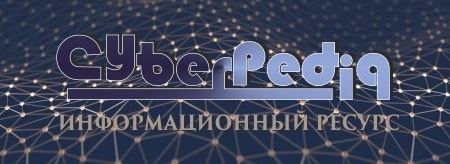
Организация стока поверхностных вод: Наибольшее количество влаги на земном шаре испаряется с поверхности морей и океанов (88‰)...
Кормораздатчик мобильный электрифицированный: схема и процесс работы устройства...
Топ:
Марксистская теория происхождения государства: По мнению Маркса и Энгельса, в основе развития общества, происходящих в нем изменений лежит...
Определение места расположения распределительного центра: Фирма реализует продукцию на рынках сбыта и имеет постоянных поставщиков в разных регионах. Увеличение объема продаж...
Генеалогическое древо Султанов Османской империи: Османские правители, вначале, будучи еще бейлербеями Анатолии, женились на дочерях византийских императоров...
Интересное:
Инженерная защита территорий, зданий и сооружений от опасных геологических процессов: Изучение оползневых явлений, оценка устойчивости склонов и проектирование противооползневых сооружений — актуальнейшие задачи, стоящие перед отечественными...
Мероприятия для защиты от морозного пучения грунтов: Инженерная защита от морозного (криогенного) пучения грунтов необходима для легких малоэтажных зданий и других сооружений...
Отражение на счетах бухгалтерского учета процесса приобретения: Процесс заготовления представляет систему экономических событий, включающих приобретение организацией у поставщиков сырья...
Дисциплины:
![]() |
![]() |
5.00
из
|
Заказать работу |
|
|
Организационное проектирование, как функция организации, состоит в разработке таких организационных элементов и отношений в создаваемой (моделируемой) системе, при реализации которых возникшее организационное целое обладало бы свойствами высокой надежности, устойчивости и экономичности.
Как известно, согласно роли в общем процессе изготовления готовой продукции в промышленности выделяют следующие производственные процессы: основные, вспомогательные, обслуживающие и управленческие.
Вспомогательные процессы – это производственные процессы, в результате которых получается продукция, как правило, используемая на самом предприятии, для обеспечения нормального функционирования основных процессов. Примерами таких процессов являются изготовление инструментов, приспособлений, штампов, средств механизации и автоматизации собственного производства, запасных частей для ремонта оборудования, производство на предприятии всех видов энергии (электрической энергии, сжатого воздуха, азота и т.д.).
Обслуживающие производства – это производства, обеспечивающие основные и вспомогательные процессы услугами, необходимыми для их нормального функционирования. Например, транспортировка материальных ценностей, складские операции всех видов, технический контроль качества продукции и др.
Вспомогательные и обслуживающие производственные процессы имеют специфические особенности и связанные с этим разные тенденции развития и совершенствования. Так, многие вспомогательные производственные процессы могут быть переданы специализированным предприятиям, что в большинстве случаев обеспечивает экономически более эффективное производство инструмента, технологической оснастки, запасных частей. С повышением уровня автоматизации вспомогательных процессов обслуживающие процессы постепенно становятся неотъемлемой частью основного производства, играют организующую роль в автоматизированных и особенно в гибких автоматизированных производствах.
|
Вспомогательные процессы способствуют бесперебойному протеканию основных производственных процессов. Полученная посредством их продукция используется на предприятии для обслуживания основного производства.
Обслуживающие процессы призваны создавать условия для успешного выполнения основных и вспомогательных процессов. К ним относятся меж- и внутрицеховые транспортные операции, обслуживание рабочих мест, складские операции, контроль качества продукции.
Рациональная организация производственного процесса и всех его частей строится на основе ряда принципов, главными из которых являются:
– дифференциация (разделение производственного процесса на отдельные технологические процессы, операции);
– концентрация и интеграция (решение нескольких производственных задач в едином комплексе);
– специализация (закрепление за одним производственным подразделением выполнения технологически однородных работ);
– параллельность (одновременное выполнение отдельных частей производственного процесса);
– пропорциональность (соответствия производительности в единицу времени всех производственных подразделений);
– непрерывность (сокращение или сведение к минимуму перерывов в процессе производства);
– ритмичность (обеспечение выпуска в равные промежутки одного и того же количества продукции на всех стадиях и операциях);
– прямоточность (обеспечение кратчайшего пути прохождения предметов труда по всем стадиям производственного процесса);
– автоматичность (внедрение автоматизации производственных процессов);
– гибкость (мобильный переход на выпуск новой продукции при освоении производства);
|
– электронизация (использование быстродействующих машин различных классов и совершенствование средств общения человека с ними).
