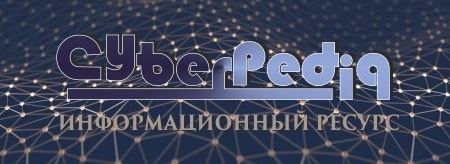
Особенности сооружения опор в сложных условиях: Сооружение ВЛ в районах с суровыми климатическими и тяжелыми геологическими условиями...
Индивидуальные очистные сооружения: К классу индивидуальных очистных сооружений относят сооружения, пропускная способность которых...
Топ:
Методика измерений сопротивления растеканию тока анодного заземления: Анодный заземлитель (анод) – проводник, погруженный в электролитическую среду (грунт, раствор электролита) и подключенный к положительному...
Выпускная квалификационная работа: Основная часть ВКР, как правило, состоит из двух-трех глав, каждая из которых, в свою очередь...
Интересное:
Как мы говорим и как мы слушаем: общение можно сравнить с огромным зонтиком, под которым скрыто все...
Подходы к решению темы фильма: Существует три основных типа исторического фильма, имеющих между собой много общего...
Лечение прогрессирующих форм рака: Одним из наиболее важных достижений экспериментальной химиотерапии опухолей, начатой в 60-х и реализованной в 70-х годах, является...
Дисциплины:
![]() |
![]() |
5.00
из
|
Заказать работу |
Содержание книги
Поиск на нашем сайте
|
|
3. Пайка на печатных платах. Общие сведения. Пайка волной припоя. Пайка в парогазовой среде. Пайка инфракрасным нагревом. Конвекционная пайка. Другие методы пайки. Припойная паста. Технология нанесения припойной пасты. Технологии изготовления трафаретов. Процесс трафаретной печати. Очистка плат после пайки.
4. Контроль в сборочном производстве печатных плат. Автоматическая оптическая инспекция. Рентгеновские контрольные технологические установки. Электрический контроль. Тестирование многослойных ПП. Платы для ВЧ-схем. Методы тестирования сборок. Внутрисхемное тестирование. Функциональное тестирование. Ремонт печатных плат.
Производство печатных плат на заключительной стадии сборочно-монтажных операций включает в себя следующие основные этапы: оплавление припоя с помощью печей или в машинах; отмывка плат; выходной контроль; ремонт дефектных плат, если он возможен; влагозащита плат; упаковка.
Пайка на печатных платах
Общие сведения. Пайка представляет собой распространенный способ монтажа компонентов в производстве радиоэлектронных узлов. При этом обеспечивается и механическое крепление выводов компонентов, и электрическое контактирование в соответствии с электрической принципиальной схемой. При пайке две металлические детали (или детали с металлическим покрытием) соединяются при помощи припоя - третьего металла или сплава. Соединяемые детали не расплавляются сами, расплавляется только припой. Поэтому пайка имеет более щадящий тепловой режим для деталей, чем сварка. Для получения качественного паяного соединения, обладающего хорошими электропроводящими и прочностными свойствами, необходимо обеспечить несколько условий:
1. Получить чистые металлические поверхности у соединяемых деталей (удалить загрязнения и пленки окислов) с помощью технологического флюса;
2. Нагреть припой выше точки плавления;
3. Обеспечить вытеснение флюса с помощью наступающего припоя;
4. Обеспечить растекание жидкого припоя по металлической поверхности;
5. Обеспечить диффузию атомов из твердой металлической фазы в жидкий припой и наоборот – образование сплавных зон.
Среди припоев в радиоэлектронике наиболее широкое распространение получили припои на основе композиции олова и свинца (ПОС). Сплав имеет особую точку, называемую точкой эвтектики. В этой точке температура кристаллизации припоя составляет 183 °С, что значительно ниже точек плавления Sn и Pb (232 °С и 327 °С).
