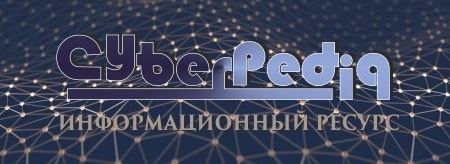
Папиллярные узоры пальцев рук - маркер спортивных способностей: дерматоглифические признаки формируются на 3-5 месяце беременности, не изменяются в течение жизни...
Поперечные профили набережных и береговой полосы: На городских территориях берегоукрепление проектируют с учетом технических и экономических требований, но особое значение придают эстетическим...
Топ:
Устройство и оснащение процедурного кабинета: Решающая роль в обеспечении правильного лечения пациентов отводится процедурной медсестре...
Марксистская теория происхождения государства: По мнению Маркса и Энгельса, в основе развития общества, происходящих в нем изменений лежит...
Интересное:
Влияние предпринимательской среды на эффективное функционирование предприятия: Предпринимательская среда – это совокупность внешних и внутренних факторов, оказывающих влияние на функционирование фирмы...
Финансовый рынок и его значение в управлении денежными потоками на современном этапе: любому предприятию для расширения производства и увеличения прибыли нужны...
Мероприятия для защиты от морозного пучения грунтов: Инженерная защита от морозного (криогенного) пучения грунтов необходима для легких малоэтажных зданий и других сооружений...
Дисциплины:
![]() |
![]() |
5.00
из
|
Заказать работу |
|
|
Уровень механизации характеризуется тремя показателями, рассчитываемыми по формулам
где У1 — количественный показатель уровня механизации; У2 — качественный показатель уровня механизации; У3 — степень охвата рабочих механизированным трудом; Тм — трудоемкость операции, выполняемой механизированным способом; Тр — суммарная трудоемкость операций, выполняемых ручным способом; П — коэффициент производительности оборудования; Рм — число рабочих, выполняющих работу механизированным способом; Рр — число рабочих, выполняющих работу вручную.
Коэффициент П характеризует рост производительности при замене ручной операции (или механизированной, принятой за базу) механизированной и определяется как отношение трудоемкости до проведения механизации Тр, к трудоемкости, достигаемой в результате механизации Тм:.
Показатели У1 и У3 изменяются от 0 до 100%. На величину показателей У1 и У3 оказывает влияние только масштаб механизации производственного процесса. Показатель У2 изменяется от 0 и стремится к 100%, но не достигает 100%, так как качественное совершенствование оборудования беспредельно.
ОПРЕДЕЛЕНИЕ ТЕХНИКО-ЭКОНОМИЧЕСКОЙ ЭФФЕКТИВНОСТИ КОМПЛЕКСНОЙ МЕХАНИЗАЦИИ И АВТОМАТИЗАЦИИ СВАРОЧНОГО ПРОИЗВОДСТВА
Общие положения и определения
Для оценки сравнительной эффективности необходимо определить следующий комплекс технико-экономических показателей по сравниваемым вариантам:
1. Капитальные вложения, т. е. одновременные капитальные затраты на реализацию запроектированной механизации — К, руб.
2. Годовые текущие затраты на производство сварной продукции (работ), т. е. себестоимость годовой продукции— С руб./год или ее передела.
|
3. Себестоимость единицы выпускаемой продукции или себестоимость передела единицы продукции — А руб./шт. или руб/т.
4. Трудоемкость производства или передела единицы выпускаемой продукции — Т чел-ч/т или чел-ч/шт.
5. Производительность труда или выработка продукции на одного работающего или на одного рабочего.
6. Срок окупаемости капиталовложений Ток,
который показывает, в течение какого периода времени за счет экономии текущих затрат, т. е. за счет снижения себестоимости продукции, окупятся дополнительные капитальные вложения по рассматриваемому варианту механизации.
где К и С — капитальные и текущие затраты по рассматриваемому варианту; К6 и Сб — то же по базовому или конкурирующему варианту
Следует также различать нормативный срок окупаемости капитальных затрат — Тв, который обычно задается директивными органами как максимально допустимый.
7. Коэффициент сравнительной экономической эффективности капитальных затрат Е, который служит мерой эффективности рассматриваемого варианта механизации и показывает, какая доля капитальных затрат ежегодно окупается за счет экономии на себестоимости продукции или ее передела. Он определяется соотношением
8. Экономия Э, получаемая от внедрения данного варианта механизации в сравнении с другим конкурирующим вариантом или с базовым. Общая экономия равна алгебраической сумме нескольких составляющих: снижению капитальных затрат; снижению текущих затрат на производство сварных конструкций; снижению расходов по отдельным статьям затрат и др. Этот показатель определяется в денежном выражении.
