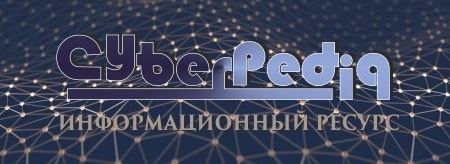
Индивидуальные и групповые автопоилки: для животных. Схемы и конструкции...
Механическое удерживание земляных масс: Механическое удерживание земляных масс на склоне обеспечивают контрфорсными сооружениями различных конструкций...
Топ:
Проблема типологии научных революций: Глобальные научные революции и типы научной рациональности...
Эволюция кровеносной системы позвоночных животных: Биологическая эволюция – необратимый процесс исторического развития живой природы...
Интересное:
Влияние предпринимательской среды на эффективное функционирование предприятия: Предпринимательская среда – это совокупность внешних и внутренних факторов, оказывающих влияние на функционирование фирмы...
Аура как энергетическое поле: многослойную ауру человека можно представить себе подобным...
Наиболее распространенные виды рака: Раковая опухоль — это самостоятельное новообразование, которое может возникнуть и от повышенного давления...
Дисциплины:
![]() |
![]() |
5.00
из
|
Заказать работу |
|
|
ДИПЛОМНЫЙ ПРОЕКТ
На тему: Реконструкция системы пылегазоочистки сушильного отделения на «Втором Березниковском калийном производственном рудоуправлении» ОАО «Уралкалий»
Студент (Иванов Иван Иванович)
Состав дипломного проекта:
1. Пояснительная записка на ____ стр.
2. Графическая часть на 6 листах.
Руководитель дипломного проекта
(Тимофеев И.Е.)
Березники, 2015 г.
Фамилия И.О. Иванов Иван Иванович
Тема: Реконструкция системы пылегазоочистки сушильного отделения на «Втором Березниковском калийном производственном рудоуправлении» ОАО «Уралкалий»
РЕФЕРАТ
Выпускная квалификационная работа стр., 6 рис., табл., источников.
ХЛОРИД КАЛИЯ, ГАЗООЧИСТКА, СУШКА, ПЫЛЕУЛАВЛИВАНИЕ, ПЕЧЬ «КС», РУКАВНЫЙ ФИЛЬТР.
Объект проектирования – отделение сушки на флотационной обогатительной фабрике.
Новизна проекта заключается в замене скруббера Вентури и каплеуловителя на рукавный фильтр на второй стадии очистки.
Замена оборудования позволит вернуть в процесс мелкую фракцию хлорида калия, которая раньше считалась потерей.
Был произведен расчет материального и теплового балансов, по результатом, которых определены размеры основного и вспомогательного оборудования: печь «КС»,циклон ЛИОТ, рукавный фильтр.
В строительной части выполнена компоновка оборудования отделения сушки представленная на плане и разрезе.
В разделе безопасности производственной деятельности предложены мероприятия по охране труда и технике безопасности.
СОДЕРЖАНИЕ
ВВЕДЕНИЕ.. 4
1. АНАЛИТИЧЕСКИЙ ОБЗОР ЛИТЕРАТУРЫ... 6
ТЕХНИКО-ЭКОНОМИЧЕСКОЕ ОБОСНОВАНИЕ СЫРЬЯ, ЭНЕРГОРЕСУРСОВ, МОЩНОСТИ ПРОИЗВОДСТВА, ГЕОГРАФИЧЕСКОЙ ТОЧКИ СТРОИТЕЛЬСТВА.. 10
|
ТЕОРЕТИЧЕСКИЙ АНАЛИЗ. 14
МАТЕРИАЛЬНЫЙ БАЛАНС.. 17
Материальный баланс сушки. 17
Материальный баланс по влаге. 18
Материальный баланс процесса пылегазоочистки. 19
Расчёт горения природного газа. 20
ТЕПЛОВОЙ БАЛАНС.. 30
ТЕХНОЛОГИЧЕСКИЕ РАСЧЁТЫ ОБОРУДОВАНИЯ.. 34
Описание и принцип действия апарата «КС». 34
Расчет основного апарата сушильного отделения. 34
6.3. Описание и расчет внедряемого в проект аппарата (рукавного фильтра) 38
МОДЕЛИРОВАНИЕ.. 42
Конструктивный расчет печи «КС» с использованием математического моделирования 42
АВТОМАТИЗАЦИЯ.. 46
Общие сведения. 46
Характеристика объекта управления. 47
Выбор точек контроля и регулирования. 47
Выбор системы приборов. 50
Описание действия контура регулирования. 50
ТЕХНОЛОГИЧЕСКАЯ СХЕМА.. 56
10. ОХРАНА ОКРУЖАЮЩЕЙ СРЕДЫ... 57
ОХРАНА ТРУДА.. 64
Охрана труда в Российской Федерации. 64
Свойства используемых и получаемых веществ. Опасные и вредные производственные факторы 65
Классификация производства. 68
