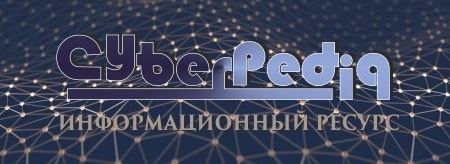
История создания датчика движения: Первый прибор для обнаружения движения был изобретен немецким физиком Генрихом Герцем...
Двойное оплодотворение у цветковых растений: Оплодотворение - это процесс слияния мужской и женской половых клеток с образованием зиготы...
Топ:
Комплексной системы оценки состояния охраны труда на производственном объекте (КСОТ-П): Цели и задачи Комплексной системы оценки состояния охраны труда и определению факторов рисков по охране труда...
Генеалогическое древо Султанов Османской империи: Османские правители, вначале, будучи еще бейлербеями Анатолии, женились на дочерях византийских императоров...
Интересное:
Национальное богатство страны и его составляющие: для оценки элементов национального богатства используются...
Финансовый рынок и его значение в управлении денежными потоками на современном этапе: любому предприятию для расширения производства и увеличения прибыли нужны...
Подходы к решению темы фильма: Существует три основных типа исторического фильма, имеющих между собой много общего...
Дисциплины:
![]() |
![]() |
5.00
из
|
Заказать работу |
|
|
3. Схематические изображения рассмотренных микроструктур сталей, а также серого литейного, ковкого и высокопрочного чугуна.
4. Краткий анализ полученных результатов.
Контрольные вопросы
1. Какие фазы входят в состав железоуглеродистых сплавов?
2. Какие превращения происходят в сталях различного состава при охлаждении из жидкого состояния?
3. На каких линиях диаграммы состояния сплавов начинается выделение Ц при охлаждении?
4. Какие линии диаграммы состояния соответствуют началу выделения Ф при охлаждении?
5. Какие процессы, происходящие в сплавах, связаны с перестройкой решетки у железа?
6. Как и почему форма графитных включений влияет на механические свойства чугунов?
Литература
1. Сидорин И.И. Основы материаловедения. - М.: Машиностроение, 1976, гл. IV.
2. Арзамасов Б.Н. Материаловедение. - М.: Машиностроение, 1986, гл.3.
3. Солнцев Ю.П. и др. Материаловедение. – М.: «МИСИС», 1999.
Часть 2. Закалка стали
Цель работы: исследовать влияние температуры нагрева под закалку на структуру и твердость стали.
Содержание работы
Закалка является основным методом упрочнения стали. Её существенное преимущество перед холодной обработкой давлением заключается в отсутствии значительного изменения формы деталей и получении более высоких прочностных свойств. Для изучения процесса закалки необходимо знать диаграмму состояния Fe - Fe 3 C (см. «Железоуглеродистые сплавы в равновесном состоянии»). Физической предпосылкой значительного повышения твердости при закалке стали является различная растворимость углерода (C) в различных модификациях железа: в ОЦК решетке Fe a(феррите) растворяется не более 0,02% С, в ГЦК решетке Fe g(аустените) до 2% C.
|
Структурам, представленным на диаграмме равновесного состояния сплавов Fe - Fe 3 C соответствует такая скорость охлаждения, при которой успевают произойти основные процессы, развивающиеся в сплавах по мере их охлаждения. В результате при комнатной температуре сталь оказывается в энергетически стабильном состоянии и имеет структуру, состоящую из двух фаз: феррита (Ф) и цементита (Ц). Происходящая в процессе охлаждения из области аустенита (А) перестройка кристаллической решетки ГЦК на ОЦК практически не зависит от скорости охлаждения, так как при этом атомы железа смещаются на расстояние меньше межатомного. Протекающий в это же время диффузионный процесс выделения из твердого раствора C и формирования Ц (рис. 1а) требует высокой температуры и значительного времени, поэтому существенно зависит от скорости охлаждения.
