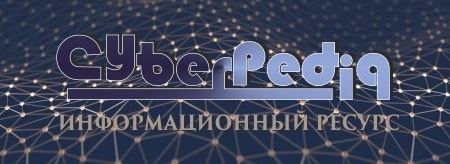
Опора деревянной одностоечной и способы укрепление угловых опор: Опоры ВЛ - конструкции, предназначенные для поддерживания проводов на необходимой высоте над землей, водой...
Адаптации растений и животных к жизни в горах: Большое значение для жизни организмов в горах имеют степень расчленения, крутизна и экспозиционные различия склонов...
Топ:
Характеристика АТП и сварочно-жестяницкого участка: Транспорт в настоящее время является одной из важнейших отраслей народного хозяйства...
Оснащения врачебно-сестринской бригады.
Особенности труда и отдыха в условиях низких температур: К работам при низких температурах на открытом воздухе и в не отапливаемых помещениях допускаются лица не моложе 18 лет, прошедшие...
Интересное:
Уполаживание и террасирование склонов: Если глубина оврага более 5 м необходимо устройство берм. Варианты использования оврагов для градостроительных целей...
Лечение прогрессирующих форм рака: Одним из наиболее важных достижений экспериментальной химиотерапии опухолей, начатой в 60-х и реализованной в 70-х годах, является...
Как мы говорим и как мы слушаем: общение можно сравнить с огромным зонтиком, под которым скрыто все...
Дисциплины:
![]() |
![]() |
5.00
из
|
Заказать работу |
|
|
Общие законы организации
Этих законов несколько:
1). Основной закон организации – это закон синергетического эффекта.
Заключается в том, что сумма свойств системы превышает арифметическую сумму свойств всех входящих в данную систему элементов.
Впервые особенности проявления синергетического эффекта рассматривал Богданов.
2). Закон единства анализа и синтеза.
Заключается в том, что процессы разделения специализации и дифференциации необходимо дополнять противоположными процессами соединения и интеграции.
3). Закон пропорциональности означает необходимость поиска и использования наиболее рационального соотношения между отдельными частями производственной структуры.
4). Закон композиции предполагает, что целью деятельности любой подсистемы промышленной структуры является выполнение основных целей организации в целом.
5). Закон организованности предполагает, что производственная структура рационально функционирует, если объем информации не превышает возможностей данной системы.
рганизации производства на промышленных предприятиях присущи определенные закономерности.
В числе этих закономерностей следует назвать соответствие организации производства ее целям.
Эта закономерность предопределяет методические подходы к формированию организации производства с учетом требований наиболее полного использования ресурсов, усиления творческого характера труда, создания организационных условий для реализации материальной заинтересованности трудящихся в результатах производства, которые отражают основные цели организации. Достижение намеченных целей обеспечивается решением соответствующих этим целям организационных задач. Характер таких задач весьма разнообразен и определяется особенностями объекта организации.
|
Так, например, важными задачами, которые должны быть решены для реализации целей организации производства на участке, являются: создание необходимых пропорций в производственной мощности участка, установление рационального баланса рабочих мест и исполнителей, согласование времени выполнения операций на всех рабочих местах, распределение трудовых функций между рабочими, формирование оперативных планов и выдача заданий рабочим, создание стимулов к труду, организация технического обслуживания рабочих мест и т.п.
Другой закономерностью является соответствие форм и методов организации производства характеристикам его материально-технического базиса. Согласно этой закономерности содержание организации производства определяется особенностями и уровнем развития техники и технологии.
Ручной труд, механизированное производство и комплексно-автоматизированный производственный процесс требует разной организации. Изменения, происходящие в технических средствах и технологии производства, ведут к переменам в содержании труда и квалификации работающих и, как следствие, к изменениям в характере организации производства.
Названная закономерность предполагает необходимость обеспечения адекватности состояния и уровня организации производства постоянно изменяющемуся под влиянием научно-технического прогресса материальному базису производства.
Соответствие организации производства конкретным производственно-техническим условиям и экономическим требованиям производства является одной из существенных закономерностей. Характер форм и методов организации производства определяется видом выпускаемой продукции, типом производства, его масштабами и т. п.