Мероприятия по технике безопасности. 71
Санитарно – технические мероприятия. 77
Противопожарные мероприятия. 78
Расчет высоты дымовой трубы.. 80
СТРОИТЕЛЬНАЯ ЧАСТЬ.. 82
Климатические и геологические условия месторасположения производства. 82
12.2. Объёмно - планировочное решение здания. 82
Компоновка оборудования отделения. 84
ЭКОНОМИЧЕСКАЯ ЧАСТЬ.. 85
Анализ рыночных перспектив и оценка производственных возможностей предприятия. 85
Анализ действующего производства. 87
Экономическое обоснование и расчёты по проекту. 90
Заключение об эффективности проекта. 117
ЗАКЛЮЧЕНИЕ.. 118
СПИСОК ИСПОЛЬЗОВАННОЙ ЛИТЕРАТУРЫ... 119
ВВЕДЕНИЕ
Открытое акционерное общество ОАО «Уралкалий» является ведущим поставщиком широкого ассортимента высококачественных продуктов на основе природных калийных, натриевых и магниевых солей.
|
ОАО "Уралкалий" - крупный производитель минеральных удобрений, в основном занимается продажей хлорида калия за границу. Основное количество выпускаемых удобрений отгружается на экспорт в такие страны, как Бразилия, Китай, Польша, ФРГ и другие.
Хлористый калий (KCl) является самым распространённым калийным удобрением.
Хлорид калия (KCl) представляет собой быстро растворимое удобрение, которое легко усваивается растениями. Может выпускаться в виде мелкозернистого или гранулированного продукта, различных оттенков красного, а также белого цвета в зависимости от способа производства.
Хлористый калий может быть сырьём в получении калиевой селитры (KNO3) и бертолетовой соли(KClO3), однако свыше 90 процентов его применяют в сельском хозяйстве в качестве минеральных удобрений, поскольку калий наряду с азотом и фосфором – один из важнейших элементов, необходимых для повышения урожайности.
Процесс сушки хлористого калия заключается в удалении влаги из материалов путем испарения ее и отвода образующихся паров, с целью улучшения качества продукта, предохранения его от слеживания, снижения массы, придания транспортабельности и т.д.
Основной задачей современной сушильной техники является создание новых комбинированных методов сушки, которые обеспечивали бы не только интенсификацию процесса, но и наилучшие технологические свойства высушиваемого материала.
В последние годы в промышленной практике широко используется метод «кипящего слоя» в качестве одного из действенных средств интенсификации производства. Целый ряд процессов химической технологии (обжиг руд и концентратов, сушка различных материалов и т.д.) производится в кипящем слое.
Важным свойством взвешенного слоя – является его текучесть, подобная текучести жидкости. Вследствие текучести «кипящий слой» («КС») называют псевдоожиженым. То есть процесс сушки в печах «КС» заключается в псевдоожижении сыпучего материала горячим потоком газа (сушильного агента) при скорости последнего, достаточной для перевода материала из неподвижного состояния в состояние кипения.
Сушка хлористого калия, в печах с псевдоожиженным слоем приводит к образованию пылегазовых выбросов, загрязняющих атмосферный воздух. Жёсткие современные требования по защите атмосферного воздуха обусловливают необходимость разработки и освоения, новых более эффективных средств и методов защиты атмосферы на предприятиях.
|
Система пылегазоочистки, рассматриваемого в проекте процесса, состоит из двух стадий. Первая стадия сухой пылегазоочистки (ПГО) и вторая стадия –мокрой. Стадия сухой ПГО происходит в циклонах ЛИОТ со вставками верхней части, выполненными из листов стали, и расположенных ступенчато, по окружности, с зазорами для прохода газов. Мокрая стадия представлена трубами Вентури с каплеуловителями.
