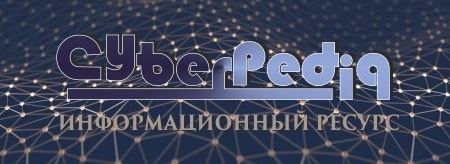
Папиллярные узоры пальцев рук - маркер спортивных способностей: дерматоглифические признаки формируются на 3-5 месяце беременности, не изменяются в течение жизни...
Состав сооружений: решетки и песколовки: Решетки – это первое устройство в схеме очистных сооружений. Они представляют...
Топ:
Отражение на счетах бухгалтерского учета процесса приобретения: Процесс заготовления представляет систему экономических событий, включающих приобретение организацией у поставщиков сырья...
Оснащения врачебно-сестринской бригады.
Теоретическая значимость работы: Описание теоретической значимости (ценности) результатов исследования должно присутствовать во введении...
Интересное:
Отражение на счетах бухгалтерского учета процесса приобретения: Процесс заготовления представляет систему экономических событий, включающих приобретение организацией у поставщиков сырья...
Принципы управления денежными потоками: одним из методов контроля за состоянием денежной наличности является...
Распространение рака на другие отдаленные от желудка органы: Характерных симптомов рака желудка не существует. Выраженные симптомы появляются, когда опухоль...
Дисциплины:
![]() |
![]() |
5.00
из
|
Заказать работу |
|
|
Из всех конструкций. материалов наибольшей стойкостью к коррозии характеризуются пластмассы, керамика, стекло, резина, асбест и бетон. Однако по многим другим эксплуатационным свойствам эти материалы не могут конкурировать с металлами. Обладающие высокой стойкостью благородные металлы слишком дороги для использования в качестве основные конструкции материалов современной техники. Наиболее доступный металл - железо, обладает требуемым комплексом физ. свойств, но низкой стойкостью к коррозии. Для повышения последней без ухудшения механических характеристик Fe легируют другими металлами, например, хромом. При легировании значительного кол-вом хрома, а иногда и никелем получают нержавеющие стали. Наибольшей стойкостью к равномерной коррозии обладают аустенитные стали, если имеются условия для поддержания их в пассивном состоянии. Аустенитные стали устойчивы к воздействию воздуха, р-ров азотной и мн. орг. кислот, серной кислоты в некотором интервале концентраций, сернистой кислоты и щелочей. Однако в других средах они подвержены питтинговой, щелевой и межкристаллитной коррозии, а также коррозионному растрескиванию. Важными коррозионностойкими материалами являются также Ni, Al, Cu, Ti и сплавы на их основе. Никель устойчив к воздействию горячих и холодных щелочей, разбавленных неокисляющих органических и неорганических кислот, а также воздушной атмосферы. Легирование медью повышает его стойкость к коррозии в восстановит. средах, а также к питтинговой коррозии в морской воде. Легирование хромом повышает сопротивление воздействию окислительных сред, а молибденом - восстановительных; одновременное легирование хромом и молибденом - воздействию тех и других сред. Алюминий обладает хорошей стойкостью к коррозии, в растворах уксусной и азотной кислот, парах S, SО2 и других. Легируют Аl небольшими количествами других металлов, главным образом для улучшения его механических характеристик. Медь устойчива к воздействию воздуха, морской и пресной (горячей и холодной) воды, деаэрирных растворов неокисляющих кислот. Сплавы Сu с Аl (алюминиевая бронза) и Ni (купроникель) используют для изготовления конденсаторных труб, а алюминиевую бронзу - также для корпусов насосов и корабельных гребных винтов. Титан и его сплавы обладают высокой коррозионной стойкостью в морской воде, воздухе, загрязненном промышлеными выбросами, в ряде агрессивных химических сред (см. также Коррозионностойкие материалы). В практике защиту от коррозии широко применяют поверхностное легирование недорогих сплавов, имеющих хорошие механические характеристики. Поверхностный слой обычной стали можно превратить в сплав с высокой коррозионной стойкостью путем нагрева в порошкообразной шихте, содержащей Zn (диффузионное цинкование), Аl (алитирование) или Сr (хромирование), иногда со спец. активирующими добавками. Можно также плакировать дешевый малостойкий материал тонким слоем более коррозионностойкого, например, путем совместной горячей прокатки двух листов до нужной толщины образующегося "биметалла". Поверхность изделий модифицируют путем нанесения тонких покрытий из других металлов или сплавов, преимлимых для защиты от атмосферной коррозии. Состав и способ нанесения покрытий может быть различными. На стальной прокат покрытия из Zn, Al и их сплавов чаще всего наносят методом напыления: металл покрытия в виде проволоки или порошка плавится в электрической дуге или пламени, распыляется газовой струей и осаждается на подготовленную поверхность. Хорошей адгезией и равномерной толщиной отличаются покрытия, образуемые окунанием защищаемых изделий в ванну расплавленного Zn или Аl. Электрохимические методы нанесения широко используют в тех случаях, когда необходимо покрытие очень малой и контролируемой толщины, а изделие не должно сильно нагреваться. Так наносят Cr, Ni, Sn, Zn, Cd и другие. Хромовые покрытия декоративны и благодаря высокой способности хрома пассивироваться могут обладать высокой защитной способностью, но, как правило, содержат трещины и потому чаще их наносят поверх никелевых покрытий.