9. Годовой экономический эффект Ф, который выражает величину уменьшения всех приведенных затрат в одном извариантов по сравнению с другим (или базовым), т. е. уменьшениясуммы капиталовложений и годовых текущих затрат, приведенных к соизмеримости посредством нормативного коэффициента экономической эффективности Ен или нормативного срока окупаемостиТн Капитальные вложения К—это единовременные затраты с размерностью руб., а годовые текущие затраты С имеют размерность руб./год.
|
10. Важными показателями, наиболее полно характеризующими
экономичность рассматриваемого варианта, являются: удельные
приведенные затраты Дуд на единицу выпускаемой продукции и удельный экономический эффект Фуд, приходящийся на единицу выпускаемой продукции.
Эти показатели легко определить делением годовых приведенных затрат Д и соответственно годового экономического эффекта Ф на величину годового выпуска продукции В, выраженного в тоннах или штуках:
Показатели Дуд и Фуд имеют размерность руб/т или руб./шт.
11. Уровень механизации и автоматизации.
На технико-экономическую эффективность комплексной механиизации оказывает существенное влияние только второй показатели У2.
12. К о э ф ф и ц и е н т производительности П0, средневзвешенный по всему запроектированному сварочному производству.
13. Уровень рентабельности, характеризующий экономическую целесообразность запроектированного производственного предприятия (цеха, комплекса) с учетом его эксплуатации в условиях новой системы планирования и экономического стимулирования. Уровень рентабельности производства
Rn =
где С3 — заводская себестоимость изделия; Сопт = фС3 — оптовая отпускная цена изделия; ф — коэффициент плановой прибыли по отношению к заводской себестоимости С3 (в машиностроении ф =1,03…1,10); В — годовой выпуск изделий; Косн— сумма основных средств; Коб — сумма оборотных средств.
Наряду с показателем уровня рентабельности предприятия Rп, следует также определять другой показатель Rи— уровень рентабельности изделия или единицы выпускаемой продукции. Его рассчитывают по формуле
Величина Rи для машиностроительных предприятий находится в пределах 3—10%, Этот показатель позволяет сравнивать между собой рентабельность различных изделий, включенных в программу производства.
В расчетах экономической эффективности необходимо учитывать влияние качества выпускаемой продукции. Если в результате механизации технологического процесса изменяется качество сварных изделий, но при этом отсутствует возможность учета экономического эффекта от этого изменения непосредственно у потребителя, в расчете экономической эффективности себестоимость продукции повышенного качества корректируется следующим образом. Если повышение качества изделий влечет за собой увеличение срока их службы, то скорректированная себестоимость определяется по формуле
|
где С — действительная себестоимость продукции после внедрения запроектированной механизации; 1сл1 и 1сл2 — срок службы продукции прежнего и повышенного качества.
Если вследствие повышения качества изделий уменьшается общая потребность в них, то себестоимость корректируется по формуле
где Л1 и Л2 — количественная потребность в этих изделиях до и после внедрения запроектированной механизации.
В соответствии с этим корректируются и другие показатели экономической эффективности, зависящие от себестоимости выпускаемой продукции.
Выбор наивыгоднейшего варианта механизации и автоматизации производится путем сравнения технико-экономических показателей запроектированного варианта с показателями базового варианта либо с показателями конкурирующих запроектированных вариантов.
В качестве исходного — базового — варианта для сравнения принимается существующий технологический процесс производства, взамен которого проектируется новый — механизированный. При отсутствии базового варианта, например, для нового вида сварной продукции, сравнение производится с аналогичными производствами, а также с другими проектными вариантами механизации.
