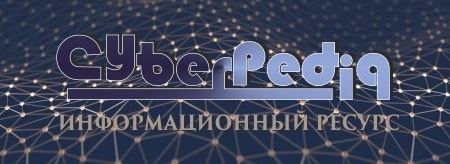
Кормораздатчик мобильный электрифицированный: схема и процесс работы устройства...
Поперечные профили набережных и береговой полосы: На городских территориях берегоукрепление проектируют с учетом технических и экономических требований, но особое значение придают эстетическим...
Топ:
Определение места расположения распределительного центра: Фирма реализует продукцию на рынках сбыта и имеет постоянных поставщиков в разных регионах. Увеличение объема продаж...
Теоретическая значимость работы: Описание теоретической значимости (ценности) результатов исследования должно присутствовать во введении...
Установка замедленного коксования: Чем выше температура и ниже давление, тем место разрыва углеродной цепи всё больше смещается к её концу и значительно возрастает...
Интересное:
Национальное богатство страны и его составляющие: для оценки элементов национального богатства используются...
Отражение на счетах бухгалтерского учета процесса приобретения: Процесс заготовления представляет систему экономических событий, включающих приобретение организацией у поставщиков сырья...
Берегоукрепление оползневых склонов: На прибрежных склонах основной причиной развития оползневых процессов является подмыв водами рек естественных склонов...
Дисциплины:
![]() |
![]() |
5.00
из
|
Заказать работу |
РАСЧЕТ И ПРОЕКТИРОВАНИЕ ВЕНТИЛЯЦИИ
Цель работы - ознакомиться со способами организации воздухообмена в производственных помещения, спроектировать и рассчитать систему метеорологических условий в производственных помещениях, освоить методику контроля параметров микроклимата с помощью контрольно- измерительных приборов и оценить их на основании ГОСТ12.1.005- 88
Расчет аэрации
Аэрацию максимально используют в горячих цехах (литейных, кузнечно-прессовых и др.) для отвода из помещений излишка выделяемой теплоты, уменьшения концентрации пыли газов и снижения энергопотребления системами вентиляции, Расчет аэрации (рис. 6) проводят без учета ветрового напора для летнего времени, как наиболее неблагоприятного для осуществления этого процесса. Сущность расчета состоит в определении площади приточных и вытяжных проемов.
Рис. 6. Схема к расчету аэрации: 1 – среднеподвесная приточная створка; 2 - верхнеподвесная приточная створка; 3 - верхнеподвесная вытяжная створка.
Сначала определяют требуемый воздухообмен, м3/ч, помещения, в воздух которого выделяются вредные вещества:
При расчете по избыткам теплоты количество воздуха L, м3/ч, поступающего через проемы в стенах и удаляемого через аэрационные фонари, рассчитывают по формуле:
где c – коэффициент, учитывающий высоту расположения центров приточных проемов от пола; kа – коэффициент, учитывающий температурный режим в помещении; Q – количество теплоты, выделяющейся в помещении, Вт; tв – температура воздуха в рабочей зоне, °С; tн – расчетная температура наружного воздуха, °С, принимаемая равной средней температуре в 13 ч самого жаркого месяца года; ty – температура удаляемого воздуха; a – градиент температуры по высоте помещения: для помещений с удельным количеством выделяемой теплоты a = 0,5° С/м; hв – расстояние от пола до оси вытяжных проемов. Как правило, принимают hв = 4,5 м. Коэффициент c принимают из следующих значений: Расстояние от пола до оси проёма, м
c 04,1,2,3,5
Коэффициент ka можно также определить в зависимости от значений отношения f / F (здесь f – площадь, занимаемая выделяющим теплоту оборудованием, F – площадь цеха):
F f 0,1 0,2 0,3 0, 4 0, 5 0, 6
kа 0,25 0,45 0,62 0, 68 0, 83 0, 87
По полученному значению воздухообмена L вычисляют площадь приточных вытяжных проемов.
Задание:
Исходными данными для расчета являются следующие величины:
- фактор направленности Ф= 2;
- пространственный угол Ω= 4π= 12,56 ср;
- производительность вентилятора;
- полное давление;
- критерий шумности вентилятора;
- расстояние от источника шума до расчетной точки определить самостоятельно
Контрольные вопросы
1. Какие существуют системы вентиляции по способу побуждения движения воздуха?
2. Под действием какого напора осуществляется вентилирование помещений в системах естественной вентиляции?
3. Какие помещения оборудуются системами вытяжной вентиляции?