В зависимости от тех или иных условий в процессе организации производства применяются соответствующие им организационные решения: выбираются вид специализации цехов и участков, способ размещения оборудования, форма организации производственных процессов (поточная, групповая и др.), определяется тип планово-учетной единицы в системе оперативного планирования.
|
Организация производства должна также адаптироваться к меняющимся экономическим условиям, требующих использования таких организационных форм, которые создавали бы необходимые предпосылки для реализации экономически обоснованных методов ведения производства.
Переход к работе в условиях рыночной экономики предъявляет ряд новых требований к организации производства. Организация производства должна стать более гибкой, эластичной, способной быстро и с минимальными затратами перестраиваться на выпуск продукции, необходимой потребителю; она в большей степени должна быть сориентирована на повышение качества. Для оценки эффективности организации производства следует применять показатели, характеризующие использование всех видов ресурсов с учетом их взаимозаменяемости.
Комплексность организации производства как общая закономерность предполагает необходимость рассмотрения всех производственных процессов, протекающих на предприятии, во взаимной связи как единое интегрированное целое.
На современном предприятии, в условиях комплексной механизации и автоматизации технические средства производства и производственные процессы все больше интегрируются. Создаются системы машин, автоматически выполняющие не только основные технологические, но и транспортные, складские, контрольные операции. На основе внедрения систем автоматизированного проектирования и автоматизации управления появляются единые системы подготовки производства и изготовления продукции.
Интегрируются основные производственные процессы, процессы технического обслуживания и материального обеспечения. Все эти изменения обусловливают комплексный характер проблем организации производства.
Непрерывное улучшение организации производства является непременным условием поддержания состояния организации на современном уровне. Эта закономерность предъявляет требование перехода от поэтапного к постоянному (текущему) совершенствованию организации производства.
|
В связи с этим в системе управления предприятием появляется новая самостоятельная функция постоянного организационного совершенствования производства. Изменения в существующую организацию производства должны вноситься непрерывно по мере изменений технического базиса производства, характера выпускаемой продукции, состава и квалификации кадров, а также как результат поисков новых, прогрессивных форм и методов организации и управления производством.
В современных условиях все более проявляется закономерность, выражающаяся в соответствии форм и методов организации производства требованиям повышения содержательности труда рабочих, расширения их трудовых функций, обеспечения привлекательности труда. При выборе форм организации труда необходимо учитывать квалификационный и культурный уровень работающих, заботиться о том, чтобы труд приносил удовлетворенность работнику, стимулировать творческую активность и рационализаторскую деятельность участников производства.
При организации производства следует учитывать особенности деятельности предприятия в условиях рынка и ориентироваться на стабилизацию занятости работников предприятия. Трудящийся должен быть уверен, что высокая производительность его личного труда и эффективная работа предприятия обеспечат ему гарантию занятости.
Взаимное соответствие структуры системы управления и характеристик организации производства, являясь одной из закономерностей организации, обусловливает необходимость постоянной работы по поддержанию этого соответствия. Производственная структура объединений и предприятий, методы организации производственных процессов находятся в постоянном движении. В большинстве случаев эти изменения требуют перемен в системе управления, в ее структуре.
Так, повышение самостоятельности и ответственности низовых звеньев предприятий и объединений в новых условиях хозяйствования ведет к сокращению числа линейных руководителей и подразделений, занятых регламентацией и контролем. Возрастает значение штабных подразделений, занятых техническим и материальным обеспечением производства. Такая перестройка системы управления требует передачи всех производственных функций из органов управления в низовые производственные звенья - цехи, участки, бригады, а всех функций технической подготовки и материального обеспечения - в штабные подразделения.
|
В передовых отраслях машиностроения осуществляется переориентация производственной структуры с производственных процессов на продукт, что ведет к созданию предметно-замкнутых цехов и участков, производств по выпуску определенных изделий. В этих условиях происходят и изменения системы управления, которые идут в направлении создания соответствующих структурных звеньев с учетом новых экономических условий.
Важной закономерностью организации производства следует считать участие трудящихся в работе по организации производства на предприятиях и в объединениях.
