимая величина непогашенного центробежного ускорения, принимаемой равной 0.7 м/с2.
Максимальная скорость движения экипажа в кривой км/ч;
радиус кривой, м.
мм.
Из полученных результатов расчётов значений и
в качестве окончательного принимается большее. Величина расчётного значения не должна превышать более
мм. Для убеждения выполнения условия
, определяем величину радиуса кривой
, который должен быть установлен при проведении работ по смягчению кривой.
м (3.6)
м
До проведения работ по смягчению кривой максимальная скорость движения допускается по кривой , определяется по формуле 3.7
км/ч (3.7)
км/ч
Таким образом, на основании полученного значения , установили допустимую скорость экипажа в кривой при обеспечении условий безопасности движения и комфортной езды локомотивных бригад.
Список литературы
1) Василенко Г.Л., Зарубин В.М., Федорова Н.Г. Методические указания по применению единой системы конструкторской документации в учебных работах
2) «Локомотивное хозяйство». Под ред. С.Я. Айзинбуда, -М; Транспорт, 1966 г.
3) Конструкция и динамика тепловозов / Под ред. В.Н. Иванова, Транспорт, 1974 г.
4) Филиппов М.М. «Железные Дороги. Общий курс»
5) С.П. Филонов, А.Е. Зиборов, В.В. Ренкунас, Г.А. Пупынин «Тепловозы 2ТЭ10М и 3ТЭ10М»
6) А.Н. Долганов, В.А. Дробинский, под ред. Н.П. Киселёва «Правила Тяговых Расчётов для поездной работы»
Кафедра «Подвижной состав железных дорог»
КУРСОВОЙ ПРОЕКТ
по дисциплине: «ПОДВИЖНОЙ СОСТАВ ЖЕЛЕЗНЫХ ДОРОГ»
на тему: «Исследование экипажной части локомотива»
Выполнил: студент II курса
|
|
Состав сооружений: решетки и песколовки: Решетки – это первое устройство в схеме очистных сооружений. Они представляют...
Папиллярные узоры пальцев рук - маркер спортивных способностей: дерматоглифические признаки формируются на 3-5 месяце беременности, не изменяются в течение жизни...
Автоматическое растормаживание колес: Тормозные устройства колес предназначены для уменьшения длины пробега и улучшения маневрирования ВС при...
Адаптации растений и животных к жизни в горах: Большое значение для жизни организмов в горах имеют степень расчленения, крутизна и экспозиционные различия склонов...
© cyberpedia.su 2017-2024 - Не является автором материалов. Исключительное право сохранено за автором текста.
Если вы не хотите, чтобы данный материал был у нас на сайте, перейдите по ссылке: Нарушение авторских прав. Мы поможем в написании вашей работы!