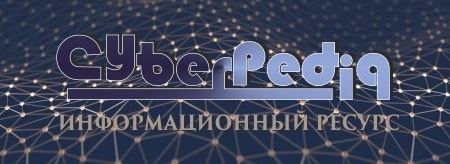
Папиллярные узоры пальцев рук - маркер спортивных способностей: дерматоглифические признаки формируются на 3-5 месяце беременности, не изменяются в течение жизни...
Поперечные профили набережных и береговой полосы: На городских территориях берегоукрепление проектируют с учетом технических и экономических требований, но особое значение придают эстетическим...
Топ:
Оснащения врачебно-сестринской бригады.
Эволюция кровеносной системы позвоночных животных: Биологическая эволюция – необратимый процесс исторического развития живой природы...
Оценка эффективности инструментов коммуникационной политики: Внешние коммуникации - обмен информацией между организацией и её внешней средой...
Интересное:
Влияние предпринимательской среды на эффективное функционирование предприятия: Предпринимательская среда – это совокупность внешних и внутренних факторов, оказывающих влияние на функционирование фирмы...
Мероприятия для защиты от морозного пучения грунтов: Инженерная защита от морозного (криогенного) пучения грунтов необходима для легких малоэтажных зданий и других сооружений...
Подходы к решению темы фильма: Существует три основных типа исторического фильма, имеющих между собой много общего...
Дисциплины:
![]() |
![]() |
5.00
из
|
Заказать работу |
Содержание книги
Поиск на нашем сайте
|
|
В настоящее время используется лишь небольшая часть гипсосодержащих отходов и основного из них — фосфогипса. Как правило этот крупнотоннажный отход удаляется с территорий предприятий в шламохранилище, что связано со значительными затратами труда и средств. Гипсосодержащие отходы, как убедительно показано результатами многочисленных исследований и практики, могут использоваться в сельском хозяйстве для химической мелиорации кислых и солонцовых почв и компостирования с органическими удобрениями; в цементной промышленности в качестве минерализатора — добавки к сырьевой смеси и как регулятор скорости схватывания — вместо природного гипса; для производства гипсовых вяжущих и изделий, наполнителя в производстве пластмасс, стекла; в строительстве автомобильных дорог, для производства серной кислоты и др.
К наиболее перспективным направлениям утилизации фосфогипса относится использование его в производстве гипсовых вяжущих материалов.
Объем гипсосодержащих побочных продуктов превышает объем специально добываемого для производства строительных материалов гипсового камня. Значительный интерес для производства вяжущих и материалов на их основе наряду с гипсосодержащими представляют также известьсодержащие отходы промышленности.
Гипсовые вяжущие на основе фосфогипса. Фосфогипс содержит от 80 до 98% гипса и может быть отнесен к гипсовому сырью. Высокая дисперсность фосфогипса (Sya = 3500—3800 см2/г) позволяет исключить из технологического процесса дробление и грубый помол. Вместе с тем высокая влажность фосфогипса (до 40%) усложняет его транспортирование и подготовку и приводит к значительным расходам топлива на сушку. Наличие в фосфогипсе водорастворимых в особенности фосфор- и фторсодержащих примесей усложняет переработку отходов по сравнению с переработкой природного гипсового камня, вызывает необходимость промывки, нейтрализации и др. и обусловливает соответственно более высокие тепловые затраты. При обычной технологии гипсовые вяжущие на основе фосфогипса низкокачественны, что объясняется высокой водопотребностью фосфогипса, обусловленной большой пористостью образуемого полугидрата. Если водопотребность обычного строительного гипса составляет 50—70%, то для получения теста нормальной густоты из фосфогип-сового вяжущего без дополнительной обработки требуется воды 120— 130%.
|
Отрицательное влияние на строительные свойства фосфогипса содержащихся в нем примесей можно несколько снизить домолом фосфогипса и формованием изделий методом виброукладки. В этом случае качество фосфогипсового вяжущего повышается, хотя и остается ниже, чем строительного гипса из природного сырья.
Исследования показали, что основной причиной ухудшения вяжущих свойств непромытого фосфогипса является образование значительного количества ангидрита т. е. безводного сульфата кальция при обжиге под влиянием кислых фосфатных и фтористых соединений. С ростом содержания нерастворимого ангидрита выше 30% прочность вяжущих приближается к нулю.
Примеси в фосфогипсе свободных фосфорной и серной кислот, растворимых солей замедляют твердение гипсовых вяжущих. Осложняет технологию также выделение фтористых газов при тепловой обработке, из-за повышенной кислотности происходит коррозия оборудования.