Занятие №5 (17.09.2015)
МЕХАНИЗИРОВАННЫЕ И АВТОМАТИЗИРОВАННЫЕ СПОСОБЬІ СВАРКИ ПЛАВЛЕНИЕМ
1.ЭЛЕКТРОДУГОВАЯ АВТОМАТИЧЕСКАЯ СВАРКА ПОД ФЛЮСОМ
При автоматической электродуговой сварке все операции по возбуждению и поддержанию дугового разряда выполняются сварочной головкой, которая непрерывно подает в зону дуги сварочную проволоку по мере ее плавления. Перемещение дуги по шву осуществляется самоходной сварочной тележкой или любым другим механизмом в зависимости от того, движется дуга относительно неподвижного свариваемого изделия или, наоборот. При сварке круговых швов механизм сварочного движения обычно представляет собой приводной вращатель того или иного типа, например, манипулятор с вращающейся планшайбой, роликовый стенд (для автосварки цилиндрических сосудов), центровой вращатель, карусельно-сварочный станок и т. д.
|
Таким образом, при автоматической сварке оба рабочих движения - подача электрода в зону дуги и его перемещение по шву — механизированы.
Рабочий, обслуживающий такую автосварочную установку (автосварщик), не принимает непосредственного участия в образовании шва, но управляет процессом сварки при помощи вспомогательных устройств — пульта управления, корректоров и т. д.
При сварке под флюсом сварочная дуга и сварочная ванна защищены от воздействия окружающего воздуха слоем порошкообразного флюса толщиной 30—50 мм и пленкой шлака, образующегося при расплавлении части флюса, примыкающей к зоне дуги.
Основным методом автоматической сварки под флюсом является сварка одним электродом, когда в зону дуги подается одна сварочная проволока или электродная лента. Однако для повышения производительности процесса применяют сварку двумя и более электродами, т. е. так называемую многоэлектродную или многодуговую сварку. При многоэлектродной сварке все электроды подсоединены к одному полюсу источника питания, при многодуговой — каждый из электродов подсоединен к отдельному источнику питания и все они изолированы друг от друга.
Преимущества автоматической сварки под флюсом: 1) по сравнению с известными способами сварки плавлением самая высокая производительность, превышающая ручную сварку в 4—6 раз при однодуговом процессе и в 15—20 раз при многодуговом процессе,
2)высокое качество и хороший внешний вид сварных соединений;
3)малый удельный расход электродного металла и электроэнергии вследствие меньшего сечения шва по наплавленному металлу, а также уменьшения потерь на угар,
4)высокий уровень локальной механизации сварочного процесса и возможность комплексной его автоматизации;
5)улучшение условий труда, так как отпадает необходимость в защите глаз и лица сварщика от действия дуги.
Недостатки:
1)невозможность сваривать швы или производить наплавку в вертикальном или наклонном положении (можно только в горизонтальном);
2)невозможность (или нецелесообразность) сварки швов малого калибра, менее 3 мм;
3)сложность и громоздкость сварочного оборудования и, как следствие, меньшая маневренность и мобильность;
4)необходимость более тщательной подготовки кромок и более точной сборки деталей под сварку;
5)затруднен контроль за направлением дуги по шву из-за невидимости дуги (если отсутствует система автоматического направления дуги по шву);
|
6)невозможность сварки стыковых швов на весу, т.е. без подкладки или предварительной подварки корня шва;
7) загрязнение воздуха флюсовой пылью.
Области рационального применения:
1.Почти все отрасли металлообрабатывающей промышленности (кроме производства изделий из металла очень малой толщины с малокалиберными швами).
2.По типу производства — от мелкосерийного до массового.
3.По типу свариваемых металлов —малоуглеродистые стали толщиной от 3 до 100 мм.
4.Сварка прямолинейных швов, стыковых и угловых калибром 5—50мм протяженностью от 0,8 м и более со свободным входом и выходом сварочной головки для начала и конца шва; сварка кольцевых швов при толщинах до 100— 120 мм.
5.Наплавочные работы, в том числе широкослойная наплавка ленточным электродом или гребенкой электродов или несколькими головками одновременно.
6.В перспективе — высокопроизводительная сварка ленточным электродом.
2. ЭЛЕКТРОДУГОВАЯ ПОЛУАВТОМАТИЧЕСКАЯ СВАРКА ПОД ФЛЮСОМ
Этот способ сварки отличается от автоматической тем, что в нем механизировано лишь одно рабочее движение — подача сварочной проволоки в зону дуги, а перемещение дуги по шву производится вручную. Подача проволоки осуществляется при помощи специального подающего механизма с электроприводом, позволяющим регулировать скорость подачи. Манипуляции дугой для поддержания заданного режима, придания шву нужной формы и перемещения дуги по шву осуществляются вручную. Сварка производится сварочной проволокой диаметром от 1,5 до 2,5 мм, намотанной в кассеты или подаваемой непосредственно из бухты. Для подвода тока к электроду служит держатель..