Планирование ремонтов. Календарные сроки ремонта определяют на основании данных журнала учета работы оборудования и материалов об агрегате исходя из фактически отработанных часов за период от последнего ремонта и результатов ежегодного технического осмотра.
В годовой план ремонтов включают осмотры и плановые ремонты. Месяц, в котором должен проводиться очередной ремонт (осмотр) по плану, определяется путем прибавления к месяцу предыдущего ремонта длительности межремонтного (межосмотрового) периода. Вид очередного ремонта устанавливается по структуре ремонтного цикла в зависимости от видов предыдущих ремонтов, Трудоемкость слесарных и станочных работ определяют путем умножения трудоемкости одной ремонтной единицы по соответствующему виду ремонта на категорию сложности.
Система ППР предусматривает установление норм простоя оборудования в ремонте
Ускорение проведения ремонта достигается:
а) сокращением трудоемкости слесарных работ за счет большей их механизации, применения прогрессивной технологии ремонта, предварительной подготовки сменных деталей и сборочных единиц и расширения их номенклатуры, упрощения конструкции оборудования (снижения ремонтной сложности);
б) увеличением числа рабочих в бригаде (расширением фронта работ) или сменности их работы;
в) большей специализацией слесарей-ремонтников, лучшей организацией труда и рабочего места ремонтных бригад и бесперебойным обеспечением их всем необходимым (чертежами, материалами, сменными деталями и др.).
Трудоемкость всех ремонтов в каждом месяце по плану должна быть примерно одинаковой, чтобы не было недостачи или излишка ремонтных рабочих в отдельные месяцы.
На основании годового плана и его фактического выполнения за предыдущие месяцы, а также числа фактически отработанных агрегатом часов с момента последнего ремонта, фактического состояния оборудования, выявленного при проведении осмотра, и обеспеченности ремонта запасными деталями и материалами составляют по каждому цеху месячный план ремонта.
Межосмотровой период не может быть удлинен. Составленный годовой план ремонта оборудования на основании нормативов системы ППР может оказаться невыполнимым из-за перегрузки ремонтных рабочих или рабочих и оборудования в ремонтно-механическом цехе предприятия для выполнения капитальных ремонтов. В этом случае необходимо определить, какое оборудование следует ремонтировать в первом месяце года и для какого оборудования сроки ремонта должны быть перенесены на следующие месяцы.
|
В первую очередь, в план капитального ремонта первого месяца года будет включаться оборудование, имеющее наибольшее превышение фактически отработанных станко-часов на начало года по сравнению с нормативными, умноженное на число ремонтных единиц.
Если некоторые единицы оборудования не попадут в результате решения задачи в план первого месяца, то они должны включаться в план второго месяца и так до 12-го месяца включительно. Оборудование, не попавшее в план 12-го месяца, переносится в план следующего года.
Если длительность капитального ремонта превышает один месяц, то данную задачу целесообразнее решать сразу для двух- и трехмесячного периода, а не для каждого месяца отдельно.
Планирование ремонтов в энергетике
Для подготовки и проведения остановочного ремонта необходима следующая документация: ведомость дефектов; сметы; план организации ремонтов (по необходимости); график сетевой (линейный); чертежи, схемы на реконструируемые объекты; технические условия на капитальный ремонт основных объектов.
Составление ремонтного плана энергообъединения включает:
- разработку календарного графика вывода оборудования в ремонт:
- определение планового объема работ по отдельным агрегатам, цехам и электростанции в целом;
- выявление потребности в запасных частях, материалах для ремонта и их стоимости;
- определение необходимого количества и состава рабочих по специальностям и квалификациям;
- расчеты по определению сметной стоимости.