Основным недостатком второй стадии очистки является образование больших объемов солевого шлама.
В данном проекте предлагается заменить скруббер Вентури на рукавный фильтр, тем самым снизить затраты на очистку газа и увеличить степень очистки газа практически до 100%.
Рукавные фильтры компактны, что делает их незаменимыми при проведении реконструкции (модернизации) газоочистного оборудования. Используемые в рукавных фильтрах фильтровальные материалы позволяют осуществлять очистку в широком диапазоне температур окружающей среды — от отрицательных значений до 300-500 °С;
Данные фильтры могут устанавливаться в различных климатических условиях.
Капитальные затраты на установку, а также время на монтаж и ввод в эксплуатацию рукавного фильтра низки, что является критически важным при проведении реконструкций, требующих остановки основного технологического оборудования.
Таким образом, можно уверенно утверждать, что использование рукавных фильтров является наиболее перспективным способом очистки газов и аспирационного воздуха от твердых компонентов.
ТЕОРЕТИЧЕСКИЙ АНАЛИЗ
Эффективность очистки газов (степень очистки, коэффициент полезного действия) обычно выражается отношением количества уловленного материала к количеству материала, поступившего в газоочистной аппарат с газовым потоком за определенный период времени.
Степень очистки газа в пылеуловителе, или его эффективность, представляет собой отношение массы пыли, уловленной пылеуловителем Gу, к массе поступившей в него пыли Gвх:
|
где Gвых – масса вынесенной пыли.
Степень очистки можно вычислить, исходя из концентраций пыли до Gвх и после пылеуловителя Gвых:
На стадию пылегазоочистки поступает 65000 м3/ч неочищенного газа.
По данным регламенты на первую стадию пылегазоочистки поступает 10500 кг/ч пыли хлористого калия. На выходе их циклона ЛИОТ – 1050 кг/ч.
Таким образом, эффективность очистки в циклоне ЛИОТ составляет:
Содержание пыли в газе после сухой очистки:
г/м3
На выходе со второй стадии пылегазооистки в скруббере Вентури запыленность газа составляет 31,5 кг/ч. Следовательно:
Эффективность второй стадии очистки составляет 97%.
Содержание пыли в газе после мокрой очистки:
г/м3
После введения новшества, скруббер Вентури будет заменен на рукавный фильтр. Исходя из паспортных данных, следует, что степень очистки в рукавных фильтрах достигается 99,99%.
Тогда:
Запыленность газа составит:
Содержание пыли в газе:
г/м3
Рисунок 4 – Эффективность пылеулавливания
1 – эффективность пылеулавливания первой стадии очистки в циклонах ЛИОТ; 2 – второй стадии до введения новшества; 3 – второй стадии после введения новшества.
Зависимость эффективности осаждения от размеров частиц.
Осаждение полидисперсных частиц в фильтрах происходит при совместном участии процессов диффузии, касания и инерции. При этом самые мелкие частицы осаждаются преимущественно в результате диффузии, а более крупные – под воздействием эффектов касания и инерции.
Определение размера наиболее проникающих частиц (rmax) для фильтров тонкой очистки имеет большое практическое значение, так как если известен размер таких частиц и обеспечена требуемая эффективность их осаждения, то более эффективное улавливание частиц всех других размеров тем более гарантировано. При разработке новых фильтров и оценке их работы необходимо применять монодисперсные аэрозоли, содержащие наиболее проникающие частицы, или полидисперсные аэрозоли, в которых медианно-весовой размер частиц близок к rmax.
Для большинства высокоэффективных фильтрующих материалов в обычных условиях фильтрации rmax составляет 0,05-0,2мкм (чаще 0,15мкм). Вследствие селективности при пропускании недостаточно монодисперсного аэрозоля через два одинаковых последовательно расположенных фильтра коэффициент проскока через второй фильтр будет всегда больше, чем через первый, который пропускает в основном наиболее проникающие частицы размером rmax. [6, 7].
