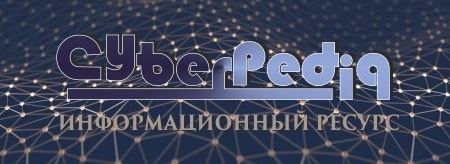
История развития пистолетов-пулеметов: Предпосылкой для возникновения пистолетов-пулеметов послужила давняя тенденция тяготения винтовок...
Эмиссия газов от очистных сооружений канализации: В последние годы внимание мирового сообщества сосредоточено на экологических проблемах...
Топ:
Техника безопасности при работе на пароконвектомате: К обслуживанию пароконвектомата допускаются лица, прошедшие технический минимум по эксплуатации оборудования...
Теоретическая значимость работы: Описание теоретической значимости (ценности) результатов исследования должно присутствовать во введении...
Марксистская теория происхождения государства: По мнению Маркса и Энгельса, в основе развития общества, происходящих в нем изменений лежит...
Интересное:
Мероприятия для защиты от морозного пучения грунтов: Инженерная защита от морозного (криогенного) пучения грунтов необходима для легких малоэтажных зданий и других сооружений...
Принципы управления денежными потоками: одним из методов контроля за состоянием денежной наличности является...
Финансовый рынок и его значение в управлении денежными потоками на современном этапе: любому предприятию для расширения производства и увеличения прибыли нужны...
Дисциплины:
![]() |
![]() |
5.00
из
|
Заказать работу |
|
|
Лабораторная работа №4
Определение угла захвата щековых дробилок
Расчет технологических параметров
Общие указания
Цель работы
Ознакомиться с видами и конструктивными особенностями щековых дробилок.
1.3 Правила техники безопасности:
1) дробилку без разрешения преподавателя не включать;
2) перед включением привода, убедиться в полной безопасности находящихся поблизости людей;
3) не производить измерений на работающей дробилке;
4) по окончании работы обесточить привод.
Основная часть
Литературный обзор
В промышленности щековые дробилки, в основном, применяют для крупного и среднего дробления. Принцип работы щековой дробилки заключается в следующем. В камеру дробления, имеющую форму клина и образованную двумя щеками, из которых одна в большинстве случаев является неподвижной, а другая подвижной, куда подается материал, подлежащий дроблению. Благодаря клинообразной форме камеры дробления куски материала располагаются по высоте камеры в зависимости от их крупности – более крупные вверху, мене крупные - внизу. Подвижная щека периодически приближается к неподвижной, причем при сближении щек куски материала раздрабливаются, при отходе подвижной щеки куски материала продвигаются в низ, под действием силы тяжести или выходят из камеры дробления, если их размеры стали меньше наиболее узкой части камеры, называемой выходной щелью, или занимают новое положение, соответствующее своему новому размеру. Затем цикл повторяется.
Щековая дробилка изобретена в 1858 г. американцем Блеком. В зависимости от кинематических особенностей механизма щековые дробилки можно разделить на две основные группы:
|
1. Дробилки, у которых движение от кривошипа к подвижной щеке передается определенной кинематической цепью. При этом траектории движения подвижной щеки представляют собой части дуги окружности. Эти машины называются щековыми дробилками с простым движением подвижной щеки.
2. Дробилки, у которых кривошип и подвижная щека образуют единую кинематическую пару. В этом случае траектории движения точек подвижной щеки представляют собой замкнутые кривые, чаще всего эллипсы. Дробилки с такой кинематикой называются щековыми дробилками со сложным движением подвижной щеки.
Лабораторная работа №5
Определение производительности щековых дробилок
Общие указания
Цель работы
Получить полное представление об устройстве и работе щековых дробилок. Приобрести навыки в расчете технологических параметров щековых дробилок.
Основная часть
Литературный обзор
В дробилке с простым движением щеки наблюдается обратное явление, т.е. наибольший ход сжатия (размах качания) имеет низ подвижной щеки, в верхней же части этот ход значительно меньше.
В дробилках со сложным движением подвижная щека шарнирно подвешена на эксцентричной части приводного вала. Низ подвижной щеки шарнирно опирается на распорную плиту. Другим концом распорная плита опирается на регулировочное устройство.
Типоразмер дробилки характеризует величина В – ширина приемного отверстия (расстояние между дробящими плитами в верхней части камеры дробления в момент максимального отхода подвижной щеки). Этот размер определяет максимально возможную крупность кусков, загружаемых в дробилку Dmax, принимаемых равными 0,85, от ширины приемного отверстия, т.е. Dmax = 0,85В.