Разработка календарного графика вывода оборудования в ремонт предполагает тщательный анализ балансов мощности в энергообъединении, выявление свободных ресурсов мощности, которые могут быть использованы для обеспечения необходимого уровня эксплуатационного резерва мощности и проведения всех видов ремонта оборудования. От графика вывода в ремонт зависит состав работающего оборудования, его изменение во времени и, следовательно, расход топлива на выполнение заданных графиков электрической и тепловой нагрузки.
|
Продолжительность капитального ремонта основного оборудования ТЭС весьма значительна, и проводятся они, как правило, весной и летом – в период сезонного спада электрической и тепловой нагрузки. Кратковременные текущие ремонты оборудования проводятся в дни с пониженной нагрузкой (выходные и праздники). По мере роста мощности электрической станции и укрупнения единичной мощности агрегатов длительность простоя в текущем ремонте возрастает. В связи с этим для обеспечения круглогодового проведения текущих ремонтов в энергообъединениях необходим определенный ремонтный резерв мощности.
При формировании календарного графика ремонта основного оборудования в энергообъединении приходиться учитывать ограничения не только по величине суммарной мощности, но и по располагаемым ресурсам рабочей силы. По этим соображениям стараются выводить в ремонт приблизительно равные мощности котлов и турбинных агрегатов; соблюдать одинаковую периодичность капитальных ремонтов для отдельных агрегатов; осуществлять ремонт ТЭЦ с преобладающей отопительной нагрузкой в летний период времени, а ремонт торфяных электростанций – весной. В энергообъединениях с мощными ГЭС стремятся максимально использовать многоводный период для ремонта оборудования ТЭС и АЭС. Крупные наиболее экономичные КЭС выводят в ремонт в период наибольшего снижения электрической нагрузки энергосистемы с целью своевременной подготовки к прохождению осенне-зимнего максимума нагрузки и экономии топлива.
На основе установленных сроков вывода в ремонт основного оборудования на электростанциях планирует сроки и объемы ремонта всего оборудования. Плановый ремонт предусматривает вывод в ремонт оборудования с учетом требований действующих в отрасли норм и нормативов.
Вид ремонта установки (капитальный, текущий, средний) определяется, как правило, видом ремонта основного оборудования, входящего в установку.
Вид ремонта вспомогательного оборудования может отличаться от вида ремонта основного оборудования установки, но выполняется в сроки, определяемые ремонтом основного оборудования.
Продолжительность ремонтного цикла для каждого вида энергетического оборудования и сетей определяется условиями эксплуатации, требованиями к степени безотказности, конструктивными особенностями, ремонтопригодностью, указаниями и инструкциями завода-изготовителя, правилами технической эксплуатации, а также другими факторами.
|
Величина ремонтного цикла исчисляется не в машино-часах, учет которого сложно организовать, а в календарном времени.
Работы производятся в соответствии с заранее составленным графиком ремонтов, предусматривающим количество и чередование периодических ремонтов на протяжении всего ремонтного цикла.
Слишком малые межремонтные периоды неоправданно увеличивают затраты на ремонт, а слишком большие могут сорвать систему ППР и в ряде случаев заменить её на аварийные ремонты, что может нанести большой ущерб потребителям и энергосистемам. В электрических сетях считается целесообразным трёхлетняя периодичность комплексного ППР подстанций и ЛЭП. Текущие ремонты более часты.
Периодичность ремонтов всех видов энергетического оборудования и длительность ремонтного простоя закрепляются в правилах технической эксплуатации и специальных инструкциях. Все остальные нормативные показатели определяются либо в результате разработки технологического процесса ремонта, либо на основе категорий ремонтосложности оборудования.
Плановые сроки вывода в капитальный и текущий ремонты предусматриваются графиками, разработанными в энергосистеме. График ремонта основного оборудования связан с балансом мощностей системы и должен быть составлен таким образом, чтобы обеспечивалось покрытие годового графика месячных максимумов электрической нагрузки, и сохранялся размер эксплуатационного резерва мощности. От графика вывода в ремонт зависит состав действующего оборудования, изменение его во времени, и, следовательно, расход топлива по энергосистеме.
Сметы на типовую номенклатуру работ составляются в уровне базовых цен (1992 г.). На один тип оборудования составляется одна смета.
К ремонтным работам по сверхтиповой номенклатуре относятся
- работы, выполняемые на основании приказов Минэнерго РФ, РАО «ЕЭС России», приказов по АО-энерго;
- противоаварийных и эксплуатационных циркуляров;
- предписаний органов Государственного надзора;
- предписаний Департамента Генеральной инспекции по эксплуатации электростанций и сетей РАО «ЕЭС России»;
- писем заводов-изготовителей;
- работы по замене износившихся механизмов и вспомогательного оборудования, являющихся неотъемлемыми элементами основного оборудования как инвентарного объекта для начисления амортизации (включая стоимость этих механизмов и оборудования), капитальный ремонт которых нецелесообразен;
- работы по поддержанию в работоспособном состоянии и обеспечению продления эксплуатации основных средств электростанций и сетей, имеющих значительный физический износ и которые в настоящее время полностью с амортизированы;
- работы, выполняемые на основании заключений лаборатории металлов или актов о техническом состоянии оборудования.