Рассчитаем зависимость эффективности пылеулавливания от диаметра частицы, используя при этом электронные таблицы.
В расчетах возьмем диаметр частиц в диапазоне от 0 мм до 0,002 мм и рассчитаем при каком диаметре частиц, работа фильтра и скруббера будет наиболее эффективна.
|
Построим график зависимости эффективности от диаметра частиц.
Рисунок 5 – Зависимость эффективности пылеулавливания от размера частиц
1 – эффективность пылеулавливания в рукавном фильтре; 2 – эффективность пылеулавливания в скруббере Вентури.
Можно сделать вывод что, чем больше диаметр частиц, тем выше степень пылегазоочистки.
Из графика видно, что эффективность очистки в рукавном фильтре выше, чем в скруббере Вентури.
МАТЕРИАЛЬНЫЙ БАЛАНС
Необходимые данные для расчета:
Производительность по выпускаемому материалу: G2 = 120,Т/ч
Влажность соли: wн = 7%;
wк = 0,1%;
Плотность соли: r = 2000 кг/м3
Удельная теплоемкость сухой соли: Ссух.= 0,712*103 кДж/кг*К
Температура плавления соли: ТС = 768,0С
Теплоемкость подводимого теплоносителя: t1 = 600,0С
Температура отходящих газов: t2 = 125,0С
Температура воздуха на входе в топку: t2 = 180С (-160С)
Относительная влажность воздуха: j = 72%(84%)
Начальная температура соли: qн = 20,0С
Конечная температура соли: qк = 110,0С
Удельные потери тепла в окружающую среду на 1кг испарённой влаги qп=42,25
Материальный баланс сушки
В аппаратах КС зоной взаимодействия твердых частиц и газов является псевдоожиженный слой, образующийся на газораспределительной решетке, при подаче на нее сверху влажного продукта, а снизу - теплоносителя, который создает эффект псевдоожижения.
Количество испаряемой влаги:
;
где G2 – производительность по готовому продукту кг/ч;
– начальная влажность соли %;
– конечная влажность соли %;
кг/ч;
Тогда условие материального баланса запишется следующим образом:
для всего материала:
;
кг/ч;
Материальный баланс по абсолютно сухому веществу, количество которого не изменяется в процессе сушки.
;
;
119880=119880
Таблица 3 - Материальный баланс по продукту
Приход | кг | Расход | кг |
G1 | 128903,23 | G2 | |
W | 8903,23 | ||
Итог | 128903,23 | Итог | 128783,23 |
Невязка баланса составляет 0,093%
ТЕПЛОВОЙ БАЛАНС
Суммарный расход тепла в сушке:
;
где - расход тепла на испарения;
- расход пепла на нагрев материала;
- потери тепла.
Расход тепла на испарения влаги.
;
;
Удельный расход топлива на испарение влаги:
;
;
Расход тепла на нагрев материала:
;
;
;
;
Удельные потери теплоты с материалом :
;
Удельные потери тепла в окружающую среду, зависят от затрат на испарение и нагрев материала :
;
где - конечная температура соли;
- начальная температура соли.
;
Потери теплоты в окружающую среду :
;
;
;
;
- что соответствует регламентным данным потерь тепла в окружающую среду 3% от затрат тепла на испарение и нагрев материала.
Запишем уравнение внутреннего теплового баланса сушилки:
;
где - разность между удельными приходом и расходом тепла непосредственно в сушильной камере;
- теплоемкость влаги во влажном материале при температуре
;
- удельный дополнительный подвод тепла в сушильную камеру, при работе сушилки по нормальному сушильному варианту
;
- удельный подвод тепла в сушилку с транспортными средствами, в нашем случае
;
- удельный подвод тепла в сушилку с высушиваемым материалом;
- удельные потери тепла в окружающую среду.
.
Тепловой баланс сушки
;
Приход.
С теплоносителем, кДж/ч;
;
кДж/ч;
где - количество теплоносителя, кг/ч;
- энтальпия газа на входе в сушку кДж/ч.
