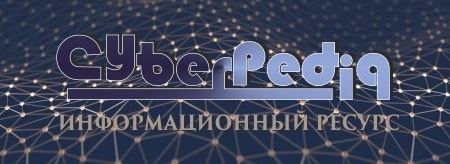
История развития хранилищ для нефти: Первые склады нефти появились в XVII веке. Они представляли собой землянные ямы-амбара глубиной 4…5 м...
Своеобразие русской архитектуры: Основной материал – дерево – быстрота постройки, но недолговечность и необходимость деления...
Топ:
Отражение на счетах бухгалтерского учета процесса приобретения: Процесс заготовления представляет систему экономических событий, включающих приобретение организацией у поставщиков сырья...
Устройство и оснащение процедурного кабинета: Решающая роль в обеспечении правильного лечения пациентов отводится процедурной медсестре...
Организация стока поверхностных вод: Наибольшее количество влаги на земном шаре испаряется с поверхности морей и океанов...
Интересное:
Инженерная защита территорий, зданий и сооружений от опасных геологических процессов: Изучение оползневых явлений, оценка устойчивости склонов и проектирование противооползневых сооружений — актуальнейшие задачи, стоящие перед отечественными...
Наиболее распространенные виды рака: Раковая опухоль — это самостоятельное новообразование, которое может возникнуть и от повышенного давления...
Подходы к решению темы фильма: Существует три основных типа исторического фильма, имеющих между собой много общего...
Дисциплины:
![]() |
![]() |
5.00
из
|
Заказать работу |
Содержание книги
Поиск на нашем сайте
|
|
Износ металлорежущего инструмента увеличивает погрешность на размер, влияет на качество обрабатываемой поверхности, увеличивает силы резания приводит к искажению поверхностного слоя детали.Износ и технологический период стойкости инструмента можно уменьшить за счет применения прогрессивных материалов и сборных инструментов оснащенных сменными многогранными пластинами.
Процесс резания сопровождается большим давлением на режущий инструмент, трением и тепловыделением. Такие условия работы выдвигают ряд требований, которым должны удовлетворять материалы, предназначенные для изготовления режущего инструмента.
Инструментальные материалы должны иметь высокую твердость, превышающую твердость обрабатываемого материала. Высокая твердость материала режущей части может быть обеспечена физико-механическими свойствами материала (алмазы, карбиды кремния, карбиды вольфрама и др.) или его термической обработкой (закалка и отпуск).
В процессе резания срезаемый слой давит на переднюю поверхность инструмента, создавая в пределах площади контакта нормальное напряжение. При резании конструкционных материалов с установленными режимами резания нормальные контактные напряжения могут достигать значительных величин. Режущий инструмент должен выдерживать такие давления без хрупкого разрушения и пластического деформирования. Так как режущий инструмент может работать в условиях переменных значений сил, например из-за неравномерно снимаемого слоя металла заготовки, важно, чтобы инструментальный материал сочетал в себе высокую твердость с сопротивляемостью на сжатие и изгиб, обладал высоким пределом выносливости и ударной вязкостью. Таким образом, инструментальный материал должен отличаться высокой механической прочностью.
|
При резании со стороны заготовки на инструмент действует мощный тепловой поток, в результате чего на передней поверхности инструмента устанавливается высокая температура. При этом режущие элементы инструмента теряют свою твердость и изнашиваются из-за интенсивного разогревания. Поэтому важнейшим требованием, предъявляемым к инструментальному материалу, является его высокая теплостойкость – способность сохранять при нагреве твердость, необходимую для осуществления процесса резания.
Перемещение стружки по передней и задней поверхностям резания инструмента при высоких контактных напряжениях и температурах приводят к изнашиванию рабочих поверхностей. Таким образом, высокая износостойкость – важнейшее требование, предъявляемое к характеристике инструментального материала. Износостойкость – это способность инструментального материала сопротивляться при резании удалению его частиц с контактных поверхностей инструмента. Она зависит от твердости, прочности и теплостойкости инструментального материала.
Инструментальный материал должен обладать высокой теплопроводностью. Чем она выше, тем меньше опасность возникновения шлифовочных ожогов и трещин.
В промышленности используется большое количество инструмента, что требует соответствующего расхода инструментального материала. Инструментальный материал должен быть по возможности дешевым, не содержать дефицитных элементов, что не будет увеличивать стоимость инструмента и, соответственно, стоимость изготовления деталей.