|
|
Методы снижения коррозионной активности среды. Наиболее распространенные агрессивные среды - вода, водные растворы кислот и щелочей, атмосфера, почва. Агрессивность водных сред зависит от растворенных в них О 2 и СО2, удаление которых является одним из методов борьбы с коррозией железа, стали, меди, латуни, цинка, свинца. Физ. удаление О 2 и СО 2 достигается нагревом воды при пониженном давлении или продувкой инертным газом, химическое - пропусканием через слой железных или стальных стружек, обработкой восстановителем (сульфатом натрия, гидразином). В энергетике и некоторых отраслях техники воду освобождают также от стимуляторов локальной коррозии, например, хлоридов. Эффективно снижают агрессивность водных сред небольшие добавки (редко более 1%) ингибиторов коррозии, защитное действие которых обусловлено образованием прочно связанных с поверхностью нерастворимых продуктов коррозии. Обычно применяют анодные ингибиторы гидроксид, карбонат, силикат, борат, фосфаты, нитрит и бензоат натрия и катодные (сульфаты цинка, бикарбонат натрия и некоторые др.). Анодные ингибиторы в недостаточной концентрации вызывают питтинговую коррозию. Они более эффективны в смеси с катодными ингибиторами, причем совместное действие часто превосходит сумму отдельных эффектов. В кислых средах используют специфические, главным образом органические ингибиторы. Особый класс составляют ингибиторы-пассиваторы, переводящие металл в пассивное состояние посредством смещения его электродного потенциала в более положит. область. Это окислители, чаще пероксидного типа, а также соединения благородных металлов, обменное осаждение которых на защищаемом металле способствует достижению потенциала пассивации. Агрессивность атмосферы сильно зависит от ее влажности и от того, является ли район промышленным, сельским, морским и т. п. (см. Атмосферная коррозия). Для любого металла в зависимости от гигроскопичности продуктов его коррозии и пылевых частиц, попадающих на поверхность, имеется некоторая критичическая относительная влажность, ниже которой он не подвергается атм. коррозии; для Fe, Cu, Ni, Zn она находится в пределах от 50 до 70%. Поэтому в открытой атмосфере целесообразна периодическая очистка поверхности изделия от гигроскопических загрязнений. Гигроскопичность продуктов коррозии стали уменьшают легированием медью в небольших количествах. Для изделий, имеющих историческая ценность, темперару их хранения иногда искусственно поддерживают несколько выше точки росы. В полостях и упаковках ценных изделий пониженную относительную влажность поддерживают с помощью поглотителей влаги. Весьма эффективны также летучие ингибиторы коррозии, например, карбонат или нитрат циклогексиламина, которые, медленно испаряясь, осаждаются на защищаемой поверхности с образованием независимой адсорбционной пленки. Однако, защищая сталь, такие ингибиторы могут усиливать коррозию др. металлов. Поэтому для защиты от коррозии изделий, включающих различные металлы, необходимы специальные составы. Распространены упаковочные материалы (бумага, картон, пленка), содержащие подходящий ингибитор коррозии. Агрессивность промышленной атмосферы определяется в основном продуктами сгорания топлив и другими выбросами (SO 2, CO 2, H 2 S, NO 2, NH 3, сажа, взвеси солей). Из них главным стимулятором коррозии является SO 2, превращающийся на поверхности металла во влажной атмосфере в серную кислоту. В закрытых объемах стимуляторами коррозии оказываются пары орг. кислот (муравьиной, уксусной, пропионовой), выделяющиеся из некоторых сортов древесины, пластмасс, клеев, красок. Единственный путь снижения агрессивности промышленной атмосферы - устранение выбросов, в помещениях кондиционирование и фильтрация поступающего воздуха. Коррозионная агрессивность почвы определяется содержанием в ней О 2, влажностью, электрической проводимостью, рН (см. Подземная коррозия). В кислых почвах куски извести вблизи зарытого в почву металла могут долго создавать рН, достаточный для поддержания металла в пассивном состоянии.