Во время сварки держатель находится в руке рабочего, что является основным признаком полуавтоматической сварки. Засыпка и уборка флюса осуществляются вручную либо с помощью специальных переносных флюсоаппаратов.
Преимущества полуавтоматической сварки под флюсом:
1)повышенная по сравнению с ручной сваркой производительность (в 1,5 раза);
2)уменьшенный расход электродного металла вследствие отсутствия огарков и разбрызгивания;
3)высокая по сравнению с автоматической сваркой маневренность и мобильность, приближающиеся к ручной сварке;
4)высокое качество швов и хороший товарный вид
Недостатки:
1) невозможность сваривать вертикальные или наклонные швы;
2)затруднена операция ручного ведения дуги по шву, так как дуга невидима. невозможность сварки стыковых швов на весу, т. е. без подкладки или предварительной подварки;
3)повышенная утомляемость сварщика из-за манипулирования ручным держателем и шлангом;
4) невозможность автоматизации технологического процесса.
Области рационального применения:
1. Единичное и мелкосерийное производство.
2.Сварка коротких или криволинейных швов среднего калибра (6—15 мм), недоступных или неудобных для автоматической сварки,
3.Сварка прерывистых угловых швов в судостроении и других отраслях.
Занятие №6 (21.09.2015)
3ЭЛЕКТРОДУГОВАЯ АВТОМАТИЧЕСКАЯ СВАРКА В СРЕДЕ ЗАЩИТНЫХ ГАЗОВ
Этот способ отличается от автоматической сварки под флюсом лишь характером физической защиты дуги и сварочной ванны от окружающего воздуха.
При сварке в защитных газах дуга, возникающая между электродом и основным металлом, со всех сторон окружена газом, подаваемым под небольшим избыточным давлением из сопла,обычно расположенного концентрично электроду. Газовая защита применяется как при сварке плавящимся электродом, так и неплавящимся, например, вольфрамовым. В последнем случае механизм подачи электрода существенно меняется в связи с тем, что отпадает обязательная необходимость непрерывной подачи электрода по мере его плавления. Во многих случаях достаточно иметь простейший механизм для периодической подачи неплавящегося электрода по мере его сгорания. В более совершенных сварочных головках для автоматической сварки имеется специальный механизм подачи с электроприводом, который автоматически компенсирует постепенное сгорание электрода (угольного, вольфрамового и др.) и поддерживает таким образом постоянную величину дугового промежутка.
Преимущества автоматической сварки в защитных газах:
1)возможность сваривать швы в любом пространственном положении;
2)повышенная по сравнению с ручной сваркой производительность в 2—2,5 раза при токах до 500 а. Наиболее эффективна сварка порошковыми проволоками АН 4 и ЛН-5 в среде С02;
3)возможность сварки малокалиберных швов и изделий малой толщины, которые под флюсом сваривать нельзя;
4)удобный контроль за направлением дуги по шву— дуга не закрыта флюсом;
5)меньшее по сравнению с автоматической сваркой под флюсом термическое воздействие на основной металл;
6)при сварке тонкого металла толщиной до 3 мм производительность выше, чем при сварке под флюсом, благодаря повышенному коэффициенту наплавки при токах 200-400 а;
7) возможность сварки стыковых швов на весу.
Недостатки:
1) при сварке крупнокалиберных швов производительность при-
мерно вдвое меньше, чем при автоматической сварке под флюсом;
2) плохой внешний вид швов;
3) большое разбрызгивание металла при сварке плавящимся
электродом па токах 250—450 а.
Области рационального применения:
1.По типу производства — в серийном и массовом производстве.
2.При изготовлении конструкций из тонколистовых высоколегированных сталей, алюминиевых и титановых сплавов.
3.Сварка швов, которые нельзя или нецелесообразно располагать в горизонтальном положении, например, неповоротных стыков труб.
4.Прихватка собранных деталей или заварка беглым швом корня шва на весу.
5. Наплавочные работы с малым термическим воздействием на основной металл.
6. Сварка неплавящимся электродом методом оплавления кромок без присадочного металла, например, при сварке канистр.
7. Производство тонкостенных изделий с малокалиберными швами.