Достоинства системы ППР:
1) простота и наглядность определения периодичности и продолжительности различных видов технического обслуживания и ремонта (ТОР);
2) возможность обеспечения высокого уровня надежности при минимизации производственных резервов;
З) возможность долгосрочного планирования ремонтной площадки, материальных, трудовых, финансовых ресурсов.
Недостатки системы ППР:
1) затратная система финансирования;
2) отсутствие гибкости планирования, возможности учета дополнительных условий.
З) отсутствие накопления информации и анализа результатов системы ТОР на уровне энергопредприятий и энергообъединений.
В качестве пути разрешения противоречий системы ППР, предлагается внедрение в практику работы электростанций системы планирования ТОиР, в основу которой положена методика определения назначенного межремонтного ресурса энергооборудования.
Суть стратегии заключается в переходе от планирования на основе жесткой структуры межремонтного цикла ППР к планированию, учитывающему наработку, достигнутую в межремонтный период каждой единицей соответствующего оборудования. Применение такой системы должно обеспечить преемственность с существующей системой, и, в общем случае, позволяет увеличить календарную продолжительность межремонтного цикла, сократить среднегодовые затраты на ТОиР и повысить общую эффективность использования ПФ при сохранении на заданном уровне надежности энергоснабжения.
Одновременно, на последующих стадиях развития этой системы, должны быть созданы экономические условия и предложены технологические решения для внедрения в энергетике средств технической диагностики и идентификации состояния оборудования, позволяющих учесть реальное состояние оборудования и уточнить межремонтный ресурс.
Материально-техническое снабжение (далее МТС) – это процесс, деятельность по обеспечению предприятия материальными ресурсами необходимого качества и комплектности в определённые сроки.
Содержание функций отдела МТС включает три направления:
планирование, организацию, контроль и координацию работы.
Планирование материально-технического обеспечения предприятия является основанием для принятия решения о закупке материальных ресурсов. При организации закупки материальных ресурсов на предприятиях необходимо определять потребность в материальных ресурсах по специфицированной номенклатуре на плановый период.
Процесс планирования предусматривает следующие этапы: исследование рынка сырья и материалов, определение потребности предприятия по всей номенклатуре потребляемых материалов, составление плана закупок материалов и стоимостный анализ заготовительной фирмы.
Изучение рынка сырья и материалов предполагает систематические сбор, обработку, анализ и оценку информации о предложении конкретных видов материалов, ассортименте и ценах на сырье, материалы, топливо и полуфабрикаты. При исследовании рынка сырья и материалов предприятие должно дать количественную оценку предложений необходимых ему материальных ресурсов в ассортименте и по предлагаемым ценам. Важное место в изучении этого рынка занимает анализ издержек по доставке материалов. Вырабатывая стратегию снабжения, предприятие сравнивает собственные расходы на производство необходимых деталей с ценой аналогичных деталей у поставщика.
Определение потребности в материальных ресурсах – центральное звено в планировании материально-технического снабжения предприятия. Потребность в материальных ресурсах складывается из потребности в ресурсах на основное производство, потребности на создание и поддержание переходящих запасов на конец планового периода и потребности на другие виды хозяйственной деятельности, включая и непроизводственную.
При расчете потребности в материальных ресурсах необходимо учитывать наличие средств для их покрытия. Источники покрытия могут быть собственными или заемными. Потребность в материальных ресурсах планируется по всей номенклатуре материалов в стоимостном и натуральном выражении. Объемы и сроки поставок материалов на предприятие обусловливаются режимом их производственного потребления, созданием и поддержанием необходимого уровня производственных запасов.
Объем требуемых материальных ресурсов складывается из потребности в материалах, необходимых для внедрения новой техники, для изготовления оснастки и инструмента, на эксплуатационные и технологические нужды, на создание необходимого задела незавершенного производства и на образование переходящих запасов. Потребность в материальных ресурсах определяется на основе баланса МТО предприятия с учетом остатков и внутренних источников обеспечения.