4. С какой целью проектируют специальные вентилируемые кабины?
5. В чем состоит расчет аэрации?
6. Назначение, устройство и принцип действия дефлектора.
7. Назначение, виды и область применения местной системы вентиляции.
Задание: Рассчитать систему вентиляции и отопления в животноводческом помещении, а так же выбрать марку вентиляторов и их количество для обеспечения микроклимата.
Конструкция коровников на 250 голов, размером 100х30м, с беспривязной системой содержания локтирующих коров с удоем 10л. до 600кг. Высота стен X метра, высота от пола до конька L метра, F окон, размером 1500х2000, с двойным переплетом расстояние между стеклами S см, две наружных одинарных двери 3000х2500мм. Стены из сплошной кладки кирпича на легком растворе толщиной 40см с температурным балансом tвн = Z0 С и tнар = Y0 С.
Высота стен | 3,5 | 4,5 | 4,5 | 3,5 | 4,5 | |||||
высота от пола до конька | 4,2 | 4,4 | 3,8 | 3,9 | 4,4 | 4,2 | 3,8 | |||
Ко-во окон | ||||||||||
расстояние между стеклами | ||||||||||
tвн | +5 | +4,5 | +3 | +5 | +5,5 | +5 | +4,5 | +3 | +5 | +5,5 |
tнар | -5 | -5 | -5 | -5 | -5 | -5 | -5 | -5 | -5 | -5 |
2.Р АСЧЕТ И ПРОЕКТИРОВАНИЕ СООРУЖЕНИЙ МЕХАНИЧЕСКОЙ ОЧИСТКИ ПЫЛЕГАЗОВЫХ ВЫБРОСОВ
Цель – состоит в получении студентами теоретических знаний и практических навыков в области проектирования систем обеспечения экологической безопасности.
В сухих инерционных пылеуловителях для очистки газов от пыли используют гравитационные, инерционные и центробежные силы. Под действием гравитационных сил пыль осаждается в пылеосадочных камерах и коллекторах. В инерционных пылеуловителях пыль улавливается из газа за счет инерционных сил, возникающих в процессе движения частиц с определенной скоростью в газовом потоке. При изменении направления движения газа пыль по инерции двигается в первоначальном направлении и в результате этого выделяется из газового потока. Для изменения направления движения газа в аппаратах устанавливают жалюзи, перегородки и другие устройства. Инерционные силы для очистки газа используют в жалюзийных пылеотделительных и инерционных пылеуловителях (пылевых мешках).
В центробежных аппаратах (циклоны, батарейные циклоны, аппараты машинного типа) очистка газа от пыли осуществляется за счет центробежной силы, развивающейся при вращательном движении запыленного газа и действующей на частицы пыли. Ввиду того, что центробежная сила во много раз больше инерционной для одних и тех же условий, в центробежных аппаратах газ очищается более эффективно, чем в инерционных аппаратах.
Пылеосадочные камеры и коллекторы
Если запыленный газ, движущийся с определенной скоростью по газоходу, ввести в камеру, имеющую площадь поперечного сечения значительно большую, чем площадь газохода, то в этой камере скорость газа резко уменьшается. В этих условиях содержащаяся в газе пыль выпадает из него под действием гравитационных сил (сил тяжести). Такие камеры называют пылеосадочными. Условия осаждения пыли в них должны быть такими, чтобы частицы пыли успели осесть на дно камеры раньше, чем газ выйдет из нее.
Если ранее пылеосадочные камеры (рис. 2.1, а) использовались довольно широко для предварительной очистка газов от крупной пыли, то
![]() |
сейчас их применение весьма ограниченно по следующим причинам: большие размеры (их длина может достигать нескольких десятков метров); установленные на камерах люки (для очистки и удаления осевшей пыли), а также во многих случаях недостаточная плотность стен камер приводят к большому подсосу атмосферного воздуха в камеры. Их применяют в основном там, где по условиям производственного процесса необходимо разделение уловленной из газа пыли на крупные и мелкие фракции. Наиболее полно в пылеосадочных камерах осаждаются частицы размером более 40 мкм, поэтому их используют в качестве первой ступени перед аппаратами, предназначенными для очистки газа от мелкодисперсной пыли.