4.ЭЛЕКТРОДУГОВАЯ ПОЛУАВТОМАТИЧЕСКАЯ СВАРКА В СРЕДЕ ЗАЩИТНЫХ ГАЗОВ
Физическая сущность этого процесса та же, что и автоматической сварки в защитных газах. Различие заключается лишь в степени автоматизации процесса, которая при полуавтоматической сварке существенно ниже, так как сварочное движение по шву осуществляется сварщиком вручную. В смысле автоматизации сварочного процесса и техники его осуществления полуавтоматическая сварка в защитных газах и полуавтоматическая сварка под флюсом почти не отличаются друг от друга. Разница лишь в том, что в рассматриваемом способе по каналам шланга подается не только сварочная про волока, но и защитный газ (С02, аргон или смесь газов).
Полуавтоматы для сварки в защитных газах, как и полуавтоматы для сварки под флюсом, выполняются обычно в виде портативных переносных аппаратов-инструментов, являющихся промежуточным звеном между сварочным автоматом и ручным инструментом. Они представляют собой, так называемую,»малую механизацию, обладающую универсальностью и маневренностью, почти такой же, как при ручной сварке.
Основное различие между автоматической и полуавтоматической сваркой заключается в разных уровнях механизации и автоматизации. Производительность автоматической сварки под флюсом в 3—11 раз выше ручной. Следовательно,,ровень механизации в 2—3 раза ниже, чем при автоматической сварке.
Преимущества полуавтоматической сварки в защитных газах:
1) повышение производительности по сравнению с ручной в
1,2—1,5 раза, а при сварке порошковой проволокой — в 1,6—
2,0 раза;
2)возможность сварки в любом пространственном положении;
3) возможность сварки стыковых швов на весу;
4) возможность и целесообразность сварки малокалиберных швов и изделий малой толщины;
5)высокая маневренность и мобильность по сравнению с автоматической сваркой;
6)возможность визуального контроля за направлением дуги по шву.
Недостатки:
1)сильное разбрызгивание металла при сварке на токах 200— 400 а и необходимость удаления брызг с поверхности изделия. Этот недостаток не относится к сварке порошковой, а также сплошной проволокой в специальной смеси газов или в аргоне;
2)низкая производительность труда, в отдельных случаях не превышает производительность ручной сварки (если много времени затрачивается на удаление брызг);
3)затруднено использование на открытом воздухе >— на ветру из-з^ сдувания защитного газа;
4)внешний (товарный) вид швов хуже, чем при сварке под флюсом.
Области рационального применения:
1. В единичном, мелкосерийном, реже в серийном производстве.
2. Сварка в аргоне (или в смеси аргона с другими газами) тонколистовых изделий из высоколегированных сталей, а также алюминиевых и титановых сплавов.
3. Преимущественно для сварки малокалиберных швов в любом пространственном положении; стыковых швов — на весу.
Занятие №7 (24.09.2015)
5. ЭЛЕКТРОЗАКЛЕПОЧНАЯ ДУГОВАЯ СВАРКА
При сварке электрозаклепками в большинстве случаев применяется дуговой процесс без перемещения дуги и без подачи электродной проволоки в зону дуги.
Сварка электрозаклепками производится с помощью переносных или стационарных электрозаклепочников. В серийном и массовом производстве применяют специализированные машины для сварки нескольких электрозаклепок — многоэлектродные или многоточечные машины, имеющие большую производительность и высокую степень автоматизации процесса. Наиболее проста многоточечная (многоэлектродпая) установка с автоматически действующей коммутацией. Для нее характерно отсутствие коммутационных устройств и изоляции между электродами. Последовательное, поочередное включение электродов достигается автоматически, естественным процессом. Во время горения одной дуги исключается возможность параллельного возникновения дугового разряда на другом электроде, так как выход осциллятора зашунтирован горящей дугой и сопротивлением ее шлаковой оболочки. Дуга загорится на каком-либо другом электроде, находящемся на наименьшем расстоянии от изделия, только после естественного обрыва первой дуги. Такая последовательность возбуждения дуги сохраняется до тех пор, пока дуга не обойдет все электроды.
Существуют также многоэлектродные машины с принудительной коммутацией, задающей определенный порядок постановки электрозаклепок, а в некоторых системах и определенное время горения дуги.
Преимущества сварки электрозаклепками:
1)высокая по сравнению с ручной сваркой производительность, хотя и уступающая контактной точечной сварке;
2)менее требовательна по сравнению с контактной точечной сваркой к чистоте свариваемых поверхностей;
3)малые остаточные деформации (коробление) по сравнению со сваркой сплошным швом;
4)простота и автоматичность процесса;
5)возможность полной автоматизации технологического процесса и создания высокопроизводительных автоматизированных много-электродных машин н линий.