Флюс является материалом, под воздействием которого происходит быстрое и совершенное смачивание металлической поверхности соединяемых деталей расплавленным припоем благодаря влиянию сил поверхностного натяжения. Кроме того, флюс обладает свойством растворения и удаления окисных слоев на контактируемых металлах и защиты очищенной поверхности от нового окисления. Остатки флюса должны легко удаляться, быть не изменять электрические параметры исходного материала и не вызывать коррозии. Распространены флюсы на основе органических кислот из смол хвойных пород деревьев (канифоль). Известно и большое количество синтетических материалов.
|
ПОС обладает практически оптимальными свойствами для РЭА: хорошей смачиваемостью, прочностью, пластичностью, удобной точкой плавления, коррозионной стойкостью, усталостной прочностью, и, наконец, стоимостью.
Появление на ПП поверхностно монтируемых компонентов существенно изменило технологию пайки. Пайка волной припоя была внедрена в середине прошлого века и до настоящего времени является единственным групповым методом пайки компонентов, устанавливаемых в отверстия ПП. Она выполняется чаще всего погружением обратной стороны платы с выступающими выводами в ванну с припоем. Для пайки плат со смешанным монтажом (компоненты, монтируемые в отверстия с одной стороны платы и простые, монтируемые на поверхность с другой) был разработан метод пайки двойной волной припоя.
Для пайки поверхностно монтируемых компонентов была разработана технология оплавления дозированного припоя. Методами трафаретной печати припой в виде пасты наносится на контактные площадки ПП, затем на него устанавливаются компоненты. В ряде случаев припойную пасту просушивают после нанесения с целью удаления из ее состава летучих ингредиентов или предотвращения смещения компонентов непосредственно перед пайкой. Оплавление припоя и получение паяных соединений происходит в нагревательном устройстве.
Пайка в парогазовой фазе (ПГФ), пайка расплавлением дозированного припоя с помощью инфракрасного нагрева (ИК-пайка), пайка в конвекционных печах, лазерная пайка.
|
Пайка волной припоя применяется только для пайки компонентов в отверстиях плат (традиционная технология), хотя некоторые изготовители утверждают, что с ее помощью можно производить пайку поверхностно монтируемых компонентов с несложной конструкцией корпусов, устанавливаемых на одной из сторон ПП.
Процесс пайки прост. Платы, установленные на транспортере, подвергаются предварительному нагреву, исключающему тепловой удар на этапе пайки. Затем плата проходит над волной припоя. Сама волна, ее форма и динамические характеристики являются наиболее важными параметрами оборудования для пайки. С помощью сопла можно менять форму волны. В настоящее время каждый производитель использует свою собственную форму волны (в виде греческой буквы «омега», Z-образную, Т-образную и др.). Могут варьироваться направление и скорость движения потока припоя, достигающего платы, но они должны быть одинаковы по всей ширине волны. Регулируется также угол наклона транспортера для плат. Некоторые установки для пайки оборудуются дешунтирующим воздушным ножом, который обеспечивает уменьшение количества перемычек припоя. Нож располагается сразу же за участком прохождения волны припоя и включается в работу, когда припой находится еще в расплавленном состоянии на ПП. Узкий поток нагретого воздуха, движущийся с высокой скоростью, уносит с собой излишки припоя, тем самым, разрушая перемычки и способствуя удалению излишков припоя.
Когда появились ПП, с обратной стороны которых устанавливались поверхностные компоненты, их пайка производилась волной припоя. При этом возникло множество проблем, а именно: непропаи и отсутствие галтелей припоя из-за эффекта затенения другими компонентами, преграждающими доступ волны припоя к соответствующим контактным площадкам, а также наличие полостей с захваченными газообразными продуктами разложения флюса, мешающих доступу припоя. Потребовалось изменить технологический процесс пайки волной, внедрив вторую волну припоя. Первая волна делается турбулентной и узкой, исходит из сопла под большим давлением. Турбулентность и высокое давление потока припоя исключает формирование полостей с газообразными продуктами разложения флюса. Однако турбулентная волна все же образует перемычки припоя, которые разрушаются второй, более пологой волной с малой скоростью истечения. Вторая волна устраняет перемычки припоя, а также завершает формирование галтелей. Для обеспечения эффективности пайки параметры каждой волны должны быть регулируемыми, волны должны иметь отдельные насосы, сопла и блоки управления.
