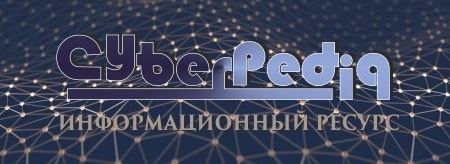
Индивидуальные очистные сооружения: К классу индивидуальных очистных сооружений относят сооружения, пропускная способность которых...
Адаптации растений и животных к жизни в горах: Большое значение для жизни организмов в горах имеют степень расчленения, крутизна и экспозиционные различия склонов...
Топ:
Проблема типологии научных революций: Глобальные научные революции и типы научной рациональности...
Отражение на счетах бухгалтерского учета процесса приобретения: Процесс заготовления представляет систему экономических событий, включающих приобретение организацией у поставщиков сырья...
Устройство и оснащение процедурного кабинета: Решающая роль в обеспечении правильного лечения пациентов отводится процедурной медсестре...
Интересное:
Уполаживание и террасирование склонов: Если глубина оврага более 5 м необходимо устройство берм. Варианты использования оврагов для градостроительных целей...
Лечение прогрессирующих форм рака: Одним из наиболее важных достижений экспериментальной химиотерапии опухолей, начатой в 60-х и реализованной в 70-х годах, является...
Подходы к решению темы фильма: Существует три основных типа исторического фильма, имеющих между собой много общего...
Дисциплины:
![]() |
![]() |
5.00
из
|
Заказать работу |
Тема 1 Технология производства сварочных конструкций и заготовленные операции
![]() |
Литые, кованые и штампованные заготовки обычно поступают на сварку в виде, не требующем дополнительных операций. По - другому обстоит дело с деталями из проката. После подбора металла по размерам и маркам стали необходимо выполнить следующие операции: правку, разметку, резку, обработку кромок, гибку и очистку под сварку.
![]() |
Zzl IЛ |
Рис. 13.29. Виды деформации листовой стали: 1 — волнистость; 2 — серповидность в плоскости; 3 — местные выпучи - ны; 4—заломленные кромки; 5 — местная погнутость; 6 — волнистость поперек части листа |
Листовой прокат требует правки в том случае, если его поставляют е неправленом виде, а также если деформации возникли при транспортировании. Наиболее часто встречающиеся виды деформирования изображены на рис. 13.29.
Правка осуществляется созданием местной пластической деформации и обычно производится в холодном состоянии. Для устранения волнистости листов и полос толщиной от 0,5 до 50 мм широко используют многовалковые машины (число валков больше пяти).
Исправление достигается многократным изгибом при пропускании листов между верхним и нижним рядами валков, расположенных в шахматном порядке (рис. 13.30,а). Листы толщиной менее 0,5 мм правят растяжением с помощью приспособлений на прессах или на специальных растяжных машинах.
Серповидность листовой и широкополосной стали поддается правке в ограниченной степени. Ее выполняют на многовалковых листоправильных вальцах с применением прокладок, выкладываемых у вогнутой кромки.
![]() |
Правку мелко - и среднесортового, а также профильного проката производят на роликовых машинах (рис. 13.30,6), работающих по той же схеме, что и листоправильные. Для двутавров и швеллеров такой способ используется только для исправления в плоскости меньшего момента сопротивления. Исправление в другой плоскости осуществляют изгибом на правильно-гибочных прессах кулачкового типа (рис. 13.30,0).
При постоянном ходе толкателя 3 задаваемая деформация профиля 2 регулируется изменением расстояния между опорами 1. На прессах правят и толстолистовой прокат с толщиной более 50 мм.
Холодная деформация сопровождается уменьшением пластичности металла. Поэтому относительное остаточное удлинение 6 наиболее деформированных волокон необходимо ограничивать. Например согласно СНиП 18—75 при холодной правке 6^1%: при холодной гибке 6^2%, что соответствует радиусу изгиба не менее 50толщин листа приправке и не менее25 толщин листа при гибке. Исходя из этого, устанавливают предельные значения искривлений, исправление которых еще допускается в холодном состоянии. Так, холодная правка серповидности широкополосной и универсальной стали на вальцах, а полос шириной до 200 мм на кулачковом прессе разрешается только при стреле серповидности f^t2!(800b), где I — длина полосы; b — ширина полосы.