|
|
Защитные изолирующие покрытия. Из органических изолирующих покрытий для защиты от атмосферной коррозии широко используют лакокрасочные, для подземных конструкций - толстые покрытия из каменного-угля пека, битумов, полиэтилена, сочетаемые с катодной электрохимической защитой. Для улучшения адгезии производится подготовка поверхности под покрытие: тщательная (мех. или хим.) очистка от грязи и продуктов коррозии, специальная химическая или электрохимическая обработка (фосфатирование, хроматирование, анодирование). Сплошность повышают использованием многослойных (обычно трехслойных) покрытий. От первого (грунтовочного) слоя требуется макс. адгезия к металлу и хорошие защитные характеристики, достигаемые введением пигментов с ингибирующими свойствами (свинцовый сурик, хромат цинка). Конечная толщина покрытия обычно не превышает 0,75 мм. Применение вместо натуральных масел современных синтетических материалов позволяет увеличить срок службы покрытия в 3-5 раз. Некоторые пластмассы, напр., эпоксидные и полиуретановые смолы, надежно защищают металл в виде тонких покрытий; другие (поливинилхлорид, полиэфиры, некоторые фторзамещенные полиолефины, полиэтилен) используются в виде относительно толстых покрытий. Толстые и особенно армированные покрытия можно рассматривать как коррозионностойкую футеровку. Среди неорганических защитных покрытий важными являются стекловидные эмали, используемые преим. для защиты чугунных и стальных изделий (резервуары, ванны, бытовая техника) от воздействия атмосферы, воды и других сред. Внутренняя поверхность стальных трубопроводов, резервуаров для горячей и холодной воды, емкостей для хранения нефти и некоторых продуктов химической промышленности можно защищать дешевыми покрытиями из цемента. Особый класс составляют т. наз. конверсионные защитные покрытия, которые состоят из стойких соединений на основе самого покрываемого металла (фосфатных, хроматных, оксидных), получаемых путем его хим. или электрохимической обработки. Их используют преим. как основу под лакокрасочные покрытия.
Электрохимическая защита основана на характерной зависимости скорости коррозионных процессов от электродного потенциала металла. Катодную защиту широко используют для снижения скорости коррозии подземных сооружений (трубопроводов, кабелей связи, свайных и стальных фундаментов), корпусов морских судов, эстакад, морских буровых скважин. Обычно катодная защита применяется в нейтральных средах, когда коррозия протекает с кислородной деполяризацией, и, следовательно, в условиях повышения катодной поляризуемости металла. Существуют два варианта катодной защиты. В первом варианте требуемое смещение электродного потенциала достигается путем катодной поляризации с помощью внеш. источника тока и вспомогательных инертных анодов (защита с наложенным током); во втором - посредством контакта его с массивными электродами из более электроотрицательного металла, которые, анодно растворяясь, обеспечивают протекание катодного тока к защищаемой конструкции (гальваническая защита). В качестве "жертвенных" анодов используют сплавы. Первый вариант применяют для защиты протяженных конструкций, обычно в комбинации с изолирующими покрытиями, в средах как с низким, так и с высоким электрическим сопротивлением. Преимущество его - в легкости регулирования защитного тока и поддержании защитного потенциала даже в условиях изменения изолирующих свойств покрытия во времени. Однако при использовании катодной защиты с наложенным током др. металлическая конструкция, расположенная вблизи защищаемой, может служить проводником и подвергаться усиленной коррозии. Гальванический вариант катодной защиты обычно применяют для защиты от коррозии небольших конструкций с хорошим покрытием и низким потреблением тока или для локальной защиты. Обычно при этом не наблюдается коррозия соседних металлических конструкций. Анодная защита, используемая в кислых средах, применима к металлам и сплавам, способным пассивироваться и оставаться пассивными в сравнительно широком интервале значений их потенциалов (большинство переходных металлов и сплавов на их основе, включая нержавеющие и углеродистые стали). Металл пассивируется и поддерживается в пассивном состоянии путем поляризации его внеш. анодным током. Ввиду малой величины тока его проникающая способность высока и защите поддаются даже отдаленные от катода участки поверхности. Чаще, однако, этот метод используют для защиты емкостей, содержащих агрессивные химические продукты.
|
Требования МК ПДНВ-78/95 к приему и несению вахты при обслуживании паровых котлов.