Пайка двойной волной припоя применяется в настоящее время для одного типа ПП: с традиционными компонентами на лицевой стороне и простыми компонентами (чипами и транзисторами) на обратной. Некоторые компоненты (даже пассивные) могут быть повреждены при погружении в припой во время пайки. Поэтому важно учитывать их термостойкость и принимать меры предосторожности: применять поверхностно монтируемые ИС, не чувствительные к тепловому воздействию; снизить скорость транспортера; проектировать ПП таким образом, чтобы исключить эффект затенения. Хорошо разнесенные, не загораживающие друг друга компоненты способствуют попаданию припоя на каждый требуемый участок платы, но при этом снижается плотность монтажа. При высокой плотности монтажа с помощью данного метода практически невозможно пропаять поверхностно монтируемые компоненты с четырехсторонней разводкой выводов.
|
Пайка в парогазовой среде (ПГФ) с расплавлением дозированного припоя применима только к сборкам с поверхностным монтажом. Суть процесса: специальная жидкость нагревается до кипения, затем ее пары конденсируются на ПП, отдавая скрытую теплоту парообразования открытым участкам сборки. При этом припойная паста расплавляется и образуется паяное соединение между выводом компонента и контактной площадкой платы. Когда температура платы достигает температуры жидкости, процесс конденсации прекращается, тем самым заканчивается и нагрев пасты. Повышение температуры платы от ее начальной температуры до температуры расплавления припоя осуществляется очень быстро и не поддается регулированию. Поэтому необходим предварительный подогрев платы с компонентами для уменьшения термических напряжений в компонентах и местах их контактов с платой. Температура расплавления припоя также не регулируется и равна температуре кипения используемой при пайке жидкости. Такой жидкостью является инертный фторуглерод (например, FC-70).
В первых установках для пайки в ПГФ применялись две рабочих жидкости. С целью предотвращения утечки паров дорогого фторуглерода и припоя поверх основной технологической среды из инертного фторуглерода создавалась дополнительная технологическая среда из более дешевого фреона. Основной недостаток этих установок состоял в том, что на границе двух технологических сред происходило образование различных кислот и для защиты ПП требовались системы их нейтрализации. Затем стали выпускаться установки для пайки в ПГФ конвейерного типа, встраиваемые в технологические сборочно-монтажные линии. Такие установки имеют относительно небольшие входное и выходное отверстия, позволяющие реализовать систему с одной технологической средой.
Пайка инфракрасным нагревом (ИК-пайка) аналогична пайке в ПГФ, за исключением того, что нагрев платы с компонентами производится не парами жидкости, а ИК-излучением. Основным механизмом передачи тепла, используемым в установках пайки с ИК-нагревом, является излучение. В отличие от пайки в ПГФ, в процессе пайки с ИК-излучением скорость нагрева регулируется изменением мощности каждого излучателя и скорости движения транспортера с ПП. Поэтому термические напряжения в компонентах и платах могут быть снижены посредством постепенного нагрева сборок.
|
Инфракрасные печи применяются при изготовлении несложных плат. Обусловлено это тем, что инфракрасный тип нагрева имеет ряд отрицательных эффектов. Наиболее существенно влияют на работу следующие:
- количество энергии излучения, поглощаемой компонентами и платами, зависит от поглощающей способности материалов, из которых они изготовлены. Поэтому нагрев осуществляется неравномерно в пределах монтируемого устройства;
- высокие элементы могут закрывать более низкие, создавая «тень», где высока вероятность непропая;
- некоторые элементы корпусом могут закрывать свои собственные выводы (кристаллоносители без выводов или с J-образными выводами).