С влажным материалом, поступающим на сушку, кДж/ч;
;
кДж/ч;
где - производительность сушки,кг/ч;
- теплоемкость высушиваемого материала, кДж/кг*К;
-начальная температура материала, 0С;
С влагой испаряемой из материала, кДж/ч:
;
кДж/ч;
где - количество испаряемой влаги, кг/ч;
- теплоемкость испаренной воды, кДж/кг*К;
-начальная температура материала, 0С.
Расход.
С отработанным теплоносителем, кДж/ч;
;
кДж/ч;
где - количество сушильного агента, кг/ч;
- теплосодержание отработанного сушильного агента, кДж/ч.
С высушенным материалом, кДж/ч:
;
кДж/ч;
где -конечная температура материала, 0С.
Потери в окружающую среду, кДж/ч:
кДж/ч
Таблица 8 - Сводный тепловой баланс
Приход, кДж/ч | % | Расход, кДж/ч | % |
1. С теплоносителем ![]() | 1. С отработанным теплоносителем ![]() | ||
Приход, ![]() | % | Расход, ![]() | % |
2. С влажным материалом, поступающим на сушку ![]() | 3,5 | 2. С высушенным материалом ![]() | |
3. С влагой испаряемой из материала 671481,61 | 1,5 | 3. Потери в окружающую среду ![]() | |
Итого: 45 442 424,69 | Итого: 45 442 562,93 | ||
Неувязка: 0,0003% |
[3, 5]
МОДЕЛИРОВАНИЕ
АВТОМАТИЗАЦИЯ
Общие сведения
Современные химические производства характеризуются значительной сложностью и высокой интенсивностью технологических процессов. Эффективное управление такими производствами основано на комплексной автоматизации технологических процессов.
Основу автоматизации производства составляют автоматизированные и автоматические системы управления технологическими процессами, агрегатами и производствами с использованием управляющих ЭВМ и средств автоматизации. Применение автоматизированных систем управления повышает уровень организации производства, оперативность управления технологическим процессом, сокращает цикл производства и внутрипроизводственные запасы, обеспечивает более полное использование материалов. Появляется возможность перехода к оптимизированным технологическим процессам, что увеличивает производительность агрегатов, повышает эффективность использования сырья и материалов, предотвращает аварийные ситуации. При этом качество готового продукта улучшается, а его характеристики стабилизируются.
В автоматизированном производстве человек переключается на творческую работу-анализ результатов управления, составление заданий и программ для автоматических устройств и т. д. Для обслуживания агрегатов, оснащенных сложными системами автоматизации, требуются специалисты с высоким уровнем знаний. С повышением квалификации и культурного уровня рабочих стирается грань между физическим и умственным трудом.
Достижение эффективности от внедрения систем и средств автоматизации в калийной промышленности особенно важно в связи с тем, что производства этой подотрасли горнорудной промышленности являются трудоемкими, выпускают продукцию, пользующуюся повышенным спросом, применяя при этом разнообразное технологическое оборудование и потребляя значительное количество материалов и энергии.
Комплексная автоматизация производственных процессов химической промышленности невозможна без автоматизации управления отдельными этапами процесса и основными аппаратами технологической линии. Процессы сушки играют существенную роль в химическом производстве как по энергоемкости, так и по влиянию на качество выпускаемой продукции. В соответствии с большим разнообразием процессов химической технологии и требований, предъявляемых к готовой продукции, в химической промышленности используют различные виды сушки и разнообразные типы и конструкции сушильных установок. Автоматизация их отличается от автоматизации прочих химико-технологических агрегатов. Эта специфика определяется особенностями динамических свойств сушильных аппаратов как объектов управления; многотонажностью производства, следствием чего зачастую является распределенность параметров объекта и необходимость обоснованного размещения датчиков в сушильной камере; многочисленностью контролируемых и регулируемых параметров и сложностью выбора критерия оптимальности, связанного с показателями качества продукта и с экономичностью процесса сушки.
Основная задача управления процессом сушки концентрата флотационной фабрики – получение продукта с влажностью не превышающей допустимую при минимальных затратах топлива.
Выбор системы приборов
Существуют следующие системы приборов:
1) Пневматические
2) Электрические
3) Гидравлические
Пневматические и гидравлические системы приборов используются при передаче сигналов на сравнительно небольшие расстояния. Электрические системы приборов используются при передаче сигналов на большие расстояния.
