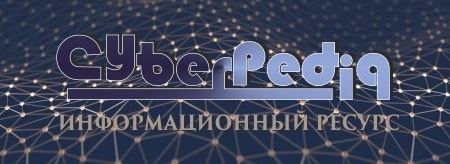
Биохимия спиртового брожения: Основу технологии получения пива составляет спиртовое брожение, - при котором сахар превращается...
Двойное оплодотворение у цветковых растений: Оплодотворение - это процесс слияния мужской и женской половых клеток с образованием зиготы...
Топ:
Проблема типологии научных революций: Глобальные научные революции и типы научной рациональности...
Техника безопасности при работе на пароконвектомате: К обслуживанию пароконвектомата допускаются лица, прошедшие технический минимум по эксплуатации оборудования...
Интересное:
Отражение на счетах бухгалтерского учета процесса приобретения: Процесс заготовления представляет систему экономических событий, включающих приобретение организацией у поставщиков сырья...
Подходы к решению темы фильма: Существует три основных типа исторического фильма, имеющих между собой много общего...
Национальное богатство страны и его составляющие: для оценки элементов национального богатства используются...
Дисциплины:
![]() |
![]() |
5.00
из
|
Заказать работу |
|
|
Влияние формы и конфигурации.
Наиболее технологичны простые поверхности (плоские, цилиндры, конусы), поскольку для обработки сложных фасонных поверхностей требуется оборудование со сложной кинематикой, с повышенной жесткостью. Такое оборудование обычно менее производительно и дорого. Габариты деталей определяют типоразмеры применяемых станков и оснастки, влияют на выбор заготовки, материалоемкость, жесткость детали.
Жесткость детали - очень важный фактор технологичности: жесткие детали в значительно меньшей степени, чем ажурные, деформируются при закреплении и обработке, при релаксации внутренних напряжений; при обработке таких деталей допустимы высокие режимы резания, возможен более широкий выбор методов обработки.
Высокопроизводительные методы обработки (многорезцовые, револьверные станки, автоматы) чаще применяют также для обработки деталей с поверхностями простых форм. Производительная обработка сложных поверхностей в настоящее время осуществляется на обрабатывающих центрах, станках с числовым программным управлением, электрофизическими методами. Например, лопатка ГТД, как нежесткая и сложная по форме, традиционно считалась крайне нетехнологичной с позиции механической обработки резанием. Однако ныне, с появлением метода электрохимической обработки пера в проточном электролите, лопатка является весьма технологичной деталью. Здесь уместно отметить, что технологичность не является абсолютным и неизменным критерием качества конструкции. Этот критерий может существенно меняться с появлением новых методов обработки, с изменением других условий производства (например, программы выпуска).
|
Конфигурация детали в целом даже при наличии простых поверхностей может затруднять применение высоко-производительной обработки. Так, ступенчатое расположение плоскостей А и Б делает невозможной обработку их на проход (рис. 3, а), в то время как в случае рис. 3, б такая возможность имеется. Наклонное расположение отверстия Ø А- не благоприятствует обработке всех отверстий в корпусе при одной установке детали (рис. 3, в). Этого недостатка лишена конструкция на рис. 3, г.
Одним из путей повышения производительности является многоместная обработка, поэтому детали, для которых применение этого вида обработки возможно, являются более технологичными (рис. 3, е). На деталях, показанных на рис. 3, д, многоместная обработка не результативна.
![]() |
Рис. 3 Конфигурации деталей
3.2.2. Инструментальная доступность.
![]() |
|
Рис. 4 Конфигурации деталей, поверхности которых доступны для обработки и измерения
Требования к точности взаимного расположения поверхностей.
Точность размеров и условия ТТ, координирующие взаимное расположение поверхностей, в еще большей степени, чем точность размера и формы отдельной поверхности, влияют на экономичность обработки и технологичность детали по процессу изготовления. Точность координирующих параметров зависит не только от оборудования, но и от выбираемой технологической схемы обработки и обеспечивающих ее мероприятий (разметка, выверка, оснастка).