В случае необходимости создания более значительных деформаций правка и гибка стали должны производиться в горячем состоянии после нагрева до 900—1000°С для стали классов до С 46/33 включительно и до 900—950°С для стали классов С 52/40 и С 60/46. Деформирование при высокой температуре сопровождается процессом рекристаллизации, и пластические свойства металла не снижаются.
Разметка. Индивидуальная разметка трудоемка. Оптический метод позволяет вести разметку без шаблона — по чертежу, проектируемому на размечаемую поверхность. Разметочно-маркировоч - ные машины с пневмокернером производят разметку со скоростью до 8—10 м/мин при погрешности ±1 мм. В этих машинах применяют программное управление. Использование приспособлений для мерной резки проката, а также машин для тепловой резки с масштабной фотокопировальной или программной системой управления позволяет обходиться без разметки.
![]() |
Резка и обработка кромок. Резка деталей с прямолинейными кромками из листов толщиной до 40 мм, как правило, производится на гильотинных ножницах (рис. 13.31,а). Разрезаемый лист 2 заводится между нижним 1 и верхним 4 ножами до упора 5 и зажимается прижимом 3. Верхний нож, нажимая на лист, производит скалывание. Погрешность размера обычно составляет ±(2,0—3,0) мм при резке по разметке и ±(1,5—2,5) мм при резке по упору. Прямой рез со скосом кромки под сварку можно получить, используя специальные ножницы (рис. 13.31,6). При включении гидроцилиндра 1 качающийся ножедержатель 3 поворачивается сначала вокруг оси А, производя прямой рез с помощью ножа 7. Когда упор 2 ножедержателя 3 дойдет до выступа детали 4, они поворачиваются совместно вокруг оси Б, отводя прижим 5 от регулируемого упора 6. Нож 8 совершает рез на скос.
Дисковые ножницы (рис. 13.31,в) позволяют осуществлять вырезку листовых деталей с непрямолинейными кромками толщиной s=20-*-25 мм. Для получения листовой заготовки заданной ширины с параллельными кромками дисковые ножи целесообразно располагать попарно на заданном расстоянии друг от друга (рис. 13.31,в, г).
При резке на ножницах металл подвергается значительной пластической деформации. Если кромка реза в. дальнейшем попадает в зону сварки и полностью переплавляется, то дополнительной обработки не требуется. Если же эта кромка остается свободной, а конструкция работает при переменных нагрузках, то слой пластически деформированного металла целесообразно удалить последующей механической обработкой.
Для поперечной резки фасонного проката применяют пресс - нооюницы с фасонными ножами или дисковые пилы. В некоторых случаях применяют резку гладким диском либо с помощью трения, либо контактно-дуговым оплавлением.
Производительным является процесс вырубки в штампах. При номинальных размерах деталей 1—4 м погрешности могут составлять +(1,0—2,5) мм.
Разделительная термическая резка менее производительна, чем резка на ножницах, но более универсальна и применяется для получения стальных заготовок разных толщин как прямолинейного, так и криволинейного очертания. Наряду с газопламенной кислородной резкой все шире применяют плазменнодуговую резку, позволяющую обрабатывать практически любые металлы и сплавы. Использование в качестве плазмообразующего газа сжатого воздуха дает не только экономические, но и технические преимущества: высокое качество реза сочетается с большой скоростью резки, особенно сталей малой и средней толщины (до 60 мм). Недостатком воздушно-плазменной резки является насыщение поверхностного слоя кромок азотом, что способствует образованию пор при сварке. Поэтому кромки в большинстве случаев зачищают стальной щеткой или подвергают дополнительной механической обработке. Предотвращение пор в швах при сварке по кромкам, подготовленным воздушно-плазменной резкой, возможно и без зачистки кромок, однако в этом случае требуется четкое соблюдение технических рекомендаций. После кислородной резки зачистки кромок под сварку, как правило, не требуется.
Ручную и полуавтоматическую резку листов производят обычно по разметке, автоматическую — с помощью копирных устройств, по масштабному чертежу или на машинах с программным управлением. Масштабные чертежи содержат информацию только о траектории, поэтому переход от одного реза к другому при раскрое целого листа приходится осуществлять вручную. Использование машин с цифровым программным управлением позволяет автоматизировать процесс резки в пределах всего листа при одновременном повышении точности реза. При вырезке заготовок небольшой толщины в ряде случаев эффективно использование резки листов пакетом толщиной порядка 100 мм.