Конструктивные и эксплуатационные характеристики камер и коллекторов
Пыль из газового потока осаждается медленно, поэтому размеры камеры, в частности ее площадь, в процессе расчета получаются большими. Для уменьшения размеров камеры в ней устанавливают горизонтальные полки, разделяющие ее на ряд небольших камер, в которые газ попадает параллельно по ходу своего движения (рис. 2.1, б). Для уменьшения скорости движения пыли вдоль камеры в ней устанавливают вертикальные перегородки (рис. 2.1, в). Газ в процессе движения огибает перегородки; пыль, ударяясь о них, теряет скорость и падает на дно.
Осевшую на полках пыль удаляют вручную. Эта операция трудоемка, поэтому полки в камерах выполняют наклонными. По мере накопления пыли на полках их поворачивают при помощи лебедок, соединенных с полками тросами, и устанавливают вертикально. При этом пыль ссыпается в бункер и удаляется из него шнековым механизмом. При необходимости непрерывной очистки газа пылеосадочные камеры разделяют на две параллельные секции, из которых одна находится в работе, а другая в это время очищается от пыли. Выполняют камеры обычно из кирпича, бетона или металла.
Скорость газа в простых камерах и камерах с вертикальными перегородками 0,2-0,8 м/с, а в камерах с горизонтальными или наклонными полками - до 3 м/с.
Основы расчета пылеосадочных камер
При приближенном расчете осадительных камер принимают, что частицы движутся вдоль камеры (рис. 2.2) со скоростью равной скорости газового потока wп, и одновременно опускаются вниз со скоростью,
Рис. 2.2. Схема пылеосадочной камеры
равной скорости витания wB. Для осаждения частица должна достичь дна раньше, чем газовый поток вынесет ее из камеры, поэтому время осаждения частицы t = Н/w в не должно превышать времени ее пребывания в камере t= L/wг:
Н/wв < L/wr
Выражая скорость газа через расход Vг, деленный на площадь поперечного сечения камеры НВ, получим Н/wв = LHB/Vг откуда следует, что
Vг = LВ wв = LB(d2pчg/18µ).
Из этой формулы находят предельное количество газа, которое можно пропустить через камеру при условии осаждения частиц диаметром d. Решая обратную задачу, можно найти диаметр частиц, которые будут осаждаться при расходе газа Vг:
Жалюзийные пылеуловители.
Инерционные пылеуловители
Жалюзийные пылеуловители просты в конструкции, имеют небольшие габариты, однако малоэффективны и пригодны для улавливания только грубых фракций пыли (гч > 20 мкм).
Жалюзийный пылеуловитель (рис. 2.3, г) состоит из двух частей: жалюзийной решетки, где пыль отделяется от газа, и аппарата, предназначенного для улавливания пыли (чаще - циклона). Жалюзийная решетка может быть выполнена из пластин, уголков или конусов колец. В основе работы жалюзийного пылеуловителя лежит инерционно-отражательный принцип. С одной стороны частицы пыли выпадают из потока газа за счет сил инерции при крутом повороте газа в жалюзийной решетке, которая может быть выполнена из пластин, уголков или конусов колец, а с другой - отражаются при непосредственном ударе о пластину. Большая часть газа (80-90 %) огибает установленные под углом пластины, резко меняя направление своего движения, освобождается от пыли и продолжает свое движение по газопроводу в первоначальном направлении. Меньшая часть газа (10-20 %), обогащенная пылью, отводится из газохода в циклон и после очистки присоединяется к газу, прошедшему через жалюзийную решетку.
![]() |
Для эффективной очистки скорость газа при прохождении через пылеуловитель должна составлять 12-20 м/с. Чем меньше размеры частиц и их плотность, тем большая скорость газа должна быть перед жалюзийной решеткой.
Общая эффективность очистки газа в жалюзийном пылеуловителе определяется произведением коэффициентов очистки решетки пр и циклона ƞц:
ƞр·ƞц.
Ввиду того что эффективность этих аппаратов невелика и срок их службы мал (быстрый износ рабочих элементов в результате ударов о них крупных частиц пыли), в последние годы эти пылеуловители используют мало и заменяют более эффективными аппаратами. Однако для очистки дымовых газов от золы крупных размеров в некоторых случаях в системах вентиляции, а также когда установка других аппаратов невозможна из-за отсутствия площади жалюзийные пылеуловители продолжают эксплуатировать.
Инерционные пылеуловители (рис. 2.3, в) используют для выделения из газа крупных (размером 25-30 мкм) и тяжелых частиц пыли перед аппаратами тонкой очистки.
