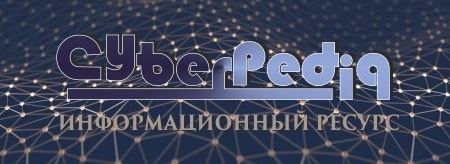
Автоматическое растормаживание колес: Тормозные устройства колес предназначены для уменьшения длины пробега и улучшения маневрирования ВС при...
Индивидуальные очистные сооружения: К классу индивидуальных очистных сооружений относят сооружения, пропускная способность которых...
Топ:
Генеалогическое древо Султанов Османской империи: Османские правители, вначале, будучи еще бейлербеями Анатолии, женились на дочерях византийских императоров...
Выпускная квалификационная работа: Основная часть ВКР, как правило, состоит из двух-трех глав, каждая из которых, в свою очередь...
Когда производится ограждение поезда, остановившегося на перегоне: Во всех случаях немедленно должно быть ограждено место препятствия для движения поездов на смежном пути двухпутного...
Интересное:
Лечение прогрессирующих форм рака: Одним из наиболее важных достижений экспериментальной химиотерапии опухолей, начатой в 60-х и реализованной в 70-х годах, является...
Отражение на счетах бухгалтерского учета процесса приобретения: Процесс заготовления представляет систему экономических событий, включающих приобретение организацией у поставщиков сырья...
Наиболее распространенные виды рака: Раковая опухоль — это самостоятельное новообразование, которое может возникнуть и от повышенного давления...
Дисциплины:
![]() |
![]() |
5.00
из
|
Заказать работу |
Сварка является основным технологическим процессом при изготовлении металлических конструкций. Обычно применяют электродуговую сварку, ручную, полуавтоматическую или автоматическую. Ручная сварка выполняется металлическим электродом (диаметром 3-6 мм) с покрытием. Полуавтоматическая и автоматическая сварка производится проволокой (диаметром 1,2-3,0 мм) под слоем флюса или в среде защитного газа. Технология сварки и подбор сварочных материалов должны обеспечивать создание бездефектного шва с механическими характеристиками наплавленного металла не ниже, чем основного металла элемента конструкции.
Сварным соединением будем называть узел конструкции, включающий соединяемые части конструктивных элементов и соединяющий их наплавленный металл. Термином сварной шов обозначим часть сварного соединения, включающую металл, который в процессе сварки был расплавлен. Сварные швы разделим на стыковые и угловые. Стыковой шов соединяет кромку тонкостенного элемента с другой кромкой или поверхностью другого элемента с полным проплавлением стыка, т. е. с образованием сплошного массива, заполняющего просвет между ними (рис. 15.1, а, б). Угловой шов накладывается в угол, образуемый двумя поверхностями свариваемых элементов. В результате расплавления металла элементов часть зазора между соединяемыми деталями заваривается, в остальной же час
ти сохраняется щель (рис. 15.1, в). Основной геометрической характеристикой углового шва является катет, который определяется как катет вписанного в сечение шва равнобедренного треугольника. Требуемый размер катета определяется расчетом: k = (0,6 + l,2)tmin (tmin—• толщина более тонкого из соединяемых элементов).
Основными типами сварных соединений, используемых в несущих конструкциях, являются стыковые, тавровые, угловые и нахлесточные.
Стыковые соединения соединяют кромки листов, лежащих в одной плоскости, и выполняются стыковыми швами. Тонкие листы (до 8 мм) можно сваривать непосредственно по кромкам. При больших толщинах проката для обеспечения полного проплавления сечения делают разделку кромок, которую заполняют за один или несколько проходов (рис. 15.2, а). Ответственные стыковые швы должны быть двусторонними (рис. 15.1, а) или с подваркой корня (рис. 15.2, а). Если подварка невозможна, то шов выполняют на подкладке, которая остается на конструкции (рис. 15.2, б, поз. 1) При стыковке листов разной толщины с разностью толщин более 25 % меньшей толщины на более толстом листе делается скос с уклоном, примерно 1: 4 (рис. 15.2, в). Для того чтобы стыковой шов полно
стью заполнил стык, вначале и в конце соединения перед сваркой закрепляют на прихватках технологические планки 2 (рис. 15.2, г). Сварку начинают на одной планке и заканчивают на другой. После сварки планки срезают, а кромки зачищают. Стыковые соединения труб выполняют на подкладном кольце 3, которое обеспечивает центровку труб при сварке и формирование корня шва (рис. 15.2, д).