2. Принципы рациональной организации производственных процессов
Всего выделяют около 25-30 принципов. Основные из них:
1. Принцип специализации. Под специализацией понимается ограничение номенклатуры изготавливаемых изделий, близких по назначению и конструкции или ограничения номенклатуры процессов, применяемых для изготовления изделий различных по назначению и конструкции.
Применительно к организации производственных процессов, принцип специализации означает сужение номенклатуры продукции, изготавливаемой в каждом производственном звене, вплоть до рабочего места, также ограничения разновидностей производственных процессов.
Уровень специализации повышается путем проведения конструктивной, технологической и организационной унификации.
Унификация – это приведение продукции, способов и методов ее производства к единой форме, размерам, структуре и составу.
2. Принцип параллельности предполагает одновременное параллельное выполнение отдельных операций и процессов по изготовлению продукции.
Принцип имеет большое значение при производстве сложных изделий, состоящих из многих деталей, узлов и агрегатов.
Параллельность достигается за счет рационального расчленения изделий на составные части и совмещение времени различных операций над изделиями одного наименования, а также одновременным изготовлением разных изделий.
На отдельных рабочих местах параллельность достигается путем многоинструментальной обработки предметов труда и совмещением времени основных и вспомогательных операций.
3. Принцип непрерывности производственных процессов требует, чтобы в процессе изготовления продукции перерывы между последовательно выполняемыми технологическими операциями были сведены к минимуму или полностью ликвидированы.
|
Полностью этот принцип выполняется в технологически непрерывных производствах.
4. Принцип пропорциональности заключается в том, что во всех частях производственного процесса или во всей взаимосвязанной системе оборудования должна быть равная пропускная способность по выпуску продукции.
Это достигается тогда, когда производительность оборудования во всех операциях технологического процесса пропорциональна трудоемкости обработки изделия на этих операциях с учетом производственной программы.
Ежегодно на предприятиях разрабатываются мероприятия по ликвидации «узких мест» производственной мощности и таким образом стремится к выравниванию нагрузок различных подразделений.
5. Принцип прямоточности предполагает, что предметы труда должны проходить кратчайший путь по всем стадиям и операциям производственного процесса без встречных и возвратных перемещений.
Соблюдение этого принципа обеспечивается расположением цехов, участков и рабочих мест по ходу технологического процесса.
6. Принцип ритмичности означает, что работа всех подразделений предприятия и выпуск готовой продукции подчиняются определенному ритму, то есть повторяемости.
При соблюдении этого принципа в равные промежутки времени выпускается одинаковое или равномерно нарастающее количество продукции, а также обеспечивается равномерная загрузка рабочих мест и исполнителей.
7. Принцип гибкости означает, что производственный процесс эффективно адаптируется к изменению рыночных требований, а также организационно-технических параметров производства.
То есть производственная система способна обеспечивать освоение новых изделий в кратчайшие сроки вне зависимости от конструктивных и технологических особенностей продукции.
Все принципы необходимо использовать одновременно для повышения эффективности производства.
3 Производственная организация как система
Классификация инструмента
КЛАССИФИКАЦИЯ ИНСТРУМЕНТА
Итак, весь инструмент можно условно поделить на следующие группы:
1. Режущий инструмент.
2. Слесарно-монтажный инструмент.
3. Вспомогательный и зажимной инструмент, а также оснастка.
4. Инструмент, работающий методом пластической деформации.
5. Абразивный инструмент.
6. Измерительный инструмент.
Режущий инструмент – инструмент для обработки резанием.
ОСНОВНЫЕ ВИДЫ РЕЖУЩЕГО ИНСТРУМЕНТА
1. Инструмент токарной группы. В основном это резцы.
2. Инструмент фрезерной группы. В основном это фрезы.
3. Инструмент для обработки отверстий. Это сверла, зенкера, развертки, зенковки.
4. Резьбонарезной инструмент. Это метчики, плашки.
5. Зубообрабатывающий инструмент. Это долбяки, червячные фрезы и прочее.
6. Протяжной инструмент. Это протяжки, прошивки и т.д.
Потребность предприятия в инструменте и технологической оснастке (далее в инструменте) складывается из расходного и оборотного фондов.