Наиболее целесообразна такая простановка размеров, которая предусматривает совмещение конструкторских и технологических баз. Это исключает ошибки базирования, а также пересчет размеров и связанное с ним ужесточение допусков на составляющие звенья. Таким образом, порядок простановки размеров должен обеспечить, их непосредственное получение и измерение. Например, размер А, обусловливающий эксплуатационные требования для диска компрессора (рис. 8, в), задан размерной цепью Б, В, Г с жесткими допусками этих
Рис. 8 Конфигурация деталей и взаимное расположение поверхностей
составляющих звеньев, что усложняет обработку и контроль детали. Целесообразнее задать размер А непосредственно: при более широком допуске проще достичь необходимой точности при обработке торцевых шлиц (рис. 8, г)
Простановка координирующих размеров должна обеспечить и удобство измерения: в отличие от размеров Б и В (рис. 8, д) размер А упрощает точное измерение глубины паза (рис. 8, с). Обычно от основных технологических баз обработать все поверхности детали невозможно. В этом случае вспомогательные технологические базы связываются с основными базами размерами с жесткими допусками. Иногда по условиям обработки связывать все обрабатываемые в одной операции поверхности с основной технологической базой нецелесообразно. Так, размеры поверхностей, обрабатываемых фасонным или сборным инструментом, должны быть связаны между собой, а для связи с установочной базой достаточно одного размера. Простановка размеров по технологическому варианту облегчит как определение размеров режущего инструмента, так и получение размера А (рис. 8, з).
|
Еще одно важное требование к координации поверхностей детали заключается в том, что точность взаимного расположения их, каким бы способом она не регламентировалась (размером или предельным отклонением расположения), должна быть задана однозначно. Например, наличие двух размеров А и Б, связывающих обрабатываемую поверхность с необрабатываемыми, создает неопределенность при выборе первичной черной базы и влечет за собой погрешность по одному из этих размеров (рис. 8, и). Необходимо обрабатываемую и необрабатываемую поверхности связать лишь одним размером и для этого лучше выбрать размер А, так как поверхность Т более удобна в качестве базы (рис. 8, к).
В заключение отметим, что иногда к точности координирующих параметров, с целью создания некоторого запаса точности, предъявляются неоправданно высокие требования, которые удорожают обработку, но не улучшают эксплуатационные показатели изделия. В подобных случаях допустима критическая переоценка требуемого параметра, но при веском технологическом обосновании.
3.4. ЧАСТНЫЕ РЕКОМЕНДАЦИИ ПО УЛУЧШЕНИЮ ТЕХНОЛОГИЧНОСТИ ОТДЕЛЬНЫХ ТИПОВ ДЕТАЛЕЙ
Кроме общих требований, предъявляемых к любой детали, подвергаемой механической обработке, к отдельным типам деталей предъявляются специфические требования. Рассмотрим их применительно к наиболее часто встречающимся при учебном проектировании типам деталей.
Корпусные детали.
Технологичность конструкции корпусов улучшается, если обеспечиваются следующие требования:
расстояния между отверстиями в стенке корпуса допускают возможность их одновременной обработки на многошпиндельных станках;
|
возможно растачивание соосных отверстий на проход с одной стороны (для этого диаметры соосных отверстий должны ступенчато уменьшаться);
не предусмотрена обработка внутренних торцов ступиц корпуса;
отсутствуют глухие отверстия, в том числе и резьбовые;
в глухих резьбовых отверстиях предусмотрен сбег резьбы;
в ступенчатых отверстиях точная ступень сквозная;
обрабатываемые плоскости расположены под прямыми углами;
отверстия каналов и другие сверления расположены под прямыми углами к плоскостям входа и выхода инструмента;
отсутствуют внутренние резьбы большого диаметра;
отсутствуют глубокие сверления (l/d>10).
Валы и оси
Технологичные валы и оси удовлетворяют следующим требованиям:
в детали предусмотрены центровые отверстия, допускающие обработку в центрах;
ступенчатые детали имеют небольшие перепады диаметров, приблизительно одинаковые на разных ступенях, что позволяет применять многорезцовые станки;
диаметральные размеры шеек убывают к концам детали; отношение длины вала lк его диаметру dне превышает следующих величин:
d, мм | 6-10 | 10-25 | 25-40 | 40-60 | 60-80 |
l/d, мм |
поперечные канавки по форме и размерам пригодны для обработки на копировальных станках;
поперечные прорези и пазы в детали таковы, что ось обрабатывающего инструмента проходит через ее центр.
Втулки и кольца.
Технологичные конструкции втулок и колец отвечают следующим требованиям:
отсутствуют глухие отверстия с разных сторон детали;
все внутренние поверхности можно расточить с одной стороны при одной установке детали;
возможна обточка центрирующих поясков и нарезка резьб при одной установке детали;
точные отверстия и отверстия со шлицами - открытые;
шлицевые поверхности не имеют перерывов, что способствует уменьшению ударов по режущему инструменту.
Технологические рекомендации к конструкциям других типов деталей (шестерен, рычагов) приведены в справочной литературе /12/ и во многом совпадают с приведенными в п. 3.4, особенно при наличии аналогичных конструктивных элементов.