Тавровые (рис. 15.3, а, б) и угловые (рис. 15.3, в) соединения предназначены для соединения кромки с поверхностью другого элемента. Тавровые соединения выполняют стыковыми швами, т. е. с полным проплавлением (рис. 15.3, а), или угловыми, двусторонними (рис. 15.3, б) либо односторонними. Сварные швы 1 ответственных тавровых соединений, выходящих на край листа,
выводят на технологические планки 2, которые удаляют после сварки (рис. 15.3, б).
Угловые соединения обычно делают с разделкой кромки, чтобы обеспечить проплавление присоединяемого листа (рис. 15.3, в).
Нахлесточные соединения образуются угловыми швами (рис. 15.3, г). В нахлесточном соединении угловые швы, расположенные вдоль направления действующей нагрузки, называют фланговыми 3, а поперек — лобовыми 4.
В соединениях этого типа между поверхностями соединяемых элементов возникает щель. Применение такого соединения в конструкции, работающей на открытом воздухе, во влажной или агрессивной среде, может вызвать развитие щелевой коррозии, способной разрушить сварной узел. Для защиты таких узлов от проникновения влаги в щель между соединяемыми деталями применяют герметики.
Требования к геометрии и качеству сварных соединений установлены в нормативных документах (ГОСТ 5264, ГОСТ 8713, ГОСТ 14771 и др.). При нарушении технологии сварки в соединениях возникают дефекты, которые снижают прочность и долговечность конструкции. Наиболее типичными дефектами являются непровары 1, 5 (внутренние и внешние), поры 2, трещины 3, подрезы 6, несплав- ления 7 (рис. 15.4). Кроме того, дефектами считаются несоответствия размеров и формы швов установленным требованиям,недопустимо большие смещения кромок (рис. 15.4, размер Д), чрезмерная выпуклость шва, неполное заполнение разделки 4 и т. п. Наиболее опасными дефектами сварки являются трещины — «горячие», образующиеся в процессе сварки, и «холодные», возникающие или сразу после остывания шва, или через некоторое время, даже через 1-2 дня. Дефекты соединений обнаруживают внешним осмотром или с помощью различных методов неразрушающего контроля — капилярного, радиационного, ультразвукового и пр.
В результате усадки сварных швов при охлаждении после сварки в элементах конструкций создаются остаточные сварочные напряжения, происходят изменение линейных
![]() |
размеров и искажение формы конструкции. Возникают общие и местные деформации. Общие сварочные деформации проявляются в изменении линейных размеров и искривлении конструкции. Местные деформации приводят к нарушению плоскостности листов, появлению «грибовидности» поясов и искривлению стенок балок (рис. 15.5, а). В результате этого меняются условия их нагружения, снижается долговечность сварных соединений. Поэтому не рекомендуется соединять сваркой листы, наложенные друг на друга (рис. 15.5, б). Местные усиления следует делать вставкой более толстого листа (рис. 15.5, в). Фланец, приваренный к балке, также теряет плоскую форму, и для качественной сборки конструкции его необходимо механически обработать (рис. 15.5, г).
Основные несущие швы по возможности надо варить автоматом. Сварные соединения в конструкциях для холодного климата должны подвергаться особо тщательному дефектоскопическому контролю качества.
Расчеты сварных соединений.