В настоящее время разработан и опробован в производственных условиях ряд технологий получения гипсовых вяжущих из фосфогипса. Промышленное производство этих вяжущих и изделий на их основе было организовано на Воскресенском и Уваровском химических заводах, Кедайняйском экспериментальном заводе.
Технологические процессы получения гипсовых вяжущих, основным компонентом которых служит полугидрат сульфата кальция или ангидрит, включают подготовку исходного продукта к обжигу и обжиг.
|
Основные методы подготовки фосфогипса в производстве гипсовых вяжущих можно разделить на 4 группы:
1-я — промывка фосфогипса водой;
2-я — промывка в сочетании с нейтрализацией и осаждением примесей в водной суспензии;
3-я — метод термического разложения примесей;
4-я — введение нейтрализующих, минерализующих и регулирующих кристаллизацию добавок перед обжигом и после него.
Методы 1-й и 2-й групп связаны с образованием значительного количества загрязненной воды (2—5 м3 на 1 т фосфогипса), большими затратами на их удаление и очистку. Большинство методов термического распада примесей (3-я группа) основано на обжиге фосфогипса до образования растворимого ангидрита с дальнейшей его гидратацией и повторным обжигом до полугидрата. Широкого применения они пока не имеют так же, как и методы 4-й группы. Для реализации последних необходимы дефицитные добавки и они не обеспечивают постоянные свойства вяжущего.
Ведущее место в разработке и практическом применении технологии гипсовых вяжущих из фосфогипса принадлежит Японии, Франции, ФРГ.
На основе фосфогипса возможно получение как высокопрочного, так и строительного гипса, отличающихся водопотребностью и соответственно прочностью достигаемой уже через 1,5 ч после затворения.
Технология получения высокопрочного гипса из фосфогипса, разработанная институтом ВНИИСТРОМ, предусматривает доведение соотношения в фосфогипсовом шламе жидкой и твердой фаз до единицы, введение в полученную суспензию добавки ПАВ — регулятора кристаллизации полугидрата — и гидротермальную обработку усредненной суспензии в автоклаве, где происходят дегидратация фосфогипса и кристаллизация полугидрата кальция а-модификации. На вакуум-фильтре твердая фаза суспензии отделяется и поступает последовательно на сушку, помол и склад готовой продукции. На подобной технологической линии получение высокопрочного гипса из фос-фогипса может быть непрерывным и полностью автоматизированным. Использование двух автоклавов вместимостью 25 м3 позволяет получать в год 100—110 тыс. т высокопрочного гипса. Цикл тепловлажно-стной обработки составляет 45 мин. Схватывание фосфогипсового вяжущего начинается через 8—10 мин, конец — через 10—15 мин, предел прочности на сжатие составляет 30—50 МПа, т. е. в 3—4 раза выше прочности на сжатие обычного строительного гипса.
|
Высокая влажность и дисперсность фосфогипса обусловливают перспективность применения автоклавных способов для получения высокопрочных гипсовых вяжущих. При автоклавных технологиях испаряется не вся свободная и выделяющаяся при дегидратации вода, а лишь вода, остающаяся после фильтрации продукта автоклавной обработки. При нагревании фосфогипсовой пульпы в автоклаве при 114—125 °С гипс растворяется и жидкая фаза становится пересыщенной по отношению к полугидрату, что и приводит к кристаллизации игольчатых кристаллов а-полугидрата. В отличие от кристаллов (3-полугидрата, образующихся в варильных котлах и других аппаратах, сообщающихся с атмосферой, относительно крупные кристаллы a-CaS03* 0,5Н2О имеют существенно меньшую водопотребность и формируют искусственный камень с более высокими физико-механическими свойствами.
На созданной во ВНИИстроме опытной установке организовано экспериментальное изготовление стеновых камней с использованием продукта автоклавной обработки сырьевой смеси фосфогипса и гидравлических компонентов.
Предложена технология получения высокопрочных гипсовых вяжущих обработкой исходного фосфогипса в растворах кислот или солей, имеющих температуру кипения 105—120 °С, с промывкой и высушиванием готового продукта.
Важным резервом значительного повышения экономичности автоклавного способа переработки фосфогипса является ликвидация сушки, помола, а в перспективе и фильтрации продукта автоклавной обработки. На эти стадии расходуется около 45% капитальных, около 50% текущих, более 60% тепловых и энергетических затрат.