В соответствии с химическим составом и физико-механическими свойствами инструментальные материалы делят на [3]:
углеродистые инструментальные стали;
легированные инструментальные стали;
быстрорежущие стали и сплавы (высоколегированные);
|
твердые сплавы;
минералокерамику;
абразивные материалы;
алмазные материалы.
Наиболее распространенными из углеродистых инструментальных материалов являются марки: У9А, У10А, У12А, У13А.
Маркировка углеродистых инструментальных сталей расшифровывается так: буква «У» означает, что сталь углеродистая; цифра указывает на содержание в ней углерода в десятых долях процента; буква «А» говорит о том, что сталь высококачественная.
Углеродистые стали из-за отсутствия легирующих химических элементов хорошо шлифуются и являются дешевым инструментальным материалом. Вместе с тем инструмент, изготовляемый из углеродистой стали, сравнительно быстро изнашивается и теряет твердость, полученную при закалке.
Из этих сталей изготовляют инструменты малых габаритных размеров для работы по мягким материалам с малой скоростью резания. Из сталей марок У7А, У7, У8А, У8, У8ГА, У9А и У9 производят различные слесарные и кузнечные инструменты, инструменты для обработки дерева, кожи и др. Из этих же марок сталей изготовляют державки и корпуса инструментов, оснащенных пластинками из твердого сплава.
Легированные инструментальные стали получаются путем добавления в углеродистые стали небольшого количества легирующих элементов: хрома (Х), вольфрама (В), ванадия (Ф), кремния (С), марганца (Г). Наибольшее применение при изготовлении инструментов нашли стали марок ХВ5, ХВГ, 9ХС.
Сталь ХВ5 после термообработки приобретает весьма высокую твердость (HRC 67…67), плохо прокаливается, но по прочности не уступает стали У12А, но из-за большой твердости обладает высоким сопротивлением малым пластическим деформациям. Для изготовленных из нее инструментов характерна высокая формоустойчивость лезвий. Эта сталь применяется для изготовления инструментов, работающих при небольших скоростях резания.
Сталь ХВГ после закалки и отпуска приобретает твердость HRC 63…65 и достаточно высокую вязкость, отличается малыми объемными изменениями при закалке, хорошо прокаливается, но имеет пониженное сопротивление малым пластическим деформациям. Инструмент, изготовленный из этой стали, мало деформируется и хорошо поддается правке.
Сталь 9ХС после термообработки приобретает твердость HRC 63…64. Она обладает хорошей закаливаемостью. Инструмент из этой стали малодеформируется. Сталь также малочувствительна к перегреву. Сталь 9ХС особо пригодна для изготовления инструментов с тонкими режущими элементами.
|
Высоколегированные инструментальные (быстрорежущие) стали и сплавы получаются при добавлении в углеродистую сталь большого количества легирующих элементов: вольфрама, ванадия, молибдена, хрома. Введением в сталь вольфрама, ванадия, молибдена и хрома в значительных количествах получают сложные карбиды, связывающие почти весь углерод, что обеспечивает возрастание теплостойкости быстрорежущей стали.
В отличие от углеродистых и легированных инструментальных сталей быстрорежущие стали обладают более высокими твердостью, прочностью, тепло- и износостойкостью, сопротивлением малым пластическим деформациям, хорошей прокаливаемостью. Благодаря высокой теплостойкости быстрорежущих сталей инструменты, изготовленные из этих сталей, работают со скоростями резания, в 2,5…3 раза более высокими, чем те, которые при равной стойкости допускают углеродистые инструменты. По уровню теплостойкости быстрорежущие стали разделяют на:
стали нормальной теплостойкости (Р18, Р9, Р12, Р6М3 и Р6М5);
стали повышенной теплостойкости, легированные ванадием (ванадиевые стали Р18Ф2, Р14Ф4, Р9Ф5) и кобальтом (кобальтовые стали Р9К5, Р9К10);
высоколегированные стали и сплавы высокой теплостойкости (быстрорежущие стали повышенной прочности) – безуглеродистые сплавы (Р18М3К25, Р18М7К25 и Р10М5К25), отличающиеся содержанием вольфрама и молибдена.
Кроме традиционных быстрорежущих сталей, получаемых плавкой, в последнее время освоено производство порошковых быстрорежущих сталей, имеющих более высокие режущие свойства за счет особой мелкозернистой структуры. Такие стали позволяют получить лезвия с очень малым начальным радиусом округления режущей кромки.