Другим важным параметром служит длина приемного отверстия, т.е. длина камеры дробления L, определяющая, сколько кусков диаметром Dmax может быть загружено одновременно. Произведение двух величин В х L называется размером приемного отверстия щековой дробилки и является ее главным параметром.
|
В зависимости от величины главного параметра (В х L в мм) щековые дробилки, выпускаемые отечественной промышленностью, составляют следующий размерный ряд: 160х250, 250х400, 250х900, 400х600, 400х900, 600х900, 900х1200, 1200х1500, 1500х2100 мм, т.е. всего девять типоразмеров, из которых шесть первых представляют собой дробилки со сложным движением подвижной щеки, четыре последних – с простым. Перечисленный ряд определился в результате многолетнего опыта по созданию и эксплуатации щековых дробилок. Размеры приемных отверстий машин ряда регламентированы Государственными стандартами и соответствуют международному ряду по рекомендациям СЭВа.
Важным параметром щековой дробилки является величина выходной щели b. Она определяется как наименьшее расстояние между дробящими плитами в камере дробления в момент максимального отхода подвижной щеки. Величина выходной щели – параметр переменный, ее можно регулировать при помощи специального устройства, что позволяет изменять крупность готового продукта, или наоборот, поддерживать постоянной в течение длительного времени независимо от степени износа дробящих плит.
Лабораторная работа №6
Общие указания
Цель работы
Ознакомиться с основными рабочими органами и конструктивными особенностями валковых дробилок. Получить полное представление об устройстве и работе валковых дробилок. Приобрести навыки в расчете угла захвата валковых дробилок.
Основная часть
Литературный обзор
Основным рабочим органом валковой дробилки является цилиндрический валок, вращающийся на горизонтальной оси. Подлежащий дроблению материал подается сверху, затягивается между валками или валком и футеровкой камеры дробления и в результате этого дробится.
По конструктивному исполнению валковые дробилки бывают одно-, двух- и четырехвалковые. В последнем случае одна пара валков располагается над другой, т.е. четырехвалковая дробилка может рассматриваться как две двухвалковые дробилки, смонтированные в один корпус.
Поверхности валков бывают гладкие, рифленые, ребристые и зубчатые. Сочетания дробящих поверхностей может быть различным: например, оба валка могут иметь гладкую поверхность, или одна гладкую, другой – рифленую и т.д.
|
При одинаковым диаметре рифленые и зубчатые валки могут захватывать более крупные куски материала, чем гладкие. Так, если D – диаметр валка, d – диаметр куска материала, то при дроблении пород средней прочности соотношение D/d для гладких валков составляет 17 – 20, для рифленых и зубчатых 2 – 6.
Промышленные валковые дробилки имеют диаметр валка 400-1500 мм и длину, равную 0,4-1,0 диаметра (длина зубчатых валков может быть больше, чем диаметр).
Валковые дробилки применяют для среднего и мелкого дробления материалов в основном средней прочности (до ) на гладких и рифленых валках и мягких (до
) – на зубчатых валках.
В промышленности строительных материалов наиболее распространены двухвалковые дробилки. Такие дробилки особенно удобны для измельчения влажных и вязких материалов (например, глин), так как другие дробильные машины забиваются подобными материалами, а на валковых дробилках могут быть установлены специальные скребки, снимающие налипший материал с поверхности валков.
Принципиальная схема двухвалковой дробилки показана на рисунке 1. Валки вращаются навстречу один другому и дробят попавший между ними материал, раздавливая его при этом и частично истирая. Иногда для увеличения истирающего эффекта, необходимого при измельчении некоторых материалов, валкам сообщают разную окружную скорость.
Рисунок 1. Принципиальная схема двухвальной дробилки
Подшипники вала одного из валков опираются на пружины и могут перемещаться. В результате этого при попадании недробимого предмета один валков может отойти от другого и пропустить недробимый предмет, после чего под действием пружин возвратится в исходное положение.
Привод валков осуществляется так, как показано на рисунке 2. От двигателя через клиноременную и шестеренчатую передачи приводится во вращение один валок, другой валок связан с первым шестернями с удлиненными зубьями, допускающими отход валков при пропуске недробимых предметов (рисунок 2, а). Такое кинематическое решение довольно сложно, кроме того, оно не обеспечивает нормальную работу шестерен с удлиненными зубьями в условиях динамических нагрузок и абразивной пыли. Поэтому в последнее время каждый валок стали приводить от электродвигателя (рисунок 2, б) или через редуктор и карданные валы (рисунок 2, в).
Рисунок 2. Кинематические схемы валовых дробилок
Лабораторная работа №4
Определение угла захвата щековых дробилок
|
|
Кормораздатчик мобильный электрифицированный: схема и процесс работы устройства...
Особенности сооружения опор в сложных условиях: Сооружение ВЛ в районах с суровыми климатическими и тяжелыми геологическими условиями...
Таксономические единицы (категории) растений: Каждая система классификации состоит из определённых соподчиненных друг другу...
Автоматическое растормаживание колес: Тормозные устройства колес предназначены для уменьшения длины пробега и улучшения маневрирования ВС при...
© cyberpedia.su 2017-2024 - Не является автором материалов. Исключительное право сохранено за автором текста.
Если вы не хотите, чтобы данный материал был у нас на сайте, перейдите по ссылке: Нарушение авторских прав. Мы поможем в написании вашей работы!