Процесс получения вяжущего заключается в дегидратации гипса, содержащегося в фосфогипсе, до полугидрата, а процесс изготовления изделий — в обратном: гидратации полугидрата до гипса в большом избытке воды. Таким образом, наблюдается парадоксальный факт: при влажном исходном сырье (фосфогипс) и влажном готовом продукте (гипсовые изделия) на промежуточной стадии технологического процесса посредством сушки получают порошкообразный продукт (гипсовое вяжущее), который при изготовлении изделий на этом же предприятии уже через короткое время вновь смешивают с водой.
|
Эффективно производство изделий непосредственно из фосфогипса по одностадийной технологии, предусматривающей осуществление обоих химических процессов — дегидратации двуводного гипса и гидратации образуемого полугидрата — в пределах одного технологического цикла. Дегидратация протекает по принципу «самозапаривания», т. е. в формах повышенной плотности кристаллизационная вода выделяется в капельножидком состоянии, оставаясь в порах зерен и пустотах кристаллической решетки гипса.
По этой технологии изделия можно формовать на установках, состоящих из двух пуансонов и наружной опалубки. Верхний пуансон служит выталкивателем отпрессованного изделия. В форму засыпают гипсовое сырье, разравнивают его, а затем верхний пуансон приводят в соприкосновение с поверхностью порошка. Таким способом создается замкнутое пространство, в котором производят термическую обработку фосфогипса, после чего полученную гидратирующуюся массу прессуют. Затвердевшие изделия распалубливают при температуре ниже 40 °С.
Разработана также технология производства высокопрочного гипса на основе фосфополугидрата — отхода производства экстракционной фосфорной кислоты по полугидратной схеме. Она состоит из следующих этапов обработки: измельчения и активирования фосфополугидрата на вальцах тонкого помола, разбавления его, перевода «пассивирующих» пленок с помощью специальных добавок в жидкую фазу, последующего фильтрования суспензии на ленточных вакуум-фильтрах; промывания твердой фазы, сушки ее до полного удаления гигроскопической влаги и помола.
Основные работы по использованию фосфополугидрата для получения гипсовых вяжущих ведутся в трех направлениях:
• гидратация до двухводного гипса и получение сырья для производства строительного и высокопрочного гипса;
• активация с сушкой;
• обжиг до ангидрита с введением активаторов твердения.
Снижение пассивирующего действия кислых примесей на зернах
фосфополугидрата достигается механической обработкой и нейтрализацией. В качестве активаторов твердения применяют добавки различных фтористых соединений. Из фосфополугидрата при его нейтрализации щелочными добавками в сочетании с механической обработкой в бегунах можно получать смеси и прессовать из них различные изделия.
Отличительными особенностями вяжущего из фосфополугидрата являются: рост прочности при хранении в нормальных условиях через 20—30 сут на 10—30%; сравнительно небольшое объемное расширение.
|
Фосфополугидрат без дополнительной обработки может быть рекомендован для сооружения оснований дорожных одежд в тех случаях, когда к последним не предъявляются повышенные требования по морозостойкости.
Водостойкое вяжущее на основе фосфогипса можно получить как смешиванием с цементом и пуццолановой добавкой (фосфогипсоцементно-пуццолановое вяжущее), так и совместной тепловой обработкой суспензии фосфогипса и различных гидравлических компонентов, например портландцемента, нефелинового шлама, металлургических шлаков со щелочными активизаторами и др. В последнем случае получают высокопрочное вяжущее повышенной водостойкости.
Технологическая схема включает: приготовление суспензии фосфогипса и подачу ее на переработку; фильтрацию суспензии фосфогипса и приготовление рабочей сырьевой смеси из фосфогипса, добавок и воды; автоклавную обработку сырьевой смеси; сушку полупродукта и его помол.
На 1 т вяжущего расходуется 1,5 т влажного фосфогипса и 0,1 т добавки. При удельной поверхности 3000—4500 см2/г водопотребность вяжущего составляет 35—45%, схватывание начинается через 30— 60 мин, конец его — через 80—120 мин, предел прочности на сжатие через 3 ч составляет 6—7 МПа, а при постоянной массе — 20—40 МПа, коэффициент размягчения 0,6—0,7.
Обжигом фосфогипса при 600—1000 °С возможно получение ангидритовых вяжущих, состоящих в основном из нерастворимого ангидрита. Они приобретают способность твердеть при введении добавки 1,5—2% извести, добавляемой при помоле обожженного материала. В качестве добавок-катализаторов твердения ангидритовых вяжущих могут быть также оксид магния, обожженный доломит (3—8%), сульфат натрия (0,5—1%) и др. Введение этих добавок позволяет в 28-су-точном возрасте достигать предел прочности при сжатии до 20 МПа. Разработан ряд патентованных рецептур ангидритовых вяжущих из фосфогипса, включающих различные комплексные добавки, в которые входят известь, кремнефторид натрия, алюмосиликатные, железистые компоненты и др.
