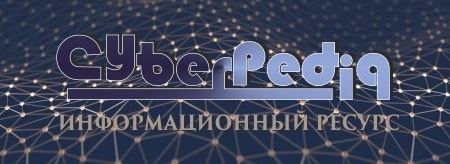
Индивидуальные очистные сооружения: К классу индивидуальных очистных сооружений относят сооружения, пропускная способность которых...
Организация стока поверхностных вод: Наибольшее количество влаги на земном шаре испаряется с поверхности морей и океанов (88‰)...
Топ:
Процедура выполнения команд. Рабочий цикл процессора: Функционирование процессора в основном состоит из повторяющихся рабочих циклов, каждый из которых соответствует...
Марксистская теория происхождения государства: По мнению Маркса и Энгельса, в основе развития общества, происходящих в нем изменений лежит...
Основы обеспечения единства измерений: Обеспечение единства измерений - деятельность метрологических служб, направленная на достижение...
Интересное:
Средства для ингаляционного наркоза: Наркоз наступает в результате вдыхания (ингаляции) средств, которое осуществляют или с помощью маски...
Подходы к решению темы фильма: Существует три основных типа исторического фильма, имеющих между собой много общего...
Национальное богатство страны и его составляющие: для оценки элементов национального богатства используются...
Дисциплины:
![]() |
![]() |
5.00
из
|
Заказать работу |
|
|
ОБРАБОТАННОЙ ПОВЕРХНОСТИ
Цель работы – Получение практических навыков оценки влияния режима точения наплавленных деталей на качество обработанной поверхности.
Задачи работы:
1. Изучить методику исследования.
2. Получить практические навыки подобных исследований.
3. Провести исследование и обработать его результаты.
Общие положения
Обработка наплавленных поверхностей заготовок точением
Предварительную обработку наплавленных поверхностей восстанавливаемых деталей типа «ступенчатый вал» осуществляют точением.
В условиях ремонтного производства обработку производят на универсальных токарных станках, используя схемы обработки, приведенные на рис. 4.1.
Рис. 4.1. Схемы обработки при точении резцами:
а - прямым проходным правым; б - отогнутым проходным;
в - проходным упорным; г - подрезным правым
Токарные резцы имеют определенную форму и углы режущей части: передний угол у, задний угол а, угол заострения β, а также главный и вспомогательный углы в плане φ и φ1 (рис. 4.2).
Углы выбирают в зависимости от марки обрабатываемого материала, условий и режима обработки, жесткости технологической системы. Для изготовления резцов наиболее широко используют быстрорежущие стали, твердые сплавы, композиционные материалы.
Быстрорежущие стали - это легированные инструментальные стали с высоким содержанием вольфрама. Маркируются буквами и цифрами, например: Р12, Р9К9, Р6М5, Р6М5К5 и др. Цифра после буквы «Р» указывает на среднее содержание вольфрама в процентах. Остальные буквы и цифры означают то же, что и в марках легированных сталей.
Рис. 4.2. Углы проходного резца
|
Твердые сплавы выпускаются чаще в виде сменных пластинок различных форм и размеров, получаемых методом порошковой металлургии (прессованием и спеканием).
Основой для них служат порошки карбидов тугоплавких металлов (вольфрама, титана, тантала), сцементированных кобальтом. Выпускаются три группы твердых сплавов: вольфрамовые - ВК (ВКЗ, ВК4, ВК6 и др.) для обработки чугунных заготовок, титановольфрамовые - ТК (Т5К10, Т15К6 и др.) и титанотанталовольфрамовые - ТТК - для обработки стальных заготовок.
В обозначениях марок твердых сплавов используют буквы: В - карбид вольфрама, К - кобальт, первая буква Т - карбид титана, вторая буква Т - карбид тантала.
Цифры после букв указывают на содержание компонентов в процентах; остальное в сплаве - карбид вольфрама. Композиционные материалы (природные и синтетические алмазы) обладают самой большой из известных в природе материалов твердостью, теплостойкостью (до 850 °С) и низким коэффициентом трения.
Однако алмазы обладают повышенной хрупкостью и интенсивно изнашиваются при резании черных металлов. Последнее свойство объясняется диффузией углерода алмаза в железе при высокой температуре.
Поэтому алмазные резцы при точении заготовок из черных металлов не применяют. Кубический нитрид бора (КНБ) по твердости приближается к алмазу, но вдвое превосходит его цо теплостойкости и обладает химической инертностью к углероду и железосодержащим материалам.
Поэтому КНБ используют при обработке заготовок, обладающих высокой твердостью. Элементами режима резания при точении являются глубина резания t, подача S и скорость резания V:
(4.1)
где D и d - размеры обрабатываемой и обработанной поверхности соответственно, мм. Подача S (мм/об) - величина перемещения инструмента за один оборот заготовки.
Скорость резания определяют по формуле:
(4.2)
где п - частота вращения заготовки, об/мин.
Режимы резания назначают на основании исходных данных: чертежа детали, размеров и материала заготовки, типа, материала и геометрии инструмента, а также паспортных данных станка в следующем порядке:
|
1. Определяют глубину резания t, мм.