Термическую резку применяют и при создании скоса кромок. Если эта операция совмещается с разделительной резкой, то односторонний скос с притуплением получают, используя одновременно два резака, а двусторонний скос — три резака. После вырезки Детали иногда приходится править.
Начинают применять лазерную резку. Ее преимущества— чрезвычайно малая ширина реза (доли миллиметра) и возможность резки материала малой толщины (от 0,05 мм).
Механическую обработку кромок на станках производят: а) для обеспечения требуемой точности сборки; б) для обработки фасок сложного очертания; в) для удаления металла кромок, обрезанных ножницами или с помощью термической резки, когда это считается необходимым. При обработке длинных кромок применяют кромкострогальные станки, более коротких — торцефрезерные.
![]() |
6) |
е)
Ь- | V | |
—>- | а | >1 — |
Рис. 13.32. Схемы вальцовки обечаек: а — обечайка с необвальцованными кромками; б, в — установка листа в трех - и четырехвалковых вальцах; г — положение листа в начале гибки в вальцах; д — гибка листа в двухвалковых вальцах |
Гибка. Холодную гибку листовых элементов толщиной до 60 мм для получения деталей цилиндрической и конической формы осуществляют на листогибочных вальцах с валками длиной до 13 м. При вальцовке в холодном состоянии отношение радиуса изгиба к толщине листа ограничивают допустимым значением создаваемой пластической деформации. При гибке в вальцах концевой участок листа размером а (рис. 13.32,а) остается почти плоским. Ширина этого участка при использовании трехвалковых вальцов определяется расстояниями между осями валков а (рис. 13.32,6). В четырехвалковых вальцах несвальцованным остается только участок шириной (1-^—2)s, где s — толщина листа (рис. 13.32,в). Более правильное очертание концевого участка листа может быть получено либо калибровкой уже сваренной обечайки, либо предварительной подгибкой кромок под прессом или на листогибочных вальцах с толстым подкладным листом, согнутым по заданному радиусу. После подгибки кромок лист устанавливают в гибочные вальцы, выверяют параллельность оси вала и кромки листа и начинают гибку со средней части листа (рис. 13.32,г).
Использование двухвалковых гибочных вальцев с эластичным полиуретановым покрытием нижнего валка (рис. 13.32,5) устраняет необходимость дополнительной подгибки кромок при вальцовке обечаек из листов толщиной до б мм. Упругое покрытие обжимает листовую заготовку вокруг жесткого верхнего валка и обеспечивает равномерный изгиб по всей длине.
Листовые элементы с поверхностью пространственной кривизны получают на специальных вальцах с валками переменного диаметра. Для формообразования элементов оболочек больших размеров применяют штамповку взрывом. При серийном и массовом производстве для получения элементов с поверхностью сложного очертания широко используют холодную штамповку из листового материала толщиной до 10 мм. Высокая производительность, точность размеров и формы получаемых заготовок, их низкая себестоимость обеспечивают создание весьма технологичных штампосварных изделий.
При холодной гибке профильного проката и труб используют роликогибочные машины и трубогибочные станки. Когда возникают трудности, связанные с нарушением формы поперечного сечения, целесообразно использовать специальные гибочные станки с индукционным нагревом непрерывно перемещаемой и изгибаемой заготовки. Деформируемый участок, нагретый до температуры 950—1000°С, имеет небольшую протяженность, обладает малым сопротивлением пластической деформации и повышенной устойчивостью, что предотвращает образование гофров в зоне сжатия.
Для получения деталей из толстого листового металла применяют горячую гибку. Ее осуществляют на гибочных вальцах и на прессах.
Тема 2 Технология изготовления сварных конструкций
Сварные металлоконструкции давно нашли свое применение в строительной отрасли, в машиностроении, в автомобильной промышленности и в других сферах производства. С каждым годом производство сварных конструкций показывает все увеличивающиеся темпы развития — и причина этого состоит в том, что потребители поняли все преимущества металлических конструкций, произведенных с помощью сварки.
К достоинствам сварных конструкций относится:
-высокое качество и прочность соединения;
-надежность;
-удобство применения;
-долгий срок службы;
-небольшой вес;
-экономия металла.