В некоторых установках для пайки с ИК-нагревом вместо ламп ИК-излучения применяются панельные излучающие системы. Излучение такой системы не нагревает непосредственно компоненты на сборке, а поглощается технологической средой (воздух или газ), которая в свою очередь передает тепло на ПП за счет конвекции. Этот способ пайки устраняет ряд недостатков, присущих пайке с ИК-нагревом, таких, как неравномерный прогрев отдельных частей сборки и невозможность пайки компонентов в корпусах, непрозрачных для ИК-излучения. Панельные излучатели обеспечивают намного меньшую скорость нагрева, чем традиционные источники ИК-излучения.
Конвекционная пайка лишена недостатков, связанных с теплопередачей излучением. Но управлять горячим воздухом труднее и технически сложнее. Конвекционная пайка реализуется в камерных или конвейерных печах. Камерные печи используются в лабораторных условиях, в единичном или мелкосерийном производстве. Конвейерные печи встраиваются в сборочные линии и используются, как правило, в крупносерийном производстве.
В камерных печах отработка профиля пайки осуществляется путем изменения температуры внутри камеры со временем, в конвейерных – перемещением платы по конвейеру через несколько зон печи (зоны нагрева и охлаждения). Как правило, максимальная температура, при которой происходит непосредственно оплавление пасты, составляет 210÷220 °C. Плата находится в печи при максимальной температуре в течение всего нескольких секунд, после чего производится ее охлаждение.
В ряде случаев применяется пайка в инертной среде, при которой осуществляется впуск азота в рабочую область печи. Эта операция используется для сведения к минимуму окислительного процесса. Однако необходимо оценивать необходимость этой операции. В случае если процесс пайки длится небольшой промежуток времени, припой не успеет окислиться, так как в его состав входит флюс, обеспечивающий растворение окислов на поверхности частиц порошка припоя. Пайка в инертной среде потребует большого расхода азота, что повлечет за собой использование азотной станции с существенными дополнительными расходами. Использование азотной среды при конвекционной пайке оправдано только в условиях серийного производства при изготовлении сложных модулей, требующих высокого качества исполнения.
|
Другие методы пайки. Метод пайки расплавлением дозированного припоя с помощью нагретого приспособления разработан в Японии применительно к изделиям бытовой электроники с невысокой плотностью монтажа. ПП с компонентами помещается на теплопроводящий транспортер, содержащий набор специальных пластин, температура которых контролируется. Пластины подбираются по габаритам компонента, прижимают выводы к контактным площадкам и передают тепло для оплавления припоя. Метод рекомендован к применению для пайки ТАВ корпусов и flat-pack, имеющих весьма тонкие выводы, подверженные изгибанию. Во время прижима осуществляется разогрев соединения до точки оплавления припоя по запланированному графику, а затем идет процесс охлаждения паяного контакта, и только затем убирается инструмент. Процесс последовательный, достаточно медленный, однако обеспечивает надежную пайку для ответственных и дорогих деталей.
Пайка расплавлением дозированного припоя с помощью лазерного излучения также является последовательным процессом. Для нагрева соединений применяются твердотельные либо газовые лазеры. Главное достоинство лазерной пайки заключается в том, что пучок лазерной энергии хорошо фокусируется. Метод особенно эффективен для пайки термочувствительных компонентов и компонентов с малым шагом выводов. Некоторые из наиболее сложных сборок на платах (например, центральные процессоры вычислительных машин) размером 254x305 мм могут иметь до 10000÷15000 паяных соединений. Главным здесь является качество и надежность паяных соединений, а не производительность установки.
На качество паяных соединений узла влияет множество факторов, в том числе и выбранный конструктором вариант размещения компонентов. Корпуса для больших и сверхбольших интегральных микросхем изготавливаются из материалов, которые должны обеспечивать хороший теплоотвод от корпуса ИМ в процессе эксплуатации. Низкое тепловое сопротивление корпуса, большая масса и теплоемкость крупных корпусов не позволяют получить одинаковую температуру в области выводов при пайке малых и больших корпусов, расположенных на плате в непосредственной близости. Такой эффект необходимо иметь в виду и технологу, и конструктору.