2. Назначают подачу S, мм/об и корректируют ее, исходя из данных станка, принимая ближайшую из имеющихся на станке.
3. Скорость резания V рассчитывают или назначают по нормативным таблицам в зависимости от свойств обрабатываемого материала, принятых значений глубины резания и подачи.
4. Определяют частоту вращения заготовки по формуле:
(4.3)
Затем подбирают ближайшее меньшее или большее (если оно не превышает на 5 % расчетное) значение п по станку.
5. По принятой частоте вращения по формуле (4.2) рассчитывают действительную скорость резания.
6. При предварительной обработке с большими значениями t и S выполняют проверку режима по мощности, соблюдая условие:
Nрез < Nшп, (4.4)
где Nрез и Nmu - мощность, необходимая на резание и мощность на шпинделе станка соответственно, кВт.
Предварительную обработку наплавленных деталей рекомендуют выполнять резцами с пластинами из твердого сплава с углами: у = 8... 10°,а=10... 15°Д = 65...75°. Применение в качестве материала инструмента поликристаллических сверхтвердых материалов позволяет существенно увеличить производительность обработки и улучшить качество обработанных деталей.
При выборе режима обработки наплавленных наружных цилиндрических поверхностей деталей можно ориентироваться на данные, приведенные в табл. 4.1.
В качестве критериев оценки технологической эффективности токарных операций используют: составляющие Рy и Рz силы резания, износ резца по задней и передней поверхностям, период стойкости резца, параметры качества, в том числе шероховатости обработанной поверхности.
К высотным параметрам шероховатости относятся: среднее арифметическое отклонение профиля Ra, мкм; высота неровностей профиля по десяти точкам Rz, мкм; наибольшая высота неровностей Rmax.
Шероховатость измеряют с помощью профилометров или профилографов.
Таблица 4.1 Режимы обработки наплавленных деталей
Значительное влияние на шероховатость оказывает подача S и скорость резания V. При исследовании влияния какого-либо входного параметрах (например, подачи S или скорости резания V) на критерий технологической эффективности операции Y (например, параметр шероховатости) на основе экспериментальных данных определяют Y = f (X), называемые эмпирическими формулами (зависимостями).
|
Процесс подбора эмпирических формул включает графическую обработку результатов исследований, в ходе которых ориентировочно выбирают тип формулы, и вычисление параметров формул (коэффициентов).
Изменение параметров качества следует, в первую очередь, описывать наиболее простыми функциями, к которым относится линейная
Y=A+BX, (4.5)
где А и В- постоянные коэффициенты.
Для определения коэффициентов А и В можно, в частности, использовать графический метод (рис. 4.3).
Для этого на график наносят экспериментальные точки и строят прямую линию так, чтобы она проходила по возможности ближе ко всем точкам (см. рис. 4.3).
Параметр А определяют как ординату точки пересечения прямой с осью У, а тангенс угла наклона прямой к оси ОХ (см. рис. 4.3):
Рис. 4.3. Графическое изображение коэффициентов
Эмпирического уравнения
Для определения параметров А и tg а можно применить также другой графический метод. В уравнение (4.5) подставляют координаты двух крайних точек прямой линии графика. Получают систему двух уравнений, из которых вычисляют коэффициенты AnB = tga.
Пример. Подобрать эмпирическую формулу, если при исследовании процесса получены следующие результаты (табл. 4.2).
Графический анализ показывает, что в прямоугольных координатах точки расположены вблизи от прямой линии.
Подставив крайние значения параметров (Х\9 Y\, Х7, Y7) в уравнение (4.5), получим систему из двух уравнений:
Аo + 0,7A1 = 54,0; Аo + 0,1A1 = 12,1,
откуда
A1 = 41,9 / 0,6 = 69,8 и Аo= 12,1-0,1 -69,8 = 5,12.
Эмпирическая формула примет вид
Y=5,12 + 69,8 X.
Таблица 4.2 Значения входного и выходного параметра процесса
Содержание работы
В процессе выполнения лабораторной работы студент назначает условия и режим точения, проводит исследование влияния указанных преподавателем элементов режима резания на качество обработанной поверхности детали.
|
|
Своеобразие русской архитектуры: Основной материал – дерево – быстрота постройки, но недолговечность и необходимость деления...
История создания датчика движения: Первый прибор для обнаружения движения был изобретен немецким физиком Генрихом Герцем...
Опора деревянной одностоечной и способы укрепление угловых опор: Опоры ВЛ - конструкции, предназначенные для поддерживания проводов на необходимой высоте над землей, водой...
Механическое удерживание земляных масс: Механическое удерживание земляных масс на склоне обеспечивают контрфорсными сооружениями различных конструкций...
© cyberpedia.su 2017-2024 - Не является автором материалов. Исключительное право сохранено за автором текста.
Если вы не хотите, чтобы данный материал был у нас на сайте, перейдите по ссылке: Нарушение авторских прав. Мы поможем в написании вашей работы!