Простейшее устройство - сухой инерционный пылеуловитель с изменением направления потока газа на 90 или 180°, который встраивают в газоход. Рост гидравлических потерь при этом незначителен, соответственно эффективность такого аппарата низка.
Более эффективны пылеуловители других типов. Так, в аппарате, представленном на рис. 2.3, а, б, частицы пыли отделяются от газа при ударе о перегородку и во время огибания ее газом. В первом случае частицы теряют скорость и падают в бункер под действием гравитационных сил, а во втором - за счет инерционных сил. Очистка газа в пылеуловителе с центрально расположенной трубой осуществляется за счет инерционных сил. Диффузорный насадок на конце трубы уменьшает скорость газа на выходе из нее, т.е. снижает силу удара газа о бункер. В пылеуловителе с вводом газа через боковую трубу (рис. 2.4, а) пыль по инерции отделяется от газа при его повороте после входа в аппарат.
В перечисленных пылеуловителях скорость газа в цилиндрической части корпуса принимают равной 1 м/с, а во входной трубе - 10 м/с; степень улавливания колошниковой пыли (более 90 % - крупнее 20 мкм) достигает 65-85 %. Повышение скорости сверх 1 м/с приводит к ухудшению очистки, а ее понижение - к неоправданному увеличению габаритов аппарата без заметного повышения эффективности. Диаметры таких пылеуловителей - 10 м и более. Высота аппарата примерно равна или немногим больше его диаметра. Гидравлическое сопротивление устройств такого типа 150-400 Па.
Сухие центробежные циклоны. Принцип действия.
Основные типы циклонов. Батарейные циклоны и их эксплуатация. Расчет циклона
Сухие центробежные циклоны
Этот способ разделения неоднородных пылегазовых смесей более эффективен, чем гравитационное осаждение, поэтому он применяется для отделения более мелких (до 50 мкм) частиц пыли.
При аппаратурном оформлении процессов разделения неоднородных систем в центробежном поле применяют два принципа: вращение пылегазового потока в неподвижном аппарате (циклон); движение пылегазового потока во вращающемся роторе (центробежной ротационный пылеуловитель).
В обоих случаях на разделение, кроме сил тяжести и центробежных сил, значительное влияние оказывают инерционные силы.
Циклонные аппараты наиболее распространены в промышленности.
Вопросы для самоконтроля
1. Какой механизм осаждения наблюдается в пылеосадочной камере?
2. Какие параметры влияют на эффективность осаждения в пылеосадочной камере?
3. Как устроены и работают пылеуловители инерционного типа?
4. От каких факторов зависит степень очистки газа в циклоне?
5. Типы циклонов и основные правила их эксплуатации.
6. Определение гидравлического сопротивления циклона.
7. Батарейные циклоны. Их преимущества и недостатки.
2.2. О СНОВНЫЕ МЕТОДЫ УЛАВЛИВАНИЯ ПЫЛЕЙ: СУХИЕ
МЕХАНИЧЕСКИЕ ПЫЛЕУЛОВИТЕЛИ; «МОКРАЯ» ОЧИСТКА ГАЗОВ;
ФИЛЬТРОВАНИЕ; ОЧИСТКА В ЭЛЕКТРИЧЕСКОМ ПОЛЕ.
А ППАРАТУРА И РАБОЧИЕ ПАРАМЕТРЫ ПРОЦЕССА УЛАВЛИВАНИЯ ПЫЛЕЙ. С ПОСОБЫ ИНТЕНСИФИК АЦИ И РАБОТЫ ГАЗООЧИСТНЫХ УСТАНОВОК.
Р ЕКУПЕРАЦИЯ ПЫЛЕЙ. Э КОНОМИЧЕСКИЕ АСПЕКТЫ
ПЫЛЕУЛАВЛИВАНИЯ
По системе регенерации
В промышленных фильтрах регенерацию проводят по двум основным принципам:
— изменение направления хода газа через фильтровальный материал обратная продувка, во время которой происходит выдувание уловленной пыли из рукавов;
— разрушение пылевого слоя на фильтровальном материале его деформацией различными способами - встряхиванием рукавов с использованием специальных механизмов, воздействием на ткань аэродинамических сил извуковых импульсов.
Кроме того, существуют еще два способа регенерации:
а) фильтры с посекционной системой регенерации, когда регенерации подвергается целая секция многосекционного фильтра, во время которой подачу газа отключают;
б) в фильтрах с поэлементной системой регенерации обратной продувке подвергают последовательно отдельные фильтрующие элементы или их группы.