Расходный фонд – это годовая потребность в инструменте для выполнения запланированного объема и номенклатуры продукции. Расчет потребности по каждому виду инструмента ведется по утвержденным нормам расхода и годовой производственной программы. Расход режущего инстру мента Rпл.р.и. по каждой операции определяется по формуле
,
где Qгод – годовой объем выпуска продукции (тыс. шт.);
nн.р.и. – норма расхода инструмента на 1000 изделий (шт.).
Обычно нормы расхода инструмента устанавливаются на 1000 деталей или 1000 станкочасов работы оборудования.
Норма расхода режущего инструмента на 1000 деталей рассчитывается по формуле
,
где tм – машинное время на обработку одной детали (мин);
kу – коэффициент случайной убыли инструмента (kу >1);
tр – расчетное время работы инструмента до полного износа (час).
Аналогично рассчитываются нормы расхода абразивного инструмента.
Расход вырубных штампов по каждой операции (Rпл.ш) можно рас считать по формулам:
где
где Qгод – годовой объем выпуска деталей (шт.);
nизн.ш – число ударов штампа до полного износа матрицы (шт.);
nм. – число сменных матриц до износа нижней плиты штампа (шт.);
kш – коэффициент снижения стойкости штампа после каждой переточки;
dст. – число переточек матрицы до полного износа;
nуд. – стойкость матрицы между двумя переточками (количество ударов штампа);
hст.м – допустимое стачивание матрицы (мм);
hпер.м – слой металла, снимаемый при переточке матрицы (мм).
Оборотный фонд – запас инструмента (Zоб.) для обеспечения нормальной работы производства, образующийся из:
– складских запасов в ЦИСе и ИРК (Zскл.);
– эксплуатационного фонда на рабочих местах (Zр);
– инструмента в заточке (Zз);
– инструмента в ремонте (Zрем);
– инструмента на контроле (Zк)
Zоб = Zскл. + Zр. + Zз. + Zрем. + Zк.
Размер запасов в основном устанавливается по системе "максимум-минимум", то есть каждый вид инструмента имеет три нормы запаса (рис.5):
– максимальный Z max;
– минимальный Z min;
– запас в "точке заказа" Z т.з.
Эти нормы запаса рассчитываются по формулам:
Zmax = Rдн. Tпз. + Zmin;
Zmin = Rдн. Tс.изг.;
Zт.з. = Rдн. Tн.изг.,
где Rдн. – среднедневная потребность ИРК цехов в данном инструменте (шт); Tп.з. – периодичность пополнения запаса (дн.); Тс.изг. и Tн.изг. – время срочного и нормального изготовления пар тии инструмента или приобретения партии покупного инструмента (дн.).
Запас точки заказа (Zт.з.) отражает такую величину запаса, при которой должен выдаваться заказ на изготовление или приобретение инструмента. Объем партии заказа (Zпар.) равен
Zпар. = Zmax – Zmin.
Рис.5. График расчета запасов инструмента по системе "максимум-минимум"
Управление запасами
Фрагмент из книги "Управление производством на базе стандарта MRP II"
Издательство "Питер"
Подробнее о книге...
Как мы уже упоминали в предыдущей главе, основной идеологией MRP-системы является планирование пополнения запасов номенклатурных позиций таким образом, чтобы как можно сильнее, в идеале полностью, исключить все запасы на предприятии. Наряду с этим мы отмечали, что реальная жизнь богаче теории, и зачастую имеют место обстоятельства, отклоняющие логику работы MRP-системы от идеала. В любом случае необходимо рассмотреть, что представляют собой запасы, каковы их основные функции, как могут быть построены системы управления ими, на какие обстоятельства необходимо обращать внимание при выборе и построении этих систем, какие операции с запасами производятся на предприятии и как они отражаются в MRP-системе и, наконец, как можно построить систему контроля за адекватностью данных о запасах в базе данных реальному положению дел. Все эти и некоторые другие вопросы мы затронем в этой главе.
Функции и виды запасов
Основной задачей управления запасами является инвестирование средств в запасы таким образом, чтобы достигать стратегических целей бизнеса. Запасы часто используются как критерий суждения об эффективности планирования, производства и управления в целом в компании. Основной мотив управления запасами - формирование <буфера> для нейтрализации колебаний в поставках и спросе. Колебания могут возникать по следующим причинам:
Запасы выполняют следующие основные функции, в соответствии с выполнением которых могут быть выделены виды запасов по исполняемым ими функциям.