Перспективными являются работы по получению безобжиговых фосфогипсовых дигидратных вяжущих. При механохимической активизации фосфогипса за счет повышения его удельной поверхности путем доизмельчения и введения некоторых добавок он приобретает способность твердеть без перевода в полугидрат. Этот эффект объясняется повышенной растворимостью высокодисперсного дигидрата, способностью его к образованию пересыщенных растворов и формированию коагуляционно-кристаллизационных структур. Наиболее значительную прочность (до 30 МПа и выше) фосфогипсовое дигид-ратное вяжущее проявляет в условиях прессования при давлении 20— 25 МПа.
Приоритет в разработке безобжиговых гипсовых вяжущих (гипсовых цементов) принадлежит П.П. Будникову. Еще в 1924 г. им было установлено, что двуводный гипс после помола в присутствии различных добавок и затворения водой приобретает способность твердеть на воздухе и достигает при этом значительной прочности. Дальнейшие исследования показали возможность получения безобжигового гипсового дигидратного вяжущего путем его тонкого помола в шаровой мельнице по сухому и мокрому способам без активизирующих добавок. Существенным недостатком предложенных технологий является необходимость высокой тонкости измельчения гипса. Изделия из безобжигового гипсового вяжущего могут быть получены при силовых методах уплотнения — прессовании, вибропрессовании. Для фосфогипса необходима предварительная подсушка до прессования или отвод жидкой фазы в процессе прессования, что усложняет и удорожает технологию изделий на основе дигидратного гипсового вяжущего.
Для повышения водостойкости дигидратного гипсового вяжущего могут быть применены те же добавки, которые используются для повышения водостойкости полугидратных вяжущих (известь, гранулированные доменные шлаки, синтетические смолы).
Технология, разработанная в МИСИ им. В.В. Куйбышева, предусматривает перемешивание смеси взятых в определенном соотношении сырого фосфогипса, молотой негашеной извести, добавки и воды в бетоносмесителе принудительного действия, формование изделий и их термообработку. Наиболее благоприятно на качество изделий влияет перемешивание фосфогипсобетонной смеси в бегунах, в которых не только смешиваются компоненты смеси, но и истираются частички фосфогипса.
Правильно выбранное соотношение между известью и активной минеральной добавкой обеспечивает не только прочность, но и долговечность получаемого на основе двуводного фосфогипса бетона при его твердении во влажной среде.
Наблюдения за состоянием образцов из фосфогипсобетона, содержащих различное количество активной минеральной добавки, показали, что при твердении в течение 1 года происходит непрерывный рост прочности. Наиболее он интенсивен во влажных условиях, где происходит более полное образование гидросиликатов и алюминатов кальция.
Из фосфогипсовых вяжущих в смеси с заполнителями можно получать перегородочные плиты и блоки, гипсопесчаный кирпич, декоративные и акустические плиты. Эти вяжущие перспективны также для изготовления стеновых гипсобетонных камней классов В7,5—В12,5 способом вибропрессования, а также крупноразмерных элементов наружных стен. Изделия на основе фосфогипсовых вяжущих характеризуются более низкой деформативностью, чем на аналогичных вяжущих из природного сырья.
На основе водостойких фосфогипсоцементно-пуццолановых вяжущих разработаны составы легких керамзитобетонов классов В3,5—В7,5. Водостойкость гипсокерамзитобетона на 40—50% выше, чем чистого вяжущего. В 3-часовом возрасте прочность бетона составляет 30—35%, в суточном — 40—45%, а к 7 сут достигает почти 100%-ной марочной прочности, определяемой в возрасте 28 сут. Интенсивный рост прочности бетона в начальный период позволяет исключить тепловую обработку изделий из него и осуществить предварительную распалубку уже через 20—25 мин, что значительно упрощает процесс производства и снижает на 10—15% стоимость изделий.
Рационально применение фосфогипсоцементно-пуццоланового вяжущего для производства санитарно-технических кабин. В расчете на одну санитарно-техническую кабину сокращаются трудовые затраты на 16 чел. • ч, энергетические затраты — на 155 кг условного топлива, высвобождается до 630 кг цемента и 25 кг арматурной стали.
|
|
История развития пистолетов-пулеметов: Предпосылкой для возникновения пистолетов-пулеметов послужила давняя тенденция тяготения винтовок...
Таксономические единицы (категории) растений: Каждая система классификации состоит из определённых соподчиненных друг другу...
Папиллярные узоры пальцев рук - маркер спортивных способностей: дерматоглифические признаки формируются на 3-5 месяце беременности, не изменяются в течение жизни...
Кормораздатчик мобильный электрифицированный: схема и процесс работы устройства...
© cyberpedia.su 2017-2024 - Не является автором материалов. Исключительное право сохранено за автором текста.
Если вы не хотите, чтобы данный материал был у нас на сайте, перейдите по ссылке: Нарушение авторских прав. Мы поможем в написании вашей работы!