Недостатки:
1)прерывистость и нестационарность процесса; сварка почти все время происходит в неустановившемся режиме (за 1—3 сек происходит возбуждение Дуги, сварка и обрыв дуги);
2)зависимость качества и размеров ядра электрозаклепки (особенно «прорезной») от зазора между свариваемыми поверхностями, плотности их сопряжения и чистоты;
3)негерметичность сварных соединений и неравнопрочность с основным металлом, свойственные любому прерывистому шву;
4)пониженная динамическая прочность сварных соединений вследствие наличия концентраторов напряжений в месте сопряжения листов (аналогично контактной точечной сварке);
5)затруднен контроль качества и размеров сварной точки (активного ядра) при «прорезных» электрозаклепках;
6)требуются добавочные операции по пробивке отверстий и усложняется установка электродов точно по оси отверстий при сварке заклепок по отверстиям (не прорезных).
Области рационального применения:
1. Любое (единичное, серийное, массовое) производство стальных щитовых конструкций, в которых лист присоединяется к раме или каркасу нахлесточным точечным швом и к которым не предъявляются требования герметичности и высокой прочности. Толщина листа от 1 до 6 мм.
2. Наиболее эффективно применение в вагоностроении, сельхозмашиностроении, автомобилестроении, особенно в виде специализированных многоэлектродных машин с программным управлением.
3. При изготовлении листовых конструкций из горячекатаного металла, который нельзя сваривать контактной точечной сваркой без удаления окалины и очистки свариваемых поверхностей.
6. СВАРКА СЖАТОЙ ДУГОЙ (ПЛАЗМЕННО-ДУГОВАЯ)
Одной из разновидностей дуговой сварки неплавящимся электродом является сварка сжатой дугой или плазменно-дуговая сварка.
При этом методе используется одно из важнейших свойств дугового разряда — повышение плотности энергии и температуры столба дуги при искусственном сжатии и охлаждении его наружных слоев. Схема процесса представлена на рис.. Дуговой разряд возникает между вольфрамовым и медным электродом (соплом), подсоединенными к источнику постоянного тока (дуга косвенного действия, рис., б), или между вольфрамовым электродом и основным металлом (дуга прямого действия, рис., а). Вдоль столба дуги через капал в концентричном медном сопле проходит струя нейтрального одноатомного (аргона, гелия) или двух- углерода) газа, который сжимает столб дуги, что приводит к повышению его температуры до 16 000° С при дуге косвенного действия и до 33 000° С при дуге прямого действия, и образует плазменную струю. Сжатая дуга является весьма концентрированным источником теплоты. Газ в столбе дуги находится в состоянии плазмы, которая характеризуется высокой степенью ионизации и значительной электропроводностью ионизированного газа.
Рис.. Схема сварки сжатой дугой (плазменно-дуговая):
1 — водоохлаждаемое медное сопло; 2 — газ; 3- вольфрамовый электрод; 4 – столб дуги; 5 – плазменная струя
Плазменная струя, выходя из сопла, расширяется и вытягивается в виде длинного луча (до 300 мм), который используется для нагрева и расплавления металла. Для защиты сварочной ванны от окружающего воздуха вокруг сжатой дуги, концентрично с ней, подается через кольцевое сопло дополнительный защитный газ (аргон, С02). Возможна также защита зоны дуги и флюсом.
Сварка осуществляется при помощи плазменной горелки или плазмотрона (рис. 9). Сжатая дуга (плазменная струя) применяется также для резки металлов.
Занятия №8 и №9 (28.09.2015 и 01.10.2015)
7. ВИБРОДУГОВАЯ СВАРКА И НАПЛАВКА
Разновидностью стационарного дугового процесса является прерывистый дуговой процесс, получивший название вибродугового. ІІри помощи электромагнитного или другого механизма электродная проволока диаметром 1,5—2 мм периодически подается к изделию и отводится от него, совершая осевые колебательные Движения (вибрацию) с амплитудой 1,2—2,5 мм. К электроду и изделию подводится напряжение от источника постоянного или переменного тока.
Основное количество теплоты, идущей на плавление металла, выделяется в период дугового разряда.
Процесс ведется при напряжении 12—25 в и токе 100—250 а. Для охлаждения детали и защиты сварочной ванны от окружающего воздуха на деталь и к месту сварки (наплавки) через специальные сопла подается струя жидкости (4%-ный раствор кальцинированной соды или 25%-ный раствор глицерина в воде). Возможна сварка с флюсовой защитой, а также в среде углекислого газа, аргона, азота.