- для нейтрализации <нормальных> колебаний спроса (изменение темпов продаж), в форме параметра планирования <страховой запас> (краткое описание данного параметра приведено в главе 4);
- для нейтрализации отклонений в поставках (по длительности цикла поставки), в форме параметра планирования <страховое время> (краткое описание данного параметра приведено в главе 4).
- для преодоления последствий неконтролируемых будущих событий (забастовки в компании и у поставщиков, политическая нестабильность в стране, откуда поставляется важное сырье, и др.);
- для страховки от вероятного повышения цены поставщиком.
ABC-анализ
Сущность этого анализа заключается в том, что производится классификация всех номенклатурных позиций, данные о запасах которых поддерживаются по признаку относительной важности этих позиций, и для каждой выделенной категории формируются свои методики управления запасами. Обычно прибегают к трехступенчатому ранжированию номенклатурных позиций: на классы A, B и C. Можно сказать также, что для различных категорий номенклатурных позиций устанавливаются различные уровни контроля за их запасами.
ABC-анализ базируется на принципе Парето (Вильфредо Парето, XIX век), сформулировавшего правило, суть которого сводится к следующему: контроль относительно небольшого количества элементов позволяет контролировать ситуацию в целом. Часто еще сформулированное Парето правило именуют правилом 80/20, что можно истолковать следующим образом: надежный контроль 20% номенклатурных позиций позволяет на 80% контролировать систему (т. е. запасы в нашем случае).
Среди основных факторов, которые могут влиять на присвоение запасам номенклатурной позиции той или иной категории контроля, Д. Фогарти, Дж. Блэкстоун и Т. Хоффманн [4] выделяют следующие.
В MRP-системах, как правило, существует возможность как задать номенклатурной позиции определенный ABC-класс вручную, так и получить отчет с рекомендациями системы относительно присвоения класса. При этом, когда MRP-система формирует соответствующий отчет, она основывается главным образом на первом из приведенных выше факторов, так как он может использоваться благодаря накоплению в системе необходимых для этого статистических данных, с одной стороны, и представляется достаточно репрезентативным признаком класса номенклатурной позиции в долгосрочной перспективе для работающих предприятий, с другой стороны.
Прочие признаки могут использоваться при проведении классификации уполномоченными на то работниками предприятия, однако значительная их часть с трудом поддается простой и полной формализации, и встречаются трудности с накоплением необходимых исходных данных.
Если компания решила применять несколько признаков классификации одновременно, то номенклатурной позиции присваивается наивысшая из категорий.
После присвоения каждой номенклатурной позиции определенного класса к каждому из классов применяются свои правила контроля запасов. В сжатом виде они указаны Д. Фогарти, Дж. Блэкстоуном и Т. Хоффманном в [4].
Для номенклатурных позиций класса A рекомендуются следующие правила.
Для номенклатурных позиций класса B применяются те же меры, что и для номенклатурных позиций класса A, но реже и с большими приемлемыми допусками.
Для номенклатурных позиций класса C сформулированы следующие правила.
Рассмотрим простой пример проведения ABC-классификации номенклатурных позиций по критерию объема потребления в стоимостном выражении.
Пусть имеется десять номенклатурных позиций, известен объем их потребления в натуральном и стоимостном выражении за некоторый плановый период (скажем, год). Сводка по этим номенклатурным позициям приведена в таблице на рис. 6.1.
Пример применения ABC-анализа
Номенклатурная позиция | Цена за единицу | Объем использования за год | Объем использования за год в стоимостном выражении | Процент от итога |
0,05 | 34,3% | |||
0,11 | 3,0% | |||
0,16 | 0,9% | |||
0,08 | 0,8% | |||
0,07 | 4,6% | |||
0,15 | 2,7% | |||
0,20 | 46,7% | |||
0,04 | 0,2% | |||
0,09 | 6,2% | |||
0,12 | 0,7% | |||
Итого | 100,% |
Рис. 6.1. Исходные данные для проведения ABC-анализа
Проводится ранжирование номенклатурных позиций по принятым критериям (в примере - по объему использования в стоимостном выражении), которое приведено на рис. 6.2, после чего номенклатурным позициям в соответствии с заданным распределением присваиваются классы относительной важности, что для рассматриваемого примера также отражено на рис. 6.2.