3.5. ОБРАБАТЫВАЕМОСТЬ МАТЕРИАЛОВ РЕЗАНИЕМ
Обрабатываемость материала, т.е. способность его, поддаваться обработке тем или иным методом резания, определяется комплексом физических свойств, химическим составом и структурным строением. Обрабатываемость, как правило, оценивается по допустимой величине скорости резания. Повышение содержания легирующих элементов в основном ухудшает обрабатываемость.
Количественно обрабатываемость резанием того или иного материала характеризуется отношением скорости резания этого материала к скорости резания стали 45 в сходных условиях обработки. Данные по обрабатываемости резанием различных материалов, применяемых в авиадвигателестроении (или аналогичных им), представлены в табл. 1.
|
Таблица 1
Характеристика материала | Типовые марки | Скорости резания, м/мин | Обрабатываемость по отношению к стали 45 | |
Твердый сплав | Быстро-режущая сталь | |||
Улучшаемые стали перлитного класса | 38ХА 30ХГСА 30ХМА 40ХН2МА | 0,8 0,65 0,6 0,8 | ||
Цементируемые и азотируемые стали | 12Х2Н4А 12Х2НВФА 13ХЗНВМ2Ф | 0,75 0,75 0,7 | ||
Высокопрочные стали | 38ХМЮА 38Х2МЮД 39МХГСНА | 0,7 0,6 0,55 | ||
Нержавеющие высокохромистые стали ферритного, мартенситного классов | 1Х13, 2Х13 1Х17Н2 1Х12Н2ВМФ | 0,65 0,65 0,55 | ||
Нержавеющие и жаропрочные стали аустенитного и аустенитно-мартенситного классов | 12Х18Н9Т Х15Н9Ю | 0,5 0,45 | ||
Жаропрочные окалиностой-кие сложнолегированные стали аустенитного класса | 4Х12Н8Г8МФБ 12Х25Н16Г7АР Х12Н2ОТЗР | 0,3 0,25 0,15 | ||
Жаропрочные деформируемые сплавы на железо-никелевой основе | ХН77ТЮР ХН60В | 0,16 0,8 | ||
Жаропрочные литейные сплавы на никелевой основе | ВЖ36-Л2 ЖСб-К ЖСЗ-ДК | 0,04 0,04 0,04 | ||
Сплавы средней прочности на основе титана | ОТ4 ОТ6 | 0,4 0,25 | ||
Высокопрочные сплавы на основе титана | ВТ16 ВТ22 | 0,2 0,15 | ||
Жаропрочные титановые сплавы | ВТЗ-1 ВТ9 | 0,25 0,2 | ||
Алюминиевые сплавы деформируемые | Д1, Д16 В95 АК4-1, АК6 | 3,5 2,0 3,5 | ||
Алюминиевые сплавы литейные | АЛ-4 | |||
Магниевые литейные сплавы | МЛ5 МЛ9 МЛ19 | 4 и более | ||
Латунь | Л62 Л63 | 2,0 2,0 | ||
Бронзы оловянные | БрОФ7-0,2 Бр019 БрОС16-5 | 1,5 1,5 1,5 | ||
Бронзы безоловянные | БрАЖ9-4 БрБ2 | 0,7 0,7 |
Обрабатываемость различных конструкционных материалов, хотя и в несколько ином понимании - как интенсивность съема материала, применительно к электрофизическим и другим методам обработки приводится в справочной литературе /13/.
3.6. РЕКОМЕНДУЕМАЯ ПОСЛЕДОВАТЕЛЬНОСТЬ АНАЛИЗА КОНСТРУКЦИИ И ТЕХНОЛОГИЧНОСТИ ДЕТАЛЕЙ, ПОДВЕРГАЕМЫХ МЕХАНИЧЕСКОЙ ОБРАБОТКЕ
Студентам, выполняющим учебное проектирование по курсу “Технология механической обработки деталей ДЛА”, при выполнении технологического анализа чертежа заданной детали следует руководствоваться указаниями, приведенными в разд. 1, 2, 4 настоящих методических указаний. Анализ чертежа надлежит проводить в следующей последовательности:
склассифицировать деталь по конструктивному принципу;
описать назначение и условия работы детали в изделии;
рассмотреть конструкцию детали как сочетание различные поверхностей, оценить габариты, жесткость, инструментальную доступность и технологичность по процессу изготовления;
выделить основные и свободные поверхности, рассмотреть их точность, характеристики качества и технологичность формы;
описать взаимосвязь между основными (конструкторскими и рабочими), а также между основными и свободными поверхностями, рассмотреть систему простановки координирующих размеров, выявить возможность их непосредственного получения и измерения, оценить технологичность по процессу изготовления;
склассифицировать материал детали, описать его химический состав, химико-термическую обработку и структурные характеристики, рассмотреть изменение механических свойств, в связи с требуемой термообработкой, оценить обрабатываемость и отмстить особые технологические свойства;
охарактеризовать назначенную конструктором заготовку;
дать итоговую характеристику технологичности детали и указать пути ее улучшения.