Широкое применение быстрорежущей стали при изготовлении самых разных инструментов объясняется ее хорошими режущими и технологическими свойствами. Из быстрорежущих сталей изготовляют различные режущие инструменты, в том числе и фрезы для обработки древесных и композиционных материалов. Ввиду высокой стоимости быстрорежущих сталей, их, в основном, применяют при изготовлении сборного инструмента в виде режущих пластин.
|
Твердые сплавы. Помимо сборного инструмента, с пластинами из быстрорежущих сталей широкое распространение получили конструкции фрез, оснащенных твердым сплавом. В отличие от углеродистых, легированных и быстрорежущих сталей, производимых методом выплавки в электроплавильных печах с последующей прокаткой, твердые сплавы получают металлокерамическим методом порошковой металлургии (спечением). Исходными материалами для изготовления твердых сплавов являются порошки карбидов тугоплавких металлов: вольфрама, титана, тантала и не образующего карбидов кобальта. Порошки смешивают в определенных пропорциях, прессуют в формах и спекают при температуре 1500…20000С. При спекании твердые сплавы приобретают высокую твердость и в дополнительной термической обработке не нуждаются.
Карбиды вольфрама, титана и тантала обладают высокими тугоплавкостью и твердостью. Они образуют режущую основу сплава, а кобальт, по сравнению с карбидами вольфрама, титана и тантала, значительно мягче и прочнее, и поэтому в сплаве он является связкой, цементирующей режущую основу. Увеличение количества карбидов вольфрама, титана, тантала приводит к увеличению твердости и теплостойкости сплава и снижает его механическую прочность. При увеличении содержания кобальта твердость и теплостойкость сплава снижаются, но возрастает его прочность.
Промышленность выпускает четыре группы твердых сплавов:
вольфрамовые однокарбидные (ВК), спекаемые из карбида вольфрама и кобальта: ВК2, ВК3М, ВК4, ВК4В, ВК6М, ВК6, ВК6В, ВК8, ВК8В;
вольфрамовые двухкарбидные (титановольфрамовые ТК), спекаемые из карбида вольфрама, карбида титана и кобальта: Т30К4, Т5К6, Т14К8, Т5К10, Т5К12В;
вольфрамовые трехкарбидные (титанотанталовольфрамовые ТТК), спекаемые из карбида титана, карбида тантала и карбида вольфрама и кобальта: ТТ7К12;
безвольфрамовые (ТНТ – КНТ), спекаемые из карбида титана (ТНТ), нитрида титана (КНТ), никеля и молибдена.
Различные физико-механические и режущие свойства инструментов определяются химическим составом марок твердых сплавов. Основные свойства твердых сплавов представлены в табл. 1.2.
Сплавы группы ВК используют для обработки хрупких материалов.
Мелкоразмерные твердосплавные инструменты изготовляют в виде припаиваемых к хвостовикам твердосплавных стержней и коронок или целиком из твердого сплава.
Наряду с вольфрамовыми твердыми сплавами существуют также сплавы, не содержащие карбида вольфрама, и называются безвольфрамовыми твердыми сплавами.
|
Причиной полной или частичной замены карбида вольфрама другими твердыми материалами послужил дефицит вольфрама в качестве сырья для получения металлокерамических твердых сплавов.
Полная замена карбида вольфрама может осуществляться тремя путями [9]:
Применение других твердых материалов, например нитридов, боридов, силицидов, окислов или карбидов неметаллов (карбидов бора и кремния);
Замена карбида вольфрама другими тугоплавкими карбидами металлов (карбидами ниобия, циркония, гафния, ванадия и др.) или их бинарными или тройными твердыми сплавами;
Простое исключение карбида вольфрама из состава твердого сплава.
Безвольфрамовые твёрдые сплавы по сравнению с вольфрамовыми имеют меньшую прочность на изгиб, но обладают более высокой твёрдостью и низкой схватываемостью со сталями. Инструменты из этих сплавов работают по сталям практически без наростообразования, что и определяет область их применения (чистовое и получистовое точение и фрезерование малолегированных, углеродистых сталей, чугуна и цветных сплавов). Износостойкость в 1,2 - 1,5 раза выше, чем у сплавов группы ТК. Основные физико-механические свойства безвольфрамовых твердых сплавов представлены в табл. 1.7.