Рис. 1. а) при медленном охлаждении образуется Ц;
б) при достаточно быстром охлаждении Ц не образуется
Если охлаждение стали из области А производить с такой скоростью, при которой не успевает произойти диффузия С, то весь С, растворенный в А, наследуется ОЦК решеткой Fe a, образуя пересыщенный твердый раствор С в Fe a- мартенсит (М) (рис.1б). Термическая обработка стали, в результате которой фиксируется энергетически неравновесная метастабильная структура - М, называется закалкой стали на М. Получающийся в процессе закалки М часто называют мартенситом закалки (Мз).
Минимальная скорость охлаждения стали, обеспечивающая образование Мз, называется критической скоростью закалки (V кр) (рис.2). Величина V кр уменьшается при увеличении концентрации С и большинства легирующих элементов.
Рис. 2.Участок диаграммы равновесного состояния сплавов Fe-Fe3C и схема изменения структуры эвтектоидной стали при изменении скорости охлаждения
Вследствие бездиффузионной, протекающей с высокой скоростью, кооперативной перестройки решетки возникают многочисленные пластические сдвиги с образованием двойников (повернутых относительно друг друга на определенный угол участков кристалла), границы которых являются эффективным препятствием для дислокаций. Кроме этого, значительно увеличивается плотность дислокаций, их взаимное торможение. Следовательно, повышаются прочностные свойств стали и снижаются пластические. Аналогичное изменение свойств кристаллических материалов, связанное с повышением плотности дислокаций, происходит в результате холодного пластического деформирования, вызванного действием внешних сил (см. «Деформационное упрочнение и рекристаллизация»). Избыточный углерод, находящийся в кристаллической решетке, сосредотачивается около дислокаций, закрепляя их, тем самым значительно увеличивая эффект упрочнения. Дополнительное повышение твердости высокоуглеродистых сталей обеспечивается частично успевающим происходить выделением очень мелких (высокодисперсных) карбидов.
|
Закалка стали приводит к изменению также и физико-химических свойств стали, но наиболее часто производится с целью упрочнения, степень которого зависит от концентрации С в М (рис.3).
Рис. 3. Зависимость твердости (НВ) мартенсита от содержания углерода
Различают полную и неполную закалки. Программа полной закалки предусматривает нагрев стали до однофазной области А с последующим охлаждением со скоростью больше V кр. Неполная закалка осуществляется со скоростью, также превышающей V кр, но из А+Ф или А+ЦIIобласти. Для доэвтектоидных сталей неполная закалка не обеспечивает максимального повышения твердости и поэтому не производится. Заэвтектоидная сталь, применяемая, как правило, в качестве инструментальной, подвергается неполной закалке, потому что ЦII, сохраняющийся в структуре, имеет большую, чем у М твердость, что способствует еще большему увеличению твердости закаленной стали.
Температура нагрева под закалку обычно выбирается не более чем на 30-50° С превышающей верхнюю температурную границу существования Ф (рис.2, заштрихованная область). Перегрев может привести к укрупнению кристаллов А, из которых образуется крупнопластинчатый М, обладающий повышенной хрупкостью.
В работе изучается влияние температуры нагрева под закалку на твердость закаленной стали. Исследование проводится на образцах стали 45 (0,45% С), каждый из которых в процессе закалки нагревают до определенной температуры. Скорость закалки выше критической обеспечивается охлаждением в воде. Твердость измеряется методом Роквелла.
|
Анализ результатов работы заключается в объяснении связи между режимом закалки, возникающей структурой и твердостью закаленной стали.
Оборудование и материалы
1. Образцы стали 45 в отожженном состоянии.
2. Малогабаритные печи.
3. Прибор для измерения твердости методом Роквелла.
Порядок выполнения работы
1. Измерить твердость образцов по Роквеллу (HRB) в исходном состоянии.
Материал | Состояние | Твердость НВ, МПа |
Сталь 45 | После отжига | |
После закалки | 650° С | |
750° С | ||
850° С |
2. Произвести нагрев образцов под закалку. Температуры нагрева: 650, 750, 850° С. Время выдержки - 10 мин.
3. Охладить образцы в воде.
4. Измерить твердость образцов по Роквеллу (HRB, HRC) в закаленном состоянии.