Так как длительность существования дугового разряда составляет всего 20% от времени общего цикла и чередуется с периодами полного отсутствия выделения теплоты (период холостого хода) и периодом незначительного его выделения (период короткого замыкания), то при вибродуговом процессе обеспечивается возможность весьма неглубокого провара основного металла, больших скоростей остывания металла сварочной ванны и создание наплавленного слоя очень малой толщины (0,5—3,0 мм).
Эти особенности вибродугового процесса дают возможность применять его при наплавке деталей небольшого размера с малой толщиной стенок, где для восстановления рабочих размеров требуется нанесение тонкого слоя металла на износившуюся поверхность детали, например, при восстановлении термически обработанных деталей машин. Производительность процесса весьма невелика и составляет 1—2 кг наплавленного металла в1ч.
Принципы механизации и автоматизации вибродуговой сварки такие же, как и других видов автоматической электродуговой сварки, за исключением механизма подачи проволоки, снабженного вибратором.
Преимущества вибродуговой сварки:
1) незначительная глубина проплавлення и слабое термическое воздействие на основной металл;
2) возможность сварки и наплавки в любом пространственном положении;
3) малая толщина (0,5—3 мм) наплавленного слоя;
4) весьма малые сварочные деформации.
Недостатки:
1) невысокая производительность процесса сварки или наплавки (1—2 кг/ч при силе тока 100—250 а);
2) неоднородность структуры и свойств наплавленного металла;
3) усложненная конструкция сварочной головки вследствие наличия вибратора и устройства для подачи охлаждающей жидкости.
Область рационального применения:
Наплавка тонкого слоя металла на детали небольшого размера, где недопустимы деформации и не предъявляются высокие требования к качеству наплавки, например, при восстановлении размеров термически обработанных деталей (оси, шейки валов, автотракторные детали и т. д.). Однако под флюсовой защитой могут наплавляться и ответственные детали с высоким качеством наплавки.
8. ЭЛЕКТРОШЛАКОВАЯ СВАРКА
Электрошлаковая сварка является разновидностью механизированной сварки плавлением, принципиально отличающейся от дуговой сварки тем, что источником нагрева является не электрическая дуга, а джоулево тепло, выделяющееся в жидкой шлаковой ванне при прохождении через нее сварочного тока.
Электрошлаковоая сварка может производиться:
а) проволочными электродами;
б) пластинчатыми электродами
В пространстве, образованном кромками свариваемых деталей и шлакоудер-живающими приспособлениями (медными пластинами или ползунами), создается ванна жидкого шлака (расплавленного флюса), в которую погружается металлический стержень—электрод (один или несколько – в зависимости от толщины свариваемых деталей). Сварочный ток, проходя между электродом и основным металлом через шлаковую ванну нагревает и поддерживает в ней высокую температуру и электропроводность.
При электрошлаковой сварке температура шлаковой ванны выше температуры плавления металла и поэтому шлак оплавляет кромки соединяемого металла и расплавляет погруженный в нее электродный стержень (проволоку, пластину и др.), непрерывноподаваемый сварочной головкой - в шлаковую ванну по мере его расплавления.
Глубина шлаковой ванны выбирается в зависимости от технологических условий (состава основного металла, режима сварки, типа и размеров электрода) и колеблется в пределах 25—70 мм. Ток подводится к шлаковой ванне от источника переменного или постоянного тока через основной металл — снизу и через непрерывно подаваемый электрод, погруженный в шлаковую ванну,— сверху. К электроду ток подводится с помощью специального криволинейного мундштука. При этом электрод располагается посредине шлаковой ванны, либо перемещается в зазоре возвратно-поступательным пилообразным движением (от ползуна к ползуну) для более равномерного прогрева ванны и проплавлення кромок по всей толщине спариваемых деталей.
В зависимости от степени автоматизации рабочих операций, электрошлаковая сварка, как и электродуговая, может быть автоматической и полуавтоматической. Различие между ними состоит в том, что при автоматической электрошлаковой сварке автоматизированы с помощью специальных электроприводов все основные рабочие движения и операции: подача электродного металла в шлаковую ванну по мере его плавления; вертикальное рабочее движение по шву с заданной скоростью сварки; горизонтальные возвратно-поступательные перемещения электрода вдоль шлаковой ванны и др. При полуавтоматической электрошлаковой сварке некоторые из рабочих движений осуществляются вручную, в частности, вертикальное рабочее движение аппарата по шву производится с помощью ручного привода типа «трещетки» или другого. Такой привод периодически приводится в движение сварщиком по мере наращивания шва.