Стыковые и тавровые соединения, качественно изготовленные с полным проплавлением корня шва (рис. 15.2, а, б,15.3, а), рассчитывают на прочность согласно (7.1), (7.3) по условиям:
(15.1) |
Эквивалентные напряжения в левой части этих неравенств вычисляются по формуле (7.5) или (7.6) с использованием максимальных нагрузок II расчетного случая в соответствующей системе расчетов, СРДН или СРПС. Если стыковой шов не выходит на кромку листа или выходящий на кромку шов сварен с технологическими планками (рис. 15.2, г), то действующие в нем максимальные нормальные напряжения а вычисляются по формулам (13.1), а касательные — по (13.11). При этом используются геометрические параметры сечения присоединяемого элемента (балки или стержня). Если стыковой шов соединяет элементы разных толщин, то в расчете фигурирует толщина более тонкого из них. Если же шов в листе шириной Ъ выходит на кромку (как, например, на поясах балок) и сварен без технологических планок, то при вычислении номинальных напряжений расчетная длина этого шва принимается ,где t— толщина более тонкого свариваемого листа или элемента.
При расчете двусторонних соединений и соединений с подваркой корня шва по (15.1) допускаемые напряжения и коэффициенты надежности определяются следующим образом. При растяжении [ ] = 0,85[
], коэффициент надежности по материалу
= 0,85. При сжатии[
] = [
]и
= 1,0. Нормативное сопротивление
. Коэффициенты
принимаются по рекомендациям табл. 1.3 и 7.2. Если соединения выполнены с выводными планками и их качество подтверждено визуальным и дефектоскопическим контролем, то и при растяжении можно принимать
] = [
] и
= 1,0. То есть в этом случае обеспечена равнопрочность сварного соединения и присоединяемых элементов.
Расчет на прочность соединений с угловыми швами. Соединения с угловыми швами при перегрузке могут разрушиться путем среза по шву или в результате разрыва по основному металлу. Угловые швы в тавровых и нахлес- точных соединениях рассчитывают на срез по условиям:
(15.2) |
Рассмотрим единичный участок тонкостенного элемента, присоединенного к остальной конструкции двусторонним угловым швом (рис. 15.6, а). Напряженное состояние элемента характеризуется нормальными напряжениями , (13.1), (13.2) и касательными
(13.11), которые создают продольную S =
и поперечную
силы. Расчет углового шва производится по площадке среза ABDC,совпадающей с гипотенузой угла. На этой площадке возникают нормальные и касательные напряжения, но в расчете (15.2) учитываются только касательные (горизонтальные
и вертикальные
). Это является допущением, подтвержденным результатами экспериментов. Касательные напряжения в шве вычисляются по формулам
(15.3) |
![]() |
Здес — расчетная высота шва, где k — катет шва. Для швов, выполненных ручной и полуавтоматической сваркой,
= 0,7, для автоматической сварки —
= 1. Множитель 2 учитывает то, что шов двусторонний. Эквивалентные касательные напряжения, действующие в плоскости среза, вычисляются как:
(15.4) |
Расчет угловых швов, например присоединяющих к фланцу балку, загруженную силами S, Qy и Qz, изгибающими моментами Мy и Мz, а также крутящим моментом
Мх, производится в два этапа (рис. 15.6, б). Отдельно выполняется расчет сварных швов, присоединяющих пояс и стенки. Конфигурация площади среза определяется контуром привариваемого элемента, а ее ширина равна расчетной высоте шва hwi соответствующего элемента (рис. 15.6, в).
В поясе балки действуют нормальные (13.1) и касательные
(13.11) напряжения:
(15.5) |
Соответственно касательные напряжения в шве, присоединяющем пояс, вычисляются как (15.3), (15.4)
(15.6) |
В стенке балки действуют максимальные нормальные напряжения касательные напряжения (13.11)
(15.7) |
Соответственно эквивалентные касательные напряжения в шве, присоединяющем стенку,
(15.8) |
В приведенных формулах обозначено: — геометрические параметры сечения балки;
— толщины пояса и стенки;
— расчетная высота шва на поясе и стенке (индекс «ww» обусловлен совпадением первых букв в словах «welding» — сварка и «web» — стенка балки). Обозначения
— см. в пояснениях к формулам (13.10), (13.14).