5. Перевести значения твердости по Роквеллу в единицы твердости по Бринеллю (НВ).
6. Внести все полученные значения твердости НВ в таблицу.
7. Построить графическую зависимость HB = f (T зак).
Содержание отчета
1. Цель работы.
2. Таблица с данными.
3. График зависимости НВ от Т зак.
4. Схематическое изображение структур стали 45, полученных при использованных режимах закалки.
5. Краткий анализ полученных результатов.
Контрольные вопросы
1. Какова роль полиморфизма Fe в процессе закалки стали?
2. Чем обусловлена высокая твердость мартенсита?
3. Каково влияние скорости охлаждения на структуру и свойства стали после закалки?
4. Каким образом изменяется структура и свойства стали в зависимости от температуры нагрева под закалку?
5. Какова оптимальная температура нагрева под закалку доэвтектоидной и заэвтектоидной стали?
Литература
1. Сидорин И.И. Основы материаловедения. - М.: Машиностроение, 1976, гл. IX, §§ I, 2.
2. Новиков И.И. Теория термической обработки. - М.: Металлургия, 1974, §§ 32, 34, 37.
3. Арзамасов Б.Н. Материаловедение - М.: Машиностроение, 1986, гл. 5.
|
4. Солнцев Ю.П. и др. Материаловедение. – М.: «МИСИС», 1999.
Часть 3. Отпуск стали
Цель работы: исследовать влияние изменения структуры в процессе отпуска на прочностные свойства закаленной стали.
Содержание работы
Мартенсит, получающийся в результате закалки (Мз), имеет высокую твердость, но очень низкую пластичность. Кроме этого значительным недостатком Мз является наличие больших остаточных растягивающих напряжений, вызывающих нестабильность размеров и формы стальных деталей.
Для придания закаленной стали оптимальной структуры и свойств, требуемых в различных условиях применения, проводится обязательная операция отпуска. Она заключается в нагреве стали, закаленной на Мз, до различных температур, но ниже температуры эвтектоидного превращения. Следует отметить, что при нагреве стали выше температуры эвтектоидного превращения и последующем, достаточно медленном, охлаждении (операция отжига) обеспечивается появление равновесной структуры, соответствующей диаграмме состояния железоуглеродистых сплавов.
Для успешного выполнения работы необходимо знать процесс закалки стали на Мз и изменения, происходящие в Мз при нагреве.
После закалки на Мз сталь находится в метастабильном состоянии. Нагрев ускоряет термоактивационные процессы, переводящие сталь в более равновесное состояние, при этом происходят превращения, изменяющие ее структуру и свойства. Управляя процессом отпуска, можно получить оптимальную структуру и свойства стали для разных условий применения. Так, режущий и измерительный инструмент, для изготовления которого используются инструментальные стали (0,7 – 1,3% С), должен обладать высокой твердостью, износостойкостью, а также размерной стабильностью. Для этого необходимо уменьшить остаточные напряжения, сохраняя высокую твердость закаленной стали. В данном случае проводится операция низкого отпуска (120-250° С), при котором происходит перераспределение С в Мз, уменьшающее упругие искажения кристаллической решетки, за счет чего снижаются остаточные напряжения до безопасного уровня. В результате формируется мартенсит отпуска (Мо) и выделяются сложные высокодисперсные карбиды железа. Структура и механические свойства стали при низком отпуске изменяются мало (рис.1, 2), но повышается стабильность размеров и формы изделий, а также уменьшается опасность самопроизвольного образования трещин.
При среднем отпуске (350-450° С) избыточный С покидает пересыщенный твердый раствор. В связи с этим Мз распадается с образованием мелких (высокодисперсных) частиц цементита (Ц), распределенных в феррите (Ф) - тростит (Т) (рис.1). Пластичность стали незначительно увеличивается из-за появления объемов, занятых Ф, перераспределения и некоторого снижения плотности дислокаций. Твердость, как правило, несколько снижается (рис.2). Дислокации тормозятся за счет взаимодействия друг с другом, а также с частицами Ц (см. «Дисперсионное упрочнение»). Средний отпуск чаще всего применяется для термической обработки упругих элементов, при изготовлении которых, как правило, используются рессорно-пружинные стали, содержащие 0,55 - 0,85% С.
|
При высоком отпуске (500-600° С) происходит дальнейшая термодинамическая стабилизация структуры, что выражается в округлении и укрупнении частиц Ц, причем их количество уменьшается (рис.1).