Применение пневматических измерительных приборов связано с их взрыво- и пожаробезопасностью, а также их более низкой стоимостью по сравнению с электрическими приборами.
Использование однотипных средств (например использование однотипных датчиков давления и однотипных вторичных приборов) дает значительные эксплуатационные преимущества, как с точки зрения настройки, так и при техническом обслуживании.
Для контроля значений расходов используются камерные и бескамерные диафрагмы, преобразователи разности давления САПФИР-22ДД, а также "Метран-43" и "Метран-45", получивших признание благодаря высоким техническим и эксплуатационным характеристикам.
Для контроля температуры применяются преобразователи термоэлектрические ТХА/ТХК-0192), сигнал которых поступает на контроллер Honeywell.
Для контроля количества произведенного хлористого калия используют Весы конвейерные фирмы "MILLTRONICS".
Также необходим контроль запального и основного факелов с помощью ионизационного датчика, фотодатчика, управляющего прибора, электромагнитного вентиля.
В ПЭВМ заложена программа, предусматривающая аварийную остановку оборудования.
ТЕХНОЛОГИЧЕСКАЯ СХЕМА
В отделении сушки концентрат хлористого калия доводится до товарной кондиции. В процессе сушки содержащаяся в концентрате вода переводится в газообразное состояние при помощи тепла. Концентрат хлористого калия сушится конвективным способом. В качестве сушильного агента используются дымовые газы, представляющие собой смесь продуктов сгорания топлива (природного газа) и воздуха. Для того чтобы готовый продукт не слёживался и не пылил, его обрабатывают реагентами - пылеподавителями и антислёживателями.
Сушка-это процесс удаления влаги путем ее испарения и отвода образовавшихся паров. Наиболее широкое применение в промышленной практике нашли установки «кипящего слоя» («КС») для сушки различных материалов. Процесс сушки в печах «КС» заключается в псевдоожижении сыпучего материала горячим потоком газа (сушильного агента) при скорости последнего, достаточной для перевода материала из неподвижного состояния в состояние кипения. Процесс сушки в СГО «БКПРУ-2» осуществляется в 5-и печах» КС»: «КС» -1, КС -2, «КС»-3 и «КС»-4, «КС»-5. В качестве сушильного агента для хлористого калия используют дымовые газы, представляющие собой смесь продуктов сгорания топлива и воздуха.
Технологический процесс сушки флотоконцентрата KCl состоит из следующих стадий:
1) Сжигание топлива для получения дымовых газов.
2) Сушка флотоконцентрата дымовыми газами в аппарате.
3) Технологическая и санитарная очистка отработанных дымовых газов.
Мелкозернистый концентрат с влажностью не более 7,0 % из главного корпуса обогатительной фабрики поступает на конвейер, далее в накопительный бункер, из которого ленточным конвейером и забрасывателем продукт загружается в аппарат “КС”-1.
Сушильные аппараты типа “КС” имеют корпус цилиндрической формы с выносной топкой, беспровальную решетку, сепарационную камеру. Беспровальная решетка со щелевидными отверстиями установлена на опорном кольце и двух балках, которые охлаждаются воздухом от вентилятора. Топка служит для сжигания природного газа и представляет собой цилиндрическую камеру, футерованную огнеупорным кирпичом и оборудованную газоструйной горелкой или паромеханической форсункой.
Газ на газоструйные горелки аппаратов «КС» подается из газораспредилительной подстанции (ГРП) по кольцевой системе. Давление газа перед горелкой должно составлять 3,6-6,0 кгс/см2 или(0,36-0,60МПа).
Продукт выгрузки печи с температурой 100-120°С поступает на аэроохладители. Аэроохладитель представляет собой сварной аппарат прямоугольного сечения, размеры которого на уровне решетки составляют 3,5х 0,6 м(2,1 м 2). Воздух на охлаждение подается вентилятором соответствующей печи. Работает аппарат по принципу установки «кипящего слоя», где происходит не только охлаждение материала на 30-50°С в процессе конвективного тепло - массообмена, а также частичное обеспыливание по классу 0,1мм.