Недостатком является то, что безвольфрамовые твердые сплавы плохо поддаются пайке и заточке вследствие неудовлетворительных термических свойств и поэтому применяются в основном в виде неперетачиваемых пластин.
Материалом для изготовления инструментов может служить также минералокерамика, представляющая собой кристаллический оксид алюминия (Al2O3). Широкое распространение получила минеральная керамика марки ЦМ-332.
В результате спекания минералокерамика становится поликристаллическим телом, которое состоит из мельчайших кристаллов корунда и межкристаллитной прослойки в виде аморфной стекловидной массы. Минералокерамика является дешевым и доступным инструментальным материалом, так как не содержит дефицитных и дорогих элементов, являющихся основой инструментальных сталей и твердых сплавов.
Кроме того, минералокерамика обладает высокой твердостью и исключительно высокой теплостойкостью. По теплостойкости минеральная керамика превосходит все распространенные инструментальные материалы, что позволяет минералокерамическому инструменту работать со скоростями резания, значительно превышающими скорости резания твердосплавных инструментов, и что является основным достоинством минеральной керамики.
Вместе с указанными достоинствами минералокерамики она имеет недостатки, ограничивающие ее применение: пониженную прочность на изгиб, низкую ударную вязкость, исключительно низкую сопротивляемость циклическому изменению тепловой нагрузки. В результате этого при прерывистом резании на контактных поверхностях инструмента возникают температурные усталостные трещины, являющиеся причиной преждевременного выхода инструмента из строя.
Низкая прочность на изгиб и высокая хрупкость минеральной керамики позволяют использовать ее лишь в инструментах для обработки конструкционных материалов на чистовых операциях с непрерывным точением и с малыми сечениями срезаемого слоя при отсутствии толчков и ударов.
Режущий инструмент оснащается пластинками из минералокерамики определенных форм и размеров. Пластинки крепятся к корпусу инструментов припаиванием, приклеиванием и механическим путем.
Все шире в деревообработке применяют алмазные и сверхтвердые материалы, которые можно разделить на три разновидности:
природные и синтетические алмазы в виде моно- и поликристаллов;
кубический нитрид бора, в виде моно- и поликристаллов;
синтетические поликристаллические композиционные материалы (композиты), получаемые путем синтеза или спекания.
Природные алмазы представляют собой особую группу материалов для оснащения режущих инструментов.
Разновидностями алмаза являются: баллас, карбонадо, борт. Полезным свойством алмазов является, в первую очередь, исключительно высокая их твердость. Высокая теплопроводность, намного превышающая теплопровод-
ность всех известных инструментальных материалов, и малый коэффициент линейного расширения алмаза позволяют проводить алмазным инструментом точную размерную обработку. Низкий коэффициент трения об обрабатываемый материал и малая склонность к адгезии обеспечивают при резании алмазными инструментами малую шероховатость поверхности.
В промышленности используют как природные (марки А), так и синтетические алмазы (марок АСО, АСР, АСВ и др.). Синтетические алмазы получают из графита и углеродистых веществ. Разновидности природного алмаза: борт и карбонадо – используют только в промышленности.
К синтетическим сверхтвердым материалом того же назначения, что и алмаз, относят кубический нитрид бора (эльбор). Он образуется в результате химического соединения бора и азота. Твердость эльбора ниже, чем алмаза, однако по теплостойкости кубический нитрид бора превосходит алмаз, но по теплопроводности примерно в 3 раза ниже его. Производство крупных поликристаллических образований кубического нитрида бора диаметром 3…4 и длиной 5…6 мм, обладающих высокой прочностью, позволяет оснащать им режущий инструмент.
|
|
Биохимия спиртового брожения: Основу технологии получения пива составляет спиртовое брожение, - при котором сахар превращается...
История создания датчика движения: Первый прибор для обнаружения движения был изобретен немецким физиком Генрихом Герцем...
Наброски и зарисовки растений, плодов, цветов: Освоить конструктивное построение структуры дерева через зарисовки отдельных деревьев, группы деревьев...
Особенности сооружения опор в сложных условиях: Сооружение ВЛ в районах с суровыми климатическими и тяжелыми геологическими условиями...
© cyberpedia.su 2017-2024 - Не является автором материалов. Исключительное право сохранено за автором текста.
Если вы не хотите, чтобы данный материал был у нас на сайте, перейдите по ссылке: Нарушение авторских прав. Мы поможем в написании вашей работы!