Определение потребности в материальных ресурсах можно осуществить тремя методами: детерминированным – на основе планов производства и нормативов расхода; стохастическим – на основе вероятностного прогноза с учетом потребностей за прошлые периоды; оценочным – на основе опытно-статистической оценки. Выбор метода зависит от особенностей материальных ресурсов, условий их потребления и наличия соответствующих данных для проведения необходимых расчетов
Методы прогнозирования потребности в материальных ресурсах применяются при внедрении новой техники. Эта потребность складывается из потребности в материалах опытных производств, исследовательских лабораторий и технических отделов.
Статистические методы определения потребности в материальных ресурсах основываются на использовании данных о фактическом расходе материальных ресурсов за прошлые периоды с учетом изменения структуры и объемов производства, а также норм расходов ресурсов, обусловленных использованием новой техники и совершенствованием организации производства.
Потребность в оборудовании (по видам) определяют исходя из производительности оборудования и плана производства продукции по видам.
Потребность в энергии (паре) для отопления зданий зависит от объема и тепловой характеристики здания, температуры внутри помещения и снаружи, длительности отопительного периода и разницы между теплосодержанием пара и конденсата.
Потребность в энергии на технологические цели определяется исходя из норм ее расхода на единицу продукции и планируемого объема ее производства в натуральном или денежном выражении.
Определение потребности в электроэнергии на освещение зависит от площади помещения, нормы и количества часов освещения. На этой основе устанавливается необходимое количество светильников соответствующей мощности.
Расход электроэнергии на вентиляцию определяется исходя из мощности вентиляционных установок и количества часов их работы в плановом периоде.
Остатки продукции на начало года (ожидаемые остатки) являются одним из важнейших источников ресурсов, которые могут быть использованы для достижения сбалансированности. Остатки на конец года (переходящие запасы) обеспечивают нормальную работу предприятий и организации в послеплановом периоде. Поскольку на их создание отвлекается часть ресурсов, остатки должны быть минимальными.
Баланс материально-технического обеспечения предприятия включает потребность в материалах на:
• производство продукции (Рп);
• внедрение новой техники (Рн.т.);
• ремонтно-эксплуатационные нужды (Ррэ);
• образование задела незавершенного производства (Рн.п.);
• образование переходящих запасов (Рз).
Источниками покрытия этой потребности могут быть:
• ожидаемые остатки на начало планового периода (Оож);
• материалы в незавершенном производстве на начало планового периода (Он.п.);
• мобилизация внутренних ресурсов (Мв.н.);
• приобретение и завоз материалов со стороны (Зс).
Таким образом, материальный баланс можно представить в следующем виде:
Рп + Рн.т. + Ррэ + Рн.п + Рз = Оож + Он.п + Мвн + Зс , (4.8)
Приведенный баланс материально-технического обеспечения служит инструментом управления движением материальных ресурсов на промышленных предприятиях.
Планирование запасов на предприятии предполагает расчет двух показателей: ожидаемых остатков на начало и переходящих запасов на конец планируемого периода. Это касается и производственных и сбытовых запасов.
Норму запаса конкретного материала (Знорм) рекомендуется определять по формуле:
Знорм = Зтек.ср + Зстр + Зподг, (4.9)
где Зтек.ср – средний текущий запас; Зстр – страховой запас; Зподг – подготовительный запас.
Эффективное использование запасов достигается правильной организацией управления ими. Управление включает разработку научно-обоснованных норм запасов, их планирование, учет, анализ, контроль за фактическим состоянием и оперативное регулирование. Главным в системе управления запасами средств производства считается нормирование. Только на основе научно обоснованных норм можно качественно анализировать, планировать, контролировать и регулировать запасы с целью достижения их общественно необходимой величины. Нормирование направлено на всемерное ускорение оборачиваемости средств, вкладываемых в запасы.
Под нормой запаса следует понимать минимальное количество материальных ресурсов, обеспечивающее непрерывность производства и обращения.
Нормы запаса устанавливаются в различных единицах: натуральных, денежных ив днях. Натуральные и денежные единицы характеризуют абсолютную величину запаса, а запас в днях – относительную.
Нормирование запасов осуществляется различными методами: расчетно-аналитическими, статистическими, математико-статистическими, методами теории вероятностей. Использование того или иного метода зависит от факторов, которые определяют величину запасов.