3.7. ПРИМЕР ТЕХНОЛОГИЧЕСКОГО АНАЛИЗА РАБОЧЕГО ЧЕРТЕЖА
В качестве примера для деталей, получаемых механической обработкой, проведем технологический анализ чертежа рабочей лопатки V ступени компрессора ГТД (рис. 9). К лопатке предъявляются следующие требования:
допустимое отклонение точек профиля пера от теоретического в расчетных сечениях-0,15мм;
допустимый разворот профилей сечений от теоретического положения ± 8 ',
допустимое смещение профиля пера относительно хвостовика лопатки в направлении, перпендикулярном оси хвостовика, ± 0,2 мм;
смещение выгодной кромки относительно основания хвостовика лопатки в направлении оси хвостовика, ± 1 мм;
разноразмерность по длине замка не более 0,01 мм;
поверхность пера упрочнить гидродробеструйной обработкой и виброгалтовкой по специальной инструкции;
рабочие (боковые) поверхности хвостовика упрочнить гидродробеструйной обработкой по специальной инструкции.
3.7.1. Назначение и условия работы.
Лопатка по своим конструктивным признакам относится к обширному классу деталей того же наименования. Лопатка ротора компрессора является основным рабочим элементом, который, воздействуя на проходящий через компрессор воздух, осуществляет его сжатие.
Рассматриваемая деталь относится к числу наиболее нагруженных деталей ГТД, определяющих его ресурс /4/. Ее профильная часть - перо лопатки - кроме растяжения и изгиба от центробежных сил, изгиба и кручения от газового потока, испытывает переменные напряжения от вибрационных нагрузок, амплитуда и частота которых меняются в широких пределах, а также тепловые нагрузки. При работе двигателей на переходных режимах в кромках пера возникают напряжения, связанные с различной величиной термического расширения тонких и утолщенных элементов пера. Условия работы пера осложняются действием пылевой эрозии и агрессивной газовой среды. В замке лопатки помимо циклических растягивающих напряжении возникают значительные контактные напряжение, которые могут вызвать локальные разрушения в зоне контакта. Тепловые нагрузки в хвостовике незначительны, чем в профильной части.
БИБЛИОГРАФИЧЕСКИЙ СПИСОК
1. Фираго В. П. Основы проектирования технологических процессов и приспособлений. Методы обработки поверхностей. Изд. 2-е. М.: Машиностроение, 1973.-468 с.
2. Евстигнеев М. И. и др. Изготовление основных деталей авиадвигателей /Под ред. А. В. Подзея. Изд. 2-е.-М.: Машиностроение, 1972.-480 с.
3. Абрамов А. М. и др. Производство газотурбинных двигателей: Справочное пособие. /Под ред. М. Ф. Идзона.- М. Машиностроение, 1966.--472 с.
4. Скубачевский Г. С. Авиационные газотурбинные двигатели. Конструкция и расчет деталей. Изд. 4-е.-М.: Машиностроение, 1974.-520 с.
5. Мягков В. Д. и др. Допуски и посадки: Справочник. Ч.1.-Л.: Машиностроение, 1978.-544 с.
6. Сулима А. М. Евстигнеев. М. И. Качество поверхностного слоя и усталостная прочность деталей из жаропрочных и титановых сплавов. М.: Машиностроение, 1974.-265 с.
7. Мягков В. Д. и др. Допуски и посадки: Справочник. Ч. II - Л.: Машиностроение, 1978, с. 545--1032.
8. Справочник металлиста. Т. II. /Под ред. А. Г. Рихштадта и В. А. Брострема. - М ·. Машиностроение, 1976.-718 с.
9. Шмыков А. А. Справочник термиста. Изд. 3-е Государственное научно-техническое издательство машиностроительной литературы. - М., 1956.-3320.
10. Вишняков А. Е. Технико-экономическое обоснование выбора способа получения заготовки: Учебное пособие. - Самара: СГАУ, 1998.
11. Технологичность конструкций: Справочное пособие. /Под ред. С. Л. Ананьева и В. П. Купровича. - М. Машиностроение, 1969.-424 с.
12. Справочник металлиста. Т. 3. /Под ред. А. Н. Малова. - М. Машиностроение. 1977. - 752 с.