Рис. 1 Структура стали после отпуска
Образующаяся структура - сорбит (С) имеет еще более низкую плотность дислокаций, чем в Т. Прочностные свойства продолжают снижаться, а пластические - возрастать (рис. 2). Высокий отпуск после закалки (улучшающая термическая обработка) применяется для конструкционных сталей (0,30-0,55% С), обеспечивая оптимальный комплекс механических свойств (повышенная прочность при достаточной пластичности).
Рис. 2. 1 - относительное сужение(y);2 - твердость HB
В данной работе определяется влияние температуры отпуска на твердость закаленной стали. Исследования проводятся на трех закаленных образцах стали 45 (0,45% С). Эти образцы подвергаются отпуску при различных температурах. Охлаждение образцов проводится в воде. Твердость определяется методом Роквелла. Полученные значения твердости сравниваются с твердостью отожженного образца стали 45.
Анализ результатов работы сводится к объяснению связи между структурой стали, получаемой при различных режимах отпуска, и ее твердостью.
Оборудование и материалы
1. Образцы стали 45 в закаленном состоянии.
2. Один образец стали 45 в отожженном состоянии.
3. Малогабаритные печи.
4. Прибор для измерения твердости по Роквеллу.
Порядок выполнения работы
1. Измерить твердость образцов по Роквеллу в отожженном (HRB) и закаленном (HRC) состояниях.
2. Произвести отпуск каждого образца при определенной температуре; температуры отпуска - 200, 400, 600° С; время выдержки 10 минут, охлаждение в воде.
3. Измерить твердость (HRC) образцов в отпущенном состоянии.
4. Перевести полученные значения твердости в единицы твердости по Бринеллю (НВ).
5. Все значения твердости НВ внести в таблицу
Материал | Состояние | Твердость НВ, МПа |
Сталь 45 | После отжига | |
После закалки | ||
После отпуска | 200° С | |
400° С | ||
600° С |
6. Построить график зависимости НВ от температуры отпуска Т отп.
Содержание отчета
1. Цель работы.
2. Таблица с данными.
3. График зависимости НВ от Т отп.
4. Схематическое изображение структур отпущенной стали (рис. 1).
5. Краткий анализ полученных результатов.
Контрольные вопросы
1. В чем состоит цель отпуска стали?
2. С чем связано изменение структуры закаленной стали при отпуске?
3. Как изменяется структура и свойства закаленной стали после различных видов отпуска?
4. В чем отличия структуры и механических свойств отожженной и высокоотпущенной стали?
5. Для каких сталей (с учетом их назначения) предназначен низкий, средний и высокий отпуск?
Литература
1. Сидорин И.И. Основы материаловедения. - М.: Машиностроение, 1976, гл. ХI § 3.
2. Новиков И. И. Теория термической обработки. - М.: Металлургия, 1974, § 47, 48.
3. Новиков И.И. Дефекты кристаллической решетки металлов. - М.: Металлургия, 1975.
4. Арзамасов Б.Н. Материаловедение. - М.: Машиностроение, 1986, гл. 5.
5. Солнцев Ю.П. и др. Материаловедение. – М.: «МИСИС», 1999.
Часть 4. Дисперсионное упрочнение
Цель работы: исследовать влияние режимов дисперсионного упрочнения на формирующуюся структуру и прочностные свойства дюралюминия.
Содержание работы
При упрочняющей термической обработке, в процессе которой производится закалка с получением пересыщенного твердого раствора, может быть использовано не только полиморфное превращение (перестройка кристаллической решетки), но и характерное для многих сплавов изменение растворимости твердых растворов при изменении температуры. К таким сплавам относятся, в частности, сплавы на основе алюминия, меди, никеля, кобальта, железа, используемые на практике. Важно отметить, что упрочнение, в данном случае, возникает за счет мелких (дисперсных) частиц, выделяющихся в процессе распада пересыщенных твердых растворов.