Международная конвенция о подготовке и дипломированию моряков и несении вахты принята в 1978 году. Основная цель поправок 1995 года ПДНВ78 направлена на повышение компетентности моряков путем применения эффективных способов образования, тренажерной и практической подготовки и оценки знаний моряков. В связи с этим в Кодексе ПДНВ95 сформированны обязательные минимальные требования к компетентности плавсостава на всех трех уровнях ответственности- управление,эксплуатация и вспомогательный.
Правилами Главы VIII Конвенции и разделами A-VIII/I, A-VIII/2 Кодекса ПДНВ95 определены организация и принцыпы, подлежащие соблюдению при несении вахты.
Для обеспечения работы судна необходима четкая организация мостика и отлаженное взаимопонимание при исполнении своих служебных обязанностей. Взаимозаменяемость и дублирование помогают избежать промахов и грубейших ошибок в управлении судном.
Организация мостика в зависимости от условий плавания должна соответствовать требованиям Системы управления безопасностью (СУБ) Компании, как того требует Международный Кодекс управления безопасностью (МКУБ) и Конвенция по подготовке и дипломированию моряков и несению вахты (ПДНВ-78/95).
Во время несения вахты OOW должен: нести вахту на мостике,не оставлять мостик без должной замены, продолжать нести ответственность за безопасность плавания, несмотря на присутствие на мостике капитана, в случае сомнений вызвать капитана, проверять достаточно часто положение судна, не выполнять посторонние обязанности, нести наблюдение
Вахтенный помощник не должен сдавать вахту если считает что заступающий не в форме.Заступающий должен перед вахтой ознакомиться с обстановкойВо время выполнения маневров вахта не передается.
Требования Правил технической эксплуатации к парогенераторам при ручном розжиге.
Непосредственно перед зажиганием огня в топке необходимо осмотреть котел и котельное помещение, в том числе:
1. убедиться, что манометры сообщены с котлом, а водоуказательные приборы функционируют нормально;
2. осмотреть крепление котла к фундаменту, убедится в отсутствии препятствий для свободного расширения котла и движения всех его подвижных опор;
3. убедиться, что в котельном помещении отсутствуют легковоспламеняющиеся материалы, а под котлами - вода, топливо и маслянистые вещества;
4. проверить готовность к действию противопожарных средств;
5. убедиться, что с дымовых труб сняты крышки или чехлы;
6. провентилировать котельное помещение.
Розжиг котлов должен начинаться:
1. при наличии пусковой топливной системы - топливом, не требующим подогрева;
2.при наличии пара и электроэнергии на судне - основным видом топлива.
Разводка огня и подъем пара в полностью автоматизированных агрегатах должен осуществляться автоматически по программе после проверки обслуживающих систем при установке органов управления и регуляторов в положение "автоматическая работа" в соответствии с инструкцией по эксплуатации.
Перед разводкой огня в котле, автоматический пуск которого не предусмотрен, все управляющие органы должны быть установлены в положение "ручное управление", а маховики и рукоятки регуляторов давления пара, питания котла, соотношения топливо-воздух - в положение полного закрытия. Все защитные и блокировочные устройства, не препятствующие пуску котла, должны быть включены.
Перед зажиганием форсунок топки должны быть осмотрены и в случае наличия скопившегося топлива последнее должно быть удалено; топку необходимо обязательно провентилировать в течение не менее 3 мин, открыв заслонки воздухонаправляющих устройств топочного фронта и включив котельные вентиляторы.
Зажигание первой форсунки производится электровоспламенителем или факелом. Последующие форсунки могут зажигаться от первой.
При зажигании форсунок факелом вначале к форсунке следует подвести факел, а затем открыть топливный клапан. Во время зажигания первой форсунки давление воздуха рекомендуется уменьшить. Котельный машинист во избежание ожога при выбросе пламени из топки должен находиться рядом с клапаном подачи топлива в стороне от окна, в которое вставляется факел.