Конструктивное исполнение фильтров этой группы сложнее, чем у первой, из-за введения каркасных элементов и устройства сложных подвижных систем.
Однако они имеют и свои преимущества, а именно: более интенсивную регенерацию и меньшую ее продолжительность; регенерация ткани осуществляют без отключения подачи газа в фильтр. По типу устройств регенерации
Фильтры с посекционной регенерацией выполняют двух основных типов:
— с обратной продувкой;
— с комбинированной регенерацией (продувка и встряхивание).
Для небольших фильтров применяют только встряхивание. Фильтры с поэлементной регенерацией бывают:
— с импульсной регенерацией;
— с обратной продувкой через подвижное сопло;
— с обратной струйной продувкой.
Осаждение пыли на твердых элементах фильтра называют стационарной фильтрацией, а очистку газа в слое пыли, уже осевшей в порах фильтра, нестационарной.
Стационарная фильтрация осуществляется в фильтрах, работающих при очень низких концентрациях аэрозолей. Нестационарная фильтрация, по существу, проходит во всех случаях очистки газов.
При стационарной фильтрации гидравлическое сопротивление и эффективность очистки газов не изменяются во времени и по величине определяются только структурой фильтровального материала, характеристиками пыли и параметрами газа. При нестационарной фильтрации и сопротивление фильтра, и эффективность очистки возрастают по мере накопления пыли в фильтровальном материале.
Эффективность очистки газа в тканевых и пористых фильтрах определяется взаимодействием взвешенных в газе частиц с отдельными элементами фильтра и зависит от характеристик частиц пыли и элементов фильтрующего материала, параметров газа и скорости фильтрации.
Поскольку все факторы, влияющие на эффективность, трудно учесть, то ее определяют опытным путем, однако в ходе экспериментов установлено, что влияют они на этот показатель следующим образом:
1) чем крупнее частицы пыли и больше их плотность, тем эффективнее они осаждаются под действием сил инерции и гравитационных сил;
2) частицы размером менее 0,3 мкм осаждаются на твердых элементах пористого материала в основном только под действием теплового движения газовых молекул;
3) чем больше размеры твердых элементов пористого материала, тем выше эффективность осаждения частиц пыли;
4) чем меньше размер пор фильтра, тем более эффективно происходит осаждение пыли, так как при малом расстоянии между твердыми элементами линии тока запыленного газа будут проходить на более близком расстоянии от этих элементов. Но при этом гидравлическое сопротивление возрастает гораздо быстрее, чем эффективность улавливания частиц пыли;
5) с повышением температуры газа повышается его вязкость. Поэтому осаждение на фильтровальной поверхности крупных частиц под действием сил инерции снижается, а эффективность осаждения мелких частиц под действием теплового движения газовых молекул увеличивается. Гидравлическое сопротивление фильтровального материала с повышением температуры газа возрастает;
6) с повышением скорости фильтрации инерционное осаждение крупных частиц возрастает, а осаждение под действием теплового движения газовых молекул уменьшается. Однако при большой скорости фильтрации возможны отрыв уже осевших частиц и унос вместе с газовым потоком;
7) чем больше поверхность фильтра, тем выше эффективность очистки;
8) с увеличением слоя пыли на фильтровальном материале эффективность улавливания пыли возрастает, однако при этом повышается гидравлическое сопротивление, при большом значении которого фильтрация газа может практически прекратиться.
Для создания требуемой скорости фильтрации по обе стороны фильтра необходимо поддерживать соответствующий перепад давлений. Величину этого перепада определяет расход энергии вентилятора или дымососа и поэтому является важной конструктивной и эксплуатационной характеристикой.
Скорость фильтрации в большинстве фильтров невелика, и процесс фильтрации происходит при ламинарном режиме движения газа.
Сопротивление фильтра пропорционально скорости газа, его вязкости и толщине слоя фильтра и зависит от структуры фильтровального материала и других факторов. Оно может быть представлено как сумма сопротивлений собственно пористого фильтрующего слоя и слоя осевшей пыли.
Эксплуатационные характеристики фильтров в значительной мере определяются их пылеемкостью (это количество пыли, которое фильтр способен удержать при непрерывной работе между периодами регенерации или смены фильтровального материала, г/м2 или мг/м2). Этот параметр зависит от размера пыли и минимален при улавливании мелких частиц. На рис. 2.5 представлены аппараты с различными фильтрующими материалами.