Эквивалентные напряжения и
подставляются в условия прочности (15.2). При необходимости площадь среза сварного шва может быть увеличена путем укрепления фланца ребрами (рис. 15.6, г).
Нахлесточные соединения создают весьма большую концентрацию напряжений в швах и соединяемых элементах (рис. 15.7, показана эпюра распределения нормальных напряжений в присоединенной детали и касательных напряжений во фланговом шве). При нагружении происходит локальная текучесть сварного шва, снижающая концентрацию напряжений (п. 7.1). Для ограничения концентрации напряжений длина фланговых швов должна быть lx ≤ 60k (k— катет шва). Если же реальная длина шва больше, в расчет вводится значение lx= 60k.Этот тип соединений не рекомендуется использовать в конструкциях, интенсивно циклически нагруженных и эксплуатируемых в условиях низких температур.
Расчетные касательные напряжения в нахлесточных соединениях с лобовыми и фланговыми швами вычисляются как (рис. 15.7)
(15.9) |
Суммирование площадей производится по всем швам. Обычно катеты швов в одном соединении одинаковые, поэтому для соединения на рис. 15.7 получится
Допускаемое напряжение в (15.2) определяется как , где [
] — допускаемое напряжение основного металла. Нормативное сопротивление —
= 0,6
. Коэффициент условий работы в данном случае отражает неравномерность загружения шва, т. е. степень достоверности определения действующих в шве напряжений. Так, для присоединений балок к фланцам
- 0,7 ÷ 0,8, меньшие значения для тонких фланцев (
— толщины фланца и пояса) без ребер. Для сварного соединения кронштейна со стенкой балки, подкрепленной диафрагмой,
.Для нахлесточного соединения
, меньшие значения для соединения с фланговыми швами большой длины, большие значения для комбинированных соединений с лобовыми и фланговыми швами меньшей длины.
Присоединение стенки балки (не ездовой) к поясу является тавровым соединением, загруженным касательными напряжениями с односторонним (в коробчатых балках) или двусторонним (в двутавровых) угловым швом. Этот шов рассчитывается по касательным напряжениям от перерезывающей силы и крутящего момента (15.7), которые подставляются в (15.8) при = 0.
Расчет сварных соединений по равнопрочности. В тех случаях, когда невозможно точно определить нагрузку, действующую на сварной узел, целесообразно рассчитывать сварные соединения по равнопрочности. Условие равнопрочности заключается в том, что сварное соединение должно выдерживать такую же нагрузку, как и присоединяемый элемент. Это значит, что расчет сварного соединения производится по вышеприведенным методикам, нов предположении, что максимальное действующее напряжение в присоединенном элементе равно допускаемому напряжению или расчетному сопротивлению
При этом, например, для двусторон
них угловых швов (рис. 15.6, а) расчетное напряжение по
Подставив это выражение в условие прочности (15.2) с учетом того, что , найдем
(15.10) |
То есть для обеспечения равной прочности двустороннего углового шва и присоединяемого листа шов должен иметь катет при ручной сварке k > 1,21, а при автоматической — k > 0,85t. Для обеспечения равнопрочности одностороннего углового шва необходим чрезмерно большой катет, который технологически недопустим. Поэтому односторонний тавровый шов не будет равнопрочен присоединенному элементу.