Если же говорить о недостатках сварных металлических конструкций, то к ним можно отнести неустойчивость металла к коррозии. Но современные технологии изготовления металлоконструкций и способы обработки металла позволяют легко справиться с этой проблемой.
Особенности сварных конструкций.
1.Сварные конструкции характеризуются максимально прочным соединением отдельных деталей между собой, так как технология производства сварных конструкций основана на слиянии частей конструкций в единое целое на молекулярном уровне. Металл на краях деталей расплавляется до жидкого состояния, и таким образом происходит обмен молекулами. В результате получается конструкция по своей прочности максимально близкая к прочности цельной детали.
2.Еще одной особенностью сварных конструкций является то, что для их изготовления требуется меньше метала, чем для изготовления конструкций, соединенных с помощью заклепок или литых соединений. Причем, экономия может достигать довольно значительных объемов — до 20%, а это значит, что сварное соединение можно считать эффективным не только с точки зрения расхода материалов, но и с точки зрения стоимости всей металлоконструкции. То есть получается, что изготовление металлоконструкций с помощью сварного соединения экономически обладает большей рентабельностью, чем любые другие конструкции.
3.Имеется у сварных конструкций и еще одна отличительная черта, логично вытекающая из предыдущей особенности — они весят меньше, чем конструкции, сделанные методом литья или собранные с помощью заклепочного соединения. И при этом по своей прочности они ничуть не уступают, а даже превосходят эти виды конструкций.
Технология производства сварных конструкций включает в себя несколько основных этапов. Для изготовления подобных металлоконструкций можно применять различные методы сварки — от автоматической и полуавтоматической до ручной электродуговой. Сварка может вестись в среде защитных газов, под флюсом и т.д. Способы сварных соединений также могут быть различными — тавровыми, торцевыми, стыковыми, угловыми и т.д.
Первым этапом производства сварных конструкций является подготовка всей технической документации, необходимой для создания детали, к которой предъявляются определенные требования.
Также важным этапом производства сварных конструкция является подготовка отдельных деталей к сварке. И здесь самое большое внимание следует уделять подготовке кромок деталей. Кромки стачиваются под определенным углом — и сделать это можно как с помощью шлифовальной машины, так и при помощи обычного напильника. Форма разделки кромок также может быть различной, но наиболее эффективной считается Х-образная разделка. Дело в том, что именно такой подход к разделке кромок может гарантировать максимально низкий объем наплавленного металла, получаемого в процессе разогрева кромок деталей, а это значит, что и качество получаемого соединения будет выше.
Одним из важных этапов при производстве сварных конструкций является их сборка. Это не только процесс, который требует большого внимания, но и работа, обладающая большой трудоемкостью — например, если производство конструкции носит индивидуальный характер, то процесс сборки может занимать до 50% всего времени ее изготовления. Дело в том, что именно от качества сборки зависит дальнейшее качество всего сварного соединения. Основными требованиями, предъявляемыми к сборке сварной конструкции, являются:
· точное соответствие размерам, указанным в проектной документации
· правильное расположение зазоров и их постоянные размеры
· точное расположение деталей конструкции, в полном соответствии с проектной документацией
· точность плоскостей конструкции и углов, под которыми они пересекаются
· обеспечение минимально возможного допуска смещения деталей, если производится их стыковое соединение.
В заключении нужно отметить, что разработка технологии производства сварной конструкции производится индивидуально для каждой отдельной подобной конструкции в соответствии с технической документацией, требованиями, предъявляемыми к готовому изделию, а также имеющимся в распоряжении производителя оборудованием.
Адаптации растений и животных к жизни в горах: Большое значение для жизни организмов в горах имеют степень расчленения, крутизна и экспозиционные различия склонов...
Архитектура электронного правительства: Единая архитектура – это методологический подход при создании системы управления государства, который строится...
Своеобразие русской архитектуры: Основной материал – дерево – быстрота постройки, но недолговечность и необходимость деления...
Папиллярные узоры пальцев рук - маркер спортивных способностей: дерматоглифические признаки формируются на 3-5 месяце беременности, не изменяются в течение жизни...
© cyberpedia.su 2017-2024 - Не является автором материалов. Исключительное право сохранено за автором текста.
Если вы не хотите, чтобы данный материал был у нас на сайте, перейдите по ссылке: Нарушение авторских прав. Мы поможем в написании вашей работы!