Требования к ним. Расчет тканевого фильтра
Классификация промышленных фильтров. В этих фильтрах фильтровальный слой выполнен в виде рукавов (тогда фильтры называют рукавными) или с плоской разверткой ткани.
Тканевые рукавные фильтры с высокой эффективностью применяют при очистке технологических и вентиляционных газов промышленных предприятий и гражданских объектов от частиц пыли размером более 0,1 мкм. Рассмотрим принцип действия такого фильтра.
Запыленный газ через входной патрубок поступает в бункер. Входной патрубок обычно располагают в верхней части бункера, но в некоторых случаях газ вводят в фильтр через патрубок, расположенный в его
Рис. 2.5. Фильтры: а - волокнистые; б - тканевые; в - зернистые; г - керамические
боковой части. В бункере газ разворачивается, в результате чего выпадают наиболее крупные частицы пыли, и входит в рукава, насаженные на патрубки, которые установлены на дырчатом листе. Число отверстий с патрубками в листе равно числу рукавов. Верхняя часть рукавов заглушена, они подвешены к раме, соединенной стержнем с механизмом встряхивания. Запыленный газ проходит через ткань рукавов и оставляет на их внутренней поверхности пыль. Очищенный от пыли газ поступает в корпус фильтра, откуда выводится через патрубок чистого газа. Осевшую в рукавах пыль удаляют при помощи механизма встряхивания и одновременно обратной продувкой рукавов. Для этого через патрубок, установленный в верхней части корпуса, подается воздух при помощи вентилятора, встроенного в рукавный фильтр или установленного вне его. Продувочный воздух проходит через ткань рукавов в направлении, обратном движению газа, и ломает корку пыли, осевшую на внутренней поверхности рукавов.
Включение механизма встряхивания и вентилятора обратной продувки осуществляется автоматически по мере достижения заданного гидравлического сопротивления фильтровальных рукавов. В период удаления пыли из рукавов в фильтр или его секцию прекращается подача газа, и фильтр отключается от коллектора чистого газа при помощи дроссель-клапана. При регенерации рукавов разрушается и удаляется из них только часть слоя пыли, в результате чего уменьшается сопротивление оставшегося слоя.
Пыль из рукавов ссыпается в бункер и при помощи шнека выводится через пылевыпускной патрубок, на котором установлен герметический затвор. Обычно фильтры выполняют с двумя и более секциями. Рукава очищают в каждой секции по очереди, в остальных в это время очищают газ.
Входные и выходные патрубки каждой секции соответственно объединяют общими коллекторами запыленного и чистого газов. Продувочный воздух через коллектор запыленного газа поступает на очистку в рабочие секции фильтра. В зависимости от конструкции фильтра количество продувочного воздуха составляет 1,5—1,8 м3/(м2 мин), а давление 1275-1470 Па.
Включение механизма встряхивания и вентилятора обратной продувки осуществляется автоматически по мере достижения заданного гидравлического сопротивления фильтровальных рукавов.
Кроме механического вибрационного встряхивания и обратной продувки удаление пыли из рукавов осуществляют кручением рукавов, аэродинамическим встряхиванием и звуковой регенерацией. При аэродинамическом встряхивании очистка рукавов происходит в результате пульсирующей подачи газа или воздуха между рукавами или подачи импульса сжатого воздуха внутрь каждого рукава при избыточном давлении сжатого воздуха 0,4-0,8 МПа и частоте импульсов 0,1-0,2 с. Расход продувочного воздуха составляет 0,1-0,4 % от количества очищаемых газов.
В этом случае отпадает необходимость в механизации операции встряхивания. Однако такой метод не обеспечивает равномерной регенерации рукавов в фильтре, так как вблизи сопел рукава очищаются слишком интенсивно, а на некотором расстоянии от них - недостаточно. Этот метод регенерации применяют при очистке газов от крупной пыли.
Фильтровальные ткани выбирают в зависимости от характеристик газа и содержащейся в нем пыли, температуры газов, стойкости против воздействия кислот, щелочей, света влаги, а также структуры пыли.
К тканям предъявляют следующие требования:
— обеспечение высокой пылеемкости при фильтрации;
— способность удерживать на своей поверхности такое количество пыли, которое обеспечивает высокую эффективность очистки газа от мелкодисперсной пыли;
— высокая механическая прочность при многократных изгибах;
— стойкость к истиранию;
— способность к легкому удалению пыли с поверхности ткани.
Фильтровальные ткани могут быть ткаными и неткаными.