Графически ABC-классификацию можно проиллюстрировать при помощи рис. 6.3, где по оси абсцисс отражено нарастание номенклатурных позиций после ранжирования, а по оси ординат нарастающим итогом показана доля (в процентном выражении), которой эти позиции обладают в общем объеме.
APICS [1] рекомендует использование определенных границ категорий A, B и C, хотя следует тут же отметить, что жесткие границы все же не устанавливаются, а все зависит от каждого конкретного предприятия. Тем не менее имеет смысл привести эти данные (см. рис. 6.4).
Пример применения ABC-анализа
Номенклатурная позиция | Объем использования за год в стоимостном выражении | Процент от итога | Процент нарастающим итогом | Классификация |
46,7% | 46,7% | A | ||
34,3% | 81,0% | A | ||
6,2% | 87,2% | B | ||
4,6% | 91,8% | B | ||
3,0% | 94,8% | B | ||
2,7% | 97,5% | B | ||
3 64 | 0,9% | 98,4% | C | |
0,8% | 99,2% | C | ||
0,7% | 99,8% | C | ||
0,2% | 100% | C | ||
Итого | 100,% |
Классификация | Номенклатурная позиция | Процент от номенклатуры | Процент от использования в стоимостном выражении |
A | 7,1 | 20% | 81,0% |
B | 9,5,2,6 | 40% | 17,5% |
C | 3,4,10,8 | 40% | 2,5% |
Рис. 6.2. ABC-классификация номенклатурных позиций
База данных о запасах
Для планирования производства и закупок и для управления запасами критически важно обладать полной и достоверной базой данных о запасах. Рассмотрим основные данные о запасах, которые необходимы.
Под запасами будем понимать запасы всех номенклатурных позиций: материалов, полуфабрикатов, деталей, готовой продукции, и т. д.
Имеется два вида данных о запасах в MRP-системе:
1. Нормативно-справочные данные, которые устанавливают общие правила манипулирования запасами той или иной номенклатурной позиции. Эти сведения были подробно рассмотрены в главе 4.
Рис. 6.3. График нарастания совокупной доли номенклатурных позиций в общем объеме стоимостного потребления
2. Оперативные данные о запасах, отражающие их текущее состояние, включающие данные о текущих складских запасах и данные об открытых и подтвержденных заказах на производство и закупку.
Вообще запасы стоит разделить на две большие категории, которые по-разному отражаются MRP-системой, а именно:
1) запасы номенклатурных позиций, располагающиеся на некоторых известных местах хранения (складских площадях, прямо в цехе);
2) запасы изделий, находящихся в процессе преобразования из одних номенклатурных позиций в другие (т. е. пребывающие в состоянии незавершенного производства) либо находящихся в пути от поставщика к предприятию.
Первая категория запасов описывается посредством модуля <Управление запасами>, а вторая - либо через модуль <Управление открытыми производственными заказами> (для открытых производственных заказов), либо через модуль <Закупки> (для открытых заказов на закупку). С точки зрения расчета потребности в материалах и компонентах первая категория запасов отражается под названием <Запасы в наличии> (Quantity on hand), а вторая - под названием <Запланированные поступления> (Scheduled receipts).
Данные об имеющихся складских запасах включают в себя следующие основные реквизиты:
|
|
Состав сооружений: решетки и песколовки: Решетки – это первое устройство в схеме очистных сооружений. Они представляют...
Архитектура электронного правительства: Единая архитектура – это методологический подход при создании системы управления государства, который строится...
История развития хранилищ для нефти: Первые склады нефти появились в XVII веке. Они представляли собой землянные ямы-амбара глубиной 4…5 м...
Папиллярные узоры пальцев рук - маркер спортивных способностей: дерматоглифические признаки формируются на 3-5 месяце беременности, не изменяются в течение жизни...
© cyberpedia.su 2017-2024 - Не является автором материалов. Исключительное право сохранено за автором текста.
Если вы не хотите, чтобы данный материал был у нас на сайте, перейдите по ссылке: Нарушение авторских прав. Мы поможем в написании вашей работы!