Методы электрошлаковой сварки различаются в зависимости от типа электрода. По этому признаку различают:
· сварку электродной проволокой диаметром 2,5—3 мм (одной или несколькими;
· сварку электродной пластиной большого сечения (одной или несколькими);
· сварку плавящимся мундштуком, который представляет собой комбинацию электродной пластины и электродных проволок. В этом случае пластина, длина которой практически равна длине свариваемого шва, укрепляется неподвижно в зазоре между свариваемыми кромками и по мере сварки шва расплавляется. Преимущества электрошлаковой сварки:
1)возможность сваривать за один проход толстостенные изделия практически неограниченной толщины — до 3000 мм и более;
2)высокая производительность сварки металла большой толщины (от 60 мм и более), превышающая производительность многослойной сварки под флюсом в 5—6 раз и ручной — в 20—25 раз;
3)высокий коэффициент плавления электрода, достигающий 20— 27 г/а-ч против 14—18 г/а-ч при сварке под флюсом, и 8— 10 г/а-ч при ручной сварке покрытыми электродами;
4)расход флюса н 15—20 раз меньше, чем при автоматической сварке под флюсом;
5)вследствие высокого коэффициента наплавки электрода и малого расхода энергии на расплавление флюса, энергоемкость процесса значительно меньше, чем сварки под флюсом (в 1,5—2 раза);
6)стоимость сварного соединения, выполненного электрошлаковой сваркой (особенно при толщинах свыше 60 мм) значительно ниже стоимости соединения, выполненного многослойной сваркой под флюсом, вследствие малого расхода флюса; малого удельного расхода электроэнергии; уменьшения количества наплавленного металла на 1 пог. м шва; упрощения и удешевления подготовки кромок, поскольку отпадает необходимость в фасонной разделке кромок и в их механической обработке на металлорежущих станках;
7)повышенное качество сварных соединений: стойкость против образования пор и кристаллизационных (горячих) трещин в металле шва; стойкость металла околошовной зоны против закалочных трещин вследствие благоприятного термического цикла сварки,
8)возможность изготовления сложных, уникальных по своим габаритам и весу машинных деталей путем электрошлаковой сварки нескольких отливок или поковок нормального размера и веса.
Недостатки:
1)невозможность или нецелесообразность сварки металла толщиной менее 20—25 мм, а также угловых швов,
2)необходимость располагать свариваемый шов в вертикальном положении;
3)металл шва имеет ярко выраженную литую структуру с несколько пониженными пластическими свойствами;
4)при сварке некоторых сталей, в частности котельных, длительное температурное воздействие на металл околошовной зоны вызывает перегрев и изменяет структуру, образуя характерную зону крупного зерна с пониженными пластическими свойствами, особенна ударной вязкостью (охрупчивание металла).
5) недопустимы или крайне нежелательны остановки процесса сварки в середине шва, так как в этом месте почти неизбежно появление пепронаров, усадочных трещин и других дефектов. После такой вынужденной остановки приходится удалять весь дефектный участок шва.
Области рационального применения:
1. Единичное и серийное производство толстостенных сварных изделий в тяжелом машиностроении, в том числе изготовление деталей уникальных крупных машин,
2. Сварные соединения из алюминия и его сплавов толщиной 60…200 мм, в том числе стыковые соединения больших сечений- до 200 000 мм2.
Занятие №10 (05.10.2015)
|
|
Поперечные профили набережных и береговой полосы: На городских территориях берегоукрепление проектируют с учетом технических и экономических требований, но особое значение придают эстетическим...
Архитектура электронного правительства: Единая архитектура – это методологический подход при создании системы управления государства, который строится...
Организация стока поверхностных вод: Наибольшее количество влаги на земном шаре испаряется с поверхности морей и океанов (88‰)...
Адаптации растений и животных к жизни в горах: Большое значение для жизни организмов в горах имеют степень расчленения, крутизна и экспозиционные различия склонов...
© cyberpedia.su 2017-2024 - Не является автором материалов. Исключительное право сохранено за автором текста.
Если вы не хотите, чтобы данный материал был у нас на сайте, перейдите по ссылке: Нарушение авторских прав. Мы поможем в написании вашей работы!