Определение потребности в средствах производства является наиболее ответственным этапом планирования снабжения. Руководит этой работой отдел МТС. Непосредственные расчеты могут выполняться вычислительным центром предприятия. Потребность в отдельных видах материалов рассчитывается другими подразделениями предприятия.
Определение запасов в планах снабжения оборудования обусловлено характером их использования.
Если оборудование предназначено для замены физически износившегося, а также для нового строительства, то задача органов материально-технического снабжения заключается в том, чтобы, оно было в наличии. Для выполнения такого условия и предотвращения возможных издержек в поставках оборудования в планах снабжения необходимо предусмотреть его изготовление, опережающее по времени установку оборудования и поставку непосредственно на строительную площадку. Время этого опережения и будет нормой запаса в относительном выражении. Абсолютным выражением запаса является стоимость неустановленного оборудования, находящегося на строительной площадке.
Величина запаса оборудования определяется оптимальным временем опережения его поступления по отношению к монтажу. Она складывается из следующих составляющих:
• текущей части запаса, которая определяется несовпадением сроков изготовления и монтажа оборудования; это время зависит от возможности изготовления продукции поставщикам, а также от степени отклонения фактических сроков монтажа оборудования от запланированных;
• страховой части запаса; это время должно гарантировать, своевременный монтаж оборудования при нарушении установленных сроков его отгрузки, увеличении времени транспортировки, опережении графиков монтажа и в ряде других непредвиденных случаев;
• подготовительной части запаса, которая включает время для разгрузки оборудования и доставки его к месту монтажа, расконсервации и снятия смазки, для комплектования, если отдельные части оборудования поступают от различных поставщиков или требуется доукомплектация инструментом, запасными частями и другими изделиями.
Обеспечение качества продукции на предприятиях определяется целым рядом внутренних факторов: технических, организационных, экономических, социально-психологических. Важное место среди этих факторов занимают организационные факторы, связанные с совершенствованием организации производства и труда и др.
Складское хозяйство является необходимым элементом производства, оно присуще всем отраслям и имеет сложную структуру.
Успешная производственная деятельность промышленных предприятий зависит от повседневного обеспечения их необходимым сырьем, материалами, топливом, инструментами, оборудованием и т. п. Производственно-технической базой снабжения и сбыта является складское хозяйство.
Главной задачей материальных сладов является концентрация и временное хранение материальных ценностей с целью полного и ритмичного обеспечения предприятий и организацией необходимыми материальными, ресурсами в соответствии с планами материально-технического снабжения.
Обычно склады оснащаются стеллажами, которые размещаются таким образом, чтобы эффективно использовать всю их кубатуру. Материалы хранятся в стандартной таре, которая удобно размещается на стеллажах и легко перевозится с помощью транспортеров и штабелеукладчиков. Размеры складов варьируются в широком диапазоне: от небольших помещений до складов-гигантов. Различают склады и по высоте укладки грузов.
При размещении складов на территории предприятия необходимо руководствоваться следующим.
Склады готовой продукции и помещения экспедиции следует размещать вблизи корпусов окончательной сборки и испытательных станций, а прицеховые склады – в зданиях цехов-потребителей в непосредственной близости к этим цехам.
Складские помещения общезаводского назначения рекомендуется размещать на окраине территории предприятия или в районе железнодорожных путей, за исключением центральных материальных складов, складов оборудования и складов моделей, которые могут быть расположены в зоне основной застройки, вблизи обслуживаемых ими объектов.
Участки для хранения грузов, горючих и легковоспламеняющихся жидкостей должны быть выделены в самостоятельную зону.
Автомобильные дороги должны обеспечивать свободный доступ ко всем складским помещениям.
Для четкой организации работы складов необходимо своевременно и правильно планировать завоз материалов. Планы завоза составляются заготовительными группами (отделами) по видам материалов и отдельным складам. Наличие таких планов дает возможность заблаговременно подготовиться к приемке: уточнить время разгрузки, выделить рабочих, механизмы и оборудование, подобрать необходимую документацию.
Главнейшими из операций являются количественная и качественная приемка материальных ценностей. Они связаны между собой. Проверка количества поступившего материала, должна предшествовать проверке качества.
При определении условий хранения материалов следует учитывать длительность хранения его на окладе. В зависимости от продолжительности хранения материалов на складе различают долгосрочное и краткосрочное хранение.