Если зажигание форсунки не произошло, необходимо немедленно закрыть топливный клапан, обеспечить циркуляцию топлива, контролируя поддержание требуемой температуры; провентилировать топку в течение не менее 3 мин, после чего снова зажечь форсунку от факела. Категорически запрещается зажигать форсунку от раскаленной кирпичной кладки.
При разводке огня и подъеме пара температура и давление топлива, число, порядок включения и периодичность горения форсунок должны устанавливаться строго в соответствии с инструкцией по эксплуатации. При отсутствии инструкций зажигание форсунок должно производиться в водотрубных котлах - последовательно в соответствии с нумерацией горелок; в газотрубных или газоводотрубных котлах стремя или четырьмя топками - одновременно в двух крайних или в нижних топках; в двухтопочных котлах - в обоих топках одновременно.
При разводке огня необходимо тщательно следить за работой форсунок, не допуская подтекания топлива.
Подъем пара в котле следует производить по возможности медленно. Минимальная продолжительность подъема пара с момента зажигания огня в топке и до получения рабочего давления пара в котле не должна быть меньше указанной в инструкции по эксплуатации.
Обо всех случаях ускоренного подъема пара надлежит сделать запись в машинном журнале.
Во время подъема пара необходимо производить осмотр котла с целью обнаружения пропусков воды и пара. Обжатие крышек лазов, лючков, фланцев разрешается производить специальным инструментом в присутствии механика, в заведовании которого находится котел, при давлении пара не более 0.5 МПа (5 кгс/см2) без ударов или применения дополнительных рычагов. В случае неустойчивой работы форсунок необходимо прекратить розжиг и устранить неполадки.
При подъеме пара в котле необходимо последовательно производить следующие операции:
1. при появлении непрерывной струи пара из воздушного клапана закрыть его; полностью закрыть паровые клапаны на котле, за исключением клапанов, обеспечивающих проток пара через пароперегреватель;
2. в течение всего периода подъема пара следить за показаниями манометров, за уровнем воды в котле, а также продувать пароперегреватели согласно инструкции по эксплуатации;
3. при достижении давления, указанного в инструкции по эксплуатации (а при отсутствии указания - при достижении половины рабочего давления пара), подрывом вручную проверить действие предохранительных клапанов и надежную их посадку при закрытии. Если предохранительные клапаны не действуют, огонь в топках должен быть потушен, давление в котле снижено до атмосферного, после чего клапаны вскрыты для устранения дефектов;
4. котел сообщить с паропроводом на вспомогательные механизмы при открытом продувании пароперегревателя;
5. при необходимости опробовать в действии вспомогательные механизмы по достижении давления пара, достаточного для их пуска. При наличии расхода пара из котла пустить питательный насос или инжектор, подавая воду в котел черезводоподогреватель и регулируя питание вручную.
Подъем пара считается законченным по достижении в котле рабочего давления. При этом регулятор питания следует включить в работу на автоматическом режиме.
При включении средств автоматизации в случае неустойчивой работы необходимо удалить воздух из импульсных трубопроводов и полостей или устройств, заполняемых конденсатом, пополнить убыль конденсата. У регуляторов уровня после продувания импульсных трубопроводов до включения в работу необходима выдержка для самозаполнения их конденсатом.
После достижения рабочего давления пара в котле необходимо произвести верхнее продувание и проверку действия предохранительных клапанов, водоуказательных приборов, средств питания, пробных клапанов, клапанов нижнего продувания, защит котла.
|
|
Своеобразие русской архитектуры: Основной материал – дерево – быстрота постройки, но недолговечность и необходимость деления...
Типы оградительных сооружений в морском порту: По расположению оградительных сооружений в плане различают волноломы, обе оконечности...
Наброски и зарисовки растений, плодов, цветов: Освоить конструктивное построение структуры дерева через зарисовки отдельных деревьев, группы деревьев...
Эмиссия газов от очистных сооружений канализации: В последние годы внимание мирового сообщества сосредоточено на экологических проблемах...
© cyberpedia.su 2017-2024 - Не является автором материалов. Исключительное право сохранено за автором текста.
Если вы не хотите, чтобы данный материал был у нас на сайте, перейдите по ссылке: Нарушение авторских прав. Мы поможем в написании вашей работы!