Расчет на сопротивление усталости. При циклическом нагружении усталостная трещина в сварном соединении может возникнуть в зоне 1 перехода от шва к основному металлу, где действует наибольшая концентрация напряжений, или в наплавленном металле шва 2 — от непрова- ра либо внутреннего дефекта (рис. 15.8). Трещина в зоне 2 более опасна, так как не может быть обнаружена визуально. В качественно изготовленном сварном соединении с размерами, выбранными из условия прочности, предел выносливости по шву (зона 2) получается больше, чем по ос-
новному металлу (зона 1). Расчет сварных соединений на сопротивление усталости выполняется по методикам, изложенным в п. 10.3.
Болтовые соединения
Общие положения
Болтовые соединения являются наиболее удобным и технологичным способом соединения элементов конструкции при монтаже. Болтовые соединения бывают двух типов: с поперечным и с продольным относительно направления нагружения стыком. К первому типу относятся фланцевые соединения (рис. 15.9, а), а ко второму — соединения, работающие на сдвиг (рис. 15.9, б). Фланцевое соединение имеет большие габаритные размеры, но позволяет соединять балки любого сечения (двутавровые, коробчатые, трубчатые и пр.). Соединения с продольным стыком незначительно увеличивают поперечные размеры соединяемых элементов, но имеют большую протяженность и применимы только для балок с плоскими стенками и поясами. Выбор того или иного вида соединения обычно производится исходя из удобства его размещения в конструкции и технологических возможностей предприятия.
Соединения всегда менее надежны, чем сплошная конструкция, поэтому их следует по возможности размещать в таких сечениях, где действуют меньшие усилия, желательно не изменяющиеся в процессе работы машины по знаку. Фланцевое соединение по существу является цепью из трех соединений (сварного — болтового — сварного), последовательно передающих нагрузку от одного конструктивного элемента к другому (рис. 15.9, а). Это снижает надежность фланцевого соединения.
Для соединения несущих металлических конструкций применяют болты, которые ставятся в отверстие с зазором или без зазора. Классы прочности болтов установлены в ГОСТ 1759.4 и обозначаются двумя цифрами, по которым можно определить предел текучести и временное сопротивление материала болта. Например, если класс прочности болта 10.9, то временное сопротивление 10 • 100 = 1000 МПа, а предел текучести 1000 • 0,9 = 900 МПа. Рекомендуется применять болты классов 5.6, 8.8, 10.9. В зависимости от допусков на размеры болтов установлены три класса точностиА, В и С (ГОСТ 1759.1-82). Кроме того, используются высокопрочные болты по ГОСТ 22356.
Болты изготавливают из углеродистых и легированных сталей с последующей закалкой и отпуском. Легирование обеспечивает повышенную прокаливаемость стержня болта. При установке высокопрочных болтов под головку и под гайку подкладывают термообработанные шайбы из углеродистых сталей. Они уменьшают трение при затягивании болта и защищают поверхность соединяемых элементов от пластических деформаций и задиров.
Болтовые соединения являются многократно статически неопределимыми системами, поэтому для расчета усилий в болтах приходится использовать определенные допущения о характере их распределения между болтами, что, безусловно, снижает достоверность расчета. При проектировании обычно производится предварительное размещение болтов в стыке, после чего рассчитывают максимальное усилие и выбирают диаметр болтов. После окончательного размещения болтов с учетом удобства затяжки и конструктивных рекомендаций выполняют проверочный расчет.
Архитектура электронного правительства: Единая архитектура – это методологический подход при создании системы управления государства, который строится...
История развития пистолетов-пулеметов: Предпосылкой для возникновения пистолетов-пулеметов послужила давняя тенденция тяготения винтовок...
Эмиссия газов от очистных сооружений канализации: В последние годы внимание мирового сообщества сосредоточено на экологических проблемах...
Особенности сооружения опор в сложных условиях: Сооружение ВЛ в районах с суровыми климатическими и тяжелыми геологическими условиями...
© cyberpedia.su 2017-2024 - Не является автором материалов. Исключительное право сохранено за автором текста.
Если вы не хотите, чтобы данный материал был у нас на сайте, перейдите по ссылке: Нарушение авторских прав. Мы поможем в написании вашей работы!