Многие отпускаемые со складов материалы должны быть предварительно подготовлены к производственному потреблению, например, металлы должны быть раскроены или разрезаны, сыпучие материалы – расфасованы, изделия смежных производств – скомплектованы. Для этой цели на складах целесообразно создавать заготовительные отделения, оборудованные ленточными и циркулярными пилами, расфасовочными и другими механизмами.
Операции, связанные с отпуском материалов и изделий потребителям, являются завершающими в работе складов промышленных предприятий. Эти операции включают отборку материалов, комплектование, подготовку их к отпуску и отпуск потребителям.
Транспортное хозяйство предприятий − комплекс технических средств промышленного предприятия, предназначенных для перевозки материалов, полуфабрикатов, готовой продукции, отходов и других грузов на территории предприятия и на его подъездных путях.
Задачи транспортного хозяйства:
– наиболее быстрое перемещение предметов труда, топлива и готовой продукции в соответствии с требованиями производственного процесса;
– эффективное использование транспортных средств;
– механизация транспортных и погрузочно-разгрузочных операций;
– снижение себестоимости транспортных операций;
– обеспечение строгой согласованности технологических и транспортных операций;
– поддержание транспортных средств в работоспособном состоянии.
Суммарное количество грузов, перемещаемых на предприятии за определенный период, представляет собой грузооборот, а количество грузов, перемещаемых за определенный период времени между отдельными погрузочно-разгрузочными пунктами - грузопоток.
Факторы, влияющие на выбор вида транспорта:
1) производственная мощность предприятия и объем грузооборота;
2) характер грузов (жидкий, сыпучий, штучный);
3) длина и направление пути;
4) устойчивость грузопотока;
5) экономические факторы (капитальные затраты, затраты на перевозку).
Количество транспортных средств (Кт.с) зависит:
– от суточного объема грузооборота;
– затрат времени на один рейс;
– числа часов работы транспорта в сутки;
– грузоподъемности транспортного средства;
– коэффициента использования грузоподъемности;
– коэффициента задержек транспорта в пути;\
– системы маршрутных перевозок.
Система управления качеством — это особая организация в производственной системе. Основным в этой организации является документированность всех процессов, имеющих отношение к производству продукции, начиная с закупки материалов и заканчивая доставкой потребителю готовой продукции. Во многих случаях это приводит к кардинальным изменениям в технике, технологии и организации производства на предприятии. Качество – это система, и этой системой надо управлять.
Современные системы управления качеством на предприятии создаются в соответствии с требованиями стандартов ИСО серии 9000:2000, представляющих собой целый комплекс документов: методические материалы, руководства по использованию стандартов.
В системе менеджмента качества в стандартах ГОСТ ИСО серии 9000 — 2001 определенное место отводится контролю, под которым понимается процедура оценивания соответствия путем наблюдений и суждений, сопровождаемых соответствующими измерениями.
На энергетических предприятиях выделяют цехи и вспомогательного основного производства.
К вспомогательному производству, назначением и результатом которого являются работы по обслуживанию основного производства (транспорт сырья, ремонт и испытания оборудования, измерения, анализы и т.п.) относят:
К вспомогательным цехам на энергетических предприятиях относят цех тепловой автоматики и измерений, механический цех (мастерские), ремонтно-строительный цех. Цех тепловой автоматики измерений осуществляет автоматический контроль и регистрацию параметров работы основного оборудования.
В результате проведения реформирования энергетики произошло выделение энергоремонта в самостоятельный бизнес.
Таким образом, говорить о вспомогательных и обслуживающих производств в энергетике неправомерно.
|
|
История создания датчика движения: Первый прибор для обнаружения движения был изобретен немецким физиком Генрихом Герцем...
Таксономические единицы (категории) растений: Каждая система классификации состоит из определённых соподчиненных друг другу...
История развития пистолетов-пулеметов: Предпосылкой для возникновения пистолетов-пулеметов послужила давняя тенденция тяготения винтовок...
Двойное оплодотворение у цветковых растений: Оплодотворение - это процесс слияния мужской и женской половых клеток с образованием зиготы...
© cyberpedia.su 2017-2024 - Не является автором материалов. Исключительное право сохранено за автором текста.
Если вы не хотите, чтобы данный материал был у нас на сайте, перейдите по ссылке: Нарушение авторских прав. Мы поможем в написании вашей работы!