Выполняя данную работу, следует помнить, что повышение прочностных свойств металлических материалов, как правило, связано с торможением дислокаций дефектами кристаллической структуры. Упрочнение, вызываемое мелкими (дисперсными) частицами химических соединений, называется дисперсионным. Степень торможения дислокаций при этом упрочнении зависит от эффективного размера частиц (d), расстояний между частицами (L) и равномерности распределения частиц. Естественно, что с увеличением числа частиц значения d и L уменьшаются (рис.1).
Рассмотрим три варианта системы частиц, равномерно размещенных в объеме твердого раствора:
1. Структура состоит из редких, крупных частиц, тогда Lmax и dmax (рис.1а). При этом дислокации могут легко пройти между частицами, не прорезая их (рис.2а). Для движения дислокации достаточно относительно небольшого напряжения
s min = (a· G · b)/ Lmax,
где G - модуль сдвига; b - вектор Бюргерса; a - константа порядка единицы.
Рис. 1. Распределение частиц в объеме сплава
2. Структура состоит из мелких, близко расположенных частиц (рис.1б), тогда dmin и Lmin. При этом дислокациям легче прорезать частицы за счет небольшого напряжения s min, чем обогнуть их (рис.2б).
Рис. 2. Прохождение дислокаций через систему частиц с разными параметрами
3. Структура имеет оптимальные значения параметров системы частиц, где dopt. и Lopt (рис.1в). В результате дислокациям одинаково трудно как прорезать, так и обогнуть частицы. При этом напряжение, необходимое для движения дислокации, наибольшее s max (рис. 2в).
Кроме этого следует обратить внимание на то, что когда частица мала, то на границе твердый раствор - частица кристаллическая решетка упруго искажена, но не прерывается, поэтому дислокация может, преодолевая искажение, пройти через частицу. По мере укрупнения частицы искажение решетки на границе нарастает, что приводит в конце концов к нарушению непрерывности кристаллической решетки, в результате чего дислокация уже не может прорезать частицу, а только огибает ее.
Таким образом, при дисперсионном упрочнении проблема состоит в получении оптимальных параметров системы частиц, обеспечивающих наибольшее упрочнение.
Дисперсионному упрочнению могут подвергаться сплавы - твердые растворы с ограниченной растворимостью, уменьшающейся при понижении температуры. Примером такого сплава может служить сплав на основе алюминия – дюралюминий марки Д1 (~4,3% Сu, ~0,6% Мg, ~0,6% Мn, ост. Al).
Рис. 3. Диаграмма состояния Al - Сu и схема процесса дисперсионного упрочнения сплава Д1
Согласно диаграмме состояния Al - Сu (рис.3а) при T = 20° С в отожженном состоянии (энергетически равновесном) дюралюминий состоит из кристаллов a - твердого раствора Сu в Al, содержащих ~ 0,1% Сu и частиц химического соединения CuAl 2(А на рис. 3б). В этом случае реализуется вариант с большими частицами (dmax) и большими расстояниями между ними (Lmax) как энергетически наиболее выгодный.
Для получения оптимальной структуры сначала необходимо избавиться от крупных частиц, содержащихся в отожженном сплаве. С этой целью производится закалка, включающая нагрев сплава до состояния однофазного твердого раствора (В на рис. 3б) и последующее охлаждение с такой скоростью, при которой не успевают произойти диффузионные процессы выделения из твердого раствора избыточных атомов Сu. В результате оказывается зафиксированным пересыщенный твердый раствор Сu в Al (С на рис. 3б). Дюралюминий при этом несколько упрочняется, что объясняется появлением в твердом растворе замещения избыточных атомов меди, способствующих увеличению плотности дислокаций и их торможению. Но, так как исчезают частицы CuAl 2, то сохраняется пластичность отожженного состояния, как следствие повышения однородности структуры сплава.