Расход воздуха на аэроохладители всех установок осуществляется дистанционно, в зависимости от нагрузки на печь
Продукт выгрузки аэроохладителя, объединяясь с циклонным продуктом системы пылегазоочистки (ПГО), направляется в смесители на обработку реагентами пылеподавителем и антислеживателем. Запыленный воздух после аэроохладителя, совместно с отходящими дымовыми газами соответствующей печи, подается в систему ПГО.
Система ПГО сушильных установок «КС»-1 и представлена двумя стадиями. Первая стадия ПГО происходит в циклонах ЛИОТ поз.13(1,2) диаметром 3400мм со вставками верхней части, выполненными из листов стали, и расположенных ступенчато, по окружности, с зазорами для прохода газов. Вторая стадия пылегазоочистки осуществляется в рукавных фильтрах ФРИ – 800.
Очищенные дымовые газы дымососами ВМ 160/850 выбрасываются в атмосферу с массовой концентрацией, мг/м3, не более:
-пыли KCl -не более 270;
-пыли NaCl -не более 270;
-диоксида серы -не более 540;
-оксида углерода -не более 450;
-оксида азота -не более100;
-хлористого водорода –не более 22;
Наряду с описанной выше схемой выгрузки печи «КС», минуя аэроохладитель, может подаваться совместно с циклонным продуктом на ленточный конвейер и далее, элеваторами, в отделение грануляции [8,9].
ОХРАНА ОКРУЖАЮЩЕЙ СРЕДЫ
ОАО «Уралкалий» понимает свою ответственность перед обществом за сохранение благоприятной экологической обстановки и проводит системную работу по охране окружающей среды.
С 2002 года в Компании внедрена и действует интегрированная система менеджмента качества и охраны окружающей среды. Система менеджмента качества и охраны окружающей среды отличается высокой степенью интеграции, имеет единую политику в области качества и охраны окружающей среды, единое руководство, положения о подразделениях. Должностные и рабочие инструкции содержат требования по менеджменту качества и экологическому менеджменту, процедурные документы максимально интегрированы для единых процессов
Ежегодно «Уралкалий» утверждает и реализует программу природоохранных мероприятий. Компания последовательно снижает сбросы сточных вод, уменьшает удельный расход воды на тонну продукции, сокращает вредные выбросы в атмосферу за счет перевода производственных объектов на газ, увеличивает объемы использования отходов производства
К решению экологических задач «Уралкалий» привлекает ведущие российские научно-исследовательские центры
В результате регулярных мер постепенное снижение уровня негативного воздействия предприятия на окружающую среду происходит по всем направлениям: в отношении атмосферы, водной среды и земной поверхности
Для компании принципиально важно, чтобы не только руководство и профильные подразделения, но и каждый ее сотрудник на своем рабочем месте проявлял заботу о состоянии окружающей среды и бережно относился к ней. В компании на высоком уровне организовано экологическое обучение сотрудников. Соблюдение норм и правил, а также уровень экологических знаний сотрудников оценивается в ходе регулярных инспекций и аудитов.
Отходами сушильного отделения в производстве хлористого калия флотационным способом являются:
-глинисто-солевые шламы, с минерализованными водами;
-выбросы в атмосферу;
Глинисто-солевые шламы из зумпфа насосами перекачиваются на шламохранилище. Характеристика глинисто-солевых шламов приведена в таблице.