Припойная паста. Для нанесения методом трафаретной печати через металлический трафарет или для нанесения дозатором разрабатываются различные варианты паяльных паст. Характеристики припойных паст в первую очередь определяются их составом.
Припойные пасты представляют собой смесь мелкодисперсного порошка материала припоя со связующей жидкой основой, в которую входит флюс. Содержание порошка припоя составляет приблизительно 88% от веса пасты. Состав паст выражают через соотношение ингредиентов материала припоя. Так, например, 63/37 означает содержание в составе материала припоя 63% олова и 37% свинца.
Характеристики частиц материала припоя в пасте оказывают существенное влияние на качество паяного соединения. Наиболее важным параметром является размер частиц припоя. Если припойная паста наносится на ПП через сеточный трафарет, рекомендуется применять припойную пасту, у которой максимальный размер частиц припоя составляет половину размера ячейки трафарета. Форма частиц материала припоя также оказывает влияние на процесс трафаретной печати. Частицы припоя сферической формы облегчают процесс трафаретной печати и позволяют получать хорошую воспроизводимость технологического процесса от одной партии изделий к другой при формировании рисунка припойной пасты. Наличие в пасте частиц другой формы может способствовать появлению загрязнений, затрудняющих процесс печати, и ускорению процессов окисления материалов припоя. Пульверизация расплавленного припоя, с помощью которой наиболее просто получить порошкообразные припои, образует частицы преимущественно сферической формы.
Флюс в составе припойных паст служит не только для активации металлических поверхностей, удаления с них окислов и предотвращения окисления припоя в процессе пайки, но и обеспечивает требуемую растекаемость и изменение вязкости со временем при нанесении припойной пасты на ПП. Если состав припойной пасты имеет недостаточную вязкость, она будет растекаться, что приведет к потере точности рисунка. Для уменьшения растекания пасты можно увеличить процентное содержание в ней порошка припоя или изменить химический состав флюса путем введения в него специальных вяжущих добавок (загустителей). Но здесь нужно соблюдать меру, ибо в противном случае может произойти закупорка сопла дозатора или ячеек трафарета.
Флюс должен удалять окислы с контактируемых металлических поверхностей при пайке. Для эффективного протекания этого процесса очень важно правильно выбрать необходимый температурно-временной режим пайки (температурный профиль). Если во время разогрева платы температура повышается слишком быстро, то растворитель, входящий в припойную пасту в составе флюса, быстро испаряется, что приводит к потере активности флюса, неравномерному расплавлению припоя, разложению или выгоранию его компонентов. Если же нагревательный цикл завершен преждевременно, то окислы в местах паяных соединений могут быть не полностью удалены.
Для избегания окисления припоя формирование слоя припойной пасты рекомендуется производить в химически инертной атмосфере. Хранение пасты рекомендуется осуществлять в прохладном месте с температурой от +5 до +10 °С. Минимальный срок хранения паяльной пасты с флюсом при такой температуре составляет 6 месяцев с даты производства. Перед применением емкость с пастой необходимо выдержать при комнатной температуре до полной стабилизации в течение 2÷8 часов. Не рекомендуется открывать холодную емкость, это может вызвать конденсацию влаги и ухудшение параметров паяльной пасты. Категорически не допускается подогрев пасты нагревательными приборами.
Как правило, паяльные пасты с флюсом полностью готовы к применению и не требуют дополнительных разбавителей. Паяльная паста, которая не была использована в течение рабочей смены, не должна смешиваться со свежей пастой. Остатки пасты рекомендуется складывать в отдельную тару и использовать в начале следующей смены. Не рекомендуется использовать пасту, которая находилась на трафарете две рабочих смены. Если устройство трафаретной печати не использовалось в течение четырех часов, рекомендуется произвести полную очистку трафарета от остатков паяльной пасты.