По характеристике поверхности ткани могут быть гладкими и ворсистыми. К первым относятся хлопчатобумажные ткани, лавсан, стекловолокно; они используются для очистки газа от волокнистой и зернистой пыли.
К ворсистым тканям относятся суконные и шерстяные ткани, нитрон, капрон с шерстью; их применяют для очистки только от зернистой пыли, так как волокнистая пыль сцепляется с ворсом ткани и плохо удаляется при регенерации. Ворсистую ткань располагаю ворсом внутрь рукава в сторону входа запыленного газа.
Хлопчатобумажные ткани и шерсть относятся к природным материалам. Хлопчатобумажные ткани обладают хорошими фильтрующими свойствами; для повышения стойкости к кислотам их подвергают специальной обработке. Но их применяют при температуре газов не выше 85 °С.
Шерстяные ткани также обеспечивают надежную очистку газа и обладают значительно большим сроком службы, чем хлопчатобумажные (9-12 мес.). Температура газового потока - не выше 100 °С.
Ткани из синтетических волокон более стойки к воздействию высоких температур и агрессивных компонентов. Для повышения сопротивляемости таких материалов механическим воздействиям и истиранию их подвергают термической обработке. Так, рукава из силиконизированного стекловолокна или из многослойных тканей могут работать при температуре выше 300 °С и обладают повышенной прочностью. Металлоткани обладают хорошей мехнической прочностью, высокой химической стойкостью и газопроницаемостью, удовлетворительной пылеемкостью в процессе фильтрации при высоких температурах. Для очистки газа, имеющего температуру до 600 °С, применяют фильтровальные ткани из иглопробивных фетров, которые выполнены из металлических волокон. Асбестовые ткани используют для очистки газов при температурах до 500 °С. Если температура газов достигает 900 °С применяют фильтровальные элементы с развернутой поверхностью из керамики.
В тканевых фильтрах из хлопчатобумажных и шерстяных тканей не допускается очистка влажных газов, так как влажная пыль может образовывать в порах ткани газонепроницаемую корку. При низких температурах возможна конденсация из газа водяных паров, которые также осаждаются на ткани. Для исключения конденсации необходимо, чтобы температура очищаемых газов была на 15-20 °С больше температуры точки росы. Поэтому при низкой температуре газов их специально подогревают перед вводом в фильтр, а корпус фильтра термоизолируют. При высокой температуре газов их специально охлаждают.
Рукавные фильтры в зависимости от конструкции могут работать под разрежением или под избыточным давлением. В первом случае вентилятор устанавливают за фильтром по ходу движения газа, который просасывается через фильтр. Во втором случае подлежащий очистке газ нагнетают в фильтр вентилятором, стоящим до фильтра. Всасывающие фильтры, работающие под разрежением, должны быть герметичными.
По форме корпуса рукавные фильтры могут быть прямоугольными и реже круглыми или овальными.
Тканевый фильтровальный материал используется также в фильтрах с плоской разверсткой ткани, которую натягивают на проволочный каркас. Фильтрующие элементы в таких фильтрах имеют прямоугольную и реже клиновидную форму, которая обеспечивает большую поверхность фильтрации, чем в рукавных. Однако в них труднее удаляется пыль, сложнее сменяется фильтрующий слой и служит он по времени меньше.
При эксплуатации рукавных фильтров требуется соблюдать правила техники безопасности, которые исключают возможность воспламенения горючей пыли и отравления обслуживающего персонала при очистке токсичных газов.
В необходимых случаях следует применять фильтры и вентиляторы во взрывобезопасном исполнении и осуществлять очистку газов только под разрежением; своевременно удалять пыль из фильтра; устранять источники возникновения искр и статических зарядов; исключать возможность образования взрывоопасных смесей газа и пыли с атмосферным воздухом.
Расчетрукавного фильтра
1. Учитывая допустимую температуру газа для ткани лавсан, равную 130 °С, определяем подсос воздуха с температурой 30 °С, необходимый для охлаждения газа с заданной температурой до tг = 130 °С. Используем балансовое уравнение:
где ,
,
, - температуры смеси, газа и воздуха, °С; V0г.,
- объемы газа и воздуха при нормальных условиях, м /ч; Ссм, Сг, Св - теплоемкости смеси, газа и воздуха, Дж/(м3 К).