13. Курсовое проектирование по технологии машиностроения. /Под ред. А. Ф. Горбацевича. Изд. 3. - Минск: Высшая школа, 1975.-289 с.
СОДЕРЖАНИЕ
1. ТЕХНОЛОГИЧЕСКИЙ АНАЛИЗ КОНСТРУКЦИИ
1.1. Назначение технологического анализа рабочего чертежа
1.2. Изучение и анализ конструкции детали
1.3. Классификация деталей
1.4. Назначение и условия работы детали
1.5. Описание конструкции детали
1.6. Характеристика взаимосвязей поверхностей деталей
1.7. Характеристика материала детали
1.8. Характеристика рекомендуемой заготовки
2. АНАЛИЗ ТЕХНОЛОГИЧНОСТИ КОНСТРУКЦИИ
2.1. Оценка технологичности конструкций
2.2. Требования к технологичности конструкции детали
3 ТЕХНОЛОГИЧНОСТЬ ДЕТАЛЕЙ, ПОДВЕРГАЕМЫХ МЕХАНИЧЕСКОЙ ОБРАБОТКЕ
3.1. Оценка технологичности механически обрабатываемых деталей
3.2. Форма детали и технологичность
3.3. Точность и технологичность
3.4. Частные рекомендации по улучшению технологичности отдельных типов деталей
3.5. Обрабатываемость материалов резанием
3.6. Рекомендуемая последовательность анализа конструкции и технологичности деталей, подвергаемых механической обработке 23
3.7. Пример технологического анализа рабочего чертежа
Библиографический список
Влияние формы и конфигурации.
Наиболее технологичны простые поверхности (плоские, цилиндры, конусы), поскольку для обработки сложных фасонных поверхностей требуется оборудование со сложной кинематикой, с повышенной жесткостью. Такое оборудование обычно менее производительно и дорого. Габариты деталей определяют типоразмеры применяемых станков и оснастки, влияют на выбор заготовки, материалоемкость, жесткость детали.
Жесткость детали - очень важный фактор технологичности: жесткие детали в значительно меньшей степени, чем ажурные, деформируются при закреплении и обработке, при релаксации внутренних напряжений; при обработке таких деталей допустимы высокие режимы резания, возможен более широкий выбор методов обработки.
Высокопроизводительные методы обработки (многорезцовые, револьверные станки, автоматы) чаще применяют также для обработки деталей с поверхностями простых форм. Производительная обработка сложных поверхностей в настоящее время осуществляется на обрабатывающих центрах, станках с числовым программным управлением, электрофизическими методами. Например, лопатка ГТД, как нежесткая и сложная по форме, традиционно считалась крайне нетехнологичной с позиции механической обработки резанием. Однако ныне, с появлением метода электрохимической обработки пера в проточном электролите, лопатка является весьма технологичной деталью. Здесь уместно отметить, что технологичность не является абсолютным и неизменным критерием качества конструкции. Этот критерий может существенно меняться с появлением новых методов обработки, с изменением других условий производства (например, программы выпуска).
Конфигурация детали в целом даже при наличии простых поверхностей может затруднять применение высоко-производительной обработки. Так, ступенчатое расположение плоскостей А и Б делает невозможной обработку их на проход (рис. 3, а), в то время как в случае рис. 3, б такая возможность имеется. Наклонное расположение отверстия Ø А- не благоприятствует обработке всех отверстий в корпусе при одной установке детали (рис. 3, в). Этого недостатка лишена конструкция на рис. 3, г.
Одним из путей повышения производительности является многоместная обработка, поэтому детали, для которых применение этого вида обработки возможно, являются более технологичными (рис. 3, е). На деталях, показанных на рис. 3, д, многоместная обработка не результативна.
![]() |
Рис. 3 Конфигурации деталей
3.2.2. Инструментальная доступность.
![]() |
Рис. 4 Конфигурации деталей, поверхности которых доступны для обработки и измерения
|
|
Автоматическое растормаживание колес: Тормозные устройства колес предназначены для уменьшения длины пробега и улучшения маневрирования ВС при...
История создания датчика движения: Первый прибор для обнаружения движения был изобретен немецким физиком Генрихом Герцем...
Своеобразие русской архитектуры: Основной материал – дерево – быстрота постройки, но недолговечность и необходимость деления...
Биохимия спиртового брожения: Основу технологии получения пива составляет спиртовое брожение, - при котором сахар превращается...
© cyberpedia.su 2017-2024 - Не является автором материалов. Исключительное право сохранено за автором текста.
Если вы не хотите, чтобы данный материал был у нас на сайте, перейдите по ссылке: Нарушение авторских прав. Мы поможем в написании вашей работы!