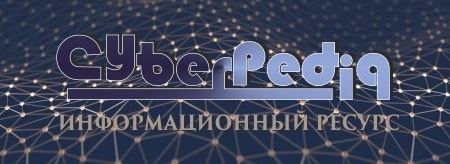
Типы сооружений для обработки осадков: Септиками называются сооружения, в которых одновременно происходят осветление сточной жидкости...
Эмиссия газов от очистных сооружений канализации: В последние годы внимание мирового сообщества сосредоточено на экологических проблемах...
Топ:
Теоретическая значимость работы: Описание теоретической значимости (ценности) результатов исследования должно присутствовать во введении...
Методика измерений сопротивления растеканию тока анодного заземления: Анодный заземлитель (анод) – проводник, погруженный в электролитическую среду (грунт, раствор электролита) и подключенный к положительному...
Особенности труда и отдыха в условиях низких температур: К работам при низких температурах на открытом воздухе и в не отапливаемых помещениях допускаются лица не моложе 18 лет, прошедшие...
Интересное:
Наиболее распространенные виды рака: Раковая опухоль — это самостоятельное новообразование, которое может возникнуть и от повышенного давления...
Как мы говорим и как мы слушаем: общение можно сравнить с огромным зонтиком, под которым скрыто все...
Средства для ингаляционного наркоза: Наркоз наступает в результате вдыхания (ингаляции) средств, которое осуществляют или с помощью маски...
Дисциплины:
![]() |
![]() |
5.00
из
|
Заказать работу |
|
|
Наиболее распространен контроль скорости нанесения пленок резонансно-частотным методом. При этом в качестве датчика используется включенный в контур генератора частоты кварцевый элемент. Принцип действия основан на зависимости частоты колебаний от изменения массы кварцевого элемента при нанесении на его поверхность пленки. С увеличением массы кварцевого элемента его резонансная частота падает. Для линейного участка зависимости частоты от массы нанесенной пленки справедливо следующее соотношение:
где и
– масса и резонансная частота кварцевого элемента до нанесения пленки;
и
изменение массы и резонансной частоты после нанесения пленки. Таким образом, скорость роста пленки определяют по изменению скорости сдвига резонансной частоты.
Основной частью кварцевого датчика является кварцевый кристалл в виде пластины, на обе поверхности которой наносят контактные слои золота или серебра. Кристаллы кварца очень чувствительны к изменениям температуры, поэтому кварцевый элемент вставляется в массивный медный держатель, охлаждаемый проточной водой. Это исключает повышение температуры кварцевого элемента, вызванное потоками тепла от испарителя и нагревателя подложки. В кожухе имеется сквозное отверстие для пропускания потока частиц наносимого материала к кварцевому элементу.
Этим методом можно также измерить толщину нанесенной пленки, используя следующую формулу:
где – площадь кварцевого кристалла, покрытая пленкой наносимого вещества;
– плотность наносимой пленки. Точность измерения толщины тонких металлических и диэлектрических пленок в интервале от 10 нм до 5 мкм составляет
%. Для выполнения точных измерений приборы градуируют отдельно для каждого материала. Максимально допустимая суммарная толщина пленки, наносимой на кварцевый датчик, определяется максимальным сдвигом частоты и примерно составляет 20 мкм алюминия. Существенным недостатком метода является то, что помимо градуировки по осаждаемому материалу необходима также периодическая чистка кварцевых элементов от осажденной пленки.
|
Порядок выполнения работы
1. Получить у преподавателя необходимые приборы и инструменты.
2. Взвесить на аналитических весах WA-31 согласно инструкции на них: пластину кремния (с точностью до 10–4 г) и одновременно четыре навески алюминия (с точностью до 10–3 г).
3. Измерить расстояние от испарителя до пластины. Рассчитать по формуле
толщину пленки алюминия для точечно-
го источника испарения. Здесь – вес всех навесок алюминия;
– удельный вес алюминия, равный 2,7 г/см
.
4. Рассчитать по формуле максимально допустимое давление
в момент напыления при условии
, где
– длина пути свободного пробега молекул воздуха, см;
– температура в объеме под колпаком;
– давление в миллиметрах ртутного столба.
5. Провести напыление алюминия на пластину под руководством преподавателя. По показаниям вакуумметра и градуировочной кривой для манометрического преобразователя ЛТ-2 определить порядок величины давления под колпаком установки в момент напыления, сравнить его с давлением, рассчитанным по п. 4, оценить и объяснить различия.
6. Взвесить пластину с напыленным на нее алюминием. Измерить линейкой диаметр пластины. По формуле рассчитать среднюю толщину пленки алюминия на пластине. Здесь
,
– вес пластины до и после напыления;
– радиус пластины.
7. Прочертить стальной иглой две царапины на пленке алюминия (по образцу).
8. Определить на микроскопе МИИ-4 толщину пленки алюминия
в области царапин согласно инструкции по эксплуатации МИИ-4. По виду царапин оценить адгезию алюминия.
|
9. Объяснить причины различия результатов пп. 3, 6 и 8. Сформулировать предложения по улучшению равномерности пленки алюминия.
Примерная последовательность операций при напылении
1. Установить подложку на подложкодержателе при поднятом колпаке.
2. Закрыть рабочую камеру, опустив колпак.
3. Откачать из камеры воздух до требуемого вакуума. Для этого выполнить операции в последовательности.
4. Включить источник, создающий атомарный поток алюминия.
5. Нанести пленку определенной толщины при постоянно работающих источнике потока частиц и вакуумной системе.
6. Выключить источник потока алюминия, дождаться охлаждения подложки.
7. Напустить воздух в рабочую камеру до атмосферного давления.
8. Поднять колпак и снять подложку с подложкодержателя.
В некоторых случаях выполняют дополнительные операции (на-пример, предварительный нагрев подложек). Эффективность процес-
са характеризуется его производительностью, чистотой и равномер-
ностью толщины наносимой пленки.
|
|
Археология об основании Рима: Новые раскопки проясняют и такой острый дискуссионный вопрос, как дата самого возникновения Рима...
Кормораздатчик мобильный электрифицированный: схема и процесс работы устройства...
История развития хранилищ для нефти: Первые склады нефти появились в XVII веке. Они представляли собой землянные ямы-амбара глубиной 4…5 м...
Эмиссия газов от очистных сооружений канализации: В последние годы внимание мирового сообщества сосредоточено на экологических проблемах...
© cyberpedia.su 2017-2024 - Не является автором материалов. Исключительное право сохранено за автором текста.
Если вы не хотите, чтобы данный материал был у нас на сайте, перейдите по ссылке: Нарушение авторских прав. Мы поможем в написании вашей работы!