Распространенными материалами выводов и внешних контактов электронных компонентов являются золото, серебро, палладий-серебро, медь, луженая медь, и припойная паста должна выбираться таким образом, чтобы исключить выщелачивание этих материалов. Большинство паяльных паст с флюсом обладают хорошими клеящими свойствами, достаточными для удержания компонентов после установки до пайки в течение до 8 часов. Клеящие свойства пасты зависят от температуры и влажности, поэтому рекомендуется произвести испытания для определения максимального времени удержания пастой компонентов в условиях реального производства. Печатные платы могут быть запаяны в течение 24 часов после нанесения паяльной пасты без ухудшения качества пайки, высокая температура и влажность могут сокращать это время.
Рекомендуемые режимы процесса пайки для наиболее популярных сплавов Sn63/Pb37 и Sn62/Pb36/Ag2, входящих в состав паст, таковы:
1) стадия предварительного нагрева от 20 до 140 °С, скорость нагрева 1 °С/сек;
2) стадия предварительной сушки от 140°С до 160°С, скорость нагрева 0,5 °С/сек;
3) стадия пайки от 160 до 215 °С, скорость нагрева 2 °С/сек.
Более длительное время стадии пайки может улучшить качество паяного соединения, уменьшить количество и сделать более инертными остатки флюса после пайки. Более короткое время пайки может также дать хорошие результаты, однако в этом случае возможно увеличение количества остатков флюса после пайки. Рекомендуется обеспечить время выдержки выше температуры плавления (+183 °С) в пределах от 30 до 60 сек. Минимальная пиковая температура в зоне пайки должна быть не менее 210 °С в течение 5 сек. Увеличение скорости повышения температуры на стадии предварительного нагрева может привести к увеличению остатков флюса после пайки и ухудшению внешнего вида паяного соединения. Этот косметический дефект полностью устраняется при отмывке остатков флюса.
Вышеуказанные рекомендации служат для первоначальной установки режимов пайки. Конкретные режимы пайки определяются технологом исходя из конструкции печатной платы и оборудования для пайки.
Технология нанесения припойной пасты. Процесс нанесения паяльной пасты зависит от большого числа составляющих:
- от характеристик оборудования – принтеров, держателей плат и др.;
- от трафаретов – формы и размеров отверстий, качества стенок отверстий, толщины трафарета;
- от параметров процесса нанесения пасты – скорости, угла атаки, давления и жесткости ракеля, скорости отделения трафарета, зазора между трафаретом и платой;
- от припойной пасты – размера частиц, объемного содержания металла, вязкости пасты, подвижности флюса;
- от параметров рабочего помещения – температуры, влажности, пыли.
Припойная паста может наноситься с помощью механических устройств для трафаретной печати (ручной способ), с помощью автоматических принтеров, с помощью дозаторов.
Дозаторы – устройства последовательной обработки, паста наносится по программе в определенном объеме на заданные точки ПП. Автоматический дозатор представляет собой рабочий стол, на который крепится обрабатываемая плата. Над рабочим полем перемещается дозатор, который осуществляет нанесение материалов на плату, для управления используется персональный компьютер. Ключевые параметры дозаторов: скорость дозирования (до 15 тыс. точек в час) и максимальный формат обрабатываемой платы (до 450x450 мм). Как и любой последовательный процесс, такой способ нанесения пасты занимает гораздо больше времени, чем трафаретная печать. Однако для дозатора не требуется разрабатывать и изготавливать трафарет. При малых объемах производства (единичные платы) для нанесения материалов можно применять и ручное дозирование.
Если на производстве изготавливается большое число конструкций плат при малом их количестве, то целесообразно применять метод дозирования, особенно при лабораторном производств, так как стоимость изготовления трафаретов (по одному на каждую сторону каждой разновидности плат) может оказаться больше стоимости изготовления самих плат. В случае промышленного производства, напротив, нанесение материалов методом дозирования нежелательно из-за низкой скорости процесса по сравнению с трафаретной печатью. На крупносерийных производствах стоимость трафаретов не вносит заметного вклада в общие расходы.