Таблица 15 – Характеристика жидких отходов
Наименование отхода | Место складирования | Количество отходов | Периодич-ность образова-ния | Характеристика отходов | |||||
Т/г | М3/г | Химический состав, массовая доля воды, % | Физические показатели, плотность, кг/м3 | Класс опаснос-ти | |||||
Стоки сушильно- грануляцион-ного отделения | Шламохрани-лище | 1.Проектная мощность 1994,9тыс.т.95% КСl | Постоянно при работе флотофабрики | NaCl - 6.55 KCl - 15.25 MgCl2 - 0.40 CaSO4 - 0.15 H2O - 77.32 | Неток-сичны | ||||
2.Плановая мощность 1203,8 тыс.т 95% КСl | |||||||||
Таблица 16 – Выбросы в атмосферу
Аппарат, диаметр, высота выброса | Количество источников выбросов | Периодичность | Характеристика выбросов | Наименование пылегазоочис-тительной установки | Степень очистки КПД, %, факт. | Суммарный объем отходящих газов, М3/сек | ||||
Темпера-тура, 0С | Наименование загрязняющих веществ | Концентрация загрязняющих веществ, мг/м3 | Допустимое количество нормируемых вредных веществ, выбросов в атмосферу | |||||||
г/с | т/год | |||||||||
Печь «КС»-1, труба, высота – 40 м, диаметр устья трубы – 1,2 м | Постоянно при работе печи | Пыль KCl Пыль NaCl HCL Амины NO2 CO | 1.08 | 6,23 6,23 0,051 0,025 2,4 10,4 | 19,2 11,4 4,0 0,21 16,5 46,6 | 1ст.- ЛИОТ со вставкой, 2 ст.-труба Вентури, капле уловитель | 99,96 99,96 85,15 99,56 ------------------ | 23,06 | ||
Печь «КС»-2, труба, высота- 40 м, диаметр устья трубы - 1,4 м | Постоянно при работе печи | Пыль KCl Пыль NaCl SO2 HCL Амины NO2 CO зола маз. | 1,08 | 6,23 6,23 12,5 0,51 0,025 2,4 10,4 3,7х 10 -5 | 20,8 12,4 108,5 4,3 0,23 19,7 50,6 0,0003 | 1 ст. ЛИОТ со вставкой 2ст.тр. Вентури, капле уловитель | 98,80 98,80 29,55 86,28 98,82 ----------------------98,80 | 23,06 | ||
Печь «КС»-3, труба, высота- 45 м, диаметр устья трубы - 1,2 м | Постоянно при работе печи | Пыль KCl Пыль NaCl SO2 HCL Амины NO2 CO зола маз. | 1,08 | 6,23 6,23 12,5 0,51 0,025 2,4 10,4 3,7х 10 -5 | 18,0 10,7 3,7 0,2 15,5 13,8 0,0003 | 1 ст. инерционный продуктоотделитель 2ст. ЛИОТ 3 ст. тр. Вентур капле уловит. | 99,98 99,98 28,81 85,09 99,31 ----------------------99,98 | 23,06 | ||
Печь «КС»-4, труба, высота- 45 м, диаметр устья трубы-1,2 м | Постоянно при работе печи | Пыль KCl Пыль NaCl HCL Амины NO2 CO | 1,08 | 6,23 6,23 0,51 0,025 2,4 10,4 | 14,7 8,7 3,2 0,16 12,6 36,5 | 1 ст. продуктоотделитель 2ст. ЛИОТ 3 ст. тр. Вентури, каплеуловит. | 99,98 99,98 87,75 98,76 ---------------------- | 23,06 |
Выброс (т/г) по каждому источнику выделения вредных веществ может быть изменен в зависимости от времени работы, но общий выброс не должен превышать установленную величину ПДВ.
Из пяти сушильных агрегатов одновременно в работе находятся два.
Таблица 17 - Перечень и количество загрязняющих веществ, разрешённых к выбросу в атмосферу
№ | Загрязняющее вещество | Суммарный нормативный выброс, т/год. |
1. | Пыль хлористого калия | 144,36 |
2. | Пыль хлористого натрия | 110,56 |
3. | Азота диоксид | 92,60 |
|
|
Биохимия спиртового брожения: Основу технологии получения пива составляет спиртовое брожение, - при котором сахар превращается...
Автоматическое растормаживание колес: Тормозные устройства колес предназначены для уменьшения длины пробега и улучшения маневрирования ВС при...
Опора деревянной одностоечной и способы укрепление угловых опор: Опоры ВЛ - конструкции, предназначенные для поддерживания проводов на необходимой высоте над землей, водой...
Своеобразие русской архитектуры: Основной материал – дерево – быстрота постройки, но недолговечность и необходимость деления...
© cyberpedia.su 2017-2024 - Не является автором материалов. Исключительное право сохранено за автором текста.
Если вы не хотите, чтобы данный материал был у нас на сайте, перейдите по ссылке: Нарушение авторских прав. Мы поможем в написании вашей работы!