Принимаем Ссм = Сг = Св тогда
2. Расход газа, идущего на фильтрование, при нормальных условиях, м3/ч
3. Запыленность газа перед фильтром в рабочих условиях, г/м3,
4. Допустимая удельная газовая нагрузка на фильтр, м3/(м2мин),
где = 1,2 м3/(м2мин) - для черных и цветных металлов; коэффициенты: С1 = 0,7 - для регенерации с обратной продувкой; С2 = 1,04 - при начальной рабочей запыленности Z1 = 7,9 г/м; С3 = 0,9 - при dm = 3 мкм; С4 = 0,725 - при tr = 130 °С; С5 = 1 - при остаточной концентрации пыли более 30 мг/м. Скорость фильтрации, м/с,
Wф= q ф /60.
5. Полное гидравлическое сопротивление фильтра ∆Р, Па, складывается из сопротивления корпуса ∆Рк и сопротивления фильтровальной перегородки ∆Рф:
∆Р = ∆Рк + ∆Рф.
Гидравлическое сопротивление корпуса фильтра, Па,
где Wвx - принимаемая скорость газа при входе в фильтр, м/с, равная 10; -задаваемый средний коэффициент сопротивления при Wвx = 5-15 м/с, равный 2; рг - плотность газа при рабочих условиях, кг/м:
Гидравлическое сопротивление фильтровальной перегородки при заданном ∆Р
6. Продолжительность периода фильтрования между двумя регенерациями
Коэффициенты А и В выбираются по нижеприведенным данным в зависимости от среднемедианного размера частиц и вида пыли:
dm, мкм | А, м 1 | В, м/кг | Вид пыли |
10-20 | (1100-1500)106 | (6,5-16) 109 | Кварцевая Цементная |
2,5-3 | (2300-2400) 106 | 80-109 | Сталеплавильная |
0,5-0,7 | (13000-15000) 106 | 330-109 | Кремниевая |
Динамический коэффициент вязкости газа при рабочих условиях, Пас,
7. Количество регенераций в течение 1 ч
8. Расход воздуха на регенерацию (скорость обратной продувки равна скорости фильтрования), м3/ч,
9. Необходимая фильтровальная площадь, м2,
10. Тип рукавного фильтра выбирается из справочников.
11. Площадь фильтрования Fp, отключаемая на регенерацию в течение 1 ч, м2,
12. Уточненное количество воздуха, расходуемое на обратную продувку в течение 1 ч, м,
13. Окончательная уточненная площадь фильтрования, м2,
14. Продолжительность периода фильтрования должна быть выше суммарного времени регенерации остальных секций, с,
15. Фактическая удельная газовая нагрузка
Рулонные фильтры.
Вопросы для самоконтроля
1. Механизмы процесса фильтрования.
2. По каким конструктивным признакам классифицируют промышленные фильтры?
3. Как устроены и работают тканевые фильтры?
4. Какие фильтровальные материалы применяют в тканевых фильтрах?
5. Какие требования предъявляют к фильтровальным тканям?
6. Какие способы регенерации ткани применяют в тканевых фильтрах?
7. Как определяют гидравлическое сопротивление тканевого фильтра?
8. Зернистые фильтры, их преимущества и недостатки, области применения.
9. Кассетные и рамочные фильтры, их преимущества и недостатки, области применения.
10. Рулонные фильтры, их преимущества и недостатки, области применения.
11. Масляные фильтры, их преимущества и недостатки, области применения.
Задание: Система аспирации шахтной мельницы удаляет V м3/ч воздуха, имеющего температуру t °С и загрязненного пылью известняка. Рассчитать параметры циклона серии ЦН-15, обеспечивающего очистку воздуха от пыли.
Обьем удаляемого воздуха | ||||||||||
температура |
((__lxGc__=window.__lxGc__||{'s':{},'b':0})['s']['_228268']=__lxGc__['s']['_228268']||{'b':{}})['b']['_697691']={'i':__lxGc__.b++};
![]() История развития хранилищ для нефти: Первые склады нефти появились в XVII веке. Они представляли собой землянные ямы-амбара глубиной 4…5 м... ![]() Папиллярные узоры пальцев рук - маркер спортивных способностей: дерматоглифические признаки формируются на 3-5 месяце беременности, не изменяются в течение жизни... ![]() Индивидуальные очистные сооружения: К классу индивидуальных очистных сооружений относят сооружения, пропускная способность которых... ![]() Биохимия спиртового брожения: Основу технологии получения пива составляет спиртовое брожение, - при котором сахар превращается... © cyberpedia.su 2017-2024 - Не является автором материалов. Исключительное право сохранено за автором текста. |