Устройства трафаретной печати могут быть как ручными, так и автоматическими.
Ручной принтер представляет собой сравнительно простое устройство: на металлической раме закрепляется трафарет, после чего раму крепят к рабочему столу, на котором находится плата, давление на ракель осуществляется оператором вручную. В автоматических принтерах все операции – совмещение трафарета и печатной платы, осуществление приводного давления на ракель, дозирование припойной пасты на трафарет – выполняются автоматически. Эти устройства могут работать как автономно, так и в составе производственной линии. Основные параметры автоматических принтеров: максимальный формат платы, который может достигать значения 510х510 мм, и скорость перемещения ракеля (до 150 мм/с).
Очистка плат после пайки. Обычная ПП содержит много внутренних полостей (в том числе и под компонентами), имеющих выход на поверхность через узкие вертикальные зазоры между компонентами или их выводами. Эти полости способны удерживать продукты разложения флюса и другие загрязнения, которые могут стать источниками коррозии или причиной проникновения внутрь корпусов компонентов веществ, вызывающие повышенные токи утечки. Усиленные попытки очистить плату, например, с помощью органических растворителей, сами по себе могут вызвать механические повреждения или коррозию.
Как правило, загрязнения бывают либо полярными (ионы), либо неполярными. Свободные ионы, особенно электроотрицательные, обладающие высокой химической активностью, быстро вступают в реакцию с металлом коммутационных дорожек и вызывают коррозию. Неполярные загрязнения ухудшают адгезию припоя, свойства защитного покрытия и электрический контакт для функционального испытания микросборки.
Органические растворители в соответствии с их очистной способностью можно разделить на три группы. Гидрофобные - не смешиваются с водой, используются для растворения органических загрязнений, например канифоли и жиров. Гидрофильные - смешиваются с водой, растворяют полярные и неполярные соединения, причем последние в меньшей степени, чем гидрофобные растворители. Азеотропные - представляют собой в основном смесь вышеуказанных типов растворителей. В их состав обязательно входят такие ингредиенты, как фреон-113 или тетрахлордифторэтан, с добавками спиртов и стабилизирующих ингредиентов.
Очистка изделий с применением растворителей может быть реализована погружением плат в ванну с растворителем, равномерным по полю платы или направленным в виде струй опрыскиванием, либо комбинацией обоих методов. Может применяться ультразвуковое перемешивание при очистке плат в ванне с растворителем. На эффективность очистки может повлиять ряд факторов, в том числе расположение компонентов. Компоненты должны размещаться на поверхности платы таким образом, чтобы их корпуса не загораживали друг друга при движении потока растворителя. Прерывания движения платы и остановки во время пайки волной припоя должны быть сведены к минимуму, чтобы флюс нигде не задерживался в полостях платы. Если используются чувствительные компоненты, рекомендуется обрабатывать микросборки в потоке растворителя. При этом необходимо обеспечить максимальную однородность потока растворителя, а интервал времени между пайкой и очисткой уменьшить до минимума.
|
|
Архитектура электронного правительства: Единая архитектура – это методологический подход при создании системы управления государства, который строится...
Организация стока поверхностных вод: Наибольшее количество влаги на земном шаре испаряется с поверхности морей и океанов (88‰)...
История развития пистолетов-пулеметов: Предпосылкой для возникновения пистолетов-пулеметов послужила давняя тенденция тяготения винтовок...
Биохимия спиртового брожения: Основу технологии получения пива составляет спиртовое брожение, - при котором сахар превращается...
© cyberpedia.su 2017-2024 - Не является автором материалов. Исключительное право сохранено за автором текста.
Если вы не хотите, чтобы данный материал был у нас на сайте, перейдите по ссылке: Нарушение авторских прав. Мы поможем в написании вашей работы!