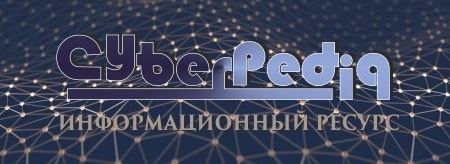
Поперечные профили набережных и береговой полосы: На городских территориях берегоукрепление проектируют с учетом технических и экономических требований, но особое значение придают эстетическим...
Папиллярные узоры пальцев рук - маркер спортивных способностей: дерматоглифические признаки формируются на 3-5 месяце беременности, не изменяются в течение жизни...
Топ:
История развития методов оптимизации: теорема Куна-Таккера, метод Лагранжа, роль выпуклости в оптимизации...
Методика измерений сопротивления растеканию тока анодного заземления: Анодный заземлитель (анод) – проводник, погруженный в электролитическую среду (грунт, раствор электролита) и подключенный к положительному...
Теоретическая значимость работы: Описание теоретической значимости (ценности) результатов исследования должно присутствовать во введении...
Интересное:
Принципы управления денежными потоками: одним из методов контроля за состоянием денежной наличности является...
Отражение на счетах бухгалтерского учета процесса приобретения: Процесс заготовления представляет систему экономических событий, включающих приобретение организацией у поставщиков сырья...
Как мы говорим и как мы слушаем: общение можно сравнить с огромным зонтиком, под которым скрыто все...
Дисциплины:
![]() |
![]() |
5.00
из
|
Заказать работу |
|
|
При испытании на твёрдость по методу Бринелля в поверхность материала вдавливается твердосплавный шарик диаметром Д под действием нагрузки Р, после снятия нагрузки измеряется диаметр отпечатка d (см. рисунок 5.1а).
Процесс измерения твёрдости по Бринеллю состоит из следующих основных последовательно выполняемых операций:
а) подготовка образцов материала к испытанию. Образец материала должен иметь параллельные поверхности (испытуемую и опорную), без окалины, ржавчины или каких-либо неровностей. При необходимости эти поверхности подвергают специальной зачистке при обработке наждачной бумагой, шлифовальным кругом или напильником, при этом образец не должен нагреваться выше 120–150 °С. Минимальная толщина образца материала должна быть не менее десятикратной глубины отпечатка;
б) находят по таблице 5.1 диаметр шарика Д, нагрузку Р и время выдержки под нагрузкой t;
Таблица 5.1 – Рекомендуемые параметры испытаний по Бринеллю
Материал | Интервал твёрдости в числах Бринелля | Толщина испытуемого образца, мм | Соотношение между нагрузкой Р и диаметром шарика Д | Диаметр шарика, мм | Нагрузка Р, числитель кГс, знаменатель Н | Выдержка под нагрузкой, с |
Чёрные металлы | 140–150 | 6-3 4-2 <2 | ![]() | 10 5 2,5 | 3000/29400 750/7358 187,5/1839 | 10 |
То же | <140 | >6 6-3 <2 | ![]() | 10 5 2,5 | 1000/9810 250/2459 62,5/613 | 10 |
Цветные металлы | >130 | 6-3 4-2 <2 | ![]() | 10 5 2,5 | 3000/29400 750/7358 187,5/1839 | 30 |
То же | 35–130 | 9-3 6-3 <3 | ![]() | 10 5 2,5 | 1000/9810 250/2459 62,5/613 | 60 |
То же | 8–35 | >6 5-3 <3 | ![]() | 10 5 2,5 | 250/2453 62,5/613 15,6/153 | 60 |
в) подготовка твердомера ТШ к испытаниям. Шарик, выбранный по таблице 5.1, закрепляют в держателе 3 (см. рисунок 3.2) и устанавливают необходимую нагрузку Р на приборе. Нагрузка создаётся массой рычажной системы 13, подвески 11 и сменными грузами 12. В зависимости от формы испытуемого образца подбирают опорный столик 6. Твёрдость плоских образцов измеряют на плоском столике, а цилиндрических – на призматическом. После этого соответствующим перемещением подвижной чашки 8 по отношению шкалы, расположенной на станине прибора, устанавливают время выдержки образца под нагрузкой. Чашку 8 в нужном положении закрепляют винтом 9;
|
г) работа с прибором при испытании. Испытуемый образец материала 5 устанавливают на столике 6 таким образом, чтобы центр отпечатка располагался от края образца на расстоянии не менее 2,5 диаметра, а от центра соседнего отпечатка – не менее двух диаметров отпечатка. Затем подводят образец к шарику, для чего вращают маховик 10 до упора образца в ограничитель 4, а при отсутствии последнего – до сжатия пружины 20. Нажатием кнопки 7 включают электродвигатель 17, который через червячный редуктор 18, кривошипный вал 16 и шатун 15 отводит вниз ролик 14. Вследствие этого действие нагрузки Р через систему рычагов 13, стержень 19, шпиндель 21 сообщается шариковому наконечнику 22. Этот момент фиксируется загоранием лампочки 1. После соответствующей выдержки испытуемого образца под действием нагрузки Р вращение электродвигателя переключается автоматически на обратное: ролик 14 перемещается вверх, возвращает рычаг 13 в исходное до нагрузки шарика положение, электродвигатель автоматически отключается, и лампочка гаснет;
Рисунок 5.2 – Схема устройства твердомера ТШ
д) определение показателя твёрдости. Для определения числа твёрдости НВ по диаметрам отпечатка d пользуются специальной таблицей. Максимальная твёрдость испытуемых образцов металлов и сплавов не должна превышать 450 НВ. Испытание более твёрдых металлов повлечёт за собой деформацию шарика, твёрдость которого 650 НВ.
Испытание на твёрдость одного и того же образца производится дважды, при этом при каждом испытании диаметр отпечатка измеряется в двух взаимно перпендикулярных направлениях с помощью специального отсчётного микроскопа МПБ-2 с точностью до сотых долей миллиметра. Схема измерения диаметров d 1и d 2 приведена на рисунке 3.3.
|
При Д = 10 мм, Р= 29400 Н и времени выдержки под нагрузкой 10 с твёрдость по Бринеллю обозначается символом НВ с указанием числа твёрдости. При этом размерность (кГс/мм2) не ставится, например 200 НВ.
При использовании шариков других диаметров (2,5 и 5 мм) изменяется нагрузка вдавливания, а символ твёрдости НВ дополняется тремя индексами.
Например, 180 НВ 2,5/187,5/30 обозначает, что при Д = 2,5 мм, Р= 187,5 кГс (1839 Н) и времени выдержки под нагрузкой 30 с число твёрдости по Бринеллю равно 180.
0 1 2 3 4 5 6 7 |
2 |
1 |
d 1 |
d 2 |
Рисунок 5.3 – Схема измерения диаметра отпечатка c помощью отсчётного микроскопа
|
|
Типы сооружений для обработки осадков: Септиками называются сооружения, в которых одновременно происходят осветление сточной жидкости...
История создания датчика движения: Первый прибор для обнаружения движения был изобретен немецким физиком Генрихом Герцем...
Автоматическое растормаживание колес: Тормозные устройства колес предназначены для уменьшения длины пробега и улучшения маневрирования ВС при...
Своеобразие русской архитектуры: Основной материал – дерево – быстрота постройки, но недолговечность и необходимость деления...
© cyberpedia.su 2017-2024 - Не является автором материалов. Исключительное право сохранено за автором текста.
Если вы не хотите, чтобы данный материал был у нас на сайте, перейдите по ссылке: Нарушение авторских прав. Мы поможем в написании вашей работы!