Выделение из пресыщенного твердого раствора частиц второй фазы с оптимальными параметрами возможно за счет естественного старения - выдержки при комнатной температуре в течение нескольких суток (D на рис. 3б) или в процессе искусственного старения - выдержки при повышенной температуре, что ускоряет выделение упрочняющих частиц (Е на рис. 3б).
С появлением упрочняющих частиц пластичность сплава уменьшается, так как частицы эффективно тормозят дислокации, сокращая длину их свободного перемещения. Искусственное старение дюралюминия в большей степени, чем естественное, понижает пластичность. Для многих сплавов возможно только искусственное старение, так как температура 20° С оказывается недостаточной для распада пересыщенного твердого раствора.
В работе предлагается исследовать степень упрочнения дюралюминия Д1 в зависимости от температуры нагрева сплава при старении. Исследования производятся на отожженных образцах сплава Д1, которые подвергаются закалке, а затем старению при различных температурах. Степень упрочнения оценивается по изменению твердости.
Анализ результатов работы сводится к объяснению связи между структурой дюралюминия, получаемой при различных режимах старения, и его твердостью.
Оборудование и материалы
1. Образцы сплава Д1 в отожженном состоянии.
2. Малогабаритные печи.
3. Прибор для измерения твердости по Бринеллю.
Порядок выполнения работы
1. Измерить твердость по Бринеллю (НВ) образцов в исходном отожженном состоянии. Среднее значение твердости внести в таблицу.
Материал | Состояние | Твердость НВ, МПа |
Дюралюминий Д1 | После отжига | |
После закалки 500° С | ||
После старения | 20° С | |
180° С | ||
300° С |
2. Закалить образцы, нагревая их до температуры 500° С в течение 10 минут и охлаждая в воде.
3. Измерить твердость НВ образцов в закаленном состоянии.
4. Произвести старение, выдерживая каждый образец при определенной температуре: 20, 180 и 300° С в течение 20 мин; охлаждение - в воде.
5. Измерить твердость НВ образцов в состаренном состоянии.
6. Все значения твердости НВ занести в таблицу.
7. Построить графическую зависимость твердости НВ от температуры старения (Т ст).
Содержание отчета
1. Цель работы.
2. Таблица с данными.
3. График зависимости НВ = f (Т ст).
4. Рисунок 3.
5. Краткий анализ полученных результатов.
Контрольные вопросы
1. Какова физическая природа дисперсионного упрочнения?
2. Для каких сплавов возможно дисперсионное упрочнение?
3. Каким образом можно управлять параметрами системы частиц при дисперсионном упрочнении?
4. В чем состоит различие между искусственным и естественным старением?
5. Из каких этапов термической обработки состоит дисперсионное упрочнение?
6. В чем состоит влияние параметров d и L системы частиц на эффективность дисперсионного упрочнения?
Литература
1. Сидорин И.И. Основы материаловедения. - М.: Машиностроение, 1976, гл. VIII, XV.
2. Арзамасов Б.Н. Материаловедение. - М.: Машиностроение, 1986, глава 5, 12.
3. Солнцев Ю.П. и др. Материаловедение. – М.: «МИСИС», 1999.
ЛАБОРАТОРНАЯ РАБОТА № 3
|
|
Наброски и зарисовки растений, плодов, цветов: Освоить конструктивное построение структуры дерева через зарисовки отдельных деревьев, группы деревьев...
Организация стока поверхностных вод: Наибольшее количество влаги на земном шаре испаряется с поверхности морей и океанов (88‰)...
История развития пистолетов-пулеметов: Предпосылкой для возникновения пистолетов-пулеметов послужила давняя тенденция тяготения винтовок...
Состав сооружений: решетки и песколовки: Решетки – это первое устройство в схеме очистных сооружений. Они представляют...
© cyberpedia.su 2017-2024 - Не является автором материалов. Исключительное право сохранено за автором текста.
Если вы не хотите, чтобы данный материал был у нас на сайте, перейдите по ссылке: Нарушение авторских прав. Мы поможем в написании вашей работы!